MEC511_Lab2
pdf
keyboard_arrow_up
School
Toronto Metropolitan University *
*We aren’t endorsed by this school
Course
511
Subject
Mechanical Engineering
Date
Feb 20, 2024
Type
Pages
11
Uploaded by EarlGrasshopperPerson4
1
Course Title:
Fluids & Thermodynamics
Course Number:
MEC 511
Semester/Year:
Fall 2023
Instructor:
Dr. Jun Cao
Assignment/Lab Number:
2
Assignment/Lab Title:
The Venturi Flow Meter
Submission Date:
Oct 20, 2023
Due Date:
Oct 20, 2023
LAST NAME
FIRST NAME
Student Number
Section
Signature
Table of Contents
Summary:
3
2
Introduction:
4
Apparatus
5
Procedure
6
Results
6
Discussion
8
Conclusion
8
Appendix
9
References
10
3
Summary
:
The purpose of the lab was to study incompressible flow through a Venturi flow meter. Initially, when we
closed the valve, all seven piezometers displayed identical readings. Upon opening the water valve, the
piezometer levels underwent significant changes before stabilizing at varying heights. Once steady states
were reached, each piezometer displayed distinct height readings. We repeated the procedure with a
different volume flow rate and calculated theoretical volume flow rates and Venturi discharge coefficients
based on these heights. The analysis showed that both experiments differed from the theoretical outcomes
predicted by Bernoulli's equation. This discrepancy can be attributed to the limitations of Bernoulli's
equation, which assumes steady, incompressible, and frictionless flow. Our experiments illustrated that
real-world fluids like water exhibit inherent viscosity, which impacts our results. In summary, Bernoulli's
equation is only suitable under ideal conditions characterized by constant flow, incompressibility, and
non-viscous fluids.
Your preview ends here
Eager to read complete document? Join bartleby learn and gain access to the full version
- Access to all documents
- Unlimited textbook solutions
- 24/7 expert homework help
4
Introduction:
The purpose of this lab is to study the volume flow rate of pipes by observing Bernoulli's principle in a
Venturi flow meter. When observing
Figure 1,
we see that the diameter D
1
is reduced to D
2
which causes
a decrease in pressure and an increase in velocity. From this, using the differential pressure (P
1
-P
2
) we can
determine the volume flow rate,
Q.
Using Figure 2 we derive Bernoulli's equation to be:
(1)
?
1
𝜸
+
?
1
2
2𝑔
+ 𝑧
1
=
?
2
𝜸
+
?
2
2
2𝑔
+ 𝑧
2
5
V
1
and V
2
are the average velocities of sections 1 & 2, therefore applying the continuity equation for
incompressible flow we get:
?
1
= ?
2
(2)
?
1
𝐴
1
= ?
2
𝐴
2
Now using equations (1) and (2) we can derive an equation for velocity V
2
which is:
(3)
?
2
=
2𝑔[(?
1
−?
2
)/𝜸+(𝑧
1
−𝑧
2
)]
(1−(𝐴
2
/𝐴
1
)
2
)
V
2
is the theoretical velocity at the throat of the Venturi meter but the actual velocity will be slightly lower
so we use the equation:
(4)
?
2𝑎
= ?
?
2𝑔[(?
1
−?
2
)/𝜸+(𝑧
1
−𝑧
2
)]
(1−(𝐴
2
/𝐴
1
)
2
)
C
v
is the discharge coefficient. Since the cross section of the Venturi flow meter is not round, the
Reynolds number is based on the hydraulic diameter which is given as the equation:
(5)
?
𝐻
=
4𝐴
1
?
?𝑒𝑡
6
Apparatus:
●
Water tank
●
Venturi Flow Meter
●
7 piezometers
●
Blue dye (for visibility)
●
Outlet valve
Procedure:
1.
Adjusted the flow through the Venturi to obtain the maximum difference between the manometer
readings at the upstream location and at the Venturi throat.
2.
Recorded all of the manometer readings.
3.
Measured the actual volume flow rate (Qₐ) of the water. Made at least two measurements and
took the average of the results.
4.
Adjusted the flow until the difference between upstream manometer reading and the throat
manometer reading is one half of the full flow value.
5.
