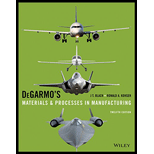
DeGarmo's Materials and Processes in Manufacturing
12th Edition
ISBN: 9781118987674
Author: J. T. Black, Ronald A. Kohser
Publisher: WILEY
expand_more
expand_more
format_list_bulleted
Concept explainers
Question
Chapter 18, Problem 13RQ
To determine
The relative advantage and typical uses of two high rolling mills with large diameter rolls, three high mills and four high mills.
Expert Solution & Answer

Want to see the full answer?
Check out a sample textbook solution
Students have asked these similar questions
6.76 A wind turbine is operating in a 12 m/s wind that has a den-
sity of 1.2 kg/m³. The diameter of the turbine silhouette is 4 m.
The constant-pressure (atmospheric) streamline has a diameter
of 3 m upstream of the windmill and 4.5 m downstream. Assume
that the velocity distributions are uniform and the air is incom-
pressible. Determine the force on the wind turbine.
m
P = Patm
4
Vz
4m
4 m
Fx.
Problem 6.76
For the position shown in the figure the spring is unstretched. The spring constant k, is designed such that after the system is released from rest, the speed of the mass is zero just as the 0.6 slug mass touches the floor. Find the spring constant, k and the maximum speed of block A and the location (distance above floor) where this occurs.
||!
Sign in
MMB241 - Tutorial L9.pd X PDF MMB241 - Tutorial L10.pX DE MMB241 - Tutorial L11.p x PDF Lecture W12 - Work and X
File C:/Users/KHULEKANI/Desktop/mmb241/MMB241%20-%20Tutorial%20L11.pdf
PDE Lecture W11 - Power and X
Draw
Alla | Ask Copilot
++
3
of 3
| D
6. If the 50-kg load A is hoisted by motor M so that the load has a constant velocity of 1.5
m/s, determine the power input to the motor, which operates at an efficiency € = 0.8.
1.5 m/s
2
7. The sports car has a mass of 2.3 Mg, and while it is traveling at 28 m/s the driver causes
it to accelerate at 5m/s². If the drag resistance on the car due to the wind is FD= 0.3v²N,
where v is the velocity in m/s, determine the power supplied to the engine at this instant.
The engine has a running efficiency of P = 0.68.
8. If the jet on the dragster supplies a constant thrust of T-20 kN, determine the power
generated by the jet as a function of time. Neglect drag and rolling resistance, and the loss
of fuel. The dragster has a mass of 1…
Chapter 18 Solutions
DeGarmo's Materials and Processes in Manufacturing
Ch. 18 - Briefly describe the evolution of forming...Ch. 18 - What are some of the possible means of classifying...Ch. 18 - How are bulk deformation processes different from...Ch. 18 - Prob. 4RQCh. 18 - Prob. 5RQCh. 18 - Prob. 6RQCh. 18 - Prob. 7RQCh. 18 - Why is it undesirable to minimize friction between...Ch. 18 - Prob. 9RQCh. 18 - Prob. 10RQ
Ch. 18 - Prob. 11RQCh. 18 - Prob. 12RQCh. 18 - Prob. 13RQCh. 18 - Prob. 14RQCh. 18 - Why is foil almost always rolled on a cluster...Ch. 18 - Prob. 16RQCh. 18 - Prob. 17RQCh. 18 - Prob. 18RQCh. 18 - Prob. 19RQCh. 18 - Explain how hot�rolled products can have...Ch. 18 - What is mill scale, and how can it be removed?Ch. 18 - Discuss the problems in producing uniform...Ch. 18 - Prob. 23RQCh. 18 - How might the addition of horizontal tensions act...Ch. 18 - What are some other techniques to reduce roll...Ch. 18 - What is thermomechanical processing, and what are...Ch. 18 - Provide a concise description of the forging...Ch. 18 - What are some of the types of flow that can occur...Ch. 18 - Prob. 29RQCh. 18 - Prob. 30RQCh. 18 - Prob. 31RQCh. 18 - Prob. 32RQCh. 18 - Prob. 33RQCh. 18 - Prob. 34RQCh. 18 - Prob. 35RQCh. 18 - Prob. 