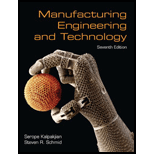
Manufacturing Engineering & Technology
7th Edition
ISBN: 9780133128741
Author: Serope Kalpakjian, Steven Schmid
Publisher: Prentice Hall
expand_more
expand_more
format_list_bulleted
Concept explainers
Textbook Question
Chapter 16, Problem 24QLP
Identify the material and process variables that influence the punch force in shearing, and explain how each of them affects this force.
Expert Solution & Answer

Want to see the full answer?
Check out a sample textbook solution
Students have asked these similar questions
R
αι
g
The system given on the left, consists of three pulleys and
the depicted vertical ropes.
Given:
ri
J₁, m1
R = 2r;
απ
r2, J2, m₂
m1; m2; M3
J1 J2 J3
J3, m3
a) Determine the radii 2 and 3.
B: Solid rotating shaft used in the boat with high speed shown in Figure. The amount of power transmitted at the
greatest torque is 224 kW with 130 r.p.m. Used DE-Goodman theory to determine the shaft diameter. Take the
shaft material is annealed AISI 1030, the endurance limit of 18.86 kpsi and a factor of safety 1. Which criterion
is more conservative?
Note: all dimensions in mm.
1
AA
Motor
300
Thrust
Bearing
Sprocket
100
9750
เอ
Q2: The plate material of a pressure vessel is AISI 1050 QT 205 °C. The plate is rolled to a
diameter of 1.2 m. The two sides of the plate are connected via a riveted joint as shown below. If
the rivet material is G10500 with HB=197 and all rivet sizes M31. Find the required rivet size
when the pressure vessel is subjected to an internal pressure of 500 MPa. Take safety factor = 2.
1.2m
A
B'
A
Chope
olm
10.5
0.23
hope
Chapter 16 Solutions
Manufacturing Engineering & Technology
Ch. 16 - How does sheet-metal forming differ from rolling,...Ch. 16 - What causes burrs? How can they be reduced or...Ch. 16 - Prob. 3RQCh. 16 - Describe the difference between compound,...Ch. 16 - Describe the characteristics of sheet metals that...Ch. 16 - Describe the features of forming-limit diagrams...Ch. 16 - List the properties of materials that influence...Ch. 16 - Give one specific application for each of the...Ch. 16 - Why do tubes buckle when bent? What is the effect...Ch. 16 - Define normal anisotropy, and explain why it is...
Ch. 16 - Describe earing and why it occurs.Ch. 16 - What are the advantages of rubber forming? Which...Ch. 16 - Explain the difference between deep drawing and...Ch. 16 - How is roll forming fundamentally different from...Ch. 16 - What is nesting? What is its significance?Ch. 16 - Describe the differences between compound,...Ch. 16 - What is microforming?Ch. 16 - Explain the advantages of superplastic forming.Ch. 16 - What is hot stamping? For what materials is it...Ch. 16 - What is springback? What is negative springback?Ch. 16 - Explain the differences that you have observed...Ch. 16 - Take any three topics from Chapter 2, and, with...Ch. 16 - Do the same as for Problem 16.22, but for Chapter...Ch. 16 - Identify the material and process variables that...Ch. 16 - Explain why springback in bending depends on yield...Ch. 16 - Explain why cupping tests may not predict well the...Ch. 16 - Identify the factors that influence the...Ch. 16 - Why are the beads in Fig. 16.36b placed in those...Ch. 16 - A general rule for dimensional relationships for...Ch. 16 - Section 16.2 stated that the punch stripping force...Ch. 16 - Is it possible to have ironing take place in an...Ch. 16 - Note the roughness of the periphery of the flanged...Ch. 16 - What recommendations would you make in order to...Ch. 16 - It has been stated that the quality of the sheared...Ch. 16 - Give several specific examples from this chapter...Ch. 16 - As you can see, some of the operations described...Ch. 16 - Through changes in clamping or die design, it is...Ch. 16 - How would you produce the part shown in Fig....Ch. 16 - It has been stated that the thicker the sheet...Ch. 16 - Prob. 41QTPCh. 