Failure Analysis Methods in Industrial and Systems Engineering
docx
keyboard_arrow_up
School
University of Florida *
*We aren’t endorsed by this school
Course
3246
Subject
Mechanical Engineering
Date
Apr 3, 2024
Type
docx
Pages
11
Uploaded by GrandJaguarMaster265
1 | P a g e F a i l u r e a n a l y s i s m e t h o d s i n M e c h E n g i n e e r i n g
Failure Analysis Methods in Industrial and Systems Engineering
ENC3246
University of Florida
10.14.2022
2 | P a g e F a i l u r e a n a l y s i s m e t h o d s i n M e c h E n g i n e e r i n g
Failure analysis methods in Mech Engineering I.
Common Types of failures in Mechanical engineering
..............................................................
3
A.
Types of failures
..............................................................................................................................
3
B.
Cause of failure
................................................................................................................................
5
II.
Failure Analysis methods
.............................................................................................................
6
C.
Preventative methods
.....................................................................................................................
6
1)
Destructive and non-destructive methods
........................................................................................
6
D.
Forensic methods
.............................................................................................................................
7
1)
Destructive and non-destructive
......................................................................................................
7
2)
Standards in mechanical engineering
...............................................................................................
7
III.
Case Study
......................................................................................................................................
8
E.
Description
.....................................................................................................................................
8
F.
Investigation
....................................................................................................................................
8
G.
Recommendations
.........................................................................................................................
10
IV.
References
....................................................................................................................................
11
3 | P a g e F a i l u r e a n a l y s i s m e t h o d s i n M e c h E n g i n e e r i n g
I.
Common Types of failures in Mechanical engineering
Mechanical engineering is a branch of engineering specialized in processing energy forms and translate it into any desired motion. Engineers in this area perform from the general to the most specific tasks. Going through the design, manufacture and testing processes of devices that alter, transform, and use energy to create any type of motion.[1] Mechanical engineers are constantly exposed to failures in their products, which they try to predict and evade through, dynamics, statics, and mechanic of materials analysis. Although, currently through simulations with CAD programs, failures can be easier predicted and before the production and testing phase.
A.
Types of failures Mechanical engineers often find failures in their mechanical systems. Much of what is taught in engineering school needs to be put in practice. To maximize the accuracy of these devices, engineers must understand the basics of mechanics of mechanic materials, statics, and dynamics. They must be aware of the definitions and features of stress, deformation, slip, fracture, tension, and compression.[1] Which lead us to the four mechanical failures: Erosion, corrosion, Fatigue, and overload.[6]
Mechanisms are commonly exposed to erosion, which implies a set of material removal through a series of impacts from a substance independent from the mechanism. Even while each collision only removes a tiny amount of material, the overall damage is frequently substantial. If you employ particles with sharp edges, erosion can get worse.[7] The effect might not be apparent until it is too late if the degraded surface is an internal surface that is not visible. In the worst-case scenario, a hole has already developed. Erosion is a common and dangerous failure that is exhaustingly analyzed by mechanical engineering. But, not considered by materials engineers in the design phase of a device.
Your preview ends here
Eager to read complete document? Join bartleby learn and gain access to the full version
- Access to all documents
- Unlimited textbook solutions
- 24/7 expert homework help
4 | P a g e F a i l u r e a n a l y s i s m e t h o d s i n M e c h E n g i n e e r i n g
Figure 1: Motor piece facing erosion
Chemicals, take an important field of study on engineers, chemical compounds can create all types of reactions. Every surface of metallic constructions is vulnerable to corrosion. resulting from electrochemical or chemical processes.[3] While general attack corrosion is a known and foreseeable issue, it can also result in metal failure. Depending on the conditions under which the metal is being corroded, there are many ways to avoid corrosion. Techniques for preventing corrosion are: Environmental Modifications, Metal selection and surface conditions, Cathodic protection, Coating, Plating, corrosion inhibitors
Mechanical engineers also face mechanic fatigue; a deficiency that happens when an item is put under
recurrent or fluctuating loading but never reaches a level high enough to result in failure in a specific application and become an overload. Fatigue occurs when mechanisms are exposed to tensions, compressions or other type of external forces acting on them during prolonged times. A crack, which could have existed in the material when it was created or could have formed over time because of cyclic deformation around stress concentrations, is always the first sign of fatigue failure.
