Lean Six Sigma in Case Studies
docx
keyboard_arrow_up
School
Strayer University *
*We aren’t endorsed by this school
Course
2105
Subject
Management
Date
Nov 24, 2024
Type
docx
Pages
13
Uploaded by vcnkemb97
1
Lean Six Sigma in Case Studies
Student’s Name
Course Name
Instructor
Date
Author’s Note
By submitting this assignment, I attest this submission represents my own work, and not that of
another student, scholar, or internet source. I understand I am responsible for knowing and
correctly utilizing referencing and bibliographical guidelines. I have not submitted this work for
any other class.
2
Abstract
The present study aims to comprehensively define and examine Lean Six Sigma and its role in
contemporary business operations. The present study identifies the dual benefits of integrating
Lean Six Sigma methodologies. The author elucidates the underlying principles of each
technique, enabling readers to comprehend the distinctiveness of implementing said practice
within their respective organizations. The DMAIC model and its constituent phases are
explicated comprehensively to demonstrate a systematic approach to resolving obstacles.
Keywords: Lean Six Sigma, lean thinking, six Sigma, DMAIC, value mapping
3
Introduction
Businesses are always looking for new ways to increase productivity and revenue. Lean
Six Sigma provides a structured method with a proven track record of success (Hall & Scott,
2016). Lean Six Sigma offers a new point of view for businesses that want to streamline their
operations, cut down on waste, and maintain an advantage in a crowded industry.
Defining Lean Six Sigma
The combination of Lean and Six Sigma methodologies, both aimed at enhancing the
efficiency and efficacy of an organization’s operations, resulted in the creation of Lean Six
Sigma, which facilitates revenue generation and expansion. Lean Six Sigma provides a
systematic method for finding, fixing, and verifying the effectiveness of organizational
improvements. Implementing Lean Six Sigma helps businesses deal with difficulties in the
current economic climate. Its implementation is a component of the never-ending process of
improvement that gives and maintains a company’s competitive advantage (Costa et al., 2018).
The first component is lean thinking, a technique that emphasizes speeding up internal
processes and enhancing manufacturing efficiency (Hall & Scott, 2016). Users that use lean
search strategies contribute value by eliminating needless activities, resources, and costs
(Chugani et al., 2017). Those who practice lean thinking are strategically realigned to function
methodically, aiming to optimize value and minimize extra expenses. According to Costa et al.
(2018), the method was developed by Toyota during a period of economic recession in Japan,
wherein the company was compelled to produce goods in limited quantities for a market that had
come to a standstill.
Your preview ends here
Eager to read complete document? Join bartleby learn and gain access to the full version
- Access to all documents
- Unlimited textbook solutions
- 24/7 expert homework help
4
Six Sigma is a methodology that aims to enhance the quality of a business process (Hall
and Scott, 2016). Motorola faced competition from a Japanese enterprise that employed a Lean-
based approach. Motorola looked for ways to increase productivity and better serve its customers
at a reasonable price (Nierola et al., 2021). Implementing the Six Sigma methodology in an
organization’s process aims to minimize the occurrence of unpredictability, thereby enhancing
the likelihood of success in the market. The Six Sigma process is characterized by a systematic,
purpose-driven approach to eliminate recurring errors and potential obstacles. The steps involved
in this process are designed to be logically structured and driven by a clear sense of purpose.
Benefits of Lean Six Sigma
Lean Six Sigma provides a powerful tool for solving business problems when used as an
entire system. There are three main areas where benefits may be summed up: more satisfied
clients, a more productive workplace, and a culture of constant development (Munteanu, 2017).
The Lean Six Sigma methodology incorporates an understanding of human fallibility. It merges
it with a data-driven approach to decision-making while also allowing for adaptability in
response to changing circumstances. All individuals participating in the economy can utilize the
aforementioned methodological tools and strategies. Lean Six Sigma may be easily implemented
to reduce inefficiencies, speed up processes, boost output, save costs, and provide businesses an
advantage in the market (Munteanu, 2017).
Principles of Lean Thinking & Lean Six Sigma
The five principles of lean thinking are the cornerstone for making long-term changes
that boost a company’s worth. Adherence to these standards will increase output and enhance
service quality. The best approach to gathering data for each principle will vary greatly across
5
various organizations. Lean thinking is used to evaluate all stakeholders, both internal and
external.
