MAAE2202_Lab C
docx
keyboard_arrow_up
School
Carleton University *
*We aren’t endorsed by this school
Course
2202
Subject
Mechanical Engineering
Date
Jan 9, 2024
Type
docx
Pages
10
Uploaded by LieutenantMetal13000
Carleton University
Laboratory Report
Course #: MAAE2202A-L3
Lab #: C
Lab Section #:
Torsion of a Hollow Circular Shaft
Summary
The purpose of this lab is to obtain the torsional stiffness of a hollow circular shaft as well as the shear
modulus of the shaft material. Another objective of this lab is to verify the simple torsion formula for
shear stresses in circular shafts. These goals were accomplished using the torsion of a hollow circular
shaft apparatus, with 3 separate trials to ensure accurate results.
Nomenclature
Table 1:
Nomenclature Used in Report
Symbol
Parameter
Unit
T
Applied Torque
Nm
J
Second Moment of Area
m
4
τ
Shear Stress
kPa
D
Beam Diameter
mm
R
Beam Radius
mm
G
Shear Modulus
GPa
θ
Angle of Deflection
rad
L
Beam Length
mm
k
Torsional Stiffness
Nm/rad
F
Force
N
m
Mass
kg
g
Gravitational Acceleration
m/s
2
d
Arm Length
mm
t
Beam Wall Thickness
mm
W
Weight
kg
´
X
Mean/Average
Depends on subject
%error
Error Percentage
%
Theory and Analysis
In this experiment, we aim to find torsional stiffness and shear modulus of the beam. To accomplish this,
multiple steps are required. Since the torque in the beam is being applied by the weights attached to the
loading bar, the applied load from the weights must be converted to an applied torque:
T
=
mg d
load
Equation 1
The torque from the weights cause the beam to twist a certain amount, which is measured using the
deflection arm’s gauge. The deflection arm is initially parallel with the ground. The angle of deflection is
the angle of the deflection arm relative to the initial angle and can be calculated using Pythagoras ratios:
θ
=
tan
−
1
(
verticaldeflection
d
deflection
)
Equation 2
P a g e 2 | 10
The torsional stiffness of the shaft is the rate of change of applied torque with respect the angle of
deflection. It can be found by using the slope of a
T vsθ
graph, and is represented by the equation:
k
=
∆T
∆θ
Equation 3
The torsional stiffness will be used to calculate the shear modulus; however, the second moment of area
must be calculated first. By using the dimensions of the beam, the second moment of area can be found:
J
=
π
2
R
4
=
π
2
(
R
out
4
−
R
¿
4
)
Equation 4
The shear modulus can now be found using the length, tortional stiffness, and second moment of area of
the shaft. It is an intrinsic property of a material and can be calculated using the equation:
G
=
∆T
∆θ
∙
L
J
=
k ∙
L
J
Equation 5
As the shear modulus of a material is an intrinsic property, the experimental value can be compared to
published values and a percentage of error can be obtained. In this experiment, the mean of the 3 trials
was used to compare to the published value. The error percentage is represented by the equation:
%error
=
(
G
´
X
−
G
pub
G
pub
)
×
100%
Equation 6
This experiment was performed under pure shear conditions. This allowed the experimental shear stress
to be calculated using only the measured shear strain in the 45
̊
plane. In these conditions, the shear
strain in the circumferential plane is equal to 2 times the shear strain in the 45
̊
plane. This, as well as the
shear modulus is used to calculate the experimental shear stress:
τ
exp
=
G∙
(
2
×gauge
2
reading
)
Equation 7
The shear stress can be calculated in another, more theoretical way. The theoretical shear stress uses
intrinsic properties of the shaft as well as the applied torque.
τ
theo
=
T ∙
R
out
J
Equation 8
P a g e 3 | 10
Your preview ends here
Eager to read complete document? Join bartleby learn and gain access to the full version
- Access to all documents
- Unlimited textbook solutions
- 24/7 expert homework help
Experimental Setup and Procedure
Figure 1:
Experiment apparatus with labeled components
Figure 2:
Set-up for vertical deflection measurements
The experiment was conducted as outlined in the lab manual.
