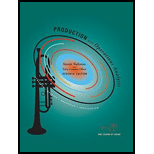
Production and Operations Analysis, Seventh Edition
7th Edition
ISBN: 9781478623069
Author: Steven Nahmias, Tava Lennon Olsen
Publisher: Waveland Press, Inc.
expand_more
expand_more
format_list_bulleted
Concept explainers
Question
Chapter 3.2, Problem 7P
Summary Introduction
To Explain:The favorable and adverse impacts of using a set of uniform key performance indicators across all departments within an organization.
Introduction:Key performance indicators are a set of measurements that provide a benchmark as to what employees are expected to achieve within a given period of time. They are a type of quantitative elements contributing to the process of sales and operations planning. Using the same set of key performance indicators across all divisions, in the process of sales and operations planning could have positive as well as negative outcomes.
Expert Solution & Answer

Want to see the full answer?
Check out a sample textbook solution
Students have asked these similar questions
How can HR proactively help ensure that other departments are operating in a legally acceptable manner?
Answers
Deliver interdepartmental training on legal compliance and requirements.
Discuss potential sources of risk with an attorney and create a plan to respond to lawsuits.
Ensure that all HR members are watching the conduct of other departments and report infractions to the head of HR.
Record improper conduct from various employees throughout the organization and pursue disciplinary measures.
Can you guys help me with this? Thank you!
Project is Terminal 1 at JFK International Airport
Question: Risk management content: Discuss a major risk management event that affected the project (Keep this content about 2 minute talking and please provide actual sources that you have the information to go over this)
use the screenshot to find the anwser to this
If the project finishes within 27 weeks of its start, the project manager receives a $500 bonus. What is the probability of a $500 bonus?
Note: Round z-value to 2 decimal places, and probability to 4 decimal places.
Chapter 3 Solutions
Production and Operations Analysis, Seventh Edition
Ch. 3.1 - Prob. 1PCh. 3.1 - Prob. 2PCh. 3.1 - Prob. 3PCh. 3.1 - Prob. 4PCh. 3.1 - Prob. 5PCh. 3.1 - Prob. 6PCh. 3.2 - Prob. 7PCh. 3.2 - Prob. 8PCh. 3.2 - Prob. 9PCh. 3.2 - Prob. 10P
Ch. 3.2 - Prob. 11PCh. 3.2 - Prob. 12PCh. 3.3 - Prob. 13PCh. 3.3 - Prob. 14PCh. 3.3 - Prob. 15PCh. 3.3 - Prob. 16PCh. 3.4 - Prob. 17PCh. 3.4 - Prob. 18PCh. 3.4 - Prob. 19PCh. 3.4 - Prob. 20PCh. 3.4 - Prob. 21PCh. 3.4 - Prob. 22PCh. 3.4 - Prob. 23PCh. 3.5 - Prob. 26PCh. 3.5 - Prob. 27PCh. 3.6 - Prob. 29PCh. 3.6 - Prob. 30PCh. 3 - Prob. 31APCh. 3 - Prob. 32APCh. 3 - Prob. 33APCh. 3 - Prob. 34APCh. 3 - Prob. 35APCh. 3 - Prob. 36AP
Knowledge Booster
Learn more about
Need a deep-dive on the concept behind this application? Look no further. Learn more about this topic, operations-management and related others by exploring similar questions and additional content below.Similar questions
- Scan To Pay Log into your own Lightning UPI account of supporting app and scan QR code below to pay! ✰ BINANCEarrow_forwardTo help with preparations, a couple has devised a project network to describe the activities that must be completed by their wedding date. Start A Ꭰ F B E The following table lists the activity time estimates (in weeks) for each activity. Optimistic Most Probable Activity Pessimistic A 4 5 6 B 2.5 3 3.5 C 5 6 7 D 5 5.5 9 E 5 7 9 F 2 3 4 G 7 9 11 H 5 6 13 H Finish Based only on the critical path, what is the estimated probability that the project will be completed within the given time frame? (Round your answers to four decimal places.) (a) Within 19 weeks? (b) Within 21 weeks? (c) Within 25 weeks?arrow_forwardYou may need to use the appropriate technology to answer this question. Mueller Associates is a urban planning firm that is designing a new public park in an Omaha suburb. Coordination of the architect and subcontractors will require a major effort to meet the 46-week completion date requested by the owner. The Mueller project manager prepared the following project network. B H Start A C G Finish E Estimates of the optimistic, most probable, and pessimistic times (in weeks) for the activities are as follows. Activity Optimistic Most Probable Pessimistic A 4 12 B 6 7 8 C 6 18 D 3 5 7 E 6 9 18 F 5 8 17 G 10 15 20 H 5 13 (a) Find the critical path. (Enter your answers as a comma-separated list.) (b) What is the expected project completion time (in weeks)? weeks i (c) Based only on the critical path, what is the estimated probability the project can be completed in 46 weeks as requested by the owner? (Round your answer to four decimal places.) (d) Based only on the critical path, what is…arrow_forward
