MECH 4013 Lab 1 Stress Shielding
pdf
keyboard_arrow_up
School
Carleton University *
*We aren’t endorsed by this school
Course
4013
Subject
Mechanical Engineering
Date
Jan 9, 2024
Type
Pages
10
Uploaded by SuperDanger388
MECH 4013 –
BIOMEDICAL DEVICE DESIGN Experiment 1
1 MECH 4013 –
BIOMEDICAL DEVICE DESIGN EXPERIMENT 1: Stress Shielding after Fracture Fixation (
Location: 7103 Canal building
) 1. Introduction The objectives of this laboratory exercise are to give students practical experience of how to treat bone fractures, evaluate a simple fracture fixation device and explore the effect of such devices on the load transfer in the bone. Fixation of fractured bone fragments involves a trade-off between rigid fixation and stress shielding. Fixation must be sufficiently rigid to allow the fracture to heal otherwise fibrous tissue forms, resulting in non-union or mal-union. However, the excessive rigidity of the fixation device causes shielding of the bone from physiological load after fracture healing has occurred, resulting in lower stresses in the bone and a localized decrease in bone density. Stress shielding can adversely affect long-term outcome and may result in implant loosening and re-fracture of the bone. In this experiment, the stress shielding effect of a fracture fixation plate is evaluated on a porcine femur. The porcine femur is loaded in a servo-hydraulic testing machine (MTS) with and without a fracture fixation plate. A transverse fracture is simulated by cutting the porcine femur with an oscillating saw. Three strain gauges glued to the femur will measure the longitudinal deformation close to the fracture and the plate. 2. Safety
•
Every student is required to bring a lab coat and safety goggles. •
While handling the biological tissue, the students are required to wear surgical gloves. •
Please advise the instructor beforehand if you are allergic to latex. •
You may use a scalpel to remove soft tissues from the cadaveric porcine bone. Use caution when using the scalpel. A special container is provided for disposal of scalpel blades after use. The scalpel blade is removed from the handle using pliers. •
While operating the drill press and the oscillating saw the students are required to wear the provided face shields. •
The servo-hydraulic testing machine will be operated by the teaching assistant (TA). •
Ref [1] contains information pertinent to the safe operation of this machine. 3. Materials •
Servo-hydraulic testing machine MTS (Canal Building Room 7103)
MECH 4013 –
BIOMEDICAL DEVICE DESIGN Experiment 1
2 •
Cadaveric porcine femur •
A custom designed fracture fixation plate appropriate for the porcine femurs. •
#8 wood screws will be used to fix the bone plate to the femur. •
The screw holes will be predrilled with a #29 drill bit •
Drill press •
Manual screwdriver to drive the screws into the bone. •
A permanent marker to mark the screw holes and the line that will be cut. •
An oscillating saw will be used to create the simulated a fracture. •
Three strain gauges, which will be glued to the femur; these will be provided with wires attached. •
Cyanoacrylate (crazy glue) •
Ruler •
Clear tape •
P-3500 Vishay bridge amplifier. •
Calipers •
Laser level •
Femur clamp fixture 4. Experimental Procedure 1.
Decide where on the femur the fixation device should be placed. Make sure you put the plate onto the side where you expect the greatest tensile stresses. Using the permanent marker, mark the position of the four screw holes and trace the edges of the fracture fixation plate. 2.
Using the permanent marker, mark the location of the simulated transverse fracture located midway between the inner two screw holes screws (i.e. middle of the plate). Mark the entire circumference of the femur. 3.
Check the distal end of the femur and the clamp fixture; some bone may need to be removed. Cut the distal end of the femur so that a flat surface will sit on the bottom of the clamp fixture and the femur will remain vertical. Do not remove too much bone from the distal end, otherwise the clamp fixture may interfere with the fixation plate. 4.
Using the drill press drill the screw holes through the full diameter of the diaphysis. Wear the face shield for your protection. 5.
Glue the strain gages just above the intended fracture line. One should be adjacent to the fixation plate, one opposite the plate, and a third midway between the other two strain gauges (i.e. the approximate neutral axis of the bone). Be sure to account for the possibility that screws may pierce the bone opposite the fixation device when placing your farthest strain gauge. Figure 1 shows a reasonable placement pattern. The gauges should be placed so that the wires are away from the fracture line. 5.