36RQCh. 18 - Prob. 37RQCh. 18 - Prob. 38RQCh. 18 - Prob. 39RQCh. 18 - Describe some of the primary differences among...Ch. 18 - What are some common examples of impression�die...Ch. 18 - What are some of the significant requirements of...Ch. 18 - Why are different tolerances usually applied to...Ch. 18 - What are some of the roles played by lubricants in...Ch. 18 - What are some of the attractive features of...Ch. 18 - What types of product geometry can be produced by...Ch. 18 - What is upset forging?Ch. 18 - What are some of the typical products produced by...Ch. 18 - What types of products can be produced by...Ch. 18 - What are some of the attractive features of...Ch. 18 - How does roll forging differ from a conventional...Ch. 18 - Describe the swaging process.Ch. 18 - What kind of products are produced by swaging?Ch. 18 - How can the swaging process impart different sizes...Ch. 18 - What are some possible objectives of...Ch. 18 - Provide a concise definition of extrusion.Ch. 18 - What metals can be shaped by extrusion?Ch. 18 - What are some of the attractive features of the...Ch. 18 - What is the primary shape limitation of the...Ch. 18 - What is the primary benefit of indirect extrusion?Ch. 18 - What are some temperature considerations in hot...Ch. 18 - Why might lubricant selection be more critical in...Ch. 18 - What are some possible causes of surface cracks in...Ch. 18 - How might tubular products be made by extrusion?Ch. 18 - What types of products are made using a...Ch. 18 - Why can lubricants not be used in spider�mandrel...Ch. 18 - What are some of the attractive features of...Ch. 18 - What are some unique concerns and limitations of...Ch. 18 - What is the unique capability provided by...Ch. 18 - How is the feedstock pushed through the die in...Ch. 18 - Describe the Conform process of continuous...Ch. 18 - What types of feedstock can be used in continuous...Ch. 18 - How is wire, rod, and tube drawing different from...Ch. 18 - Why are rods generally drawn on draw benches,...Ch. 18 - Why is the reduction in area significantly...Ch. 18 - What is the difference between tube drawing and...Ch. 18 - For what types of products might a floating plug...Ch. 18 - What are some of the benefits of cold drawing of...Ch. 18 - What types of materials are used for...Ch. 18 - What is the benefit of a tandem wire drawing...Ch. 18 - What is cold forming?Ch. 18 - What types of products are produced by cold...Ch. 18 - What is impact extrusion and what variations...Ch. 18 - If a product contains a large�diameter head and...Ch. 18 - What are some of the attractive properties or...Ch. 18 - What process can be used to produce seamless pipe...Ch. 18 - What type of products can be made by the...Ch. 18 - What types of rivets can be used when there is...Ch. 18 - How is coining different from a process known as...Ch. 18 - Why might hubbing be an attractive way to produce...Ch. 18 - How might a peening operation increase the...Ch. 18 - What is burnishing?Ch. 18 - Prob. 1PCh. 18 - Consider the extrusion of a cylindrical billet,...Ch. 18 - The force required to compress a cylindrical solid...Ch. 18 - Prob. 4PCh. 18 - Prob. 5PCh. 18 - Prob. 6PCh. 18 - Prob. 7PCh. 18 - Prob. 8PCh. 18 - Based on the size, shape, and desired precision,...Ch. 18 - What types of engineering materials might be able...Ch. 18 - For each of the shape generation methods in part...Ch. 18 - Which of the combinations of part 4 do you feel...Ch. 18 - For this system, outline the specific steps that...Ch. 18 - For your proposed solution, would any additional...
