Final_Project_Report
docx
keyboard_arrow_up
School
Georgia Southern University *
*We aren’t endorsed by this school
Course
3331
Subject
Mechanical Engineering
Date
Feb 20, 2024
Type
docx
Pages
9
Uploaded by ProfessorLightningPartridge33
MENG 3331 Materials Science
Department of Mechanical Engineering
Nov. 27, 2023, Statesboro, Georgia, USA
Technical Report 7
WELD ANALYSIS FINAL PROJECT
Bryce Cone
Georgia Southern University
Sparks, Georgia, USA
Dylan Butler
Georgia Southern University
Albany, Georgia, USA
Scott Rhodes
Georgia Southern University Warner Robins,GA,USA
Lawrence Almeter
Georgia Southern University
Dearing, GA, USA
A
BSTRACT
In the following lab a series of experiments were
conducted on a weld sample. These experiments consist of a
metallography, a tensile test, and a hardness test experiment. In
the following experiments, two pieces of welded samples were
provided. The first weld sample was cut on both sides of the
weld then split directly down the middle and placed in an epoxy
resin. This piece was used for the metallography and the
hardness portion of the lab. For the metallography portion of
the lab the sample metal in the resin was sanded against various
pieces of sandpaper while rotating 90 degrees in between each
piece of sandpaper. After the initial sanding process the metal
undergoes the process of polishing. This allows the metal to
gain a mirror finish. This portion of the metallography
experiment took quite a bit of time due to the delicacy. An
etching process is then taken place with an acidic chemical
called Nital. This sample is then placed under a microscope to
view the fusion zone, transition zone, and base metal zone. The
photos taken are in a 100x zoom and a 1000x zoom. The next
portion of the lab conducted is the hardness portion. For this
portion, the sample used in the metallography lab is being
placed in the Rockwell Hardness tester. The goal here is to
calculate the tensile strength after being given the results of the
test. The scale used for this experiment on the Rockwell
Hardness Tester is the HRB scale. The sample metal had
several tests performed on it and the results of that are 92.5
HRB for the weld, 87 for the HAZ short side, and 79.5 HAZ
long side. The results for the area going down the length of the
sample are recorded as 82.5, 80, 82, 79, and 78. The final
experiment performed was the tensile test. This was the act of
placing the second weld sample in the ADMET testing system
and recording the results of the test. Once the results are
recorded, a calculation to determine the engineering stress. The
results of the tensile test were recorded as a range from 28.068
lbF to a max of 7278.000 lbF as shown in Table 4. Tensile Test
Calculations
N
OMENCLATURE
ADMET
Tensile Testing Machine
HAZ
Heat Affected Zone
HRB Rockwell Hardness B Scale
INTRODUCTION
This experiment consists of taking two samples of welded
3/16ths inch steel plate samples and performing tensile testing
on one sample while performing metallography and hardness
testing on the other. To begin, take one sample and cut a
perpendicular cross section of the weld and trim down the
length to include the HAZ (Heat Affected Zone), Fusion zone,
and the unaffected region of the plate. Once the sample is
prepared the sample will be set into a mold and suspended in
epoxy resin then when the resin is set the sample will be sanded
and polished to allow for observation of the microstructures of
each zone. After metallography is performed the sample’s
hardness will be tested using a rockwell hardness tester
observing the hardness of each zone. Metallography can be
accredited to Henry Clifton Sorby in the late 19th century [2].
While Rockwell Hardness testing can be credited to Stanley
Rockwell and Hugh Rockwell with the creation of the
standardized hardness testing machine [3]. The second sample will be used to observe the tensile
strength of the weld. The sample will be set into an ADMET
tensile tester and secured in place. Then the ADMET tester will
be turned on with the software recording all the data and will
record until the sample fails. Robert Hooke can be credited with
the efforts put forth to standardize the testing of properties of
metals [1]. σ
=
Force
Area
=
F
[
N
]
A
[
mm
¿¿
2
]=
Stress
[
MPa
]
¿
(1)
1
Copyright © 2023 by ASME
ε
=
Deformation
Originallength
=
ΔL
L
0
=
Strain
(2)
E
=
Stress
Strain
=
σ
ε
=
Youn g
'
s Modulus
(3)
EXPERIMENTAL METHODS
The weld test experiment is begun by cutting off
excess material using the band saw. To do this mark off two
sections about ¾ inch from the weld. Once the excess material
is removed, file and grind the edges to make smooth. Now the
abrasive saw will be used to cut the weld sample directly in half
long ways. Once the sample is in two, one side will be picked
to be placed into a cylindrical shaped form and then filled with
a resin. Once the resin is set perform the metallography
experiment on the cross-section of the weld still exposed on the
surface. Performing this includes sanding it down, then
polishing and finally acid etching it. Once completed, the
sample will be brought under the microscope and analyzed.