Thoroughly clean the areas where the strain gauges will go. Pick up a strain gauge with the tape, put cyanoacrylate on the part of the bone where the gauge is to be placed, and press the
MECH 4013 –
BIOMEDICAL DEVICE DESIGN Experiment 1
3 strain gauge down. Hold it until the cyanoacrylate dries, then carefully remove the tape. Repeat this procedure for the other two strain gauges. See Appendix A for more details. 6.
Place the femur into the clamp fixture and tighten the eight securing screws. Ensure that the metal buffer plates stay between the femur and the securing screws. Make sure you mark the alignment in case you have to remove the femur. 7.
Attach the strain gauges to the amplifier. 8.
Ensure that the cooling valve for the MTS is open, that the machinery is on and the emergency stop buttons are pulled out. Note all operation of the MTS machine will be performed by the TA but are noted here to document the procedure. 9.
At the computer terminal, open ft40 and use the manual command button to enable exclusive control. 10.
Zero the amplifier connected to the strain gauges by pressing the “balance”
button. 11.
Lower the actuator of the MTS machine so that it just touches the femoral head. Using the ruler measure and record the perpendicular distance from the point of contact to the neutral axis of the femoral diaphysis. 12.
Using the MTS program, load the porcine femur in increments of 0.2 kN up to a maximum of 1.2 kN. Record the applied force and the strain at each gauge for each load step. Repeat these measurements 3 times. Note the exact load applied can vary, but should be the same (within 10-20 N) for each test. 13.
Unload the femur and fix the fracture fixation plate to the femur without removing it from the clamp fixture. The screws should project through the opposite cortex. Be very careful not to disturb the strain gauges. This configuration simulates a healed fracture. 14.
Using the MTS program, load the porcine femur with the plate in increments of 0.2 kN up to a maximum of 1.2 kN. Record the applied force and the strain at each gauge for each load step. Repeat these measurements 3 times. 15.
Unload the femur and without removing the femur, using the oscillating saw cut the femur along the line you marked in step 2 all the way to the fixation device. This cut should be level with the centre of the fracture fixation device and slightly below the strain gauges. This configuration simulates the initial fracture fixation situation. 16.
Using the MTS program, load the porcine femur with the plate and simulated fracture in increments of 0.2 kN up to a maximum of 1.2 kN. Record the applied load and the strain at each gauge for each load. Repeat these measurements 3 times. Try to determine at which load the gap is closing. 17.
Unload the femur, ensure the MTS is immobile and remove your femur from the clamp fixture. Disconnect the wires from the amplifier. 18.
Remove the plate and measure the average outer and inner diameter of the bone at the fracture site and the width and height of the fracture fixation plate 19.
Clean all the instruments and fixation devices. Wipe down the MTS and the tables with soap.
Your preview ends here
Eager to read complete document? Join bartleby learn and gain access to the full version
- Access to all documents
- Unlimited textbook solutions
- 24/7 expert homework help
MECH 4013 –
BIOMEDICAL DEVICE DESIGN Experiment 1
4 5. Theory Bone plates serve two primary functions. They are intended to hold bone fragments in place while the bone heals and they carry some of the load the bone would otherwise have to carry alone. Although it is necessary for a fixation device to carry a large part of the load in the short term to allow healing, the bone plate will continue to carry a large part of the load after the bone has healed. From solid mechanics, we know that for two parallel elements subject to a load, the stiffer element will carry a greater portion of the load, and will thus be subjected to higher stress. In this case, bone is the less stiff element, and in the region of fixation the stresses are reduced compared to an intact bone with no fixation. Another possible cause of concern can occur soon after the bone plate is installed. A bone fracture can leave a gap between bone fragments. This gap opens and closes depending on the kind of load applied. This further complicates the shared-loading dynamic between the bone and the fixation device. Its effects will be exaggerated in this experiment by creating a large gap in the bone. Observing the effects of this change will help students understand how a gap between bone fragments would affect the load dynamics experienced by the plate and bone system. It is possible to make predictions about the stress experienced by a bone and plate system. Numerous simplifying assumptions must be made about the system to allow this. It is assumed Figure 1: Example of placement pattern of strain gauges. The clamp fixture is partially visible at the bottom.
