MENG_3331-Charpy_Lab_Group_Technical_Report_resubmission
docx
keyboard_arrow_up
School
Georgia Southern University *
*We aren’t endorsed by this school
Course
3331
Subject
Mechanical Engineering
Date
Feb 20, 2024
Type
docx
Pages
4
Uploaded by ProfessorLightningPartridge33
MENG 3331 Materials Science
Department of Mechanical Engineering
Sept. 20, 2023, Statesboro, Georgia, USA
Technical Report 4
CHARPY TEST
Bryce Cone
Georgia Southern Student
Sparks, GA, United States
Dylan Butler
Georgia Southern University
Albany, Georgia, United States
Scott Rhodes Georgia Southern University
Warner Robins, GA, United
States
Lawrence Almeter
Georgia Southern University
Dearing, GA, United States
A
BSTRACT
Charpy testing is a test used to study the toughness of
a material. In this test, a material is struck at different
temperatures to see how it absorbs energy and deforms. In this
test, the material is a mild steel kept at different temperatures,
71.4, -92.4, 209.5, -94.3, -0.6. All these measurements are
taken in degrees Fahrenheit. Each of the materials had a slight
notch made in them and were each placed in the Charpy testing
machine with the grove facing outward. The Charpy testing
machine consists of a giant swing hammer on a pendulum
which swings down and strikes the material. Upon conducting
the experiment, it was discovered that the boiled and the freezer
material had a more ductile behavior while the room temp and
dry ice material had a more brittle behavior. Ductile materials
under certain conditions can display brittleness.
N
OMENCLATURE
CVN
Charpy V-Notch Test
ft-lb
Energy [foot pounds]
INTRODUCTION
The Charpy test is performed by machining a V-notch into
a 10mm x 10mm x 55mm on one of the rectangular faces of the
sample. Next the pendulum will be set, and the sample will be
set center in the fixture with the notch facing away from the
point of impact/ towards the wall opposite of the side of the
hammer. Then the pendulum will be released causing the
hammer to smash into the sample allowing the Charpy test
machine to record the difference of the original height and the
highest point reached after the collision, which gives a
measured value of the energy absorbed due to the machine
being built in such a way that the pendulum is set at a
predetermined height and with a set weight [1].
The standardized Charpy test was developed in 1901 by
Georges Charpy who standardized S.B. Russell’s idea of
residual fracture energy [1]. These impact tests are carried out
generally only on materials whose brittle/ductile properties are
affected by temperature. Generally, the Charpy test is used to
show a ductile-brittle transition in a material due to change of
temperature. This ductile-brittle transition can be used to
determine the ductile-brittle transition temperature, which is the
temperature at which there is a large change in the energy
needed to fracture a material [1].
EXPERIMENTAL METHODS
To begin the Charpy test, pick out 5 soft steel samples
with a square face of 10x10 mm and 55mm long. Each sample
will need to be given a V-notch with the manual V-notch
Charpy machine. To do this, place the metal sample into the
slot and tighten up the pins to lock it in place. Now release the
pin on the machine and slowly crank the wheel down until the
blade has fully gone past the sample. Remove the sample and
repeat for all samples. Next will be to prep each sample for
what environment they are going into. One sample will be room
temperature, one goes into the freezer, two go into dry ice, and
1
Copyright © 2023 by ASME
one goes into boiling water. Once each sample is undergoing a
temperature change, it will be time to set up the Charpy
hammer. To do this the hammer will be lifted until it latches
onto the lever, once the hammer is latched, slide the safety onto
the lever which locks the lever in place. Now that the hammer
is set, take the room temperature sample and place it on the
little platform with the V-notch facing the opposite wall of the
hammer. Once the sample is set, release the safety and push the
lever forward. Once the hammer is released it will strike the
sample. Take the sample, examine it, and record the foot
pounds from the dial on the Charpy machine. This process will
be repeated for each sample after the desired temperature is
reached. The sample in the boiling water will boil for 20
minutes, the sample in the freezer should freeze for 45 minutes,
one dry ice sample stays in the box for 15 minutes and the other
stays in the dry ice for 35 minutes. DATA AND
R
ESULTS
Table 1 contains all measurements and results taken from
each sample test. Figure 1 shows the visual results of the
Charpy test. Figure 2 displays the trend of the data found in
Table 1. The two dry ice samples performed as expected during
the test. Both samples were brittle from the colder temperature
and therefore had the lowest absorption energy. The dry ice
sample prepared at 15 min had a higher absorbed energy of 34
ft-lb while the 35 min dry ice sample had a absorbed energy of
23 ft-lb. This was expected as the 35 min sample had longer to
cool down and become more brittle. Both dry ice samples fully
separated and broke in half during the collision. The room
temperature and boiled samples also performed as expected.