16 - Calculate the value of R in Problem 16.41. Will...Ch. 16 - Estimate the limiting drawing ratio for the...Ch. 16 - Using Eq. (16.15) and the K value for TNT, plot...Ch. 16 - Section 16.5 states that the k values in bend...Ch. 16 - For explosive forming, calculate the peak pressure...Ch. 16 - Measure the respective areas of the solid outlines...Ch. 16 - Plot Eq. (16.6) in terms of the elastic modulus,...Ch. 16 - What is the minimum bend radius for a 1.0-mm-thick...Ch. 16 - Survey the technical literature and explain the...Ch. 16 - Using the data in Table 16.3 and referring to Eq....Ch. 16 - What is the force required to punch a square hole...Ch. 16 - In Case Study 16.2, it was stated that the reason...Ch. 16 - A cup is being drawn from a sheet metal that has a...Ch. 16 - Prob. 55QTPCh. 16 - Figure P16.57 shows a parabolic profile that will...Ch. 16 - Prob. 59SDPCh. 16 - Consider several shapes to be blanked from a large...Ch. 16 - Prob. 61SDPCh. 16 - Many axisymmetric missile bodies are made by...Ch. 16 - Metal cans are either two-piece (in which the...Ch. 16 - The design shown in Fig. P16.65 is proposed for a...Ch. 16 - Suggest consumer-product designs that could...Ch. 16 - How would you produce the part shown in Fig. 16.44...Ch. 16 - Using a ball-peen hammer, strike the surface of...Ch. 16 - Inspect a common paper punch and observe the shape...Ch. 16 - Obtain an aluminum beverage can and slit it in...Ch. 16 - Prob. 71SDPCh. 16 - Prob. 73SDPCh. 16 - On the basis of experiments, it has been suggested...Ch. 16 - Design a box that will contain a 4-in. 6-in. ...Ch. 16 - Repeat Problem 16.77, but design the box from a...
Knowledge Booster
Learn more about
Need a deep-dive on the concept behind this application? Look no further. Learn more about this topic, mechanical-engineering and related others by exploring similar questions and additional content below.Similar questions
- Continuity equation A y x dx D T معادلة الاستمرارية Ly X Q/Prove that ди хе + ♥+ ㅇ? he me ze ོ༞“༠ ?arrow_forwardQ Derive (continuity equation)? I want to derive clear mathematics.arrow_forwardmotor supplies 200 kW at 6 Hz to flange A of the shaft shown in Figure. Gear B transfers 125 W of power to operating machinery in the factory, and the remaining power in the shaft is mansferred by gear D. Shafts (1) and (2) are solid aluminum (G = 28 GPa) shafts that have the same diameter and an allowable shear stress of t= 40 MPa. Shaft (3) is a solid steel (G = 80 GPa) shaft with an allowable shear stress of t = 55 MPa. Determine: a) the minimum permissible diameter for aluminum shafts (1) and (2) b) the minimum permissible diameter for steel shaft (3). c) the rotation angle of gear D with respect to flange A if the shafts have the minimum permissible diameters as determined in (a) and (b).arrow_forward