Under the microscope each microstructure zone of the weld
will be looked at. The zones being looked at will include the
base metal, fusion zone, HAZ, and transition zone. Next
experiment performed on the sample will be the hardness test.
Set up the rockwell hardness machine and start performing the
hardness B scale test. Multiple hardnesses will be recorded for
each zone on the weld sample to analyze how welding affects
the hardness of the metal. Finally it will be time to perform the
tensile test on the other fully intact weld sample to test how
strong the weld is on it. Place the weld sample into the ADMET
testing and record the original length,thickness and width. Once
started the machine will begin applying a tensile load on the
sample until it snaps. Take pictures and obtain the numerical
results from the software to then plot the stress-strain curve
created from the test. DATA AND
R
ESULTS
The results of the three experiments were as expected.
In the metallurgy experiment, the different zones around the
weld were extremely clear. In figures 1 and 6, the Martensite
phase is clearly visible as the shiny brass material. Around it,
the dark pearlite and white ferrite phases are visible as well.
Figure 2 displays the transition zone extremely well, and the
discoloration from the heat is visible along the edge between
the fusion zone and the HAZ. Figures 3 and 4 show the base
metal which is unaffected by the heat caused by the welding
process. The grain of the metal is still linear with mostly ferrite
phase and some pearlite phase. Figure 5 is a photo of the fusion
zone or the weld itself. The discoloration from the heat is
clearly visible.
In the hardness experiment, the hardness was tested at
the fusion zone, HAZ, and along the base metal away from the
HAZ. The data can be found in Annex A Table 1. The highest
hardness was 92.500 HRB in the fusion zone on the weld. The
HAZ had the next highest hardness value of 87.000 HRB. The
HAZ on the other side of the weld had a much lower value of
79.5 HRB. This lower value could be due to a slower cooling
rate on the longer side of the sample. Then going down the
length of the base metal, the hardness slowly decreases from
82.5 HRB closest to the HAZ to 78 HRB furthest from the
HAZ. A graphical representation of the data is shown in Figure
9. The highest value is at the fusion zone, and the hardness
slowly decreases with the increasing distance from the fusion
and HAZ. Figure 10 is an image of the weld sample after
testing the hardness.
In the tensile test, the sample performed reasonably
well. The sample did fail at the weld due to a poor fusion
between the weld and the base metal. The data and graphs can
be found in Annex A. Table 2 contains the weld sample
dimensional measurements and calculations. Table 3 shows the
first and last ten points of load data from the tensile test as well
as calculations to show the stress and strain values. Table 4
contains the calculated values of the UTS, Yield Strength,
Young’s Modulus, and elongation percentage. All the values
seem reasonable considering the sample failed prematurely due
to the poor fusion between the base metal and the weld. The
stress strain graph is shown in Figure 9. The curve is
reasonable, and it is clear that the curve ends prematurely since
the full curve would have been much more gradual in the
plastic deformation region. Figure 10 shows the Young’s
Modulus calculated from the graph. The values from the tables
and graphs align extremely close to the values of 1018 mild
steel. So it is likely that the weld samples were made from this
steel. The test was done along the length of the entire sample.
Figure 11 is an image of the sample in the tensile testing
machine before fracture. Figure 12 is a picture of the sample
after fracture. Figures 13 and 14 show the fracture more clearly,
and it is easier to see the location of the failure which is right
along the fusion line between the weld and base metal.
Figure 1.Photo of HAZ 1000x Martensite
2
Copyright © 2023 by ASME
Figure 2.
Photo of the transition / fusion zone 100x
Figure 3.
Photo of Base Metal 100x
Figure 4.
Photo of Base Metal 1000x
Figure 5.
Photo of fusion zone 100x
Figure 6.
Photo of HAZ 1000x
DISCUSSION
Upon completion of the following experiments, it is
discovered that the metal is affected in many different ways by
the weld. In the metallography portion it is noticeable that the
heat of the weld greatly affects the metal as shown in Figure 2.
Photo of transition / fusion zone 100x. This photo represents an
accurate response to great heat from the welding process.
