28. The shaft shown in Figure P5-28 is supported by bear- ings at each end, which have bores of 20.0 mm. Design the shaft to carry the given load if it is steady and the shaft is stationary. Make the dimension a as large as pos- sible while keeping the stress safe. Determine the required d = 20mm D= ? -a R = ? Length not to scale 5.4 kN d 20mm -125 mm. -250 mm- FIGURE P5-28 (Problems 28, 29, and 30) Problem 5-30 INPUT DATA: Bore Sizes, d= Applied force = Max fillet allowed- Metal Required= Design Factor, N = Length of bore to middle = Full length = RESULTS: Manufacturing Process: Tensile Strength, S_u = Endurance Strength, S_n - Material Factor, C_m= Stress Factor, C_st = 20 5.4 2 SAE 1137 cold-drawn steel 3 125 250 =Stress cold-drawn 676 MPa 252 MPa 1 Unitless 1 Unitless 0.81 Unitless 0.813070766 Unitless 95.76123077 MPa Reliability Factor, C_R= Size Factor, C_S= S'_sm= S_su 507 MPa Estimated Actual Endurnace limit S_n' = 165.9640048 k_t= 1.6 Q= 23113.18372 49.0090887 D= Size Factor when d=20mm, C_S= Estimated Actual Endurnace limit S_n' = S'_sm when d=20 mm = k_t= Max Moment = d = 0.899294106 Unitless 183.563913 105.9163778 MPa 1.8 13288.83958 N*mm 4.921481481 mm mm KN mm mm mm FORMULAS: diameter in the middle portion. The maximum fillet per- missible is 2.0 mm. Use SAE 1137 cold-drawn steel. Use a design factor of 3. 29. Repeat Problem 28, except using a rotating shaft. 30. Repeat Problem 28, except using a shaft that is rotating and transmitting a torque of 150 N m from the left bear- ing to the middle of the shaft. Also, there is a profile key- seat at the middle under the load. Appendix 3 Figure 5-11 Wrought steel has C_m-1.0 C_st 0 for bending stress Table 5-3 C_S=(D/7.62)^-0.11 0.577*S_n'=S'_sm S_su 0.75*S_u S_n'=(S_n)*(C_m)*(C_st)*(C_R)"(C_S) Figure A18-1 Iforgor ((Q*16)/pi)^1/3=D C_S=(D/7.62)^-0.11 S_n'=(S_n)*(C_m)*(C_st)*(C_R)*(C_S) 0.577*S_n' I forgor again d=Moment/Force
28. The shaft shown in Figure P5-28 is supported by bear- ings at each end, which have bores of 20.0 mm. Design the shaft to carry the given load if it is steady and the shaft is stationary. Make the dimension a as large as pos- sible while keeping the stress safe. Determine the required d = 20mm D= ? -a R = ? Length not to scale 5.4 kN d 20mm -125 mm. -250 mm- FIGURE P5-28 (Problems 28, 29, and 30) Problem 5-30 INPUT DATA: Bore Sizes, d= Applied force = Max fillet allowed- Metal Required= Design Factor, N = Length of bore to middle = Full length = RESULTS: Manufacturing Process: Tensile Strength, S_u = Endurance Strength, S_n - Material Factor, C_m= Stress Factor, C_st = 20 5.4 2 SAE 1137 cold-drawn steel 3 125 250 =Stress cold-drawn 676 MPa 252 MPa 1 Unitless 1 Unitless 0.81 Unitless 0.813070766 Unitless 95.76123077 MPa Reliability Factor, C_R= Size Factor, C_S= S'_sm= S_su 507 MPa Estimated Actual Endurnace limit S_n' = 165.9640048 k_t= 1.6 Q= 23113.18372 49.0090887 D= Size Factor when d=20mm, C_S= Estimated Actual Endurnace limit S_n' = S'_sm when d=20 mm = k_t= Max Moment = d = 0.899294106 Unitless 183.563913 105.9163778 MPa 1.8 13288.83958 N*mm 4.921481481 mm mm KN mm mm mm FORMULAS: diameter in the middle portion. The maximum fillet per- missible is 2.0 mm. Use SAE 1137 cold-drawn steel. Use a design factor of 3. 29. Repeat Problem 28, except using a rotating shaft. 30. Repeat Problem 28, except using a shaft that is rotating and transmitting a torque of 150 N m from the left bear- ing to the middle of the shaft. Also, there is a profile key- seat at the middle under the load. Appendix 3 Figure 5-11 Wrought steel has C_m-1.0 C_st 0 for bending stress Table 5-3 C_S=(D/7.62)^-0.11 0.577*S_n'=S'_sm S_su 0.75*S_u S_n'=(S_n)*(C_m)*(C_st)*(C_R)"(C_S) Figure A18-1 Iforgor ((Q*16)/pi)^1/3=D C_S=(D/7.62)^-0.11 S_n'=(S_n)*(C_m)*(C_st)*(C_R)*(C_S) 0.577*S_n' I forgor again d=Moment/Force
Elements Of Electromagnetics
7th Edition
ISBN:9780190698614
Author:Sadiku, Matthew N. O.
Publisher:Sadiku, Matthew N. O.
ChapterMA: Math Assessment
Section: Chapter Questions
Problem 1.1MA
Related questions
Question
Repeat Problem 28, except using a shaft that is rotating
and transmitting a torque of 150 N * m from the left bearing to the middle of the shaft. Also, there is a profile keyseat at the middle under the load.
(I want to understand this problem)

