MENG_3331-Group_report_Lab_5_Hardness_Resubmission
docx
keyboard_arrow_up
School
Georgia Southern University *
*We aren’t endorsed by this school
Course
3331
Subject
Mechanical Engineering
Date
Feb 20, 2024
Type
docx
Pages
5
Uploaded by ProfessorLightningPartridge33
MENG 3331 Material Science
Department of Mechanical Engineering
Sept. 6, 2023, Statesboro, Georgia, USA
Technical Report 2
HARDNESS TESTING
Dylan Butler
Georgia Southern University
Albany, Ga, USA
Bryce Cone
Georgia Southern University
Sparks, GA, USA
Scott Rhodes
Georgia Southern University
Warner Robins, GA, USA
Lawrence Almeter
Georgia Southern University
Dearing, GA, USA
A
BSTRACT
The experiment was conducted to become familiar
with the Rockwell Hardness Tester and be able to calculate
tensile strength given the results of the test. The Rockwell
hardness Tester is a very common tool used for determining
hardness since it is a very simple tool to use and requires no
experience or certifications to use. In the experiment several
materials were given to use which include 1018 steel, two
samples of 1045 steel, and cast iron. The Rockwell Hardness
Tester is then used to determine the hardness number of each
material on the HRB scale. A graph of all scales and their
equivalent tensile strength is given in the lab manual. Using the
chart, the tensile strength of 1018 steel is 88000 psi, 92000 psi,
94000 psi in three trials. The first bar of 1045 steel measured a
tensile of 112000 psi, 115,000 psi, and 115,000 psi in three
trials. The second bar of 1045 steel read a tensile strength of
109,000 psi, 113,500 psi, and 107,500 psi in three trials. The
final piece of material, cast iron, read a tensile strength of
101,000 psi, 104,500 psi, 109,000 psi in three trials.
N
OMENCLATURE
HRB Rockwell Hardness B Scale
Psi
pounds per square inch (lb/in
2
)
kgf
kilogram force (kg x f)
INTRODUCTION
The Rockwell Hardness tester was created by Stanley
Rockwell and Hugh Rockwell which was a differential depth
measurement device aimed at standardizing strength testing of
different materials [1]. The differential depth measurement test
was first performed by Professor Paul Ludwik in 1908 the idea
of applying a conical bit (indenter) with a predetermined load
(pre-load) to the face of a clean finished piece of material then
adding an additional load (major load) of a standard amount to
cause deformation in the specimen, after the deformation was
complete the major load would be removed and the difference
in the deformation with the major load and without would give
a standard measurement of the hardness of materials [1,2]. The
purpose of this experiment is to establish standardized values of
measurement for the hardness of different materials. The
Rockwell test consists of multiple different scales which are all
used to measure different types of materials as to not damage
the machine when testing. This experiment will be focused on
the B scale due to the materials being tested, which consist of
1018, 1045, and Cast Iron. Different scales entail different test
parameters such as major load and indenters, in the case of
scale B the parameters are a major load of 100 kgf and an
indenter tipped with a 1/16” radius tungsten carbide ball [1].
In Eqn 1. The variable (d) corresponds to the depth of
penetration after the major load is removed.
Mean
=
Σx
N
(2)
1
Copyright © 2023 by ASME
HRB = 130 - (2.5 x d) (1)
In Eqn 2. The variable x corresponds to measured values and N
corresponds to the total number of values.
Standard Deviation
=
√
❑
(3)
In Eqn 3. The variable X corresponds to the values measured,
the variable X
corresponds to the mean of values measured, and
N corresponds to the total number of values.
EXPERIMENTAL METHODS
To perform the hardness test, a series of steps needs to
be followed. Starting with using the vice grip and file to smooth
the metal face down. Followed by using the lap wheel grinder
to make the face of the metal smooth and flat. Once the subject
is prepared, the Rockwell Hardness Tester will need to be
tested for calibration. This will be done using a metal with a
known hardness and perform the hardness test on trial metal
three times. Once the calibration is confirmed, the tester will
need to be loaded to 100 kgf. This ensures the scale will be read
in HRB. Place the metal subject onto the anvil of the tester and
raise it until the 1/16th ballpoint indenter pushes down on the
metal and the small arrow on the scale hits the little red dot.