Figure 3. Photo of Base Metal 100x represents the area of the
metal that is unaffected from heat because it is far away from
the area from where the heat was applied. Figure 5. Photo of
fusion zone 100x, this photo accurately shows what the
structure of the weld is and how the heat applied to the metal
can change crystal formation and it can be strengthened or
weakened. Upon conducting the hardness test, it is determined
that the metal becomes softer the further away from the weld.
The result for the hardness at the weld was 92.500 HRB. The
result for the HAZ short side is recorded as 87.000 HRB. The
result for HAZ long side is recorded as 79.500 HRB. As the test
was taken going down the sample weld from here, it was
recorded as 82.500 HRB,80.000 HRB, 82.000 HRB, 79.000
3
Copyright © 2023 by ASME
Your preview ends here
Eager to read complete document? Join bartleby learn and gain access to the full version
- Access to all documents
- Unlimited textbook solutions
- 24/7 expert homework help
HRB, and 78.000 HRB. This might be due to the fact that the
further a test performed from the heat applied area, the lesser
possibility of the structures were able to be properly aligned.
Finally in the tensile test a max force of 7278.000 lbF and a
Max Force of 32371.000 N was achieved. With this a Young’s
Modulus of 7.990 GPa and Yield Strength 230.000 MPa was
calculated.
CONCLUSION
This experiment was done to see how a weld affects
the metal mechanical properties. Using two different weld
samples a metallography, tensile, and hardness test were
performed. The tensile test showed the sample with a yield
strength of 230. MPa and an ultimate tensile strength of 235
MPa. Performing the hardness test on each zone showed a 92.5
HRB on the weld itself, a 87 HRB on the HAZ short side, a
79.5 HRB on the HAZ long side, and an average of 80.3 HRB
on the base metal. As the hardness test was performed further
away from the weld the metal was recorded to be softer. Upon
performing the metallography experiment it was seen that the
closer the microscope was moved to the heat affected zones
that the metal was heated very hot and cooled very fast. This
process formed martensite around the HAZ. R
EFERENCES
[1]
“Robert Hooke.” Encyclopædia Britannica
, Encyclopædia Britannica, inc., 24 July 2023, www.britannica.com/biography/Robert-Hooke. [2]
Diez, Dionis, and James DeRose. “Metallography – an
Introduction.” Science Lab | Leica Microsystems
, 5 July 2021, [3]
“Rockwell Scale.” Wikipedia
, Wikimedia Foundation, 28 May 2023, en.wikipedia.org/wiki/Rockwell_scale.
4
Copyright © 2023 by ASME
A
NNEX
A
T
ABLES
AND
G
RAPHICAL
F
IGURES
Table 1.
Hardness data
Distance [in]
Hardness [HRB]
-0.0625
87
0
92.5
0.0625
79.5
0.21875
82.5
0.34
80
0.50
82
0.66
79
0.75
78
0.8125
77
Figure 7. Hardness of the Weld Sample
Figure 8. Hardness Test on Weld Sample
Table 2.
Weld Sample Dimensions and Measurements
T
[in]
T
[mm
]
W
[in]
W
[mm
]
A
[in]
A
[mm]
GL
[in]
GL
[mm]
0.2
26
5.74
04
1.03
9
26.3
906
5.96
43
151.
493
3.95
5
100.4
57
0.1
87
4.74
98
1.03
9
26.3
906
4.93
50
125.
350
3.95
5
100.4
57
0.2
04
5.18
16
1.03
9
26.3
906
5.38
37
136.
746
3.95
5
100.4
57
A
vg
0.2
06
5.22
4
1.03
9
26.3
91
5.42
8
137.
863
3.95
5
100.4
57
St
d
D
0
0
0.00
00
0.00
00
0.51
60
13.1
070
0.00
00
0.000
0
Table 3.
Weld Sample Tensile Test Data and Calculations
Read
ing
Load
[lbF]2
Disp
[in]
Disp
[mm]
t
[s]
F
[N]
σ
[M
Pa]
ε
[mm/
mm]
1
28.06
7.31
0.018
0
124
0.9
0.000
5
Copyright © 2023 by ASME
8106
E-04
5674
.85
055
9
1848
3
2
50.68
8396
0.00
1557
0.039
5576
8
0.
5
225
.46
1.6
354
1
0.000
3937
8
3
79.11
179
0.00
2393
0.060
7878
5
1
351
.89
2.5
524
6
0.000
6051
1
4
117.0
0966
0.00
3225
0.081
9220
6
1.
5
520
.46
3.7
752
0.000
8154
9
5
164.1
4514
0.00
4058
0.103
0802
6
2
730
.12
5.2
959
7
0.001
0261
1
6
225.0
1859
0.00
4892
0.124
2624
5
2.