Results and Discussion
Requirement A
One of the steps in the procedure was to adjust the shackle to ensure the vertical deflection at the tip of
the beam was zero for each applied load. This was done to prevent the beam from bending and twisting
as it would have affected the readings for the deflection arm, and all gauges. If this was not done,
separate calculations for the curvature of the beam would have been required to achieve the same
result with more inaccuracies. By zeroing the vertical deflection of the beam, it ensured that most of the
deformation was in the torsional direction.
The strains in the circumferential and longitudinal strain
gauges were also zeroed to maximize accuracy of the strain gauge in the 45
̊
plane (gauge 2). This is
important as it is the only strain used to calculate the shear stress in pure shear conditions (this
experiment).
P a g e 4 | 10
Requirement B
The applied torques for each trial were calculated using equation 1. The twisting angles for each trial
were calculated using equation 2. The calculated results were tabulated in appendix c and plotted on a
graph shown in
Figure 3
. The torsional stiffness can be seen as the slope of each trial’s relation.
Figure 3:
Applied Torque versus Twisting Angle for Trials 1, 2, and 3
The second moment of area was calculated using equation 4 with the given dimensions of the shaft. The
shear modulus was calculated using equation 5 for each trial with the torsional stiffness and the second
moment of area. The results for torsional stiffness and shear modulus were tabulated in
Table 2
.
Table 2:
Calculated Torsional Stiffness and Shear Modulus for Each Trial
Torsional Stiffness,
k
(Nm/rad)
Shear Modulus,
G
(GPa)
Trial 1
10484
29.45
Trial 2
10575
29.71
Trial 3
11029
30.98
Requirement C
The mean shear modulus across the 3 trials was calculated to be 30.0 GPa. When comparing this to the
published value of 28 GPa, an error percentage of 7.3% was obtained using equation 6. There are several
reasons for an error percentage of this magnitude. To start, the clearest source of error in this
experiment was the jumpiness of the vertical deflection gauge dials. This provided early inaccuracies in
the calculations for torsional stiffness and subsequently shear modulus. The deflection gauges also could
have been improperly zeroed at the start of each trial, which would affect the results as well.
P a g e 5 | 10
Requirement D
The experimental stresses for trial 1 were calculated using equation 7. The shear strains on the 45
̊
plane
were used from the gauge 2 readings as well as the calculated shear modulus for trial 1. The theoretical
stresses were calculated using equation 8 with the applied torques for trial 1. The calculated results for
the stresses were catalogued in appendix c and plotted on the graph in
Figure 4
.
Figure 4:
Theoretical and Experimental Stresses vs Applied Torque for Trial 1
As seen in the graph, the theoretical and experimental stresses vary from each other. The experimental
stresses could have a few sources of error, one being the strain gauges attached to the shaft. As observed
in the previous lab, strain gauges are extremely sensitive parts, and the slightest discrepancies can affect
the results. The gauges could have also been put on imperfectly, which would result in them accounting
for strains in unintentional directions. The readings for longitudinal and hoop strain were not always
zero, which is an indication that the experiment could have not been under pure shear conditions, and
perhaps there were deformations in other directions than the torsional. This would affect the shear
strain in the 45
̊
plane and subsequently the experimental shear stresses.
Conclusion
Through the use of the Torsion of a Hollow Circular Shaft apparatus, the torsional stiffness of the beam
was calculated to be between 10.4 and 11.1 kN*m/rad from 3 trials. The average shear modulus across
the trials was found to be 30.0 GPa, which had an error percentage of 7.3%. This is accurate enough to
call the experiment successful in that regard. The experiment was also a success in gaining experience
with torsion, stiffness, shear modulus, and shear stress.