Current Value
Leaders ask customers what they think their product or service is valuable. The value of
an organization is reliant upon its ability to cater to the preferences and aversions of its
consumers, thus underscoring the importance of discerning their inclinations. According to
Almutairi et al. (2020), medical facilities must provide high-quality care and quick turnaround
times to satisfy patients’ needs. Similarly, after a course, students provide teachers and the
institution with valuable insight and insight into the viewpoint of students. Clarifying the
advantages and disadvantages of an organization’s overall value is a crucial initial measure in
applying lean thinking.
Value Mapping
The process of mapping value stream displays involves identifying the specific locations
and timings of actions that contribute to the overall value of a given system. Leadership involves
establishing a set of desired values and modifying the course of action by selectively
incorporating or eliminating activities to achieve the desired outcome. The abovementioned
principle necessitates a thorough analysis of the present operations and comprehensive
documentation. It may require considerable time to depict the value stream accurately. It is
advisable to start with a basic description of the activity and then add substages as leaders dig
further into its relevance to value (Sommer & Blumenthal, 2019).
Creating Flow
6
In the past, extra processes were eliminated from the value chain. There can be no
breakdowns in the new value stream’s progress (Almutairi et al., 2020). At this stage, further
waste-generating actions may be identified. Wasteful activities, known in Japan as Muda, include
unnecessary repetition, excessive waiting, and extra precautions taken beyond what is necessary
to deal with errors and accidents (Sommer & Blumenthal, 2019). While tools like process
mapping and flow testing may be helpful, they won’t catch every inefficient action. Instead,
engaging with workers and soliciting their input can provide valuable insights that can be used to
refine lean practices.
Testing the Value & Repeating it
Once the final flow has been determined, a second round of value assessments with
customers is warranted. A product or service is not created until there is a demand for it, a
concept known as “letting the consumers pull” (Almutairi et al., 2020). Companies don’t force
their new flow on customers. Instead, the value obtained must be measured when customers
make a demand. The 5S methodology (sort, put in order, shine, standardize, and sustain) may
help businesses consistently identify the stages that can be removed to save time and resources
(Sommer & Blumenthal, 2019). Organizing tasks according to their frequency highlights the
crucial processes that must be maintained, stabilizing the flow in a logical sequence that
customers may access at their convenience. Bring into focus the procedures and their specifics
that are necessary yet unproven. The whole team has to get on board with the new and enhanced
processes that have been put in place. Finally, maintain the current pace and periodically assess
its effectiveness to see where improvements may be made.
7 Principles of Lean Six Sigma
Your preview ends here
Eager to read complete document? Join bartleby learn and gain access to the full version
- Access to all documents
- Unlimited textbook solutions
- 24/7 expert homework help
7
Customer-centric
Organizations only survive as long as their product or service is in demand. Failed
businesses put external validation of their performance and product quality ahead of their
internal performance evaluation. Employees in today’s businesses are taught that satisfying
consumers is crucial (Hall & Scott, 2016). Lean Six Sigma is geared toward retaining and
attracting customers by concentrating on their wants, needs, and desires. Customers often
experience issues such as finding extra tasks, mistakes, process delays, and lengthy wait times
(Hall & Scott, 2016). It’s important to hear the opinions of both internal and external customers.
Customers’ feedback may be gathered via various channels (surveys, customer reviews, a legally
compliant database, etc.) (Hall & Scott, 2016).
The Value Stream, Flow, & Waste Elimination
Lean Six Sigma combines lean thinking by analyzing a company’s value stream, process
flow, and waste reduction potential. The efforts of these businesses directly result in products and
services for customers. Performing a value stream analysis and optimizing it to the value that
executives want to see from customers is the first step in reducing unnecessary expenditures.
Each step along the value stream should be completely transparent to the customer and
contribute value to the final product. Reviewing the stream periodically is necessary to keep a
competitive edge in the market.
Data Collection
Before implementing modifications to an organization’s procedures, it is imperative to
possess empirical evidence demonstrating the existing challenges and facilitating their resolution
(Hall & Scott, 2016). It is imperative to uphold the integrity and accuracy of collections
8
comprising reports and metrics that effectively depict the organization’s status. Following the
implementation of modifications, it is recommended that leaders maintain a reference report to
facilitate comparisons between the current and intended activities, thereby enabling further
evaluations. The extent of deviation from the intended outcome will ascertain the necessity and
timing of taking appropriate measures.
