Team-19_Lab-2_Charpy_Impact_Test
pdf
keyboard_arrow_up
School
University of Ottawa *
*We aren’t endorsed by this school
Course
2360
Subject
Mechanical Engineering
Date
Jan 9, 2024
Type
Pages
14
Uploaded by AmbassadorMetal9316
CHARPY IMPACT TEST OF 1018 STEEL AT DUCTILE-TO-BRITTLE TRANSITION TEMPERATURES
Engineering Materials I MCG 2360[B] Laboratory Report Lab 2: Charpy Impact Test Team #19 Student Number Name 300241579 Gautam Mehta 300298485 George Lai 300298002 Phone Thant Htet 300293604 Ryan Gorodezky Experiment Date: November 3, 2023 Date Submitted: November 17, 2023 Professor: Dr. Nafisa Bano TA: Behrang Asghari Shirvani Faculty of Engineering Department of Mechanical Engineering 2023
1 Abstract In this experiment, the Charpy Impact test was conducted in order to determine the impact energy (K) absorbed by the Steel samples at 3 different temperatures. The Charpy impact test consists of a hammer attached to a rod which swings from an initial height creating a pendulum motion. The impact energy depends on gravity, mass, and the initial/maximum height of the hammer. The impact energy can then be used to calculate the impact toughness, which is proportional to the cross-sectional area of the sample. The calculation requires dividing the impact energy with the area. The three identical samples of 1018 Steel were tested at different temperatures of -80°C, 21°C (Room temperature), and 100°C. These samples are 55x10x10 mm and are fabricated with this experiment in mind to include a Charpy V-notch design, that is in line with ASTM E-23 Standard. A 2 mm deep cut at the midline at an angle of 45 degrees is included. The ‘V
-
notch’ focuses the energy and promotes a consistent fracture result. The main purpose of this lab is to show how the mechanical properties of a metal can be altered by temperature. A major factor to consider when analyzing the results of this lab is whether the sample displays brittle or ductile behavior when fractured. The transition between brittle and ductile happens at the transition temperature, where the energy absorbed on impact is quickly increasing. By assumption, the sample at -80°C will absorb less energy and display a brittle fracture, whereas it is predicted that the sample at room temperature and 100°C will display a Ductile fracture, with the 100°C sample absorbing more energy.
2 1.
Table of Contents Abstract ...........................................................................................................................................
1
1.
Introduction .............................................................................................................................
1
1.1
Objective ..........................................................................................................................
1
1.1.1
Equipment and Materials ..........................................................................................
1
2.
Methodology ...........................................................................................................................
2
3.
Results and Discussion ...........................................................................................................
2
3.1
Results ..............................................................................................................................
2
3.2
Charpy Impact test and material structure variation with temperature ............................
6
3.3
Discussion ........................................................................................................................
6
3.4
Sample Calculations .........................................................................................................
9
4.
Conclusion ............................................................................................................................
10
References .....................................................................................................................................
11
Your preview ends here
Eager to read complete document? Join bartleby learn and gain access to the full version
- Access to all documents
- Unlimited textbook solutions
- 24/7 expert homework help
LAB 2: CHARPY IMPACT TEST 1 1.
Introduction The impact test is a high-strain rate assessment of the material properties where a hammer attached to an arm will drop in a pendulum motion and impact the test specimen. The critical part of this experiment is the samples which will be prefabricated into the Charpy V-notch design which is a 55x10x10 mm rectangular specimen with a 2 mm deep cut at the midline at an angle off 45 degrees (the sample dimensions should follow the ASTM E-23 standard). This notch will focus the energy during the experiment. This lab report will compare the different impact strengths and energy absorbed on impact by three specimens of ASTM E-23 standard 1018 Steel at three different temperatures of 100°C, room temperature at 21°C and -80°C. The report will also illustrate how the mechanical properties of a sample can be affected by the temperature shown in ductile-brittle transition temperature graphs of the material. 1.1
Objective The objective of this lab report is to measure the impact energy, and calculate the impact toughness, of 1018 Steel V-notch samples at three different temperature that corresponds to differing areas of the ductile-to-brittle transition temperature relationship. The report will also illustrate how mechanical properties of a sample can vary depending on the temperature by ductile-
brittle transition temperature of the material. 1.1.1
Equipment and Materials To exert impact on the specimen a Zwick-Roell pendulum impact testing machine will be used. Test subjects will be samples of 1018 annealed steel that are prefabricated Charpy notched specimens in line with ASTM standard E-
23 for “Notched bar impact testing of metallic materials”.