MECH 4013 –
BIOMEDICAL DEVICE DESIGN Experiment 1
5 that the bone and plate act as a composite beam, and that both components exhibit elastic behaviour. The bone is modelled as an intact hollow cylinder rather than a fractured asymmetric body for simplicity. The plate can be assumed to have a square cross-section and is rigidly attached to the femur (Figure 2). Using composite beam theory, the stresses in the bone can be estimated using: for axial load for bending With the neutral axis located at: With:
MECH 4013 –
BIOMEDICAL DEVICE DESIGN Experiment 1
6 6. Analysis Calculate the average measured strain at the three locations and report the average and standard deviations for each load step and each condition (intact, healed, fracture). Using the averaged strain values calculate the stresses at these positions for all three scenarios, intact femur, femur with plate (healed condition) and simulated fracture (initial fixation condition). Using composite beam theory calculate the maximum strains and stresses at the measured locations for the intact femur and the femur with the plate (healed condition). Address the following questions in your discussion: 1.
What are the strains in the bone for the fracture condition? If this differs from the expected values, explain the possible cause(s). 2.
What is the percentage difference of your measured and calculated stresses? (Use the average values at the maximum load step). 3.
What are the sources of error? 4.
Determine the Young’s modulus that best fits your model. 5.
How does the closing of the gap affect your measurements? 6.
Where do the max. and min. stresses occur in the 3 different scenarios? 7.
What is the amount of stress shielding of the bone due to the plate? 8.
What is the stress in the plate? 9.
Estimate the max number of load cycles the plate could sustain without fracture. 10.
Based on your analysis where would you expect changes in the bone to occur? Figure 2: Simplified bone fracture plate model
Your preview ends here
Eager to read complete document? Join bartleby learn and gain access to the full version
- Access to all documents
- Unlimited textbook solutions
- 24/7 expert homework help
MECH 4013 –
BIOMEDICAL DEVICE DESIGN Experiment 1
7 7 References [1] Authors unknown, (2008) Series 370 Load Unit Product Information Manual Part Number 100-184-093 A, 100-184-093 B, MTS systems corporation, Minnesota
[2] D.L. Bartel, D.T. Davy and T.M. Keaveny (2006) Orthopaedic Biomechanics: Mechanics and Design in Musculoskeletal Systems. New Jersey: Pearson Prentice Hall.
MECH 4013 –
BIOMEDICAL DEVICE DESIGN Experiment 1
8 Appendix
Placing strain gauges 1. Remove all soft tissues and clean the bone thoroughly, especially around the fracture site and gauge locations. Any tissues or fluids will prevent adhesion of the gauges. 2. Place tape on top side of gauge.
MECH 4013 –
BIOMEDICAL DEVICE DESIGN Experiment 1
9 3. Place Cyanoacrylate on the bone where gauge will go. 4. Press gauge down firmly and hold thumb on gauge until cyanoacrylate has set.
Your preview ends here
Eager to read complete document? Join bartleby learn and gain access to the full version
- Access to all documents
- Unlimited textbook solutions
- 24/7 expert homework help
MECH 4013 –
BIOMEDICAL DEVICE DESIGN Experiment 1
10 5. Carefully peel tape off the gauge at an acute angle. 6. Secure the connections with more cyanoacrylate. Wires may be glued to the bone surface to limit any accidental forces that could pull gauges off bone.
Related Questions
need help with this review part A
engineering of materials
arrow_forward
Flag question
You have been given the following test sample data following mechanical testing of 15 test pieces of a modified Alumina.
What is the Weibull modulus of this material?
Would you advise the use of this material over one with a Weibull Modulus of 19.6 and a mean failure stress of 270 MPa, if you
anticipate that the peak stress on the material could be 255 MPa?
