MENG_3331_Lab_2_individual_report
pdf
keyboard_arrow_up
School
Georgia Southern University *
*We aren’t endorsed by this school
Course
3331
Subject
Mechanical Engineering
Date
Feb 20, 2024
Type
Pages
3
Uploaded by ProfessorLightningPartridge33
Executive Summary Department of Mechanical Engineering Aug.24, 2021, Statesboro, Georgia, USA 1 Copyright © 2023 by ASME TENSILE TESTING ON BRASS Lawrence Almeter Group 5 Objective
The objective of this experiment is to find the stress-strain curve, ultimate tensile strength, Young’s Modulus, yield strength, and percent elongation of a brass tensile testing coupon. These values can be solved using the load and displacement over time data given by the tensile testing machine as well as the dimensions of our sample. Brief Introduction/Theory The modern UTM or universal testing machine was not formally developed until the 19
th
century. However, Robert Hooke, who discovered Hooke’s law or the law of Elasticity, put forth many efforts during the 17
th
century for testing the properties of materials. [1] Stress is equal to force over the cross-sectional area. Strain is equal to the length of deformation over the original length of the deformed material. The stress-strain curve is used to graphically represent the overall performance that the material exhibits while under load, and it allows many different mechanical properties of materials to be found easily. [2] Method/Procedure Start by turning on the material testing machine and starting the data collection software. Select the Gauge + ESM 303 with Travel configuration and open the setup file MENG 3331 Tensile. After setting up the machine and software, prepare the sample. Draw two lines centered on the sample 2” apart along the width of the sample. Measure the distance again three times and record the average and standard deviation for better data. Measure the width and thickness three times and record the average and standard deviation. With the sample prepared, it can be put in the testing machine. Place the sample in the lower grip and then adjust the upper grip till it is at the height of the two lines drawn previously. Adjust the upper grip as close to zero travel as possible. Click start on the software and wait till the sample fails. Data& Results The sample dimensions were 0.160in or 4.056mm in width, 0.003in or 0.076mm in thickness, 2.567in or 65.21mm in gauge length, and the cross-sectional area was 0.12in
2
or 0.309mm
2
. These values are found in Table 1. The data given by the machine over 108.4 seconds showed the max load applied to the sample was 31.7lbf, and the max displacement in the brass was 0.901in or 22.8854mm. The max force calculated was 141.00N. The max stress was 456.269MPa, and the max strain was 0.3509mm/mm. These values are found in Table 2. Discussion Most of our results compared neatly to the known values. Our calculated cross-sectional area of 0.309mm
2
was close to the known 0.303mm
2
. The known tensile max tensile strength of brass is 430 MPa and our value is close at 458 MPa. Our estimation of elongation percent was 35% which is off from the known value of 25%. This is partially due to calculating it by converting the max strain into a percent which is not highly accurate, but it is a rough estimation. Our calculated Modulus of Elasticity was 41.18 GPa which was far off from the known 117 GPa. This could be due to defects in the material, improper placement in the testing machine, or even a bad estimation of the slope [Figure 2]. Performing more tests could give more consistent data and remove many outliers. Conclusion These are the calculated values for the brass testing material. The Young’s Modulus is 41.14 GPa. The Yield Strength is 300 MPa. The Ultimate Tensile Strength is 458 MPa. The percent elongation is 35%. These values are found in Table 4. Lab Questions 1.
The upper yield strength of the 1004 steel is approximately 380 MPa and the lower yield strength is approximately 360 MPa. 2.
Copper has a higher ductility since it has a larger strain value. 3.
The 1020 steel has a higher toughness since the area under its curve is larger than the area under the 1004 steel curve.