Knowledge Booster
Learn more about
Need a deep-dive on the concept behind this application? Look no further. Learn more about this topic, mechanical-engineering and related others by exploring similar questions and additional content below.Similar questions
- Q | Sign in PDE Lecture W09.pdf PDF MMB241 - Tutorial L9.pdi X PDF MMB241 - Tutorial L10.p X PDF MMB241 - Tutorial L11.p X Lecture W12-Work and X + File C:/Users/KHULEKANI/Desktop/mmb241/Lecture%20W12%20-%20Work%20and%20Energy.pdf ||! Draw | IA | a | Ask Copilot Class Work + 33 of 34 D Question 1 The engine of a 3500-N car is generating a constant power of 50 hp (horsepower) while the car is traveling up the slope with a constant speed. If the engine is operating with an efficiency of € 0.8, determine the speed of the car. Neglect drag and rolling resistance. Use g 9.81 m/s² and 1 hp = 745.7 W. 10 го Question 2 A man pushes on a 60-N crate with a force F. The force is always directed downward at an angle of 30° from the horizontal, as shown in the figure. The magnitude of the force is gradually increased until the crate begins to slide. Determine the crate's initial acceleration once it starts to move. Assume the coefficient of static friction is μ = 0.6, the coefficient of kinetic…arrow_forwardstate is Derive an expression for the volume expansivity of a substance whose equation of RT P = v-b a v(v + b)TZ where a and b are empirical constants.arrow_forwardFor a gas whose equation of state is P(v-b)=RT, the specified heat difference Cp-Cv is equal to which of the following (show all work): (a) R (b) R-b (c) R+b (d) 0 (e) R(1+v/b)arrow_forward
- of state is Derive an expression for the specific heat difference of a substance whose equation RT P = v-b a v(v + b)TZ where a and b are empirical constants.arrow_forwardTemperature may alternatively be defined as T = ди v Prove that this definition reduces the net entropy change of two constant-volume systems filled with simple compressible substances to zero as the two systems approach thermal equilibrium.arrow_forwardUsing the Maxwell relations, determine a relation for equation of state is (P-a/v²) (v−b) = RT. Os for a gas whose av Tarrow_forward
- (◉ Homework#8arrow_forwardHomework#8arrow_forwardBox A has a mass of 15 kilograms and is attached to the 20 kilogram Box B using the cord and pulley system shown. The coefficient of kinetic friction between the boxes and surface is 0.2 and the moment of inertia of the pulley is 0.5 kg * m^ 2. After 2 seconds, how far do the boxes move? A бро Barrow_forwardBox A has a mass of 15 kilograms and is attached to the 20 kilogram Box B using the cord and pulley system shown. The coefficient of kinetic friction between the boxes and surface is 0.2 and the moment of inertia of the pulley is 0.5 kg * m^2. Both boxes are 0.25 m long and 0.25 m high. The cord is attached to the bottom of Box A and the middle of box B. After 2 seconds, how far do the boxes move? A From бро Barrow_forwardarrow_back_iosSEE MORE QUESTIONSarrow_forward_iosRecommended textbooks for you
- Elements Of ElectromagneticsMechanical EngineeringISBN:9780190698614Author:Sadiku, Matthew N. O.Publisher:Oxford University PressMechanics of Materials (10th Edition)Mechanical EngineeringISBN:9780134319650Author:Russell C. HibbelerPublisher:PEARSONThermodynamics: An Engineering ApproachMechanical EngineeringISBN:9781259822674Author:Yunus A. Cengel Dr., Michael A. BolesPublisher:McGraw-Hill Education
- Control Systems EngineeringMechanical EngineeringISBN:9781118170519Author:Norman S. NisePublisher:WILEYMechanics of Materials (MindTap Course List)Mechanical EngineeringISBN:9781337093347Author:Barry J. Goodno, James M. GerePublisher:Cengage LearningEngineering Mechanics: StaticsMechanical EngineeringISBN:9781118807330Author:James L. Meriam, L. G. Kraige, J. N. BoltonPublisher:WILEY
Elements Of ElectromagneticsMechanical EngineeringISBN:9780190698614Author:Sadiku, Matthew N. O.Publisher:Oxford University PressMechanics of Materials (10th Edition)Mechanical EngineeringISBN:9780134319650Author:Russell C. HibbelerPublisher:PEARSONThermodynamics: An Engineering ApproachMechanical EngineeringISBN:9781259822674Author:Yunus A. Cengel Dr., Michael A. BolesPublisher:McGraw-Hill EducationControl Systems EngineeringMechanical EngineeringISBN:9781118170519Author:Norman S. NisePublisher:WILEYMechanics of Materials (MindTap Course List)Mechanical EngineeringISBN:9781337093347Author:Barry J. Goodno, James M. GerePublisher:Cengage LearningEngineering Mechanics: StaticsMechanical EngineeringISBN:9781118807330Author:James L. Meriam, L. G. Kraige, J. N. BoltonPublisher:WILEY
Types of Manufacturing Process | Manufacturing Processes; Author: Magic Marks;https://www.youtube.com/watch?v=koULXptaBTs;License: Standard Youtube License