Total Quality Management .edited
docx
keyboard_arrow_up
School
Rehman College of Rehabilitation Science Hayatabad, Peshawar (Dr of Physical Therpay 5 Years) *
*We aren’t endorsed by this school
Course
CREATIVE W
Subject
Management
Date
Nov 24, 2024
Type
docx
Pages
8
Uploaded by MagistrateSnail3903
Introduction
What is meant by Total quality Management?
Total quality management (TQM), an all-encompassing strategy of oversight of associations, is to
improve the measure of products and services by effortlessly incorporating individuals, approaches,
and culture within an organization. Its central purpose is frequently overextending client anticipations,
employing a cohesive devotion to remarkable quality.
Discussion
Q1. Maxx Industry is in the process of implementing TQM across the entire organization. You are
asked to make a presentation to the senior managers on the aspects of TQM and points to consider
while implementing. Discuss your presentation. (10 Marks) – 800 Words
Enriching the standard of products and services by integrating all elements of a corporation is the
pursuit of Total Quality Management (TQM), an integrated strategy for managing organizations. It
will cover paramount factors of adopting TQM to promote an ongoing enhancement and quality
environment in this presentation to senior managers at Maxx Industry.
●
Leadership Commitment: The leadership's devotion is one of the keystones of an effective
TQM implementation. In order to promote an environment of quality across the entire
company, I want to underline how crucial senior management is. The dedication to quality
that leaders show in their daily activities and managerial procedures is not limited to just
endorsing the values of TQM. An organization's fundamental culture is exploited by intense
leadership about value.
●
Employee Involvement: Total Quality Management (TQM) accomplishment underscores
the requirement for staff engagement at all sets. Employee involvement is critical to fostering
a sense of accountability and ownership because workers are the foundation of any business.
Employers may access a helpful tool for improving their processes by involving staff
members in decision-making while motivating them to share their knowledge. An
environment of creation and steady advancement is encouraged by this coordinated
procedure.
●
Constant Advancement: A key element of Total Quality Management underscores the
essential of persistent enhancement. Process inefficiency can be found and eliminated using
techniques like Kaizen, Six Sigma, and Lean. Whereas Six Sigma concentrates on minimizing
errors and variances, Kaizen encourages modest, gradual changes. The goal of lean
approaches is to reduce process waste. When employed in the team, these resources propose a
potent framework that facilitates corporations to transform, expand, and continually improve
their procedures.
●
Focus on the Customer: One of TQM's pillars is articulating how vital it is to comprehend
and fulfill consumer demands. Organizations must prioritize customer satisfaction by
proactively obtaining and integrating customer input. This customer-first strategy improves
goods and services, fosters commitment, and boosts the company's standing. Long-term
success involves understanding what customers desire from you and concocting methods to
meet those anticipations.
●
Management of Processes: A fundamental element of Total Quality Management (TQM)
stresses the significance of efficient process management. Process mapping, evaluation, and
optimization are all done methodically in this. Organizations can find areas for enhancement,
bottlenecks, and redundancy in a procedure by comprehending and recording every phase.
Process oversight confirms that workflow is efficacious, trustworthy, and aligned with
corporation ideals.
●
Supplier Relationships:
In demand to secure the effectiveness of inputs, it is compulsory to
determine the importance of solid associations with suppliers. Working with suppliers reduces
supply chain defects by fostering a shared comprehension of quality norms and specifications.
Proactively acquiring supplier relationships improves belief, engagement, and quality of the
finished good or service.
●
Training and Education: In order to prepare staff members with the capabilities needed for
high-quality work, it is essential to talk about the necessity for continual training and
education. Employees engaged in continuous learning are guaranteed to be knowledgeable
about emerging technologies, changing customer demands, and commercial best practices.
Employee attitudes and beliefs can be facilitated by customizing training programs to fit the
necessities of respective job positions.
●
Measurement and Analysis: In tracking and enhancing processes, it is vital to underscore
the significance of data-driven choices, key performance indicators (KPIs), and statistical
approaches. Organizations may make well-informed decisions using measurement and
analysis, offering insightful information about different processes' operations. Tracking
trends, outliers, and concern areas with standard KPI inspections assists in uncovering these
zones.