This means the minor load is being applied to the metal. Now
align the big needle of the scale to align with the B. Push the
handle on the side of the tester to the loaded position and now
the major and minor loads are being applied. The needle will
flicker until it stops; this is when the major load will need to be
pulled back to unloaded. The needle will move and once it
stops moving this is the number that will need to be recorded as
hardness. Record the hardness of the metal used and repeat
three times for each sample of metal. From the hardness
recorded, a hardness vs tensile strength will be calculated.
Figure 1 shows a schematic of the process used to perform the
hardness test on the Rockwell Hardness test machine. Figure 1. Schematic Process of Using Rockwell Hardness
Test Machine
DATA AND
R
ESULTS
Table 1 represents the hardness data collected from
testing. Table 2 displays the hardness and tensile strength
values for the 1018 steel, 1045 steel, 1045 steel test 2, and cast
iron. The average hardness for the 1018 steel was 91.0 HRB
which is higher than the standard for cold drawn 1018 steel [4].
The average hardness for the 1045 steel was 98.67 HRB and
97.33 HRB which is slightly higher than the standard for cold
drawn 1045 steel [5]. The average hardness for the cast iron
was 95.67 HRB which is slightly lower than the standard for
Gray Cast Iron [6]. All these discrepancies are due to the fact
that the type of forging and heat treatment of the samples are
unknown.
Table 1. Hardness Data For Measured Samples
Table 2. Hardness vs Tensile Strength Data Collected
Figures
2, 3, 4,
and 5
graphically display the relationship between material hardness
and tensile strength. The data is found in Table 2.
2
Copyright © 2023 by ASME
Materia
l
Scal
e
Trial
1
Tria
l 2
Tria
l 3
Avg
Std
1018
HRB
89.5
91.5
92.0
91.00
1.08
1045
HRB
98.0
99.0
99.0
98.67
0.47
1045 #2
HRB
97.0
98.5
96.5
97.33
0.85
Cast
Iron
HRB
94.5
95.5
97.0
95.67
1.03
Material
Hardness
TS (10
3
psi)
1018
89.5
88.0
91.5
92.0
92.0
94.0
1045
98.0
112.0
99.0
115.0
99.0
115.0
1045
97.0
109.0
98.5
113.5
96.5
107.5
Cast Iron
94.5
101.0
95.5
104.5
97.0
109.0
Figure 2. 1018 Steel Hardness vs Tensile Strength Curve
Figure 3. 1045 Steel Hardness vs Tensile Strength Curve
Figure 4. 1045 Steel #2 Hardness vs Tensile Strength
Curve
Figure 5. Cast Iron Hardness vs Tensile Curve
DISCUSSION
The experiment required three trials for each of the
materials. The results for the hardness were recorded on the
HRB scale and the tensile was calculated to PSI. The results for
1018 hardness were 89.5, 91.5, 92.0 with a standard deviation
of 1.08. The tensile strength of the 1018 steel came to 88000
psi, 92000 psi, and 94,000 psi. The first 1045 steel has a
hardness of 98.0, 99.0, 99.0 with a standard deviation of .47.
The tensile strength calculated for the first bar of 1045 steel
was 112000 psi, 115000 psi, and 115000 psi. The second bar of
1045 steel was slightly lower than the first bar with a hardness
of 97.0, 98.5, 96.5, with a standard deviation .85. The tensile
strength was also lower than the first bar of 1045 with the
values being 109000 psi, 113500 psi, and 107500 psi. The final
piece of material tested was cast iron. The hardness of cast iron
is recorded as 94.5, 95.5, 97.0 with a standard deviation of
1.03. The tensile strength of the cast iron is calculated to
101000 psi, 104500 psi, and 109000 psi. After conducting the
experiment, it is discovered that in each of the samples of
materials there are small dimples left from the hardness tester.