P a g e 6 | 10
Your preview ends here
Eager to read complete document? Join bartleby learn and gain access to the full version
- Access to all documents
- Unlimited textbook solutions
- 24/7 expert homework help
References
MAAE 2202 - Lab Manual pages 20-25 (MAAE 2202A/B Brightspace course page, Administration tab)
Appendices
Appendix A: Lab Data
Beam Information
Beam Length,
L
(mm)
Deflection Arm Length
d
deflection
,
(mm)
Beam Outer Diameter
R
out
,
(mm)
Beam Wall Thickness
t,
(mm)
760
180
50.8
3.175
Trial 1: 140 mm from centre
Weight
(kg)
Gauge 1
(microstrain)
Gauge 2
(microstrain)
Gauge 3
(microstrain)
Vertical Deflection
(mm)
4.597
-2
-11
0
0.1143
9.171
-5
-23
2
0.2286
13.766
-6
-33
2
0.3048
18.368
-6
-44
2
0.4064
22.931
-9
-57
3
0.5588
Trial 2: 118 mm from centre
Weight
(kg)
Gauge 1
(microstrain)
Gauge 2
(microstrain)
Gauge 3
(microstrain)
Vertical Deflection
(mm)
4.597
-2
-10
1
0.0381
9.171
-5
-21
2
0.1397
13.766
-4
-28
1
0.2286
18.368
-7
-39
3
0.3048
22.931
-8
-49
3
0.4064
Trial 3: 80 mm from centre
Weight
(kg)
Gauge 1
(microstrain)
Gauge 2
(microstrain)
Gauge 3
(microstrain)
Vertical Deflection
(mm)
4.597
-2
-8
0
0.0762
9.171
-4
-15
1
0.127
13.766
-5
-21
1
0.1778
18.368
-6
-29
2
0.254
22.931
-8
-35
2
0.3048
Appendix B: Sample Calculations for Trial 1, Weight 1
Sample calculation for applied torque from weights using equation 1
P a g e 7 | 10
T
=
mg d
load
T
=
(
4.597
kg
)
(
9.81
m
s
2
)
(
140
×
10
−
3
m
)
T
=
6.314
N ∙m
Sample calculation for angle of deflection using equation 2
θ
=
tan
−
1
(
verticaldeflection
d
deflection
)
θ
=
tan
−
1
(
0.1143
mm
180
mm
)
θ
=
0.000635
rad
Sample calculation for torsional stiffness using equation 3 (unused value)
k
=
∆T
∆θ
k
=
25.18
N ∙m
0.002469
rad
k
=
10196.63
N ∙m
rad
Sample calculation for second moment of area using equation 4
J
=
π
2
R
4
=
π
2
(
R
out
4
−
R
¿
4
)
J
=
π
2
(
(
50.8
2
×
10
−
3
m
)
4
−
(
(
50.8
2
−
3.175
)
×
10
−
3
m
)
4
)
J
=
2.7056
×
10
−
7
m
4
Sample calculation for shear modulus using equation 5
G
=
∆T
∆θ
∙
L
J
=
k ∙
L
J
G
=
(
10484
N ∙m
rad
)
∙
(
760
×
10
−
3
m
2.7056
×
10
−
7
m
4
)
G
=
2.945
×
10
10
Pa
=
29.45
GPa
P a g e 8 | 10
Sample calculation for mean shear modulus
G
´
X
=
1
n
∑
i
=
1
n
G
i
G
´
X
=
1
3
(
29.45
GPa
+
29.71
GPa
+
30.98
GPa
)
G
´
X
=
30.0
GPa
Sample calculation for error percentage using equation 6
%error
=
(
G
´
X
−
G
pub
G
pub
)
×
100%
%error
=
(
30
GPa
−
28
GPa
28
GPa
)
×
100%
%error
=
7.3%
Sample calculation for experimental shear stress using equation 7
τ
exp
=
G∙
(
2
×gauge
2
reading
)
τ
exp
=
(
2.945
×
10
10
Pa
)
∙
(
2
×
11
×
10
−
6
)
τ
exp
=
647888
Pa
=
647.888
kPa
Sample calculation for theoretical shear stress using equation 8
τ
theo
=
T ∙
R
out
J
τ
theo
=
(
6.314
N ∙m
)
∙
(
50.8
2
×
10
−
3
m
2.7056
×
10
−
7
m
4
)
τ
theo
=
592709
Pa
=
592.709
kPa
P a g e 9 | 10
Your preview ends here
Eager to read complete document? Join bartleby learn and gain access to the full version
- Access to all documents
- Unlimited textbook solutions
- 24/7 expert homework help
Appendix C: Tables of Calculated Results
Table #:
ads
Applied Torque,
T
(Nm)
Weight
Trial 1
Trial 2
Trial 3
1
6.31352
5.321395
3.607726
2
12.59545
10.61617
7.197401
3
18.90622
15.93525
10.80356
4
25.22661
21.26243
14.41521
5
31.49344
26.54447
17.99625
Table #:
ads
Angle of Deflection,
θ
(Nm)
Weight
Trial 1
Trial 2
Trial 3
1
0.000635
0.000212
0.000423
2
0.00127
0.000776
0.000706
3
0.001693
0.00127
0.000988
4
0.002258
0.001693
0.001411
5
0.003104
0.002258
0.001693
Table #:
ads
Torsional Stiffness,
k
(Nm/rad)
Shear Modulus,
G
(GPa)
Trial 1
10484
29.45
Trial 2
10575
29.71
Trial 3
11029
30.98
Table #:
Experimental and Theoretical Shear Stresses for Trial 1
Applied Torque,
T
(Nm)
Experimental Stress,
τ
exp
(kPa)
Theoretical Stress,
τ
theo
(kPa)
6.31352
647.8876
592.7092065
12.59545
1354.674
1182.452933
18.90622
1943.663
1774.904272
25.22661
2591.551
2368.258148
31.49344
3357.236
2956.583601
P a g e 10 | 10
Related Questions
HEAT TRANSFER
CASE: I want to know what temperature in (°F) the cylinder will have inside. It's a heat transfer problem.