●
Award and Appreciation: One encouraging element of enhancing quality is underlining the
significance of acknowledging and rewarding employees. It is suitable for the workplace to
recognize the contributions made by staff members who actively participate in TQM projects.
Awarding someone for a job done well is just one way to show appreciation; other forms
include incentives and prizes. This favorable feedback promotes a surroundings of superiority
and responsibility.
●
Benchmarking: Concerning the advantages of benchmarking against enterprise norms in
encountering sites that require advancement, it is compulsory. By benchmarking their
accomplishments against leading competitors, businesses can identify areas for growth or
success and make the necessary changes. A strategic process for enhancing a business's
general efficiency is understanding both the tribulations and accomplishments of others.
Overall, Total Quality Management is an all-encompassing method that necessitates belief, teamwork,
and a priority on constant enhancement. Maxx Industry can establish an excellent basis for quality
management and maintain its competitive edge in the ever-changing marketplace by incorporating
these fundamental elements into its everyday functions.
Q2. What would be your advice to a design team on quality management techniques that may support
in removing defects in products at design phase or the production phase? (10 Marks) – 800 Words
Any latest product development approach must include quality control, and an incredible outcome
primarily counts on the design step. It is where I offer the design team an in-depth manual that
possesses many methods for quality control meant to keep blunders at bay and boost expertness.
●
Early Design Analysis: In the design section, detouring imperfections begins with fostering
an environment of careful investigation. Issues can be found early on and prevented from
becoming expensive production-related issues by establishing an attitude that values thorough
inspection. Expanding close awareness of details, going over design specifications
methodically, and taking proactive actions to mitigate possible hazards are all essential.
Several aspects, including probable reasons for failure, manufacturing strategies, and material
preference, are assessed during early design investigation. By taking this proactive approach,
the design team can reduce risks early, facilitating production and increasing the likelihood of
creating a flawless defect-free.
●
Failure Mode and Effect Analysis (FMEA): A purposeful step to methodically consider and
rank probable failure ways in the design procedure is the preface of Failure Mode and Effect
Analysis (FMEA). The team can recognize, understand, and rank potential causes of failure
according to their severity, frequency, and detection using FMEA. This methodical procedure
helps foresee situations and makes it easier to make well-informed determinations about
assigning resources for preventative measurements.
The design unit may accomplish specific procedures for avoiding imperfections by employing
FMEA, which improves awareness of the possible hazards linked to the design. By employing
this analytical mechanism as a proactive technique for solving issues, the team can tackle
deficiencies before they harm the quality of the outcome.
●
Interdepartmental Cooperation: Cross-functional associations must be prioritized if
blemish prevention is to be approached holistically. Including teams from design, production,
and quality confirmation in a collaborative endeavor proves that different stances are
considered, resulting in a more thorough comprehension of possible barriers.
By fostering open lines of discourse among teams, the cross-functional association
encourages shared accountability for the quality of the outcome. The team working on the
design can leverage the combined knowledge of several departments by dismantling
departmental silos and encouraging a collaborative mindset. It results in a more cultivated and
resilient layout that is less likely to have mistakes during manufacturing.
●
Prototyping: Encouraging the growth of prototypes is a substantial measure of the demand
for diminishing mistakes. Before going into full-scale production, the design team can test
and improve their concepts through prototyping. By determining shortcomings in design,
functionality problems, and manufacturing obstacles early on, this continued procedure helps
avoid these issues from arising during production in large portions.
By equipping insights that might not be perceptible through theoretical evaluation alone,
prototyping acts as a beneficial and hands-on confirmation of the design. It permits the team
Your preview ends here
Eager to read complete document? Join bartleby learn and gain access to the full version
- Access to all documents
- Unlimited textbook solutions
- 24/7 expert homework help
to scrutinize the product in an actual setting and guarantee that any requisite modifications are
enforced before considerable resources are assigned toward comprehensive manufacturing.
●
Normative Framework: It assures consistency and lower variability, and it is crucial to
boost the adoption of standardized design approaches and documentation. Design activities
are given a defined framework by establishing standardized practices, procedures, and
formats for documentation. The design procedure is facilitated by this consistency,
diminishing the chance of blunders and divergences.