The room temperature sample had an absorption value of 63 ft-
lb that was in between the dry ice and the boiled samples. The
room temperature sample also broke completely in half. The
boiled sample had a high absorption energy of 195 ft-lb and did
not fully separate from the collision. The freezer sample
performed differently than expected. It should have had a value
somewhere between the dry ice samples and the room
temperature sample or between 34 and 63 ft-lb. However, it
had a higher absorbed energy than the boiled sample at 203 ft-
lb and it did not break in half during the collision. Figure 3
shows the expected data trend including a theoretical freezer
value of around 40 ft-lb. The lower shelf, transitional
temperature, and upper shelf are more distinguishable in this
figure.
Table 1. Steel Sample Data
Sample
Time [min]
Temperatur
e [°F]
Absorbed Energy
[ft-lb]
Dry Ice
35
-94.3
23
Dry Ice
15
-92.4
34
Freezer
45
-0.6
203
Room -
71.4
63
Temp
Boiled
20
209.5
195
Figure 1. Fracture Surface of Samples at Different
Temperatures
Figure 2. Absorbed Energy vs Temperature Curve
Figure 3. Theoretical Absorbed Energy vs Temperature
Curve
DISCUSSION
The following experiment requires an individual to be
quick when working with material because in order to get the
2
Copyright © 2023 by ASME
most accurate result the material must be tested quickly after
the temperature has been taken. This experiment requires one
trial for each of the 5 temperatures of material. The first piece
of material tested was room temperature steel. Its temperature
was recorded at 71.4° F and its absorbed energy is 63 ft-lb.
Next was the first dry ice material which was recorded at -
92.4°F and it absorbed 34 ft-lb. This temperature is obtained by
letting the steel bar sit in dry ice for 15 minutes. The boiled
steel was 209.5° and withstood 195 ft-lb of force. This
temperature was reached by allowing the steel bar to sit in
boiling water for 20 minutes. The second dry ice material had a
recorded temperature of -94.3°F and withstood 23 ft-lb of
force. This temperature was achieved by letting the steel bar sit
in dry ice for 35 minutes. The final piece of material tested was
the freezer material. The recorded temperature was -.06° F and
it withstood 203 ft-lb of force. The temperature was recorded
after letting the bar sit in the freezer for 45 minutes. Before
testing it was believed that the colder materials would handle
more force but after testing the freezer sample, the hypothesis
was incorrect. There are many reasons as to why the test for the
freezer material could be invalid. It could have taken too long
to transfer material from the freezer to the testing station, the
notch could have been off center, and a tougher material could
have been used since the given samples were unlabeled and
could have been a variety of different steels.
CONCLUSION
The Charpy test is done by a big hammer on a
pendulum and is released to strike a metal sample. After
performing the test 5 times on metal subjects with each a
different temperature. It was observed that the 71.4° Fahrenheit
sample absorbed 63 ft/lb. The 209.5° Fahrenheit sample
absorbed 195 ft/lb. The -94.3° Fahrenheit sample absorbed 23
ft/lb. The -92.4° Fahrenheit sample absorbed 34 ft/lb. The -0.6°
Fahrenheit sample absorbed 203 ft/lb. Q
UESTIONS
1.