LAB 2: CHARPY IMPACT TEST 2 2.
Methodology Three samples of 1018 Steel V-notch samples are collected to be tested at three different temperatures. A sample is placed in a Styrofoam container with dry ice to lower the temperature of the sample to approximately -80°C. Another sample is placed in boiling water to increase the temperature of the sample to 100°C. The remaining sample is kept at room temperature which was round 21°C. To initiate the testing phase, the Zwick-Roell RKP200 Pendulum impact testing machine
’s power breaker and secondary power switch is turned on. The hammer-arm is ensured to be retraced and locked. When the samples are at their respective temperatures, custom forceps are used to place the specimen in the holder with the notch facing away from the hammer. The field is inspected to be clear of obstructions and the access door is closed. The dial is set so that the arm is at zero. The hammer is released, after the hammer breaks the specimen, the pendulum is halted and retracted. Upon completion of the testing phase, the energy value recorded on the dial is recorded with their respective temperatures. The fractured samples are retrieved to access the fracture. The collected data will be used to plot the fracture energy over the temperature for the three materials and discussion will be made on how the structure of the material is dependent on temperature. 3.
Results and Discussion 3.1
Results This section of the lab report will present the results of the Charpy impact test of 1018 annealed steel Charpy notched specimens in line with ASTM Standard E-23. The test is performed 4 times to get 4 data sets at the same temperature range. These data sets will be plotted to visualize the change in material ductility with respect to temperature. Table 1: Data from Charpy Impact Test
LAB 2: CHARPY IMPACT TEST 3 Data Set W (J) 100°C 21°C -80°C 1 259 195 7 2 252 205 8 3 255 199 7 4 260 196 9 Average 256.5 198.75 7.75 Below are the plots the fracture energy over the temperature for the three material conditions. Figure 3.1: Graph of Fracture Energy Over Temperature for Data Set 1
Your preview ends here
Eager to read complete document? Join bartleby learn and gain access to the full version
- Access to all documents
- Unlimited textbook solutions
- 24/7 expert homework help
LAB 2: CHARPY IMPACT TEST 4 Figure 3.2: Graph of Fracture Energy Over Temperature for Data Set 2 Figure 3.3: Graph of Fracture Energy Over Temperature for Data Set 3
LAB 2: CHARPY IMPACT TEST 5 Figure 3.4: Graph of Fracture Energy Over Temperature for Data Set 4 An mean value of each data point is found and plotted for a more accurate representation of how the material properties changes according to their respective temperature. Figure 3.5: Graph of Fracture Energy Over Temperature for the Average
LAB 2: CHARPY IMPACT TEST 6 3.2
Charpy Impact test and material structure variation with temperature In conducting the Charpy Impact test, the objective is to quantitatively assess the energy absorbed by materials, such as steel, during fracture, a key indicator of material toughness under various thermal conditions. At markedly low temperatures, specifically –
70°C, steel manifests a heightened brittleness, characterized by a reduced capacity to absorb energy prior to fracturing. This results in a fracture that is abrupt and exhibits minimal plastic deformation. At room temperature, steel presents an equilibrium between ductility and strength, leading to an intermediate level of energy absorption and a fracture pattern that displays both brittle and ductile characteristics. Conversely, at elevated temperatures, such as 100°C, an increase in the ductility of steel is observed. This enhanced ductility facilitates greater plastic deformation, allowing the material to absorb more energy before fracturing, which is indicative of increased toughness. These observations from the Charpy Impact test provide critical insights into the variations in the internal structure of steel across different temperature regimes, thereby underscoring the dynamic nature of material toughness in response to thermal changes. 3.3
Discussion In steel, the interplay between carbon content and its mechanical properties, particularly strength and hardness versus ductility and toughness. As the carbon content in steel increases, its strength and hardness typically rise. Since Carbon atoms are smaller than iron atoms. The carbon atoms distort the lattice structure in iron when they occupy interstitial positions in the iron lattice. This distortion hampers the movement of dislocations, which are defects in the lattice that allow for plastic deformation. This makes high-carbon steel exceptionally strong and hard, suitable for applications requiring resistance to wear and deformation. However, this increase in strength and hardness comes at the cost of reduced ductility and toughness. High-carbon steels, while hard, are also more brittle, making them more susceptible to cracking under stress or impact. This brittleness
