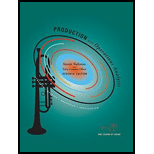
Production and Operations Analysis, Seventh Edition
7th Edition
ISBN: 9781478623069
Author: Steven Nahmias, Tava Lennon Olsen
Publisher: Waveland Press, Inc.
expand_more
expand_more
format_list_bulleted
Concept explainers
Question
Chapter 4, Problem 42AP
Summary Introduction
Interpretation:The optimal size of each production run are tibe determined assuming that cards are produced at the rate of 75,000 per week.
Concept Introduction:
Economic order quantity sometimes EOQ refers to the technique that is used by the organizations to determine the quantity and volumeororder needed to fulfill the customer demand while minimizing the cost of the item.
Expert Solution & Answer

Want to see the full answer?
Check out a sample textbook solution
Students have asked these similar questions
1) View the video Alton Bridge (12.16 mins, Ctrl + Click on the link), and please answer the following questions: https://meida.gaspar.mheducation.com/GASPARPlayer/play.html?id=24qHEm8aNZExFciJtZQbqli
a) According to the video, what are the various steps involved in managing projects?
b) What were the different phases of the Alton Bridge project?
c) What are the two widely used scheduling techniques, and under what phase of the Alton Bridge project are they discussed?
Note: As a rough guideline, please try to keep the written submission to a paragraph or so for each of the questions.
2) The following is a table of activities associated with a mining project at Lunar Industries, their durations, and what activities each must precede:
Activity
Duration (weeks)
Precedes
A (start)
1
B, C
B
1
E
C
4
F
E
2
F
F (end)
2
-
The AOM project diagram is as given below:
a) What is the critical path (list all activities in the…
1) View the video Alton Bridge (12.16 mins, Ctrl + Click on the link), and please answer the following questions:
a) According to the video, what are the various steps involved in managing projects?
b) What were the different phases of the Alton Bridge project?
c) What are the two widely used scheduling techniques, and under what phase of the Alton Bridge project are they discussed?
Note: As a rough guideline, please try to keep the written submission to a paragraph or so for each of the questions.
2) The following is a table of activities associated with a mining project at Lunar Industries, their durations, and what activities each must precede:
Activity
Duration (weeks)
Precedes
A (start)
1
B, C
B
1
E
C
4
F
E
2
F
F (end)
2
-
The AOM project diagram is as given below:
With all the problems companies are currently facing, why do so many choose to expand into international markets? What are the advantages of expanding beyond the domestic market?
Chapter 4 Solutions
Production and Operations Analysis, Seventh Edition
Ch. 4.4 - Prob. 1PCh. 4.4 - Prob. 2PCh. 4.4 - Prob. 3PCh. 4.4 - Prob. 4PCh. 4.4 - Prob. 5PCh. 4.4 - Prob. 6PCh. 4.4 - Prob. 7PCh. 4.4 - Prob. 8PCh. 4.4 - Prob. 9PCh. 4.5 - Prob. 10P
Ch. 4.5 - Prob. 11PCh. 4.5 - Prob. 12PCh. 4.5 - Prob. 13PCh. 4.5 - Prob. 14PCh. 4.5 - Prob. 15PCh. 4.5 - Prob. 16PCh. 4.6 - Prob. 17PCh. 4.6 - Prob. 18PCh. 4.6 - Prob. 19PCh. 4.6 - Prob. 20PCh. 4.7 - Prob. 21PCh. 4.7 - Prob. 22PCh. 4.7 - Prob. 23PCh. 4.7 - Prob. 24PCh. 4.7 - Prob. 25PCh. 4.8 - Prob. 26PCh. 4.8 - Prob. 27PCh. 4.8 - Prob. 28PCh. 4.9 - Prob. 29PCh. 4.9 - Prob. 30PCh. 4 - Prob. 31APCh. 4 - Prob. 32APCh. 4 - Prob. 33APCh. 4 - Prob. 34APCh. 4 - Prob. 35APCh. 4 - Prob. 36APCh. 4 - Prob. 37APCh. 4 - Prob. 38APCh. 4 - Prob. 39APCh. 4 - Prob. 40APCh. 4 - Prob. 41APCh. 4 - Prob. 42APCh. 4 - Prob. 43APCh. 4 - Prob. 44APCh. 4 - Prob. 45AP
Knowledge Booster
Learn more about
Need a deep-dive on the concept behind this application? Look no further. Learn more about this topic, operations-management and related others by exploring similar questions and additional content below.Similar questions
- Perform resource leveling. Assume that each task can be performed independently of the other tasks.arrow_forwardher psychological test and interview while Ms. Domingo got a good score and good psychological result. Ms. Sabado’s father is your godfather and a good friend of yours. Ms. Sabado asked you a favor to consider her daughter and if possible she will be hired. He also added that every job can be learned through training and mentoring. The situation bothers you since it’s your duty to recommend to the higher authority whom to hire.Questions:1. As a supervisor how will you diced on this situation?2. It’s time to decide, who among the two (2) will be hired? Why?arrow_forwardHelp me solve part C.arrow_forward
