Week 4 Lab
docx
keyboard_arrow_up
School
ECPI University *
*We aren’t endorsed by this school
Course
220
Subject
Mechanical Engineering
Date
Jan 9, 2024
Type
docx
Pages
8
Uploaded by PrivateElement11067
EET 220 Industrial Applications
Professor D. Overbye
Week 4 Lab 6 “Proportional and Proportional-Integral Control System”
By: Deandre Wheelington
ECPI University
I pledge to support the Honor System of ECPI. I will refrain from any form of academic
dishonesty or deception, such as cheating or plagiarism. I am aware that as a member
of the academic community it is my responsibility to turn in all suspected violators of the
honor code. I understand that any failure on my part to support the Honor System will
be turned over to a Judicial Review Board for determination. I will report to a Judicial
Review Board hearing if summoned.
Name Deandre Wheelington
Date: 03 Dec 23
1
Abstract:
In this lab, we will be using an application known as LabView. Within this
application we will be determining the difference between input gain and steady
state error can make on a tank controlled by a setpoint value and an added slow
leak. In a second portion, we will discuss the effect of a time integral on the
steady state error. The variables used in this lab will help determine how
imperative an inputted gain could be to the output of a system that would
experience steady state error due to the fault of the system.
Introduction:
We will first discuss the process of proportional control. With proportional control,
we will be covering how the tank level output follows the setpoint value given a
small amount of gain with no added time integral. We will discuss oscillations of
the steady state error as we add different values to the setpoint of the tank and
different values of gain at the input of the controller. With both values at play, we
will determine how it affects the steady state error. In the second part of the lab,
we will discuss the process of proportional integral control. In this process, we
will determine the effect of adding a time interval to the input of the controller has
on the steady state error with a given gain amount.
2
Lab 6: Proportional and Proportional - Integral Control System
I.
Objectives
:
After completing this lab experiment you should be able to tune and understand the,
1.
Behavior of Proportional (P) system.
2.
Behavior of Proportional – Integral (PI) system.
II.
Procedures
:
1.
Download the LabVIEW file
EET220_Lab_6_LabVIEW_file_Online.vi
file from canvas.
2.
On the front panel, there should be two tabs Introduction and Operations as seen in
Figure 1 below. The introduction tab gives an overview of the simulator with a review of
Piping and Instrumentation Diagrams (P&ID). The operation tab has the tank simulator.
3
Your preview ends here
Eager to read complete document? Join bartleby learn and gain access to the full version
- Access to all documents
- Unlimited textbook solutions
- 24/7 expert homework help
Figure 1: Introduction tab of VI
3.
Select the operation tab in the LabVIEW VI it should look like Figure 2 below.
4
Tabs
Figure 2: Operation Tab of VI
4.
Review the Figure 2 above to become familiar with your Setpoint and PID gains before
getting started.
5.
Run the LabVIEW VI, by clicking on the white Run button or using shortcut Ctrl + R.
6.
Leave the VI in the RUN mode. Now tune the setpoint slider and observe the red plot
which is the set point changes from 100 to 0.
7.
On the graph, the blue plot is the current location of the process variable which is the
feedback signal coming from the tank level sensor.
8.
Now tune the setpoint Slider. Since the PID gains are set to zero, the controller output
(Green Plot) should stay at 0, so the tank level will not change.
9.
Going forward, we will tune the PID gains of this control system such that the blue plot
(current level of the tank from the tank level sensor) should follow the red plot (set point)
as quickly and as closely as possible.
Part I: Proportional Control
10. Now, set the proportional gain (Kc) to 5 and integral time to 0.
5
Setpoint
Slider
PID Gains
11. Fill the following table by tuning the Setpoint Slider.
Setpoint Slider
Set point
value
Tank Level
Sensor output
Steady State
Error (SSE)
Oscillations
(yes/no/small/large
)
Setpoint @ 20
20.00
15.92
21.06
no
Setpoint @ 100
100
86.66
68.89
no
Table 3: Output and error reading when Kc = 5
12. Does the tank level output (blue plot) follow the set point (red plot) closely? Explain the
reason below.