5 | P a g e F a i l u r e a n a l y s i s m e t h o d s i n M e c h E n g i n e e r i n g
Figure 2: A piece that failed due to fatigue
Engineers must consider loads; any mass will generate a force through gravity. These forces are often
called “loads.” They can be classified into "permanent loads" and "accidental loads" depending on the length of the buildings' useful lives. Being the constant loads, those in play throughout the useful construction beam's wide range. While the accidental loads or overloads, are bodies or a group of bodies with a huge difference in mass that generates a force in a mechanism or structure. When the force becomes too large in magnitude, it breaks the static system and produces the failure called overload.
B.
Cause of failure Failure is a broad phrase used to describe when a machine, piece of equipment, or component fails while in use. When a component completely ceases to function, when it still functional but unable to perform the intended function for which it was created, designed, and manufactured, or when the component's deterioration has advanced to the point where it is no longer reliable or safe to use are some of the behaviors that can be considered failures.[8] Over time, the primary causes of failure have been identified as, design, Inadequate selection of material, faulty heat treatment, erroneous manufacturing, lack of maintenance and faulty machining. It is difficult to pinpoint the precise reason for a failure, but the issue can be fixed following a thorough analysis.
6 | P a g e F a i l u r e a n a l y s i s m e t h o d s i n M e c h E n g i n e e r i n g
Figure 3: Forces causing failure 1
II.
Failure Analysis methods
C. Preventative methods
It is crucial that the analyst design the investigation in accordance with the fundamental objective of any failure analysis investigation, which is to stop failures. All engineering failures, without exception, occur at the weakest link in the design-manufacturing-performance chain of a product. The ability to identify his weakest link and proposing corrective measures is the key to a successful failure analysis investigation.[1]
1)
Destructive and non-destructive methods In mechanical engineering, professionals use testing methods to analyze the reaction of the pieces against external threats. Testing can divide two subsections; non-destructive and destructive methods; those that intend to destroy, are the destructive methods and consists in the use of invasive methods to find surface flaws or problems deep within a substance, quantitatively assess a property of an object or to Measure or inspect with the intention of endangering the component to analyze its behavior. Some of the destructive methods consists in applying some sorts of rays of currents to the object. On the other hand, non-destructive method is a collection of several inspection methods that can be applied separately or in combination to evaluate the quality and characteristics of a substance, component, or system. Some of the
Your preview ends here
Eager to read complete document? Join bartleby learn and gain access to the full version
- Access to all documents
- Unlimited textbook solutions
- 24/7 expert homework help
7 | P a g e F a i l u r e a n a l y s i s m e t h o d s i n M e c h E n g i n e e r i n g
non-destructive methods use by mechanical engineers are control by ultrasound, radiography, electromagnetic control, penetrating liquids, and visual inspection. Mechanical engineers use different methods to create a reaction and analyze it.[5]
D.
Forensic methods Failure analysis is the process of identifying the factors that lead to a vital part or component of a system failing, such as the material choice, design, application of the product, manufacturing processes, and failure mechanics inside the part. An examination of the failure's management processes is referred to
as the root cause. The combination of the two creates a strong framework for the study of forensic engineering because failure analysis identifies the precise area of failure and root cause analysis identifies
a comprehensive picture to ensure that it does not occur again.
1)
Destructive and non-destructive When thinking of forensic methodologies, it is crucial to consider the reasons why other mechanical systems in the same field have failed. A company can more accurately calculate how much a stress, tension, or compression a mechanism of the same type can hold, to know how our device will behave .