The 1045 steel has a visibly larger dimple compared to the cast
iron and the 1018 steel. This is likely due to the larger amount
of carbon content found, thus making it a harder and stronger
metal. The graphs in figures 2, 3, 4, and 5 show the relationship
between tensile and strength to support this reasoning.
CONCLUSION
After using the Rockwell Hardness Test Machine and
performing 12 hardness tests with 3 different kinds of metal,
the following calculations could be concluded. The 1018 steel
had an average hardness of 91 with a standard deviation of
1.08. The first 1045 steel subject had an average hardness of
98.67 with a standard deviation of 0.47. The second 1045 steel
subject had an average hardness of 97.33 and standard
deviation of 0.85. The cast iron had an average hardness of
95.67 with a standard deviation of 1.03. Q
UESTIONS
1.
The Rockwell C scale uses a diamond tip with a 150
kgf major load while the Rockwell B scale uses a
1/16” steel ball tip with 100 kgf major load.
2.
The indentations must be at least three diameter
lengths apart from each other and from the edge of the
sample. 3.
The thickness requirement for a Rockwell hardness
testing sample is a 0.25in (6.35mm) minimum
thickness. Superficial testing is used for testing both
small and thin samples.
4.
The units for Rockwell Hardness are HRB. The units
for Brinell Hardness are BHN (kgf/mm
2
). The units for
Vickers Hardness are HV (kgf/mm
2
).
R
EFERENCES
[1]
“Rockwell Scale.” Wikipedia
, Wikimedia Foundation,
28 May 2023, en.wikipedia.org/wiki/Rockwell_scale. [2]
“Differential Depth Measurement.” Differential Depth
Measurement, Measurement Evaluation
, 30 July 2018,
www.emcotest.com/en/the-world-of-hardness-
testing/hardness-know-how/hardness-testing-
3
Copyright © 2023 by ASME
Your preview ends here
Eager to read complete document? Join bartleby learn and gain access to the full version
- Access to all documents
- Unlimited textbook solutions
- 24/7 expert homework help
technologies/measurement-evaluation/differential-
depth-measurement/. [3]
Shubber, Ahmed, et al. Schematic process of the
Rockwell Hardness Test Machine
. 14 Feb. 2018.
Developing Educational Simulation for Rockwell
HardnessTestMachine
,
https://cdnintech.com/media/chapter/57381/15123451
23/media/F5.png. Accessed 6 Sept. 2023. [4]
Aisi
1018
Steel,
Cold
Drawn
,
www.matweb.com/search/datasheet_print.aspx?
matguid=3a9cc570fbb24d119f08db22a53e2421.
Accessed 6 Sept. 2023. [5]
Aisi 1045 Steel, as Cold Drawn, 22-32 Mm (0.875-
1.25
in)
Round
,
www.matweb.com/search/datasheet_print.aspx?
matguid=9aa951ba895940159b45c570be74b036.
Accessed 6 Sept. 2023. [6]
Gray Cast Iron, ASTM a 48 Class 40
,
www.matweb.com/search/datasheet_print.aspx?
matguid=ec56a89f37f74e2f867a64b0f87f1e9d&n=1.
Accessed 6 Sept. 2023. 4
Copyright © 2023 by ASME
A
NNEX
A
P
UT
A
NNEX
TITLE
HERE
Put text of Annex here
5
Copyright © 2023 by ASME
Related Documents
Related Questions
The following data were obtained from the tensile test of Aluminum alloy. The initial diameter of testspecimen was 0.505 inch and gauge length was 2.0 inch. Plot the stress strain diagram and determine(a) Proportional Limit (b) Modulus of Elasticity (c) Yield Stress at 0.2% offset (d) Ultimate Stress and(e) Nominal Rupture Stress.
arrow_forward
Results:
material
iron
brass
aluminum
copper
NH
VINI
Discussion:
vickers hardnes test
Load(kg)
50
50
30
30
Diameter of
trace
d1 d2
0.58 0.65
0.68
0.74
0.94 0.86
0.72 0.76
d1+d2
2
VHN
Kg/mm²
1- Calculate the Vickers hardness number for the previous samples and
compare the results and discuss them according to the table.