Executive Summary Department of Mechanical Engineering Aug.24, 2021, Statesboro, Georgia, USA 2 Copyright © 2023 by ASME Support Materials Data Table 1 summarizes the measurements taken on the brass testing material. Table 2 shows the data given by the testing machine as well as converted and calculated values used to find our resulting values. Due to the vast number of data points, only the first and last ten data points are shown in Table 2. Table 3 contains two data points that are used to solve the slope which is the Young’s Modulus. Table 4 contains the results and values of the experiment. Table 1. Measurements T [in] T [mm] W [in] W [mm] A [in
2
] A [mm
2
] GL [in] GL [mm] 0.003 0.0762 0.161 4.0894 0.0123 0.3116 2.5 63.5 0.003 0.0762 0.16 4.064 0.0122 0.3097 2.622 66.5988 0.003 0.0762 0.158 4.0132 0.0120 0.3058 2.58 65.532 Avg 0.003 0.076 0.160 4.056 0.012 0.309 2.567 65.210 StdD 0 0 0.0015 0.0388 0.0001 0.0030 0.0620 1.5743 Table 2. Testing Data and Calculations Load [lbF] Disp [in] Disp [mm] t [s] F [N] σ [MPa]
ε [mm/mm]
0.6000 0.0010 0.0254 0.4000 2.6688 8.6360 0.0004 3.0000 0.0030 0.0762 0.6000 13.3440 43.1800 0.0012 4.9000 0.0040 0.1016 0.8000 21.7952 70.5274 0.0016 6.9000 0.0060 0.1524 1.0000 30.6912 99.3141 0.0023 8.9000 0.0070 0.1778 1.2000 39.5872 128.1008 0.0027 10.5000 0.0090 0.2286 1.4000 46.7040 151.1302 0.0035 12.3000 0.0110 0.2794 1.6000 54.7104 177.0382 0.0043 14.2000 0.0120 0.3048 1.8000 63.1616 204.3855 0.0047 15.8000 0.0140 0.3556 2.0000 70.2784 227.4149 0.0055 17.3000 0.0160 0.4064 2.2000 76.9504 249.0049 0.0062 31.7000 0.8860 22.5044 106.6000 141.0016 456.2691 0.3451 31.7000 0.8870 22.5298 106.8000 141.0016 456.2691 0.3455 31.7000 0.8890 22.5806 107.0000 141.0016 456.2691 0.3463 31.8000 0.8900 22.6060 107.2000 141.4464 457.7085 0.3467 31.8000 0.8920 22.6568 107.4000 141.4464 457.7085 0.3474 31.8000 0.8940 22.7076 107.6000 141.4464 457.7085 0.3482 31.8000 0.8960 22.7584 107.8000 141.4464 457.7085 0.3490 31.8000 0.8970 22.7838 108.0000 141.4464 457.7085 0.3494 31.7000 0.8990 22.8346 108.2000 141.0016 456.2691 0.3502 0.0000 0.9010 22.8854 108.4000 0.0000 0.0000 0.3509 Detail Results Table 3. Calculation of Slope (Young’s Modulus) x y Point 1 0.0012 43.1800 Point 2 0.0066 267.7163 Slope 41175.668 Table 4. Calculations UTS [MPa] 458 %EL 35 Young's Modulus [MPa] 41176 Young's Modulus [GPa] 41.18 Yield Strength [MPa] 300 Stress is defined as force applied over a cross-sectional area (see equation 1). Strain is defined as the ratio of the length of deformation and original length (see equation 2). Stress and strain are both calculated in Table 2. Figure 1 describes the relationship between the calculated stress and strain. Figure 2 shows a closer view of the elastic region and the linear approximation of the slop (modulus of elasticity) as well as the yield strength. Figure 1. Stress over Strain for Brass
Figure 2. Yield Strength and Young’s Modulus 𝜎 =
ி
=
ி[ே]
[
మ
]
= 𝑆𝑡𝑟𝑒𝑠𝑠 [𝑀𝑃𝑎]
- Equation 1 𝜀 =
௧
ை ௧
=
௱
బ
= 𝑆𝑡𝑟𝑎𝑖𝑛
- Equation 2 0
100
200
300
400
500
0.00
0.10
0.20
0.30
0.40
Stress [MPa]
Strain [mm/mm]
Brass…
0
100
200
300
400
500
0.000
0.005
0.010
0.015
0.020
Stress [MPa]
Strain [mm/mm]
Brass…
Yield Strength
Slope (Young’s Modulus)
0.2% off set
Executive Summary Department of Mechanical Engineering Aug.24, 2021, Statesboro, Georgia, USA 3 Copyright © 2023 by ASME Reference [1]
“Robert Hooke.” Encyclopædia Britannica
, Encyclopædia Britannica, inc., 24 July 2023, www.britannica.com/biography/Robert-Hooke. [2]
“What Is Stress-Strain Curve?” Xometrys RSS
, Xometry, 30 Mar. 2023, www.xometry.com/resources/3d-
printing/stress-strain-curve/
Your preview ends here
Eager to read complete document? Join bartleby learn and gain access to the full version
- Access to all documents
- Unlimited textbook solutions
- 24/7 expert homework help
Related Documents
Related Questions
Figure 1 shows the tensile testing results for different materials. All specimens have an initial
diameter of 12 mm and an initial gauge length of 50 mm.
