Lab 1 Tension Test
pdf
keyboard_arrow_up
School
Northeastern University *
*We aren’t endorsed by this school
Course
2355
Subject
Mechanical Engineering
Date
Jan 9, 2024
Type
Pages
10
Uploaded by extrahi4
ME 2356 Laboratory Template
1
Department of Mechanical and Industrial Engineering
ME 2356: Laboratory for Mechanics of Materials
Tension Testing
Submitted by
Sydney Rodriguez
Date Submitted:10/21/2023
Date Performed: 10/06/2023
Lab Section: 12
Lab TA: Lindsey Young
Course Instructor: Marguerite Matherne
ME 2356 Laboratory Template
2
1.
Introduction
The objective of this phase of the experiment is to gather data concerning the strength of the
supplied sample and to examine material of Steel’s attributes in depth.
2.
Methods and results
2.1
Instron
Procedure
In this experiment, an Instron 5582 apparatus is employed to assess compression and tension in a
given sample. The machine operates by applying force to the material, recording parameters such
as time, displacement, and force. Additionally, an extensometer is utilized, a compact device
attached to the sample to precisely calculate minor degrees of strain. Data from both these
sources are subsequently employed to generate graphs, thereby providing valuable insights into
the characteristics of the sample.
Results
Sample material and measurements table
Table 1. “Steel” sample.
Parameter
Initial value
Final value
Unit
Length
101.63
N/A
mm
Diameter
8.960
5.940
mm
Area
63.05
27.71
mm^2
Load vs. displacement plot
ME 2356 Laboratory Template
3
Stress vs. strain plot
Mechanical properties table
Table 2. “Steel” mechanical properties.
Parameter
Value
Unit
Young’s modulus
2.08e+09
N/m^2
Proportional limit
5.79e+08
Pa
Yield strength
1.73e+07
Pa
Ultimate strength
6.43e+08
Pa
True stress
1.14e+09
Pa
Reduction of area
45.9
%
Elastic energy density
7.19e+06
J/m^3
Discussion
6. On a stress-strain chart, the region beneath the curve at a specific point represents the strain
energy density necessary to subject the material to that point on the curve. As the modulus of
resilience encompasses the area under the curve until the yield point, it essentially signifies the
strain energy density needed to subject the material to its yield strength.
7. The calculated values closely approximate the reference values; however, it's crucial to
acknowledge potential sources of error in this experiment. Firstly, discrepancies may
inadvertently arise in the procedure and setup due to human error. Additionally, human error can
affect the values calculated, as the selection of data points may vary among individuals.
Nonetheless, in general, anyone conducting this experiment should achieve comparable results if
using the same material and procedure.
Your preview ends here
Eager to read complete document? Join bartleby learn and gain access to the full version
- Access to all documents
- Unlimited textbook solutions
- 24/7 expert homework help
ME 2356 Laboratory Template
4
2.2
Manual tester
Procedure
This phase of the experiment closely resembles the initial part, employing a tensile test.
However, in this case, the operation is manual rather than being performed with the Instron
machine. The sample is securely positioned in the apparatus, and the PASCOCapstone software
is configured to capture data as the user applies and removes the load from the sample.
Results
Sample material and measurements table
Table 3.
“Aluminum” sample.
Parameter
Initial value
Unit
Length
3.2
cm
Diameter
3.33
mm
Load vs. displacement plot
ME 2356 Laboratory Template
5
Stress vs. strain plot
Mechanical properties table
Table 4.
“Aluminum” mechanical properties.
Parameter
Value
Unit
Loading Young’s
modulus
1.29e+10
N/m^2
Reloading Young’s
modulus
1.30e+09
N/m^2
Yield strength
3.64e+07
Pa
Ultimate strength
1.89e+07
Pa
Discussion
4.