Sample
1
2
3
4
5
6
7
8
9
10
11
12
13
14
15
Select one or more:
Failure Stress (MPa)
297
293
270
300
260
286
265
295
4
293
280
288
263
290
298
275
arrow_forward
1. Which ASTM Testing Standards define the testing methodology for impact testing of:
a. Metallic Materials
b. Plastic Materials
2. Describe the difference between Ductile and Brittle Fracture in polycrystalline materials
arrow_forward
You are called as an expert witness to analyze the fracture of a sintered silicon carbide plate that was fractured in bending when a blunt load was applied to the plate center. Measurement of the distance between the fracture origin and the mirror/mist boundary on the fracture surface gives a radius of 0.796 mm. You are given three pieces of the same SiC to test, and you determine that the mirror radius is 0.603, 0.203, and 0.162 mm for bending failure stress levels of 225, 368, and 442 MPa, respectively. What is your estimate of the stress present at the time of fracture for the original plate?
arrow_forward
3. A structural component is made from a steel alloy with a plain strain fracture toughness
of 77.0 MPa √m and a yield strength of 1400 MPa. The dimensions of the component
allow it to be modeled as a wide plate. (a) If the design stress is half of the yield strength
and Y =1, determine the critical flaw size, a. (b) If the flaw size resolution limit of the flaw
detection equipment is 4mm, determine if a critical flaw can be detected. Consider both
an internal flaw and a surface flaw.
arrow_forward
QUESTION 18
A chemicals company is looking to optimise the materials selection for their synthesis vessel with safety being the key priority. The tank can be treated as a
small thin-walled spherical pressure vessel and the engineers are considering a 'yield before break' design concept.
Given that a crack of length will propagate by fast fracture when the stress intensity factor reaches the fracture toughness of the material select the correct
materials property index relevant to this design criterion.
Fracture toughness K₁=Y₁₁√√
IC
O M=
O M=
OM=
OM=
O M=
OM=
K
f
P
K 2
IC
K
IC
6
f
6
P
K
f
IC
σα
y
K
IC
2
f
IC
arrow_forward
QUESTION 18
A chemicals company is looking to optimise the materials selection for their synthesis vessel with safety being the key priority. The tank can be treated as a
small thin-walled spherical pressure vessel and the engineers are considering a 'yield before break' design concept.
Given that a crack of length will propagate by fast fracture when the stress intensity factor reaches the fracture toughness of the material select the correct
materials property index relevant to this design criterion.
Fracture toughness K₁=Y₁₁√√
IC
O M=
O M=
O M=
COM: =
O M=
O M=
K
6
6
P
K
IC
K
K
IC
P
σα
y
6
IC
K
IC
2
f
IC
2
arrow_forward
Stuck need help!
Problem is attached. please view attachment before answering.
Really struggling with this concept.
Please show all work so I can better understand !
Thank you so much.
arrow_forward
Question 4
Figure 3 shows the impact of temperature and stress on mechanical properties of
materials
(a) 1200
High temperature
or high stress
(b)
900
Medium temperature
or medium stress
Brittle
Ductile
Low temperature
or low stress
600
300
+Transition
temperature
-80
-40
40
80
Time
Temperature (°C)
Figure 3 (a) Izod impact test results for nylon thermoplastic polymer. (b) Creep
test results
Using Figure 3, explain:
(a) The dependence of failure modes on temperature.
(b) The effect of temperature changes and stress on the creep rate.
Impact strength (J/m)
Strain
arrow_forward
How does the field of mechanical engineering contribute to advancements in renewable energy technologies and sustainable solutions?
arrow_forward
Table 1: Mechanical behavior of human cadaver tibial bones
during pure torsional loads applied with the proximal tibia
fixed and the torque applied to the distal tibia until there is
bone fracture.
Medial condyle
Tibial tuberosity-
Medial malleolus
-Lateral condyle
Head of fibula
Ti-6Al-4V grade 5
Stainless Steel 316L
Region of bone
resection
-Lateral malleolus
L = 365 mm
Annealed
Annealed
Torque at ultimate failure (bone fracture)
Displacement (twist angle) at ultimate failure
Torsional Stiffness
Table 2: Mechanical properties of candidate materials for the rod.
