Team-19_Lab-1_Tensile_Test
pdf
keyboard_arrow_up
School
University of Ottawa *
*We aren’t endorsed by this school
Course
2360
Subject
Mechanical Engineering
Date
Jan 9, 2024
Type
Pages
13
Uploaded by AmbassadorMetal9316
TENSILE TEST OF 1018 STEEL AND
6061-O ALUMINIUM ALLOY
Engineering Materials I
MCG 2360[B]
Laboratory Report
Lab 1: Tensile Test
Team #19
Student Number
Name
300241579
Gautam Mehta
300298485
George Lai
300298002
Phone Thant Htet
300293604
Ryan Gorodezky
Experiment Date: October 20, 2023
Date Submitted: November 3, 2023
Professor: Dr. Nafisa Bano
TA: Behrang Asghari Shirvani
Faculty of Engineering
Department of Mechanical Engineering
2023
1
Abstract
This laboratory experiment sought to understand and compare the stress-strain relationships
between two metallic materials: 6061-O annealed aluminum alloy and 1018 annealed steel. A
tensile testing machine will apply stress onto the two specimens of different properties until both
fail in the way of necking. Utilizing the ASTM E-8 standards for sample design and testing, each
material's mechanical properties, including elastic modulus, yield strength, ultimate tensile stress,
reduction in area, and elongation, are assessed. An emphasis was placed on keeping consistent
testing procedures to ensure comparability.
During the experiment it was noted that the steel had a larger tensile strength and a larger
ductility because it was able to go under more stress before starting to plastically deform and start
necking than the aluminium specimen. Furthermore, when the steel specimen broke there was a
loud noise while for the aluminium it was quiet. The results of this lab will contribute to a greater
understanding of the mechanical behaviours of these metals and it useful for engineering
applications that require knowledge of such properties.
2
1.
Table of Contents
Abstract
...........................................................................................................................................
1
1.
Introduction
.............................................................................................................................
1
1.1
Objective
..........................................................................................................................
1
1.1.1
Equipment and Materials
..........................................................................................
2
2.
Methodology
...........................................................................................................................
2
3.
Results and Discussion
...........................................................................................................
3
3.1
Results
..............................................................................................................................
3
3.2
Discussion
........................................................................................................................
6
3.3
Sample Calculations
.........................................................................................................
7
4.
Conclusion
..............................................................................................................................
9
References
.....................................................................................................................................
10
Appendix
.........................................................................................................................................
8
Your preview ends here
Eager to read complete document? Join bartleby learn and gain access to the full version
- Access to all documents
- Unlimited textbook solutions
- 24/7 expert homework help
LAB 1: TENSILE TEST
1
1.
Introduction
Stress can be described as the internal resistance to deformation by external load and strain
would be the amount of normalized material displacement due to stress. To understand the critical
material properties, it is important to understand the relationship of stress-strain. Material
properties such as stiffness of the material (i.e., Elastic modulus), the point of change from elastic
deformation to plastic deformation (i.e., yield strength) and the amount of plastic deformation that
the material can undergo before failure (i.e., ductility) are important properties to consider when
choosing a material for application.
This lab report will compare the two metallic materials: 1018 Steel and 6061-O Aluminium
Alloy and analyze how mechanical properties such as carbon content and crystallinity leads to
changes in the resultant mechanical properties. The lower density, non-ferrous aluminium alloy
6061-O will be compared to higher density, ferrous, low-carbon steel AISI 1018. Both specimens
have been subject to annealing. The material test will be using the guidelines set by the American
Society for Testing and Materials (ASTM) E-8 specifications. The test will be supplying data on
the force applied to the sample during tension and its relationship to the elongation of the sample
during its transition from elastic to plastic deformation followed by failure.
1.1
Objective
The objective of this lab report is to compare the stress-strain relationship between two
varied materials by using a screw based
“Tension testing of metallic materials”. The
data from the
experiment such as elastic modulus, yield strength, ultimate tensile stress, reduction in area and
elongation will be used to relate to the composition of the metals.