The notch is necessary for the notched-bar impact
testing in order for the samples to perform similarly to
each other and to give more accurate testing results.
The notch gives a consistent striking target that is
easily controllable by the depth of the notch.
2.
The sharper the point in the notch the faster the crack
will develop due to the smaller radius. The notch also
needs to be centered as best as possible so that the
tests have less variability. The faster the hammer
swings, the more kinetic energy it will have. So the
speed needs to be consistent in order to correctly find
the energy absorbed by the material.
3.
In general, the colder the temperature, the more brittle
the mild steel should be resulting in lower toughness.
Raising the temperature increases the ductility, which
increases the amount of energy the material can
absorb, therefore making the toughness of the material
greater.
4.
E
=
ΔPE
+
ΔKE ΔKE
=
0
Since v
1
=
v
2
=
0
E
=
mgh
=(
60
lb
/
32.2
ft
/
s
2
)(
32.2
ft
/
s
2
)
¿
R
EFERENCES
[1]
"Charpy
Impact
Test."
Wikipedia
,
Wikimedia
Foundation,22,Oct.,2022,
en.wikipedia.org/wiki/Charpy_impact_test. Accessed 20
Sept. 2023.
3
Copyright © 2023 by ASME
Your preview ends here
Eager to read complete document? Join bartleby learn and gain access to the full version
- Access to all documents
- Unlimited textbook solutions
- 24/7 expert homework help
A
NNEX
A
P
UT
A
NNEX
TITLE
HERE
Put text of Annex here
4
Copyright © 2023 by ASME
Related Documents
Related Questions
Figure 1 shows the tensile testing results for different materials. All specimens have an initial
diameter of 12 mm and an initial gauge length of 50 mm.
300
250
Low carbon steel
Network polymer
200
Crystalline polymer
150
Amorphous polymer
100
50
5
10
15
20
25
30
Strain (%)
Figure 1: Stress-strain curve
b. Determine the following parameters for each material:
• the tensile strength
the 0.2% offset yield strength
the modulus of elasticity
• the ductility
Stress (MPa)
LO
arrow_forward
You have been given the following test sample data following mechanical testing of 15
test pieces of a modified Alumina.
What is the Weibull modulus of this material?
Would you advise the use of this material over one with a Weibull Modulus of 19.6 and a
mean failure stress of 270 MPa, if you anticipate that the peak stress on the material
could be 255 MPa?
Sample
1
2
3
4
5
6
7
8
9
10
11
12
13
14
15
Select one or more:
a. 185
b. No
Yes
□d. 49
□e. 28.6
3.7
Failure Stress (MPa)
297
293
270
300
g. 22.8
260
296
265
295
280
288
263
290
298
275
arrow_forward
I need the answer as soon as possible
arrow_forward
I need the answer as soon as possible
arrow_forward
1. A tensile test was conducted on a metal "505" specimen and the following stress-strain curves
were generated, both curves generated from the same set of data. Use the graphs to fill in the
mechanical properties of the material tested in the box below. Don't forget units!
Stress vs Strain
Stress, psi
Stress, psi
80000
70000
60000
50000
40000
30000
20000
10000
0
0.00
80000
70000
60000
50000
40000
30000
20000
10000
0.02
0
0.000 0.002
0.04
0.004
0.06
0.006
0.08
0.10
Strain
Stress vs Strain
0.008
0.12
Elastic Modulus, E:
0.2% Offset Yield Strength, oo:
Tensile Strength, ou:
Breaking Strength, of:
% Elongation:
0.14
0.010 0.012 0.014
Strain
0.16
0.18
0.016 0.018
0.20
0.020
arrow_forward
Flag question
You have been given the following test sample data following mechanical testing of 15 test pieces of a modified Alumina.
What is the Weibull modulus of this material?
Would you advise the use of this material over one with a Weibull Modulus of 19.6 and a mean failure stress of 270 MPa, if you
anticipate that the peak stress on the material could be 255 MPa?