2- Draw a graphic relationship between the diameter of the trace and the
hardness of Vickers.
3- What is the condition for using the Vickers hardness device?
arrow_forward
I need the answer as soon as possible
arrow_forward
A tensile test was performed on a metal specimen with a diameter of
1/2 inch and a gage length (the length over which the elongation is meas-
ured) of 4 inches. The data were plotted on a load-displacement graph,
P vs. AL. A best-fit line was drawn through the points, and the slope of
the straight-line portion was calculated to be P/AL = 1392 kips/in. What
is the modulus of elasticity?
BI
arrow_forward
The following stress-strain curve was prepared based on a tensile test of a specimen that had a circular cross-section. The gage
diameter of the specimen was 0.25 inches and the gage length was 4 inches. The stress scale of the stress-strain diagram is
given with the factor a = 10 ksi. Estimate:
(a) The modulus of elasticity.
(b) The ultimate strength.
(c) The yield strength (0.2% offset).
(d) The percent elongation at fracture.
2013 Michael Swanbom
STRESS VS. STRAIN
BY NC SA
7a
bat
Sat
2at
at
0.05
STRAIN
0.01
0.04
0.06
0.08
0.02
0.03
0.07
0.09
STRESS
arrow_forward
1. A tensile test was conducted on a metal "505" specimen and the following stress-strain curves
were generated, both curves generated from the same set of data. Use the graphs to fill in the
mechanical properties of the material tested in the box below. Don't forget units!
Stress vs Strain
Stress, psi
Stress, psi
80000
70000
60000
50000
40000
30000
20000
10000
0
0.00
80000
70000
60000
50000
40000
30000
20000
10000
0.02
0
0.000 0.002
0.04
0.004
0.06
0.006
0.08
0.10
Strain
Stress vs Strain
0.008
0.12
Elastic Modulus, E:
0.2% Offset Yield Strength, oo:
Tensile Strength, ou:
Breaking Strength, of:
% Elongation:
0.14
0.010 0.012 0.014
Strain
0.16
0.18
0.016 0.018
0.20
0.020
arrow_forward
6. The following engineering stress-strain data were obtained for 0.2% C plain
carbon steel.
(a) Plot the engineering stress-strain curve
(b) Determine the ultimate tensile strength for the alloy
(c) Determine the percent elongation at fracture
(d) Plot the true stress-strain curve
Engineering strain, in./in.
Engineering stress, ksi
30
0.001
55
0.002
60
0.005
68
0.01
72
0.02
74
0.04
75
0.06
76
0.08
75
0.1
73
0.12
69
0.14
65
0.16
56
0.18
51
0.19(fracture)
arrow_forward
Figure 1 shows the tensile testing results for different materials. All specimens have an initial
diameter of 12 mm and an initial gauge length of 50 mm.
300
250
Low carbon steel
Network polymer
200
Crystalline polymer
150
Amorphous polymer
100
50
5
10
15
20
25
30
Strain (%)
Figure 1: Stress-strain curve
b. Determine the following parameters for each material:
• the tensile strength
the 0.2% offset yield strength
the modulus of elasticity
• the ductility
Stress (MPa)
LO
arrow_forward
Stress Strain Diagram
The Data shown in the table have been obtained from a tensile test conducted on
a high-strength steel. The test specimen had a diameter of 0.505 inch and a gage
length of 2.00 inch. Using software. plot the Stress-Strain Diagram for this steel
and determine its:
A= TTdT(050s
A
%3D
1. Proportional Limit,
2. Modulus of Elasticity,
3. Yield Strength (SY) at 0.2% Offset,
4. Ultimate Strength (Su),
5. Percent Elongation in 2.00 inch,
6. Percent Reduction in Area,
7. Present the results (for Steps 1-6) in a highly organized table.
e Altac ie sheet (as problelle
4
A = 0.2.002
BEOINNING of the effort
Elongation
(in)
Elongation
(In)
Load
Load
#:
#3
(Ib)
(Ib)
1
0.0170
15
12,300
0.0004
1,500
16
12,200
0.0200
0.0010
3.
