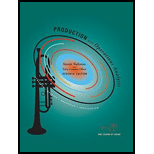
Concept explainers
a
To determine:
Inventory at the end of each month assuming excess demand are back − ordered.
Introduction:
Demand of any product is the total units of product demanded by a consumer at a given price during a given period of time.
b
To determine:
Stock − out cost when excess demand at the end of each month is lost and when excess demand at the end of each month is back ordered.
Introduction:
Stock out cost is the income which is unearned due to shortage in inventory.
c
To determine:
Stock out cost incurred during six months when demand is fulfilled on a first − come, first basis.
Introduction:
Stock out cost is the income which is unearned due to shortage in inventory.
d
To determine:
Circumstances under which cost criteria is most appropriate.
Introduction:
Stock out cost is the income which is unearned due to shortage in inventory.

Want to see the full answer?
Check out a sample textbook solution
Chapter 4 Solutions
Production and Operations Analysis, Seventh Edition
- Perform resource leveling. Assume that each task can be performed independently of the other tasks.arrow_forwardher psychological test and interview while Ms. Domingo got a good score and good psychological result. Ms. Sabado’s father is your godfather and a good friend of yours. Ms. Sabado asked you a favor to consider her daughter and if possible she will be hired. He also added that every job can be learned through training and mentoring. The situation bothers you since it’s your duty to recommend to the higher authority whom to hire.Questions:1. As a supervisor how will you diced on this situation?2. It’s time to decide, who among the two (2) will be hired? Why?arrow_forwardHelp me solve part C.arrow_forward
- Boreki Enterprise has the following 10 items in inventory. Theodore Boreki asks you, a recent OM graduate, to divide these items into ABC classifications. Fill in the blanks and then answer the following questions. (Round dollar volume to the nearest whole number and percentage of dollar volume to two decimal places.) Dollar Item Annual Demand Cost/Unit Volume % of Total Dollar Volume A2 10 120 B8 4000 12 48,000 5.65 C7 1500 45 67,500 7.94 D1 2000 44 E9 1000 20 20,000 2.35 F3 25 40 G2 200 1500 300,000 35.29 H2 600 20 12,000 1.41 15 1000 300 J8 2500 5 12,500 1.47arrow_forwardBobby Flay is responsible for assigning steel workers to a structural steel infrastructure construction task. Having taken Project Management at the University of Portland, he understands the importance of managing risk. To ensure that the task takes place as scheduled, Bobby must ensure that there are at least 8 steel workers available at the start of the task. Based on analysis of similar tasks, he estimates that steel workers will show up for the task with probability 0.9. If Bobby wants to be 97% sure that there are enough tasks to begin as scheduled, he should assign ______ steel workers to the task.arrow_forwardMarcela Valladolid needs to assign resources to a task on a new high-tech development project at Jonathon's Pool Supplies. According to her estimates, the task's work content (in hours) is 408. Marcela needs help in determining an appropriate number of resources to allocate to the task. Marcela read somewhere that, when it comes to project staffing, more is not always better. Assuming that the direct labor rate per hour is $93, the indirect and over head rate per unit time is $73.62, assigned resources are dedicated to the task full time, and that 0.02 hours of communication per coordination are required per link per hour worked, help Marcela by determining the following: What is the minimum total cost: What resource allocation minimizes the total cost: What is the minimum duration: What is the duration minimizing number of resources: If Marcela assigns 12 FTEs to the task, the task metrics would be: Total Cost: Total Duration: Note: enter durations to 1 decimal place and costs…arrow_forward
- 1 point) Market Fresh Foods is looking to develop a new strategic plan. Guillermo Santiago has been developing a project plan and has identified the following tasks, precedence relations, normal task durations, and resource requirements. Guillermo has studied project management at the University of Portland and knows that the makespan of the project may be determined from the information in the table using the critical path method. Guillermo also learned a simple heuristic for evaluating resource sufficiency. Help Guillermo by answering the following related assuming 3 workers per week and a due date of 302.8: Project Work Content: Total Resource Capacity: Minimum due date for which 3 resources is sufficient: Minimum resource level that could make due date of 302.8 feasible:arrow_forwardHow an individual attending a university can help the development of a country?arrow_forwardWhat are the job description or role in Operations management? Please answer at your own easy words.arrow_forward
- I am currently working as a Sub Assistant Manager at Advance Personal Care Limited (APCL), a concern of Pran Group. I hold a Bachelor of Pharmacy (Professional) degree. I recently came across a job posting on BD Jobs for a position in Project Management within Quality Operations. I want to apply for this role and need to update my CV accordingly. Could you please guide me on what key information, achievements, and skills I should add or highlight in my CV to align with this new role? Note that i have 8 months experience on this role. Please write at your own easy words. Please don't use Ai answering this question. I will rate you positive if you do so.arrow_forwardI am currently working as a Sub Assistant Manager at Advance Personal Care Limited (APCL), a concern of Pran Group. I hold a Bachelor of Pharmacy (Professional) degree. I recently came across a job posting on BD Jobs for a position in Project Management within Quality Operations. I want to apply for this role and need to update my CV accordingly. Could you please guide me on what key information, achievements, and skills I should add or highlight in my CV to align with this new role? Note that i have 8 months experience on this role. Please don't use Ai answering this question. I will rate you positive if you do so.arrow_forwardWhat are the three main concepts of understanding in Operations Management?arrow_forward
- Purchasing and Supply Chain ManagementOperations ManagementISBN:9781285869681Author:Robert M. Monczka, Robert B. Handfield, Larry C. Giunipero, James L. PattersonPublisher:Cengage LearningPractical Management ScienceOperations ManagementISBN:9781337406659Author:WINSTON, Wayne L.Publisher:Cengage,
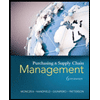
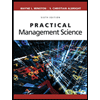