MFGEN 481 Final Project Case Study 2023
pdf
keyboard_arrow_up
School
Brigham Young University *
*We aren’t endorsed by this school
Course
105
Subject
Mechanical Engineering
Date
Jan 9, 2024
Type
Pages
14
Uploaded by MasterBarracuda1151
Process Improvement Case Study Door Assembly Process Plant Background
The problem setting is a small furniture plant that primarily manufactures case goods, such as entertainment centers. Operating for a single eight-hour shift, the plant produces 150 to 200 cases each day. The plant makes approximately 30 unique case styles, and each case can be made from a variety of wood species including Oak, Cherry, Pine, etc. An example of one such case is shown below. Production Process:
The production of a cabinet begins with the machining of a core of solid wood into a variety of machined parts, such as rails and moldings. In addition, front panels, shelving and side panels are cut from flat stock. This forming of parts takes place in the Machine Room. Also in the machine room, sub-assemblies, such as doors, are assembled. The parts for a two panel door are shown below:
The completed parts are then transported in batches to the Cabinet Room. In the Cabinet Room, the parts and subassemblies are assembled and take on the form of a cabinet. A Cabinet Room build schedule determines how many of each case to assemble. This build schedule generates the schedules of what to machine in the Machine Room as well. Once assembled, the case is placed on a continuously moving conveyor which transports the cabinet through the Finishing Room. In this room several operators use spray guns to apply paints, stains, and varnishes. The area also includes wiping and touch-up operations. Upon completion, the cabinets are offloaded onto a roller conveyor for the final assembly and packing. In the Packing Room, activities such as inserting glass panels for doors, installing electrical power strips, and adding door knobs are performed. Finally, the case is wrapped in protective material and placed in a cardboard box for shipping. The diagram below shows the basic flow of parts between the different processing areas.
Your preview ends here
Eager to read complete document? Join bartleby learn and gain access to the full version
- Access to all documents
- Unlimited textbook solutions
- 24/7 expert homework help
Process Description
The process of interest in this case study is the door assembly operation. The reason for studying the door assembly process is that it requires 10 hours a day, and even some Saturdays to meet the daily cabinet room production schedule. The plant manager and machine room supervisor want the operation to produce the schedule during the normal shift (7.6 hours), working only 5 days a week. In the door assembly operation, cabinet doors are produced in batches. The plant produces approximately 60 different door styles. But in general, from a time to produce perspective, doors can be grouped into categories by the number of panels. There are one-panel, two-panel, four-panel, and six-panel doors. The figure below shows the parts that compose a door. Doors always have a top rail, bottom rail, and side rails. Doors also contain inserts (or panels), usually made from wood, but occasionally from glass. Rails separating the inserts are called center rails or munts. The side rails, top and bottom rails, and munts are all machined in the Machine Room and are delivered to the Door Assembly Operation in batches. Batch sizes are matched to the cabinet room build schedule. In the door assembly process, these parts are assembled, glued, and nailed together. The nailing process essentially holds the parts together until the glue dries. A layout of the door assembly process is shown below.
This process consists of three operations which are detailed with pictures and descriptions below. In addition to the assembly operations, a setup occurs between batches of doors. The setup consists of locating the rails and inserts for the new batch and stacking these parts at the first operation. Once all the parts are located, a single door is assembled so that the clamp can be properly adjusted for the new door. If a batch of parts has been incorrectly machined, the parts must be reworked. These setups can take anywhere from 20-60 minutes. However, if parts are missing, an even longer setup will occur. 1. Assembly Operations: First, two operators in parallel apply glue to the rails and assemble all the pieces together (side rails, end rails, inserts, and munts). Once assembled, the operator pushes the door to a holding fixture, shown as a V in the diagram above. If their side of the V contains a door, the operator will wait till that door is removed before pushing forward their most recent assembly. The operator will not begin assembling the next door until they have pushed the preceding door to the holding fixture.
2. Clamp Operations:
Second, the clamp operator removes the assembled door from the V holding fixture and places the assembly into a pneumatic clamp. The operator activates the clamp with a foot pedal, which presses and "squares" the pieces together. The operator then applies nails to all joints using a nail gun. The clamp operator then releases the clamp and slides the door to the mud and stack operator. There is essentially an unlimited queue between the clamp operator and the mud & stack operator, because the clamp operator can stack up doors in front of the mud operator. 3. Mud & Stack
: Finally, a single operator applies putty to the nail depressions and places the door on a cart to be sent to the next operation.
