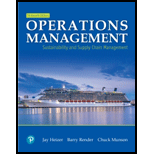
Mylab Operations Management With Pearson Etext -- Access Card -- For Operations Management: Sustainability And Supply Chain Management (13th Edition)
13th Edition
ISBN: 9780135225899
Author: Jay Heizer, Barry Render, Chuck Munson
Publisher: PEARSON
expand_more
expand_more
format_list_bulleted
Question
Chapter 5, Problem 11DQ
Summary Introduction
To determine: Theinformation included in the engineering drawing.
Introduction: A technical image which clearly and completely defines the requirements of engineering items in a diagrammatic form is known as engineering drawing.
Expert Solution & Answer

Want to see the full answer?
Check out a sample textbook solution
Students have asked these similar questions
What should leaders do after conducting an employee survey?
take immediate action on results
take at least 6 months to review the results to make sure the leader understands them
review them immediately, but do not take action right away
keep results confidential from employees
One of the best ways to encourage teamwork is to:
continually promote from outside of the department
recognize employees who focus on their personal performance goals only
reward employees who complete their own tasks and also assist with problems outside of their department
discuss individual performance issues at staff meetings
What can happen if a leader doesn't encourage teamwork?
team members will support each other more
the environment can become overly competitive and hostile
turnover will descrease
team members become more motivated
Chapter 5 Solutions
Mylab Operations Management With Pearson Etext -- Access Card -- For Operations Management: Sustainability And Supply Chain Management (13th Edition)
Ch. 5.S - Prob. 1DQCh. 5.S - Prob. 2DQCh. 5.S - Prob. 3DQCh. 5.S - Prob. 5DQCh. 5.S - Prob. 6DQCh. 5.S - Prob. 7DQCh. 5.S - Prob. 1PCh. 5.S - Prob. 2PCh. 5.S - Prob. 3PCh. 5.S - Prob. 4P
Ch. 5.S - Prob. 9PCh. 5.S - Prob. 5PCh. 5.S - Prob. 6PCh. 5.S - Prob. 8PCh. 5.S - Prob. 10PCh. 5.S - Prob. 11PCh. 5.S - Prob. 12PCh. 5.S - Prob. 13PCh. 5.S - Prob. 14PCh. 5.S - Prob. 15PCh. 5.S - Prob. 16PCh. 5.S - Prob. 17PCh. 5 - Prob. 1EDCh. 5 - Prob. 1DQCh. 5 - Prob. 2DQCh. 5 - In what ways is product strategy linked to product...Ch. 5 - Prob. 4DQCh. 5 - Prob. 5DQCh. 5 - Prob. 6DQCh. 5 - Prob. 7DQCh. 5 - Prob. 8DQCh. 5 - Prob. 9DQCh. 5 - Prob. 10DQCh. 5 - Prob. 11DQCh. 5 - Prob. 12DQCh. 5 - Prob. 13DQCh. 5 - Prob. 14DQCh. 5 - Prob. 15DQCh. 5 - Prob. 18DQCh. 5 - Prob. 16DQCh. 5 - Prob. 17DQCh. 5 - Prob. 4PCh. 5 - Prob. 5PCh. 5 - Question 5.3 Prepare a house of quality fora...Ch. 5 - Prob. 7PCh. 5 - Prob. 9PCh. 5 - Prob. 10PCh. 5 - Prob. 11PCh. 5 - Prob. 12PCh. 5 - Prob. 1PCh. 5 - Prob. 18PCh. 5 - Prob. 19PCh. 5 - Residents of Mill River have fond memories of ice...Ch. 5 - Prob. 21PCh. 5 - Prob. 22PCh. 5 - Prob. 23PCh. 5 - Prob. 8PCh. 5 - Prob. 24PCh. 5 - Prob. 2PCh. 5 - Prob. 3PCh. 5 - Prob. 13PCh. 5 - Prob. 14PCh. 5 - Prob. 15PCh. 5 - Prob. 16PCh. 5 - Prob. 17PCh. 5 - Prob. 25PCh. 5 - Prob. 1CSCh. 5 - Prob. 2CSCh. 5 - Prob. 3CSCh. 5 - Prob. 1.1VCCh. 5 - Prob. 1.2VCCh. 5 - Prob. 1.3VCCh. 5 - Prob. 1.4VCCh. 5 - Prob. 2.1VCCh. 5 - Prob. 2.2VC
Knowledge Booster
Similar questions
- understand 4 Classwork LSC Drag the name of the figure of speech to its example. 12 February 2025 personification Onomatopoeia Simile Metaphor Hyperbole Onomatopoeia metaphor 1. He tried to help but his legs were wax. Metaphor 2. The man flights like a lion on the soccer field. Simile 3. The books fell on the table with a loud thump. Onomatopoeia 4. Rita heard the last piece of pie calling her name. Personification 5. The rustling leaves kept me away. Personification 6. Kisses are the flowers of affection. 7. He's running faster than the windarrow_forwardAnswer the question in the attached photo and draw the network that interprets the dataarrow_forwardnot use ai pleasearrow_forward
- oimmnjjjharrow_forwardSummarize the ethical dilemma encountered in Walmart Inc. Which of Kohlberg's stages of moral development is represented? Is there other theories of moral development that better describes the example? Postulate the (hypothetical or real) best- and worst-case outcomes of this dilemma. Is it agreeable with the selection of Kohlberg's stages of moral development for their examples? Is there another theory of moral development that would better describe their examples?arrow_forwardFour-drive theory recommends that companies must keep fulfillment of the four drives in balance. What is this “balance” and why is it important? Can you Give an example (real or hypothetical) of how a company maintains balanced drive fulfillment. Also describe a company that does not provide this balance, including the consequences of this imbalance on employees’ attitudes and behavior. Thank youarrow_forward