3,100
17
12,000
0.0275
0.0016
4,700
18
13,000
0.0335
5.
6,300
0.0022
19
15,000
0.0400
0.0026
6.
8,000
20
16,200
0.055
0.0032
9,500
21
17,500
0.0680
0.0035
8.
11,000
22
18,800
0.1080
0.0041
11,800
23
19,600
0.1515
0.0051
24
20,100
0.2010
10
12,300
0.0071
25…
arrow_forward
Consider the graph below for 3 test samples A, B and C of the same metal
composition which have been cold-worked, but to different extents. If you had to
sort the samples by the degree of cold-working they have undergone, how would
you rank them?
Stress (MPa)
600
500
4006
300
200
100
0
A
B
0.05
1
0.1
0.15
Strain
Select the correct answer:
a. A
arrow_forward
The % of error between a theoretical shear modulus of 65 GPa and an experimental modulus of rigidity of 60235 MPa is:
Select one:
O a. 0.0791 %
O b. 7.33 %
O c. 0.0668 %
O d. 7.9 %
Torrion test is annlied to study the properties of a material subjected to tensile force.
arrow_forward
The engineering stress-strain curve below was obtained for a
precipitation hardened Aluminum alloy.
What is the approximate Yield Strength for this alloy in psi?
Engineering Stress Based on Original Area (psi)
50,000
45,000
40,000
35,000
30,000
25,000
20,000
15,000
10,000
5,000
0
O
0.02
0.04
0.06
Aluminum 6061-T6
0.08
0.1
0.12
Engineering Strain (in/in)
0.14
X
0.16
0.18
arrow_forward
The results of a tensile test are:
Diameter of the specimen
Gauge length
Load at limit of Proportionality
Extension at the limit of Proportionality
Maximum Load
: 10mm
:40 mm
: 70kN
:0.08mm.
:100 kN
Calculate stress at limit of proportionality and young's modulus.
arrow_forward
SEE MORE QUESTIONS
Recommended textbooks for you
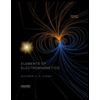
Elements Of Electromagnetics
Mechanical Engineering
ISBN:9780190698614
Author:Sadiku, Matthew N. O.
Publisher:Oxford University Press
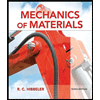
Mechanics of Materials (10th Edition)
Mechanical Engineering
ISBN:9780134319650
Author:Russell C. Hibbeler
Publisher:PEARSON
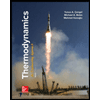
Thermodynamics: An Engineering Approach
Mechanical Engineering
ISBN:9781259822674
Author:Yunus A. Cengel Dr., Michael A. Boles
Publisher:McGraw-Hill Education
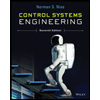
Control Systems Engineering
Mechanical Engineering
ISBN:9781118170519
Author:Norman S. Nise
Publisher:WILEY
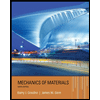
Mechanics of Materials (MindTap Course List)
Mechanical Engineering
ISBN:9781337093347
Author:Barry J. Goodno, James M. Gere
Publisher:Cengage Learning
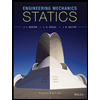
Engineering Mechanics: Statics
Mechanical Engineering
ISBN:9781118807330
Author:James L. Meriam, L. G. Kraige, J. N. Bolton
Publisher:WILEY
Related Questions
- The following data were obtained from the tensile test of Aluminum alloy. The initial diameter of testspecimen was 0.505 inch and gauge length was 2.0 inch. Plot the stress strain diagram and determine(a) Proportional Limit (b) Modulus of Elasticity (c) Yield Stress at 0.2% offset (d) Ultimate Stress and(e) Nominal Rupture Stress.arrow_forwardResults: material iron brass aluminum copper NH VINI Discussion: vickers hardnes test Load(kg) 50 50 30 30 Diameter of trace d1 d2 0.58 0.65 0.68 0.74 0.94 0.86 0.72 0.76 d1+d2 2 VHN Kg/mm² 1- Calculate the Vickers hardness number for the previous samples and compare the results and discuss them according to the table. 2- Draw a graphic relationship between the diameter of the trace and the hardness of Vickers. 3- What is the condition for using the Vickers hardness device?arrow_forwardI need the answer as soon as possiblearrow_forward