Your preview ends here
Eager to read complete document? Join bartleby learn and gain access to the full version
- Access to all documents
- Unlimited textbook solutions
- 24/7 expert homework help
Problem Statement
The problem as stated earlier, is that the door assembly process is taking about 10 hours a day, and is often working 6 days a week, rather than 5, to keep up with the cabinet room schedule. Plant management wants to determine how to improve the process so that the schedule can be accomplished in 5 days during the normal 7.6 hour shift. After observing the process, a time study was performed and the following process data was collected. Also a representative door assembly schedule was generated which represents the door demand generated by a daily cabinet room build schedule. During the observation and time study of the process, the assembly operation itself ran smoothly. There were times when the clamp was not functioning properly, and times when the quality of the incoming parts impacted production. But in general, when the assembly team was producing parts, the workload appeared balanced and they produced at a constant and adequate rate. What became readily apparent was that the setup process was an extremely time-consuming task. Since setup time is essentially non-value added from the standpoint of producing parts, reducing setup time could dramatically increase the throughput of this process. Your Project:
1) Build a Simulation model to analyze each of the three scenarios below to determine the impact on setup time and time to produce the schedule. •
Scenario 1 - use one of the assembly operators to begin a pre-setup •
Scenario 2 - hire an operator dedicated to setup •
Scenario 3 - increase the batch sizes 2) Provide a brief write up on each scenario that includes data from the simulation to support your conclusions. 3) Make a final recommendation which gives the most cost-effective solution for assembling doors during the normal shift.
The following summarizes the data collected during the time study: Assembly Operator 1 Cycle time ~ triangular(35,65,40)seconds * Difficulty Multiplier Assembly Operator 2 Cycle time ~ triangular (35,65,40)seconds * Difficulty Multiplier Clamp Operator Cycle time ~ triangular (20 ,60,41)seconds * Difficulty Multiplier Mud/Putty Operator Cycle time ~ triangular (15,30,20)seconds * Difficulty Multiplier Difficulty Multiplier* 1 panel door = 1.0 2 panel door = 1.2 4 panel door = 1.4 6 panel door = 1.6 * A Difficulty Multiplier is necessary since a single panel door is easier/quicker to assembly than a six-panel door. To account for this, a Difficulty Multiplier is applied to the cycle time distributions. Setup Setup time ~ triangular (20,65,30) minutes
Door Assembly Schedule Four different door types are manufactured at the facility. The type and number of doors are based on a build schedule. Directions for Operating the Schedule:
A one-day schedule is listed below. You can rearrange the schedule to get the quickest time to finish the schedule. Then use your optimum schedule to run each scenario to determine the best option. Batch Number Batch Size Number of Panels 1 100 1 2 100 2 3 140 4 4 80 6 5 120 1 6 120 2 7 50 2 8 20 1 9 22 2 10 25 2
Your preview ends here
Eager to read complete document? Join bartleby learn and gain access to the full version
- Access to all documents
- Unlimited textbook solutions
- 24/7 expert homework help
Scenario 1 Use one of the Assembly Operators to begin a pre-setup
Looking at a layout of the process, there are two assembly and glue operators that work in parallel. Theoretically, one assembly operator could leave and the operation would continue to run, although at a reduced rate. When the operator leaves, effects how long production will operate at the reduced rate, but will also impact how long the setup will take. Model Logic: Construct your model so that Assembler 2 can leave to perform setups based on the number of doors remaining in the current batch. The schedule below shows the setup times if Assembler 2 starts the setup with the associated doors remaining. Setup Schedule: Doors Remaining Set Up Time 0 triangular (20,65,30) 10 triangular (20,50,30) 20 triangular (20,45,25) 30 triangular (15,40,22) 40 triangular (13,40,21) 50 triangular (12,39,20)
Use the simulation model and the cost data below to determine the best time for Assembler 2 to be released to perform pre-setup tasks. Use the default daily door assembly schedule. Remember to run enough days in order to improve the confidence level of your results. Be sure to include the total costs (standard and over time) associated with each option in your report. Cost Data: Assembly Operator Standard Time $15.00/hr Over Time $20.00/hr Clamp Operator Standard Time $20.00/hr Over Time $27.50/hr Putty Operator Standard Time $15.00/hr Over Time $20.00/hr Note: Overtime begins after 7.6 hours Objective
: Minimize overtime to reduce costs You need to determine:
1.