LAB 1: TENSILE TEST
2
1.1.1
Equipment and Materials
To apply stress, the Instron Universal Testing Machine equipped with a screw tension test
apparatus will be used. Samples of the test material will be prefabricated into cylindrical specimens
in line with the ASTM Standard E-8 for
the “Tension testing of metallic materials”.
2.
Methodology
Three samples of both AISI 1018 steel and 6061-O aluminum alloy are collected. Before
testing, precise measurements were taken, specimen length, the total length of the sample; gauge
length, the specific length of the cylinder being tested; and gauge diameter, denoting the diameter
of the inner cylinder under examination.
The samples of AISI 1018 were securely screwed into the Instron Universal Testing
Machine. The testing began with samples progressing through the stages of elastic modulus, elastic
deformation, plastic deformation and then finally, failure. Records are taken by the Instron and
then these steps repeated using samples of 6061-O aluminum.
Upon completion of the testing phase, the now fractured samples have these measurements
recorded: specimen length; gauge length; gauge diameter at the shoulder, where the cylinder tapers
up to the threads; gauge diameter at the fracture. Lastly, recorded numbers and measurements are
formulated into results where conclusions can be drawn.
LAB 1: TENSILE TEST
3
3.
Results and Discussion
3.1
Results
This section of the lab report will present the results of the tensile strength test of the two
materials: AISI 1018 Steel and 6061-O Aluminum Alloy. The results will cover stress-strain
curves of the two different materials each tested with 3 samples. The material properties such as
the Elastic Modulus, Yield Strength, Ultimate Tensile Strength, Reduction in Area, and Elongation
will be calculated based on the data points plotted on the stress-strain curve of the respective
materials and the values will be used to find the mean and standard deviation for more accurate
representation.
Figure 3.1: Stress-Strain Curve of AISI 1018 Steel
Figure 3.1 shows the stress-strain cure of the tested steel specimen. From the graph
of steel, Steel 3 is deemed as an outlier since the curve is very distant to the remaining 2 curves of
Steel 1 and 2. Among the two samples, the graph of steel 1 has clear … Therefore, steel 1 is chosen
to be the representative of the material.
Your preview ends here
Eager to read complete document? Join bartleby learn and gain access to the full version
- Access to all documents
- Unlimited textbook solutions
- 24/7 expert homework help
LAB 1: TENSILE TEST
4
Table 1: Properties of AISI 1018 Steel
Property of Steel
Mean
Standard Deviation
Elastic Modulus (E)
10007.96592
+/- 1911.111063
Yield Strength (σ
y
)
299.0981035
+/- 15.37825599
Ultimate Tensile Strength (UTS) (MPA)
456.8425362
+/- 10.62442253
Reduction in Area
59.89%
+/- 0.77057
Elongation
41.34%
+/- 0.36037018
Figure 3.2: Stress-Strain Curve of 6061-O Aluminum
From Figure 3.2, the curve for Aluminum 3 will be considered as an outlier since
it has vastly different data points comparted to the graph of Al 1 and Al 2. For 6061-O Aluminum,
the graph of Al 1 will be taken as a representative of the material since it
’s point of failure is
approximately in the range of the average points of failure of the other two curves.
LAB 1: TENSILE TEST
5
Table 2: Properties of 6061-O Aluminum
Property of Aluminum
Mean
Standard Deviation
Elastic Modulus (E)
2736.461901
+/- 410.41171659
Yield Strength (σ
y
)
29.81641496
+/- 6.58086175
Ultimate Tensile Strength (UTS) (MPA)
109.8707964
+/- 12.30482598
Reduction in Area
79.2%
+/- 0.428548
Elongation
42.48%
+/- 0.17204651
Figure 3.3: Stress-Strain Curve Comparison of Steel and Aluminum
The above figure is a graph plotted using the representatives of both materials for the
purposes of comparison and understanding the different material properties of steel and aluminum.