Employee Readiness
Understanding the human capital and resources inside the company is crucial to its
success. The steps of a business process cannot be completed without first gaining the
appropriate training and experience. As the market evolves, equipping employees with the
knowledge and abilities they’ll need to do their jobs well becomes more important. Employee
engagement is essential to maintain employee autonomy and motivation for organizational
progress.
Systematic Improvements
It’s unlikely that a company will continue if its operations become perfectly efficient.
Competition from new entrants, technological advancements, and unforeseen difficulties. Lean
Six Sigma recommends that businesses regularly do process evaluations to assess their current
operations and identify improvement areas. Lean Six Sigma includes frameworks that detail how
to deal with both new and current issues that arise in businesses (Hall & Scott, 2016).
DMAIC: The Problem-Solving Process
The DMAIC model of Lean Six Sigma comprises five stages: define, measure, analyze,
improve, and control. The model comprises distinct phases complemented by various tools and
techniques to facilitate optimal critical processes (Uluskan & Oda, 2020). The DMAIC model
9
has demonstrated a sound rationale by systematically examining each step. According to George
et al. (2005), it is not advisable to overlook or bypass stages to expedite the problem-solving
process, as individuals tend to have a propensity for expeditious solutions.
The basic principles of Lean Six Sigma place significant emphasis on the necessity of
possessing empirical evidence to substantiate the existence of a given issue. According to the
DMAIC framework, leaders must identify the issue and confirm that it is urgent and potentially
harmful if left unchecked (Hall and Scott, 2016). The statement above shall delineate the
requisite resources, stipulated timeframe, and constituent elements of a prosperous outcome
while maintaining reasonable expectations.
In the measure phase, the issue is quantified to give decision-makers a picture of the
existing state. This gives you something to work with, a starting point to alter things (Hall &
Scott, 2016). A trustworthy data recording and analysis system is essential for producing realistic
forecasts. At the end of the measure phase, you should have a mapped value stream, customer-
and project-related variable data, and a strategy for gathering missing data (George et al., 2005).
Leaders should look for the root causes of inefficiencies in the analysis phase (Hall &
Scott, 2016Leaders should start with the value stream to emphasize wasteful processes and those
that provide value to the product for consumers. They may be compared to preexisting standards
to ensure processes run efficiently (Hall & Scott, 2016). In this step, you’ll review the data you
gathered in the prior one and try to fill in any blanks.
Multiple potential approaches toward implementation are evaluated, and the optimal one
is ultimately selected. After collecting and evaluating pertinent information, a resolution can be
devised during the enhancement process. The chosen solution outcomes in this stage are
Your preview ends here
Eager to read complete document? Join bartleby learn and gain access to the full version
- Access to all documents
- Unlimited textbook solutions
- 24/7 expert homework help
10
monitored and compared to the reference or baseline established during the measurement phase
(Hall & Scott, 2016). When the outcomes of the enhancement stage show promise, we enter the
control phase. Results from the new methods should be kept. Consequential impacts in any
section of the organization may be monitored by inspections and obtaining measurements.
Application of Lean Six Sigma
Employing all available study techniques. The Lean Six Sigma methodology integrates
research approaches, including qualitative, quantitative, and mixed methods, to conduct case
study analysis and implement contemporary business strategies. The methodology involves
employing multiple strategies until a satisfactory outcome is achieved. Conducting a singular
type of study may result in an incomplete understanding of the phenomenon under investigation,
thereby precluding the possibility of uncovering potential solutions. To comprehensively
understand their position, individuals must gather and analyze quantitative and qualitative data.
The Lean Six Sigma methodology was formulated to incorporate a comprehensive spectrum of
cognitive faculties exhibited by human beings. Comprehending each pivotal stage entails delving
into all avenues of inquiry, and the procedure is contingent upon the user’s willingness to be
receptive to such an approach.
Conclusion
Combining the principles of lean thinking and the six sigma methods results in the Lean
Six Sigma approach. The objective is to optimize the efficiency of the organization’s activities to
enhance profitability and facilitate expansion. These approaches’ amalgamation capitalizes on
their strengths to broaden the scope of possibilities and avenues for resolving issues.