Repeat for the lower flow rate
Results:
T = 10
o
C
Your preview ends here
Eager to read complete document? Join bartleby learn and gain access to the full version
- Access to all documents
- Unlimited textbook solutions
- 24/7 expert homework help
7
Table 1
- Sample experimental data at a flow rate of 0.259 and 0.157 liters per second
Piezometer
A
B
C
D (throat)
E
F
G
Piezometric Height (m)
Q = 0.259
0.496
0.482
0.448
0.344
0.407
0.429
0.438
Piezometric Height (m)
Q = 0.157
0.516
0.513
0.498
0.456
0.481
0.490
0.494
Table 2
- Theoretical calculations given different flow rates.
(m/s)
?
?
(L/s)
?
?
Re
?
?
Q = 0.259 L/s
1.8835
0.3038
10,450.97
0.853
Q = 0.157 L/s
1.183
0.1908
6564.82
0.823
Table 3
- Theoretical values of each venturi meter region (Q = 0.259).
Region
A
B
C
D
(throat)
E
F
G
V (m/s)
0.6423
0.8030
1.070
1.606
1.070
0.803
0.6423
Piezometric
Height (m)
0.497
0.484
0.458
0.386
0.458
0.484
0.496
Cross Section
Height (m)
0.03175
0.0254
0.01905
0.0127
0.01905
0.0254
0.03175
Area (
)
?
2
4. 032?10
−4
3. 226?10
−4
2. 419?10
−4
1. 613?10
−4
2. 419?10
−4
3. 226?10
−4
4. 032?10
−4
Table 4
- Theoretical values of each venturi meter region (Q = 0.157).
Region
A
B
C
D
(throat)
E
F
G
V (m/s)
0.3894
0.4870
0.6490
0.9730
0.6490
0.4870
0.3894
Piezometric
Height (m)
0.516
0.512
0.502
0.475
0.502
0.512
0.516
8
Cross Section
Height (m)
0.03175
0.0254
0.01905
0.0127
0.01905
0.0254
0.03175
Area (
)
?
2
4. 032?10
−4
3. 226?10
−4
2. 419?10
−4
1. 613?10
−4
2. 419?10
−4
3. 226?10
−4
4. 032?10
−4
Graph 1
- Theoretical vs Actual Height (Q = 0.259)
Graph 2
- Theoretical vs Actual Height (Q = 0.157)
9
Discussion:
1.
Why is the actual fluid velocity different from the theoretical velocity predicted by
Bernoulli’s equation?
The actual fluid velocity is different from the theoretical velocity predicted by Beronulli’s equation due to
factors such as the viscous shear stress on the walls and turbulent mixing which causes energy loss. As
well, the actual fluid velocity depends on the discharge coefficient of the venturi flow meter. Bernoulli’s
equation assumes that there are no head losses in the venturi flow meter which is impossible in real life
because there will always be a small amount of head losses. This discrepancy causes the values of the
theoretical and experimental velocities to deviate.
2.
Is the discharge coefficient within the expected range? If not, discuss the possible reasons
for the discrepancy.
With a Reynolds number of 10450.97 the expected range for the discharge coefficient is 0.94-0.98. Our
experimental results show a discharge coefficient of 0.853 and 0.823. This result is noticeably different
from the expected range.
A possible reason for this can be due to incorrect manufacturing of the Venturi flow meter as any
imperfections within the device could cause more frictional force against the fluid flow. This will
therefore decrease the actual velocity of the fluid, and a decreased actual velocity would result in a
decreased discharge coefficient.
3.
According to your results, where are the head losses the greatest in the venturi flow meter?
The greatest head losses in the Venturi flow meter are seen at the throat, piezometer D, where the pressure
is lowest. The effect of the throat can be easily seen at piezometer G, where the height of the water has
dropped significantly in comparison to piezometer A. This can be explained by the fact that the throat has
the highest amount of shearing stress in the Venturi flow meter due to its smaller cross sectional area.
Conclusion:
This lab focused on incompressible flow through a Venturi meter. Using Bernoulli’s equation, the
theoretical volume flow rate for
Q = 0.259 L/s
and
Q = 0.157 L/s
were calculated as
0.3038 L/s
and
0.1908 L/s
respectively. The Venturi discharge coefficients for
Q = 0.259 L/s
and Q =
0.157 L/s
were
calculated as
0.823
and
0.158
respectively. The theoretical Piezometric heights were also calculated and
compared with the heights found during the experiment.