Gauge Diameter
Gauge Length
Sample
Initial (mm)
Final (mm)
Initial (mm)
Final (mm)
Aluminum
1
12.5
5.72
50
71.35
2
12.5
5.76
50
71.23
3
12.5
5.62
50
71.14
Steel
4
12.5
8.02
50
70.65
LAB 1: TENSILE TEST
6
5
12.5
7.89
50
70.46
6
12.5
7.84
50
70.9
3.2
Discussion
Based on the stress-strain graphs, a prominent distinction in the material behavior of steel
and aluminum is evident. Steel showcases a superior yield strength relative to aluminum. This
becomes especially pronounced when comparing the average yield strength; with aluminum
registering at 29.82MPa and steel at 299.1MPa. Consequently, once these materials surpass their
yield points, they exhibit plastic deformation. Aluminum enters this phase of deformation
considerably sooner, due to its lower yield strength.
The characteristics of steel become even more pronounced when examining its behaviour
near its ultimate tensile strength. Steel exhibits a brittleness, evidenced by its almost immediate
necking followed by a sharp and loud fracturing. To compare, aluminum, which possesses a more
ductile nature, necks gradually upon reaching its ultimate tensile strength and continues to deform
plastically until the point of fracture. The fracture process of aluminum is clearly a quieter and
more prolonged breakage compared to the abruptness of steel.
Elastic modulus serves as a measure of a material's resistance to elastic deformation and is
quantified as the ratio of stress to strain. For this test, the elastic modulus stood at 2736.46Pa for
aluminum and 10007.97Pa for steel. A material with a high elastic modulus will resist deformation
more effectively, meaning it will exhibit lesser deformation for the same applied force relative to
materials with a lower modulus.
Introducing an extensometer to the test setup could offer enhanced precision in strain
measurements. The device measures the elongation and contraction of a sample directly, making
it possible to determine material properties with a higher degree of accuracy. Properties like yield
Your preview ends here
Eager to read complete document? Join bartleby learn and gain access to the full version
- Access to all documents
- Unlimited textbook solutions
- 24/7 expert homework help
LAB 1: TENSILE TEST
7
strength, modulus of elasticity, and Poisson's ratio would be directly impacted using an
extensometer.
Fracture surface analysis provides insightful data regarding the nature of material failure.
Observations from the fracture surfaces can reveal patterns of deformation, potential inclusions,
or voids that might have contributed to premature failure. Specific anomalies or patterns, such as
dimples, could indicate ductile failure, while flat and shiny surfaces might point towards brittle
fractures.
When considering the percentage elongation, it was found that aluminum, with a value of
42.48%, surpasses steel, which was at 41.34%. This indicates that aluminum exhibits a greater
capability for deformation before reaching the point of failure, reinforcing its inherent ductility
compared to steel. Furthermore, the percent reduction, a crucial indicator of ductility, was
determined to be 59.89% for steel and 79.2% for aluminum. The data implies that aluminum, in
the event of failure, undergoes a more substantial reduction in its cross-sectional area than steel.
Finally, it's imperative to recognize potential sources of error that could have influenced
the results. These might encompass inaccuracies in measurements, imperfections inherent in the
steel manufacturing process, or miscalculations. Ensuring rigorous adherence to experimental
protocols and using precise instruments can help mitigate these errors in future tests.
3.3
Sample Calculations
***Note - Data for sample calculations can be found in the spreadsheet***
An example of each type of calculation will be presented with accuracy of 8 decimals.
Sample 1
–
AISI 1018 Steel:
E = Elastic Modulus = Stress / Strain
LAB 1: TENSILE TEST
8
P
1
=
(0 , 0)
P
2
where stress is at its highest before its first decline = (0.03484136 , 315.0102757)
E
Steel 1
= Slope = (y
2 -
y
1
) / (x
2 -
x
1
)
= (315.0102757 - 0) / (0.03484136 - 0
= 9041.273811
Mean = Sum of Samples / # of Samples
Mean
E-Steel
= (9041.273811 + 8305.528805 + 12677.09513) / 3
= 10007.96592
Std. Deviation = SQRT[
(Σ(
x
i
–
Mean)
2
) / # of Samples ]
Std. Deviation
E-Steel
= SQRT[((9041.273811 - 10007.96592)
2
+ (8305.528805 - 10007.96592)
2
+
(12677.09513 - 10007.96592)
2
) / 3]
= +/- 1911.111063
% Reduction in Area = ((Initial Area
–
Final Area) / Initial Area) * 100
Area of Initial Cylinder =
π(d/2)
2
=
π(
12.5mm/2)
2
= 122.718463mm
2
Area of Fracture Steel
1
Cylinder
= π(d/2)
2
= π(
8.02mm/2)
2
= 50.51712403mm
2
Mean
= (50.51712403 + 48.89268501 + 48.27496935) / 3
= 49.22825946mm
2
Elongation =
𝐿𝑓 – 𝐿0
𝐿0
∗ 100 =
71.35−50
50
∗ 100
= 42.7
LAB 1: TENSILE TEST
9
4.
