MECH 4013 Lab 3 Spinal fixation
pdf
keyboard_arrow_up
School
Carleton University *
*We aren’t endorsed by this school
Course
4013
Subject
Mechanical Engineering
Date
Jan 9, 2024
Type
Pages
4
Uploaded by SuperDanger388
MECH 4013 –
BIOMEDICAL DEVICE DESIGN
Experiment 4
1
MECH 4013 –
BIOMEDICAL DEVICE DESIGN
EXPERIMENT 3: Posterior Spinal Fixation
(
Location: 7103 Canal building
)
1. Introduction
Four out of five adults experience at least one episode of low back pain during their life.
Although not all of these patients will require surgery, there is an increasing number of people that
need fusion of one or more levels of their vertebrae. The major challenge in spinal fusion surgery
is to achieve a rigid clinical stabilization (i.e. reduce the movement of two adjacent vertebrae) to
allow the vertebrae to fuse through bone growth. There are a number of techniques used to fuse
vertebrae, but the most common is known as posterior stabilization. The major challenge for the
orthopaedic surgeon is to achieve sufficient “stabilization”
so that bony fusion can occur. In this
lab we will measure the 3D motion of a porcine cadaveric cervical spine before and after the
implantation of a posterior instrumentation
2. Safety
•
Every student is required to bring a lab coat and safety goggles.
•
While handling the biological tissue, students are required to wear surgical gloves.
•
Please advise the instructor beforehand if you are allergic to latex.
•
You may use a scalpel to remove soft tissues from the cadaveric porcine bone. Use caution
when using the scalpel. A special container is provided for disposal of scalpel blades after
use.
3. Materials
•
Cadaveric porcine cervical spine
•
Scalpel
•
A custom designed posterior fixation device with pedicle screws.
•
Drill bit
•
Drill press/ hand drill
•
Custom spine tester
•
Optotrak system with computer
•
Orthopaedic Research pins with Rigid Bodies
•
6-axis load cell
•
Computer to record force and moment data.
MECH 4013 –
BIOMEDICAL DEVICE DESIGN
Experiment 4
2
4.
Experimental Procedure
1.
Dissect any extraneous soft tissue such as muscles and tendon. Do not damage the facet
joint capsules or the ligaments.
2.
Clamp lowest vertebra in the lower fixture, with the thin plate and four clamping screws
anterior, and the other side within the spinal canal. This should leave an intervertebral disc
exposed just above the plate. If the lowest vertebra does not fit in the clamp, it can be
removed and the next vertebra secured in the clamp. Record the number of vertebral bodies
in the spine segment that is used.
3.
Mount the upper fixture on the axis (C2) vertebra and screw into place.
4.
Place the lower fixture in the clamps of the six axis load cell so that the left side is facing
the torque device. This will orient the specimen for flexion-extension loading. Align the
plate so that it is flush with the back of the load cell. Tighten the four bolts.
5.
Attach the torsion arm to the upper fixture using two bolts.
6.
Use two orthopaedic research pins with rigid bodies and insert in the transverse process
above the lowest exposed disc. These should be inserted with one above the vertebral disc
that will be ‘injured’ (the lowest exposed disc) and the other in the top vertebra. These can
be inserted without pre-drilling (Figure 1). A third rigid body is mounted on the load cell
and is used as a reference for the bottom vertebra within the fixture.
7.
Use a third orthopaedic research pin with rigid body that has been calibrated as a digitiser
with the NDI First Principles software. With the help of the TA, place the tip of the device
Figure 1:
MECH 4013 –
BIOMEDICAL DEVICE DESIGN
Experiment 4
3
on each landmark listed below and record the coordinates with the NDI First Principles
program. Record landmarks for the lowest two vertebra, above and below the injury level,
and the top vertabra; coordinates will be associated with the orthopaedic research pin
secured to the same vertebra so that the 3D coordinates of the landmarks (virtual markers)
are tracked and recorded during spine motions. Landmarks to be recorded: anterior
vertebral body; left lateral vertebral body; right lateral vertebral body. Repeat for each
required vertebra and ensure that each set of three points are not collinear.
8.
Set the angle control to 15 degrees for both directions in the Labview program and run
three preconditioning cycles.
9.
Set the Collection Settings in NDI First Principles to record for 10 seconds.
10.
Set the angle control to 15 degrees for both directions in the Labview program.
11.
Ensure that all orthopaedic research pins are visible to the Optotrak camera throughout the
range of motion.
12.
Press start on Labview and Record in the First Principles software and the test will run for
three cycles. Do not stand between the Optotrack camera and the specimen during this
time. Once the collection is complete, save both the Labview and Optotrack data files with
appropriate file names (e.g. Intact_flex-ext).