2)
Standards in mechanical engineering
Standards are imposed by recognized organizations around the world, like (ASME). They intend to maintain the public's safety and the uniformity of products produced by professional, even such small pieces like screws and nuts must follows standards.[6] Standards on how to test and a construct a steel bride, its safety rules, material properties and exposure to recognized failure causes is a technique for ensuring that modules are functioning properly. All can be found in[6]. For a mechanical engineer, when building a bridge is important to understand all the standards, the properties of the materials using as well as all the rules in a static equilibrium system.
8 | P a g e F a i l u r e a n a l y s i s m e t h o d s i n M e c h E n g i n e e r i n g
III.
Case Study
E. Description In this paper, we will examine the collapse that went on the Minneapolis I-35W Bridge, where there
appeared to be a failure in the trusses. According to bystanders, the south end was impacted first. Then, the malfunction dispersed across the bridge. By means of a 1990 evaluation, it was declared to be "structurally weak”, and corrosion issues were mentioned. Unexpected out-of-plane distortion of the crossbeams and ensuing stress cracking were induced by the main trusses' connections to these crossbeams. Additionally, there was resistance to movement at the connection point bearings.
F. Investigation
The bridge was classified as hazardous terrain for driving in the winter months in 1996. Additionally, the Minnesota Department of Transportation, which was in charge of maintenance, put in place a system that prevented the creation of ice by spraying chemical compounds on the surface. It was shown that this technique might have accelerated foundation corrosion after the bridge fell. It should be mentioned that it was one of the first bridges of its kind to use this anti-ice technology in the United States.
However, numerous studies on this bridge conducted before the collapse suggested that its structural integrity needed improvement. The forensic investigation's mechanical engineers concluded that the bridge was "structurally defective" and pointed to corrosion issues. They also identified more structural flaws.[4]
It was also labeled as "structurally deficient" in 2005, per information found in the national inventory of federal bridges maintained by the US Department of Transportation. Like the previous inspection, this direction's 2006 inspection also ranked this bridge lower than average. Out of a potential 100 points, it received a score of 50. It should be noted that ratings below 80 denote a need for
9 | P a g e F a i l u r e a n a l y s i s m e t h o d s i n M e c h E n g i n e e r i n g
rehabilitation, while ratings of 50 or lower denote a need for total replacement. Therefore, state and federal officials had grave concerns about the I-35 W bridge's structural integrity.
Figure 4: Corrosion on the trusses 1
From a mechanical point of view, the failure due to corrosion was not the only reason. The metal sheet plaque reinforcing each of the joints in the trusses were erroneously elected. Since the thickness of the plaque was half of what the standards of a steel bridge of that magnitude is established. The plaque was around ¼” while the standards established by the US transportation recommends plaques of at least ½”. This action, the corrosion generated by the chemicals used on the bridge, and an overload created by construction vehicles as well as the enormous number of cars driving over the bridge because it was rush hours in the city, were responsible for this tragedy.
Your preview ends here
Eager to read complete document? Join bartleby learn and gain access to the full version
- Access to all documents
- Unlimited textbook solutions
- 24/7 expert homework help
10 | P a g e F a i l u r e a n a l y s i s m e t h o d s i n M e c h E n g i n e e r i n g
Figure 5: compression on overload 1
G. Recommendations Thinking about evading this tragedy and save all the lives involved might be a little presumptuous.
It is a fact that overload, corrosion and neglection of standards are failures that can be easily discarded in the testing phase and materials election. But the problem relies in that the circumstances coincided and that cannot be predicted. Even though the problem was matter of three failures coinciding, my recommendation is to check the plans and informs about the bridge before doing any change in the bridge, such as including a chemical that was never used before. Checking the standards established, so you know you will assure the public’s safety and control those overloads.
11 | P a g e F a i l u r e a n a l y s i s m e t h o d s i n M e c h E n g i n e e r i n g
IV.
References
[1] Tawancy, Hani M., Nureddin Mohamed. Abbas, and Anwar. Ul-Hamid. Practical Engineering Failure Analysis. New York: M. Dekker, 2004.