what is T2 ?
HEAT TRANSFER
They gave me an answer all squashed together that i can't make sense of it. If you could help me makes sense of it thank you!
arrow_forward
I need assistance designing three structural models on Fusion 360 (bamboo-inspired, bone-inspired, and a control cylinder) for a mechanics project. These models will be tested under compression to compare their load-bearing capacity, energy absorption, and failure modes. Here are the specific details and requirements for each design:
General Requirements:
External Dimensions:
All models must have the same outer dimensions: height = 15 cm, diameter = 5 cm.
Material Volume:
Ensure each design uses approximately the same material volume (e.g., relative density = 30% of the total volume). If you have any other ideas on how to ensure the test is fair between all 3 samples please note it!
File Format:
Provide the designs as STL files compatible with 3D printing or a step-by-step process.
Design Specifications:
1. Control Cylinder:
A simple hollow cylinder with:
Wall Thickness: 2 mm.
Inner Diameter: 4.6 cm (to maintain the outer diameter and wall thickness).
No additional…
arrow_forward
i want a displacement and stress equations and mak calculation
arrow_forward
Please use ANSYS SOFTWARE
arrow_forward
Need help with this engineering of materials
arrow_forward
I need only MATLAB coding please.....
arrow_forward
The purpose of this problem is to
show the relationship between material constants typically used in engineering practice. This
is useful because you may often have access to measurements of or tabulated values of some
constants (e.g., Young's modulus and Poisson's ratio) but need another constant (e.g., shear
modulus) for a calculation. Use the expression Cijkl = µ(dildjk + dikdjl) + Ad¿jdkl to derive
the following:
(a) Young's modulus, E = µ(3X+2µ)/(X+μ), from the definition 11 = Ee11 in a unconfined
(022 = 0,033 = 0) uniaxial tension test.
(b) Poisson's ratio, v = \/(2(X + μ)), from the definition v = €22/11 in the same test as
in (a).
(c) Shear modulus, μ = G = 012/(2€12) = E/(2(1 + v)).
Use the results to show that C can also be written Cijkl
Ev/((1+v)(1 − 2v))dij§kl.
=
E/(2(1 + v))(duðjk + dikdjl) +
arrow_forward
E and 5 v X
O file:///C:/Users/Hp/Desktop/mm/OUTCOME%20NO.2%20and%205%20with%20Problems.pdf
+
O Fit to page
D Page view
A Read aloud
1 Add notes
Problems
1. A brass rod of diameter 25 mm and length 250 mm is
subjected to a tensile load of 50 kN and the extension of
the rod is equal to 0.3 mm. Find the Young's Modulus or
Modulus of Elasticity.
99+
to search
hp
delete
prt sc
14 DI
backs
&
7
8
24
4
P
EJR
-0
J
K
H
D.
F
arrow_forward
1- what materials are included here (z parameter), type of materials considered, property or properties plotted, domain of c, parameter identified
2- what are the vertical and horizontal trends presented
3-what is the take away story from this plot
please answer i will upvote
arrow_forward
Calculate the stiffness matrix for the Q8 element shown below. Make use of the shape functions in natural coordinates and the Jacobian calculated in previous problems. Use 2x2 Gaussian numerical integration. Use plane strain conditions (for unit thickness) with E=200E9 (MPa) and nu=0.25.