- Boreki Enterprise has the following 10 items in inventory. Theodore Boreki asks you, a recent OM graduate, to divide these items into ABC classifications. Fill in the blanks and then answer the following questions. (Round dollar volume to the nearest whole number and percentage of dollar volume to two decimal places.) Dollar Item Annual Demand Cost/Unit Volume % of Total Dollar Volume A2 10 120 B8 4000 12 48,000 5.65 C7 1500 45 67,500 7.94 D1 2000 44 E9 1000 20 20,000 2.35 F3 25 40 G2 200 1500 300,000 35.29 H2 600 20 12,000 1.41 15 1000 300 J8 2500 5 12,500 1.47arrow_forwardBobby Flay is responsible for assigning steel workers to a structural steel infrastructure construction task. Having taken Project Management at the University of Portland, he understands the importance of managing risk. To ensure that the task takes place as scheduled, Bobby must ensure that there are at least 8 steel workers available at the start of the task. Based on analysis of similar tasks, he estimates that steel workers will show up for the task with probability 0.9. If Bobby wants to be 97% sure that there are enough tasks to begin as scheduled, he should assign ______ steel workers to the task.arrow_forwardMarcela Valladolid needs to assign resources to a task on a new high-tech development project at Jonathon's Pool Supplies. According to her estimates, the task's work content (in hours) is 408. Marcela needs help in determining an appropriate number of resources to allocate to the task. Marcela read somewhere that, when it comes to project staffing, more is not always better. Assuming that the direct labor rate per hour is $93, the indirect and over head rate per unit time is $73.62, assigned resources are dedicated to the task full time, and that 0.02 hours of communication per coordination are required per link per hour worked, help Marcela by determining the following: What is the minimum total cost: What resource allocation minimizes the total cost: What is the minimum duration: What is the duration minimizing number of resources: If Marcela assigns 12 FTEs to the task, the task metrics would be: Total Cost: Total Duration: Note: enter durations to 1 decimal place and costs…arrow_forward
- 1 point) Market Fresh Foods is looking to develop a new strategic plan. Guillermo Santiago has been developing a project plan and has identified the following tasks, precedence relations, normal task durations, and resource requirements. Guillermo has studied project management at the University of Portland and knows that the makespan of the project may be determined from the information in the table using the critical path method. Guillermo also learned a simple heuristic for evaluating resource sufficiency. Help Guillermo by answering the following related assuming 3 workers per week and a due date of 302.8: Project Work Content: Total Resource Capacity: Minimum due date for which 3 resources is sufficient: Minimum resource level that could make due date of 302.8 feasible:arrow_forwardHow an individual attending a university can help the development of a country?arrow_forwardWhat are the job description or role in Operations management? Please answer at your own easy words.arrow_forward
- I am currently working as a Sub Assistant Manager at Advance Personal Care Limited (APCL), a concern of Pran Group. I hold a Bachelor of Pharmacy (Professional) degree. I recently came across a job posting on BD Jobs for a position in Project Management within Quality Operations. I want to apply for this role and need to update my CV accordingly. Could you please guide me on what key information, achievements, and skills I should add or highlight in my CV to align with this new role? Note that i have 8 months experience on this role. Please write at your own easy words. Please don't use Ai answering this question. I will rate you positive if you do so.arrow_forwardI am currently working as a Sub Assistant Manager at Advance Personal Care Limited (APCL), a concern of Pran Group. I hold a Bachelor of Pharmacy (Professional) degree. I recently came across a job posting on BD Jobs for a position in Project Management within Quality Operations. I want to apply for this role and need to update my CV accordingly. Could you please guide me on what key information, achievements, and skills I should add or highlight in my CV to align with this new role? Note that i have 8 months experience on this role. Please don't use Ai answering this question. I will rate you positive if you do so.arrow_forwardWhat are the three main concepts of understanding in Operations Management?arrow_forward
arrow_back_ios
SEE MORE QUESTIONS
arrow_forward_ios
Recommended textbooks for you
- Practical Management ScienceOperations ManagementISBN:9781337406659Author:WINSTON, Wayne L.Publisher:Cengage,Purchasing and Supply Chain ManagementOperations ManagementISBN:9781285869681Author:Robert M. Monczka, Robert B. Handfield, Larry C. Giunipero, James L. PattersonPublisher:Cengage Learning
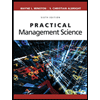
Practical Management Science
Operations Management
ISBN:9781337406659
Author:WINSTON, Wayne L.
Publisher:Cengage,
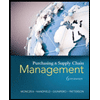
Purchasing and Supply Chain Management
Operations Management
ISBN:9781285869681
Author:Robert M. Monczka, Robert B. Handfield, Larry C. Giunipero, James L. Patterson
Publisher:Cengage Learning
Inventory Management | Concepts, Examples and Solved Problems; Author: Dr. Bharatendra Rai;https://www.youtube.com/watch?v=2n9NLZTIlz8;License: Standard YouTube License, CC-BY