Your preview ends here
Eager to read complete document? Join bartleby learn and gain access to the full version
- Access to all documents
- Unlimited textbook solutions
- 24/7 expert homework help
LAB 2: CHARPY IMPACT TEST 7 is a critical limitation in applications where flexibility and impact resistance are essential. The observation that steel exhibits greater brittleness at low temperatures, as evidenced by the more jagged or jarred edges at the fracture point in comparison to smoother edges when the same material was tested at room temperature and high temperatures. Therefore, it can be reasonably inferred that to mitigate the occurrence of brittle fracture, maintaining the steel at room temperature or elevating it to higher temperatures is beneficial, as this promotes a more ductile fracture response. The fracture resistance of the tested samples was dependent on the energy absorption of the metal. Since higher temperatures increase the energy absorption of the metal, the fracture resistance also increases with heat. The surfaces of the fracture also changed with the temperature. The ductile to brittle transition temperature for steel is 0°C. Between our tests at 21°C and -80°C, the fracture energy greatly decreases, indicating that the transition temperature lines in between these two temperatures. The ductile to brittle temperature that was found lies in between 21°C and -80°C, which is expected. The ideal temperature for the metal to avoid sudden brittle fracture upon impact is any temperature above the ductile to brittle transition temperature which is around 0°C. The 100°C sample plastically deformed when hammer contacted the steel and did not completely break. The sample at -80°C was extremely brittle and fractured rapidly. The sample at 20°C was close to the fracture point and underwent plastic deformation. These results align with our understanding of fracture energy and temperature. Steel becomes more ductile at higher temperatures and as a result it plastically deforms instead of undergoing a fracture when the hammer hits it. Steel becomes more brittle when at lower temperatures, as a result it is more susceptible to brittle fractures. When the hammer hit the sample at -80°C it fractured quickly.
LAB 2: CHARPY IMPACT TEST 8 Under room temperature, steel is a very tough and durable material, as a result it won’t plastically deform or fracture easily. The possible sources of error include temperatures of the metals are not precisely monitored and can affect the results. The lack of sample data has impeded us while making the graph and forced us to make gross assumptions for the ductile to brittle transition temperature. The sample size needs to increase and include a wider range of steel samples at different temperatures.
LAB 2: CHARPY IMPACT TEST 9 3.4
Sample Calculations
Your preview ends here
Eager to read complete document? Join bartleby learn and gain access to the full version
- Access to all documents
- Unlimited textbook solutions
- 24/7 expert homework help
LAB 2: CHARPY IMPACT TEST 10 4.
Conclusion In conclusion, by completing the Charpy Impact test, it was determined that a sample of steel will deform in a brittle or ductile manner depending on the temperature of the metal at the time of impact. At -80°C, the sample only absorbed an average of 7.75 J of energy which resulted in a quick brittle break. At 21°C & 100°C, the average fracture energy was 198.75 J & 256.5 J respectively. The high fracture energy observed in these temperatures which are past the transition temperature result in plastic deformation. To avoid brittle fractures, 1018 Steel should be kept above 0°C, which was observed to be roughly the average transition temperature.
11 References •
N. Bano, B.A. Shirvani, X. Xie, Data - Lab 2 –
Charpy Impact Test, University of Ottawa, Department of Mechanical Engineering, 2023 •
Zwick-Roell, Product Information HIT450P/HIT300P Pendulum Impact Tester for Metal Specimens, 2023, https://www.zwickroell.com/products/products-for-impact-
testing/pendulum-impact-testers-for-tests-on-metals/
Related Documents
Related Questions
How did temperature affect the toughness of the specimens?
arrow_forward
NEED IN RUSH
THANK YOU
arrow_forward
Mild steel 1
Young;s modulus 1219.5
Yield strain and stress (0.4101,500.08)
Failure stress and strain :not able to find because the given data shows the experiment did not reach the failure point.
if the material stress and strain does not reach a failure point ,what dose it means , does it means that the material is more stronger?
arrow_forward
6. The following engineering stress-strain data were obtained for 0.2% C plain
carbon steel.