- First monthly exam Gas dynamics Third stage Q1/Water at 15° C flow through a 300 mm diameter riveted steel pipe, E-3 mm with a head loss of 6 m in 300 m length. Determine the flow rate in pipe. Use moody chart. Q2/ Assume a car's exhaust system can be approximated as 14 ft long and 0.125 ft-diameter cast-iron pipe ( = 0.00085 ft) with the equivalent of (6) regular 90° flanged elbows (KL = 0.3) and a muffler. The muffler acts as a resistor with a loss coefficient of KL= 8.5. Determine the pressure at the beginning of the exhaust system (pl) if the flowrate is 0.10 cfs, and the exhaust has the same properties as air.(p = 1.74 × 10-3 slug/ft³, u= 4.7 x 10-7 lb.s/ft²) Use moody chart (1) MIDAS Kel=0.3 Q3/Liquid ammonia at -20°C is flowing through a 30 m long section of a 5 mm diameter copper tube(e = 1.5 × 10-6 m) at a rate of 0.15 kg/s. Determine the pressure drop and the head losses. .μ= 2.36 × 10-4 kg/m.s)p = 665.1 kg/m³arrow_forward2/Y Y+1 2Cp Q1/ Show that Cda Az x P1 mactual Cdf Af R/T₁ 2pf(P1-P2-zxgxpf) Q2/ A simple jet carburetor has to supply 5 Kg of air per minute. The air is at a pressure of 1.013 bar and a temperature of 27 °C. Calculate the throat diameter of the choke for air flow velocity of 90 m/sec. Take velocity coefficient to be 0.8. Assume isentropic flow and the flow to be compressible. Quiz/ Determine the air-fuel ratio supplied at 5000 m altitude by a carburetor which is adjusted to give an air-fuel ratio of 14:1 at sea level where air temperature is 27 °C and pressure is 1.013 bar. The temperature of air decreases with altitude as given by the expression The air pressure decreases with altitude as per relation h = 19200 log10 (1.013), where P is in bar. State any assumptions made. t = ts P 0.0065harrow_forward36 2) Use the method of MEMBERS to determine the true magnitude and direction of the forces in members1 and 2 of the frame shown below in Fig 3.2. 300lbs/ft member-1 member-2 30° Fig 3.2. https://brightspace.cuny.edu/d21/le/content/433117/viewContent/29873977/Viewarrow_forward
- Can you solve this for me?arrow_forward5670 mm The apartment in the ground floor of three floors building in Fig. in Baghdad city. The details of walls, roof, windows and door are shown. The window is a double glazing and air space thickness is 1.3cm Poorly Fitted-with Storm Sash with wood strip and storm window of 0.6 cm glass thickness. The thickness of door is 2.5 cm. The door is Poor Installation. There are two peoples in each room. The height of room is 280 cm. assume the indoor design conditions are 25°C DBT and 50 RH, and moisture content of 8 gw/kga. The moisture content of outdoor is 10.5 gw/kga. Calculate heat gain for living room : الشقة في الطابق الأرضي من مبنى ثلاثة طوابق في مدينة بغداد يظهر في مخطط الشقة تفاصيل الجدران والسقف والنوافذ والباب. النافذة عبارة عن زجاج مزدوج وسمك الفراغ الهوائي 1.3 سم ضعيف الاحكام مع ساتر حماية مع إطار خشبي والنافذة بسماكة زجاج 0.6 سم سماكة الباب 2.5 سم. الباب هو تركيب ضعيف هناك شخصان في كل غرفة. ارتفاع الغرفة 280 سم. افترض أن ظروف التصميم الداخلي هي DBT25 و R50 ، ومحتوى الرطوبة 8…arrow_forwardHow do i solve this problem?arrow_forward
- Q4/ A compressor is driven motor by mean of a flat belt of thickness 10 mm and a width of 250 mm. The motor pulley is 300 mm diameter and run at 900 rpm and the compressor pulley is 1500 mm diameter. The shaft center distance is 1.5 m. The angle of contact of the smaller pulley is 220° and on the larger pulley is 270°. The coefficient of friction between the belt and the small pulley is 0.3, and between the belt and the large pulley is 0.25. The maximum allowable belt stress is 2 MPa and the belt density is 970 kg/m³. (a) What is the power capacity of the drive and (b) If the small pulley replaced by V-grooved pulley of diameter 300 mm, grooved angle of 34° and the coefficient of friction between belt and grooved pulley