Standardization shields documentation designs, protocols for communication, and
examination of design strategies in addition to the design stage. Via allegiance to
predetermined criteria, the design group forms a quality framework that interpenetrates the
entire product development lifespan and ultimately helps avoid flaws.
●
Mechanisms for Feedback:
Installing robust feedback mechanisms to acquire ideas from
client input and production encounters is crucial. By functioning as a never-ending loop of
enhancement, these procedures help the designers to take lessons from genuine outcomes and
make essential modifications to their initial designs.
Facts about how the procedure is enforced in fundamental production approaches can be
acquired through feedback from manufacturing encounters. A similar viewpoint on how the
good fulfills consumer demands and functions in actual situations can be found in client
feedback. The design team can improve the product's quality and avoid flaws in future
iterations by pursuing and blending feedback into their decision-making procedure.
●
Supplier Involvement: An intelligent action to certify a precise grasp of quality benchmarks
and avoid troubles with input materials is to include vendors in the design procedure.
Operating with providers during the design stage improves alignment on quality standards,
which is vital because suppliers particularly impact the finished item's quality.
It is easier to have conversations about material requirements, quality control procedures, and
potential difficulties when suppliers are involved early in the planning process. Through this
relationship, suppliers can align their goals with the design team's quality standards, which
assists in avoiding defects linked to input segments.
●
Training and Skill Development: The design team must receive sufficient training in quality
management concepts and procedures to apply successful defect prevention strategies. In
order to keep the team up to date on the newest techniques, tools, and best practices,
continuous training is necessary in the dynamic field of quality administration.
An assortment of subjects, such as managing risks, control of statistical processes, and using
high-quality tools, should be covered in training. A proactive mindset toward quality is
additionally supported by creating a culture of ongoing development of knowledge and
abilities within the design team. It makes team members better equipped to handle new
challenges and aid in avoiding deficiencies.
Overall, offering the design team thorough recommendations necessitates a multipronged strategy
incorporating various quality control methodologies. A solid structure for avoiding errors and
encouraging an atmosphere of constant enhancement within the development process is created by
early design evaluation, mechanisms for feedback, cross-functional cooperation, prototyping,
standardization, early design analysis, supplier participation, and training. By implementing these
tactics, the development team can make a substantial contribution to the product's quality as a whole,
which will ultimately result in increased customer satisfaction and long-term success in the
marketplace.
Q3. Below is data collected for the percentage of defective from a process (n=100).
Sample
1 2 3 4 5 6 7 8 9 10 11
12 13
14
15
p .04
.02
.05
.03
.06
.04
.03
.07
.01
.02
.03
.02
.02
.08
.0
3
a. Find all control limits for this process. (
5 Marks) – 400 Words
A methodical technique involving statistical computations is utilized to establish efficient control
limits for a particular process. The data gathered, which shows the proportion of faulty items in the
process, is the foundation for these computations. The main parameters operated in this investigation
are the mean (μ) and standard deviation (σ), which aid in defining the control limits that are higher
and lower.
Summing up all the values and dividing the outcome by the total number of values in the sample
yields the mean (μ). Regarding the dataset that has been given:
Calculating the Mean (μ)
μ = (sum of all values) / (number of values)
μ = (0.04 + 0.02 + 0.05 + 0.03 + 0.06 + 0.04 + 0.03 + 0.07 + 0.01 + 0.02 + 0.03 + 0.02 + 0.02
+ 0.08 + 0.03) / 15
When we simplify this expression, we get:
μ = 0.4 / 15
μ = 0.0267
Therefore, 0.0267 is the process mean (μ).
After that, by taking the square root of the sum of the squared deviations from the mean and
dividing it by the number of values less than one, one can compute the standard deviation (σ).
Here is how the formula looks:
Calculating the Standard Deviation (σ)
σ = √(sum of squared deviations from the mean) / (number of values - 1)
σ = √[((0.04 - 0.0267)^2 + (0.02 - 0.0267)^2 + ... + (0.03 - 0.0267)^2)] /
14
σ = √0.001326 / 14
σ = 0.0364
Following computation, 0.0364 is the standard deviation (σ).