[2] Noon, R.K. (2000). Forensic Engineering Investigation (1st ed.). CRC Press. https://doi.org/10.1201/9781420041415
[3] Tawancy, H.M., Ul-Hamid, A., & Abbas, N.M. (2004). Practical Engineering Failure Analysis (1st ed.). CRC Press. https://doi.org/10.1201/9780203026298
[4] Mechanical Design Failure Analysis: With Failure Analysis System Software for
the IBM PC, David G. Ullman.
[5] H. M. Tawancy, H. M. Tawancy, A. Ul-Hamid, and N. M. Abbas, Practical Engineering Failure
Analysis
. New York, NY: Marcel Dekker, 2005. [6] Woo, Seongwoo. (2020). Mechanical System Failures. 10.1007/978-981-13-7236-0_7.
[7] International Journal of Erosion Control Engineering. 東京
: 砂防学会
, n.d.
[8] M. T. U. Michigan Technological University, “What is mechanical engineering?” Michigan Technological University
, 13-May-2022. [Online]. Available: https://www.mtu.edu/mechanical/engineering/. [Accessed: 14-Oct-2022]. .
Related Documents
Related Questions
Part B
Data taken from a stress-strain test for a ceramic are
given in the table. The curve is linear between the origin
and the first point.
Determine the modulus of elasticity.
VO AEO vec
?
E =
ksi
Submit
Request Answer
Figure
1 of 1
Part C
σ (ksi)
e (in./in.)
Determine the modulus of resilience.
ΑΣφ
?
vec
33.2
0.0006
45.5
0.0010
in-lb
Up =
in
49.4
0.0014
51.5
0.0018
Submit
Request Answer
53.4
0.0022
arrow_forward
12:48 PM E O ĕ ..
all 6 57
01:12:47 Remaining
Muitipie ChOice
Cylindrical samples of steel, glass
and rubber are each subjected to a
gradually increasing tensile force F.
The extensions are measured and
graphs are plotted as shown below.
Which row in the following table
correctly relates the graphs to the
materials?
1 attachment •
graph Y
grapl
Steel X, Glass Y, Rubber Z
Steel X, Glass Z, Rubber Y
Steel Y, Glass X , Rubber Z
Steel Y, Glass Z, Rubber X
3 of 30
arrow_forward
The bent rod ACDB is supported by a sleeve at A and a ball-and-socket joint at B. Determine the components of the reactions and the
tension in the cable. Neglect the mass of the rod and any moment reactions at A.
0.5 ml
0.7 m
0.4 m
0.2 m
82 kg
0.4 m
0.2 m
arrow_forward
B
12:09 A
A beam is held by 2 steel rods, AB and CD. Three dead load
forces are applied to the beam. The normal failure stress of
the steel is o fail = 260 MPa. The resistance factor is = 0.92
. The dead load factor is yp= 1.6.
A
d₁
F₁
d2
wamap.org
F₂
Variable
Value
F₁
5 KN
F2
7 kN
F3
6.5 KN
d₁
2 m
d₂
1 m
d3
2.25 m
d₁
3.75 m
Using the LSD/LRFD method,
F3
d4
Values for the figure are given in the following table. Note
the figure may not be to scale.
KN
с
a. Determine normal force in rod AB after accounting for
the dead load factor, NAB.
b. Determine normal force in rod CD after accounting for
the dead load factor, NCD.
c. Determine minimum radius needed for rod AB, TAB.
d. Determine minimum radius needed for rod CD, CD.
Round your final answers to 3 significant digits/figures.
