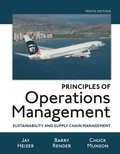
Concept explainers
a capacity expansion plan and a new 11-story hospital building across the street from the existing facility.
Thirty-five planning teams were established to study such issues as (1) specific forecasts. (2) services that would transfer to the new facility. (3) services that would remain in the existing facility. (4) staffing needs. (5) capital equipment. (6) pro forma accounting data, and (7) regulatory- requirements. Ultimately, Arnold Palmer Hospital was ready to move ahead with a budget of S100 million and a commitment to an additional 150 beds. But given the growth of the central Florida region. Swanson decided to expand the hospital in stages: the top two floors would be empty interiors ("shell”) to be completed at a later date, and the fourth-floor operating room could be doubled in size when needed. "With the new facility in place, we are now able to handle up to 16,000 births per year." says Swanson.
Discussion Questions*
1. Given the capacity planning discussion m the text (see Figure S7.6), what approach it being taken by Arnold Palaver Hospital toward matching capacity to demand?
2. What kind of major changes could take place in Arnold Palaver Hospitals demand
3. Use regression analysis to forecast the point at which Swanson needs to "build out" the top two floors of the new building, namely, when demand will exceed 16,000 births
*You may wish to view the video that accompanies the case before addressing these questions.
TABLE S7.4 Births at Arnold Palmer Hospital
YEAR | BIRTHS |
1995 | 6,144 |
1996 | 6,230 |
1997 | 6,432 |
1998 | 6,950 |
1999 | 7,377 |
2000 | 8,655 |
2001 | 9,536 |
2002 | 9,825 |
2003 | 10,253 |
2004 | 10,555 |
2005 | 12,316 |
2006 | 13,070 |
2007 | 14,028 |
2008 | 14,241 |
2009 | 13,050 |
2010 | 12,571 |
2011 | 12,978 |
2012 | 13,529 |
2013 | 13,576 |
2014 | 13,994 |

Want to see the full answer?
Check out a sample textbook solution
Chapter 7 Solutions
EBK PRINCIPLES OF OPERATIONS MANAGEMENT
- Ruby-Star Incorporated is considering two different vendors for one of its top-selling products which has an average weekly demand of 40 units and is valued at $80 per unit. Inbound shipments from vendor 1 will average 340 units with an average lead time (including ordering delays and transit time) of 2 weeks. Inbound shipments from vendor 2 will average 550 units with an average lead time of 1 week. Ruby-Star operates 52 weeks per year; it carries a 2-week supply of inventory as safety stock and no anticipation inventory. a. The average aggregate inventory value of the product if Ruby-Star used vendor 1 exclusively is $ (Enter your response as a whole number.)arrow_forwardThe Carbondale Hospital is considering the purchase of a new ambulance. The decision will rest partly on the anticipated mileage to be driven next year. The miles driven during the past 5 years are as follows: Year Mileage 1 3,000 2 3 4 4,000 3,450 3,850 5 3,800 a) Using a 2-year moving average, the forecast for year 6 = miles (round your response to the nearest whole number). b) If a 2-year moving average is used to make the forecast, the MAD based on this = miles (round your response to one decimal place). (Hint: You will have only 3 years of matched data.) c) The forecast for year 6 using a weighted 2-year moving average with weights of 0.40 and 0.60 (the weight of 0.60 is for the most recent period) = ☐ miles (round your response to the nearest whole number). miles (round your response to one decimal place). (Hint: You will have only 3 years of The MAD for the forecast developed using a weighted 2-year moving average with weights of 0.40 and 0.60 = matched data.) d) Using…arrow_forwardTask time estimates for the modification of an assembly line at Jim Goodale's Carbondale, Illinois, factory are as follows: B D G Time Activity (in hours) Immediate Predecessor(s) A 5.0 B 7.5 C 5.0 A DEFC 8.0 B, C 4.5 Figure 2 A B, C 7.7 D G 5.0 E, F This exercise contains only part a. a) The correct precedence diagram for the project is shown in 目 F B Figure 3 A E B E ☑ D Farrow_forward