Your preview ends here
Eager to read complete document? Join bartleby learn and gain access to the full version
- Access to all documents
- Unlimited textbook solutions
- 24/7 expert homework help
10
Appendices:
Bernoulli’s equation
?
1
γ
+
?
2
1
γ
+ 𝑧
1
=
?
2
γ
+
?
2
2
γ
+ 𝑧
2
Actual Velocity
?
2𝑎
= ?
2
?
?
= ?
?
2𝑔[
(?
1
− ?
2
) γ
+ (𝑧
1
−𝑧
2
) ]
[ 1 −( 𝐴
1
𝐴
2
)
2
]
Hydraulic Diameter
?
𝐻
=
4𝐴
1
?
?𝑒𝑡
Reynold’s Number
?
?
=
ρ?
1
?
𝐻
µ
Calculations for Table 2
?
?
=
2𝑔[
(?
1
− ?
2
) γ
+ (𝑧
1
−𝑧
2
) ]
[ 1 −( 𝐴
1
𝐴
2
)
2
]
?
?
= 𝐴
?
?
?
?
𝐴
=
?
?
𝐴
?
𝐴
𝐴
?
𝐻
=
4𝐴
𝐴
2(12.7?10
−3
)+2(31.75?10
−3
)
?𝑒 =
?
𝐻
?
𝐴
ρ
ℎ20
µ
ℎ20
?
?
=
?
??𝑝
?
?𝑎?𝑐
11
Calculations for Table 3 & 4
? = ?/𝐴
𝐴 = (ℎ)(12. 7?10
−3
)
ℎ
2
=
(?
2
)
2
(1 − 𝐴
2
𝐴
1
)
2
2𝑔
References:
1.
D. F. Young, T. H. Okiishi, J. I. Hochstein, A. L. Gerhart, and B. R. Munson,
Young, Munson and
Okiishi's a brief introduction to Fluid Mechanics
. Wiley, 2021.
Related Documents
Related Questions
please read everything properly... Take 3 4 5 hrs but solve full accurate drawing on bond paper don't use chat gpt etc okk
arrow_forward
Mech. Engg. Dept.
4th year 2022-2023
Solar Energy
Spring course MEC364
Dr. Mahmoud U. Jasim
Review/Recap Sheet
Q1- Answer with true or false and rewrite the false statements completely in
correct form, otherwise no mark will be put on the false statements.
1
2
To represent a location on earth surface you need to define its altitude and longitude
angles.
3
Solar zenith and solar incidence angles have the same value for horizontal surface.
At sunset time the value of solar altitude angle is maximum.
4
The angle which represents the inclination of a given surface is the zenith angle
5
6
7
8
When the absolute value of sun-wall azimuth angle exceeds 90' this means that the sun
rays are reaching the receiving plane.
The solar irradiance and the solar irradiation have the same physical meaning.
In the case of clear sky weather, the beam solar irradiation on a horizontal surface is less
than the diffused irradiation.
The total solar radiation received by a tilted surface is the same as that…
arrow_forward
Please answer the 4th question
arrow_forward
Case Study – The New Engineer
Jeff was just hired by GSI, Inc. to be their Environmental and Safety Coordinator. This is Jeff's first position after completing his engineering degree. He had taken a course in safety engineering as part of his studies and felt confident that he could handle the job.
Management at GSI, Inc. has assured him that they are committed to maintaining a safe workplace. They have never had an individual dedicated to this task full-time. They will implement his recommendations if he can justify them.
As Jeff begins to get familiar with the operations, he spends considerable time on the production floor. He notices workers clean their tools before break with a liquid from an unmarked 55-gallon drum. They also use this liquid to clean residue from their skin. They use paper towels to dry their tools and hands, throw these towels in the trash, and head to the break room for a snack and/or smoke.
In talking with the workers, Jeff learns of some of…
arrow_forward
Case Study – The New Engineer
Jeff was just hired by GSI, Inc. to be their Environmental and Safety Coordinator. This is Jeff's first position after completing his engineering degree. He had taken a course in safety engineering as part of his studies and felt confident that he could handle the job.