Cost if Assembler 2 doesn't leave 2.
Cost if Assembler 2 leaves with 10 doors remaining 3.
Cost if Assembler 2 leaves with 20 doors remaining 4.
Cost if Assembler 2 leaves with 30 doors remaining 5.
Cost if Assembler 2 leaves with 40 doors remaining 6.
Cost if Assembler 2 leaves with 50 doors remaining
Scenario 2
Hire an Operator dedicated to Setup
Currently there is an unused door clamp machine in the building. A parallel door assembly line could be activated at very little cost. Therefore, a second scenario is to add an additional operator. His job would be dedicated to setting up the next batch on the parallel line while the other four operators are producing doors on the other line. When the four operators complete a batch, they could simply move over to the parallel line and begin the production of the next batch of doors with a significant reduction in their setup time. This additional operator will have a cost of $15/hr and $20/hr for standard time and overtime, respectively. By adding the operator, the setup time between production runs is reduced to a triangular (5,9,7)min distribution. Also, this operator only needs to devote 50% of his time to the door assembly setups. The rest of his time (and therefore his cost) will be applied to a nearby department. You need to
: 1.
Develop a cost comparison between Scenario 1 and Scenario 2.
Your preview ends here
Eager to read complete document? Join bartleby learn and gain access to the full version
- Access to all documents
- Unlimited textbook solutions
- 24/7 expert homework help
Scenario 3
Because of the long setup times, a third way to improve costs for the door assembly process is to increase the batch sizes and reduce the number of setups. To assess the impact of larger batches, you first need a little background on the scheduling process within the plant. Background: The door assembly schedule is based on the cabinet line schedule. For example, a model 9350 cabinet require two 2-panel and two 1-panel doors. So, if the cabinet line schedule called for 50 of the 9350 cabinets, a demand for one-hundred 9350 model 2-panel and one-
hundred 9350 model 1-panel doors is generated for the door assembly schedule. A representative for a single day of the door assembly schedule has been included in the base simulation model. In addition, the plant manufactures up to thirty different cabinets, which translates to approximately 50 different doors. Therefore, the representative door assembly schedule may not repeat for a week or more. Currently, the door assembly schedule is synchronized with the cabinet line schedule. In other words, just enough doors are made to meet next day’s cabinet line schedule. So, if the batch size for the door assembly line is increased without increasing the batch size of the cabinet line, doors must typically be carried in inventory for at least a week before another build of that model will be called for by the cabinet line. Your task: Your task is to use the following data to determine how large to make the batch size. Assume the representative door assembly schedule requires no inventory control because the doors are immediately installed on the cabinets. Also, assume that the cabinet line schedule cannot be manipulated. Thus, increasing the batch sizes for the representative door assembly schedule requires a new mechanism (and cost) for managing assembled door inventory. Also, assume for simplicity sake that batch sizes can only be increased in integer multiples. Two costs are associated with carrying doors in inventory. The first cost is a onetime fixed cost for the equipment, procedures and controls put in place to establish the ability to physically carry doors in inventory. The table displays these costs as a function of the increase in the size of the representative daily door assembly schedule. Assume that there is only enough floor space to hold three weeks of inventory (quadruple the batch size). Batch Size Fixed Cost x1 $0 x2 $10,000 x3 $10,000 x4 $20,000 The second cost is associated with carrying the inventory. This is often referred to as a holding cost (
h
). The table below show the yearly holding cost for a single door by type.
Door Type Fixed Cost 1 panel $5.00 2 panel $6.50 4 panel $7.50 6 panel $8.50 You need to determine:
1.
Costs associated with the base schedule 2.
Costs of doubling the batch sizes 3.
Costs of tripling the batch sizes 4.
Costs of quadrupling the batch sizes Note: Don't forget that by increasing the batch size and reducing the number of setups, overtime and overtime costs will be reduced.