Yes, the tank level output follows the set point closely because the controller is trying
to match the setpoint and the proportional side of the house is trying to match that
input. However, there is a slow leak in the tank, so the output will never quite reach
the designated setpoint (input). The higher the set point value, the bigger the gap
between output and setpoint
13. Put back the Setpoint slider to 100. Now, set the proportional gain (Kc) to 10 and integral
time to 0. Write your observations below?
There is a higher tank level output (closer to setpoint) and a controller output
because you’re adding more gain to the input. The difference between controller
output to setpoint is about the same amount of gap.
14. Fill the following table by tuning the setpoint slider.
Setpoint Slider
Setpoint
Output
Tank Level
Sensor
Output
Steady State
Error (SSE)
Oscillations
(yes/no/small/large
)
Setpoint @ 100
100
92.94
72.67
small
Setpoint @ 20
20
17.85
22.65
small
Table 4: Output and error reading when Kc = 10
15. Compare the results from Table and with Table 4 with the Setpoint at 100, what
happened to the steady state error (SSE)?
The SSE relatively did not change too
much even though we added gain, we just saw a higher tank level sensor output.
16. Now, change the value of Kc to 15 and integral time to 0.
6
Your preview ends here
Eager to read complete document? Join bartleby learn and gain access to the full version
- Access to all documents
- Unlimited textbook solutions
- 24/7 expert homework help
17. Now, now adjust the Setpoint slider to 50. Now the Tank level (blue plot) should begin to
move towards the setpoint (red plot). The system begins to oscillate sometimes for a
long time before reaching to the steady state. The steady state error (SSE) when
compared to Kc = 10 is
increased
(
increased/decreased)
18. Now change the gain Kc to 20. Write your observations below.
When the gain is changed to 20, there is a dramatic oscillation of steady state error,
where the controller output can not reach a point of steady output. The gain added to
the tank level is so high that the value of the output is increasing to its max and then
decreasing to its minimum never able to reach that solid output. Its trying to
compensate for itself almost as an infinite pendulum never reaching back to its flat
steady output.
19. So, in a proportional control system, as the proportional gain (Kc) increases, the steady
state error
Increases.
(
increases/decreases) and tendency for oscillations are
Increased.
(
increased/decreased)
20. Increase the Kc value in steps of 1 and move the Setpoint slider, observe the response
of the system and from your testing choose proper Kc value required, so that the
oscillations are minimum. The chosen kc value is __________
50___.
Part II: Proportional – Integral Control
21. Since proportional control alone cannot eliminate the steady state error, we will
incorporate integral action into the control loop. When we add integral mode to the
system, the controller continues to make the adjustments until the Tank level feedback
voltages match with the setpoint voltage meaning
until the SSE is zero
.
22. Leave the Setpoint slider around 50% and adjust the Integral time to Ti = 0.01.
23. What happened to the system?
It adds a 1 second integral to the steady state error when accounting for input gain.
24. Increase the value of Integral time (Ti) by considering all the following guidelines
a.
After setting Ti, move the setpoint slider from one value to the other and wait. The tank
level should move gradually without developing large oscillations (It is recommended
that Ti should be increased by 0.01 with each test).
b.
When you see the oscillations are large, increase the Ti.
c.
Also make sure the blue signal will not overshoot the red one.
7
d.
Reach to the setpoint as quickly as possible without large oscillations and overshoot.
25. As you increase the Ti, what happened to the following?
a.
Oscillations
decreased because it adds a delay in the controller output (SSE)
b.
Time to reach towards the set point
0.07
c.
Steady state error
10.3
26. Amount of overshoot
.10
below process variable (basically right on the dot)
27. Based on the above tuning process the Ti value you end up with is
0.07
Conclusion:
To conclude this lab, we determined that with a given gain input at our controller, our steady
state error increases on the output of our controller. The higher the gain no matter the setpoint,
the more oscillations and higher steady state error you will receive. This is because once the
steady state error becomes so large, it is essentially uncontrollable because of the constant
compensation it is trying to make between both the highest point of oscillation and the lowest
point of oscillation. With less gain added, the steady state error will decrease again. In the
second portion of the lab, we determined that if we add a slight time integral (delay) in the input
of the controller, it tends to delay the amount of gain thus smoothing out the oscillations of
steady state error and providing for a cleaner output as close to the setpoint as possible
(because of the slow leak).