Conclusion
From the collected data and the generated stress-strain graphs, a clear understanding of the
behavior of steel and aluminium under tensile stress was obtained. The results indicate that steel
not only possesses a superior strength compared to aluminium but also displays a higher degree of
brittleness. This shows that inducing plastic deformation in steel demands a substantially greater
force than what's required for aluminium. The observed behavior proves the superiority of steel's
strength over aluminium, making it an ideal choice for applications demanding high stress loads.
Furthermore, the toughness of steel, as gauged by the larger area beneath its stress-strain
curve, surpasses that of aluminium. This can be attributed to steel's elevated yield strength and
ultimate tensile strength. The prolonged duration to fracture and extended necking observed in
aluminium, when contrasted with steel, reveals a notable difference in their respective cross-
sectional areas, both before and after the test. Specifically, aluminium exhibited a more significant
change in cross-sectional area from its original state, due to its ductile nature. Looking at the
fracture points of both materials further proves the higher ductility of aluminium as opposed to
steel.
Potential sources of error in this experiment include imperfections originating from the
manufacturing process of the steel and aluminium specimens. Additionally, measurement
discrepancies, potentially arising from gauging the samples pre and post the tensile test, could
skew the results. To enhance the accuracy and minimize the margin of error in future iterations of
this lab, it's important to take multiple measurements, followed by a comparative analysis to ensure
precision and reliability.
Your preview ends here
Eager to read complete document? Join bartleby learn and gain access to the full version
- Access to all documents
- Unlimited textbook solutions
- 24/7 expert homework help
10
References
•
Lambros S. Athanasiou, Dimitrios I. Fotiadis, Lampros K. Michalis, 10 - Structure and
Mechanical Behavior of Atherosclerotic Plaque, Editor(s): Lambros S. Athanasiou,
Dimitrios I. Fotiadis, Lampros K. Michalis, Atherosclerotic Plaque Characterization
Methods Based on Coronary Imaging, Academic Press, 2017, Pages 181-198, ISBN
9780128047347,
https://doi.org/10.1016/B978-0-12-804734-7.00010-5
.
•
N. Bano, B.A. Shirvani, X. Xie,
Data - Lab 1 - Tensile Test, University of Ottawa,
Department of Mechanical Engineering, 2023
•
Siplyarsky, Alex. “The Importance of an Extensometer in Materials Testing.”
NextGen
Material Testing
, 9 Oct. 2019,
www.nextgentest.com/blog/the-importance-of-an-
extensometer-in-materials-
testing/#:~:text=An%20extensometer%20is%20an%20accessory,they%20can%20be%20
clearly%20visible
.
Related Documents
Related Questions
Hi can you please help me with the attached question?
arrow_forward
UzNDU3NTYyMjk0/a/MjYOMzAwMjMOOTM5/details
Further questions
4.The graphs show how the extension changes with stretching force for four different materials.
a. Which two graphs show materials that follow Hooke's law?
A
B
b. Which two graphs show materials that become less stiff as
they are stretched?
force
force
D
C. Which graph shows a material that maintains the same
stiffness throughout?
force
force
1. A force of 20N stretches a spring by 0.5m. The spring obeys Hooke's law.
a. Calculate the spring constant including a suitable unit.
b. How much force must a man use to stretch it by 1.5m?
5. A car has a weight of 240OON which is distributed equally over all four wheels. Each wheel has a spring of
spring constant 400N/cm.
a.