5
100
0.9
7.2
599
9
0.001
2369
7
7
286.6
026
0.00
5725
0.145
4206
5
3
127
4.8
9.2
469
4
0.001
4475
9
8
342.7
3883
0.00
6559
0.166
6028
4
3.
5
152
4.5
11.
058
1
0.001
6584
5
9
396.7
433
0.00
7393
0.187
7850
3
4
176
4.7
12.
800
5
0.001
8693
1
10
447.6
6855
0.00
8227
0.208
9672
2
4.
5
199
1.2
14.
443
6
0.002
0801
7
176
3456.
2854
0.14
6559
3.722
5960
6
87
.5
153
74
111
.51
4
0.037
0566
1
177
3229.
0166
0.14
7393
3.743
7781
4
88
143
63
104
.18
1
0.037
2674
7
178
1403.
7606
0.14
8226
3.764
9363
88
.5
624
3.9
45.
290
0.037
4780
4
9
9
179
-
0.118
4308
0.14
9059
3.786
0942
8
89
-
0.5
268
-
0.0
038
0.037
6887
1
180
0.236
8616
6
0.14
9893
3.807
2768
7
89
.5
1.0
536
0.0
076
4
0.037
8995
7
181
0.236
8616
6
0.15
0725
3.828
4109
4
90
1.0
536
0.0
076
4
0.038
1099
5
182
0.236
8616
6
0.15
1559
3.849
5932
7
90
.5
1.0
536
0.0
076
4
0.038
3208
1
183
0.355
2925
0.15
2391
3.870
7273
4
91
1.5
803
0.0
114
6
0.038
5311
9
184
0.473
7233
2
0.15
3225
3.891
9094
1
91
.5
2.1
071
0.0
152
8
0.038
7420
4
185
0.473
7233
2
0.15
4058
3.913
0678
7
92
2.1
071
0.0
152
8
0.038
9526
6
Table 4.
Tensile Test Calculations
UTS [MPa]
235
%EL
4
Young's Modulus [MPa]
7990
Young's Modulus [GPa]
7.99
Yield Strength [MPa]
230
Max Force [lbF]
7278
Max Force [N]
32371
6
Copyright © 2023 by ASME
Your preview ends here
Eager to read complete document? Join bartleby learn and gain access to the full version
- Access to all documents
- Unlimited textbook solutions
- 24/7 expert homework help
Figure 9. Weld Sample Stress/Strain graph
Figure 10. Yield Strength and Young’s Modulus
Figure 11. Weld sample before fracture
7
Copyright © 2023 by ASME
Figure 12. Weld sample after fracture
Figure 13. Close view of fracture weld side
8
Copyright © 2023 by ASME
Figure 14. Close view of fracture base metal side
9
Copyright © 2023 by ASME
Your preview ends here
Eager to read complete document? Join bartleby learn and gain access to the full version
- Access to all documents
- Unlimited textbook solutions
- 24/7 expert homework help
Related Documents
Related Questions
Q1. Well water contained in an AISI 304 SS pipe network for chemical treatment and posterior distribution by aerial water pipes to different locations in a food manufacturing facility was analysed. The AISI 304 SS pipe network had an approximate 300 m length, 154 mm diameter and 2.0 mm wall thickness. The AISI 304 SS pipes were welded using a Tungsten Inert Gas (TIG) welding procedure. In-situ weld quality assurance was tested by pressurized WW, and no pinhole leakage was detected. After the pipe network remained out of service for 6 months at room temperature containing stagnant, pressurized well water, pitting corrosion was observed on the weld joints and the base material by the presence of multiple pinhole leaks.(a) Discuss, with chemical equations if relevant, TWO corrosion events that may have caused the pitting corrosion.(b) What practical steps could have been taken to mitigate for this potential outcome?(c) Identify corrosion inhibition methods to mitigate for the corrosion…
arrow_forward
Two 3.5 mm thick metal (Um = 9.5 J/mm?)
sheets are being joined using resistance spot welding. To achieve
required strength, it is desired to form a weld nugget that is 5.5 mm in
diameter and 4.0 mm thick. The weld duration will be set at 0.3 sec. If
the electrical resistance between the surfaces is 140 microohms, and
only onethird of the electrical energy generated will be used to form the
weld nugget determine the current.
arrow_forward
Pls don’t use ai and fast :)
arrow_forward
Need help with this Mechanics of Materials review
arrow_forward
Question 1
You are working on a design team at a small orthopaedic firm. You have been asked to select a cobalt-
chrome-molybdenum (CoCr) material that will not experience plastic deformation under a specific mechanical test, as follows...