Management at GSI, Inc. has assured him that they are committed to maintaining a safe workplace. They have never had an individual dedicated to this task full-time. They will implement his recommendations if he can justify them.
As Jeff begins to get familiar with the operations, he spends considerable time on the production floor. He notices workers clean their tools before break with a liquid from an unmarked 55-gallon drum. They also use this liquid to clean residue from their skin. They use paper towels to dry their tools and hands, throw these towels in the trash, and head to the break room for a snack and/or smoke.
In talking with the workers, Jeff learns of some of…
arrow_forward
The answer from Bartleby is missing/blank. Can someone help answer it please and credit this question if possible since it would have been included/explained?
Thank you
Chapter 50 multiple Choice #5 what is the cause of an extremely hard brake pedal
arrow_forward
4
arrow_forward
Please show work in a handwritten format.
Don't use chatgpt.
Mechanics of materials/design.
arrow_forward
Task 1
You are employed as a mechanical engineer within an unnamed research center, specializing in the
development of innovative air conditioning systems. Your division is tasked with providing computer-based
modeling and design solutions using computational fluid dynamics through ANSYS software. Your primary
responsibilities involve the analysis of horizontal channel dynamics to meet specific criteria. Under the
guidance of your immediate supervisor, you have been assigned unique responsibilities within an ongoing
project. As a member of the research team, your role includes constructing an appropriate model and
executing a sequence of simulation iterations to explore and enhance channel performance. Figure 1
provides a visualization of the horizontal channel under consideration. Consider 2D, incompressible, steady
flow in a horizontal channel at a Reynolds number of 150. The schematic below illustrates the channel flow,
not drawn to scale. For simplicity, neglect gravity. The…
arrow_forward
I need help solving this problem.
arrow_forward
The first photo is the question, where the 2nd shows some problem solving strategies
arrow_forward
Subject: mechanical engi
arrow_forward
Part II.
Longer problem focused on problem solving multiple steps. This problem will be graded based
on process, clarity of work, and correct answer and units.
a. A spring is stretched, with a force, F = 442 lbf, along the outside of a pipe as shown with a = 53°
and ẞ 69° and the coordinates of the force are (15,37,-71 ). How far does the spring stretch if
the spring constant is k=67 lb/in? Hint: The force that stretches the spring is the projected force
along the pipe
F
(x, y, z)
arrow_forward
The University of Oklahoma School of Civil Engineering and Environmental Science
spring 2024 Semester
Problem 3 (30 pts.)
ENGR 2411 Applied Engineering Statics
Prerequisite Quiz
Page 4 of a
Your friend Dave loves hanging on the OU banner poles attached to the light poles on campus,
this is despite your strong disapproval of their behavior. As an engineering student you are super
concerned about the moment acting at the base of the light pole. What if Dave breaks the light
pole! Calculate the moment acting about the base of the light pole (point O) when Dave is angled
45° from the horizontal banner pole. Dave weighs 120 lbs. Assume the force exerted by Dave on
the banner pole is aligned with their arm that is holding onto the pole (ie. at 45°).
B 15ft
tf8
Disclaimer: Dave is fictional and does
not represent any actual person.
arrow_forward
LESSON: AUTODESK AUTOCAD
Choose from the choices:
arrow_forward
Please give me the answers for this i been looking at this for a hour and my head hurts
arrow_forward
I need parts 8, 9, and 10 answered. Number 1 is an example of how it should be answered.
NOTE: Read the instructions, no where does it say any drawing is required. It is really frustrating when I wait all this time for an answer to a question and some tutor does even read the instructions and just declines it...its ridicilous.
arrow_forward
SEE MORE QUESTIONS
Recommended textbooks for you
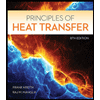
Principles of Heat Transfer (Activate Learning wi...
Mechanical Engineering
ISBN:9781305387102
Author:Kreith, Frank; Manglik, Raj M.
