Case Study 1The manufacturing plant of Caricarn Ltd. specializes in crafting specialized pieces for carnival.With a monthly production capacity of 15,000 pieces, the company currently manufactures andsells 11,000 pieces per month. Typically priced at $200 per piece, the company's costbreakdown for the ongoing production level is outlined below: Variable costs that vary with number of units produced Direct materials $ 440,000 Direct manufacturing labor 495,000 Variable costs (for setups, materials handling, quality control, etc.) that vary with number of batches, 220 batches * $500 per batch 110,000 Fixed Costs Fixed manufacturing costs 300,000 Fixed marketing costs 200,000Total costs $1,545,000Caricarn has just received a special one-time-only order for 4,000 pieces at $150 per piece.Accepting the special order would not affect the company’s regular business. Caricarn makespieces for its existing customers in batch sizes of 50 pieces (220 batches 50 pieces per batch =11,000 pieces). The special order requires Caricarn to make the pieces in 40 batches of 100each.Required1. Should Caricarn accept this special order? 2. Assume that plant capacity were only 13,000 pieces instead of 15,000 pieces each month. Thespecial order must either be taken in full or be rejected completely.Should Caricarn accept the special order? 3. As in requirement 1, assume that monthly capacity is 15,000 pieces. Caricarn is concernedthat if it accepts the special order, its existing customers will immediately demand a pricediscount of $20 in the month in which the special order is being filled. They would argue thatCaricarn’s capacity costs are now being spread over more units and that existing customersshould get the benefit of these lower costs.Should Caricarn accept the special order under these conditions? 4. By reference to the above data:a) Explain whether historical costs and future costs are relevant? b) Differentiate between quantitative and qualitative aspects in the process of decisionmaking?
Case Study 1
The manufacturing plant of Caricarn Ltd. specializes in crafting specialized pieces for carnival.
With a monthly production capacity of 15,000 pieces, the company currently manufactures and
sells 11,000 pieces per month. Typically priced at $200 per piece, the company's cost
breakdown for the ongoing production level is outlined below:
Variable costs that vary with number of units produced
Direct materials $ 440,000
Direct manufacturing labor 495,000
Variable costs (for setups, materials handling, quality control, etc.)
that vary with number of batches, 220 batches * $500 per batch 110,000
Fixed
Fixed manufacturing
Fixed marketing costs 200,000
Total costs $1,545,000
Caricarn has just received a special one-time-only order for 4,000 pieces at $150 per piece.
Accepting the special order would not affect the company’s regular business. Caricarn makes
pieces for its existing customers in batch sizes of 50 pieces (220 batches 50 pieces per batch =
11,000 pieces). The special order requires Caricarn to make the pieces in 40 batches of 100
each.
Required
1. Should Caricarn accept this special order?
2. Assume that plant capacity were only 13,000 pieces instead of 15,000 pieces each month. The
special order must either be taken in full or be rejected completely.
Should Caricarn accept the special order?
3. As in requirement 1, assume that monthly capacity is 15,000 pieces. Caricarn is concerned
that if it accepts the special order, its existing customers will immediately demand a price
discount of $20 in the month in which the special order is being filled. They would argue that
Caricarn’s capacity costs are now being spread over more units and that existing customers
should get the benefit of these lower costs.
Should Caricarn accept the special order under these conditions?
4. By reference to the above data:
a) Explain whether historical costs and future costs are relevant?
b) Differentiate between quantitative and qualitative aspects in the process of decisionmaking?

Step by step
Solved in 2 steps

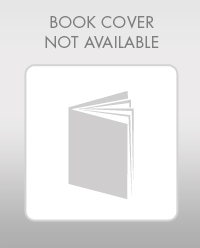
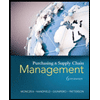
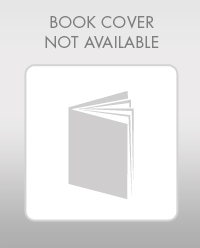
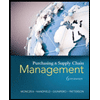
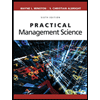