NAB =
arrow_forward
1. A tension test on an aluminum plate resulted in the following engineering stress-engineering strain data
as reported in the first and second column of the table below (reduction of area, RA=17%):
S (psi)
e (in/in)
σ (psi)
ε (in/in)
10500
0.001
10510.5
0.000995
21000 0.002
31200 0.003
41300 0.004
51200 0.005
61200 0.006
70600 0.007
74700 0.0075
76800 0.008
77600 0.0085
78000 0.009
78400 0.0095
78700 0.01
81200 0.02
83000 0.03
84200 0.04
85400 0.05
86200 0.06
86800 0.07
*87200 0.08
**86200 0.1
Note: *
maximum load, ** load at fracture
a) Calculate the corresponding true stress and true strain and give your results in a table along with the
engineering stress, engineering strain shown in the of table above (column 3 and 4).
b) Plot the true stress-true strain curve on a rectangular coordinate.
c) Plot the true stress-true strain curve on a log-log graph and determine the plastic flow curve parameters
K and n, the yield strength, Y, and the elastic modulus, E of the material.
arrow_forward
Find the value of M1, M2, and what is the percent error if the true value is 149 grams?
arrow_forward
The shear modulus, G, of an alloy can be determined by measuring the angular twist, θ,resulting from a torque applied to a cylindrical rod made from the alloy. For a rod of radius Rand a torque applied at a length L from a fixed end, the modulus is found by G=2LT/pR4θ.Examine the effect of the relative uncertainty of each measured variable on the shearmodulus. If during test planning all of the uncertainties are estimated to be 1%, what is theuncertainty in G?
arrow_forward
The cross-section of an earth dam sitting on an impermeable base is shown in figure 2. Determine the critical failure surface and the center of the circle by assuming failure surface is circular. Use Bishop’s conventional or rigorous method.
arrow_forward
I want handwriteen and correct answer only don't do if u don't knowpls
arrow_forward
Please show handwritten solution
arrow_forward
E2008 Mechanics of Materials
/attempt.php
The strain at point A on the bracket has normal components 750x106 and 150x10-6 in x
Sına
and y directions, respectively and shear component -600 x10 in x-y plane. Determine the
di
absolute maximum shear strain in 106 unit.
Lutfen birini seçin.
a None
b 808.5
C653.8
d. 735 4
pt=175487
arrow_forward
Find the tension in cables CF and DE and the
support reactions at A. The pin at A exerts couples
about the x and z axes and forces along the x and z
axes on the collar.
arrow_forward
The tensile 0.2 percent offset yield strength of AISI 1137 cold-drawn steel bars up to 1 inch in diameter from 2 mills and 25 heats is
reported as follows:
Sy 93
95
101
f
97 99
107 109 111
19 25 38 17 12 10 5 4
103
105
4
2
where Sy is the class midpoint in kpsi and fis the number in each class.
Presuming the distribution is normal, determine the yield strength exceeded by 99.0% of the population.
The yield strength exceeded by 99.0% of the population is
kpsi.
arrow_forward
35)
arrow_forward
8. Solve 8..show complete STEP BY STEP solution, and draw a FBD
arrow_forward
30°
T₂
7
m
T₁
OF OF OLE
T
9
m
T₁₁
10
O
T₁
5
m
То
6
m
arrow_forward
你(
esc
Ductile failure is characterised by:
Select one or more:
1
7
a. Minimal reduction in cross sectional area
0
b. Significant elongation to failure
c.
The component breaking into many pieces
Od. Cavity Coalescence
Previous page
Q
A
e. A smooth fracture surface
F1
2
F2
W
ㅁㅁ
#
3
F3
E
C
DOD
DOD
$
S 4
F4
R
%
5
F5
MacBook Pro
T
A
6
F6
Y
&
7
F7
*
U
Next
▶11
8
F8
arrow_forward
SEE MORE QUESTIONS
Recommended textbooks for you
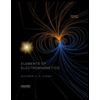
Elements Of Electromagnetics
Mechanical Engineering
ISBN:9780190698614
Author:Sadiku, Matthew N. O.