- Bridge City Developers is coordinating the construction of an office complex. As part of the planning process, the company generated the following activity list. Draw a project network that can be used to assist in the scheduling of the project activities. Activity Immediate Predecessor ABC E FGH ] A, B A, B D E с с F, G, H, I A E Start B D A E Start B D H H E A E Finish Start D F J Finish Start B D F Finish Finish C H I Harrow_forwardHow can mindfulness be combined with cognitive reframing to build emotional regulation and mental flexibility? What is the strategy for maintaining mental well-being to improve through deliberate practice? How to engage in practices that help regulate emotions and build resilience?arrow_forward• We Are HIRING Salesforce Developer (2 - 4 Years) @ Cloudodyssey It Solutions Requirement : Appropriate knowledge on Salesforce standard objects Leads, Account, Contacts, Opportunity, Products, Lead process, Sales process, is required. • Hands-on experience in Salesforce Experience Cloud, Sales Cloud and Lightning. • • Hands experience with Salesforce development, administration, system integrations, Lightning Design System, and bug fixes. Experience in configuration, integration, APIs creation, testing and deployment of Salesforce.com functionality. Eloquent verbal and written communication skills. • Familiar with Agile framework. Work Location: Bangalore SUBMIT YOUR CV hello@cloudodyssey.coarrow_forward
- Agree or disagree with post On the surface, the numbers in financial statements do present a snapshot of a company's financial position and performance. However, just looking at the raw numbers often doesn't tell the whole story or reveal underlying trends and relationships that are crucial for making informed decisions. Think of it like looking at individual pieces of a puzzle. Each number is a piece, providing some information. But to see the complete picture – the company's overall financial health, its performance over time, how it compares to its peers, and its potential future – you need to assemble those pieces using different analytical tools. For example: Horizontal analysis helps us understand how specific financial statement items have changed over multiple periods. Is revenue growing? Are expenses increasing at a faster rate than sales? This reveals trends that a single year's numbers wouldn't show. Vertical analysis allows us to see the relative size of each item within…arrow_forwardWhat can you do in response to an insulting offer?arrow_forwardAgree or disagree with post If someone hits you with an insulting offer, the first thing to do is not take it personally. It’s normal to feel a little offended, but blowing up or shutting down won’t help your case. Better move is to stay calm and treat it like a misunderstanding or just the first step in the conversation. That way, you keep things respectful but still let them know the offer doesn’t sit right with you. It also helps to back up your response with facts. Bring in things like your experience, numbers, or any specific results you delivered. That can shift the conversation away from feelings and toward the value you bring. Agree or disagree with postarrow_forward
- Agree or disagree with the post When you get an insulting offer, the best thing to do is stay calm and professional. Try not to take it personally or react out of anger. Instead, ask questions to understand why the offer was so low. This helps you get a better idea of what the other person is thinking. After that, you can respond with a counteroffer that shows your value. Use simple facts like your skills, experience, and what others in your field are getting paid to back up your request. If the person still refuses to offer something fair, it’s okay to politely say no and walk away. Standing up for yourself in a respectful way shows confidence and helps others take you seriously. Agree or disagree with the postarrow_forwardRegarding perceptions that can occur when negotiating in different places and at different times, the continuation norm in e-negotiations is best described as _____. Group of answer choices A. negotiators' beliefs that negotiations are worth continuing B. the act of thinking about how things might have turned out differently C. the tendency for e-communicators to ascribe diabolical intentions to the other party D. the tendency for negotiators to behave as if they are communicating synchronously when in fact they are notarrow_forwardIn any discussion or meeting, there is a tendency for a minority of people to do most of the talking. A key determinant of who dominates the conversation is _____. Group of answer choices A. their status within the group B. their network of social connections C. their gender D. their agearrow_forward
arrow_back_ios
SEE MORE QUESTIONS
arrow_forward_ios
Recommended textbooks for you
- Purchasing and Supply Chain ManagementOperations ManagementISBN:9781285869681Author:Robert M. Monczka, Robert B. Handfield, Larry C. Giunipero, James L. PattersonPublisher:Cengage LearningContemporary MarketingMarketingISBN:9780357033777Author:Louis E. Boone, David L. KurtzPublisher:Cengage Learning
- MarketingMarketingISBN:9780357033791Author:Pride, William MPublisher:South Western Educational PublishingPractical Management ScienceOperations ManagementISBN:9781337406659Author:WINSTON, Wayne L.Publisher:Cengage,
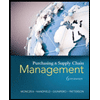
Purchasing and Supply Chain Management
Operations Management
ISBN:9781285869681
Author:Robert M. Monczka, Robert B. Handfield, Larry C. Giunipero, James L. Patterson
Publisher:Cengage Learning
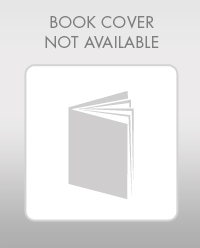
Contemporary Marketing
Marketing
ISBN:9780357033777
Author:Louis E. Boone, David L. Kurtz
Publisher:Cengage Learning
Marketing
Marketing
ISBN:9780357033791
Author:Pride, William M
Publisher:South Western Educational Publishing
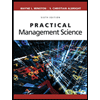
Practical Management Science
Operations Management
ISBN:9781337406659
Author:WINSTON, Wayne L.
Publisher:Cengage,