Sample
1
2
3
4
5
6
7
8
9
10
11
12
13
14
15
Select one or more:
Failure Stress (MPa)
297
293
270
300
260
286
265
295
4
293
280
288
263
290
298
275
arrow_forward
Given the following data for five different materials answer parts A B C D E & F with an explanation
arrow_forward
Mild steel 1
Young;s modulus 1219.5
Yield strain and stress (0.4101,500.08)
Failure stress and strain :not able to find because the given data shows the experiment did not reach the failure point.
if the material stress and strain does not reach a failure point ,what dose it means , does it means that the material is more stronger?
arrow_forward
UzNDU3NTYyMjk0/a/MjYOMzAwMjMOOTM5/details
Further questions
4.The graphs show how the extension changes with stretching force for four different materials.
a. Which two graphs show materials that follow Hooke's law?
A
B
b. Which two graphs show materials that become less stiff as
they are stretched?
force
force
D
C. Which graph shows a material that maintains the same
stiffness throughout?
force
force
1. A force of 20N stretches a spring by 0.5m. The spring obeys Hooke's law.
a. Calculate the spring constant including a suitable unit.
b. How much force must a man use to stretch it by 1.5m?
5. A car has a weight of 240OON which is distributed equally over all four wheels. Each wheel has a spring of
spring constant 400N/cm.
a.
Determine the force through the spring on each wheel.
b. Calculate the compression of each spring when the car rests on the ground.
6.In a spring experiment the results were as follows:
Force (N)
Length (mpm
1
2
4
6.
7
50
58
70
74
82
9n
102
125
LELL
arrow_forward
Question 8. The following figure represents three hardness-testing techniques of materials.
Describe their specifications, how there are conducted and their potential applications?
8 -
Shape of Indentation
Test
Indenter
Side View
Top View
Load
Brinell
10-mm sphere
P
of steel or
tungsten carbide
Vickers
Diamond
136°
microhardness
ругamid
Rockwell and
60 kg)
100 kg } Rockwell
150 kg)
Diamond
120°
superficial
cone:
s - in.-
diameter
Rockwell
15 kg
30 kg } Superficial Rockwell
45 kg)
steel spheres
arrow_forward
6. The following engineering stress-strain data were obtained for 0.2% C plain
carbon steel.
(a) Plot the engineering stress-strain curve
(b) Determine the ultimate tensile strength for the alloy
(c) Determine the percent elongation at fracture
(d) Plot the true stress-strain curve
Engineering strain, in./in.
Engineering stress, ksi
30
0.001
55
0.002
60
0.005
68
0.01
72
0.02
74
0.04
75
0.06
76
0.08
75
0.1
73
0.12
69
0.14
65
0.16
56
0.18
51
0.19(fracture)
arrow_forward
Consider the graph below for 3 test samples A, B and C of the same metal
composition which have been cold-worked, but to different extents. If you had to
sort the samples by the degree of cold-working they have undergone, how would
you rank them?
Stress (MPa)
600
500
4006
300
200
100
0
A
B
0.05
1
0.1
0.15
Strain
Select the correct answer:
a. A
arrow_forward
The answer is one of the options below please solve carefully and circle the correct option Please write clear .
arrow_forward
Test Specimen
4140 CF steel
6061 T6 Al
Gray Cast iron 40
FC Brass 360
Impact Energy (J or ft-lb)
48.5 ft-lb
25 ft-lb
12 ft-lb
27 ft-lb
Impact Strength (J/m
or ft-lb/in)
123.096 ft-lb/in
63.452 ft-lb/in
What is the final analysis/ overall observation from the data?
30.457 ft-lb/in
68.528 ft-lb/in
arrow_forward
Question 2
Figure 2 shows the dependence of fatigue strength on testing cycles (S-N curve) of an acetal
polymer.
