MENG_3331-Fatigue_Lab-group_report_Resubmission
docx
keyboard_arrow_up
School
Georgia Southern University *
*We aren’t endorsed by this school
Course
3331
Subject
Mechanical Engineering
Date
Feb 20, 2024
Type
docx
Pages
4
Uploaded by ProfessorLightningPartridge33
MENG 3331 Materials Science
Department of Mechanical Engineering
Sept. 27, 2023, Statesboro, Georgia, USA
Technical Report 5
FATIGUE LAB
Bryce Cone
Georgia Southern University
Sparks, GA, United States
Dylan Butler
Georgia Southern University
Albany, GA, United States
Scott Rhodes
Georgia Southern University Warner Robins, GA, United
States
Lawrence Almeter
Georgia Southern University
Dearing, GA, United States
A
BSTRACT
Fatigue testing is a test conducted to study how a material
reacts to weight being added to the end of it while being rotated
at a high rpm (rotations per minute). In the following lab four
samples of materials are tested and studied how they react.
Each of the materials had a channel, or groove milled in the
center. This allows the test to be conducted more accurately and
more controlled. Each one of the materials had a different
weight applied to the end of the rod. It is discovered that as
more weight was added to the rod, the less amount of lifetime
rotations would be made. The amount of weight applied to the
bars started at 50 in-lbs and went up in increments of 15 in-lbs,
thus making the weights used 50 in-lbs, 65 in-lbs, 80 in-lbs, and
95 in-lbs. After taking note of observations and results, the
stress acted upon the material can then be calculated.
N
OMENCLATURE
d
Diameter, inches or meters
in-lb Bending Moment, inch-pound
Nm
Bending Moment, Newton Meter
M
Moment (Bending Torque), in-lb or N*m
Pa
Pascal, N/m^2
σ
Stress, Pascal
INTRODUCTION
In this lab Fatigue testing will be conducted to determine
the maximum stress leading to failure. The Origins of this test
can be traced back to the first documented cases of metal
fatigue failures in 1838 documented by Wilhelm Albert. By the
1850’s fatigue testing was a standard practice for companies
attempting to correct fatigue cracks in horse drawn carriages
and railroad car axles [1]. August Wöhler, another German
scientist conducted a 20-year load cycles to failure test which
led to his popularization of the S-N Curve which is a plot of the
Stress versus the number of life cycles in logarithmic scale [1].
The primary uses of fatigue testing today are to generate data
on crack propagation, identify critical locations of samples, and
demonstrate safety of certain designs. Cyclic loading causes the
sample’s surface to go through very fast changes of tension and
compression with varying loads allowing for the observation of
failure. MaximumStress
=
σ
=
32
M
π d
3
=
Pa
Standard Deviation
=
σ
=
¿
1
∈
– lb
=
0.11298482933333
Newton meters
1
inches
=
0.0254
meters
(1)
(2)
(3)
(4)
EXPERIMENTAL METHODS
The fatigue test will begin with selecting 4 metal samples
that have been machined specifically for the test. Use a caliber
to first measure the middle diameter to obtain the radius for
each sample. Once measured, slide each end of the sample into
1
Copyright © 2023 by ASME
the fittings and secure the threaded ends of the fittings to the
machine using the two wrenches. Secure the back end of the
fitting by sliding the arm to the bolt to make sure the sample
does not break instantly. Once the sample is connected to the
fatigue testing machine the inch pound scale will need to be
adjusted. For the first sample an inch poundage of 50 will be
used. Now that the sample is secured, and the inch poundage is
set it will be time to turn it on. Flip the switch and slowly adjust
the rpms until it reaches ~4000. Once 4000 rpms have been
reached turn the wheel on the life cycle until all digits reach
zero. As soon as they reach 0 release the arm from the back
fitting to allow the sample to now be undergoing the test. Wait
until the sample has broken, record the number of life cycles it
endured and remove the now broken sample from the fittings.