Publisher:Cengage Learning
Related Questions
- please read everything properly... Take 3 4 5 hrs but solve full accurate drawing on bond paper don't use chat gpt etc okkarrow_forwardMech. Engg. Dept. 4th year 2022-2023 Solar Energy Spring course MEC364 Dr. Mahmoud U. Jasim Review/Recap Sheet Q1- Answer with true or false and rewrite the false statements completely in correct form, otherwise no mark will be put on the false statements. 1 2 To represent a location on earth surface you need to define its altitude and longitude angles. 3 Solar zenith and solar incidence angles have the same value for horizontal surface. At sunset time the value of solar altitude angle is maximum. 4 The angle which represents the inclination of a given surface is the zenith angle 5 6 7 8 When the absolute value of sun-wall azimuth angle exceeds 90' this means that the sun rays are reaching the receiving plane. The solar irradiance and the solar irradiation have the same physical meaning. In the case of clear sky weather, the beam solar irradiation on a horizontal surface is less than the diffused irradiation. The total solar radiation received by a tilted surface is the same as that…arrow_forwardPlease answer the 4th questionarrow_forward
- Case Study – The New Engineer Jeff was just hired by GSI, Inc. to be their Environmental and Safety Coordinator. This is Jeff's first position after completing his engineering degree. He had taken a course in safety engineering as part of his studies and felt confident that he could handle the job. Management at GSI, Inc. has assured him that they are committed to maintaining a safe workplace. They have never had an individual dedicated to this task full-time. They will implement his recommendations if he can justify them. As Jeff begins to get familiar with the operations, he spends considerable time on the production floor. He notices workers clean their tools before break with a liquid from an unmarked 55-gallon drum. They also use this liquid to clean residue from their skin. They use paper towels to dry their tools and hands, throw these towels in the trash, and head to the break room for a snack and/or smoke. In talking with the workers, Jeff learns of some of…arrow_forwardCase Study – The New Engineer Jeff was just hired by GSI, Inc. to be their Environmental and Safety Coordinator. This is Jeff's first position after completing his engineering degree. He had taken a course in safety engineering as part of his studies and felt confident that he could handle the job. Management at GSI, Inc. has assured him that they are committed to maintaining a safe workplace. They have never had an individual dedicated to this task full-time. They will implement his recommendations if he can justify them. As Jeff begins to get familiar with the operations, he spends considerable time on the production floor. He notices workers clean their tools before break with a liquid from an unmarked 55-gallon drum. They also use this liquid to clean residue from their skin. They use paper towels to dry their tools and hands, throw these towels in the trash, and head to the break room for a snack and/or smoke. In talking with the workers, Jeff learns of some of…arrow_forwardThe answer from Bartleby is missing/blank. Can someone help answer it please and credit this question if possible since it would have been included/explained? Thank you Chapter 50 multiple Choice #5 what is the cause of an extremely hard brake pedalarrow_forward
- 4arrow_forwardPlease show work in a handwritten format. Don't use chatgpt. Mechanics of materials/design.arrow_forwardTask 1 You are employed as a mechanical engineer within an unnamed research center, specializing in the development of innovative air conditioning systems. Your division is tasked with providing computer-based modeling and design solutions using computational fluid dynamics through ANSYS software. Your primary responsibilities involve the analysis of horizontal channel dynamics to meet specific criteria. Under the guidance of your immediate supervisor, you have been assigned unique responsibilities within an ongoing project. As a member of the research team, your role includes constructing an appropriate model and executing a sequence of simulation iterations to explore and enhance channel performance. Figure 1 provides a visualization of the horizontal channel under consideration. Consider 2D, incompressible, steady flow in a horizontal channel at a Reynolds number of 150. The schematic below illustrates the channel flow, not drawn to scale. For simplicity, neglect gravity. The…arrow_forward
arrow_back_ios
SEE MORE QUESTIONS
arrow_forward_ios
Recommended textbooks for you
- Principles of Heat Transfer (Activate Learning wi...Mechanical EngineeringISBN:9781305387102Author:Kreith, Frank; Manglik, Raj M.Publisher:Cengage Learning
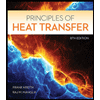
Principles of Heat Transfer (Activate Learning wi...
Mechanical Engineering
ISBN:9781305387102
Author:Kreith, Frank; Manglik, Raj M.
Publisher:Cengage Learning