Determine the force through the spring on each wheel.
b. Calculate the compression of each spring when the car rests on the ground.
6.In a spring experiment the results were as follows:
Force (N)
Length (mpm
1
2
4
6.
7
50
58
70
74
82
9n
102
125
LELL
arrow_forward
Mild steel 1
Young;s modulus 1219.5
Yield strain and stress (0.4101,500.08)
Failure stress and strain :not able to find because the given data shows the experiment did not reach the failure point.
if the material stress and strain does not reach a failure point ,what dose it means , does it means that the material is more stronger?
arrow_forward
Figure 1 shows the tensile testing results for different materials. All specimens have an initial
diameter of 12 mm and an initial gauge length of 50 mm.
300
250
Low carbon steel
Network polymer
200
Crystalline polymer
150
Amorphous polymer
100
50
5
10
15
20
25
30
Strain (%)
Figure 1: Stress-strain curve
b. Determine the following parameters for each material:
• the tensile strength
the 0.2% offset yield strength
the modulus of elasticity
• the ductility
Stress (MPa)
LO
arrow_forward
You have been given the following test sample data following mechanical testing of 15
test pieces of Silicon Nitride.
What is the Weibull modulus of this material?
Would you advise the use of a similar material with a Weibull Modulus of 16.3 and a
mean failure stress of 485 MPa, if you anticipate that the peak stress on the material
could be 430 MPa?
Sample
1
2
3
4
5
6
7
8
9
10
11
12
13
14
15
Select one or more:
O a. No
O b. 18.6
O C.
13.4
O d. Yes
O e. 15.7
f. 17.1
Failure Stress (MPa)
423
459
496
432
447
467
473
499
485
479
505
530
526
490
510
<
arrow_forward
The answer is one of the options below please solve carefully and circle the correct option Please write clear .
arrow_forward
Flag question
You have been given the following test sample data following mechanical testing of 15 test pieces of a modified Alumina.
What is the Weibull modulus of this material?
Would you advise the use of this material over one with a Weibull Modulus of 19.6 and a mean failure stress of 270 MPa, if you
anticipate that the peak stress on the material could be 255 MPa?
Sample
1
2
3
4
5
6
7
8
9
10
11
12
13
14
15
Select one or more:
Failure Stress (MPa)
297
293
270
300
260
286
265
295
4
293
280
288
263
290
298
275
arrow_forward
Review
Data taken from a stress-strain test for a ceramic are
given in the table. The curve is linear between the origin
and the first point.
No elements selected
a(ksi)
50 +
40 -
30
Figure
1 of 1
20
10 +
o (ksi)
€ (in./in.)
ex 10(in./in.)
0.5
1.0
1.5
2.0
2.5
33.2
0.0006
45.5
0.0010
Press (ENTER) to select this element. Press ESC) to return to the main menu. Press CTRL+Q) to quit the application.
49.4
0.0014
51.5
0.0018
53.4
0.0022
arrow_forward
Select All the correct statements from below.
a. If the averaged distance between partial dislocations for material A observed under TEM is smaller than material B, the estimated stacking fault energy of material A is lower than material B.
b. K_IC is a material property that doesn't change with testing conditions
c. The main difference between high cycle fatigue and low cycle fatigue is the difference in the number of cycles to failure
d. A negative R value in fatigue test indicate the minimum stress is compressive in nature
arrow_forward
A sample of crosslinked polvisoprene rubber undergoes a constant strain rate axial tension experiment
The initial sample measurements are 3.60 cm gauge length (axial direction); 0.b2 cm wide; 0.1/ cm thick:
arrow_forward
Please help with all, and desbribe how the table is used, thank you in advance! Will give thumbs up
arrow_forward
Given the following data for five different materials answer parts A B C D E & F with an explanation
arrow_forward
Read and Solve carefully please Write clearly and Box the Final answer Express your answer to 3 Significant figures and include appropriate units.
arrow_forward
Need help with this Mechanics of Materials review
arrow_forward
How did temperature affect the toughness of the specimens?
arrow_forward
Please find the following using the graph provided.
