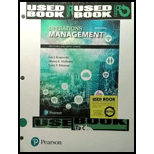
Operations Management: Processes And Supply Chains (12th Edition) (what's New In Operations Management)
12th Edition
ISBN: 9780134742205
Author: Lee J. Krajewski, Manoj K. Malhotra, Larry P. Ritzman
Publisher: PEARSON
expand_more
expand_more
format_list_bulleted
Concept explainers
Textbook Question
Chapter 11, Problem 5P
Tabard Industries forecasted the following demand for one of its most profitable products for the next 8 weeks: 120, 120, 120, 100, 100, 100, 80, and 80 units. The booked customer orders for this product, starting in week 1 are: 100, 80, 60, 40, 10, 10, 0, and 0 units. The current on-hand inventory is 150 units, the order quantity is 200 units, and the lead time is 1 week.
- Develop a MPS for this product.
- The marketing department revised its
forecast. Starting with week 1, the new forecasts are: 120, 120, 120, 150, 150, 150, 100, and 100 units. Assuming that the prospective MPS you developed in part (a) does not change, prepare a revised MPS record. Comment on the situation that Tabard now faces. - Returning to the original forecasted demand level and the MPS record you developed in part (a), assume that marketing accepted a new customer order for 200 units in week 2, and thereby booked orders in week 2 is now 280 units. Assuming that the prospective MPS you developed in part (a) does not change, prepare a revised MPS record. Comment on the situation that Tabard now faces.
Expert Solution & Answer

Want to see the full answer?
Check out a sample textbook solution
Students have asked these similar questions
not use ai please
oimmnjjjh
Summarize the ethical dilemma encountered in Walmart Inc.
Which of Kohlberg's stages of moral development is represented? Is there other theories of moral development that better describes the example?
Postulate the (hypothetical or real) best- and worst-case outcomes of this dilemma.
Is it agreeable with the selection of Kohlberg's stages of moral development for their examples?
Is there another theory of moral development that would better describe their examples?
Chapter 11 Solutions
Operations Management: Processes And Supply Chains (12th Edition) (what's New In Operations Management)
Ch. 11 - Consider the master flight schedule of a major...Ch. 11 - For an organization of your choice, such as where...Ch. 11 - Consider a service provider that is in the...Ch. 11 - Complete the MPS record in Figure 11.29 for a...Ch. 11 - Complete the MPS record in Figure 11.30 for a...Ch. 11 - Prob. 3PCh. 11 - Figure 11.31 shows a partially completed MPS...Ch. 11 - Tabard Industries forecasted the following demand...Ch. 11 - Figure 11.32 shows a partially completed MPS...Ch. 11 - The forecasted requirements for an electric hand...
Ch. 11 - A forecast of 240 units in January, 320 units in...Ch. 11 - An end items demand forecasts for the next 6 weeks...Ch. 11 - An end items demand forecasts for the next 10...Ch. 11 - Consider the bill of materials (BOM) in Figure...Ch. 11 - Product A is made from components B, C, and D....Ch. 11 - What is the lead time (in weeks) to respond to a...Ch. 11 - Product A is made from components B and C. Item B,...Ch. 11 - Refer to Figure 11.23 and Solved Problem 1. If...Ch. 11 - The partially completed inventory record for the...Ch. 11 - The partially completed inventory record for the...Ch. 11 - The partially completed inventory record for the...Ch. 11 - Figure 11.38 shows a partially completed inventory...Ch. 11 - A partially completed inventory record for the...Ch. 11 - The BOM for product A is shown in Figure 11.40,...Ch. 11 - The BOMs for products A & B and data from the...Ch. 11 - Figure 11.42 illustrates the BOM for product A....Ch. 11 - The following information is available for three...Ch. 11 - Figure 11.44 shows the BOMs for two products, A...Ch. 11 - The BOM for product A is shown in Figure 11.45....Ch. 11 - Refer to Solved Problem 1 (Figure 11.23) for the...Ch. 11 - The bill of materials and the data from the...Ch. 11 - The bill of materials and the data from the...Ch. 11 - The McDuff Credit Union advertises their ability...Ch. 11 - Suppose that the POQ for item B is changed from 3...Ch. 11 - As the on-hand inventory for item C increases from...Ch. 11 - As the fixed order quantity (FOQ) for item D...Ch. 11 - As the lead time for item C changes, what happens...
Additional Business Textbook Solutions
Find more solutions based on key concepts
Which of the following is a primary activity in the value chain?
purchasing
accounting
post-sales service
human...