The values in this segment do not closely approximate the reference values, considering
there is a higher degree of error compared to the first part of the experiment. Naturally,
manual operation of the tensile test introduces some inconsistencies, leading to
irregularities in the graph. Similar errors in calculations might also manifest in this phase,
as in the first one. With repeated experiments by others they should experience different
results closer to the reference values online.
ME 2356 Laboratory Template
6
a.
Polariscope
Procedure
In the final stage of the experiment, two samples of the identical material but with distinct shapes
are employed. These samples are situated beneath a loading mechanism that can be adjusted to
augment the applied load. Additionally, a polarized light source and polarizer are incorporated,
enabling the user to visually assess the stress at various locations within the material and observe
disparities between the two samples.
Results
3 photos of the first sample
3 photos of the second sample
Your preview ends here
Eager to read complete document? Join bartleby learn and gain access to the full version
- Access to all documents
- Unlimited textbook solutions
- 24/7 expert homework help
ME 2356 Laboratory Template
7
Discussion
3.
In the second images of both samples, the regions experiencing the most significant stress
are highlighted. In the first sample, it's apparent that the point of contact with the load
and the immediate vicinity display the highest stress concentrations. Additionally, there
are observable stress wave patterns throughout the sample, a consequence of the
concentrated nature of the applied load. For the second sample featuring a hole, it's
evident that the areas surrounding the hole exhibit the highest stress levels. This is
attributed to the varying cross-sectional area at these specific locations, which differs
from the rest of the sample.
4.
The polariscope method offers numerous potential applications owing to its
straightforward approach to stress observation. For those seeking to assess relative stress
and make material comparisons without the need for precise data, this method proves
highly effective. A company engaged in product design can readily identify both the
strongest and weakest areas within the material by simply peering through the
polariscope, facilitating informed decisions on necessary reinforcements.
ME 2356 Laboratory Template
8
3.
Appendix:
Part 1:
%clear file
clearvars;
clc;
%read data
filename =
'Lab1_InstronData_Steel.csv'
;
T = readtable(filename);
%sample properties
di = 8.960e-3;
ri = di/2;
li = 101.63e-3;
df = 5.940e-3;
rf = df/2;
Af = pi*rf^2;
Ai = pi*ri^2;
%conversions
Force = T.Force*9.80665;
%Load in N
Displace = T.Displacement*10^-3;
%Extension in m
%stress and strain
Stress = Force/Ai;
Strain = Displace/li;
eStrain = T.Strain1;
%youngs modulus
F = polyfit(eStrain(5:100), Stress(5:100), 1);
E = F(1)
%yield strength
P = polyfit(Strain(20:170), Stress(20:170), 1);
oStress = P(1)*Strain(1:200);
oStrain = Strain(1:200)+0.002;
%Elastic energy density
U = 0.5*Stress(870)*Strain(870)
%ultimate strength
StrengthUlt = Stress(4050)
%true stress at failure
TrueStress = Force(5000)/Af
%proportional limit
PL = [Strain(1100), Stress(1100)];
%plot load vs displacement
figure(1)
ME 2356 Laboratory Template
9
plot(Displace*10^3, Force)
title(
'Load vs. displacement (steel)'
);
xlabel(
'Extension (mm)'
);
ylabel(
'Load (N)'
);
%plot stress vs strain
figure(2)
plot(Strain, Stress)
hold
on
plot(eStrain, Stress)
hold
on
plot(oStrain, oStress)
hold
on
plot(PL(1), PL(2),
'r*'
)
title(
'Stress vs Strain (steel)'
);
xlabel(
'Strain (-)'
);
ylabel(
'Stress (Pa)'
);
legend(
'Crosshead displacement strain'
,
'Extensometer strain'
,
'0.2%
Offset'
,
'Proportional limit'
,
'Location'
,
'southeast'
);
Part 2:
clearvars;
clc;
filename =
'lab 1 thur 03 (1).xlsx'
;
T = readtable(filename);