I have attached my matlab code below. Please look thru it and correct it. Thanks.
u=sym('u') %%ztav=sym('v') %%eta
x1=1x2=2x3=3.5x4=3.6x5=4.0x6=2.3x7=1.2x8=0.8
y1=1y2=1y3=1.3y4=2.3y5=3.3y6=3.2y7=3.0y8=2.0X=[x1;x2;x3;x4;x5;x6;x7;x8]Y=[y1;y2;y3;y4;y5;y6;y7;y8]%% diff of ztaDN1Du=1/4*(1-v)*(2*u+v);DN2Du=-u*(1-v);DN3Du=1/4*(1-v)*(2*u-v);DN4Du=1/2*(1-v^2);DN5Du=1/4*(1+v)*(2*u+v);DN6Du=-u*(1+v);DN7Du=1/4*(1+v)*(2*u-v);DN8Du=-1/2*(1-v^2);
%% diff of etaDN1Dv=1/4*(1-u)*(2*v+u);DN2Dv=-1/2*(1-u^2);DN3Dv=1/4*(1+u)*(2*v-u);DN4Dv=-v*(1+u);DN5Dv=1/4*(1+u)*(2*v+u);DN6Dv=1/2*(1-u^2);DN7Dv=1/4*(1-u)*(2*v+u);DN8Dv=-v*(1-u);%% find dx/du dx/dv, dy/du and dy/dva=[DN1Du, DN2Du, DN3Du, DN4Du, DN5Du, DN6Du,DN7Du,…
arrow_forward
Unlike the tensile effort, which tends to straighten the parts, the compression effort tends to accentuate the effect of the initial curvature. The lateral displacements produced make up the flexural buckling process. The buckling of the part tends to reduce its load capacity.Source: Neto, J. G. R. Class notes - Metallic Structures: Compressed parts. DEC/PUC. Available at: https://professor.pucgoias.edu.br/SiteDocente/admin/arquivosUpload/17448/material/5%20-%20PECAS%20COMPRIMIDAS.pdf. Accessed on: 05/10/2024.
Checking the safety of compressed parts varies depending on the slenderness of the part. A column with a circular section and buckling length equal to 320 cm is classified as moderately slender. Knowing that it receives a centered force of 480kN, carry out the necessary calculations and select the alternative that presents the requirements associated with its correct dimensioning. AlternativesAlternative 1:A simple compression generated by the load 480.0 kN.
Alternative 2:A…
arrow_forward
Calculate the stiffness matrix for the Q8 element shown below. Make use of the shape functions in natural coordinates and the Jacobian calculated in previous problems. Use 2x2 Gaussian numerical integration. Use plane strain conditions (for unit thickness) with E=200E9 (MPa) and nu=0.25.
The final answers is F1= 0.18452e12. I have attached my matlab code below. Please look thru it and correct it. Thanks.
u=sym('u') %%ztav=sym('v') %%eta
x1=1x2=2x3=3.5x4=3.6x5=4.0x6=2.3x7=1.2x8=0.8
y1=1y2=1y3=1.3y4=2.3y5=3.3y6=3.2y7=3.0y8=2.0X=[x1;x2;x3;x4;x5;x6;x7;x8]Y=[y1;y2;y3;y4;y5;y6;y7;y8]%% diff of ztaDN1Du=1/4*(1-v)*(2*u+v);DN2Du=-u*(1-v);DN3Du=1/4*(1-v)*(2*u-v);DN4Du=1/2*(1-v^2);DN5Du=1/4*(1+v)*(2*u+v);DN6Du=-u*(1+v);DN7Du=1/4*(1+v)*(2*u-v);DN8Du=-1/2*(1-v^2);
%% diff of etaDN1Dv=1/4*(1-u)*(2*v+u);DN2Dv=-1/2*(1-u^2);DN3Dv=1/4*(1+u)*(2*v-u);DN4Dv=-v*(1+u);DN5Dv=1/4*(1+u)*(2*v+u);DN6Dv=1/2*(1-u^2);DN7Dv=1/4*(1-u)*(2*v+u);DN8Dv=-v*(1-u);%% find dx/du dx/dv, dy/du and dy/dva=[DN1Du, DN2Du, DN3Du,…
arrow_forward
Using the four-point bending tool, discuss how measurements of transverse
strain using DIC and compare with those from the strain gauge attached at
the centre top of the specimen. In your answer, include the following:
a. A short explanation of how each of the strain measurement techniques
works.