13.
Rotate the specimen so that anterior is facing the torque device. This will align the
specimen for lateral bending. BE EXTREMELY CAREFUL NOT TO BUMP THE
TRACKING DEVICES. Ensure that the Optotrak rigid bodies are visible. Note that the
camera and/or entire test apparatus may be moved between tests. The spine must not be
moved within the clamp.
14.
Re-attach the torsion arm and repeat the test. Save the data files with appropriate names
(e.g. Intact_lateralbending)
14.
Various injury models may be applied to the specimen shown below, after which the
specimen will be retested in flexion-extension and lateral bending. The configurations are:
a.
Cut the capsules and cartilage of the facet joints on both sides, between the lowest
and next lowest vertebrae.
b.
Cut the lowest exposed disc (as described in #2).
c.
Apply pedicle screw fixation to the posterior spine, across the injured level. Locate
the pedicles by resecting soft tissues in the posterior and lateral region above and
below the cuts in part a. Drill a small hole down the pedicle and insert a pedicle
screw. Repeat above and below the injury on both sides. Fix a connecting rod
between upper and lower pedicle screws (Figure 2).
Choose one injury model to apply to your specimen (a or b above, or both simultaneously) and
report your choice. Include photo(s) of the injury. After testing the injured spine, apply pedicle
screw fixation described in c. Note you will have three configurations: in-tact, injured and with
fixation, with two test directions for each (flexion-extension and lateral bending).
Note: For each test you will have two files, one from each computer.
The Labview file will
contain measurements from all six axes of the load cell. The Optotrak file will have the rigid
Your preview ends here
Eager to read complete document? Join bartleby learn and gain access to the full version
- Access to all documents
- Unlimited textbook solutions
- 24/7 expert homework help
MECH 4013 –
BIOMEDICAL DEVICE DESIGN
Experiment 4
4
body data of each tracking device. This will be explained in more detail by the TA. You may
have to manually synchronize the two data collections when analyzing the data.
5. Analysis
Document the preparation of the specimen and how the simulated injuries were performed.
From the Optotrak data calculate the relative rotation of the adjacent vertebrae and the entire spine.
Using the 6-axis load cell data, plot rotation vs moment for the complete last testing cycle of the
intact specimen, the injury model and for the posterior fixation for each of the six test cases, and
include all plots in your report. From this data set determine the range of motion (ROM) and the
neutral zone (NZ).
Summarise your ROM and NZ results in a bar graph. Comment on how the
injury model and the posterior fixation affect the ROM and NZ. Remember to do this analysis for
both the two adjacent vertebrae and the entire spine.
Figure 2:
Related Questions
University of Babylon
Collage of Engineering\Al-Musayab
Department of Automobile
Engineering
Under Grad/Third stage
Notes:
1-Attempt Four Questions.
2- Q4 Must be Answered
3-Assume any missing data.
4 تسلم الأسئلة بعد الامتحان مع الدفتر
Subject: Mechanical
Element Design I
Date: 2022\01\25
2022-2023
Time: Three Hours
Course 1
Attempt 1
Q1/ Design a thin cylindrical pressure tank (pressure vessel) with hemispherical ends to the
automotive industry, shown in figure I below. Design for an infinite life by finding the
appropriate thickness of the vessel to carry a sinusoidal pressure varied from {(-0.1) to (6) Mpa}.
The vessel is made from Stainless Steel Alloy-Type 316 sheet annealed. The operating
temperature is 80 C° and the dimeter of the cylinder is 36 cm. use a safety factor of 1.8.
Fig. 1
(15 Marks)
Q2/ Answer the following:
1- Derive the design equation for the direct evaluation of the diameter of a shaft to a desired
fatigue safety factor, if the shaft subjected to both fluctuated…
arrow_forward
MECT361
Mechatronics Components and Instrumentation
8.1. Why is it not possible to connect sensors such as thermocouples, strain gages, and
accelerometers directly to a digital computer or microprocessor?
PLEASE GIVE ME THE REFRENCE
I Will get zero if you didn't put the refrence
arrow_forward
What are the major stages of a mechanical design process?
. Discuss the importance of innovation in the design process.
What are the categories of system requirements that design engineers
must consider when they start a design process?
arrow_forward
Calculate the magnitude of the resultant joint force
at L5/S1 joint for the stoop lift. The
worker has a height of 1.8 meters and a mass of 84
kg. The box has a mass of 30 kg.
- Assume that the back extensor muscles have a line
of action parallel to and 5 cm
posterior (on the back side) to the trunk.