Related Documents
Related Questions
Task 1:
Produce a report by applying the concepts of engineering
materials relating to a tricycle as shown in Figure 1, with
the following incorporated:
3. Choose the most appropriate material from your point
of view that can be used to produce the item/product
with reasons discussed.
Figure 1: Tricycle
arrow_forward
Can you please answer these 3 questions from material engineering.....
arrow_forward
Example 5
Material Balance Analysis
A cannery receives on a given day:
12 tons of raw produce,
5 tons of cans,
0.5 ton of cartons,
and 0.3 ton of miscellaneous materials.
Its output includes:
10 tons of processed product,
the remaining becoming part of waste,
four tons of the cans are stored for future use and the remainder are used to package
the produce.
About 3 percent of the cans used are damaged and recycled.
The cartons are also used for packaging, except for 3 percent which become damaged
and are incinerated with other paper wastes.
of the miscellaneous materials, 75 percent become paper wastes that are incinerated,
and the remainder are disposed of by the municipal collection agency.
Draw a materials flow diagram for this activity.
Solution
arrow_forward
TWM Company purchases 8000 units of product each year at a unit cost of $10.00. The order cost is
$30.00 per order, and the holding cost per unit per year is $3.00.
a) What are the economic order quantity, the total annual cost, the number of orders to place in one
year, and the reorder point when the lead time is two weeks?
b) What happens to the EOQ if backordering is possible and the stockout cost per unit per year is
$1.00?
c) The supplier is offering a special discount and has temporarily reduced his unit price from $10.00
to $9.00. What amount should be purchased to take advantage of the discount?
d) The supplier will increase his unit price from $10.00 to $11.00 on 1 January. What amount should be
purchased and delivered on 31 December before the price increase is effective if the stock position is
346 units? What will be the cost saving of the special purchase
arrow_forward
Item A is one of the products manufactured at ABC Manufacturing.
• Each order for producing the product has a cost of $300/order, regardless of the number of units ordered.
. The lead time for placing the order is 2 week(s).
• The inventory cost is $3/unit/week and the on-hand inventory at the beginning of week 1 is 145 units.
The gross requirement for Item A is specified for the beginning of weeks 1 through 8 in the table that follows.
Item A
Week 1 Week 2 Week 3 Week 4 Week 5 Week 6 Week 7 Week 8
60
65
0
90
0
55
95
85
Gross Requirement
On-hand Inventory
Net Requirement
Planned Order Receipt
Planned Order Release
For a "lot size using Part Period" scheduling policy, determine the total cost for the 8 week period. Assume that inventory
is tracked at the beginning of the period. The number of units ordered can be a multiple of the Part Period, depending on
the computed net requirement in a week.
What is total number of units held in inventory during the planning period (i.e. weeks 1…
arrow_forward
5 Look at the flow chart showing the steps of the design process. Then read the list of
steps for designing a thermos. These steps are not in order. Write the letter of each
step in the appropriate box of the flow chart.
The Design Process
Find a problem
Keep records
Plan and build
a prototype
Keep records
Test and
improve
Keep records
Communicate
the solution
arrow_forward
The worker shown below is using a 10-lb pneumatic nut runner to tighten nuts within a tractor cab compartment. What are health and safety problems likely to result from her job? Evaluate the job and the
workstation identifying poor work design features. Please come up with at least five poor design features.
(Please refer to the format of the answers in the class example solution)
No.
1
2
3
4
園
5
Problem
Ergonomics Improvement
Design Principle
arrow_forward
The BOM for product A is shown in Figure 11.40, and datafrom the inventory records are shown in Table 11.9. In theMPS for product A, the MPS start row has 100 units in week 3and 200 in week 6. Develop the material requirements planfor the next 6 weeks for items C, D, and E.a. Develop the material requirements plan for the next6 weeks for items C, D, and E.b. What specific managerial actions are required inweek 1?
arrow_forward
Please answer this question,it really important for me
arrow_forward
The title of our study is "Design and Fabrication of an Agricultural Spraying Attachment for
an Autonomous Rover"
we need help in the machine design part of our study, specifically Pump selection, battery
selection, and center of gravity computation
Rover weight capacity 35 kilo grams (payload)
Rover measurements:
Wheel distance - 14.5 inches and 8.5 inches
Rover platform size (width & length) 14.4 inches x 10.4 inches
Height- 15.8 inches
arrow_forward
A specialty coffeehouse sells Colombian coffee at a fair rate of 300 kilograms annually. the beans are purchased from a local supplier for $3 per
kilogram. the coffeehouse estimates that it costs $50 in paperwork and labor to place an order for the coffee, and holding costs are based on a 10
percent annual interest rate.
a. determine the optimal order quantity for Coffee?
b. what is the time between the placement of orders?