This process will be repeated 4 times in total with the only
change being a 15 inch-pound increase on each sample starting
with the 50 inch-pound sample. DATA AND
R
ESULTS
Table 1 is a summary of the experimental data gathered
during testing. There were four samples each under an applied
bending moment of increasing magnitude. The measured radius
was extremely consistent between the four samples which will
help keep the rest of the data consistent as well. The number of
life cycles that the samples survived were as expected. The
samples under less load had a much longer lifetime while the
samples under heavy load had an extremely short lifetime.
Table 2 shows the conversion of Table 1 into SI Units from
English Units using Equation 3 and 4. It also shows the stress
amplitude which was calculated using Equation 1. Figure 1 is a
graphical representation of the stress amplitude versus the
number of life- cycles the sample was able to reach. This
Stress-Life curve visibly shows how the lifetime of the sample
improved when under less stress. Table 1.
Collected Experimental Data
Sample ID
Bending Torque
[in-lb]
Min Radius
[in]
Life Cycles x100
1
50
0.1355
320
2
65
0.1355
40
3
80
0.1355
32
4
95
0.1355
12
Table 2.
Conversion of Table 1 to SI Units for
Experiment Results
Sample
ID
Bending Torque [N*m]
Min Radius [m]
Life Cycles x100
Stress Amplitude [Pa]
1
5.6492
0.003442
320
176.4336
2
7.3440
0.003442
40
229.3636
3
9.0388
0.003442
32
282.2937
4
10.7336
0.003442
12
335.2238
Figure 1. Stress-Life Curve of Samples
DISCUSSION
After conducting the following experiment, it was
discovered that each piece of material broke. Those pieces of
materials with more weight added onto the end broke much
more quickly than the lighter ones. The weights used in the
experiment were 50 in-lbs, 65 in-lbs, 80 in-lbs, and 95 in-lbs.
These weights then had to be converted into N*m making the
values 5.6492 N*m, 7.344 N*m, 9.0388 N*m, and 10.7336
N*m. The sample that was tested with 5.6492 N*m made a
total of 320 lifetime cycles *100. The stress amplitude
calculated for this sample was 176.4336 Pa. The next sample
was tested using 7.344 N*m and made a total of 40 lifetime
cycles *100. This made the stress amplitude acting upon it to be
229.3636 Pa. The next weight used for the experiment was
9.0388 N*m and it made a total 32 lifetime cycles *100. The
following amplitude stress for this sample was 282.2937 Pa.
The final weight used for the experiment was 10.7336 N*m and
it made only 12 lifetime cycles before breaking. This made the
total amplitude stress for this material to be 335.2238 Pa. the
standard deviation of the stress amplitude is 69.5008. It is
believed that the tests are accurate, but there can be errors in the
material being used since it is not clearly stated what material
was being provided.
CONCLUSION
The fatigue test is a test in which the metal sample
undergoes a cyclic load while going a set number of rpms until
failure. The results obtained from the test are under the 50 inch-
2
Copyright © 2023 by ASME
pound force the sample underwent a maximum stress of 176.4
MPa. Under the 65 inch-pound force the sample underwent a
maxim stress of 229.4 MPa. Under 80 inch-pound force the
sample underwent a maximum stress of 282.3 MPa. And under
95 inch-pounds the sample underwent a maximum stress of
335.2 MPa. R
EFERENCES
[1]
Anderson, G. (2021). Fatigue testing, pt. 1: History,
methodology, and role in Lightweighting
. Engineering
Plastics
Resources.
https://etp.teknorapex.com/blog/fatigue-testing-
history-methodology-role-in-lightweighting 3
Copyright © 2023 by ASME
Your preview ends here
Eager to read complete document? Join bartleby learn and gain access to the full version
- Access to all documents
- Unlimited textbook solutions
- 24/7 expert homework help
A
NNEX
A
P
UT
A
NNEX
TITLE
HERE
Put text of Annex here
4
Copyright © 2023 by ASME
Related Documents
Related Questions
You have been given the following test sample data following mechanical testing of 15
test pieces of a modified Alumina.
