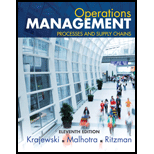
Concept explainers
a
Interpretation: Quarterly production rate which minimize the anticipatory inventory is to be determined.
Concept Introduction:
Anticipatory production is the stock kept by firms to meet uncertain demand or any increase in price of inputs or any uncertain situation.
b
Interpretation: The Anticipatory gallons that will be produced are to be specified.
Introduction:
Anticipatory production is the stock kept by firms to meet uncertain demand or any increase in price of inputs or any uncertain situation.
c
Interpretation: Level of production rate required is to be determined.
Introduction:
Anticipatory production is the stock kept by firms to meet uncertain demand or any increase in price of inputs or any uncertain situation.

Want to see the full answer?
Check out a sample textbook solution
Chapter 10 Solutions
Operations Management: Processes and Supply Chains (11th Edition)
- Communication Tips (2015) Tactful bragging Respond to the question "So, what do you do?" Whether you are student or have a job/internship, how can you tactfully brag in your answer to this question? Use the three elements from the video (listed below) when crafting your brag statement: Focus on results vs title Process vs job description Loop back to listener Example of an instructor's brag statement: "I help hundreds of students each semester to connect with one another, develop communication skills and prepare for upcoming interviews. Through improv games we explore presence, flexibility, and storytelling. How have your networking experiences on campus been so far?"arrow_forwardAccounting problemarrow_forwardGovernment's new plan to shift cargo from roads back to rail 26TH JANUARY 2024 Government is seeking to finalise a plan aimed at improving its rail network and move cargo away from a billion rand per day to its logistics crises, government has said an urgentturnaround is needed to improve its 31 000km locomotive network as more and more cargo moves from rail to trucks. The Department of Transport (DoT) hosted a discussion with industry stakeholders regarding the Freight Road to Rail Migration Plan on Thursday - the latest development in the wake of President Cyril Ramphosa forming the National Logistics Crisis Committee last year. Transnet, the South African National Roads Agency (Sanral) and private sector companies were all in attendance. The Freight Road to Rail Migration Plan is part of government's strategies to improve the country's ongoing logistics crises. In October last year, the government unveiled its Freight Logistics Roadmap to improve the ports and rail networks and…arrow_forward
- Assess what led to such logistical inefficiencies / collapse of a previously world class freight networkarrow_forwardWhich of the following statements concerning the evaluation of training programs is true? Most companies thoroughly evaluate the return on investment of their training programs It is relatively easy to establish a control group and a treatment group for evaluation Results level of evaluation measures how well participants liked the program Behavior level criteria measure whether skills learned in training result in behavior changes back on the jobarrow_forwardEligibility testing is an disparate impact validation method none of the above a method to validate promotions and progressive discipline activity a test an employee administers to ensure that the potential employee is capable and qualified to perform the requirements of the positionarrow_forward
- A no-strike pledge by a union in a collective bargaining agreement is given in return for management’s agreement to: a grievance procedure a union shop a wage increase a fringe benefit increase binding arbitration of grievancesarrow_forwardWhich is the major OD technique that is used for increasing the communication, cooperation, and cohesiveness of work units? Leadership analysis Developing objectives Groupthink Strategic Planning team Buildingarrow_forwardAn American multinational firm usually is less than fully successful in adapting itself to local practices in each country because: American managers are often ignorant of local conditions None of the above management direction may be centralized in the home office All of the above Foreign subsidiaries often have American managersarrow_forward
- When salary increases are based on inputs, or performance, companies are following: agency theory equality theory equity theory compliance theory need theoryarrow_forwardThe most frequently used techniques for measuring job satisfaction involves Direct observation Questionnaires Interviews Psychological testsarrow_forwardWhich of the following is not an advantage of on-the-job training? Transfer is less difficult Transfer is less difficult The training is inexpensive Any organizational member can be the trainer without preparation It is relatively easy to use this methodarrow_forward
- Practical Management ScienceOperations ManagementISBN:9781337406659Author:WINSTON, Wayne L.Publisher:Cengage,MarketingMarketingISBN:9780357033791Author:Pride, William MPublisher:South Western Educational PublishingPurchasing and Supply Chain ManagementOperations ManagementISBN:9781285869681Author:Robert M. Monczka, Robert B. Handfield, Larry C. Giunipero, James L. PattersonPublisher:Cengage Learning
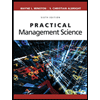
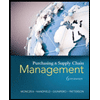