60
50
40
30
20
10
104
105
106
107
108
Number of cycles to failure
Figure 2 The S-N fatigue curve for an acetal polymer
a. What is the fatigue strength, or maximum stress amplitude, at one million cycles of
loading?
b. An acetal polymer 30-cm-long bar with a diameter of 20 mm is designed to survive
one million cycles of loading, what is the maximum allowable axial load that can be
applied on one end of the bar?
Magnitude of stress
Reversal, MPa
arrow_forward
(d) Following experimental data (TableQ1b) has obtained from the
torsion test for the specimen dimension given in Table Q1a.
Determine the material of a circular bar. (Take the material
Poisson's Ratio as 0.32)
Table Q1a Specimen Dimensions
Dimensions
Material
Diameter (mm)
6
Length (mm)
77.15
TableQ1b Experimental Results from Torsion test
Angular Deflection
Degree
Radian
Torque/Nm
0.5
0.008727
0.06
1
0.017453
0.47
1.5
0.02618
0.76
2
0.034907
1.01
2.5
0.043633
1.32
3
0.05236
1.65
3.5
0.061087
1.99
4
0.069813
2.32
4.5
0.07854
2.66
5
0.087267
3.00
5.5
0.095993
3.33
6
0.10472
3.64
10
0.174533
5.92
20
0.349066
7.74
30
0.523599
8.07
40
0.698132
8.17
50
0.872665
7.93
60
1.047198
8.10
70
1.221731
8.2
80
1.396264
8.4
90
1.570797
8.24
100
1.74533
8.7
110
1.919863
8.7
120
2.094396
8.7
180
3.141594
9.02
240
4.188792
9.11
300
5.23599
9.48
360
6.283188
9.51
420
7.330386
9.71
arrow_forward
5. The following data were collected from a standard 0.505-in.-diameter test
specimen of a copper alloy (initial length lo= 2.0 in.). After fracture, the total
length was 3.014 in. and the diameter was 0.374 in.
Load
(Ib)
Al
(in.)
00000
3,000
6,000
0.00167
0.00333
7,500
0.00417
9,000
10,500
0.0090
0.040
12,000
0.26
12,400
11,400
0.50 (maximum load)
1.02 (fracture)
a)
Plot the data as engineering stress versus engineering strain.
b)
Compute the modulus of elasticity.
c)
Determine the yield strength at a strain offset of 0.002.
d)
Determine the tensile strength of this alloy.
e)
What is the approximate ductility, in percent elongation?
f)
Compute the modulus of resilience.
g)
Compute from the data and plot true stress versus true strain diagram.
arrow_forward
The engineering stress-strain curve below was obtained for a
precipitation hardened Aluminum alloy.
What is the approximate Yield Strength for this alloy in psi?
Engineering Stress Based on Original Area (psi)
50,000
45,000
40,000
35,000
30,000
25,000
20,000
15,000
10,000
5,000
0
O
0.02
0.04
0.06
Aluminum 6061-T6
0.08
0.1
0.12
Engineering Strain (in/in)
0.14
X
0.16
0.18
arrow_forward
Please show work for practice problem 12
arrow_forward
SEE MORE QUESTIONS
Recommended textbooks for you
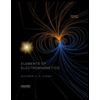
Elements Of Electromagnetics
Mechanical Engineering
ISBN:9780190698614
Author:Sadiku, Matthew N. O.