SOURCES:
Bartelt, T. L. (2011). Industrial Automated Systems: Instrumentation and Motion Control.
Cengage Limited.
https://ecpi.vitalsource.com/books/9781305474277
8
Related Documents
Related Questions
Identify the lines
arrow_forward
Q1:
A. One of the researchers discovered a patent related to the development of a
certain software module in mobile devices, and when he emailed one of the
companies producing these devices, they asked him to send the research to try it on
their devices, and after a while this researcher discovered that his discovery was
used by this company without referring to him or buying this discovery, What do
you think about the above.
B. As a quality control engineer in one of the electrical appliance factories, I
discovered that the technical worker responsible for inspecting one of these
products seals its validity without inspecting it. when I filed a complaint with the
administration, the administration neglected the complaint, arguing that there was
no time to inspect it again due to lack of time to prepare the consumer.
1. What are the consequences of this action, it is possible that there is a bad in the
product due to lack of examination.
2. The actions that you should take because of…
arrow_forward
Please do not copy other's work and do not use ChatGPT or Gpt4,i will be very very very appreciate!!!
Thanks a lot!!!!!
arrow_forward
University of Babylon
Collage of Engineering/
Al-Musayab
Department of Automobiles
Mid Examination/ Stage: 3rd
Subject: Theory of Vehicles
Date: 14 \ 4 \2025
Time: 1.5 Hours
2025-2024
Q1: The arms of a Porter governor are 250 mm long. The upper arms are pivoted on
the axis of revolution, but the lower arms are attached to a sleeve at a distance of 50
mm from the axis of rotation. The weight on the sleeve is 600 N and the weight of
each ball is 80 N. Determine the equilibrium speed when the radius of rotation of the
balls is 150 mm. If the friction is equivalent to a load of 25 N at the sleeve, determine
the range of speed for this position.
Q2: In a loaded Proell governor shown in Figure below each ball weighs 3 kg and
the central sleeve weighs 25 kg. The arms are of 200 mm length and pivoted about
axis displaced from the central axis of rotation by 38.5 mm, y=238 mm, x=303.5
mm, CE 85 mm, MD 142.5 mm. Determine the equilibrium speed.
Fe
mg
E
M
2
Q3: In a spring loaded Hartnell type…
arrow_forward
I want to answer all the questions by handwriting.
arrow_forward
In a hypothetical scenario respond to the following email to reasuure the owner and in an informative and professional way.
Dear Project Manager-
I am so excited to have broken ground on the new mixed use space. As I watch the underground utilities such as water, storm drain, and sewer get installed I find myself worrying about failures. What steps are you taking to ensure those systems will not have to be dug up and repaired later in the construction process? We cannot afford a delay of any kind. Could you please explain how you plan to prevent any delays and ensure that the systems are functional and leak free.
The other concern that has come up that I would like to address now is the comfort of the office staff. Our current building is not comfortable. I am wondering why. We have the temperature appropriately set and it is easily maintained, but people still complain. What can we do to ensure they will be comfortable in the new building? A few months ago I asked one of our…
arrow_forward
Problem 1: You are working in a consulting company that does a lot of hand calculations for designs in
Aerospace Industry for mechanical, thermal, and fluidic systems. You took the Virtual engineering
course, and you want to convince your boss and the team you work to move to modelling and simulation
in computers using a certain software (Ansys, Abaqus, etc). Discuss the benefits and pitfalls of computer
based models used within an industrial environment to solve problems in engineering.
arrow_forward
I want to briefly summarize what he is talking about and what you conclude.