C. what is the average optimal annual cost?
d. Suppose the coffee is ordered in a box of 50kg each. how many boxes should the coffee shop order?
A-
B.
問
arrow_forward
A Team of Engineers asked for an internal combustion engine to use it in a designed car. Your role is to describe the operation sequence of different types of available engines, explain their mechanical efficiency, and deliver a detailed technical report to show your approach in solving and discussing the following tasks and issues.
You must follow the following steps to help the team:
STEP 1
Describe the operational sequence of four-stroke spark ignition and four-stroke compression ignition engines with the aid of sketches by constructing simple sketch representing the operation and plotting the P-V diagrams for each process during the cycle to show the following:
The input and output heat and net output work
The expansion and compression strokes
The air-fuel mixture intake and exhaust gasses
The spark plug when it is in the active mode
The complete cycle of ideal Otto and Diesel cycles that shows the input and output heat and net output work.
STEP 2
Explain the mechanical…
arrow_forward
Your capstone design team is prototyping (e.g. you are building a model to test not a final product) a
"fire identification drone. The final product is intended to fly over rugged wilderness areas and look
for small fires that should be monitored and potentially fought or contained. It is NOT intended to be
used in large active fires. Your subteam's job is to design and build the support frame for the drone
(e.g. the structure where the motors, propellers, guidance electronics and GPS, heat sensors, radio
receiver and transmitter, etc. are attached) for the prototype. You have access to a machine shop
with saws, lathes (for removing material by rotating it and using a cutting tool), drills and a facility
with 3-D printers that can print a variety of plastics using fused deposition modeling (this is the
technique where a polymer filament is melted and forced through a nozzle to build a structure layer
by layer). You will be testing in a summer/fall timeframe so you expect temperatures…
arrow_forward
Your capstone design team is prototyping (e.g. you are building a model to test not a final product) a
"fire identification drone. The final product is intended to fly over rugged wilderness areas and look
for small fires that should be monitored and potentially fought or contained. It is NOT intended to be
used in large active fires. Your subteam's job is to design and build the support frame for the drone
(e.g. the structure where the motors, propellers, guidance electronics and GPS, heat sensors, radio
receiver and transmitter, etc. are attached) for the prototype. You have access to a machine shop
with saws, lathes (for removing material by rotating it and using a cutting tool), drills and a facility
with 3-D printers that can print a variety of plastics using fused deposition modeling (this is the
technique where a polymer filament is melted and forced through a nozzle to build a structure layer
by layer). You will be testing in a summer/fall timeframe so you expect temperatures…
arrow_forward
I need answers to questions 10, 11, and 12 pertaining to the print provided.
Note: A tutor keeps putting 1 question into 3 parts and wasted so many of my questions. Never had a issue before until now, please allow a different tutor to answer because I was told I am allowed 3 of these questions.
arrow_forward
The MPS start quantities for product A calls for the assembly department to begin final assembly accordingto the following schedule: 100 units in week 2; 200 units in week 4; 120 units in week 6; 180 units in week 7;and 60 units in week 8. Develop a material requirements plan for the next 8 weeks for items B, C, and D.The BOM for A is shown in Figure 11.26, and data from the inventory records are shown in Table 11.4.
arrow_forward
SEE MORE QUESTIONS
Recommended textbooks for you
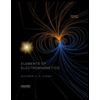
Elements Of Electromagnetics
Mechanical Engineering
ISBN:9780190698614
Author:Sadiku, Matthew N. O.
