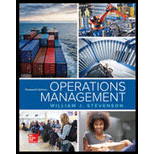
MORTON SALT
Introduction
Morton Salt is a subsidiary of Morton International, a manufacturer of specialty chemicals, air bags, and salt products. The Morton salt-processing facility in Silver Springs, New York, between Buffalo and Rochester, is one of six similar Morton salt-processing facilities in the United States. The Silver Springs plant employs about 200 people, ranging from unskilled to skilled. It produces salt products for water conditioning, grocery, industrial, and agricultural markets. The grocery business consists of 26-oz. round cans of iodized salt. Although the grocery business represents a relatively small portion of the total output (approximately 15 percent), it is the most profitable.
Salt production
The basic raw material, salt, is obtained by injecting water into salt caverns that are located some 2,400 feet below the surface. There, the salt deposits dissolve in the water. The resulting brine is pumped to the surface where it is converted into salt crystals. The brine is boiled, and much of the liquid evaporates, leaving salt crystals and some residual moisture, which is removed in a drying process. This process is run continuously for about six weeks at a time. Initially, salt is produced at the rate of 45 tons per hour. But the rate of output decreases due to scale buildup, so that by the sixth week, output is only 75 percent of the initial rate. At that point, the process is halted to perform maintenance on the equipment and remove the scale, after which salt production resumes.
The salt is stored in silos until it is needed for production, or it is needed for production, or it is shipped in bulk to industrial customers. Conveyors move the salt to each of the four dedicated production areas, one of which is round can production (see diagram.). The discussion here focuses exclusively on round can production.
Round Can Production
Annual round can production averages roughly 3.8 million cans. Approximately 70 percent of the output is for the Morton label, and the rest is for private label. There are two parallel, high-speed production lines. The lines share common processes at the beginning of the lines, and then branch out into two identical lines. Each line is capable of producing 9,600 cans per hour (160 cans per minute). The equipment is not flexible, so the production rate is fixed. The operations are completely standardized; the only variable is the brand label that is applied. One line requires 12 production workers, while both lines together can be operated by 18 workers because of the common processes. Workers on the line perform low-skilled, repetitive tasks.
The plant produces both the salt and the cans the salt is packaged in. The cans are essentially a cylinder with a top and a bottom; they are made of cardboard, except for a plastic pour spout in the top. The cylinder portion is formed from two sheets of chip board that are glued together and then rolled into a continuous tube. The glue not only binds the material, it also provides a moisture barrier. The tube is cut in a two-step process. It is first cut into long sections, and those sections are then cut into can-size pieces. The top and bottom pieces for the cans are punched from a continuous strip of cardboard. The separate pieces move along conveyor belts to the lines where the components are assembled into cans and glued. The cans are then filled with salt and the pour spout is added. Finally, the cans are loaded onto pallets and placed into inventory, ready to be shipped to distributors.
Quality
Quality is checked at several points in the production process. Initially, the salt is checked for purity when it is obtained from the wells, Iodine and an anti-caking compound are added to the salt, and their levels are verified using chemical analysis. Crystal size is important. In order to achieve the desired size and to remove lumps, the salt is forced through a scraping screen, which can cause very fine pieces of metal to mix with the salt. However, these pieces are effectively removed by magnets that are placed at appropriate points in the process. If, for any reason, the salt is judged to be contaminated, it is diverted to a nonfood product.
Checking the quality of the cans is done primarily by visual inspection, including verifying the assembly operation is correct, checking filed cans for correct weight, inspecting cans to see that labels are labels are properly aligned, and checking to see that plastic pour spouts are correctly attached.
The equipment on the production line is sensitive to misshapen or damaged cans, and frequently jams, cussing production delays. This greatly reduces the chance of a defective can getting through the process, but it reduces productivity, and the salt in the defective cans must be scrapped. The cost of quality is fairly high, owing to the amount of product that is scrapped, the large number of inspectors, and the extensive laboratory testing that is needed.
Production Planning and Inventory
The plant can sell all of the salt it produces. The job of the production
Equipment Maintenance and Repair
The equipment is 1950s vintage, and it requires a fair amount of maintenance to keep it in good working order. Even so, breakdowns occur as parts wear out. The plant has its own tool shop where skilled workers repair parts or make new parts because replacement parts are no longer available for the old equipment.
1. Briefly describe salt production, from brine production to finished round cans.

Want to see the full answer?
Check out a sample textbook solution
Chapter 6 Solutions
Operations Management
Additional Business Textbook Solutions
Accounting Information Systems (14th Edition)
Operations Management: Processes and Supply Chains (12th Edition) (What's New in Operations Management)
Financial Accounting, Student Value Edition (5th Edition)
Advanced Financial Accounting
Principles of Operations Management: Sustainability and Supply Chain Management (10th Edition)
Horngren's Cost Accounting: A Managerial Emphasis (16th Edition)
- In the 2016, "ATB: digital disruption in the parking meter industry" perform a finanacial analysis and make a chart similar to this one 2013 2014 Current Ratio 1.88 1.41 Quick Ratio 0.49 0.29 Debt to Equity 0.95 1.92 Return on Assets 5.47% 2.76% Net Profit Margin 2.71% 1.89%arrow_forwardPerform a VRIO Analysis on the 2016 "ATB: Digital disruption in the parking meter industry" and make a chart similar to this one V R I O Topic Y Y Y Y Relations with John Deere and Paccar Y N N Y Customer Relations Y Y Y Y Acquisition and Integration Process Y Y Y N Cervus Leadership University Y Y N Y Proactive Management Y Y N Y Financial Position Y N N N Scale of Organizationarrow_forwardHow do incorporated stress management techniques impact future emotional strength and wellness? What are the lesson learned from incorporating stress management techniques in the past that reflects developing emotional resilience?arrow_forward
- Purchasing and Supply Chain ManagementOperations ManagementISBN:9781285869681Author:Robert M. Monczka, Robert B. Handfield, Larry C. Giunipero, James L. PattersonPublisher:Cengage LearningPractical Management ScienceOperations ManagementISBN:9781337406659Author:WINSTON, Wayne L.Publisher:Cengage,
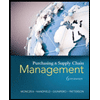
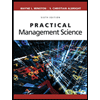