Problem 1 (20 Points) Davison Electronics manufactures three LED television monitors, identified as Model A, Model B, and Model C. Davison Electronics four manufacturing plants. Each model has its lowest possible production cost when produced at Plant 1. However, Plant 1 does not have the capacity to handle the total production of all three models. As a result, at least some of the production must be routed to the other manufacturing plants. The following table shows the minimum production requirements for next month, the plant capacities in units per month, and the production cost per unit at each plant: Production Cost per Unit Minimum Model Production Plant 1 Plant 2 Plant 3 Plant 4 Requirements A $25 $28 $37 $34 48,000 B $26 $35 $36 $41 75,000 C $20 $31 $26 $23 60,000 65,000 50,000 32,000 43,000 Production Capacity Davison's objective is to determine the cost-minimizing production plan. [We have formulated the problem and solved the problem using Excel's solver in Homework 2. If you want to, you can also use my solution of Homework 2 available in the folder "Homework Solution" after I receive the solutions from all the students.] Without resolving the problem, please use the information in Excel's Answer and Sensitivity Reports to answer the following questions. 1) (5 Points) Would an increase in production capacity at Plant 3 be desirable? Please explain. 2) (5 Points) Suppose that the production capacity at Plant 1 changes to 69,000 units and the minimum production requirement for Model B changes to 78,000 units. What would be the minimum production cost? Please explain. 3) (5 Points) The production cost of Model A at Plant 3 is $37 per unit. How much would this cost have to change to make it worthwhile to produce Model A at Plant 3? Please explain. 4) (5 Points) Suppose the production cost of Model A at Plant 3 changes to $30 per unit and the production cost of Model C at Plant 2 changes to $27 per unit. Will the optimal production plan change? Please explain.
Problem 1 (20 Points)
Davison Electronics manufactures three LED television monitors, identified as Model A, Model B, and Model C. Davison Electronics four manufacturing plants. Each model has its lowest possible production cost when produced at Plant 1. However, Plant 1 does not have the capacity to handle the total production of all three models. As a result, at least some of the production must be routed to the other manufacturing plants. The following table shows the minimum production requirements for next month, the plant capacities in units per month, and the production cost per unit at each plant:
Model |
Production Cost per Unit |
Minimum Production Requirements |
|||
Plant 1 |
Plant 2 |
Plant 3 |
Plant 4 |
||
A |
$25 |
$28 |
$37 |
$34 |
48,000 |
B |
$26 |
$35 |
$36 |
$41 |
75,000 |
C |
$20 |
$31 |
$26 |
$23 |
60,000 |
Production Capacity |
65,000 |
50,000 |
32,000 |
43,000 |
|
Davison’s objective is to determine the cost-minimizing production plan.
Without resolving the problem, please use the information in Excel’s Answer and Sensitivity Reports to answer the following questions.
- (5 Points) Would an increase in production capacity at Plant 3 be desirable? Please explain.
- (5 Points) Suppose that the production capacity at Plant 1 changes to 69,000 units and the minimum production requirement for Model B changes to 78,000 units. What would be the minimum production cost? Please explain.
- (5 Points) The production cost of Model A at Plant 3 is $37 per unit. How much would this cost have to change to make it worthwhile to produce Model A at Plant 3? Please explain.
- (5 Points) Suppose the production cost of Model A at Plant 3 changes to $30 per unit and the production cost of Model C at Plant 2 changes to $27 per unit. Will the optimal production plan change? Please explain.
![Problem 1 (20 Points)
Davison Electronics manufactures three LED television monitors, identified as Model A, Model B,
and Model C. Davison Electronics four manufacturing plants. Each model has its lowest possible
production cost when produced at Plant 1. However, Plant 1 does not have the capacity to handle
the total production of all three models. As a result, at least some of the production must be
routed to the other manufacturing plants. The following table shows the minimum production
requirements for next month, the plant capacities in units per month, and the production cost
per unit at each plant:
Production Cost per Unit
Minimum
Model
Production
Plant 1
Plant 2
Plant 3
Plant 4
Requirements
A
$25
$28
$37
$34
48,000
B
$26
$35
$36
$41
75,000
C
$20
$31
$26
$23
60,000
65,000
50,000
32,000
43,000
Production Capacity
Davison's objective is to determine the cost-minimizing production plan.
[We have formulated the problem and solved the problem using Excel's solver in Homework 2. If
you want to, you can also use my solution of Homework 2 available in the folder "Homework
Solution" after I receive the solutions from all the students.]
Without resolving the problem, please use the information in Excel's Answer and Sensitivity
Reports to answer the following questions.
1) (5 Points) Would an increase in production capacity at Plant 3 be desirable? Please
explain.
2) (5 Points) Suppose that the production capacity at Plant 1 changes to 69,000 units and
the minimum production requirement for Model B changes to 78,000 units. What would
be the minimum production cost? Please explain.
3) (5 Points) The production cost of Model A at Plant 3 is $37 per unit. How much would this
cost have to change to make it worthwhile to produce Model A at Plant 3? Please explain.
4) (5 Points) Suppose the production cost of Model A at Plant 3 changes to $30 per unit and
the production cost of Model C at Plant 2 changes to $27 per unit. Will the optimal
production plan change? Please explain.](/v2/_next/image?url=https%3A%2F%2Fcontent.bartleby.com%2Fqna-images%2Fquestion%2Fafb35d62-6245-40da-b5d2-74fad3e6ad86%2Ff5386619-6dae-4b86-adf8-f4007ef52ea1%2F76grqjs_processed.png&w=3840&q=75)

Step by step
Solved in 2 steps

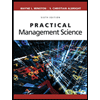
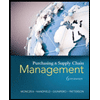
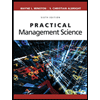
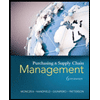