Transcribed Image Text:28. The shaft shown in Figure P5-28 is supported by bear-
ings at each end, which have bores of 20.0 mm. Design
the shaft to carry the given load if it is steady and the
shaft is stationary. Make the dimension a as large as pos-
sible while keeping the stress safe. Determine the required
d = 20mm
D= ?
-a
R = ?
Length not
to scale
5.4 kN
d 20mm
-125 mm.
-250 mm-
FIGURE P5-28 (Problems 28, 29, and 30)

Transcribed Image Text:Problem 5-30
INPUT DATA:
Bore Sizes, d=
Applied force =
Max fillet allowed-
Metal Required=
Design Factor, N =
Length of bore to middle =
Full length =
RESULTS:
Manufacturing Process:
Tensile Strength, S_u =
Endurance Strength, S_n -
Material Factor, C_m=
Stress Factor, C_st =
20
5.4
2
SAE 1137 cold-drawn steel
3
125
250
=Stress
cold-drawn
676 MPa
252 MPa
1 Unitless
1 Unitless
0.81 Unitless
0.813070766 Unitless
95.76123077 MPa
Reliability Factor, C_R=
Size Factor, C_S=
S'_sm=
S_su
507 MPa
Estimated Actual Endurnace limit S_n' =
165.9640048
k_t=
1.6
Q=
23113.18372
49.0090887
D=
Size Factor when d=20mm, C_S=
Estimated Actual Endurnace limit S_n' =
S'_sm when d=20 mm =
k_t=
Max Moment =
d =
0.899294106 Unitless
183.563913
105.9163778 MPa
1.8
13288.83958 N*mm
4.921481481 mm
mm
KN
mm
mm
mm
FORMULAS:
diameter in the middle portion. The maximum fillet per-
missible is 2.0 mm. Use SAE 1137 cold-drawn steel. Use a
design factor of 3.
29. Repeat Problem 28, except using a rotating shaft.
30. Repeat Problem 28, except using a shaft that is rotating
and transmitting a torque of 150 N m from the left bear-
ing to the middle of the shaft. Also, there is a profile key-
seat at the middle under the load.
Appendix 3
Figure 5-11
Wrought steel has C_m-1.0
C_st 0 for bending stress
Table 5-3
C_S=(D/7.62)^-0.11
0.577*S_n'=S'_sm
S_su 0.75*S_u
S_n'=(S_n)*(C_m)*(C_st)*(C_R)"(C_S)
Figure A18-1
Iforgor
((Q*16)/pi)^1/3=D
C_S=(D/7.62)^-0.11
S_n'=(S_n)*(C_m)*(C_st)*(C_R)*(C_S)
0.577*S_n'
I forgor again
d=Moment/Force
Expert Solution

This question has been solved!
Explore an expertly crafted, step-by-step solution for a thorough understanding of key concepts.
Step by step
Solved in 2 steps with 2 images

Recommended textbooks for you
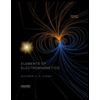
Elements Of Electromagnetics
Mechanical Engineering
ISBN:
9780190698614
Author:
Sadiku, Matthew N. O.
Publisher:
Oxford University Press
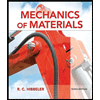
Mechanics of Materials (10th Edition)
Mechanical Engineering
ISBN:
9780134319650
Author:
Russell C. Hibbeler
Publisher:
PEARSON
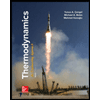
Thermodynamics: An Engineering Approach
Mechanical Engineering
ISBN:
9781259822674
Author:
Yunus A. Cengel Dr., Michael A. Boles
Publisher:
McGraw-Hill Education
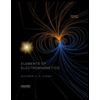
Elements Of Electromagnetics
Mechanical Engineering
ISBN:
9780190698614
Author:
Sadiku, Matthew N. O.
Publisher:
Oxford University Press
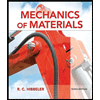
Mechanics of Materials (10th Edition)
Mechanical Engineering
ISBN:
9780134319650
Author:
Russell C. Hibbeler
Publisher:
PEARSON
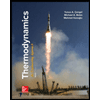
Thermodynamics: An Engineering Approach
Mechanical Engineering
ISBN:
9781259822674
Author:
Yunus A. Cengel Dr., Michael A. Boles
Publisher:
McGraw-Hill Education
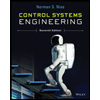
Control Systems Engineering
Mechanical Engineering
ISBN:
9781118170519
Author:
Norman S. Nise
Publisher:
WILEY
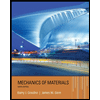
Mechanics of Materials (MindTap Course List)
Mechanical Engineering
ISBN:
9781337093347
Author:
Barry J. Goodno, James M. Gere
Publisher:
Cengage Learning
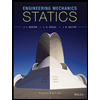
Engineering Mechanics: Statics
Mechanical Engineering
ISBN:
9781118807330
Author:
James L. Meriam, L. G. Kraige, J. N. Bolton
Publisher:
WILEY