What is the Weibull modulus of this material?
Would you advise the use of this material over one with a Weibull Modulus of 19.6 and a
mean failure stress of 270 MPa, if you anticipate that the peak stress on the material
could be 255 MPa?
Sample
1
2
3
4
5
6
7
8
9
10
11
12
13
14
15
Select one or more:
a. 185
b. No
Yes
□d. 49
□e. 28.6
3.7
Failure Stress (MPa)
297
293
270
300
g. 22.8
260
296
265
295
280
288
263
290
298
275
arrow_forward
Question 2
Figure 2 shows the dependence of fatigue strength on testing cycles (S-N curve) of an acetal
polymer.
60
50
40
30
20
10
104
105
106
107
108
Number of cycles to failure
Figure 2 The S-N fatigue curve for an acetal polymer
a. What is the fatigue strength, or maximum stress amplitude, at one million cycles of
loading?
b. An acetal polymer 30-cm-long bar with a diameter of 20 mm is designed to survive
one million cycles of loading, what is the maximum allowable axial load that can be
applied on one end of the bar?
Magnitude of stress
Reversal, MPa
arrow_forward
Flag question
You have been given the following test sample data following mechanical testing of 15 test pieces of a modified Alumina.
What is the Weibull modulus of this material?
Would you advise the use of this material over one with a Weibull Modulus of 19.6 and a mean failure stress of 270 MPa, if you
anticipate that the peak stress on the material could be 255 MPa?
Sample
1
2
3
4
5
6
7
8
9
10
11
12
13
14
15
Select one or more:
Failure Stress (MPa)
297
293
270
300
260
286
265
295
4
293
280
288
263
290
298
275
arrow_forward
Figure 1 shows the tensile testing results for different materials. All specimens have an initial
diameter of 12 mm and an initial gauge length of 50 mm.
300
250
Low carbon steel
Network polymer
200
Crystalline polymer
150
Amorphous polymer
100
50
5
10
15
20
25
30
Strain (%)
Figure 1: Stress-strain curve
b. Determine the following parameters for each material:
• the tensile strength
the 0.2% offset yield strength
the modulus of elasticity
• the ductility
Stress (MPa)
LO
arrow_forward
I need the answer as soon as possible
arrow_forward
A cylindrical acetal polymer bar 64 cm long and 1.27 cm in diameter is subjected to a vibrational (tension) load at a frequency of 501 vibrations per minute with a load of 4,849 N. How many hours will the part survive before breaking? Use stress = force/area and WATCH YOUR UNITS!!
arrow_forward
Mild steel 1
Young;s modulus 1219.5
Yield strain and stress (0.4101,500.08)
Failure stress and strain :not able to find because the given data shows the experiment did not reach the failure point.
if the material stress and strain does not reach a failure point ,what dose it means , does it means that the material is more stronger?
arrow_forward
A study investigated the effects of cyclic loading and environmental conditions on fatigue crack growth at a constant 22 MPa stress for a particular material. The data from this experiment are shown below (the response is crack growth rate).
Frequency
Environment
Air
H2O
Salt H2O
10
2.29
2.06
1.90
2.47
2.05
1.93
2.48
2.23
1.75
2.12
2.03
2.06
1
2.65
3.20
3.10
2.68
3.18
3.24
2.06
3.96
3.98
2.38
3.64
3.24
0.1
2.24
11.00
9.96
2.71
11.00
10.01
2.81
9.06
9.36
2.08
11.30
10.40
Analyze the data from this experiment (use α = 0.05). Show the ANOVA table.
Analyze the residuals. Show the residual plots.
Repeat the analyses from parts (a) and (b) using ln(y) - natural log as the response. Comment on the results.
arrow_forward
5. The following data were collected from a standard 0.505-in.-diameter test
specimen of a copper alloy (initial length lo= 2.0 in.). After fracture, the total
length was 3.014 in. and the diameter was 0.374 in.