is 0.35. What will be the power capacity in this case, assuming that the diameter of the large pulley remain the same of 1500 mm.arrow_forwardYou are tasked with designing a power drive system to transmit power between a motor and a conveyor belt in a manufacturing facility as illustrated in figure. The design must ensure efficient power transmission, reliability, and safety. Given the following specifications and constraints, design drive system for this application: Specifications: Motor Power: The electric motor provides 10 kW of power at 1,500 RPM. Output Speed: The output shaft should rotate at 150 rpm. Design Decisions: Transmission ratio: Determine the necessary drive ratio for the system. Shaft Diameter: Design the shafts for both the motor and the conveyor end. Material Selection: Choose appropriate materials for the gears, shafts. Bearings: Select suitable rolling element bearings. Constraints: Space Limitation: The available space for the gear drive system is limited to a 1-meter-long section. Attribute 4 of CEP Depth of knowledge required Fundamentals-based, first principles analytical approach…arrow_forward- | العنوان In non-continuous dieless drawing process for copper tube as shown in Fig. (1), take the following data: Do-20mm, to=3mm, D=12mm, ti/to=0.6 and v.-15mm/s. Calculate: (1) area reduction RA, (2) drawing velocity v. Knowing that: ti: final thickness V. Fig. (1) ofthrearrow_forward
arrow_back_ios
SEE MORE QUESTIONS
arrow_forward_ios
Recommended textbooks for you
- Elements Of ElectromagneticsMechanical EngineeringISBN:9780190698614Author:Sadiku, Matthew N. O.Publisher:Oxford University PressMechanics of Materials (10th Edition)Mechanical EngineeringISBN:9780134319650Author:Russell C. HibbelerPublisher:PEARSONThermodynamics: An Engineering ApproachMechanical EngineeringISBN:9781259822674Author:Yunus A. Cengel Dr., Michael A. BolesPublisher:McGraw-Hill Education
- Control Systems EngineeringMechanical EngineeringISBN:9781118170519Author:Norman S. NisePublisher:WILEYMechanics of Materials (MindTap Course List)Mechanical EngineeringISBN:9781337093347Author:Barry J. Goodno, James M. GerePublisher:Cengage LearningEngineering Mechanics: StaticsMechanical EngineeringISBN:9781118807330Author:James L. Meriam, L. G. Kraige, J. N. BoltonPublisher:WILEY
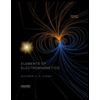
Elements Of Electromagnetics
Mechanical Engineering
ISBN:9780190698614
Author:Sadiku, Matthew N. O.
Publisher:Oxford University Press
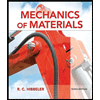
Mechanics of Materials (10th Edition)
Mechanical Engineering
ISBN:9780134319650
Author:Russell C. Hibbeler
Publisher:PEARSON
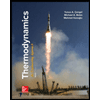
Thermodynamics: An Engineering Approach
Mechanical Engineering
ISBN:9781259822674
Author:Yunus A. Cengel Dr., Michael A. Boles
Publisher:McGraw-Hill Education
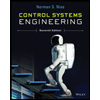
Control Systems Engineering
Mechanical Engineering
ISBN:9781118170519
Author:Norman S. Nise
Publisher:WILEY
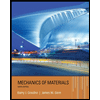
Mechanics of Materials (MindTap Course List)
Mechanical Engineering
ISBN:9781337093347
Author:Barry J. Goodno, James M. Gere
Publisher:Cengage Learning
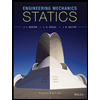
Engineering Mechanics: Statics
Mechanical Engineering
ISBN:9781118807330
Author:James L. Meriam, L. G. Kraige, J. N. Bolton
Publisher:WILEY
Types of Manufacturing Process | Manufacturing Processes; Author: Magic Marks;https://www.youtube.com/watch?v=koULXptaBTs;License: Standard Youtube License