Material
Process
Yield Strength
(MPa)
880
220-270
Do = 23 mm
Elastic
Modulus (GPa)
115
190
d₁ = 14 mm
Figure 1: Representative tibia bone showing the resection region (blue arrows) and median length (L). A circular cross section of distal tibia
taken at the level of resection) showing the median inner (di) and outer (Do) diameters of the cortical bone. A tibia bone after resection with the
proposed metal solid rod (black line)…
arrow_forward
Calculate the impacts on size (diameter) and mass/unit length of replacing a natural bone in the leg with one made of steel, aluminum, or titanium. Use compressive strengths and densities provided in class for bone, steel, and aluminum. Use r=0.00443 kg/cm3, and s=848 MPa for titanium. Assume the bone is hollow with outside diameter 2.5 cm and inside diameter 3 cm. Maintain the same inside diameter. HINT: first calculate the load on the bone..
arrow_forward
Please see attachments
arrow_forward
please can you assist me in answering the question i have added in the images. many thanks.
arrow_forward
You have been asked to draw up a specification for a ceramic cladding tile that is likely to experience tensile stresses
of 89 MPa during its installation and service lifetime.
If the ceramic has a specific surface energy of 0.35 J/m2 and its Youngs Modulus is 85 GPa what would be the
maximum length of an internal flaw that would not result in fracture of the tile?
(This question has only one correct answer)
a. 2.53 µm
b. 5.06 µm
c. 4.78 μm
d. 2.53 mm
e. 2.39 mm
f. 4.78 mm
g. 2.39 um
arrow_forward
Which of the following statements is incorrect for polymers?
(This question has only one correct answer)
а.
The fatigue behavior of polymers is more sensitive to loading frequency than for metals
Ob.
Amorphous and semi-crystalline polymers both have lower strength than crystalline polymers
О с.
Strength increases at higher temperatures as the material softens
O d.
It is desirable to have a ductile-to-brittle transition temperature below room temperature
arrow_forward
QUESTION 1
Select from the following statements, those which describe the process and conditions required for brittle fracture.
(Note: Partial credit is not available for this question. Credit will only be awarded if all correct answers, and no incorrect answers, are selected).
A. Occurs along defined crystallographic planes, thus leaving smooth fracture surfaces
B. Occurs due to repeated loading and unloading below the yield strength of the material
OC. Occurs in materials where the bonding strength is high relative to the yield strength
D. The stress concentration at the crack tip exceeds the inter-atomic bonding energy
☐ E. Involves the nucleation, growth and coalescence of voids, thus resulting in rough fracture surfaces
OF. Is a slow process whereby there is warning prior to failure
arrow_forward
A fracture surface of a metal matrix composite (nickel with silicon carbide
fibres) is investigated with a Scanning Electron Microscope (SEM).
Questions:
a. Which signals can you use to make an image of the sample?
b. Which signal do you prefer to observe the fracture surface?
c. How can you discriminate between the matrix and the fibres?
d. How can you increase the magnification to observe a detail with the
SEM?
arrow_forward
FRACTURE TOUGHNESS
arrow_forward
1. Glass and epoxy have stiffnesses of Eglass = 70 GPa and Eepoxy = 3.5 GPa and fracture toughness
values of Kic-glass = KIC-epoxy = 1 MPa√m.
a. Which has a higher toughness (GC)?
b. What might the broken surfaces look like after failure, and how does that relate to the energy
dissipated during fracture?
arrow_forward
SEE MORE QUESTIONS
Recommended textbooks for you
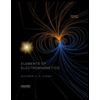
Elements Of Electromagnetics
Mechanical Engineering
ISBN:9780190698614
Author:Sadiku, Matthew N. O.