Publisher:Oxford University Press
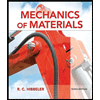
Mechanics of Materials (10th Edition)
Mechanical Engineering
ISBN:9780134319650
Author:Russell C. Hibbeler
Publisher:PEARSON
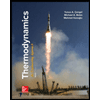
Thermodynamics: An Engineering Approach
Mechanical Engineering
ISBN:9781259822674
Author:Yunus A. Cengel Dr., Michael A. Boles
Publisher:McGraw-Hill Education
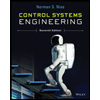
Control Systems Engineering
Mechanical Engineering
ISBN:9781118170519
Author:Norman S. Nise
Publisher:WILEY
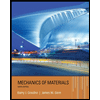
Mechanics of Materials (MindTap Course List)
Mechanical Engineering
ISBN:9781337093347
Author:Barry J. Goodno, James M. Gere
Publisher:Cengage Learning
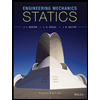
Engineering Mechanics: Statics
Mechanical Engineering
ISBN:9781118807330
Author:James L. Meriam, L. G. Kraige, J. N. Bolton
Publisher:WILEY
Related Questions
- Part B Data taken from a stress-strain test for a ceramic are given in the table. The curve is linear between the origin and the first point. Determine the modulus of elasticity. VO AEO vec ? E = ksi Submit Request Answer Figure 1 of 1 Part C σ (ksi) e (in./in.) Determine the modulus of resilience. ΑΣφ ? vec 33.2 0.0006 45.5 0.0010 in-lb Up = in 49.4 0.0014 51.5 0.0018 Submit Request Answer 53.4 0.0022arrow_forward12:48 PM E O ĕ .. all 6 57 01:12:47 Remaining Muitipie ChOice Cylindrical samples of steel, glass and rubber are each subjected to a gradually increasing tensile force F. The extensions are measured and graphs are plotted as shown below. Which row in the following table correctly relates the graphs to the materials? 1 attachment • graph Y grapl Steel X, Glass Y, Rubber Z Steel X, Glass Z, Rubber Y Steel Y, Glass X , Rubber Z Steel Y, Glass Z, Rubber X 3 of 30arrow_forwardThe bent rod ACDB is supported by a sleeve at A and a ball-and-socket joint at B. Determine the components of the reactions and the tension in the cable. Neglect the mass of the rod and any moment reactions at A. 0.5 ml 0.7 m 0.4 m 0.2 m 82 kg 0.4 m 0.2 marrow_forward
- B 12:09 A A beam is held by 2 steel rods, AB and CD. Three dead load forces are applied to the beam. The normal failure stress of the steel is o fail = 260 MPa. The resistance factor is = 0.92 . The dead load factor is yp= 1.6. A d₁ F₁ d2 wamap.org F₂ Variable Value F₁ 5 KN F2 7 kN F3 6.5 KN d₁ 2 m d₂ 1 m d3 2.25 m d₁ 3.75 m Using the LSD/LRFD method, F3 d4 Values for the figure are given in the following table. Note the figure may not be to scale. KN с a. Determine normal force in rod AB after accounting for the dead load factor, NAB. b. Determine normal force in rod CD after accounting for the dead load factor, NCD. c. Determine minimum radius needed for rod AB, TAB. d. Determine minimum radius needed for rod CD, CD. Round your final answers to 3 significant digits/figures. NAB =arrow_forward1. A tension test on an aluminum plate resulted in the following engineering stress-engineering strain data as reported in the first and second column of the table below (reduction of area, RA=17%): S (psi) e (in/in) σ (psi) ε (in/in) 10500 0.001 10510.5 0.000995 21000 0.002 31200 0.003 41300 0.004 51200 0.005 61200 0.006 70600 0.007 74700 0.0075 76800 0.008 77600 0.0085 78000 0.009 78400 0.0095 78700 0.01 81200 0.02 83000 0.03 84200 0.04 85400 0.05 86200 0.06 86800 0.07 *87200 0.08 **86200 0.1 Note: * maximum load, ** load at fracture a) Calculate the corresponding true stress and true strain and give your results in a table along with the engineering stress, engineering strain shown in the of table above (column 3 and 4). b) Plot the true stress-true strain curve on a rectangular coordinate. c) Plot the true stress-true strain curve on a log-log graph and determine the plastic flow curve parameters K and n, the yield strength, Y, and the elastic modulus, E of the material.arrow_forwardFind the value of M1, M2, and what is the percent error if the true value is 149 grams?arrow_forward