pls very urgent
arrow_forward
Please solve, engineering econ
arrow_forward
Access Pearson
Mastering Engineering
Back to my courses
Course Home
Course Home
Scores
Review
Next >
arrow_forward
Answer all the calculations questions, if you are not not expert please don't attempt, don't use artificial intelligence
arrow_forward
+ → CO
A student.masteryconnect.com/?iv%3D_n5SY3Pv5S17e01Piby
Gr 8 Sci Bench 1 GradeCam Rutherford TN 2021
AHMAD, ASHNA
D0
3 of 35
A student develops a model of an electric motor using two pins, a wire coil,
coil continues to spin with a certain speed.
wire coil
pins
magnet
tape
battery
How can the student increase the speed of the electric motor?
O by using wider pins
O by using thinner pins
O by using less wire in the clil
O by using more wire in the coil
e Type here to search
近
arrow_forward
DISCUSS THE STEP-BY-STEP PROCESS OF HOW TO COME UP WITH A SOLUTION.
*Preferably if you typed the answer
Thumbs up guaranteed If you discuss the steps. Thankyou!
arrow_forward
I Blackboard @ Texas Tech Uni x
Bb MasteringEngineering - Spri x
E MasteringEngineering Maste X
C Suppose That H = 3.8 M . (Fi x
X Mathway | Calculus Problem x
y! how to take a full page scree
A session.masteringengineering.com/myct/itemView?assignmentProblemID=12360392&offset=next
ABP O
Tp E
G
KAssignment #3
Fundamental Problem 2.29
5 of 6
>
I Review
Part A
Find the magnitude of the projected component of the force along the pipe AO.
(Figure 1)
Express your answer to three significant figures and include the appropriate units.
µA
FAO =
Value
Units
Submit
Request Answer
Figure
4 m
F = 400 N
6 m
5 m
B
4 m
10:31 PM
O Type here to search
2/7/2021
arrow_forward
Problem 3: A small gearing system in your brand-new 3D printer fails as you were printing,
leading to an overload in the motor and a fire in your home. The fire spreads, burning half of
Everglades National Park in the worst environmental disaster in US history.
The printer company blames you! Stating that you must have been misusing the printer some-
how. Use your engineering knowledge to "show those jerks you mean business!"
You investigate and find a serial number on the gears and type it into Google, finding the
company that manufactures the gears. Their website provides some info that this series of gear is
made from AISI 4340 steel and the yield strength is 125 kpsi.
Assuming each gear tooth acts as a small cantilever, prove to the 3D printer company that they
are liable for the fire.
oct
#
Gear Information
Gear radius (r): 1.00 in
Tooth length (1): 0.15 in
Tooth height (h): 0.15 in
Tooth thickness (b): 0.1 in
Angular velocity (w): 0.1 rad/s
Motor Information
Power (H): 0.009 hp
1…
arrow_forward
Hartley Electronics, Inc., in Nashville, producesshort runs of custom airwave scanners for the defense industry.The owner, Janet Hartley, has asked you to reduce inventory byintroducing a kanban system. After several hours of analysis, youdevelop the following data for scanner connectors used in onework cell. How many kanbans do you need for this connector?Daily demand 1,000 connectorsLead time 2 daysSafety stock 12 dayKanban size 500 connectors
arrow_forward
reply to the jobsite owner effectivlr and clearl
I would like to explore the possibility of using a lighting control system. There are times when office staff works long hours and researchers sometimes need to be in the building on nights and weekends. Often times they leave the lights on which increases my electricity costs. I would like to be able to program the lights on a schedule and if the staff needs to work outside that schedule they could request a change with our maintenance staff ahead of time. Could you please look into this and provide me with some potential options.
Regards-Owner
arrow_forward
Mini project
You are an engineer working for a power systems company responsible for ensuring grid
stability. Your team has recently observed low-frequency oscillations in the system following
disturbances such as load changes, faults, and switching operations. These oscillations have
led to voltage instability, frequency deviations, and, in severe cases, system blackouts.
A task force has been formed to address this issue, and you have been assigned a critical
role in developing a damping control strategy. Your objective is to analyze system
performance, propose engineering solutions, and compare the effects of different damping
approaches.
