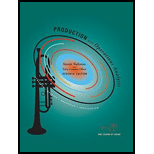
Production and Operations Analysis, Seventh Edition
7th Edition
ISBN: 9781478623069
Author: Steven Nahmias, Tava Lennon Olsen
Publisher: Waveland Press, Inc.
expand_more
expand_more
format_list_bulleted
Concept explainers
Question
Chapter 4, Problem 35AP
Summary Introduction
Interpretation:The supplier that should be used from the available two options is to be determined.
Concept introduction: Economic order quantity refers to the ideal quantity which an organization should order in order to minimize inventory costs.
Expert Solution & Answer

Want to see the full answer?
Check out a sample textbook solution
Students have asked these similar questions
Agree or disagree with post
On the surface, the numbers in financial statements do present a snapshot of a company's financial position and performance. However, just looking at the raw numbers often doesn't tell the whole story or reveal underlying trends and relationships that are crucial for making informed decisions. Think of it like looking at individual pieces of a puzzle. Each number is a piece, providing some information. But to see the complete picture – the company's overall financial health, its performance over time, how it compares to its peers, and its potential future – you need to assemble those pieces using different analytical tools.
For example:
Horizontal analysis helps us understand how specific financial statement items have changed over multiple periods. Is revenue growing? Are expenses increasing at a faster rate than sales? This reveals trends that a single year's numbers wouldn't show.
Vertical analysis allows us to see the relative size of each item within…
What can you do in response to an insulting offer?
Agree or disagree with post
If someone hits you with an insulting offer, the first thing to do is not take it personally. It’s normal to feel a little offended, but blowing up or shutting down won’t help your case. Better move is to stay calm and treat it like a misunderstanding or just the first step in the conversation. That way, you keep things respectful but still let them know the offer doesn’t sit right with you. It also helps to back up your response with facts. Bring in things like your experience, numbers, or any specific results you delivered. That can shift the conversation away from feelings and toward the value you bring.
Agree or disagree with post
Chapter 4 Solutions
Production and Operations Analysis, Seventh Edition
Ch. 4.4 - Prob. 1PCh. 4.4 - Prob. 2PCh. 4.4 - Prob. 3PCh. 4.4 - Prob. 4PCh. 4.4 - Prob. 5PCh. 4.4 - Prob. 6PCh. 4.4 - Prob. 7PCh. 4.4 - Prob. 8PCh. 4.4 - Prob. 9PCh. 4.5 - Prob. 10P
Ch. 4.5 - Prob. 11PCh. 4.5 - Prob. 12PCh. 4.5 - Prob. 13PCh. 4.5 - Prob. 14PCh. 4.5 - Prob. 15PCh. 4.5 - Prob. 16PCh. 4.6 - Prob. 17PCh. 4.6 - Prob. 18PCh. 4.6 - Prob. 19PCh. 4.6 - Prob. 20PCh. 4.7 - Prob. 21PCh. 4.7 - Prob. 22PCh. 4.7 - Prob. 23PCh. 4.7 - Prob. 24PCh. 4.7 - Prob. 25PCh. 4.8 - Prob. 26PCh. 4.8 - Prob. 27PCh. 4.8 - Prob. 28PCh. 4.9 - Prob. 29PCh. 4.9 - Prob. 30PCh. 4 - Prob. 31APCh. 4 - Prob. 32APCh. 4 - Prob. 33APCh. 4 - Prob. 34APCh. 4 - Prob. 35APCh. 4 - Prob. 36APCh. 4 - Prob. 37APCh. 4 - Prob. 38APCh. 4 - Prob. 39APCh. 4 - Prob. 40APCh. 4 - Prob. 41APCh. 4 - Prob. 42APCh. 4 - Prob. 43APCh. 4 - Prob. 44APCh. 4 - Prob. 45AP
Knowledge Booster
Learn more about
Need a deep-dive on the concept behind this application? Look no further. Learn more about this topic, operations-management and related others by exploring similar questions and additional content below.Similar questions
- Agree or disagree with the post When you get an insulting offer, the best thing to do is stay calm and professional. Try not to take it personally or react out of anger. Instead, ask questions to understand why the offer was so low. This helps you get a better idea of what the other person is thinking. After that, you can respond with a counteroffer that shows your value. Use simple facts like your skills, experience, and what others in your field are getting paid to back up your request. If the person still refuses to offer something fair, it’s okay to politely say no and walk away. Standing up for yourself in a respectful way shows confidence and helps others take you seriously. Agree or disagree with the postarrow_forwardRegarding perceptions that can occur when negotiating in different places and at different times, the continuation norm in e-negotiations is best described as _____. Group of answer choices A. negotiators' beliefs that negotiations are worth continuing B. the act of thinking about how things might have turned out differently C. the tendency for e-communicators to ascribe diabolical intentions to the other party D. the tendency for negotiators to behave as if they are communicating synchronously when in fact they are notarrow_forwardIn any discussion or meeting, there is a tendency for a minority of people to do most of the talking. A key determinant of who dominates the conversation is _____. Group of answer choices A. their status within the group B. their network of social connections C. their gender D. their agearrow_forward
- With regard to intergenerational negotiation, the _____ generation has vast numbers of relationships but few of them are deep. They spend more time communicating virtually than face-to-face. Their personal and work networks are vital to their on-the-fly learning and problem-solving skills. Armed with tools for working anywhere at any time, this generation puts more value in leading a balanced life and flexibility with their work and life demands. Group of answer choices A. mature B. boomer C. millennial D. Generation Xarrow_forwardIf a negotiator has less power than the counterparty and an unattractive BATNA, which communication medium might help the less-powerful negotiator claim more resources?arrow_forwardCould you help explain what the foundations of faith are? What are their strategies?arrow_forward