A tensile stress is applied along the long axis of a solid cylindrical rod that has a diameter of 10 mm. An applied load of some
magnitude F produces a 7x10³ mm change in diameter (see figure below, original shape is blue, elongated shape is unshaded).
Q1C-D: Using the table of material properties below, calculate the magnitude of stress (o) and applied load (F) required to produce
the 7x10-³ mm change in diameter for rods fabricated from F75 CoCr alloy (as cast) and F90 CoCr alloy (hot forged) materials.
arrow_forward
Test Specimen
4140 CF steel
6061 T6 Al
Gray Cast iron 40
FC Brass 360
Impact Energy (J or ft-lb)
48.5 ft-lb
25 ft-lb
12 ft-lb
27 ft-lb
Impact Strength (J/m
or ft-lb/in)
123.096 ft-lb/in
63.452 ft-lb/in
What is the final analysis/ overall observation from the data?
30.457 ft-lb/in
68.528 ft-lb/in
arrow_forward
Question 1
You are working on a design team at a small orthopaedic firm. You have been asked to select a cobalt-
chrome-molybdenum (CoCr) material that will not experience plastic deformation under a specific mechanical test, as follows...
A tensile stress is applied along the long axis of a solid cylindrical rod that has a diameter of 10 mm. An applied load of some
magnitude F produces a 7x10-³ mm change in diameter (see figure below, original shape is blue, elongated shape is unshaded).
Q1E: Of those two materials (F75 CoCr alloy (as cast) and F90 CoCr alloy (hot forged)), which materials would you select to assure
that the deformation is entirely elastic (No yield!)?
arrow_forward
Question 1
You are working on a design team at a small orthopaedic firm. You have been asked to select a cobalt-
chrome-molybdenum (CoCr) material that will not experience plastic deformation under a specific mechanical test, as follows...
A tensile stress is applied along the long axis of a solid cylindrical rod that has a diameter of 10 mm. An applied load of some
magnitude F produces a 7x10-³ mm change in diameter (see figure below, original shape is blue, elongated shape is unshaded).
Q1G: If your design required using the new material to create a wire, what is the largest diameter that would lead to ductile
behavior while still avoiding plastic deformation when exposed to the above loading conditions?
arrow_forward
3. Two specimens with the same dimensions and made from two different materials, A and B, were subjected to tensile testing. The percentage
reduction in the area of the specimen made of material 'A' was calculated 3 times that of the specimen made of material B. In this case,
O A lthe ductility of material A and B is equal
O Bthe material A is brittle and material B is ductile
O Cthe material B is more ductile than material A
O D nhe material A is more ductile than material B
1.
20
O Aramak için buraya yazıin
arrow_forward
QUESTION 15
A bimetallic bar is made of two equal length steel and brass bars of same width firmly bonded
together. The cross-sectional area of the brass bar is twice that of the steel bar. The Young's
modulus of steel is twice that of brass. The coefficient of linear expansion of brass is twice
that of steel.
When the compound bar is subjected to a temperature rise of 50°C, what is the ratio of stress
generated in steel to stress generated in brass?
Note: Please study lecture slides and tutorial problem on thermal stress - strain
O a. 1:(-2)
O b. 1 : (-1)
C. 2: (-1)
O d.4:(-1)
QUESTION 16
arrow_forward
QUESTION
The following data were obtained during a tension test of a low carbon steel specimen
having a gauge length of 100 mm.
At the point where the stress strain curve deviated from linearity, the load was 35KN, the
gauge length was 102.5 mm and the diameter of the specimen was 1.6 mm. Before necking
began, loads of 45 KN and 55 KN produced gauge lengths of 103.4 mm and 107.7 mm
respectively.
Calculate
(a) The Modulus of elasticity
(b) The Strainhardening exponent
arrow_forward
1. A tensile test was conducted on a metal "505" specimen and the following stress-strain curves
were generated, both curves generated from the same set of data. Use the graphs to fill in the
mechanical properties of the material tested in the box below. Don't forget units!
Stress vs Strain
Stress, psi
Stress, psi
80000
70000
60000
50000
40000
30000
20000
10000
0
0.00
80000
70000
60000
50000
40000
30000
20000
10000
0.02
0
0.000 0.002
0.04
0.004
0.06
0.006
0.08
0.10
Strain
Stress vs Strain
0.008
0.12
Elastic Modulus, E:
0.2% Offset Yield Strength, oo:
Tensile Strength, ou:
Breaking Strength, of:
% Elongation:
0.14
0.010 0.012 0.014
Strain
0.16
0.18
0.016 0.018
0.20
0.020
arrow_forward
UzNDU3NTYyMjk0/a/MjYOMzAwMjMOOTM5/details
Further questions
4.The graphs show how the extension changes with stretching force for four different materials.
a. Which two graphs show materials that follow Hooke's law?