di = 3.33e-3;
ri = di/2;
li = 3.2e-2;
df = 6.35e-3;
rf = df/2;
Af = pi*rf^2;
Ai = pi*ri^2;
Force = T.Force_N_Run_2;
Displace = T.Position_m_Run_2;
Stress = Force/Ai;
Strain = Displace/li;
F = polyfit(Strain(15:300), Stress(15:300), 1);
E = F(1);
F2 = polyfit(Strain(581:640), Stress(581:640), 1);
E2 = F2(1);
P = polyfit(Strain(15:300), Stress(15:300), 1);
oStress = P(1)*Strain(1:425);
oStrain = Strain(1:425)+0.002;
StrengthUlt = Stress(431)
Your preview ends here
Eager to read complete document? Join bartleby learn and gain access to the full version
- Access to all documents
- Unlimited textbook solutions
- 24/7 expert homework help
ME 2356 Laboratory Template
10
figure(1)
plot(Displace, Force)
title(
'Load vs. displacement (Aluminum)'
);
xlabel(
'Extension (m)'
);
ylabel(
'Load (N)'
);
figure(2)
plot(Strain, Stress)
hold
on
plot(oStrain, oStress)
title(
'Stress vs. Strain'
);
Related Questions
Show work
Part 1 website: https://ophysics.com/r5.html
PArt 2 website: https://ophysics.com/r3.html
arrow_forward
Question 2
You are a biomedical engineer working for a small orthopaedic firm that fabricates rectangular shaped fracture
fixation plates from titanium alloy (model = "Ti Fix-It") materials. A recent clinical report documents some problems with the plates
implanted into fractured limbs. Specifically, some plates have become permanently bent while patients are in rehab and doing partial
weight bearing activities.
Your boss asks you to review the technical report that was generated by the previous test engineer (whose job you now have!) and used to
verify the design. The brief report states the following... "Ti Fix-It plates were manufactured from Ti-6Al-4V (grade 5) and machined into
solid 150 mm long beams with a 4 mm thick and 15 mm wide cross section. Each Ti Fix-It plate was loaded in equilibrium in a 4-point bending
test (set-up configuration is provided in drawing below), with an applied load of 1000N. The maximum stress in this set-up was less than the
yield stress for the…
arrow_forward
Help!!! Please answer all Correctly!!! Please
arrow_forward
dear tutor please provide neat and clean and detailed answer.
dont copy from google
adress both questions well
arrow_forward
Statics of Rigid Bodies (S1)
Note: I will report you if you answer this post multiple times so please follow it.Thank you for understanding, Tutor!
Content Covered:
- Analysis of Structures
Direction: Solve the problem below by giving the complete solution. In return, I will give you a good and high rating. Thank you so much!
Note: Be careful with the calculations in the problem. Kindly double check the solution and answer if there is a deficiency. And also, box the final answer. Thank you so much!
arrow_forward
Part 1: Suppose that our company performs DNA analysis for a law enforcement agency. We currently have 1 machine that are essential to performing the analysis. When an analysis is performed, the machine is in use for half of the day. Thus, each machine of this type can perform at most two DNA analyses per day. Based on past experience, the distribution of analyses needing to be performed on any given day are as follows: (Fill in the table)
Part2: We are considering purchasing a second machine. For each analysis that the machine is in use, we profit 1400$. What is the YEARLY expected value of this new machine ( ASSUME 365 days per year - no weekends or holidays
arrow_forward
Please give the detailed solution.
Don't use chatgpt for this question.
Thanks
arrow_forward
You are a biomedical engineer working for a small orthopaedic firm that fabricates rectangular shaped fracture
fixation plates from titanium alloy (model = "Ti Fix-It") materials. A recent clinical report documents some problems with the plates
implanted into fractured limbs. Specifically, some plates have become permanently bent while patients are in rehab and doing partial
weight bearing activities.