- Assume the hands are at the center of the box.
- Use the following masses and COM locations to
calculate the moment at the L5/S1 joint
- Note: the body masses and COM positions for the
parts of the body are not in kg or cm.
They are % of the whole body mass/% away from L5/
S1 joint. You need to convert these
percentages to kg and cm.
- Only consider the FBD and forces for one arm.
Assume each arm holds 15kg of the box
weight
arrow_forward
Question 2
You are a biomedical engineer working for a small orthopaedic firm that fabricates rectangular shaped fracture
fixation plates from titanium alloy (model = "Ti Fix-It") materials. A recent clinical report documents some problems with the plates
implanted into fractured limbs. Specifically, some plates have become permanently bent while patients are in rehab and doing partial
weight bearing activities.
Your boss asks you to review the technical report that was generated by the previous test engineer (whose job you now have!) and used to
verify the design. The brief report states the following... "Ti Fix-It plates were manufactured from Ti-6Al-4V (grade 5) and machined into
solid 150 mm long beams with a 4 mm thick and 15 mm wide cross section. Each Ti Fix-It plate was loaded in equilibrium in a 4-point bending
test (set-up configuration is provided in drawing below), with an applied load of 1000N. The maximum stress in this set-up was less than the
yield stress for the…
arrow_forward
Problem 3: A small gearing system in your brand-new 3D printer fails as you were printing,
leading to an overload in the motor and a fire in your home. The fire spreads, burning half of
Everglades National Park in the worst environmental disaster in US history.
The printer company blames you! Stating that you must have been misusing the printer some-
how. Use your engineering knowledge to "show those jerks you mean business!"
You investigate and find a serial number on the gears and type it into Google, finding the
company that manufactures the gears. Their website provides some info that this series of gear is
made from AISI 4340 steel and the yield strength is 125 kpsi.
Assuming each gear tooth acts as a small cantilever, prove to the 3D printer company that they
are liable for the fire.
oct
#
Gear Information
Gear radius (r): 1.00 in
Tooth length (1): 0.15 in
Tooth height (h): 0.15 in
Tooth thickness (b): 0.1 in
Angular velocity (w): 0.1 rad/s
Motor Information
Power (H): 0.009 hp
1…
arrow_forward
How may acoustic designers alter the design of a room, which was previously used for music performances, into a room now to be used for spoken word performances? Use annotated diagrams for your response
arrow_forward
I need help solving this problem.
arrow_forward
what is f and g ?
what is g and f ?
l = .5 finger width
x = Arm length
g = eye level height
d = object distace
A = angle from eye level to top of the object
f = object height from eye level
h = diameter of the sun
.0127 m
.7112 m
1.49668x 10^11 m
1.023 degrees
2.673 x 10^9 m
arrow_forward
Stuck need help!
Problem is attached. please view attachment before answering.
Really struggling with this concept.
Please show all work so I can better understand !
Thank you so much.
arrow_forward
I want to briefly summarize what he is talking about and what you conclude.
pls very urgent
arrow_forward
Please give a complete solution in Handwritten format.
Strictly don't use chatgpt,I need correct answer.
Engineering dynamics
arrow_forward
Pressurized eyes Our eyes need a certain amount of internal pressure in order to work properly, with the normal range being between 10 and 20 mm of mercury. The pressure is determined by a balance between the fluid entering and leaving the eye. If the pressure is above the normal level, damage may occur to the optic nerve where it leaves the eye, leading to a loss of the visual field termed glaucoma. Measurement of the pressure within the eye can be done by several different noninvasive types of instruments, all of which measure the slight deformation of the eyeball when a force is put on it. Some methods use a physical probe that makes contact with the front of the eye, applies a known force, and measures the deformation. One non-contact method uses a calibrated “puff” of air that is blown against the eye. The stagnation pressure resulting from the air blowing against the eyeball causes a slight deformation, the magnitude of which is correlated with the pressure within the eyeball.…
arrow_forward
CHAPTER 5 : DIESEL ENGINE POWER PLANT
A six cylinder, four-stroke CI engine is tested against a water brake dynamometer for which
B.P = WN/17x10' in kW, where W is the brake load in newton and N is the speed of the
engine in the r.p.m. The air consumption was measured by means of a sharp edged orifice.
During the test following observersations were taken :
• Bore
• Stroke
• Speed
• Brake load
Barometer reading
= 10 cm
= 14 cm
= 2500 rpm
= 480 N
= 76 cm Hg
• Orifice diameter
• Co-efficient of discharge of orifice
• Pressure drop across orifice
• Room temperature
Fuel Consumption
= 3.3 cm
= 0.62
= 14 cm of Hg
= 25°C
= 0.32 kg/min
Calculate following :
i.