- Hi! Can you guys help me with this? Thank you! Please write-up summarizing the core message of the movie/documentary and the connection to the course material The documentary is Poisoned: The Dirty Truth About Your Food directed by Stephanie Soechtig from Netflix. * Here are the course material: Global Logistics Global Transportation; Global Inventory Management Global Operation Global Market Channels Purchasing Stategies: Outsourcing; Offshoring; Nearshoring; Multi-sourcing & Co-sourcing Make or Buy decisions Global Supply Chain Infrastructure: Transportation Infrastructure; Communication Infrastructure; Utilities Infrastructure; Technology Infrastructure Supply Chain Risks: • Supply Risks – disruption of supply, inventory and schedules. • Operational Risks – breakdown of operations, changes in technologies. • Demand Risks – variations in demand.• Security Risks – theft, sabotage, terrorism, counterfeiting.• Macro Risks – economic shifts, recession, wage hikes, varying…arrow_forwardHi! Can you guys help me with this? Thank you! Please write-up summarizing the core message of the movie/documentary and the connection to the course material The documentary is American Factory by Steven Bognar & Julia Reichert from Netflix * Here the course material: Global Logistics Global Transportation; Global Inventory Management Global Operation Global Market Channels Purchasing Stategies: Outsourcing; Offshoring; Nearshoring; Multi-sourcing & Co-sourcing Make or Buy decsions Global Supply Chain Infrastructure: Transportation Infrastructure; Communication Infrastructure; Utilities Infrastructure; Technology Infrastructure Supply Chain Risks: • Supply Risks – disruption of supply, inventory and schedules. • Operational Risks – breakdown of operations, changes in technologies. • Demand Risks – variations in demand.• Security Risks – theft, sabotage, terrorism, counterfeiting.• Macro Risks – economic shifts, recession, wage hikes, varying exchangerates.• Policy Risks –…arrow_forward1) View the video Alton Bridge (12.16 mins, Ctrl + Click on the link), and please answer the following questions: https://meida.gaspar.mheducation.com/GASPARPlayer/play.html?id=24qHEm8aNZExFciJtZQbqli a) According to the video, what are the various steps involved in managing projects? b) What were the different phases of the Alton Bridge project? c) What are the two widely used scheduling techniques, and under what phase of the Alton Bridge project are they discussed? Note: As a rough guideline, please try to keep the written submission to a paragraph or so for each of the questions. 2) The following is a table of activities associated with a mining project at Lunar Industries, their durations, and what activities each must precede: Activity Duration (weeks) Precedes A (start) 1 B, C B 1 E C 4 F E 2 F F (end) 2 - The AOM project diagram is as given below: a) What is the critical path (list all activities in the…arrow_forward
- 1) View the video Alton Bridge (12.16 mins, Ctrl + Click on the link), and please answer the following questions: a) According to the video, what are the various steps involved in managing projects? b) What were the different phases of the Alton Bridge project? c) What are the two widely used scheduling techniques, and under what phase of the Alton Bridge project are they discussed? Note: As a rough guideline, please try to keep the written submission to a paragraph or so for each of the questions. 2) The following is a table of activities associated with a mining project at Lunar Industries, their durations, and what activities each must precede: Activity Duration (weeks) Precedes A (start) 1 B, C B 1 E C 4 F E 2 F F (end) 2 - The AOM project diagram is as given below:arrow_forwardWith all the problems companies are currently facing, why do so many choose to expand into international markets? What are the advantages of expanding beyond the domestic market?arrow_forwardPerform resource leveling. Assume that each task can be performed independently of the other tasks.arrow_forward
arrow_back_ios
SEE MORE QUESTIONS
arrow_forward_ios
Recommended textbooks for you
- Purchasing and Supply Chain ManagementOperations ManagementISBN:9781285869681Author:Robert M. Monczka, Robert B. Handfield, Larry C. Giunipero, James L. PattersonPublisher:Cengage LearningPractical Management ScienceOperations ManagementISBN:9781337406659Author:WINSTON, Wayne L.Publisher:Cengage,
- MarketingMarketingISBN:9780357033791Author:Pride, William MPublisher:South Western Educational PublishingFoundations of Business (MindTap Course List)MarketingISBN:9781337386920Author:William M. Pride, Robert J. Hughes, Jack R. KapoorPublisher:Cengage LearningFoundations of Business - Standalone book (MindTa...MarketingISBN:9781285193946Author:William M. Pride, Robert J. Hughes, Jack R. KapoorPublisher:Cengage Learning
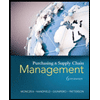
Purchasing and Supply Chain Management
Operations Management
ISBN:9781285869681
Author:Robert M. Monczka, Robert B. Handfield, Larry C. Giunipero, James L. Patterson
Publisher:Cengage Learning
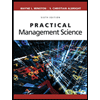
Practical Management Science
Operations Management
ISBN:9781337406659
Author:WINSTON, Wayne L.
Publisher:Cengage,
Marketing
Marketing
ISBN:9780357033791
Author:Pride, William M
Publisher:South Western Educational Publishing
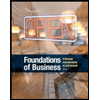
Foundations of Business (MindTap Course List)
Marketing
ISBN:9781337386920
Author:William M. Pride, Robert J. Hughes, Jack R. Kapoor
Publisher:Cengage Learning
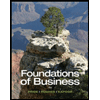
Foundations of Business - Standalone book (MindTa...
Marketing
ISBN:9781285193946
Author:William M. Pride, Robert J. Hughes, Jack R. Kapoor
Publisher:Cengage Learning
Inventory Management | Concepts, Examples and Solved Problems; Author: Dr. Bharatendra Rai;https://www.youtube.com/watch?v=2n9NLZTIlz8;License: Standard YouTube License, CC-BY