Control Limits
Establishing the control limits comes after figuring out the mean and standard deviation. The
standard deviation of control limits from the mean is typically set at ±3. Thus, the upper
control limit (UCL) is computed using the following formula:
Upper Control Limit (UCL) = μ + 3σ = 0.0267 + 3 * 0.0364 = 0.1295
Additionally, the following formula is used to determine the lower control limit (LCL):
Your preview ends here
Eager to read complete document? Join bartleby learn and gain access to the full version
- Access to all documents
- Unlimited textbook solutions
- 24/7 expert homework help
Lower Control Limit (LCL) = μ - 3σ = 0.0267 - 3 * 0.0364 = -0.0861
The following are the computed control limits for this process as a result:
Upper Control Limit (UCL) = 0.1295
Lower Control Limit (LCL) = -0.0861
For process tracking, these regulatory limits serve as benchmarks. Any data beyond these
ranges might point to unique sources of variation, necessitating more research. By applying
statistical methods, companies can keep their procedures within acceptable quality bounds,
promoting ongoing enhancement and defect avoidance.
b. Discuss two types of control charts you will use for attributes data. (
5 Marks) – 400 Words
Control charts customized for particular data types are frequently used in quality management to
enable efficient process monitoring. The p-chart and the c-chart are frequently used control charts
when working with feature data.
The proportional chart, or p-chart for short, helps examine the percentage of unconventional items in a
sample. This kind of control chart is handy when the sample size is kept constant and the goal is to
count the total number of nonconforming items. The binomial distribution is the foundation for
calculating control limits for p-charts, ensuring that the diversity in the data is accurately portrayed.
The c-chart, or count chart, is used to track how many nonconformities there are in each sample unit.
It works well in situations where the sample size stays constant, just like the p-chart, but in this
instance, the focus is on collecting the instances of nonconformities per unit. A mathematical
framework called a Poisson distribution is used to determine the control limits of a c-chart. It is
intended explicitly for counting occurrences that happen arbitrarily and autonomously over a
predetermined intermission.
The kind of process being observed will determine which control chart is best. For processes that
result in discrete products, like assembled components, the c-chart is the recommended option. On the
other hand, the p-chart is a better choice when the process produces batches of items, such as a mass-
produced batch of cookies.
To understand how this works in practice, picture a situation in which the manufacturing process is
closely examined. Every component is carefully examined for flaws, and each component's number of
flaws is recorded. Because the c-chart aligns with the distinct nature of the defects in individual items,
it becomes the favoured chart in this position.
On the other hand, consider a situation where batches of cookies are being produced. Examining
every batch for flaws is part of quality control, and the main goal is to figure out how many cookies
are flawed in each batch. Because it can accurately depict the variation in percentages within distinct
batches, the p-chart is the appropriate alternative.
Overall, the type of data and the manufacturing process features determine which of the two charts is
better: a p-chart or a c-chart. Quality management professionals can make wise decisions by being
aware of the subtle differences between each chart, which guarantees accurate and insightful
information about the procedure's effectiveness.
Conclusion
Ultimately, Total Quality Management (TQM) is a broad approach that can improve the quality of
products and services when devoted to loyalty and careful deliberation of essential details, setting up
companies like Maxx Industry for long-term success. Furthermore, statistical instruments such as
control charts and quality management strategies used during the product design and production
stages play a noteworthy role in blemish prevention and persistent enhancement.
Related Documents
Recommended textbooks for you
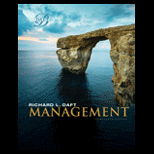
Management, Loose-Leaf Version
Management
ISBN:9781305969308
Author:Richard L. Daft
Publisher:South-Western College Pub
Recommended textbooks for you
- Management, Loose-Leaf VersionManagementISBN:9781305969308Author:Richard L. DaftPublisher:South-Western College Pub
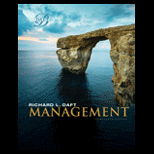
Management, Loose-Leaf Version
Management
ISBN:9781305969308
Author:Richard L. Daft
Publisher:South-Western College Pub