The volumetric efficiency
The brake mean effective pressure ( b.m.e.p)
The engine torque
The brake specific fuel consumption ( b.s.f.c )
ii.
iv.
arrow_forward
https://www.sciencedirect.com/science/article/abs/pii/S0965997822001569
In the literature review, they should present the system installed and the main results obtained. In other words, the enhancement due to the installed system. They have to define the system used in this study. (the report talking about ventilation) pls in briefly
Don’t using chatgpt please urgent
i will give u good feedback
arrow_forward
SEE MORE QUESTIONS
Recommended textbooks for you
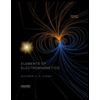
Elements Of Electromagnetics
Mechanical Engineering
ISBN:9780190698614
Author:Sadiku, Matthew N. O.
Publisher:Oxford University Press
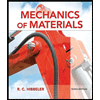
Mechanics of Materials (10th Edition)
Mechanical Engineering
ISBN:9780134319650
Author:Russell C. Hibbeler
Publisher:PEARSON
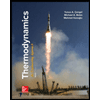
Thermodynamics: An Engineering Approach
Mechanical Engineering
ISBN:9781259822674
Author:Yunus A. Cengel Dr., Michael A. Boles
Publisher:McGraw-Hill Education
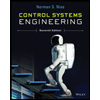
Control Systems Engineering
Mechanical Engineering
ISBN:9781118170519
Author:Norman S. Nise
Publisher:WILEY
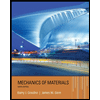
Mechanics of Materials (MindTap Course List)
Mechanical Engineering
ISBN:9781337093347
Author:Barry J. Goodno, James M. Gere
Publisher:Cengage Learning
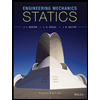
Engineering Mechanics: Statics
Mechanical Engineering
ISBN:9781118807330
Author:James L. Meriam, L. G. Kraige, J. N. Bolton
Publisher:WILEY
Related Questions
- University of Babylon Collage of Engineering\Al-Musayab Department of Automobile Engineering Under Grad/Third stage Notes: 1-Attempt Four Questions. 2- Q4 Must be Answered 3-Assume any missing data. 4 تسلم الأسئلة بعد الامتحان مع الدفتر Subject: Mechanical Element Design I Date: 2022\01\25 2022-2023 Time: Three Hours Course 1 Attempt 1 Q1/ Design a thin cylindrical pressure tank (pressure vessel) with hemispherical ends to the automotive industry, shown in figure I below. Design for an infinite life by finding the appropriate thickness of the vessel to carry a sinusoidal pressure varied from {(-0.1) to (6) Mpa}. The vessel is made from Stainless Steel Alloy-Type 316 sheet annealed. The operating temperature is 80 C° and the dimeter of the cylinder is 36 cm. use a safety factor of 1.8. Fig. 1 (15 Marks) Q2/ Answer the following: 1- Derive the design equation for the direct evaluation of the diameter of a shaft to a desired fatigue safety factor, if the shaft subjected to both fluctuated…arrow_forwardMECT361 Mechatronics Components and Instrumentation 8.1. Why is it not possible to connect sensors such as thermocouples, strain gages, and accelerometers directly to a digital computer or microprocessor? PLEASE GIVE ME THE REFRENCE I Will get zero if you didn't put the refrencearrow_forwardWhat are the major stages of a mechanical design process? . Discuss the importance of innovation in the design process. What are the categories of system requirements that design engineers must consider when they start a design process?arrow_forward
- Calculate the magnitude of the resultant joint force at L5/S1 joint for the stoop lift. The worker has a height of 1.8 meters and a mass of 84 kg. The box has a mass of 30 kg. - Assume that the back extensor muscles have a line of action parallel to and 5 cm posterior (on the back side) to the trunk. - Assume the hands are at the center of the box. - Use the following masses and COM locations to calculate the moment at the L5/S1 joint - Note: the body masses and COM positions for the parts of the body are not in kg or cm. They are % of the whole body mass/% away from L5/ S1 joint. You need to convert these percentages to kg and cm. - Only consider the FBD and forces for one arm. Assume each arm holds 15kg of the box weightarrow_forwardQuestion 2 You are a biomedical engineer working for a small orthopaedic firm that fabricates rectangular shaped fracture fixation plates from titanium alloy (model = "Ti Fix-It") materials. A recent clinical report documents some problems with the plates implanted into fractured limbs. Specifically, some plates have become permanently bent while patients are in rehab and doing partial weight bearing activities. Your boss asks you to review the technical report that was