Publisher:Oxford University Press
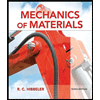
Mechanics of Materials (10th Edition)
Mechanical Engineering
ISBN:9780134319650
Author:Russell C. Hibbeler
Publisher:PEARSON
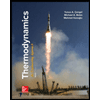
Thermodynamics: An Engineering Approach
Mechanical Engineering
ISBN:9781259822674
Author:Yunus A. Cengel Dr., Michael A. Boles
Publisher:McGraw-Hill Education
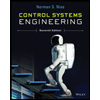
Control Systems Engineering
Mechanical Engineering
ISBN:9781118170519
Author:Norman S. Nise
Publisher:WILEY
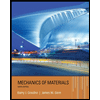
Mechanics of Materials (MindTap Course List)
Mechanical Engineering
ISBN:9781337093347
Author:Barry J. Goodno, James M. Gere
Publisher:Cengage Learning
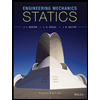
Engineering Mechanics: Statics
Mechanical Engineering
ISBN:9781118807330
Author:James L. Meriam, L. G. Kraige, J. N. Bolton
Publisher:WILEY
Related Questions
- Figure 1 shows the tensile testing results for different materials. All specimens have an initial diameter of 12 mm and an initial gauge length of 50 mm. 300 250 Low carbon steel Network polymer 200 Crystalline polymer 150 Amorphous polymer 100 50 5 10 15 20 25 30 Strain (%) Figure 1: Stress-strain curve b. Determine the following parameters for each material: • the tensile strength the 0.2% offset yield strength the modulus of elasticity • the ductility Stress (MPa) LOarrow_forwardYou have been given the following test sample data following mechanical testing of 15 test pieces of a modified Alumina. What is the Weibull modulus of this material? Would you advise the use of this material over one with a Weibull Modulus of 19.6 and a mean failure stress of 270 MPa, if you anticipate that the peak stress on the material could be 255 MPa? Sample 1 2 3 4 5 6 7 8 9 10 11 12 13 14 15 Select one or more: a. 185 b. No Yes □d. 49 □e. 28.6 3.7 Failure Stress (MPa) 297 293 270 300 g. 22.8 260 296 265 295 280 288 263 290 298 275arrow_forwardI need the answer as soon as possiblearrow_forward
- I need the answer as soon as possiblearrow_forward1. A tensile test was conducted on a metal "505" specimen and the following stress-strain curves were generated, both curves generated from the same set of data. Use the graphs to fill in the mechanical properties of the material tested in the box below. Don't forget units! Stress vs Strain Stress, psi Stress, psi 80000 70000 60000 50000 40000 30000 20000 10000 0 0.00 80000 70000 60000 50000 40000 30000 20000 10000 0.02 0 0.000 0.002 0.04 0.004 0.06 0.006 0.08 0.10 Strain Stress vs Strain 0.008 0.12 Elastic Modulus, E: 0.2% Offset Yield Strength, oo: Tensile Strength, ou: Breaking Strength, of: % Elongation: 0.14 0.010 0.012 0.014 Strain 0.16 0.18 0.016 0.018 0.20 0.020arrow_forwardFlag question You have been given the following test sample data following mechanical testing of 15 test pieces of a modified Alumina. What is the Weibull modulus of this material? Would you advise the use of this material over one with a Weibull Modulus of 19.6 and a mean failure stress of 270 MPa, if you anticipate that the peak stress on the material could be 255 MPa? Sample 1 2 3 4 5 6 7 8 9 10 11 12 13 14 15 Select one or more: Failure Stress (MPa) 297 293 270 300 260 286 265 295 4 293 280 288 263 290 298 275arrow_forward
- Given the following data for five different materials answer parts A B C D E & F with an explanationarrow_forwardMild steel 1 Young;s modulus 1219.5 Yield strain and stress (0.4101,500.08) Failure stress and strain :not able to find because the given data shows the experiment did not reach the failure point. if the material stress and strain does not reach a failure point ,what dose it means , does it means that the material is more stronger?arrow_forwardUzNDU3NTYyMjk0/a/MjYOMzAwMjMOOTM5/details Further questions 4.The graphs show how the extension changes with stretching force for four different materials. a. Which two graphs show materials that follow Hooke's law? A B b. Which two graphs show materials