1. Resilience (use calculated yield point)
2. Toughness
please explain the calcualtion and equation needed. Thank you!
arrow_forward
SEE MORE QUESTIONS
Recommended textbooks for you
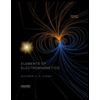
Elements Of Electromagnetics
Mechanical Engineering
ISBN:9780190698614
Author:Sadiku, Matthew N. O.
Publisher:Oxford University Press
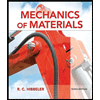
Mechanics of Materials (10th Edition)
Mechanical Engineering
ISBN:9780134319650
Author:Russell C. Hibbeler
Publisher:PEARSON
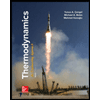
Thermodynamics: An Engineering Approach
Mechanical Engineering
ISBN:9781259822674
Author:Yunus A. Cengel Dr., Michael A. Boles
Publisher:McGraw-Hill Education
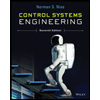
Control Systems Engineering
Mechanical Engineering
ISBN:9781118170519
Author:Norman S. Nise
Publisher:WILEY
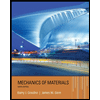
Mechanics of Materials (MindTap Course List)
Mechanical Engineering
ISBN:9781337093347
Author:Barry J. Goodno, James M. Gere
Publisher:Cengage Learning
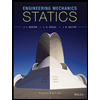
Engineering Mechanics: Statics
Mechanical Engineering
ISBN:9781118807330
Author:James L. Meriam, L. G. Kraige, J. N. Bolton
Publisher:WILEY
Related Questions
- Hi can you please help me with the attached question?arrow_forwardUzNDU3NTYyMjk0/a/MjYOMzAwMjMOOTM5/details Further questions 4.The graphs show how the extension changes with stretching force for four different materials. a. Which two graphs show materials that follow Hooke's law? A B b. Which two graphs show materials that become less stiff as they are stretched? force force D C. Which graph shows a material that maintains the same stiffness throughout? force force 1. A force of 20N stretches a spring by 0.5m. The spring obeys Hooke's law. a. Calculate the spring constant including a suitable unit. b. How much force must a man use to stretch it by 1.5m? 5. A car has a weight of 240OON which is distributed equally over all four wheels. Each wheel has a spring of spring constant 400N/cm. a. Determine the force through the spring on each wheel. b. Calculate the compression of each spring when the car rests on the ground. 6.In a spring experiment the results were as follows: Force (N) Length (mpm 1 2 4 6. 7 50 58 70 74 82 9n 102 125 LELLarrow_forwardMild steel 1 Young;s modulus 1219.5 Yield strain and stress (0.4101,500.08) Failure stress and strain :not able to find because the given data shows the experiment did not reach the failure point. if the material stress and strain does not reach a failure point ,what dose it means , does it means that the material is more stronger?arrow_forward
- Figure 1 shows the tensile testing results for different materials. All specimens have an initial diameter of 12 mm and an initial gauge length of 50 mm. 300 250 Low carbon steel Network polymer 200 Crystalline polymer 150 Amorphous polymer 100 50 5 10 15 20 25 30 Strain (%) Figure 1: Stress-strain curve b. Determine the following parameters for each material: • the tensile strength the 0.2% offset yield strength the modulus of elasticity • the ductility Stress (MPa) LOarrow_forwardYou have been given the following test sample data following mechanical testing of 15 test pieces of Silicon Nitride. What is the Weibull modulus of this material? Would you advise the use of a similar material with a Weibull Modulus of 16.3 and a mean failure stress of 485 MPa, if you anticipate that the peak stress on the material could be 430 MPa? Sample 1 2 3 4 5 6 7 8 9 10 11 12 13 14 15 Select one or more: O a. No O b. 18.6 O C. 13.4 O d. Yes O e. 15.7 f. 17.1 Failure Stress (MPa) 423 459 496 432 447 467 473 499 485 479 505 530 526 490 510 <arrow_forwardThe answer is one of the options below please solve carefully and circle the correct option Please write clear .arrow_forward