generated by the previous test engineer (whose job you now have!) and used to verify the design. The brief report states the following... "Ti Fix-It plates were manufactured from Ti-6Al-4V (grade 5) and machined into solid 150 mm long beams with a 4 mm thick and 15 mm wide cross section. Each Ti Fix-It plate was loaded in equilibrium in a 4-point bending test (set-up configuration is provided in drawing below), with an applied load of 1000N. The maximum stress in this set-up was less than the yield stress for the…arrow_forwardProblem 3: A small gearing system in your brand-new 3D printer fails as you were printing, leading to an overload in the motor and a fire in your home. The fire spreads, burning half of Everglades National Park in the worst environmental disaster in US history. The printer company blames you! Stating that you must have been misusing the printer some- how. Use your engineering knowledge to "show those jerks you mean business!" You investigate and find a serial number on the gears and type it into Google, finding the company that manufactures the gears. Their website provides some info that this series of gear is made from AISI 4340 steel and the yield strength is 125 kpsi. Assuming each gear tooth acts as a small cantilever, prove to the 3D printer company that they are liable for the fire. oct # Gear Information Gear radius (r): 1.00 in Tooth length (1): 0.15 in Tooth height (h): 0.15 in Tooth thickness (b): 0.1 in Angular velocity (w): 0.1 rad/s Motor Information Power (H): 0.009 hp 1…arrow_forward
- How may acoustic designers alter the design of a room, which was previously used for music performances, into a room now to be used for spoken word performances? Use annotated diagrams for your responsearrow_forwardI need help solving this problem.arrow_forwardwhat is f and g ? what is g and f ? l = .5 finger width x = Arm length g = eye level height d = object distace A = angle from eye level to top of the object f = object height from eye level h = diameter of the sun .0127 m .7112 m 1.49668x 10^11 m 1.023 degrees 2.673 x 10^9 marrow_forward
- Stuck need help! Problem is attached. please view attachment before answering. Really struggling with this concept. Please show all work so I can better understand ! Thank you so much.arrow_forwardI want to briefly summarize what he is talking about and what you conclude. pls very urgentarrow_forwardPlease give a complete solution in Handwritten format. Strictly don't use chatgpt,I need correct answer. Engineering dynamicsarrow_forward
arrow_back_ios
SEE MORE QUESTIONS
arrow_forward_ios
Recommended textbooks for you
- Elements Of ElectromagneticsMechanical EngineeringISBN:9780190698614Author:Sadiku, Matthew N. O.Publisher:Oxford University PressMechanics of Materials (10th Edition)Mechanical EngineeringISBN:9780134319650Author:Russell C. HibbelerPublisher:PEARSONThermodynamics: An Engineering ApproachMechanical EngineeringISBN:9781259822674Author:Yunus A. Cengel Dr., Michael A. BolesPublisher:McGraw-Hill Education
- Control Systems EngineeringMechanical EngineeringISBN:9781118170519Author:Norman S. NisePublisher:WILEYMechanics of Materials (MindTap Course List)Mechanical EngineeringISBN:9781337093347Author:Barry J. Goodno, James M. GerePublisher:Cengage LearningEngineering Mechanics: StaticsMechanical EngineeringISBN:9781118807330Author:James L. Meriam, L. G. Kraige, J. N. BoltonPublisher:WILEY
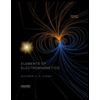
Elements Of Electromagnetics
Mechanical Engineering
ISBN:9780190698614
Author:Sadiku, Matthew N. O.
Publisher:Oxford University Press
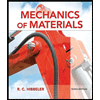
Mechanics of Materials (10th Edition)
Mechanical Engineering
ISBN:9780134319650
Author:Russell C. Hibbeler
Publisher:PEARSON
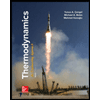
Thermodynamics: An Engineering Approach
Mechanical Engineering
ISBN:9781259822674
Author:Yunus A. Cengel Dr., Michael A. Boles
Publisher:McGraw-Hill Education
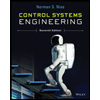
Control Systems Engineering
Mechanical Engineering
ISBN:9781118170519
Author:Norman S. Nise
Publisher:WILEY
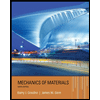
Mechanics of Materials (MindTap Course List)
Mechanical Engineering
ISBN:9781337093347
Author:Barry J. Goodno, James M. Gere
Publisher:Cengage Learning
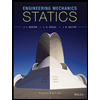
Engineering Mechanics: Statics
Mechanical Engineering
ISBN:9781118807330
Author:James L. Meriam, L. G. Kraige, J. N. Bolton
Publisher:WILEY