Your boss asks you to review the technical report that was generated by the previous test engineer (whose job you now have!) and used to
verify the design. The brief report states the following... "Ti Fix-It plates were manufactured from Ti-6Al-4V (grade 5) and machined into
solid 150 mm long beams with a 4 mm thick and 15 mm wide cross section. Each Ti Fix-It plate was loaded in equilibrium in a 4-point bending
test (set-up configuration is provided in drawing below), with an applied load of 1000N. The maximum stress in this set-up was less than the
yield stress for the Ti-6Al-4V…
arrow_forward
Please give a complete solution in Handwritten format.
Strictly don't use chatgpt,I need correct answer.
Engineering dynamics
arrow_forward
Subject : engineering design - DFMA
arrow_forward
Please give the detailed solution.
Don't use chatgpt for this question.
arrow_forward
Help!!! Please answer part b correctly like part A. Please!!!!
arrow_forward
Create a reading outline for the given text "STRESS and STRAIN".
arrow_forward
QUESTION 7
A model tow-tank test is conducted on a bare hull model at the model design
speed in calm water. Determine the effective horsepower (hp) for the ship,
including appendage and air resistances. The following parameters apply to the
ship and model:
Ship
1,100
Model
Length (ft)
Hull Wetted Surface Area (ft2)
Speed (knots)
30
250,000
15
Freshwater
Water
Seawater 50°F
70°F
Projected Transverse Area (ft²)
Cair
7,500
0.875
Appendage Resistance (% of bare hull)
10%
Hull Resistance (Ibf)
20
arrow_forward
Case Study
Determine Properties from Tensile Test Data
A cylindrical specimen of stainless steel having an initial diameter of 12.8mm and initial length
of 50.8mm is pulled in tension. Use the data provided below to
a) Plot the data as engineering stress versus engineering strain using excel or similar
software.
b) Compute the modulus of elasticity.
c) Determine the yield strength at a strain offset of 0.002.
d) Determine the tensile strength of this alloy.
e) What is the approximate ductility, in percent elongation?
f) Compute the modulus of resilience.
Load (N)
Length (mm)
50.800
12,700
25,400
38,100
50,800
76,200
50.825
50.851
50.876
50.902
50.952
89,100
92,700
51.003
51.054
102,500
107,800
119,400
128,300
149,700
159,000
160,400
159,500
151,500
124,700
51.181
51.308
51.562
51.816
52.832
53.848
54.356
54.864
55.880
56.642
Fracture
arrow_forward
Pls don’t use ai and fast :)
arrow_forward
Kindly do not re-submit your answers if you have solved the problems in this post. I post multiple questions of the same type to get an idea from other tutors. Thank you, Tutor! S.2
Statics of Rigid Bodies
Content Covered:
- Method of Sections
Direction: Create 1 problem based on the topic "Method of Sections" and then solve them with a complete solution. In return, I will give you a good rating. Thank you so much!
Note: Please bear in mind to create 1 problem based on the topic "Method of Sections." Be careful with the calculations in the problem. Kindly double check the solution and answer if there is a deficiency. And also, box the final answer. Thank you so much!
arrow_forward
Learning Goal:
To use fundamental geometric and statics methods to determine the state of plane stress at the point on an element of material that is rotated clockwise through an angle from the in-
plane stress representation of the point.
The state of in-plane stress at a point on an element of material is shown. Let o,
the same point that is rotated through an angle of 0-35
45.0 ksi, o, 19.0 ksi, and Ty 12.0 kai. Use this information to represent the state of stress of
arrow_forward
Help!!! Please answer part B correctly!!! Please
arrow_forward
Academic)
The following tensile data were collected from a standard 12.827 mm diameter test specimen of
copper alloy. The specimen was tested under tensile load until rupture.
After fracture, the sample length is 76.708 mm and the diameter is 9.5 mm.