300
250
Low carbon steel
Network polymer
200
Crystalline polymer
150
Amorphous polymer
100
50
5
10
15
20
25
30
Strain (%)
Figure 1: Stress-strain curve
b. Determine the following parameters for each material:
• the tensile strength
the 0.2% offset yield strength
the modulus of elasticity
• the ductility
Stress (MPa)
LO
arrow_forward
1. A tensile test was conducted on a metal "505" specimen and the following stress-strain curves
were generated, both curves generated from the same set of data. Use the graphs to fill in the
mechanical properties of the material tested in the box below. Don't forget units!
Stress vs Strain
Stress, psi
Stress, psi
80000
70000
60000
50000
40000
30000
20000
10000
0
0.00
80000
70000
60000
50000
40000
30000
20000
10000
0.02
0
0.000 0.002
0.04
0.004
0.06
0.006
0.08
0.10
Strain
Stress vs Strain
0.008
0.12
Elastic Modulus, E:
0.2% Offset Yield Strength, oo:
Tensile Strength, ou:
Breaking Strength, of:
% Elongation:
0.14
0.010 0.012 0.014
Strain
0.16
0.18
0.016 0.018
0.20
0.020
arrow_forward
You have been given the following test sample data following mechanical testing of 15
test pieces of a modified Alumina.
What is the Weibull modulus of this material?
Would you advise the use of this material over one with a Weibull Modulus of 19.6 and a
mean failure stress of 270 MPa, if you anticipate that the peak stress on the material
could be 255 MPa?
Sample
1
2
3
4
5
6
7
8
9
10
11
12
13
14
15
Select one or more:
a. 185
b. No
Yes
□d. 49
□e. 28.6
3.7
Failure Stress (MPa)
297
293
270
300
g. 22.8
260
296
265
295
280
288
263
290
298
275
arrow_forward
A tensile test was performed on a metal specimen with a diameter of
1/2 inch and a gage length (the length over which the elongation is meas-
ured) of 4 inches. The data were plotted on a load-displacement graph,
P vs. AL. A best-fit line was drawn through the points, and the slope of
the straight-line portion was calculated to be P/AL = 1392 kips/in. What
is the modulus of elasticity?
BI
arrow_forward
Given the following data for five different materials answer parts A B C D E & F with an explanation
arrow_forward
A high-impulse universal testing machine is being used to determine the Young's Modulus of a rectangular solid specimen (l = 20 cm, t = 1.5 cm, w = 2 cm). The machine produces 35,000 Ns that causes the impact force of compression resulted to a 1 mm deformation in the length of the specimen in 0.05 s. Determine the Young's modulus of the specimen expressed in MPa. Round off your answer to the nearest whole number
arrow_forward
i need the answer quickly
arrow_forward
Stress Strain Diagram
The Data shown in the table have been obtained from a tensile test conducted on
a high-strength steel. The test specimen had a diameter of 0.505 inch and a gage
length of 2.00 inch. Using software. plot the Stress-Strain Diagram for this steel
and determine its:
A= TTdT(050s
A
%3D
1. Proportional Limit,
2. Modulus of Elasticity,
3. Yield Strength (SY) at 0.2% Offset,
4. Ultimate Strength (Su),
5. Percent Elongation in 2.00 inch,
6. Percent Reduction in Area,
7. Present the results (for Steps 1-6) in a highly organized table.
e Altac ie sheet (as problelle
4
A = 0.2.002
BEOINNING of the effort
Elongation
(in)
Elongation
(In)
Load
Load
#:
#3
(Ib)
(Ib)
1
0.0170
15
12,300
0.0004
1,500
16
12,200
0.0200
0.0010
3.
3,100
17
12,000
0.0275
0.0016
4,700
18
13,000
0.0335
5.
6,300
0.0022
19
15,000
0.0400
0.0026
6.
8,000
20
16,200
0.055
0.0032
9,500
21
17,500
0.0680
0.0035
8.
11,000
22
18,800
0.1080
0.0041
11,800
23
19,600
0.1515
0.0051
24
20,100
0.2010
10
12,300
0.0071
25…
arrow_forward
The following data was obtained as a result of tensile testing of a standard 0.505 inch diameter test specimen of magnesium. After fracture, the gage length is 2.245 inch and the diameter is 0.466 inch.
a). Calculate the engineering stress and strain values to fill in the blank boxes and plot the data.
Load(lb)
Gage Length (in)
Stress (kpsi)
Strain
0
2
1000
2.00154
2000
2.00308
3000
2.00462
4000
2.00615
5000
2.00769
5500
2.014
6000
2.05
6200 (max)
2.13
6000 (fracture)
2.255
b). Calculate the modulus of elasticity
c). If another identical sample of the same material is pulled only to 6000 pounds and is unloaded from there, determine the gage length of the sample after unloading.
arrow_forward
6. The following engineering stress-strain data were obtained for 0.2% C plain
carbon steel.
(a) Plot the engineering stress-strain curve
(b) Determine the ultimate tensile strength for the alloy
(c) Determine the percent elongation at fracture
(d) Plot the true stress-strain curve
Engineering strain, in./in.
Engineering stress, ksi
30
0.001
55
0.002
60
0.005
68
0.01
72
0.02
74
0.04
75
0.06
76
0.08
75
0.1
73
0.12
69
0.14
65
0.16
56
0.18
51
0.19(fracture)
arrow_forward
The following stress-strain curve was prepared based on a tensile test of a specimen that had a circular cross-section. The gage
diameter of the specimen was 0.25 inches and the gage length was 4 inches. The stress scale of the stress-strain diagram is
given with the factor a = 10 ksi. Estimate:
(a) The modulus of elasticity.
(b) The ultimate strength.
(c) The yield strength (0.2% offset).
(d) The percent elongation at fracture.
2013 Michael Swanbom
STRESS VS. STRAIN
BY NC SA
7a
bat
Sat
2at
at
0.05
STRAIN
0.01
0.04
0.06
0.08
0.02
0.03
0.07
0.09
STRESS
arrow_forward
Read and Solve carefully please Write clearly and Box the Final answer Express your answer to 3 Significant figures and include appropriate units.
arrow_forward
I just can't find The percent elongation at fracture.
arrow_forward
The engineering stress-strain curve below was obtained for a
precipitation hardened Aluminum alloy.
What is the approximate Yield Strength for this alloy in psi?
Engineering Stress Based on Original Area (psi)
50,000
45,000
40,000
35,000
30,000
25,000
20,000
15,000
10,000
5,000
0
O
0.02
0.04
0.06
Aluminum 6061-T6
0.08
0.1
0.12
Engineering Strain (in/in)
0.14
X
0.16
0.18
arrow_forward
A 11 in. inner diameter, 0.35 " wall thickness pipe is under a pressure of 2.5 ksi where strain gages installed along axial and circumferential directions register strains of 180 and 900 micro-strains (x10^-6), respectively.