- what criteria would you utilize to determine if someone's pay is “fair” or “egregious?” Additionally, what should be the mechanism or process to determine how much greater an organizational executive should be paid versus line-level employees?arrow_forwardDefine the concept of a compensation philosophy, including the components that should be addressed in a compensation philosophy. Assess why a compensation philosophy is so foreign to most organizations and how you can best encourage an organization to create its own compensation philosophy that is beneficial to attracting the best talent.arrow_forward1) View the videos Taco Bell test-drives Live Mas restaurant concept in South Bay (0.32 mins, Ctrl+Click on the link) https://www.youtube.com/watch?v=04wRc5Wg8GU , and First-ever Taco Bell Live Mas Café serving exclusive drinks in Chula Vista (1.56 mins, Ctrl+Click on the link) https://www.youtube.com/watch?v=fq6jDxJk1LM , and answer the following questions: a) What is driving Taco Bell to try a beverage-focused format? b) What type of a process strategy does their beverage-focused format represent? c) What operational issues do you think Taco Bell would face from their beverage-focused format? d) What do you think are the main advantages and disadvantages of kiosk ordering? Note: As a rough guideline, please try to keep the written submission to one or two paragraphs for each of the questions. 2) Taipei Pharmaceuticals is planning to open a new manufacturing facility as part of its expansion plans. The firm has narrowed down the search to locate its new manufacturing facility…arrow_forward
- 1) View the videos Taco Bell test-drives Live Mas restaurant concept in South Bay (0.32 mins, Ctrl+Click on the link) https://www.youtube.com/watch?v=04wRc5Wg8GU , and First-ever Taco Bell Live Mas Café serving exclusive drinks in Chula Vista (1.56 mins, Ctrl+Click on the link) https://www.youtube.com/watch?v=fq6jDxJk1LM , and answer the following questions: a) What is driving Taco Bell to try a beverage-focused format? b) What type of a process strategy does their beverage-focused format represent? c) What operational issues do you think Taco Bell would face from their beverage-focused format? d) What do you think are the main advantages and disadvantages of kiosk ordering? Note: As a rough guideline, please try to keep the written submission to one or two paragraphs for each of the questions. 2) Taipei Pharmaceuticals is planning to open a new manufacturing facility as part of its expansion plans. The firm has narrowed down the search to locate its new manufacturing facility…arrow_forwardThe Clothing Shack is an online retailer of men's, women's, and children's clothing. The company has been in business for four years and makes a modest profit from its online sales. However, in an effort to compete successfully against online retailing heavyweights, the Clothing Shack's marketing director, Makaya O'Neil, has determined that the Clothing Shack's marketing information systems need improvement. Ms. O'Neil feels that the Clothing Shack should begin sending out catalogs to its customers, keep better track of its customer's buying habits, perform target marketing, and provide a more personalized shopping experience for its customers. Several months ago, Ms. O'Neil submitted a systems service request (SSR) to the Clothing Shack's steering committee. The committee unanimously approved this project. You were assigned to the project at that time and have since helped your project team successfully complete the project initiation and planning phase. Your team is now ready to move…arrow_forwardb-1. Activity ES EF LS LF Slack 1 2 3 4 5 6 7 8 9 b-2. Identify the critical activities, and determine the duration of the project. The critical activities are .arrow_forward
arrow_back_ios
SEE MORE QUESTIONS
arrow_forward_ios
Recommended textbooks for you
- Purchasing and Supply Chain ManagementOperations ManagementISBN:9781285869681Author:Robert M. Monczka, Robert B. Handfield, Larry C. Giunipero, James L. PattersonPublisher:Cengage LearningMarketingMarketingISBN:9780357033791Author:Pride, William MPublisher:South Western Educational PublishingPractical Management ScienceOperations ManagementISBN:9781337406659Author:WINSTON, Wayne L.Publisher:Cengage,
- Foundations of Business - Standalone book (MindTa...MarketingISBN:9781285193946Author:William M. Pride, Robert J. Hughes, Jack R. KapoorPublisher:Cengage LearningFoundations of Business (MindTap Course List)MarketingISBN:9781337386920Author:William M. Pride, Robert J. Hughes, Jack R. KapoorPublisher:Cengage Learning
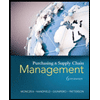
Purchasing and Supply Chain Management
Operations Management
ISBN:9781285869681
Author:Robert M. Monczka, Robert B. Handfield, Larry C. Giunipero, James L. Patterson
Publisher:Cengage Learning
Marketing
Marketing
ISBN:9780357033791
Author:Pride, William M
Publisher:South Western Educational Publishing
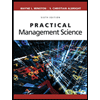
Practical Management Science
Operations Management
ISBN:9781337406659
Author:WINSTON, Wayne L.
Publisher:Cengage,
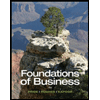
Foundations of Business - Standalone book (MindTa...
Marketing
ISBN:9781285193946
Author:William M. Pride, Robert J. Hughes, Jack R. Kapoor
Publisher:Cengage Learning
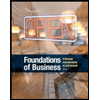
Foundations of Business (MindTap Course List)
Marketing
ISBN:9781337386920
Author:William M. Pride, Robert J. Hughes, Jack R. Kapoor
Publisher:Cengage Learning