Publisher:Oxford University Press
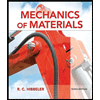
Mechanics of Materials (10th Edition)
Mechanical Engineering
ISBN:9780134319650
Author:Russell C. Hibbeler
Publisher:PEARSON
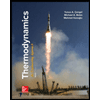
Thermodynamics: An Engineering Approach
Mechanical Engineering
ISBN:9781259822674
Author:Yunus A. Cengel Dr., Michael A. Boles
Publisher:McGraw-Hill Education
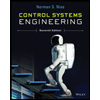
Control Systems Engineering
Mechanical Engineering
ISBN:9781118170519
Author:Norman S. Nise
Publisher:WILEY
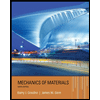
Mechanics of Materials (MindTap Course List)
Mechanical Engineering
ISBN:9781337093347
Author:Barry J. Goodno, James M. Gere
Publisher:Cengage Learning
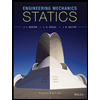
Engineering Mechanics: Statics
Mechanical Engineering
ISBN:9781118807330
Author:James L. Meriam, L. G. Kraige, J. N. Bolton
Publisher:WILEY
Related Questions
- need help with this review part A engineering of materialsarrow_forwardFlag question You have been given the following test sample data following mechanical testing of 15 test pieces of a modified Alumina. What is the Weibull modulus of this material? Would you advise the use of this material over one with a Weibull Modulus of 19.6 and a mean failure stress of 270 MPa, if you anticipate that the peak stress on the material could be 255 MPa? Sample 1 2 3 4 5 6 7 8 9 10 11 12 13 14 15 Select one or more: Failure Stress (MPa) 297 293 270 300 260 286 265 295 4 293 280 288 263 290 298 275arrow_forward1. Which ASTM Testing Standards define the testing methodology for impact testing of: a. Metallic Materials b. Plastic Materials 2. Describe the difference between Ductile and Brittle Fracture in polycrystalline materialsarrow_forward
- You are called as an expert witness to analyze the fracture of a sintered silicon carbide plate that was fractured in bending when a blunt load was applied to the plate center. Measurement of the distance between the fracture origin and the mirror/mist boundary on the fracture surface gives a radius of 0.796 mm. You are given three pieces of the same SiC to test, and you determine that the mirror radius is 0.603, 0.203, and 0.162 mm for bending failure stress levels of 225, 368, and 442 MPa, respectively. What is your estimate of the stress present at the time of fracture for the original plate?arrow_forward3. A structural component is made from a steel alloy with a plain strain fracture toughness of 77.0 MPa √m and a yield strength of 1400 MPa. The dimensions of the component allow it to be modeled as a wide plate. (a) If the design stress is half of the yield strength and Y =1, determine the critical flaw size, a. (b) If the flaw size resolution limit of the flaw detection equipment is 4mm, determine if a critical flaw can be detected. Consider both an internal flaw and a surface flaw.arrow_forwardQUESTION 18 A chemicals company is looking to optimise the materials selection for their synthesis vessel with safety being the key priority. The tank can be treated as a small thin-walled spherical pressure vessel and the engineers are considering a 'yield before break' design concept. Given that a crack of length will propagate by fast fracture when the stress intensity factor reaches the fracture toughness of the material select the correct materials property index relevant to this design criterion. Fracture toughness K₁=Y₁₁√√ IC O M= O M= OM= OM= O M= OM= K f P K 2 IC K IC 6 f 6 P K f IC σα y K IC 2 f ICarrow_forward
- QUESTION 18 A chemicals company is looking to optimise the materials selection for their synthesis vessel with safety being the key priority. The tank can be treated as a small thin-walled spherical pressure vessel and the engineers are considering a 'yield before break' design concept. Given that a crack of length will propagate by fast fracture when the stress intensity factor reaches the fracture toughness of the material select the correct materials property index relevant to this design criterion. Fracture toughness K₁=Y₁₁√√ IC O M= O M= O M= COM: = O M= O M= K 6 6 P K IC K K IC P σα y 6 IC K IC 2 f IC 2arrow_forwardStuck need help! Problem is attached. please view attachment before answering. Really