- A tensile test was performed on a metal specimen with a diameter of 1/2 inch and a gage length (the length over which the elongation is meas- ured) of 4 inches. The data were plotted on a load-displacement graph, P vs. AL. A best-fit line was drawn through the points, and the slope of the straight-line portion was calculated to be P/AL = 1392 kips/in. What is the modulus of elasticity? BIarrow_forwardThe following stress-strain curve was prepared based on a tensile test of a specimen that had a circular cross-section. The gage diameter of the specimen was 0.25 inches and the gage length was 4 inches. The stress scale of the stress-strain diagram is given with the factor a = 10 ksi. Estimate: (a) The modulus of elasticity. (b) The ultimate strength. (c) The yield strength (0.2% offset). (d) The percent elongation at fracture. 2013 Michael Swanbom STRESS VS. STRAIN BY NC SA 7a bat Sat 2at at 0.05 STRAIN 0.01 0.04 0.06 0.08 0.02 0.03 0.07 0.09 STRESSarrow_forward1. A tensile test was conducted on a metal "505" specimen and the following stress-strain curves were generated, both curves generated from the same set of data. Use the graphs to fill in the mechanical properties of the material tested in the box below. Don't forget units! Stress vs Strain Stress, psi Stress, psi 80000 70000 60000 50000 40000 30000 20000 10000 0 0.00 80000 70000 60000 50000 40000 30000 20000 10000 0.02 0 0.000 0.002 0.04 0.004 0.06 0.006 0.08 0.10 Strain Stress vs Strain 0.008 0.12 Elastic Modulus, E: 0.2% Offset Yield Strength, oo: Tensile Strength, ou: Breaking Strength, of: % Elongation: 0.14 0.010 0.012 0.014 Strain 0.16 0.18 0.016 0.018 0.20 0.020arrow_forward
- 6. The following engineering stress-strain data were obtained for 0.2% C plain carbon steel. (a) Plot the engineering stress-strain curve (b) Determine the ultimate tensile strength for the alloy (c) Determine the percent elongation at fracture (d) Plot the true stress-strain curve Engineering strain, in./in. Engineering stress, ksi 30 0.001 55 0.002 60 0.005 68 0.01 72 0.02 74 0.04 75 0.06 76 0.08 75 0.1 73 0.12 69 0.14 65 0.16 56 0.18 51 0.19(fracture)arrow_forwardFigure 1 shows the tensile testing results for different materials. All specimens have an initial diameter of 12 mm and an initial gauge length of 50 mm. 300 250 Low carbon steel Network polymer 200 Crystalline polymer 150 Amorphous polymer 100 50 5 10 15 20 25 30 Strain (%) Figure 1: Stress-strain curve b. Determine the following parameters for each material: • the tensile strength the 0.2% offset yield strength the modulus of elasticity • the ductility Stress (MPa) LOarrow_forwardStress Strain Diagram The Data shown in the table have been obtained from a tensile test conducted on a high-strength steel. The test specimen had a diameter of 0.505 inch and a gage length of 2.00 inch. Using software. plot the Stress-Strain Diagram for this steel and determine its: A= TTdT(050s A %3D 1. Proportional Limit, 2. Modulus of Elasticity, 3. Yield Strength (SY) at 0.2% Offset, 4. Ultimate Strength (Su), 5. Percent Elongation in 2.00 inch, 6. Percent Reduction in Area, 7. Present the results (for Steps 1-6) in a highly organized table. e Altac ie sheet (as problelle 4 A = 0.2.002 BEOINNING of the effort Elongation (in) Elongation (In) Load Load #: #3 (Ib) (Ib) 1 0.0170 15 12,300 0.0004 1,500 16 12,200 0.0200 0.0010 3. 3,100 17 12,000 0.0275 0.0016 4,700 18 13,000 0.0335 5. 6,300 0.0022 19 15,000 0.0400 0.0026 6. 8,000 20 16,200 0.055 0.0032 9,500 21 17,500 0.0680 0.0035 8. 11,000 22 18,800 0.1080 0.0041 11,800 23 19,600 0.1515 0.0051 24 20,100 0.2010 10 12,300 0.0071 25…arrow_forward