A) What is the Poisson's Ratio of this material and it's Elastic Modulus?
B) In a uniaxial test, the pipe's material is observed to yield at a longitudinal strain of 0.1 in/in. Assuming a factor of safety of 2, the pipe can withstand impact energy of _______ lb - in per foot without suffering permanent deformation.
C) If the pipe is depressurized and then subjected to a torque of 50 lblb - ft.ft., it will experience a shear strain of ________ rad.
arrow_forward
A 11 in. inner diameter, 0.35 " wall thickness pipe is under a pressure of 2.5 ksi where strain gages installed along axial and circumferential directions register strains of 180 and 900 micro-strains (x10^-6), respectively.
A) What is the Poisson's Ratio of this material and it's Elastic Modulus?
B) In a uniaxial test, the pipe's material is observed to yield at a longitudinal strain of 0.1 in/in.in/in. Assuming a factor of safety of 2, the pipe can withstand impact energy of _______ lblb - in.in. per foot without suffering permanent deformation.
C) If the pipe is depressurized and then subjected to a torque of 50 lblb - ft.ft., it will experience a shear strain of ________ rad.
arrow_forward
Flag question
You have been given the following test sample data following mechanical testing of 15 test pieces of a modified Alumina.
What is the Weibull modulus of this material?
Would you advise the use of this material over one with a Weibull Modulus of 19.6 and a mean failure stress of 270 MPa, if you
anticipate that the peak stress on the material could be 255 MPa?
Sample
1
2
3
4
5
6
7
8
9
10
11
12
13
14
15
Select one or more:
Failure Stress (MPa)
297
293
270
300
260
286
265
295
4
293
280
288
263
290
298
275
arrow_forward
SEE MORE QUESTIONS
Recommended textbooks for you
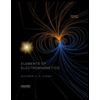
Elements Of Electromagnetics
Mechanical Engineering
ISBN:9780190698614
Author:Sadiku, Matthew N. O.
Publisher:Oxford University Press
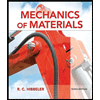
Mechanics of Materials (10th Edition)
Mechanical Engineering
ISBN:9780134319650
Author:Russell C. Hibbeler
Publisher:PEARSON
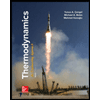
Thermodynamics: An Engineering Approach
Mechanical Engineering
ISBN:9781259822674
Author:Yunus A. Cengel Dr., Michael A. Boles
Publisher:McGraw-Hill Education
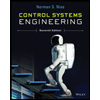
Control Systems Engineering
Mechanical Engineering
ISBN:9781118170519
Author:Norman S. Nise
Publisher:WILEY
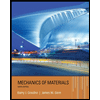
Mechanics of Materials (MindTap Course List)
Mechanical Engineering
ISBN:9781337093347
Author:Barry J. Goodno, James M. Gere
Publisher:Cengage Learning
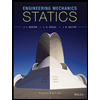
Engineering Mechanics: Statics
Mechanical Engineering
ISBN:9781118807330
Author:James L. Meriam, L. G. Kraige, J. N. Bolton
Publisher:WILEY
Related Questions
- Figure 1 shows the tensile testing results for different materials. All specimens have an initial diameter of 12 mm and an initial gauge length of 50 mm. 300 250 Low carbon steel Network polymer 200 Crystalline polymer 150 Amorphous polymer 100 50 5 10 15 20 25 30 Strain (%) Figure 1: Stress-strain curve b. Determine the following parameters for each material: • the tensile strength the 0.2% offset yield strength the modulus of elasticity • the ductility Stress (MPa) LOarrow_forward1. A tensile test was conducted on a metal "505" specimen and the following stress-strain curves were generated, both curves generated from the same