- Flag question You have been given the following test sample data following mechanical testing of 15 test pieces of a modified Alumina. What is the Weibull modulus of this material? Would you advise the use of this material over one with a Weibull Modulus of 19.6 and a mean failure stress of 270 MPa, if you anticipate that the peak stress on the material could be 255 MPa? Sample 1 2 3 4 5 6 7 8 9 10 11 12 13 14 15 Select one or more: Failure Stress (MPa) 297 293 270 300 260 286 265 295 4 293 280 288 263 290 298 275arrow_forwardReview Data taken from a stress-strain test for a ceramic are given in the table. The curve is linear between the origin and the first point. No elements selected a(ksi) 50 + 40 - 30 Figure 1 of 1 20 10 + o (ksi) € (in./in.) ex 10(in./in.) 0.5 1.0 1.5 2.0 2.5 33.2 0.0006 45.5 0.0010 Press (ENTER) to select this element. Press ESC) to return to the main menu. Press CTRL+Q) to quit the application. 49.4 0.0014 51.5 0.0018 53.4 0.0022arrow_forwardSelect All the correct statements from below. a. If the averaged distance between partial dislocations for material A observed under TEM is smaller than material B, the estimated stacking fault energy of material A is lower than material B. b. K_IC is a material property that doesn't change with testing conditions c. The main difference between high cycle fatigue and low cycle fatigue is the difference in the number of cycles to failure d. A negative R value in fatigue test indicate the minimum stress is compressive in naturearrow_forward
- A sample of crosslinked polvisoprene rubber undergoes a constant strain rate axial tension experiment The initial sample measurements are 3.60 cm gauge length (axial direction); 0.b2 cm wide; 0.1/ cm thick:arrow_forwardPlease help with all, and desbribe how the table is used, thank you in advance! Will give thumbs uparrow_forwardGiven the following data for five different materials answer parts A B C D E & F with an explanationarrow_forward
arrow_back_ios
SEE MORE QUESTIONS
arrow_forward_ios
Recommended textbooks for you
- Elements Of ElectromagneticsMechanical EngineeringISBN:9780190698614Author:Sadiku, Matthew N. O.Publisher:Oxford University PressMechanics of Materials (10th Edition)Mechanical EngineeringISBN:9780134319650Author:Russell C. HibbelerPublisher:PEARSONThermodynamics: An Engineering ApproachMechanical EngineeringISBN:9781259822674Author:Yunus A. Cengel Dr., Michael A. BolesPublisher:McGraw-Hill Education
- Control Systems EngineeringMechanical EngineeringISBN:9781118170519Author:Norman S. NisePublisher:WILEYMechanics of Materials (MindTap Course List)Mechanical EngineeringISBN:9781337093347Author:Barry J. Goodno, James M. GerePublisher:Cengage LearningEngineering Mechanics: StaticsMechanical EngineeringISBN:9781118807330Author:James L. Meriam, L. G. Kraige, J. N. BoltonPublisher:WILEY
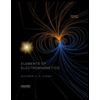
Elements Of Electromagnetics
Mechanical Engineering
ISBN:9780190698614
Author:Sadiku, Matthew N. O.
Publisher:Oxford University Press
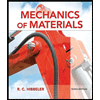
Mechanics of Materials (10th Edition)
Mechanical Engineering
ISBN:9780134319650
Author:Russell C. Hibbeler
Publisher:PEARSON
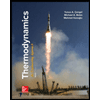
Thermodynamics: An Engineering Approach
Mechanical Engineering
ISBN:9781259822674
Author:Yunus A. Cengel Dr., Michael A. Boles
Publisher:McGraw-Hill Education
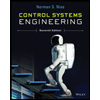
Control Systems Engineering
Mechanical Engineering
ISBN:9781118170519
Author:Norman S. Nise
Publisher:WILEY
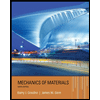
Mechanics of Materials (MindTap Course List)
Mechanical Engineering
ISBN:9781337093347
Author:Barry J. Goodno, James M. Gere
Publisher:Cengage Learning
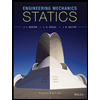
Engineering Mechanics: Statics
Mechanical Engineering
ISBN:9781118807330
Author:James L. Meriam, L. G. Kraige, J. N. Bolton
Publisher:WILEY