Load
(Ib)
Al
(in.)
00000
3,000
6,000
0.00167
0.00333
7,500
0.00417
9,000
10,500
0.0090
0.040
12,000
0.26
12,400
11,400
0.50 (maximum load)
1.02 (fracture)
a)
Plot the data as engineering stress versus engineering strain.
b)
Compute the modulus of elasticity.
c)
Determine the yield strength at a strain offset of 0.002.
d)
Determine the tensile strength of this alloy.
e)
What is the approximate ductility, in percent elongation?
f)
Compute the modulus of resilience.
g)
Compute from the data and plot true stress versus true strain diagram.
arrow_forward
Results:
material
iron
brass
aluminum
copper
NH
VINI
Discussion:
vickers hardnes test
Load(kg)
50
50
30
30
Diameter of
trace
d1 d2
0.58 0.65
0.68
0.74
0.94 0.86
0.72 0.76
d1+d2
2
VHN
Kg/mm²
1- Calculate the Vickers hardness number for the previous samples and
compare the results and discuss them according to the table.
2- Draw a graphic relationship between the diameter of the trace and the
hardness of Vickers.
3- What is the condition for using the Vickers hardness device?
arrow_forward
Given the following data for five different materials answer parts A B C D E & F with an explanation
arrow_forward
6. The following engineering stress-strain data were obtained for 0.2% C plain
carbon steel.
(a) Plot the engineering stress-strain curve
(b) Determine the ultimate tensile strength for the alloy
(c) Determine the percent elongation at fracture
(d) Plot the true stress-strain curve
Engineering strain, in./in.
Engineering stress, ksi
30
0.001
55
0.002
60
0.005
68
0.01
72
0.02
74
0.04
75
0.06
76
0.08
75
0.1
73
0.12
69
0.14
65
0.16
56
0.18
51
0.19(fracture)
arrow_forward
Load
(N)
Al
(mm)
0.0000
0.0296
0.0592
5,000
10,000
15,000
20,000
25,000
26,500
27,000
26,500
25,000
0.0888
0.15
0.51
0.90
1.50 (maximum load)
2.10
2.79 (fracture)
Pull test result data in Table 1. Obtained from the tensile testing of an ingredient. Specimen
diameter A (A=11.75 mm), with gauge length = 30.00 mm. After breaking, the gauge length
becomes 32.61 mm and the diameter is broken B (B=11.51 mm). From the data of the tensile
test results:
a. Plot the stress curve of the engineering strain from the test.
b. Determine the modulus of elasticity of the material.
c. Calculate the strain that occurs, if the material is loaded with a force of 7158 (N).
What defromation happened?
arrow_forward
Cyclic Stresses (Fatigue); The S-N Curve
4. The fatigue data for a ductile cast iron are given as follows:
Cycles to Failure
Stress
Amplitude
[MPa (ksi)]
248 (36.0)
236 (34.2)
224 (32.5)
213 (30.9)
201 (29.1)
193 (28.0)
193 (28.0)
193 (28.0)
1 × 105
3 x 105
1 x 10⁰
3 x 106
1 x 107
3 x 107
1 108
3 × 108
(a) Make an S-N plot (stress amplitude versus logarithm cycles to failure) using these data.
(b) What is the fatigue limit for this alloy?
(c) Determine fatigue lifetimes at stress amplitudes of 230 MPa (33,500 psi) and 175 MPa (25,000
psi).
(d) Estimate fatigue strengths at 2 × 105 and 6 × 106 cycles.
arrow_forward
By looking at these graphs, answer the following answer:
1/ Is the material is ductile or brittle? explain by using information from the graphs.
2/ What are the differences between these two graphs?
arrow_forward
Project 2:
Table 3 & 4 shows the fatigue data for two different materials to be used for an automobile rotating
parts at an average rotational speed of 750 revolutions per minute:
Stress in Mpa
170
148
130
114
92
80
74
Table 3: Summary of fatigue data part 1
Number of cycles
37000
100000
300000
1000000
10000000
100000000
1000000000
arrow_forward
(d) Following experimental data (TableQ1b) has obtained from the
torsion test for the specimen dimension given in Table Q1a.