Accounting Information Systems (14th Edition)
Fundamental and Enhancing Characteristics. Identify whether the following items are fundamental characteristics...
Intermediate Accounting (2nd Edition)
E6-14 Using accounting vocabulary
Learning Objective 1, 2
Match the accounting terms with the corresponding d...
Horngren's Accounting (12th Edition)
1-1. Define marketing and outline the steps in the marketing process. (AASCB: Communication)
Marketing: An Introduction (13th Edition)
How is activity-based costing useful for pricing decisions?
Horngren's Cost Accounting: A Managerial Emphasis (16th Edition)
Knowledge Booster
Learn more about
Need a deep-dive on the concept behind this application? Look no further. Learn more about this topic, operations-management and related others by exploring similar questions and additional content below.Similar questions
- Four-drive theory recommends that companies must keep fulfillment of the four drives in balance. What is this “balance” and why is it important? Can you Give an example (real or hypothetical) of how a company maintains balanced drive fulfillment. Also describe a company that does not provide this balance, including the consequences of this imbalance on employees’ attitudes and behavior. Thank youarrow_forwardwhat criteria would you utilize to determine if someone's pay is “fair” or “egregious?” Additionally, what should be the mechanism or process to determine how much greater an organizational executive should be paid versus line-level employees?arrow_forwardDefine the concept of a compensation philosophy, including the components that should be addressed in a compensation philosophy. Assess why a compensation philosophy is so foreign to most organizations and how you can best encourage an organization to create its own compensation philosophy that is beneficial to attracting the best talent.arrow_forward
- 1) View the videos Taco Bell test-drives Live Mas restaurant concept in South Bay (0.32 mins, Ctrl+Click on the link) https://www.youtube.com/watch?v=04wRc5Wg8GU , and First-ever Taco Bell Live Mas Café serving exclusive drinks in Chula Vista (1.56 mins, Ctrl+Click on the link) https://www.youtube.com/watch?v=fq6jDxJk1LM , and answer the following questions: a) What is driving Taco Bell to try a beverage-focused format? b) What type of a process strategy does their beverage-focused format represent? c) What operational issues do you think Taco Bell would face from their beverage-focused format? d) What do you think are the main advantages and disadvantages of kiosk ordering? Note: As a rough guideline, please try to keep the written submission to one or two paragraphs for each of the questions. 2) Taipei Pharmaceuticals is planning to open a new manufacturing facility as part of its expansion plans. The firm has narrowed down the search to locate its new manufacturing facility…arrow_forward1) View the videos Taco Bell test-drives Live Mas restaurant concept in South Bay (0.32 mins, Ctrl+Click on the link) https://www.youtube.com/watch?v=04wRc5Wg8GU , and First-ever Taco Bell Live Mas Café serving exclusive drinks in Chula Vista (1.56 mins, Ctrl+Click on the link) https://www.youtube.com/watch?v=fq6jDxJk1LM , and answer the following questions: a) What is driving Taco Bell to try a beverage-focused format? b) What type of a process strategy does their beverage-focused format represent? c) What operational issues do you think Taco Bell would face from their beverage-focused format? d) What do you think are the main advantages and disadvantages of kiosk ordering? Note: As a rough guideline, please try to keep the written submission to one or two paragraphs for each of the questions. 2) Taipei Pharmaceuticals is planning to open a new manufacturing facility as part of its expansion plans. The firm has narrowed down the search to locate its new manufacturing facility…arrow_forwardThe Clothing Shack is an online retailer of men's, women's, and children's clothing. The company has been in business for four years and makes a modest profit from its online sales. However, in an effort to compete successfully against online retailing heavyweights, the Clothing Shack's marketing director, Makaya O'Neil, has determined that the Clothing Shack's marketing information systems need improvement. Ms. O'Neil feels that the Clothing Shack should begin sending out catalogs to its customers, keep better track of its customer's buying habits, perform target marketing, and provide a more personalized shopping experience for its customers. Several months ago, Ms. O'Neil submitted a systems service request (SSR) to the Clothing Shack's steering committee. The committee unanimously approved this project. You were assigned to the project at that time and have since helped your project team successfully complete the project initiation and planning phase. Your team is now ready to move…arrow_forward