set of data. Use the graphs to fill in the mechanical properties of the material tested in the box below. Don't forget units! Stress vs Strain Stress, psi Stress, psi 80000 70000 60000 50000 40000 30000 20000 10000 0 0.00 80000 70000 60000 50000 40000 30000 20000 10000 0.02 0 0.000 0.002 0.04 0.004 0.06 0.006 0.08 0.10 Strain Stress vs Strain 0.008 0.12 Elastic Modulus, E: 0.2% Offset Yield Strength, oo: Tensile Strength, ou: Breaking Strength, of: % Elongation: 0.14 0.010 0.012 0.014 Strain 0.16 0.18 0.016 0.018 0.20 0.020arrow_forwardYou have been given the following test sample data following mechanical testing of 15 test pieces of a modified Alumina. What is the Weibull modulus of this material? Would you advise the use of this material over one with a Weibull Modulus of 19.6 and a mean failure stress of 270 MPa, if you anticipate that the peak stress on the material could be 255 MPa? Sample 1 2 3 4 5 6 7 8 9 10 11 12 13 14 15 Select one or more: a. 185 b. No Yes □d. 49 □e. 28.6 3.7 Failure Stress (MPa) 297 293 270 300 g. 22.8 260 296 265 295 280 288 263 290 298 275arrow_forward
- A tensile test was performed on a metal specimen with a diameter of 1/2 inch and a gage length (the length over which the elongation is meas- ured) of 4 inches. The data were plotted on a load-displacement graph, P vs. AL. A best-fit line was drawn through the points, and the slope of the straight-line portion was calculated to be P/AL = 1392 kips/in. What is the modulus of elasticity? BIarrow_forwardGiven the following data for five different materials answer parts A B C D E & F with an explanationarrow_forwardA high-impulse universal testing machine is being used to determine the Young's Modulus of a rectangular solid specimen (l = 20 cm, t = 1.5 cm, w = 2 cm). The machine produces 35,000 Ns that causes the impact force of compression resulted to a 1 mm deformation in the length of the specimen in 0.05 s. Determine the Young's modulus of the specimen expressed in MPa. Round off your answer to the nearest whole numberarrow_forward
- i need the answer quicklyarrow_forwardStress Strain Diagram The Data shown in the table have been obtained from a tensile test conducted on a high-strength steel. The test specimen had a diameter of 0.505 inch and a gage length of 2.00 inch. Using software. plot the Stress-Strain Diagram for this steel and determine its: A= TTdT(050s A %3D 1. Proportional Limit, 2. Modulus of Elasticity, 3. Yield Strength (SY) at 0.2% Offset, 4. Ultimate Strength (Su), 5. Percent Elongation in 2.00 inch, 6. Percent Reduction in Area, 7. Present the results (for Steps 1-6) in a highly organized table. e Altac ie sheet (as problelle 4 A = 0.2.002 BEOINNING of the effort Elongation (in) Elongation (In) Load Load #: #3 (Ib) (Ib) 1 0.0170 15 12,300 0.0004 1,500 16 12,200 0.0200 0.0010 3. 3,100 17 12,000 0.0275 0.0016 4,700 18 13,000 0.0335 5. 6,300 0.0022 19 15,000 0.0400 0.0026 6. 8,000 20 16,200 0.055 0.0032 9,500 21 17,500 0.0680 0.0035 8. 11,000 22 18,800 0.1080 0.0041 11,800 23 19,600 0.1515 0.0051 24 20,100 0.2010 10 12,300 0.0071 25…arrow_forwardThe following data was obtained as a result of tensile testing of a standard 0.505 inch diameter test specimen of magnesium. After fracture, the gage length is 2.245 inch and the diameter is 0.466 inch. a). Calculate the engineering stress and strain values to fill in the blank boxes and plot the data. Load(lb) Gage Length (in) Stress (kpsi) Strain 0 2 1000 2.00154 2000 2.00308 3000 2.00462 4000 2.00615 5000 2.00769 5500 2.014 6000 2.05 6200 (max) 2.13 6000 (fracture) 2.255 b). Calculate the modulus of elasticity c). If another identical sample of the same material is pulled only to 6000 pounds and is unloaded from there, determine the gage length of the sample after unloading.arrow_forward