Determine the material of a circular bar. (Take the material
Poisson's Ratio as 0.32)
Table Q1a Specimen Dimensions
Dimensions
Material
Diameter (mm)
6
Length (mm)
77.15
TableQ1b Experimental Results from Torsion test
Angular Deflection
Degree
Radian
Torque/Nm
0.5
0.008727
0.06
1
0.017453
0.47
1.5
0.02618
0.76
2
0.034907
1.01
2.5
0.043633
1.32
3
0.05236
1.65
3.5
0.061087
1.99
4
0.069813
2.32
4.5
0.07854
2.66
5
0.087267
3.00
5.5
0.095993
3.33
6
0.10472
3.64
10
0.174533
5.92
20
0.349066
7.74
30
0.523599
8.07
40
0.698132
8.17
50
0.872665
7.93
60
1.047198
8.10
70
1.221731
8.2
80
1.396264
8.4
90
1.570797
8.24
100
1.74533
8.7
110
1.919863
8.7
120
2.094396
8.7
180
3.141594
9.02
240
4.188792
9.11
300
5.23599
9.48
360
6.283188
9.51
420
7.330386
9.71
arrow_forward
1. A tensile test was conducted on a metal "505" specimen and the following stress-strain curves
were generated, both curves generated from the same set of data. Use the graphs to fill in the
mechanical properties of the material tested in the box below. Don't forget units!
Stress vs Strain
Stress, psi
Stress, psi
80000
70000
60000
50000
40000
30000
20000
10000
0
0.00
80000
70000
60000
50000
40000
30000
20000
10000
0.02
0
0.000 0.002
0.04
0.004
0.06
0.006
0.08
0.10
Strain
Stress vs Strain
0.008
0.12
Elastic Modulus, E:
0.2% Offset Yield Strength, oo:
Tensile Strength, ou:
Breaking Strength, of:
% Elongation:
0.14
0.010 0.012 0.014
Strain
0.16
0.18
0.016 0.018
0.20
0.020
arrow_forward
A sample of crosslinked polvisoprene rubber undergoes a constant strain rate axial tension experiment
The initial sample measurements are 3.60 cm gauge length (axial direction); 0.b2 cm wide; 0.1/ cm thick:
arrow_forward
SEE MORE QUESTIONS
Recommended textbooks for you
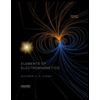
Elements Of Electromagnetics
Mechanical Engineering
ISBN:9780190698614
Author:Sadiku, Matthew N. O.
Publisher:Oxford University Press
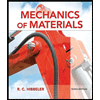
Mechanics of Materials (10th Edition)
Mechanical Engineering
ISBN:9780134319650
Author:Russell C. Hibbeler
Publisher:PEARSON
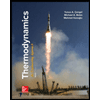
Thermodynamics: An Engineering Approach
Mechanical Engineering
ISBN:9781259822674
Author:Yunus A. Cengel Dr., Michael A. Boles
Publisher:McGraw-Hill Education
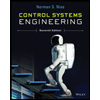
Control Systems Engineering
Mechanical Engineering
ISBN:9781118170519
Author:Norman S. Nise
Publisher:WILEY
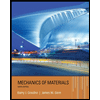
Mechanics of Materials (MindTap Course List)
Mechanical Engineering
ISBN:9781337093347
Author:Barry J. Goodno, James M. Gere
Publisher:Cengage Learning
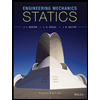
Engineering Mechanics: Statics
Mechanical Engineering
ISBN:9781118807330
Author:James L. Meriam, L. G. Kraige, J. N. Bolton
Publisher:WILEY
Related Questions
- You have been given the following test sample data following mechanical testing of 15 test pieces of a modified Alumina. What is the Weibull modulus of this material? Would you advise the use of this material over one with a Weibull Modulus of 19.6 and a mean failure stress of 270 MPa, if you anticipate that the peak stress on the material could be 255 MPa? Sample 1 2 3 4 5 6 7 8 9 10 11 12 13 14 15 Select one or more: a. 185 b. No Yes □d. 49 □e. 28.6 3.7 Failure Stress (MPa) 297 293 270 300 g. 22.8 260 296 265 295 280 288 263 290 298 275arrow_forwardQuestion 2 Figure 2 shows the dependence of fatigue strength on testing cycles (S-N curve) of an acetal polymer. 