Answer the following questions
1. Identify the Engineering Problem:
- What is the fundamental issue affecting power grid stability?
- How do low-frequency oscillations impact the system's reliability?
- What parameters indicate system instability?
2. Assess the Current Status Using Equations and Calculations:
- Given the characteristic roots of the…
arrow_forward
Please answer the 4th question
arrow_forward
University of Babylon
Collage of Engineering\Al-Musayab
Department of Automobile
Engineering
Under Grad/Third stage
Notes:
1-Attempt Four Questions.
2- Q4 Must be Answered
3-Assume any missing data.
4 تسلم الأسئلة بعد الامتحان مع الدفتر
Subject: Mechanical
Element Design I
Date: 2022\01\25
2022-2023
Time: Three Hours
Course 1
Attempt 1
Q1/ Design a thin cylindrical pressure tank (pressure vessel) with hemispherical ends to the
automotive industry, shown in figure I below. Design for an infinite life by finding the
appropriate thickness of the vessel to carry a sinusoidal pressure varied from {(-0.1) to (6) Mpa}.
The vessel is made from Stainless Steel Alloy-Type 316 sheet annealed. The operating
temperature is 80 C° and the dimeter of the cylinder is 36 cm. use a safety factor of 1.8.
Fig. 1
(15 Marks)
Q2/ Answer the following:
1- Derive the design equation for the direct evaluation of the diameter of a shaft to a desired
fatigue safety factor, if the shaft subjected to both fluctuated…
arrow_forward
Don't copy paste someone else answer if I get to know I'll report and downvote too do on your own and only handwritten with proper steps not that handwritten only
arrow_forward
As an engineer responsible for monitoring works in the area of mechanical systems, you must evaluate the following situation: a large client in the retail area has a refrigeration system where it stores some chilled or frozen products to be sold on the sales floor.Recently, the customer's maintenance department has been questioning the system's performance and requested an evaluation of the system's behavior. You went to the location and requested some information from the maintenance manager about the system, who provided the following data: - The system operates with R-134a refrigerant;- The refrigerated environment is maintained at 0°C and the external environment at 26°C;- The refrigerant flow rate in the system is 0.08 kg/s; In addition to the data provided, you carried out some tests and measured the temperature of the refrigerant fluid at some specific points in the system, such as the compressor inlet and condenser outlet, finding values of 0°C and 26°C respectively.…
arrow_forward
As an engineer responsible for monitoring works in the area of mechanical systems, you must evaluate the following situation: a large client in the retail area has a refrigeration system where it stores some chilled or frozen products to be sold on the sales floor.Recently, the customer's maintenance department has been questioning the system's performance and requested an evaluation of the system's behavior. You went to the location and requested some information from the maintenance manager about the system, who provided the following data: - The system operates with R-134a refrigerant;- The refrigerated environment is maintained at 0°C and the external environment at 26°C;- The refrigerant flow rate in the system is 0.08 kg/s; In addition to the data provided, you carried out some tests and measured the temperature of the refrigerant fluid at some specific points in the system, such as the compressor inlet and condenser outlet, finding values of 0°C and 26°C respectively.…
arrow_forward
SEE MORE QUESTIONS
Recommended textbooks for you
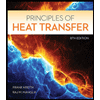
Principles of Heat Transfer (Activate Learning wi...
Mechanical Engineering
ISBN:9781305387102
Author:Kreith, Frank; Manglik, Raj M.