Load (kN) Sample Length (mm)
50.8
13.4
50.842
26.7
50.897
33.4
50.957
40.0
51.0286
46.7
51.816
53.4
57.404
55.2
63.5
50.7
76.708
Calculate:
1. Ultimate Engineering Tensile strength:
2. Engineering stress at fracture:
3. True stress at fracture:
4. Percent elongation of the tested copper alloy specimen:
5. Percent reduction of area of the tested copper alloy specimen:
arrow_forward
Test Specimen
4140 CF steel
6061 T6 Al
Gray Cast iron 40
FC Brass 360
Impact Energy (J or ft-lb)
48.5 ft-lb
25 ft-lb
12 ft-lb
27 ft-lb
Impact Strength (J/m
or ft-lb/in)
123.096 ft-lb/in
63.452 ft-lb/in
What is the final analysis/ overall observation from the data?
30.457 ft-lb/in
68.528 ft-lb/in
arrow_forward
SEE MORE QUESTIONS
Recommended textbooks for you
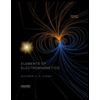
Elements Of Electromagnetics
Mechanical Engineering
ISBN:9780190698614
Author:Sadiku, Matthew N. O.
Publisher:Oxford University Press
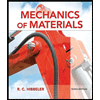
Mechanics of Materials (10th Edition)
Mechanical Engineering
ISBN:9780134319650
Author:Russell C. Hibbeler
Publisher:PEARSON
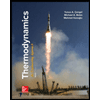
Thermodynamics: An Engineering Approach
Mechanical Engineering
ISBN:9781259822674
Author:Yunus A. Cengel Dr., Michael A. Boles
Publisher:McGraw-Hill Education
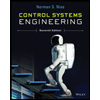
Control Systems Engineering
Mechanical Engineering
ISBN:9781118170519
Author:Norman S. Nise
Publisher:WILEY
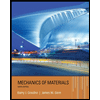
Mechanics of Materials (MindTap Course List)
Mechanical Engineering
ISBN:9781337093347
Author:Barry J. Goodno, James M. Gere
Publisher:Cengage Learning
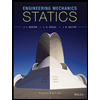
Engineering Mechanics: Statics
Mechanical Engineering
ISBN:9781118807330
Author:James L. Meriam, L. G. Kraige, J. N. Bolton
Publisher:WILEY
Related Questions
- Show work Part 1 website: https://ophysics.com/r5.html PArt 2 website: https://ophysics.com/r3.htmlarrow_forwardQuestion 2 You are a biomedical engineer working for a small orthopaedic firm that fabricates rectangular shaped fracture fixation plates from titanium alloy (model = "Ti Fix-It") materials. A recent clinical report documents some problems with the plates implanted into fractured limbs. Specifically, some plates have become permanently bent while patients are in rehab and doing partial weight bearing activities. Your boss asks you to review the technical report that was generated by the previous test engineer (whose job you now have!) and used to verify the design. The brief report states the following... "Ti Fix-It plates were manufactured from Ti-6Al-4V (grade 5) and machined into solid 150 mm long beams with a 4 mm thick and 15 mm wide cross section. Each Ti Fix-It plate was loaded in equilibrium in a 4-point bending test (set-up configuration is provided in drawing below), with an applied load of 1000N. The maximum stress in this set-up was less than the yield stress for the…arrow_forwardHelp!!! Please answer all Correctly!!! Pleasearrow_forward
- dear tutor please provide neat and clean and detailed answer. dont copy from google adress both questions wellarrow_forwardStatics of Rigid Bodies (S1) Note: I will report you if you answer this post multiple times so please follow it.Thank you for understanding, Tutor! Content Covered: - Analysis of Structures Direction: Solve the problem below by giving the complete solution. In return, I will give you a good and high rating. Thank you so much! Note: Be careful with the calculations in the problem. Kindly double check the solution and answer if there is a deficiency. And also, box the final answer. Thank you so much!arrow_forwardPart 1: Suppose that our company performs DNA analysis for a law enforcement agency. We currently have 1 