A
B
b. Which two graphs show materials that become less stiff as
they are stretched?
force
force
D
C. Which graph shows a material that maintains the same
stiffness throughout?
force
force
1. A force of 20N stretches a spring by 0.5m. The spring obeys Hooke's law.
a. Calculate the spring constant including a suitable unit.
b. How much force must a man use to stretch it by 1.5m?
5. A car has a weight of 240OON which is distributed equally over all four wheels. Each wheel has a spring of
spring constant 400N/cm.
a.
Determine the force through the spring on each wheel.
b. Calculate the compression of each spring when the car rests on the ground.
6.In a spring experiment the results were as follows:
Force (N)
Length (mpm
1
2
4
6.
7
50
58
70
74
82
9n
102
125
LELL
arrow_forward
do not copy wrong solution
arrow_forward
How did temperature affect the toughness of the specimens?
arrow_forward
Consider the graph below for 3 test samples A, B and C of the same metal composition which have been cold-worked, but to different extents. If you had to
sort the samples by the degree of cold-working they have undergone, how would you rank them?
Stress (MPa)
600
500
400
300
200
100
05
0
Select one:
O a.
A
arrow_forward
Which of these statements are correct?
arrow_forward
6. State your answers to the following questions.Strain Gauge represents the deformation of a material through a change in resistance. If so, explain how temperature will affect the strain gauge in the experimental environment.①:In this experiment, the Strain Gauge measures the strain in micro units. Explain one possible error factor when applying a load by hanging a weight on the material with the strain gauge attached. (Hint: It is easy to shake by hanging the weight using a thread)①:
arrow_forward
Question 2
You are a biomedical engineer working for a small orthopaedic firm that fabricates rectangular shaped fracture
fixation plates from titanium alloy (model = "Ti Fix-It") materials. A recent clinical report documents some problems with the plates
implanted into fractured limbs. Specifically, some plates have become permanently bent while patients are in rehab and doing partial
weight bearing activities.
Your boss asks you to review the technical report that was generated by the previous test engineer (whose job you now have!) and used to
verify the design. The brief report states the following... "Ti Fix-It plates were manufactured from Ti-6Al-4V (grade 5) and machined into
solid 150 mm long beams with a 4 mm thick and 15 mm wide cross section. Each Ti Fix-It plate was loaded in equilibrium in a 4-point bending
test (set-up configuration is provided in drawing below), with an applied load of 1000N. The maximum stress in this set-up was less than the
yield stress for the…
arrow_forward
7. The following data were collected from a 20-mm diameter test specimen of a
ductile cast iron (lo = 40.00 mm). After fracture, the total length was 47.42 mm
and the diameter was 18.35 mm.
Load
Al
(N)
(mm)
0.0000
25,000
0.0185
50,000
75,000
90,000
105,000
120,000
131,000
0.0370
0.0555
0.20
0.60
1.56
4.00 (maximum load)
7.52 (fracture)
125,000
a)
Plot the data as engineering stress versus engineering strain.
b)
Compute the modulus of elasticity.
c)
Determine the yield strength at a strain offset of 0.002.
d)
Determine the tensile strength of this alloy.
e)
What is the approximate ductility, in percent elongation?
f)
Compute the modulus of resilience.
g)
Compute from the data and plot true stress versus true strain diagram.
arrow_forward
SEE MORE QUESTIONS
Recommended textbooks for you
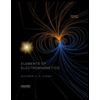
Elements Of Electromagnetics
Mechanical Engineering
ISBN:9780190698614
Author:Sadiku, Matthew N. O.