(a) Plot the engineering stress-strain curve
(b) Determine the ultimate tensile strength for the alloy
(c) Determine the percent elongation at fracture
(d) Plot the true stress-strain curve
Engineering strain, in./in.
Engineering stress, ksi
30
0.001
55
0.002
60
0.005
68
0.01
72
0.02
74
0.04
75
0.06
76
0.08
75
0.1
73
0.12
69
0.14
65
0.16
56
0.18
51
0.19(fracture)
arrow_forward
Question 2
Figure 2 shows the dependence of fatigue strength on testing cycles (S-N curve) of an acetal
polymer.
60
50
40
30
20
10
104
105
106
107
108
Number of cycles to failure
Figure 2 The S-N fatigue curve for an acetal polymer
a. What is the fatigue strength, or maximum stress amplitude, at one million cycles of
loading?
b. An acetal polymer 30-cm-long bar with a diameter of 20 mm is designed to survive
one million cycles of loading, what is the maximum allowable axial load that can be
applied on one end of the bar?
Magnitude of stress
Reversal, MPa
arrow_forward
Need help with this Mechanics of Materials review
arrow_forward
Test Specimen
4140 CF steel
6061 T6 Al
Gray Cast iron 40
FC Brass 360
Impact Energy (J or ft-lb)
48.5 ft-lb
25 ft-lb
12 ft-lb
27 ft-lb
Impact Strength (J/m
or ft-lb/in)
123.096 ft-lb/in
63.452 ft-lb/in
What is the final analysis/ overall observation from the data?
30.457 ft-lb/in
68.528 ft-lb/in
arrow_forward
Figure 1 shows the tensile testing results for different materials. All specimens have an initial
diameter of 12 mm and an initial gauge length of 50 mm.
300
250
Low carbon steel
Network polymer
200
Crystalline polymer
150
Amorphous polymer
100
50
5
10
15
20
25
30
Strain (%)
Figure 1: Stress-strain curve
b. Determine the following parameters for each material:
• the tensile strength
the 0.2% offset yield strength
the modulus of elasticity
• the ductility
Stress (MPa)
LO
arrow_forward
UzNDU3NTYyMjk0/a/MjYOMzAwMjMOOTM5/details
Further questions
4.The graphs show how the extension changes with stretching force for four different materials.
a. Which two graphs show materials that follow Hooke's law?
A
B
b. Which two graphs show materials that become less stiff as
they are stretched?
force
force
D
C. Which graph shows a material that maintains the same
stiffness throughout?
force
force
1. A force of 20N stretches a spring by 0.5m. The spring obeys Hooke's law.
a. Calculate the spring constant including a suitable unit.
b. How much force must a man use to stretch it by 1.5m?
5. A car has a weight of 240OON which is distributed equally over all four wheels. Each wheel has a spring of
spring constant 400N/cm.
a.
Determine the force through the spring on each wheel.
b. Calculate the compression of each spring when the car rests on the ground.
6.In a spring experiment the results were as follows:
Force (N)
Length (mpm
1
2
4
6.
7
50
58
70
74
82
9n
102
125
LELL
arrow_forward
Stuck need help!
Problem is attached. please view attachment before answering.
Really struggling with this concept.
Please show all work so I can better understand !
Thank you so much.
arrow_forward
Following is the Tensile stress-strain data for several hypothetical metals to be used.
Answer the following questions referring to table 1.1.
Table 1.1: Material Property Data
Material Tensile Strength
Fracture Strength Strain at Strength
(MPa)
(MPa)
340
265
550
505
112
150
Fracture before yielding
A
B
C
D
0.23
0.15
0.40
a. Which will experience the greatest percent reduction in area? Why?
b. Which is the strongest? Why?
c. Which is the stiffest? Why?