(4 marks)
b. A description of the methodology you have used to make the data that
you discussed from each technique as comparable as possible.
(6 marks)
c. A set of figures (images, graphs and/or tables as necessary) with
appropriate captions demonstrating the comparability of data extracted
from the two strain measurement methods. This should include at least
three different applied loads.
(10 marks)
d. A brief description of the findings.
(5 marks)
arrow_forward
Please show all work
arrow_forward
Which of these statements are correct?
arrow_forward
7. A steel connecting rod is subjected to a completely reversed axial load of 160 kN. Suggest the suitable
diameter of the rod using a factor of safety 2. The ultimate tensile strength of the material is 1100
MPa, and yield strength 930 MPa. Neglect column action and the effect of stress concentration.
[Ans. 30.4 mm]
arrow_forward
For the stress-strain curves below, which statements are correct?
Stress (MPa)
60
50
40
30
20
10
0
0
A
B
C.
1 2 3 4
Strain
5 6
7 8
a.
The mechanical behavior shown in C is that of an elastomer with low elastic modulus
b. While the deformation in polymer A is fully reversible until breakage, polymer B and C only display
reversible deformation until 0.1X and 5x elongations respectively
The mechanical behavior shown in B is that of an elastomer with low elasticity
d.
Polymer B and C have an elastic behavior whereas A has a plastic behavior
e. The polymer with the necking behavior has the highest strength
Of. The polymer with brittle nature is the one that possesses the highest elastic modulus
arrow_forward
Chapter 12 - Lecture Notes.pptx: (MAE 272-01) (SP25) DY...
Scores
arrow_forward
Mild steel 1
Young;s modulus 1219.5
Yield strain and stress (0.4101,500.08)
Failure stress and strain :not able to find because the given data shows the experiment did not reach the failure point.
if the material stress and strain does not reach a failure point ,what dose it means , does it means that the material is more stronger?
arrow_forward
SEE MORE QUESTIONS
Recommended textbooks for you
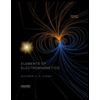
Elements Of Electromagnetics
Mechanical Engineering
ISBN:9780190698614
Author:Sadiku, Matthew N. O.
Publisher:Oxford University Press
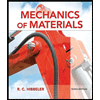
Mechanics of Materials (10th Edition)
Mechanical Engineering
ISBN:9780134319650
Author:Russell C. Hibbeler
Publisher:PEARSON
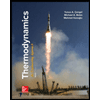
Thermodynamics: An Engineering Approach
Mechanical Engineering
ISBN:9781259822674
Author:Yunus A. Cengel Dr., Michael A. Boles
Publisher:McGraw-Hill Education
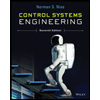
Control Systems Engineering
Mechanical Engineering
ISBN:9781118170519
Author:Norman S. Nise
Publisher:WILEY
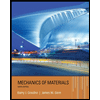
Mechanics of Materials (MindTap Course List)
Mechanical Engineering
ISBN:9781337093347
Author:Barry J. Goodno, James M. Gere
Publisher:Cengage Learning
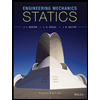
Engineering Mechanics: Statics
Mechanical Engineering
ISBN:9781118807330
Author:James L. Meriam, L. G. Kraige, J. N. Bolton
Publisher:WILEY
Related Questions