The critical
thinking incorporates tools and techniques informed by Lean thinking and Lean Six Sigma
11
principles. The DMAIC model serves as the primary framework utilized in the Lean Six Sigma
approach, enabling the identification and selection of an appropriate solution for organizational
challenges. Leaders of all backgrounds can comprehend the Lean Six Sigma methodology, as it
equips them with the necessary tools to comprehend their organization and identify optimal
solutions for enhancing their market position.
12
References
Almutairi, A. M., Salonitis, K., & Al-Ashaab, A. (2020). A framework for implementing lean
principles in the supply chain management at health-care organizations: Saudi’s
perspective.
International Journal of Lean Six Sigma
, 11(3), 463-492.
http://dx.doi.org/10.1108/IJLSS-01-2019-0002
Chugani, N., Kumar, V., Garza-Reyes, J. A., Rocha-Lona, L., & Upadhyay, A. (2017).
Investigating the green impact of lean, six Sigma, and lean six Sigma: A systematic
literature review.
International Journal of Lean Six Sigma
, 8(1), 7-32.
https://doi.org/10.1108/IJLSS-11-2015-0043
Costa, L. B. M., Godinho Filho, M., Fredendall, L. D., & Gómez Paredes, F. J. (2018). Lean, six
sigma and lean six sigma in the Food Industry: A systematic literature review.
Trends in
Food Science & Technology
, 82, 122-133.
https://doi.org/10.1016/j.tifs.2018.10.002
Hall, J. & Scott, T. (2016).
Lean Six Sigma: A Beginners Guide to Understanding and Practicing
Lean Six Sigma
. Columbia, SC: CreateSpace Receiving.
Munteanu, A. M. C. (2017). Comparative analysis between lean, six Sigma, and lean six sigma
concepts. Management and Economics Review, 2(1), 78-89.
Niñerola, A., Sánchez-Rebull, M., & Hernández-Lara, A. (2021). Six Sigma literature: A
bibliometric analysis.
Total Quality Management & Business Excellence
, 32(9-10), 959-
980.
https://doi.org/10.1080/14783363.2019.1652091
Your preview ends here
Eager to read complete document? Join bartleby learn and gain access to the full version
- Access to all documents
- Unlimited textbook solutions
- 24/7 expert homework help
13
Sommer, A. C., & Blumenthal, E. Z. (2019). Implementation of lean and six sigma principles in
ophthalmology for improving quality of care and patient flow.
Survey of Ophthalmology
,
64(5), 720-728. https://doi.org/10.1016/j.survophthal.2019.03.007
Uluskan, M., & Oda, E. P. (2020). A thorough six sigma DMAIC application for household
appliance manufacturing systems: Oven door-panel alignment case.
TQM Journal
, 32(6),
1683-1714. https://doi.org/10.1108/TQM-06-2019-0171
Recommended textbooks for you
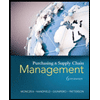
Purchasing and Supply Chain Management
Operations Management
ISBN:9781285869681
Author:Robert M. Monczka, Robert B. Handfield, Larry C. Giunipero, James L. Patterson
Publisher:Cengage Learning
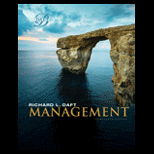
Management, Loose-Leaf Version
Management
ISBN:9781305969308
Author:Richard L. Daft
Publisher:South-Western College Pub
Recommended textbooks for you
- Purchasing and Supply Chain ManagementOperations ManagementISBN:9781285869681Author:Robert M. Monczka, Robert B. Handfield, Larry C. Giunipero, James L. PattersonPublisher:Cengage LearningManagement, Loose-Leaf VersionManagementISBN:9781305969308Author:Richard L. DaftPublisher:South-Western College Pub
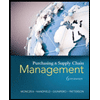
Purchasing and Supply Chain Management
Operations Management
ISBN:9781285869681
Author:Robert M. Monczka, Robert B. Handfield, Larry C. Giunipero, James L. Patterson
Publisher:Cengage Learning
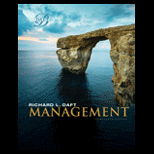
Management, Loose-Leaf Version
Management
ISBN:9781305969308
Author:Richard L. Daft
Publisher:South-Western College Pub