Publisher:Oxford University Press
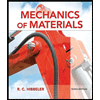
Mechanics of Materials (10th Edition)
Mechanical Engineering
ISBN:9780134319650
Author:Russell C. Hibbeler
Publisher:PEARSON
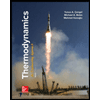
Thermodynamics: An Engineering Approach
Mechanical Engineering
ISBN:9781259822674
Author:Yunus A. Cengel Dr., Michael A. Boles
Publisher:McGraw-Hill Education
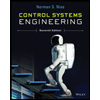
Control Systems Engineering
Mechanical Engineering
ISBN:9781118170519
Author:Norman S. Nise
Publisher:WILEY
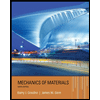
Mechanics of Materials (MindTap Course List)
Mechanical Engineering
ISBN:9781337093347
Author:Barry J. Goodno, James M. Gere
Publisher:Cengage Learning
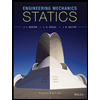
Engineering Mechanics: Statics
Mechanical Engineering
ISBN:9781118807330
Author:James L. Meriam, L. G. Kraige, J. N. Bolton
Publisher:WILEY
Related Questions
- Q1. Well water contained in an AISI 304 SS pipe network for chemical treatment and posterior distribution by aerial water pipes to different locations in a food manufacturing facility was analysed. The AISI 304 SS pipe network had an approximate 300 m length, 154 mm diameter and 2.0 mm wall thickness. The AISI 304 SS pipes were welded using a Tungsten Inert Gas (TIG) welding procedure. In-situ weld quality assurance was tested by pressurized WW, and no pinhole leakage was detected. After the pipe network remained out of service for 6 months at room temperature containing stagnant, pressurized well water, pitting corrosion was observed on the weld joints and the base material by the presence of multiple pinhole leaks.(a) Discuss, with chemical equations if relevant, TWO corrosion events that may have caused the pitting corrosion.(b) What practical steps could have been taken to mitigate for this potential outcome?(c) Identify corrosion inhibition methods to mitigate for the corrosion…arrow_forwardTwo 3.5 mm thick metal (Um = 9.5 J/mm?) sheets are being joined using resistance spot welding. To achieve required strength, it is desired to form a weld nugget that is 5.5 mm in diameter and 4.0 mm thick. The weld duration will be set at 0.3 sec. If the electrical resistance between the surfaces is 140 microohms, and only onethird of the electrical energy generated will be used to form the weld nugget determine the current.arrow_forwardPls don’t use ai and fast :)arrow_forward
- Need help with this Mechanics of Materials reviewarrow_forwardQuestion 1 You are working on a design team at a small orthopaedic firm. You have been asked to select a cobalt- chrome-molybdenum (CoCr) material that will not experience plastic deformation under a specific mechanical test, as follows... A tensile stress is applied along the long axis of a solid cylindrical rod that has a diameter of 10 mm. An applied load of some magnitude F produces a 7x10³ mm change in diameter (see figure below, original shape is blue, elongated shape is unshaded). Q1C-D: Using the table of material properties below, calculate the magnitude of stress (o) and applied load (F) required to produce the 7x10-³ mm change in diameter for rods fabricated from F75 CoCr alloy (as cast) and F90 CoCr alloy (hot forged) materials.arrow_forwardTest Specimen 4140 CF steel 6061 T6 Al Gray Cast iron 40 FC Brass 360 Impact Energy (J or ft-lb) 48.5 ft-lb 25 ft-lb 12 ft-lb 27 ft-lb Impact Strength (J/m or ft-lb/in) 123.096 ft-lb/in 63.452 ft-lb/in What is the final analysis/ overall observation from the data? 30.457 ft-lb/in 68.528 ft-lb/inarrow_forward
- Question 1 You are working on a design team at a small orthopaedic firm. You have been asked to select a cobalt- chrome-molybdenum (CoCr) material that will not experience plastic deformation under a specific mechanical test, as follows... A tensile stress is applied along the long axis of a solid cylindrical rod that has a diameter of 10 mm. An applied load of some magnitude F produces a 7x10-³ mm change in diameter (see figure below, original shape is blue, elongated shape is unshaded). Q1E: Of those two materials (F75 CoCr alloy (as cast) and F90 CoCr alloy (hot forged)), which materials would you select to assure that the deformation is entirely elastic (No yield!)