60 50 40 30 20 10 104 105 106 107 108 Number of cycles to failure Figure 2 The S-N fatigue curve for an acetal polymer a. What is the fatigue strength, or maximum stress amplitude, at one million cycles of loading? b. An acetal polymer 30-cm-long bar with a diameter of 20 mm is designed to survive one million cycles of loading, what is the maximum allowable axial load that can be applied on one end of the bar? Magnitude of stress Reversal, MPaarrow_forwardFlag question You have been given the following test sample data following mechanical testing of 15 test pieces of a modified Alumina. What is the Weibull modulus of this material? Would you advise the use of this material over one with a Weibull Modulus of 19.6 and a mean failure stress of 270 MPa, if you anticipate that the peak stress on the material could be 255 MPa? Sample 1 2 3 4 5 6 7 8 9 10 11 12 13 14 15 Select one or more: Failure Stress (MPa) 297 293 270 300 260 286 265 295 4 293 280 288 263 290 298 275arrow_forward
- Figure 1 shows the tensile testing results for different materials. All specimens have an initial diameter of 12 mm and an initial gauge length of 50 mm. 300 250 Low carbon steel Network polymer 200 Crystalline polymer 150 Amorphous polymer 100 50 5 10 15 20 25 30 Strain (%) Figure 1: Stress-strain curve b. Determine the following parameters for each material: • the tensile strength the 0.2% offset yield strength the modulus of elasticity • the ductility Stress (MPa) LOarrow_forwardI need the answer as soon as possiblearrow_forwardA cylindrical acetal polymer bar 64 cm long and 1.27 cm in diameter is subjected to a vibrational (tension) load at a frequency of 501 vibrations per minute with a load of 4,849 N. How many hours will the part survive before breaking? Use stress = force/area and WATCH YOUR UNITS!!arrow_forward
- Mild steel 1 Young;s modulus 1219.5 Yield strain and stress (0.4101,500.08) Failure stress and strain :not able to find because the given data shows the experiment did not reach the failure point. if the material stress and strain does not reach a failure point ,what dose it means , does it means that the material is more stronger?arrow_forwardA study investigated the effects of cyclic loading and environmental conditions on fatigue crack growth at a constant 22 MPa stress for a particular material. The data from this experiment are shown below (the response is crack growth rate). Frequency Environment Air H2O Salt H2O 10 2.29 2.06 1.90 2.47 2.05 1.93 2.48 2.23 1.75 2.12 2.03 2.06 1 2.65 3.20 3.10 2.68 3.18 3.24 2.06 3.96 3.98 2.38 3.64 3.24 0.1 2.24 11.00 9.96 2.71 11.00 10.01 2.81 9.06 9.36 2.08 11.30 10.40 Analyze the data from this experiment (use α = 0.05). Show the ANOVA table. Analyze the residuals. Show the residual plots. Repeat the analyses from parts (a) and (b) using ln(y) - natural log as the response. Comment on the results.arrow_forward5. The following data were collected from a standard 0.505-in.-diameter test specimen of a copper alloy (initial length lo= 2.0 in.). After fracture, the total length was 3.014 in. and the diameter was 0.374 in. Load (Ib) Al (in.) 00000 3,000 6,000 0.00167 0.00333 7,500 0.00417 9,000 10,500 0.0090 0.040 12,000 0.26 12,400 11,400 0.50 (maximum load) 1.02 (fracture) a) Plot the data as engineering stress versus engineering strain. b) Compute the modulus of elasticity. c) Determine the yield strength at a strain offset of 0.002. d) Determine the tensile strength of this alloy. e) What is the approximate ductility, in percent elongation? f) Compute the modulus of resilience. g) Compute from the data and plot true stress versus true strain diagram.arrow_forward