machine that are essential to performing the analysis. When an analysis is performed, the machine is in use for half of the day. Thus, each machine of this type can perform at most two DNA analyses per day. Based on past experience, the distribution of analyses needing to be performed on any given day are as follows: (Fill in the table) Part2: We are considering purchasing a second machine. For each analysis that the machine is in use, we profit 1400$. What is the YEARLY expected value of this new machine ( ASSUME 365 days per year - no weekends or holidaysarrow_forward
- Please give the detailed solution. Don't use chatgpt for this question. Thanksarrow_forwardYou are a biomedical engineer working for a small orthopaedic firm that fabricates rectangular shaped fracture fixation plates from titanium alloy (model = "Ti Fix-It") materials. A recent clinical report documents some problems with the plates implanted into fractured limbs. Specifically, some plates have become permanently bent while patients are in rehab and doing partial weight bearing activities. Your boss asks you to review the technical report that was generated by the previous test engineer (whose job you now have!) and used to verify the design. The brief report states the following... "Ti Fix-It plates were manufactured from Ti-6Al-4V (grade 5) and machined into solid 150 mm long beams with a 4 mm thick and 15 mm wide cross section. Each Ti Fix-It plate was loaded in equilibrium in a 4-point bending test (set-up configuration is provided in drawing below), with an applied load of 1000N. The maximum stress in this set-up was less than the yield stress for the Ti-6Al-4V…arrow_forwardPlease give a complete solution in Handwritten format. Strictly don't use chatgpt,I need correct answer. Engineering dynamicsarrow_forward
arrow_back_ios
SEE MORE QUESTIONS
arrow_forward_ios
Recommended textbooks for you
- Elements Of ElectromagneticsMechanical EngineeringISBN:9780190698614Author:Sadiku, Matthew N. O.Publisher:Oxford University PressMechanics of Materials (10th Edition)Mechanical EngineeringISBN:9780134319650Author:Russell C. HibbelerPublisher:PEARSONThermodynamics: An Engineering ApproachMechanical EngineeringISBN:9781259822674Author:Yunus A. Cengel Dr., Michael A. BolesPublisher:McGraw-Hill Education
- Control Systems EngineeringMechanical EngineeringISBN:9781118170519Author:Norman S. NisePublisher:WILEYMechanics of Materials (MindTap Course List)Mechanical EngineeringISBN:9781337093347Author:Barry J. Goodno, James M. GerePublisher:Cengage LearningEngineering Mechanics: StaticsMechanical EngineeringISBN:9781118807330Author:James L. Meriam, L. G. Kraige, J. N. BoltonPublisher:WILEY
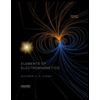
Elements Of Electromagnetics
Mechanical Engineering
ISBN:9780190698614
Author:Sadiku, Matthew N. O.
Publisher:Oxford University Press
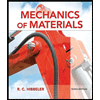
Mechanics of Materials (10th Edition)
Mechanical Engineering
ISBN:9780134319650
Author:Russell C. Hibbeler
Publisher:PEARSON
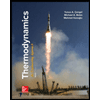
Thermodynamics: An Engineering Approach
Mechanical Engineering
ISBN:9781259822674
Author:Yunus A. Cengel Dr., Michael A. Boles
Publisher:McGraw-Hill Education
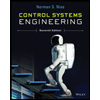
Control Systems Engineering
Mechanical Engineering
ISBN:9781118170519
Author:Norman S. Nise
Publisher:WILEY
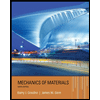
Mechanics of Materials (MindTap Course List)
Mechanical Engineering
ISBN:9781337093347
Author:Barry J. Goodno, James M. Gere
Publisher:Cengage Learning
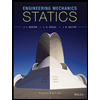
Engineering Mechanics: Statics
Mechanical Engineering
ISBN:9781118807330
Author:James L. Meriam, L. G. Kraige, J. N. Bolton
Publisher:WILEY