struggling with this concept. Please show all work so I can better understand ! Thank you so much.arrow_forwardQuestion 4 Figure 3 shows the impact of temperature and stress on mechanical properties of materials (a) 1200 High temperature or high stress (b) 900 Medium temperature or medium stress Brittle Ductile Low temperature or low stress 600 300 +Transition temperature -80 -40 40 80 Time Temperature (°C) Figure 3 (a) Izod impact test results for nylon thermoplastic polymer. (b) Creep test results Using Figure 3, explain: (a) The dependence of failure modes on temperature. (b) The effect of temperature changes and stress on the creep rate. Impact strength (J/m) Strainarrow_forward
- How does the field of mechanical engineering contribute to advancements in renewable energy technologies and sustainable solutions?arrow_forwardTable 1: Mechanical behavior of human cadaver tibial bones during pure torsional loads applied with the proximal tibia fixed and the torque applied to the distal tibia until there is bone fracture. Medial condyle Tibial tuberosity- Medial malleolus -Lateral condyle Head of fibula Ti-6Al-4V grade 5 Stainless Steel 316L Region of bone resection -Lateral malleolus L = 365 mm Annealed Annealed Torque at ultimate failure (bone fracture) Displacement (twist angle) at ultimate failure Torsional Stiffness Table 2: Mechanical properties of candidate materials for the rod. Material Process Yield Strength (MPa) 880 220-270 Do = 23 mm Elastic Modulus (GPa) 115 190 d₁ = 14 mm Figure 1: Representative tibia bone showing the resection region (blue arrows) and median length (L). A circular cross section of distal tibia taken at the level of resection) showing the median inner (di) and outer (Do) diameters of the cortical bone. A tibia bone after resection with the proposed metal solid rod (black line)…arrow_forwardCalculate the impacts on size (diameter) and mass/unit length of replacing a natural bone in the leg with one made of steel, aluminum, or titanium. Use compressive strengths and densities provided in class for bone, steel, and aluminum. Use r=0.00443 kg/cm3, and s=848 MPa for titanium. Assume the bone is hollow with outside diameter 2.5 cm and inside diameter 3 cm. Maintain the same inside diameter. HINT: first calculate the load on the bone..arrow_forward
arrow_back_ios
SEE MORE QUESTIONS
arrow_forward_ios
Recommended textbooks for you
- Elements Of ElectromagneticsMechanical EngineeringISBN:9780190698614Author:Sadiku, Matthew N. O.Publisher:Oxford University PressMechanics of Materials (10th Edition)Mechanical EngineeringISBN:9780134319650Author:Russell C. HibbelerPublisher:PEARSONThermodynamics: An Engineering ApproachMechanical EngineeringISBN:9781259822674Author:Yunus A. Cengel Dr., Michael A. BolesPublisher:McGraw-Hill Education
- Control Systems EngineeringMechanical EngineeringISBN:9781118170519Author:Norman S. NisePublisher:WILEYMechanics of Materials (MindTap Course List)Mechanical EngineeringISBN:9781337093347Author:Barry J. Goodno, James M. GerePublisher:Cengage LearningEngineering Mechanics: StaticsMechanical EngineeringISBN:9781118807330Author:James L. Meriam, L. G. Kraige, J. N. BoltonPublisher:WILEY
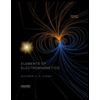
Elements Of Electromagnetics
Mechanical Engineering
ISBN:9780190698614
Author:Sadiku, Matthew N. O.
Publisher:Oxford University Press
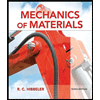
Mechanics of Materials (10th Edition)
Mechanical Engineering
ISBN:9780134319650
Author:Russell C. Hibbeler
Publisher:PEARSON
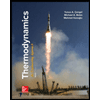
Thermodynamics: An Engineering Approach
Mechanical Engineering
ISBN:9781259822674
Author:Yunus A. Cengel Dr., Michael A. Boles
Publisher:McGraw-Hill Education
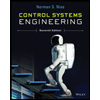
Control Systems Engineering
Mechanical Engineering
ISBN:9781118170519
Author:Norman S. Nise
Publisher:WILEY
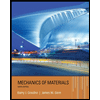
Mechanics of Materials (MindTap Course List)
Mechanical Engineering
ISBN:9781337093347
Author:Barry J. Goodno, James M. Gere
Publisher:Cengage Learning
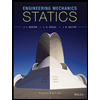
Engineering Mechanics: Statics
Mechanical Engineering
ISBN:9781118807330
Author:James L. Meriam, L. G. Kraige, J. N. Bolton
Publisher:WILEY