- Consider the graph below for 3 test samples A, B and C of the same metal composition which have been cold-worked, but to different extents. If you had to sort the samples by the degree of cold-working they have undergone, how would you rank them? Stress (MPa) 600 500 4006 300 200 100 0 A B 0.05 1 0.1 0.15 Strain Select the correct answer: a. Aarrow_forwardThe % of error between a theoretical shear modulus of 65 GPa and an experimental modulus of rigidity of 60235 MPa is: Select one: O a. 0.0791 % O b. 7.33 % O c. 0.0668 % O d. 7.9 % Torrion test is annlied to study the properties of a material subjected to tensile force.arrow_forwardThe engineering stress-strain curve below was obtained for a precipitation hardened Aluminum alloy. What is the approximate Yield Strength for this alloy in psi? Engineering Stress Based on Original Area (psi) 50,000 45,000 40,000 35,000 30,000 25,000 20,000 15,000 10,000 5,000 0 O 0.02 0.04 0.06 Aluminum 6061-T6 0.08 0.1 0.12 Engineering Strain (in/in) 0.14 X 0.16 0.18arrow_forwardarrow_back_iosSEE MORE QUESTIONSarrow_forward_ios
Recommended textbooks for you
- Elements Of ElectromagneticsMechanical EngineeringISBN:9780190698614Author:Sadiku, Matthew N. O.Publisher:Oxford University PressMechanics of Materials (10th Edition)Mechanical EngineeringISBN:9780134319650Author:Russell C. HibbelerPublisher:PEARSONThermodynamics: An Engineering ApproachMechanical EngineeringISBN:9781259822674Author:Yunus A. Cengel Dr., Michael A. BolesPublisher:McGraw-Hill Education
- Control Systems EngineeringMechanical EngineeringISBN:9781118170519Author:Norman S. NisePublisher:WILEYMechanics of Materials (MindTap Course List)Mechanical EngineeringISBN:9781337093347Author:Barry J. Goodno, James M. GerePublisher:Cengage LearningEngineering Mechanics: StaticsMechanical EngineeringISBN:9781118807330Author:James L. Meriam, L. G. Kraige, J. N. BoltonPublisher:WILEY
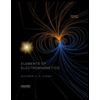
Elements Of Electromagnetics
Mechanical Engineering
ISBN:9780190698614
Author:Sadiku, Matthew N. O.
Publisher:Oxford University Press
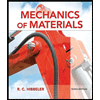
Mechanics of Materials (10th Edition)
Mechanical Engineering
ISBN:9780134319650
Author:Russell C. Hibbeler
Publisher:PEARSON
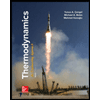
Thermodynamics: An Engineering Approach
Mechanical Engineering
ISBN:9781259822674
Author:Yunus A. Cengel Dr., Michael A. Boles
Publisher:McGraw-Hill Education
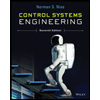
Control Systems Engineering
Mechanical Engineering
ISBN:9781118170519
Author:Norman S. Nise
Publisher:WILEY
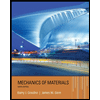
Mechanics of Materials (MindTap Course List)
Mechanical Engineering
ISBN:9781337093347
Author:Barry J. Goodno, James M. Gere
Publisher:Cengage Learning
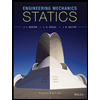
Engineering Mechanics: Statics
Mechanical Engineering
ISBN:9781118807330
Author:James L. Meriam, L. G. Kraige, J. N. Bolton
Publisher:WILEY