- HEAT TRANSFER CASE: I want to know what temperature in (°F) the cylinder will have inside. It's a heat transfer problem. what is T2 ? HEAT TRANSFER They gave me an answer all squashed together that i can't make sense of it. If you could help me makes sense of it thank you!arrow_forwardI need assistance designing three structural models on Fusion 360 (bamboo-inspired, bone-inspired, and a control cylinder) for a mechanics project. These models will be tested under compression to compare their load-bearing capacity, energy absorption, and failure modes. Here are the specific details and requirements for each design: General Requirements: External Dimensions: All models must have the same outer dimensions: height = 15 cm, diameter = 5 cm. Material Volume: Ensure each design uses approximately the same material volume (e.g., relative density = 30% of the total volume). If you have any other ideas on how to ensure the test is fair between all 3 samples please note it! File Format: Provide the designs as STL files compatible with 3D printing or a step-by-step process. Design Specifications: 1. Control Cylinder: A simple hollow cylinder with: Wall Thickness: 2 mm. Inner Diameter: 4.6 cm (to maintain the outer diameter and wall thickness). No additional…arrow_forwardi want a displacement and stress equations and mak calculationarrow_forward
- The purpose of this problem is to show the relationship between material constants typically used in engineering practice. This is useful because you may often have access to measurements of or tabulated values of some constants (e.g., Young's modulus and Poisson's ratio) but need another constant (e.g., shear modulus) for a calculation. Use the expression Cijkl = µ(dildjk + dikdjl) + Ad¿jdkl to derive the following: (a) Young's modulus, E = µ(3X+2µ)/(X+μ), from the definition 11 = Ee11 in a unconfined (022 = 0,033 = 0) uniaxial tension test. (b) Poisson's ratio, v = \/(2(X + μ)), from the definition v = €22/11 in the same test as in (a). (c) Shear modulus, μ = G = 012/(2€12) = E/(2(1 + v)). Use the results to show that C can also be written Cijkl Ev/((1+v)(1 − 2v))dij§kl. = E/(2(1 + v))(duðjk + dikdjl) +arrow_forwardE and 5 v X O file:///C:/Users/Hp/Desktop/mm/OUTCOME%20NO.2%20and%205%20with%20Problems.pdf + O Fit to page D Page view A Read aloud 1 Add notes Problems 1. A brass rod of diameter 25 mm and length 250 mm is subjected to a tensile load of 50 kN and the extension of the rod is equal to 0.3 mm. Find the Young's Modulus or Modulus of Elasticity. 99+ to search hp delete prt sc 14 DI backs & 7 8 24 4 P EJR -0 J K H D. Farrow_forward1- what materials are included here (z parameter), type of materials considered, property or properties plotted, domain of c, parameter identified 2- what are the vertical and horizontal trends presented 3-what is the take away story from this plot please answer i will upvotearrow_forward
- Calculate the stiffness matrix for the Q8 element shown below. Make use of the shape functions in natural coordinates and the Jacobian calculated in previous problems. Use 2x2 Gaussian numerical integration. Use plane strain conditions (for unit thickness) with E=200E9 (MPa) and nu=0.25. I have attached my matlab code below. Please look thru it and correct it. Thanks. u=sym('u') %%ztav=sym('v') %%eta x1=1x2=2x3=3.5x4=3.6x5=4.0x6=2.3x7=1.2x8=0.8 y1=1y2=1y3=1.3y4=2.3y5=3.3y6=3.2y7=3.0y8=2.0X=[x1;x2;x3;x4;x5;x6;x7;x8]Y=[y1;y2;y3;y4;y5;y6;y7;y8]%% diff of ztaDN1Du=1/4*(1-v)*(2*u+v);DN2Du=-u*(1-v);DN3Du=1/4*(1-v)*(2*u-v);DN4Du=1/2*(1-v^2);DN5Du=1/4*(1+v)*(2*u+v);DN6Du=-u*(1+v);DN7Du=1/4*(1+v)*(2*u-v);DN8Du=-1/2*(1-v^2); %% diff of etaDN1Dv=1/4*(1-u)*(2*v+u);DN2Dv=-1/2*(1-u^2);DN3Dv=1/4*(1+u)*(2*v-u);DN4Dv=-v*(1+u);DN5Dv=1/4*(1+u)*(2*v+u);DN6Dv=1/2*(1-u^2);DN7Dv=1/4*(1-u)*(2*v+u);DN8Dv=-v*(1-u);%% find dx/du dx/dv, dy/du and dy/dva=[DN1Du, DN2Du, DN3Du, DN4Du, DN5Du, DN6Du,DN7Du,…arrow_forwardUnlike the tensile effort, which tends to straighten the parts, the compression effort tends to accentuate the effect of the initial curvature. The lateral displacements produced make up the flexural buckling process. The buckling of the part tends to reduce its load capacity.Source: Neto, J. G. R. Class notes - Metallic Structures: Compressed parts. DEC/PUC. Available at: https://professor.pucgoias.edu.br/SiteDocente/admin/arquivosUpload/17448/material/5%20-%20PECAS%20COMPRIMIDAS.pdf. Accessed on: 05/10/2024. Checking the safety of compressed parts varies depending on the slenderness of the part. A column with a circular section and buckling length equal to 320 cm is classified as moderately slender. Knowing that it receives a centered force of 480kN, carry out the necessary calculations and select the alternative that presents the requirements associated with its correct dimensioning. AlternativesAlternative 1:A simple compression generated by the load 480.0 kN. Alternative 2:A…arrow_forwardCalculate the stiffness matrix for the Q8 element shown below. Make use of the shape functions in natural coordinates and the Jacobian calculated in previous problems. Use 2x2 Gaussian numerical integration. Use plane strain conditions (for unit thickness) with E=200E9 (MPa) and nu=0.25. The final answers is F1= 0.18452e12. I have attached my matlab code below. Please look thru it and correct it. Thanks. u=sym('u') %%ztav=sym('v') %%eta x1=1x2=2x3=3.5x4=3.6x5=4.0x6=2.3x7=1.2x8=0.8 y1=1y2=1y3=1.3y4=2.3y5=3.3y6=3.2y7=3.0y8=2.0X=[x1;x2;x3;x4;x5;x6;x7;x8]Y=[y1;y2;y3;y4;y5;y6;y7;y8]%% diff of ztaDN1Du=1/4*(1-v)*(2*u+v);DN2Du=-u*(1-v);DN3Du=1/4*(1-v)*(2*u-v);DN4Du=1/2*(1-v^2);DN5Du=1/4*(1+v)*(2*u+v);DN6Du=-u*(1+v);DN7Du=1/4*(1+v)*(2*u-v);DN8Du=-1/2*(1-v^2); %% diff of etaDN1Dv=1/4*(1-u)*(2*v+u);DN2Dv=-1/2*(1-u^2);DN3Dv=1/4*(1+u)*(2*v-u);DN4Dv=-v*(1+u);DN5Dv=1/4*(1+u)*(2*v+u);DN6Dv=1/2*(1-u^2);DN7Dv=1/4*(1-u)*(2*v+u);DN8Dv=-v*(1-u);%% find dx/du dx/dv, dy/du and dy/dva=[DN1Du, DN2Du, DN3Du,…arrow_forward
arrow_back_ios
SEE MORE QUESTIONS
arrow_forward_ios
Recommended textbooks for you
- Elements Of ElectromagneticsMechanical EngineeringISBN:9780190698614Author:Sadiku, Matthew N. O.Publisher:Oxford University PressMechanics of Materials (10th Edition)Mechanical EngineeringISBN:9780134319650Author:Russell C. HibbelerPublisher:PEARSONThermodynamics: An Engineering ApproachMechanical EngineeringISBN:9781259822674Author:Yunus A. Cengel Dr., Michael A. BolesPublisher:McGraw-Hill Education
- Control Systems EngineeringMechanical EngineeringISBN:9781118170519Author:Norman S. NisePublisher:WILEYMechanics of Materials (MindTap Course List)Mechanical EngineeringISBN:9781337093347Author:Barry J. Goodno, James M. GerePublisher:Cengage LearningEngineering Mechanics: StaticsMechanical EngineeringISBN:9781118807330Author:James L. Meriam, L. G. Kraige, J. N. BoltonPublisher:WILEY
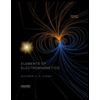
Elements Of Electromagnetics
Mechanical Engineering
ISBN:9780190698614
Author:Sadiku, Matthew N. O.
Publisher:Oxford University Press
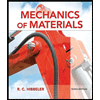
Mechanics of Materials (10th Edition)
Mechanical Engineering
ISBN:9780134319650
Author:Russell C. Hibbeler
Publisher:PEARSON
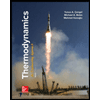
Thermodynamics: An Engineering Approach
Mechanical Engineering
ISBN:9781259822674
Author:Yunus A. Cengel Dr., Michael A. Boles
Publisher:McGraw-Hill Education
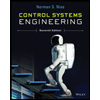
Control Systems Engineering
Mechanical Engineering
ISBN:9781118170519
Author:Norman S. Nise
Publisher:WILEY
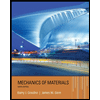
Mechanics of Materials (MindTap Course List)
Mechanical Engineering
ISBN:9781337093347
Author:Barry J. Goodno, James M. Gere
Publisher:Cengage Learning
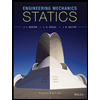
Engineering Mechanics: Statics
Mechanical Engineering
ISBN:9781118807330
Author:James L. Meriam, L. G. Kraige, J. N. Bolton
Publisher:WILEY