Publisher:Cengage Learning
Related Questions
- Identify the linesarrow_forwardQ1: A. One of the researchers discovered a patent related to the development of a certain software module in mobile devices, and when he emailed one of the companies producing these devices, they asked him to send the research to try it on their devices, and after a while this researcher discovered that his discovery was used by this company without referring to him or buying this discovery, What do you think about the above. B. As a quality control engineer in one of the electrical appliance factories, I discovered that the technical worker responsible for inspecting one of these products seals its validity without inspecting it. when I filed a complaint with the administration, the administration neglected the complaint, arguing that there was no time to inspect it again due to lack of time to prepare the consumer. 1. What are the consequences of this action, it is possible that there is a bad in the product due to lack of examination. 2. The actions that you should take because of…arrow_forwardPlease do not copy other's work and do not use ChatGPT or Gpt4,i will be very very very appreciate!!! Thanks a lot!!!!!arrow_forward
- University of Babylon Collage of Engineering/ Al-Musayab Department of Automobiles Mid Examination/ Stage: 3rd Subject: Theory of Vehicles Date: 14 \ 4 \2025 Time: 1.5 Hours 2025-2024 Q1: The arms of a Porter governor are 250 mm long. The upper arms are pivoted on the axis of revolution, but the lower arms are attached to a sleeve at a distance of 50 mm from the axis of rotation. The weight on the sleeve is 600 N and the weight of each ball is 80 N. Determine the equilibrium speed when the radius of rotation of the balls is 150 mm. If the friction is equivalent to a load of 25 N at the sleeve, determine the range of speed for this position. Q2: In a loaded Proell governor shown in Figure below each ball weighs 3 kg and the central sleeve weighs 25 kg. The arms are of 200 mm length and pivoted about axis displaced from the central axis of rotation by 38.5 mm, y=238 mm, x=303.5 mm, CE 85 mm, MD 142.5 mm. Determine the equilibrium speed. Fe mg E M 2 Q3: In a spring loaded Hartnell type…arrow_forwardI want to answer all the questions by handwriting.arrow_forwardIn a hypothetical scenario respond to the following email to reasuure the owner and in an informative and professional way. Dear Project Manager- I am so excited to have broken ground on the new mixed use space. As I watch the underground utilities such as water, storm drain, and sewer get installed I find myself worrying about failures. What steps are you taking to ensure those systems will not have to be dug up and repaired later in the construction process? We cannot afford a delay of any kind. Could you please explain how you plan to prevent any delays and ensure that the systems are functional and leak free. The other concern that has come up that I would like to address now is the comfort of the office staff. Our current building is not comfortable. I am wondering why. We have the temperature appropriately set and it is easily maintained, but people still complain. What can we do to ensure they will be comfortable in the new building? A few months ago I asked one of our…arrow_forward
- Problem 1: You are working in a consulting company that does a lot of hand calculations for designs in Aerospace Industry for mechanical, thermal, and fluidic systems. You took the Virtual engineering course, and you want to convince your boss and the team you work to move to modelling and simulation in computers using a certain software (Ansys, Abaqus, etc). Discuss the benefits and pitfalls of computer based models used within an industrial environment to solve problems in engineering.arrow_forwardI want to briefly summarize what he is talking about and what you conclude. pls very urgentarrow_forwardPlease solve, engineering econarrow_forward
- Access Pearson Mastering Engineering Back to my courses Course Home Course Home Scores Review Next >arrow_forwardAnswer all the calculations questions, if you are not not expert please don't attempt, don't use artificial intelligencearrow_forward+ → CO A student.masteryconnect.com/?iv%3D_n5SY3Pv5S17e01Piby Gr 8 Sci Bench 1 GradeCam Rutherford TN 2021 AHMAD, ASHNA D0 3 of 35 A student develops a model of an electric motor using two pins, a wire coil, coil continues to spin with a certain speed. wire coil pins magnet tape battery How can the student increase the speed of the electric motor? O by using wider pins O by using thinner pins O by using less wire in the clil O by using more wire in the coil e Type here to search 近arrow_forward
arrow_back_ios
SEE MORE QUESTIONS
arrow_forward_ios
Recommended textbooks for you
- Principles of Heat Transfer (Activate Learning wi...Mechanical EngineeringISBN:9781305387102Author:Kreith, Frank; Manglik, Raj M.Publisher:Cengage Learning
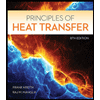
Principles of Heat Transfer (Activate Learning wi...
Mechanical Engineering
ISBN:9781305387102
Author:Kreith, Frank; Manglik, Raj M.
Publisher:Cengage Learning