- Dave Fletcher was able to determine the activity times for constructing his laser scanning machine. Fletcher would like to determine ES, EF, LS, LF, and slack for each activity. The total project completion time and the critical path should also be determined. Here are the activity times: Activity Time (weeks) Immediate Predecessor(s) Activity Time (weeks) Immediate Predecessor(s) A 6 E 3 B B 8 F 6 B C 3 A G 11 C, E D 1 A H 7 D, F Dave's earliest start (ES) and earliest finish (EF) are: Activity ES .EF A 0 6 B 0 8 C 3 9 D 6 E F 8 G 22 H 21 Dave's latest start (LS) and latest finish (LF) are: Activity LS LF H 15 G 11 F 9arrow_forwardThere are multiple ways a company can enter a foreign market. Explore two possibilities such as exporting, foreign direct investment, and collaborations (joint ventures, alliances, licensing, franchising), and evaluate the pros and cons of each method. Which types of products and services would be appropriate for each market entry method?arrow_forward01,3 ☐ Question 3 Scenario 9.3 4 pts The Talbot Company uses electrical assemblies to produce an array of small appliances. One of its high cost/high volume assemblies, the XO-01, has an estimated annual demand of 8,000 units. Talbot estimates the cost to place an order is $50, and the holding cost for each assembly is $20 per year. The company operates 250 days per year. Use the information in Scenario 9.3. What is the annual inventory holding cost if Talbot orders using the EOQ quantity? O less than or equal to $1,500 Ogreater than $4,000 but less than or equal to $6,500 O greater than $6,500 O greater than $1,500 but less than or equal to $4,000 Nextarrow_forward
- Analyze Walmart Inc. operations and conducting a strengths, weaknesses, opportunities, and threats (SWOT) analysis. Pay attention to Walmart Inc. strengths and opportunities to come up with a social cause that meshes well with them. Focusing on areas where Walmart Inc. excels and then finding a social cause that can benefit from Walmart Inc. strengths can also ultimately help Consider how shareholder and stakeholder theories of ethics will impact the selection of a target social cause for Walmart Inc to pursue. What responsibility does Walmart Inc. owe to its stockholders and stakeholders? Will pursuing a social responsibility program detract from the responsibilities to these two groups? Any program that is implement will redirect resources toward the social cause and away from the stockholders and stakeholders. Is it ethical? Walmart Inc SWOT analysis. Justify each item of the analysis. Evaluate the ethical implications of pursuing a social responsibility program in terms of the…arrow_forwardDetail Instructions Consider the following activities, activity times and precedence relations for a hypothetical Athletic Club Building project. Activity Activity Description Normal Time (weeks) Immediate Predecessors A Form project team 9 B Prepare renovation plans 12 A C Demolish interior space 10 B D Upgrade utility systems 20 A E Select equipment, furniture & 10 B fixtures F Hire Staff 10 A G Renovate building 30 B,C H Purchase equipment, furniture & 26 E fixtures Install equipment, furniture & 4 D.G.H fixtures 3 FI J Train staffarrow_forwardHow do you think smaller companies, with less sophisticated systems compared to giants like Amazon, can apply Little's Law to optimize their operations? Please Provide a referencearrow_forward
- What are your thoughts on how businesses can account for real-world variability when applying Little's Law, especially in industries where demand is highly unpredictable? Please provide referencearrow_forwardHow can businesses integrate Petri Net modeling with Little's Law to enhance supply chain resilience, especially in unexpected disruptions such as supplier delays or demand fluctuations? Please provide a refernencearrow_forwardHow can businesses integrate Petri Net modeling with Little's Law to enhance supply chain resilience, especially in unexpected disruptions such as supplier delays or demand fluctuations?arrow_forward
- Purchasing and Supply Chain ManagementOperations ManagementISBN:9781285869681Author:Robert M. Monczka, Robert B. Handfield, Larry C. Giunipero, James L. PattersonPublisher:Cengage LearningManagement, Loose-Leaf VersionManagementISBN:9781305969308Author:Richard L. DaftPublisher:South-Western College PubMarketingMarketingISBN:9780357033791Author:Pride, William MPublisher:South Western Educational Publishing
- Practical Management ScienceOperations ManagementISBN:9781337406659Author:WINSTON, Wayne L.Publisher:Cengage,
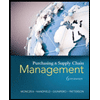
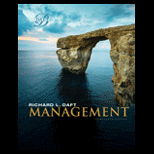
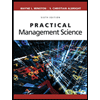