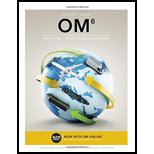
OM (with OM Online, 1 term (6 months) Printed Access Card)
6th Edition
ISBN: 9781305664791
Author: David Alan Collier, James R. Evans
Publisher: Cengage Learning
expand_more
expand_more
format_list_bulleted
Concept explainers
Question
Chapter 5, Problem 3PA
Summary Introduction
Interpretation: Value of k and economic loss.
Concept Introduction:
Reliability is the probability of a product which performs under designed and controlled atmosphere in a given period of time. This is checked to know the accuracy of the product.
Expert Solution & Answer

Want to see the full answer?
Check out a sample textbook solution
Students have asked these similar questions
her psychological test and interview while Ms. Domingo got a good score and good psychological result. Ms. Sabado’s father is your godfather and a good friend of yours. Ms. Sabado asked you a favor to consider her daughter and if possible she will be hired. He also added that every job can be learned through training and mentoring. The situation bothers you since it’s your duty to recommend to the higher authority whom to hire.Questions:1. As a supervisor how will you diced on this situation?2. It’s time to decide, who among the two (2) will be hired? Why?
Help me solve part C.
Boreki Enterprise has the following 10 items in inventory. Theodore Boreki asks you, a recent OM graduate, to divide these items into ABC classifications. Fill in the blanks and then answer the
following questions. (Round dollar volume to the nearest whole number and percentage of dollar volume to two decimal places.)
Dollar
Item
Annual Demand Cost/Unit
Volume
% of Total Dollar
Volume
A2
10
120
B8
4000
12
48,000
5.65
C7
1500
45
67,500
7.94
D1
2000
44
E9
1000
20
20,000
2.35
F3
25
40
G2
200
1500
300,000
35.29
H2
600
20
12,000
1.41
15
1000
300
J8
2500
5
12,500
1.47
Chapter 5 Solutions
OM (with OM Online, 1 term (6 months) Printed Access Card)
Knowledge Booster
Learn more about
Need a deep-dive on the concept behind this application? Look no further. Learn more about this topic, operations-management and related others by exploring similar questions and additional content below.Similar questions
- Bobby Flay is responsible for assigning steel workers to a structural steel infrastructure construction task. Having taken Project Management at the University of Portland, he understands the importance of managing risk. To ensure that the task takes place as scheduled, Bobby must ensure that there are at least 8 steel workers available at the start of the task. Based on analysis of similar tasks, he estimates that steel workers will show up for the task with probability 0.9. If Bobby wants to be 97% sure that there are enough tasks to begin as scheduled, he should assign ______ steel workers to the task.arrow_forwardMarcela Valladolid needs to assign resources to a task on a new high-tech development project at Jonathon's Pool Supplies. According to her estimates, the task's work content (in hours) is 408. Marcela needs help in determining an appropriate number of resources to allocate to the task. Marcela read somewhere that, when it comes to project staffing, more is not always better. Assuming that the direct labor rate per hour is $93, the indirect and over head rate per unit time is $73.62, assigned resources are dedicated to the task full time, and that 0.02 hours of communication per coordination are required per link per hour worked, help Marcela by determining the following: What is the minimum total cost: What resource allocation minimizes the total cost: What is the minimum duration: What is the duration minimizing number of resources: If Marcela assigns 12 FTEs to the task, the task metrics would be: Total Cost: Total Duration: Note: enter durations to 1 decimal place and costs…arrow_forward1 point) Market Fresh Foods is looking to develop a new strategic plan. Guillermo Santiago has been developing a project plan and has identified the following tasks, precedence relations, normal task durations, and resource requirements. Guillermo has studied project management at the University of Portland and knows that the makespan of the project may be determined from the information in the table using the critical path method. Guillermo also learned a simple heuristic for evaluating resource sufficiency. Help Guillermo by answering the following related assuming 3 workers per week and a due date of 302.8: Project Work Content: Total Resource Capacity: Minimum due date for which 3 resources is sufficient: Minimum resource level that could make due date of 302.8 feasible:arrow_forward
- How an individual attending a university can help the development of a country?arrow_forwardWhat are the job description or role in Operations management? Please answer at your own easy words.arrow_forwardI am currently working as a Sub Assistant Manager at Advance Personal Care Limited (APCL), a concern of Pran Group. I hold a Bachelor of Pharmacy (Professional) degree. I recently came across a job posting on BD Jobs for a position in Project Management within Quality Operations. I want to apply for this role and need to update my CV accordingly. Could you please guide me on what key information, achievements, and skills I should add or highlight in my CV to align with this new role? Note that i have 8 months experience on this role. Please write at your own easy words. Please don't use Ai answering this question. I will rate you positive if you do so.arrow_forward
- I am currently working as a Sub Assistant Manager at Advance Personal Care Limited (APCL), a concern of Pran Group. I hold a Bachelor of Pharmacy (Professional) degree. I recently came across a job posting on BD Jobs for a position in Project Management within Quality Operations. I want to apply for this role and need to update my CV accordingly. Could you please guide me on what key information, achievements, and skills I should add or highlight in my CV to align with this new role? Note that i have 8 months experience on this role. Please don't use Ai answering this question. I will rate you positive if you do so.arrow_forwardWhat are the three main concepts of understanding in Operations Management?arrow_forwardNeed help please not sure where to start or how to write it.arrow_forward
- Need help please not sure where to start or how to write it.arrow_forwardSIPOC Process Supplier Machines Quality Group Leader Double Output Customers Inputs Solutions End of batch Inspection verification Scrap evaluation Sampling Verification Batch complete Evaluation Completed Quality Group Leader Samplings verified Quality Samplings verified Quality Barcode programed Mechanic Parameters registered Quality Line verified Quality Line Verified Quality Second verification Barcode Parameters Line Inspection Second Line Inspection Lot and Expiration Date Quality Quality Mechanic Mechanic Quality Machines Quality Group Leader Quality Quality Quality Batch Verification Process complete Revision Review Sampling Verification Barcode Scanner Machine Parameters Line Clearance Line Clearance Machine Remove Lot Status Verification Close floor Final MFG Review Final QA Review Close Batch Machine removed Lot verified Floor closed MFG Reviewed Process reviewed Batch closed Mechanic Group Leader Quality Quality Quality Group Leaderarrow_forwardAn assessment of gender leadership and corporate culture.Kindly provide the following, citing it using in-text referencing: • A thorough exploration of gender dynamics and concepts.• Creating a clear plan to address gender bias and promote inclusive leadership.• An examination of female leadership dynamics and their impact on performance. • Comprehensive justification behind the proposal.arrow_forward
arrow_back_ios
SEE MORE QUESTIONS
arrow_forward_ios
Recommended textbooks for you
- Management, Loose-Leaf VersionManagementISBN:9781305969308Author:Richard L. DaftPublisher:South-Western College PubPractical Management ScienceOperations ManagementISBN:9781337406659Author:WINSTON, Wayne L.Publisher:Cengage,
- MarketingMarketingISBN:9780357033791Author:Pride, William MPublisher:South Western Educational Publishing
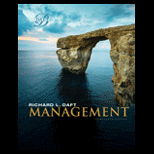
Management, Loose-Leaf Version
Management
ISBN:9781305969308
Author:Richard L. Daft
Publisher:South-Western College Pub
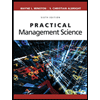
Practical Management Science
Operations Management
ISBN:9781337406659
Author:WINSTON, Wayne L.
Publisher:Cengage,
Marketing
Marketing
ISBN:9780357033791
Author:Pride, William M
Publisher:South Western Educational Publishing