Elastic Modulus
(GPa)
210
310
180
400
arrow_forward
Carbonitriding is a case-hardening process in which a steel is heated in a gaseous atmosphere of such composition that carbon and nitrogen are absorbed simultaneously. Carbonitriding is a modification of the nitriding process.
True
False
Based upon the percent elongation of a tensile sample, a ductile engineering material is defined by a value equal to or greater than 5% and a brittle material is defined by a value less than 5%.
True
False
arrow_forward
Question 5:
Following is tabulated data that were gathered from a series of Charpy impact tests on a
tempered 4140 steel alloy.
Temperature (°C)
100
75
50
25
0
-25
-50
-65
-75
-85
-100
-125
-150
-175
Impact Energy (J)
89.3
88.6
87.6
85.4
82.9
78.9
73.1
66.0
59.3
47.9
34.3
29.3
27.1
25.0
(a) Plot the data as impact energy versus temperature. (you can use Excel or other
software).
(b) Determine a ductile-to-brittle transition temperature as that temperature
corresponding to the average of the maximum and minimum impact energies.
(c) Determine a ductile-to-brittle transition temperature as that temperature at which the
impact energy is 70 J.
arrow_forward
Small Question please answer
arrow_forward
1. What is the approximate ductility (%EL) of a cold worked brass that has a yield strength of 345 MPa (50,000 psi)
140
120
1040 Steel
1040 Steel
120
700
600
100
500
Brass
Brass eo
S400
Brass
300
Copper
40
200
Copper
040 e
00
40
Copper
100
O 10 20 30 40 50 60 70
Percent cold work
200
0 10 20 30 40 50 60 70
Percent cold work
O 10 20 30 40 D0 60 70
Percent cold work
(a)
(b)
arrow_forward
Cyclic Stresses (Fatigue); The S-N Curve
4. The fatigue data for a ductile cast iron are given as follows:
Cycles to Failure
Stress
Amplitude
[MPa (ksi)]
248 (36.0)
236 (34.2)
224 (32.5)
213 (30.9)
201 (29.1)
193 (28.0)
193 (28.0)
193 (28.0)
1 × 105
3 x 105
1 x 10⁰
3 x 106
1 x 107
3 x 107
1 108
3 × 108
(a) Make an S-N plot (stress amplitude versus logarithm cycles to failure) using these data.
(b) What is the fatigue limit for this alloy?
(c) Determine fatigue lifetimes at stress amplitudes of 230 MPa (33,500 psi) and 175 MPa (25,000
psi).
(d) Estimate fatigue strengths at 2 × 105 and 6 × 106 cycles.
arrow_forward
I need the answer as soon as possible
arrow_forward
The answer is one of the options below please solve carefully and circle the correct option Please write clear .
arrow_forward
Tensile engineering stress-strain curves through failure are depicted below.
Which specimen features the highest toughness?
Engineering Stress, MPa
1800-
1600-
1400-
1200-
1000-
800-
600-
400-
200-
Ol
0
Aluminum Alloy 2024-T81
0.04
0.08
Stainless Steel (18-8)
1340 Steel, Water-Quenched
& Tempered at 370 C
Magnesium
0.12
Structural Steel (Mild Steel)
Engineering Strain
0.16
1340 Steel, Water-Quenched & Tempered at 370°C
Aluminum Alloy 2024-T81
Structural Steel (Mild Steel)
Stainless Steel (18-8)
Magnesium
0.20
0.24
arrow_forward
5. The following data were collected from a standard 0.505-in.-diameter test
specimen of a copper alloy (initial length lo= 2.0 in.). After fracture, the total
length was 3.014 in. and the diameter was 0.374 in.
Load
(Ib)
Al
(in.)
00000
3,000
6,000
0.00167
0.00333
7,500
0.00417
9,000
10,500
0.0090
0.040
12,000
0.26
12,400
11,400
0.50 (maximum load)
1.02 (fracture)
a)
Plot the data as engineering stress versus engineering strain.
b)
Compute the modulus of elasticity.
c)
Determine the yield strength at a strain offset of 0.002.
d)
Determine the tensile strength of this alloy.
e)
What is the approximate ductility, in percent elongation?
f)
Compute the modulus of resilience.
g)
Compute from the data and plot true stress versus true strain diagram.
arrow_forward
SEE MORE QUESTIONS
Recommended textbooks for you
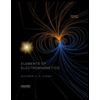
Elements Of Electromagnetics
Mechanical Engineering
ISBN:9780190698614
Author:Sadiku, Matthew N. O.