- The shear modulus, G, of an alloy can be determined by measuring the angular twist, θ,resulting from a torque applied to a cylindrical rod made from the alloy. For a rod of radius Rand a torque applied at a length L from a fixed end, the modulus is found by G=2LT/pR4θ.Examine the effect of the relative uncertainty of each measured variable on the shearmodulus. If during test planning all of the uncertainties are estimated to be 1%, what is theuncertainty in G?arrow_forwardThe cross-section of an earth dam sitting on an impermeable base is shown in figure 2. Determine the critical failure surface and the center of the circle by assuming failure surface is circular. Use Bishop’s conventional or rigorous method.arrow_forwardI want handwriteen and correct answer only don't do if u don't knowplsarrow_forward
- Please show handwritten solutionarrow_forwardE2008 Mechanics of Materials /attempt.php The strain at point A on the bracket has normal components 750x106 and 150x10-6 in x Sına and y directions, respectively and shear component -600 x10 in x-y plane. Determine the di absolute maximum shear strain in 106 unit. Lutfen birini seçin. a None b 808.5 C653.8 d. 735 4 pt=175487arrow_forwardFind the tension in cables CF and DE and the support reactions at A. The pin at A exerts couples about the x and z axes and forces along the x and z axes on the collar.arrow_forward
arrow_back_ios
SEE MORE QUESTIONS
arrow_forward_ios
Recommended textbooks for you
- Elements Of ElectromagneticsMechanical EngineeringISBN:9780190698614Author:Sadiku, Matthew N. O.Publisher:Oxford University PressMechanics of Materials (10th Edition)Mechanical EngineeringISBN:9780134319650Author:Russell C. HibbelerPublisher:PEARSONThermodynamics: An Engineering ApproachMechanical EngineeringISBN:9781259822674Author:Yunus A. Cengel Dr., Michael A. BolesPublisher:McGraw-Hill Education
- Control Systems EngineeringMechanical EngineeringISBN:9781118170519Author:Norman S. NisePublisher:WILEYMechanics of Materials (MindTap Course List)Mechanical EngineeringISBN:9781337093347Author:Barry J. Goodno, James M. GerePublisher:Cengage LearningEngineering Mechanics: StaticsMechanical EngineeringISBN:9781118807330Author:James L. Meriam, L. G. Kraige, J. N. BoltonPublisher:WILEY
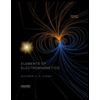
Elements Of Electromagnetics
Mechanical Engineering
ISBN:9780190698614
Author:Sadiku, Matthew N. O.
Publisher:Oxford University Press
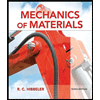
Mechanics of Materials (10th Edition)
Mechanical Engineering
ISBN:9780134319650
Author:Russell C. Hibbeler
Publisher:PEARSON
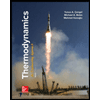
Thermodynamics: An Engineering Approach
Mechanical Engineering
ISBN:9781259822674
Author:Yunus A. Cengel Dr., Michael A. Boles
Publisher:McGraw-Hill Education
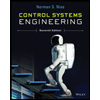
Control Systems Engineering
Mechanical Engineering
ISBN:9781118170519
Author:Norman S. Nise
Publisher:WILEY
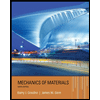
Mechanics of Materials (MindTap Course List)
Mechanical Engineering
ISBN:9781337093347
Author:Barry J. Goodno, James M. Gere
Publisher:Cengage Learning
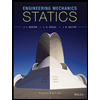
Engineering Mechanics: Statics
Mechanical Engineering
ISBN:9781118807330
Author:James L. Meriam, L. G. Kraige, J. N. Bolton
Publisher:WILEY