that become less stiff as they are stretched? force force D C. Which graph shows a material that maintains the same stiffness throughout? force force 1. A force of 20N stretches a spring by 0.5m. The spring obeys Hooke's law. a. Calculate the spring constant including a suitable unit. b. How much force must a man use to stretch it by 1.5m? 5. A car has a weight of 240OON which is distributed equally over all four wheels. Each wheel has a spring of spring constant 400N/cm. a. Determine the force through the spring on each wheel. b. Calculate the compression of each spring when the car rests on the ground. 6.In a spring experiment the results were as follows: Force (N) Length (mpm 1 2 4 6. 7 50 58 70 74 82 9n 102 125 LELLarrow_forward
- Question 8. The following figure represents three hardness-testing techniques of materials. Describe their specifications, how there are conducted and their potential applications? 8 - Shape of Indentation Test Indenter Side View Top View Load Brinell 10-mm sphere P of steel or tungsten carbide Vickers Diamond 136° microhardness ругamid Rockwell and 60 kg) 100 kg } Rockwell 150 kg) Diamond 120° superficial cone: s - in.- diameter Rockwell 15 kg 30 kg } Superficial Rockwell 45 kg) steel spheresarrow_forward6. The following engineering stress-strain data were obtained for 0.2% C plain carbon steel. (a) Plot the engineering stress-strain curve (b) Determine the ultimate tensile strength for the alloy (c) Determine the percent elongation at fracture (d) Plot the true stress-strain curve Engineering strain, in./in. Engineering stress, ksi 30 0.001 55 0.002 60 0.005 68 0.01 72 0.02 74 0.04 75 0.06 76 0.08 75 0.1 73 0.12 69 0.14 65 0.16 56 0.18 51 0.19(fracture)arrow_forwardConsider the graph below for 3 test samples A, B and C of the same metal composition which have been cold-worked, but to different extents. If you had to sort the samples by the degree of cold-working they have undergone, how would you rank them? Stress (MPa) 600 500 4006 300 200 100 0 A B 0.05 1 0.1 0.15 Strain Select the correct answer: a. Aarrow_forwardarrow_back_iosSEE MORE QUESTIONSarrow_forward_ios
Recommended textbooks for you
- Elements Of ElectromagneticsMechanical EngineeringISBN:9780190698614Author:Sadiku, Matthew N. O.Publisher:Oxford University PressMechanics of Materials (10th Edition)Mechanical EngineeringISBN:9780134319650Author:Russell C. HibbelerPublisher:PEARSONThermodynamics: An Engineering ApproachMechanical EngineeringISBN:9781259822674Author:Yunus A. Cengel Dr., Michael A. BolesPublisher:McGraw-Hill Education
- Control Systems EngineeringMechanical EngineeringISBN:9781118170519Author:Norman S. NisePublisher:WILEYMechanics of Materials (MindTap Course List)Mechanical EngineeringISBN:9781337093347Author:Barry J. Goodno, James M. GerePublisher:Cengage LearningEngineering Mechanics: StaticsMechanical EngineeringISBN:9781118807330Author:James L. Meriam, L. G. Kraige, J. N. BoltonPublisher:WILEY
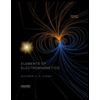
Elements Of Electromagnetics
Mechanical Engineering
ISBN:9780190698614
Author:Sadiku, Matthew N. O.
Publisher:Oxford University Press
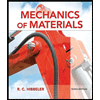
Mechanics of Materials (10th Edition)
Mechanical Engineering
ISBN:9780134319650
Author:Russell C. Hibbeler
Publisher:PEARSON
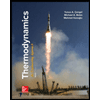
Thermodynamics: An Engineering Approach
Mechanical Engineering
ISBN:9781259822674
Author:Yunus A. Cengel Dr., Michael A. Boles
Publisher:McGraw-Hill Education
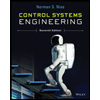
Control Systems Engineering
Mechanical Engineering
ISBN:9781118170519
Author:Norman S. Nise
Publisher:WILEY
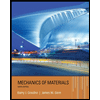
Mechanics of Materials (MindTap Course List)
Mechanical Engineering
ISBN:9781337093347
Author:Barry J. Goodno, James M. Gere
Publisher:Cengage Learning
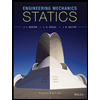
Engineering Mechanics: Statics
Mechanical Engineering
ISBN:9781118807330
Author:James L. Meriam, L. G. Kraige, J. N. Bolton
Publisher:WILEY