- b-1. Activity ES EF LS LF Slack 1 2 3 4 5 6 7 8 9 b-2. Identify the critical activities, and determine the duration of the project. The critical activities are .arrow_forwardThe forecast for each week of a four-week schedule is 50 units. The MPS rule is to schedule production if the projected on-hand Inventory would be negative without it. Customer orders (committed) are follows: Week Customer Order 1 52 35 20 12 Use a production lot size of 75 units and no beginning Inventory. Determine the available-to-promise (ATP) quantities for each period. Note: Leave no cells blank - be certain to enter "0" wherever required. Period ATP 1 2 3arrow_forwardPrepare a master schedule given this information: The forecast for each week of an eight-week schedule is 60 units. The MPS rule is to schedule production if the projected on-hand Inventory would be negative without it. Customer orders (committed) are as follows: Week Customer Orders 1 2 36 28 4 1 Use a production lot size of 85 units and no beginning inventory. Note: In the ATP row, enter a value of 0 (zero) in any periods where ATP should not be calculated. Leave no cells blank - be certain to enter "0" wherever required. June July 1 2 3 4 5 8 7 8 Forecast 60 60 60 60 60 60 60 60 Customer Orders 38 28 4 1 0 0 0 0 Projected On-Hand Inventory MPS ATParrow_forward
- Sales of tablet computers at Marika Gonzalez's electronics store in Washington, D.C., over the past 10 weeks are shown in the table below: Week 1 2 3 4 5 6 7 8 9 10 Demand 21 21 27 38 25 30 35 24 25 30 a) The forecast for weeks 2 through 10 using exponential smoothing with a = 0.50 and a week 1 initial forecast of 21.0 are (round your responses to two decimal places): Week 1 2 3 4 5 6 7 8 9 10 Demand 21 21 27 38 25 30 35 24 25 30 Forecast 21.0 21 21 24 31 28 29 32 28 26.50 b) For the forecast developed using exponential smoothing (a = 0.50 and initial forecast 21.0), the MAD = |||||sales (round your response to two decimal places).arrow_forwardSales of tablet computers at Marika Gonzalez's electronics store in Washington, D.C., over the past 10 weeks are shown in the table below: Week Demand 1 2 3 4 5 6 7 8 9 10 21 21 27 38 25 30 35 24 25 30 a) The forecast for weeks 2 through 10 using exponential smoothing with a = 0.50 and a week 1 initial forecast of 21.0 are (round your responses to two decimal places): Week 1 2 3 4 5 Demand 21 21 27 38 Forecast 21.0 ☐ G ☐ ☐ 6 7 25 30 35 ∞ ☐ 8 9 10 24 25 30arrow_forwardEach machine costs $3 Million. Building the room with all its attendant safety protection and other ancillary costs increases the spending by an additional $2.0 million dollars per MRI suite. Each machine can perform 2000 scans per year. Each reading of an MRI scan by a radiologist, along with other per-scan-related costs, is $500 per scan. The machine will last five years. Don’t worry about discount rates for this problem Graph the total costs over 5 years as a function of sales for 0-3000 patients annually. Hint: you may need to add a second MRI at some point. Suppose that you want to make a profit of $500 per scan at a target volume of 1000 patients per year, and you purchase only one machine. Superimpose the total revenue curve on top of the total cost curve in (1).arrow_forward
arrow_back_ios
SEE MORE QUESTIONS
arrow_forward_ios
Recommended textbooks for you
- Practical Management ScienceOperations ManagementISBN:9781337406659Author:WINSTON, Wayne L.Publisher:Cengage,Purchasing and Supply Chain ManagementOperations ManagementISBN:9781285869681Author:Robert M. Monczka, Robert B. Handfield, Larry C. Giunipero, James L. PattersonPublisher:Cengage LearningMarketingMarketingISBN:9780357033791Author:Pride, William MPublisher:South Western Educational Publishing
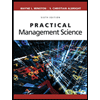
Practical Management Science
Operations Management
ISBN:9781337406659
Author:WINSTON, Wayne L.
Publisher:Cengage,
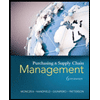
Purchasing and Supply Chain Management
Operations Management
ISBN:9781285869681
Author:Robert M. Monczka, Robert B. Handfield, Larry C. Giunipero, James L. Patterson
Publisher:Cengage Learning
Marketing
Marketing
ISBN:9780357033791
Author:Pride, William M
Publisher:South Western Educational Publishing
Inventory Management | Concepts, Examples and Solved Problems; Author: Dr. Bharatendra Rai;https://www.youtube.com/watch?v=2n9NLZTIlz8;License: Standard YouTube License, CC-BY