Publisher:Oxford University Press
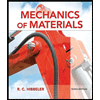
Mechanics of Materials (10th Edition)
Mechanical Engineering
ISBN:9780134319650
Author:Russell C. Hibbeler
Publisher:PEARSON
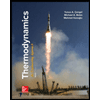
Thermodynamics: An Engineering Approach
Mechanical Engineering
ISBN:9781259822674
Author:Yunus A. Cengel Dr., Michael A. Boles
Publisher:McGraw-Hill Education
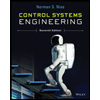
Control Systems Engineering
Mechanical Engineering
ISBN:9781118170519
Author:Norman S. Nise
Publisher:WILEY
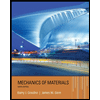
Mechanics of Materials (MindTap Course List)
Mechanical Engineering
ISBN:9781337093347
Author:Barry J. Goodno, James M. Gere
Publisher:Cengage Learning
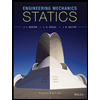
Engineering Mechanics: Statics
Mechanical Engineering
ISBN:9781118807330
Author:James L. Meriam, L. G. Kraige, J. N. Bolton
Publisher:WILEY
Related Questions
- How did temperature affect the toughness of the specimens?arrow_forwardNEED IN RUSH THANK YOUarrow_forwardMild steel 1 Young;s modulus 1219.5 Yield strain and stress (0.4101,500.08) Failure stress and strain :not able to find because the given data shows the experiment did not reach the failure point. if the material stress and strain does not reach a failure point ,what dose it means , does it means that the material is more stronger?arrow_forward
- 6. The following engineering stress-strain data were obtained for 0.2% C plain carbon steel. (a) Plot the engineering stress-strain curve (b) Determine the ultimate tensile strength for the alloy (c) Determine the percent elongation at fracture (d) Plot the true stress-strain curve Engineering strain, in./in. Engineering stress, ksi 30 0.001 55 0.002 60 0.005 68 0.01 72 0.02 74 0.04 75 0.06 76 0.08 75 0.1 73 0.12 69 0.14 65 0.16 56 0.18 51 0.19(fracture)arrow_forwardQuestion 2 Figure 2 shows the dependence of fatigue strength on testing cycles (S-N curve) of an acetal polymer. 60 50 40 30 20 10 104 105 106 107 108 Number of cycles to failure Figure 2 The S-N fatigue curve for an acetal polymer a. What is the fatigue strength, or maximum stress amplitude, at one million cycles of loading? b. An acetal polymer 30-cm-long bar with a diameter of 20 mm is designed to survive one million cycles of loading, what is the maximum allowable axial load that can be applied on one end of the bar? Magnitude of stress Reversal, MPaarrow_forwardNeed help with this Mechanics of Materials reviewarrow_forward
- Test Specimen 4140 CF steel 6061 T6 Al Gray Cast iron 40 FC Brass 360 Impact Energy (J or ft-lb) 48.5 ft-lb 25 ft-lb 12 ft-lb 27 ft-lb Impact Strength (J/m or ft-lb/in) 123.096 ft-lb/in 63.452 ft-lb/in What is the final analysis/ overall observation from the data? 30.457 ft-lb/in 68.528 ft-lb/inarrow_forwardFigure 1 shows the tensile testing results for different materials. All specimens have an initial diameter of 12 mm and an initial gauge length of 50 mm. 300 250 Low carbon steel Network polymer 200 Crystalline polymer 150 Amorphous polymer 100 50 5 10 15 20 25 30 Strain (%) Figure 1: Stress-strain curve b. Determine the following parameters for each material: • the tensile strength the 0.2% offset yield strength the modulus of elasticity • the ductility Stress (MPa) LOarrow_forwardUzNDU3NTYyMjk0/a/MjYOMzAwMjMOOTM5/details Further questions 4.The graphs show how the extension changes with stretching force for four different materials. a. Which two graphs show materials that follow Hooke's law? A B b. Which two graphs show materials that become less stiff as they are stretched? force force D C. Which graph shows a material that maintains the same stiffness throughout? force force 1. A force of 20N stretches a spring by 0.5m. The spring obeys Hooke's law. a. Calculate the spring constant including a suitable unit. b. How much force must a man use to stretch it by 1.5m? 5. A car has a weight of 240OON which is distributed equally over all four wheels. Each wheel has a spring of spring constant 400N/cm. a. Determine the force through the spring on each wheel. b. Calculate the compression of each spring when the car rests on the ground. 