?arrow_forwardQuestion 1 You are working on a design team at a small orthopaedic firm. You have been asked to select a cobalt- chrome-molybdenum (CoCr) material that will not experience plastic deformation under a specific mechanical test, as follows... A tensile stress is applied along the long axis of a solid cylindrical rod that has a diameter of 10 mm. An applied load of some magnitude F produces a 7x10-³ mm change in diameter (see figure below, original shape is blue, elongated shape is unshaded). Q1G: If your design required using the new material to create a wire, what is the largest diameter that would lead to ductile behavior while still avoiding plastic deformation when exposed to the above loading conditions?arrow_forward3. Two specimens with the same dimensions and made from two different materials, A and B, were subjected to tensile testing. The percentage reduction in the area of the specimen made of material 'A' was calculated 3 times that of the specimen made of material B. In this case, O A lthe ductility of material A and B is equal O Bthe material A is brittle and material B is ductile O Cthe material B is more ductile than material A O D nhe material A is more ductile than material B 1. 20 O Aramak için buraya yazıinarrow_forward
- QUESTION 15 A bimetallic bar is made of two equal length steel and brass bars of same width firmly bonded together. The cross-sectional area of the brass bar is twice that of the steel bar. The Young's modulus of steel is twice that of brass. The coefficient of linear expansion of brass is twice that of steel. When the compound bar is subjected to a temperature rise of 50°C, what is the ratio of stress generated in steel to stress generated in brass? Note: Please study lecture slides and tutorial problem on thermal stress - strain O a. 1:(-2) O b. 1 : (-1) C. 2: (-1) O d.4:(-1) QUESTION 16arrow_forwardQUESTION The following data were obtained during a tension test of a low carbon steel specimen having a gauge length of 100 mm. At the point where the stress strain curve deviated from linearity, the load was 35KN, the gauge length was 102.5 mm and the diameter of the specimen was 1.6 mm. Before necking began, loads of 45 KN and 55 KN produced gauge lengths of 103.4 mm and 107.7 mm respectively. Calculate (a) The Modulus of elasticity (b) The Strainhardening exponentarrow_forward1. A tensile test was conducted on a metal "505" specimen and the following stress-strain curves were generated, both curves generated from the same set of data. Use the graphs to fill in the mechanical properties of the material tested in the box below. Don't forget units! Stress vs Strain Stress, psi Stress, psi 80000 70000 60000 50000 40000 30000 20000 10000 0 0.00 80000 70000 60000 50000 40000 30000 20000 10000 0.02 0 0.000 0.002 0.04 0.004 0.06 0.006 0.08 0.10 Strain Stress vs Strain 0.008 0.12 Elastic Modulus, E: 0.2% Offset Yield Strength, oo: Tensile Strength, ou: Breaking Strength, of: % Elongation: 0.14 0.010 0.012 0.014 Strain 0.16 0.18 0.016 0.018 0.20 0.020arrow_forward
arrow_back_ios
SEE MORE QUESTIONS
arrow_forward_ios
Recommended textbooks for you
- Elements Of ElectromagneticsMechanical EngineeringISBN:9780190698614Author:Sadiku, Matthew N. O.Publisher:Oxford University PressMechanics of Materials (10th Edition)Mechanical EngineeringISBN:9780134319650Author:Russell C. HibbelerPublisher:PEARSONThermodynamics: An Engineering ApproachMechanical EngineeringISBN:9781259822674Author:Yunus A. Cengel Dr., Michael A. BolesPublisher:McGraw-Hill Education
- Control Systems EngineeringMechanical EngineeringISBN:9781118170519Author:Norman S. NisePublisher:WILEYMechanics of Materials (MindTap Course List)Mechanical EngineeringISBN:9781337093347Author:Barry J. Goodno, James M. GerePublisher:Cengage LearningEngineering Mechanics: StaticsMechanical EngineeringISBN:9781118807330Author:James L. Meriam, L. G. Kraige, J. N. BoltonPublisher:WILEY
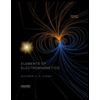
Elements Of Electromagnetics
Mechanical Engineering
ISBN:9780190698614
Author:Sadiku, Matthew N. O.
Publisher:Oxford University Press
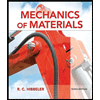
Mechanics of Materials (10th Edition)
Mechanical Engineering
ISBN:9780134319650
Author:Russell C. Hibbeler
Publisher:PEARSON
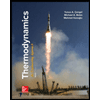
Thermodynamics: An Engineering Approach
Mechanical Engineering
ISBN:9781259822674
Author:Yunus A. Cengel Dr., Michael A. Boles
Publisher:McGraw-Hill Education
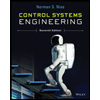
Control Systems Engineering
Mechanical Engineering
ISBN:9781118170519
Author:Norman S. Nise
Publisher:WILEY
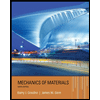
Mechanics of Materials (MindTap Course List)
Mechanical Engineering
ISBN:9781337093347
Author:Barry J. Goodno, James M. Gere
Publisher:Cengage Learning
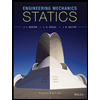
Engineering Mechanics: Statics
Mechanical Engineering
ISBN:9781118807330
Author:James L. Meriam, L. G. Kraige, J. N. Bolton
Publisher:WILEY