Publisher:Oxford University Press
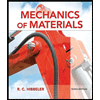
Mechanics of Materials (10th Edition)
Mechanical Engineering
ISBN:9780134319650
Author:Russell C. Hibbeler
Publisher:PEARSON
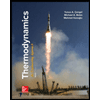
Thermodynamics: An Engineering Approach
Mechanical Engineering
ISBN:9781259822674
Author:Yunus A. Cengel Dr., Michael A. Boles
Publisher:McGraw-Hill Education
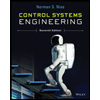
Control Systems Engineering
Mechanical Engineering
ISBN:9781118170519
Author:Norman S. Nise
Publisher:WILEY
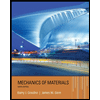
Mechanics of Materials (MindTap Course List)
Mechanical Engineering
ISBN:9781337093347
Author:Barry J. Goodno, James M. Gere
Publisher:Cengage Learning
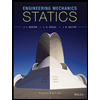
Engineering Mechanics: Statics
Mechanical Engineering
ISBN:9781118807330
Author:James L. Meriam, L. G. Kraige, J. N. Bolton
Publisher:WILEY
Related Questions
- Task 1: Produce a report by applying the concepts of engineering materials relating to a tricycle as shown in Figure 1, with the following incorporated: 3. Choose the most appropriate material from your point of view that can be used to produce the item/product with reasons discussed. Figure 1: Tricyclearrow_forwardCan you please answer these 3 questions from material engineering.....arrow_forwardExample 5 Material Balance Analysis A cannery receives on a given day: 12 tons of raw produce, 5 tons of cans, 0.5 ton of cartons, and 0.3 ton of miscellaneous materials. Its output includes: 10 tons of processed product, the remaining becoming part of waste, four tons of the cans are stored for future use and the remainder are used to package the produce. About 3 percent of the cans used are damaged and recycled. The cartons are also used for packaging, except for 3 percent which become damaged and are incinerated with other paper wastes. of the miscellaneous materials, 75 percent become paper wastes that are incinerated, and the remainder are disposed of by the municipal collection agency. Draw a materials flow diagram for this activity. Solutionarrow_forward
- TWM Company purchases 8000 units of product each year at a unit cost of $10.00. The order cost is $30.00 per order, and the holding cost per unit per year is $3.00. a) What are the economic order quantity, the total annual cost, the number of orders to place in one year, and the reorder point when the lead time is two weeks? b) What happens to the EOQ if backordering is possible and the stockout cost per unit per year is $1.00? c) The supplier is offering a special discount and has temporarily reduced his unit price from $10.00 to $9.00. What amount should be purchased to take advantage of the discount? d) The supplier will increase his unit price from $10.00 to $11.00 on 1 January. What amount should be purchased and delivered on 31 December before the price increase is effective if the stock position is 346 units? What will be the cost saving of the special purchasearrow_forwardItem A is one of the products manufactured at ABC Manufacturing. • Each order for producing the product has a cost of $300/order, regardless of the number of units ordered. . The lead time for placing the order is 2 week(s). • The inventory cost is $3/unit/week and the on-hand inventory at the beginning of week 1 is 145 units. The gross requirement for Item A is specified for the beginning of weeks 1 through 8 in the table that follows. Item A Week 1 Week 2 Week 3 Week 4 Week 5 Week 6 Week 7 Week 8 60 65 0 90 0 55 95 85 Gross Requirement On-hand Inventory Net Requirement Planned Order Receipt Planned Order Release For a "lot size using Part Period" scheduling policy, determine the total cost for the 8 week period. Assume that inventory is tracked at the beginning of the period. The number of units ordered can be a multiple of the Part Period, depending on the computed net requirement in a week. What is total number of units held in inventory during the planning period (i.e. weeks 1…arrow_forward5 Look at the flow chart showing the steps of the design process. Then read the list of steps for designing a thermos. These steps are not in order. Write the letter of each step in the appropriate box of the flow chart. The Design Process Find a problem Keep records Plan and build a prototype Keep records Test and improve Keep records Communicate the solutionarrow_forward