6.In a spring experiment the results were as follows: Force (N) Length (mpm 1 2 4 6. 7 50 58 70 74 82 9n 102 125 LELLarrow_forward
- Stuck need help! Problem is attached. please view attachment before answering. Really struggling with this concept. Please show all work so I can better understand ! Thank you so much.arrow_forwardFollowing is the Tensile stress-strain data for several hypothetical metals to be used. Answer the following questions referring to table 1.1. Table 1.1: Material Property Data Material Tensile Strength Fracture Strength Strain at Strength (MPa) (MPa) 340 265 550 505 112 150 Fracture before yielding A B C D 0.23 0.15 0.40 a. Which will experience the greatest percent reduction in area? Why? b. Which is the strongest? Why? c. Which is the stiffest? Why? Elastic Modulus (GPa) 210 310 180 400arrow_forwardCarbonitriding is a case-hardening process in which a steel is heated in a gaseous atmosphere of such composition that carbon and nitrogen are absorbed simultaneously. Carbonitriding is a modification of the nitriding process. True False Based upon the percent elongation of a tensile sample, a ductile engineering material is defined by a value equal to or greater than 5% and a brittle material is defined by a value less than 5%. True Falsearrow_forward
arrow_back_ios
SEE MORE QUESTIONS
arrow_forward_ios
Recommended textbooks for you
- Elements Of ElectromagneticsMechanical EngineeringISBN:9780190698614Author:Sadiku, Matthew N. O.Publisher:Oxford University PressMechanics of Materials (10th Edition)Mechanical EngineeringISBN:9780134319650Author:Russell C. HibbelerPublisher:PEARSONThermodynamics: An Engineering ApproachMechanical EngineeringISBN:9781259822674Author:Yunus A. Cengel Dr., Michael A. BolesPublisher:McGraw-Hill Education
- Control Systems EngineeringMechanical EngineeringISBN:9781118170519Author:Norman S. NisePublisher:WILEYMechanics of Materials (MindTap Course List)Mechanical EngineeringISBN:9781337093347Author:Barry J. Goodno, James M. GerePublisher:Cengage LearningEngineering Mechanics: StaticsMechanical EngineeringISBN:9781118807330Author:James L. Meriam, L. G. Kraige, J. N. BoltonPublisher:WILEY
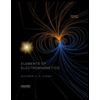
Elements Of Electromagnetics
Mechanical Engineering
ISBN:9780190698614
Author:Sadiku, Matthew N. O.
Publisher:Oxford University Press
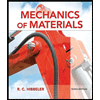
Mechanics of Materials (10th Edition)
Mechanical Engineering
ISBN:9780134319650
Author:Russell C. Hibbeler
Publisher:PEARSON
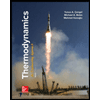
Thermodynamics: An Engineering Approach
Mechanical Engineering
ISBN:9781259822674
Author:Yunus A. Cengel Dr., Michael A. Boles
Publisher:McGraw-Hill Education
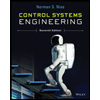
Control Systems Engineering
Mechanical Engineering
ISBN:9781118170519
Author:Norman S. Nise
Publisher:WILEY
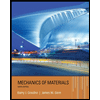
Mechanics of Materials (MindTap Course List)
Mechanical Engineering
ISBN:9781337093347
Author:Barry J. Goodno, James M. Gere
Publisher:Cengage Learning
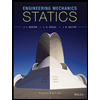
Engineering Mechanics: Statics
Mechanical Engineering
ISBN:9781118807330
Author:James L. Meriam, L. G. Kraige, J. N. Bolton
Publisher:WILEY