- Results: material iron brass aluminum copper NH VINI Discussion: vickers hardnes test Load(kg) 50 50 30 30 Diameter of trace d1 d2 0.58 0.65 0.68 0.74 0.94 0.86 0.72 0.76 d1+d2 2 VHN Kg/mm² 1- Calculate the Vickers hardness number for the previous samples and compare the results and discuss them according to the table. 2- Draw a graphic relationship between the diameter of the trace and the hardness of Vickers. 3- What is the condition for using the Vickers hardness device?arrow_forwardGiven the following data for five different materials answer parts A B C D E & F with an explanationarrow_forward6. The following engineering stress-strain data were obtained for 0.2% C plain carbon steel. (a) Plot the engineering stress-strain curve (b) Determine the ultimate tensile strength for the alloy (c) Determine the percent elongation at fracture (d) Plot the true stress-strain curve Engineering strain, in./in. Engineering stress, ksi 30 0.001 55 0.002 60 0.005 68 0.01 72 0.02 74 0.04 75 0.06 76 0.08 75 0.1 73 0.12 69 0.14 65 0.16 56 0.18 51 0.19(fracture)arrow_forward
arrow_back_ios
SEE MORE QUESTIONS
arrow_forward_ios
Recommended textbooks for you
- Elements Of ElectromagneticsMechanical EngineeringISBN:9780190698614Author:Sadiku, Matthew N. O.Publisher:Oxford University PressMechanics of Materials (10th Edition)Mechanical EngineeringISBN:9780134319650Author:Russell C. HibbelerPublisher:PEARSONThermodynamics: An Engineering ApproachMechanical EngineeringISBN:9781259822674Author:Yunus A. Cengel Dr., Michael A. BolesPublisher:McGraw-Hill Education
- Control Systems EngineeringMechanical EngineeringISBN:9781118170519Author:Norman S. NisePublisher:WILEYMechanics of Materials (MindTap Course List)Mechanical EngineeringISBN:9781337093347Author:Barry J. Goodno, James M. GerePublisher:Cengage LearningEngineering Mechanics: StaticsMechanical EngineeringISBN:9781118807330Author:James L. Meriam, L. G. Kraige, J. N. BoltonPublisher:WILEY
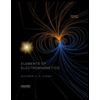
Elements Of Electromagnetics
Mechanical Engineering
ISBN:9780190698614
Author:Sadiku, Matthew N. O.
Publisher:Oxford University Press
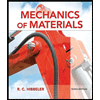
Mechanics of Materials (10th Edition)
Mechanical Engineering
ISBN:9780134319650
Author:Russell C. Hibbeler
Publisher:PEARSON
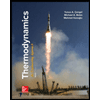
Thermodynamics: An Engineering Approach
Mechanical Engineering
ISBN:9781259822674
Author:Yunus A. Cengel Dr., Michael A. Boles
Publisher:McGraw-Hill Education
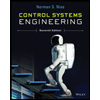
Control Systems Engineering
Mechanical Engineering
ISBN:9781118170519
Author:Norman S. Nise
Publisher:WILEY
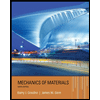
Mechanics of Materials (MindTap Course List)
Mechanical Engineering
ISBN:9781337093347
Author:Barry J. Goodno, James M. Gere
Publisher:Cengage Learning
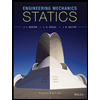
Engineering Mechanics: Statics
Mechanical Engineering
ISBN:9781118807330
Author:James L. Meriam, L. G. Kraige, J. N. Bolton
Publisher:WILEY