- 6. The following engineering stress-strain data were obtained for 0.2% C plain carbon steel. (a) Plot the engineering stress-strain curve (b) Determine the ultimate tensile strength for the alloy (c) Determine the percent elongation at fracture (d) Plot the true stress-strain curve Engineering strain, in./in. Engineering stress, ksi 30 0.001 55 0.002 60 0.005 68 0.01 72 0.02 74 0.04 75 0.06 76 0.08 75 0.1 73 0.12 69 0.14 65 0.16 56 0.18 51 0.19(fracture)arrow_forwardThe following stress-strain curve was prepared based on a tensile test of a specimen that had a circular cross-section. The gage diameter of the specimen was 0.25 inches and the gage length was 4 inches. The stress scale of the stress-strain diagram is given with the factor a = 10 ksi. Estimate: (a) The modulus of elasticity. (b) The ultimate strength. (c) The yield strength (0.2% offset). (d) The percent elongation at fracture. 2013 Michael Swanbom STRESS VS. STRAIN BY NC SA 7a bat Sat 2at at 0.05 STRAIN 0.01 0.04 0.06 0.08 0.02 0.03 0.07 0.09 STRESSarrow_forwardRead and Solve carefully please Write clearly and Box the Final answer Express your answer to 3 Significant figures and include appropriate units.arrow_forward
arrow_back_ios
SEE MORE QUESTIONS
arrow_forward_ios
Recommended textbooks for you
- Elements Of ElectromagneticsMechanical EngineeringISBN:9780190698614Author:Sadiku, Matthew N. O.Publisher:Oxford University PressMechanics of Materials (10th Edition)Mechanical EngineeringISBN:9780134319650Author:Russell C. HibbelerPublisher:PEARSONThermodynamics: An Engineering ApproachMechanical EngineeringISBN:9781259822674Author:Yunus A. Cengel Dr., Michael A. BolesPublisher:McGraw-Hill Education
- Control Systems EngineeringMechanical EngineeringISBN:9781118170519Author:Norman S. NisePublisher:WILEYMechanics of Materials (MindTap Course List)Mechanical EngineeringISBN:9781337093347Author:Barry J. Goodno, James M. GerePublisher:Cengage LearningEngineering Mechanics: StaticsMechanical EngineeringISBN:9781118807330Author:James L. Meriam, L. G. Kraige, J. N. BoltonPublisher:WILEY
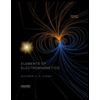
Elements Of Electromagnetics
Mechanical Engineering
ISBN:9780190698614
Author:Sadiku, Matthew N. O.
Publisher:Oxford University Press
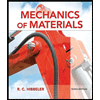
Mechanics of Materials (10th Edition)
Mechanical Engineering
ISBN:9780134319650
Author:Russell C. Hibbeler
Publisher:PEARSON
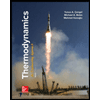
Thermodynamics: An Engineering Approach
Mechanical Engineering
ISBN:9781259822674
Author:Yunus A. Cengel Dr., Michael A. Boles
Publisher:McGraw-Hill Education
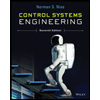
Control Systems Engineering
Mechanical Engineering
ISBN:9781118170519
Author:Norman S. Nise
Publisher:WILEY
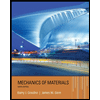
Mechanics of Materials (MindTap Course List)
Mechanical Engineering
ISBN:9781337093347
Author:Barry J. Goodno, James M. Gere
Publisher:Cengage Learning
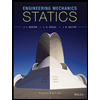
Engineering Mechanics: Statics
Mechanical Engineering
ISBN:9781118807330
Author:James L. Meriam, L. G. Kraige, J. N. Bolton
Publisher:WILEY