- The worker shown below is using a 10-lb pneumatic nut runner to tighten nuts within a tractor cab compartment. What are health and safety problems likely to result from her job? Evaluate the job and the workstation identifying poor work design features. Please come up with at least five poor design features. (Please refer to the format of the answers in the class example solution) No. 1 2 3 4 園 5 Problem Ergonomics Improvement Design Principlearrow_forwardThe BOM for product A is shown in Figure 11.40, and datafrom the inventory records are shown in Table 11.9. In theMPS for product A, the MPS start row has 100 units in week 3and 200 in week 6. Develop the material requirements planfor the next 6 weeks for items C, D, and E.a. Develop the material requirements plan for the next6 weeks for items C, D, and E.b. What specific managerial actions are required inweek 1?arrow_forwardPlease answer this question,it really important for mearrow_forward
- The title of our study is "Design and Fabrication of an Agricultural Spraying Attachment for an Autonomous Rover" we need help in the machine design part of our study, specifically Pump selection, battery selection, and center of gravity computation Rover weight capacity 35 kilo grams (payload) Rover measurements: Wheel distance - 14.5 inches and 8.5 inches Rover platform size (width & length) 14.4 inches x 10.4 inches Height- 15.8 inchesarrow_forwardA specialty coffeehouse sells Colombian coffee at a fair rate of 300 kilograms annually. the beans are purchased from a local supplier for $3 per kilogram. the coffeehouse estimates that it costs $50 in paperwork and labor to place an order for the coffee, and holding costs are based on a 10 percent annual interest rate. a. determine the optimal order quantity for Coffee? b. what is the time between the placement of orders? C. what is the average optimal annual cost? d. Suppose the coffee is ordered in a box of 50kg each. how many boxes should the coffee shop order? A- B. 問arrow_forwardA Team of Engineers asked for an internal combustion engine to use it in a designed car. Your role is to describe the operation sequence of different types of available engines, explain their mechanical efficiency, and deliver a detailed technical report to show your approach in solving and discussing the following tasks and issues. You must follow the following steps to help the team: STEP 1 Describe the operational sequence of four-stroke spark ignition and four-stroke compression ignition engines with the aid of sketches by constructing simple sketch representing the operation and plotting the P-V diagrams for each process during the cycle to show the following: The input and output heat and net output work The expansion and compression strokes The air-fuel mixture intake and exhaust gasses The spark plug when it is in the active mode The complete cycle of ideal Otto and Diesel cycles that shows the input and output heat and net output work. STEP 2 Explain the mechanical…arrow_forward
arrow_back_ios
SEE MORE QUESTIONS
arrow_forward_ios
Recommended textbooks for you
- Elements Of ElectromagneticsMechanical EngineeringISBN:9780190698614Author:Sadiku, Matthew N. O.Publisher:Oxford University PressMechanics of Materials (10th Edition)Mechanical EngineeringISBN:9780134319650Author:Russell C. HibbelerPublisher:PEARSONThermodynamics: An Engineering ApproachMechanical EngineeringISBN:9781259822674Author:Yunus A. Cengel Dr., Michael A. BolesPublisher:McGraw-Hill Education
- Control Systems EngineeringMechanical EngineeringISBN:9781118170519Author:Norman S. NisePublisher:WILEYMechanics of Materials (MindTap Course List)Mechanical EngineeringISBN:9781337093347Author:Barry J. Goodno, James M. GerePublisher:Cengage LearningEngineering Mechanics: StaticsMechanical EngineeringISBN:9781118807330Author:James L. Meriam, L. G. Kraige, J. N. BoltonPublisher:WILEY
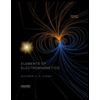
Elements Of Electromagnetics
Mechanical Engineering
ISBN:9780190698614
Author:Sadiku, Matthew N. O.
Publisher:Oxford University Press
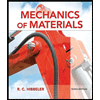
Mechanics of Materials (10th Edition)
Mechanical Engineering
ISBN:9780134319650
Author:Russell C. Hibbeler
Publisher:PEARSON
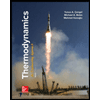
Thermodynamics: An Engineering Approach
Mechanical Engineering
ISBN:9781259822674
Author:Yunus A. Cengel Dr., Michael A. Boles
Publisher:McGraw-Hill Education
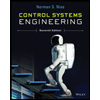
Control Systems Engineering
Mechanical Engineering
ISBN:9781118170519
Author:Norman S. Nise
Publisher:WILEY
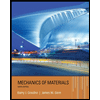
Mechanics of Materials (MindTap Course List)
Mechanical Engineering
ISBN:9781337093347
Author:Barry J. Goodno, James M. Gere
Publisher:Cengage Learning
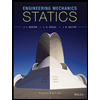
Engineering Mechanics: Statics
Mechanical Engineering
ISBN:9781118807330
Author:James L. Meriam, L. G. Kraige, J. N. Bolton
Publisher:WILEY