Lab 5 strain gage application and testing (starts feb 22) (2)
pdf
keyboard_arrow_up
School
Iowa State University *
*We aren’t endorsed by this school
Course
322
Subject
Mechanical Engineering
Date
Apr 3, 2024
Type
Pages
26
Uploaded by Voklo
Aer E 322 Aerospace Structures Laboratory Spring 2024
Lab 5 Strain Gage Application and Testing rev F23
1 Objective
Learn how to install strain gages on specimens and apply them to bending and tensile tests. Introduction
Strain gages are commonly used to measure strain changes on structural parts, which in turn allow us to determine, e.g. how external loads are distributed in the aircraft structure and the actual aerodynamic loads that occur during flight. In Week 6&7 lecture [1] we have learned the basics of strain gages including how they are used in various Wheatstone bridge configurations for bending and tensile tests. In the next two weeks, we will put all the knowledge into practice. The minimum task for the first week (Lab 5a) is to install strain gages on both sides of an aluminum specimen. You will use all the tools and materials shown in Fig. 1 to do so. The process is a bit involved, so carefully follow TA’s instructions, the specific application manuals (available from Canvas) and this manual. The gages can be wired to observe bending (difference between front and back strains) as well as tension (average of front and back strains). After the strain gages are installed successfully, you may move ahead to perform the mechanical tests if time permits. In the second week (Lab 5b), you will then finish all tests (bending, tensile and the supplemental compliance tests) and analyze the data obtained from these tests to determine the aluminum specimen’s mechanical properties such as the Young’s modulus. Starting fall semester of 2023, a state-of-the-art video extensometer was integrated into AerE’s Instron test systems enabling a new way of strain measurements (Fig. 2) and will be utilized extensively in this lab. “A video extensometer is a non-contacting extensometer that can measure deformation by tracking the movement of two attached markers on the specimen, using high-resolution digital camera technology. Key advantages of video extensometers are that they do not exhibit any influence on the test specimen, problems with knife-edge slippage are eliminated, and errors due to inertia of moving parts are also eliminated” [2] (see also [3]). Now it is time for you to “walk the walk” – you need to learn how to be a good technician before you can be a good engineer! References [1] Week 6&7 lecture notes in Canvas [2] Instron web site: https://www.instron.com/th-th/products/testing-accessories/extensometers
[3] see tutorial on video extensometer in “Extensometer wiki.pdf ” (available in Misc
module of Canvas; original source: https://en.wikipedia.org/wiki/Extensometer)
Aer E 322 Aerospace Structures Laboratory Spring 2024
Lab 5 Strain Gage Application and Testing rev F23
2 Figure 2. New Instron video extensometer (enclosed in yellow) to be used in this lab. Figure 1. The tools and materials and the finished specimen with the strain gages installed.
Aer E 322 Aerospace Structures Laboratory Spring 2024
Lab 5 Strain Gage Application and Testing rev F23
3 Work to be done 1.
Prelab
Week 1 (a)
Look into Canvas under module Misc
the three manuals: Strain_gage_datasheet_SGD-5_350-LY13.pdf, Strain_gage_adhesive_user_manual.pdf, Strain_gage_technical_data.pdf
, (b)
Read through the strain gage information, technical data, and attachment procedure in general. Specifically look for gage Omega SGD-5/350-LY13 that we will use in this lab. Review Week 6&7 lecture notes as well, (c)
Make a brief checklist of strain gage installation procedure to yourself for use in lab. Be sure to include all steps involving surface preparation, gluing, and soldering, (d)
Review materials in this lab manual, Week 6&7 lecture notes and demo video. (e)
Work on week 1 prelab and submit to Canvas. Week 2 (a)
Again review materials in this lab manual, Week 6&7 lecture notes and demo video to gain deeper understanding. (b)
Extend your study to video extensometer by reading e.g. extensometer wiki.pdf
available in class Canvas site, (c)
Work on week 2 prelab and submit to Canvas. 2. In lab As always, you MUST wear safety goggles during the lab. Also be careful not to burn your fingers when do soldering
. Our specimen is the same thin aluminum plate used in riveting lab. It is made of 2024-O Aluminum alloy with size 2” x 8” x 0.025". Its nominal value of Young's Modulus is 10600 ksi (or 73.1 GPa) and tensile yield strength is 11000 psi (or 75.8 Mpa) (source: Matweb). Throughout Weeks 1 and 2 labs, remember to take sufficient photos and draw necessary diagrams for later lab report writing. Please also preview the demo video thoroughly – you will learn a lot of technical details that make your work in lab much easier! Strain gage installation (a)
Obtain the aluminum specimen from TA. Double check the dimensions. Double check
Your preview ends here
Eager to read complete document? Join bartleby learn and gain access to the full version
- Access to all documents
- Unlimited textbook solutions
- 24/7 expert homework help
Aer E 322 Aerospace Structures Laboratory Spring 2024
Lab 5 Strain Gage Application and Testing rev F23
4 to make sure the protective plastic film on one or both sides of the specimen has been removed. (b)
Mark clearly the center of the specimen on both sides of specimen surface – these are the locations you will install the gages. Be sure to draw the centerline across the long side. Later we will use it to align the markers for the video extensometer. (c)
Prepare surfaces on both sides of the specimen through a series of degreasing (with degreaser), sanding (with sandpaper) and cleaning (with cotton swabs and acetone if available) (Fig. 3). Please closely follow the demo video, TA’s instructions and the application manuals as follows: use sandpaper to lightly roughen the area where strain gages are to be installed for better bonding between the strain gage and specimen surface through the adhesive. You only need to sand off an area that is about twice the length of the strain gage on both dimensions. For aluminum, 200 to 400-grit sandpaper would work fine. The sanding should be done in a circular motion to allow adhesive to fit with specimen surface contour in all directions. Wipe off the dirt and dust using cleaning paper; only wipe in single direction and use fresh cleaning paper in each pass. Further clean up the sanded area with the degreaser. Then do a final deep cleaning using swabs. Also clean up the glass slide which we will use for transporting the strain gages. (d)
After the surface preparation on both sides of the specimen is done, obtain one strain gage from the TA. Make note of the exact gage factor and resistance specifications. Use tweezer to take out the strain gage from packaging and place it on the glass slide. Make sure the side having lead wires and terminals is facing up. (e)
Cut a strip of the tape about the same two inches width of the specimen. Fold in the sticky side end to end to form a non-sticky plastic patch; set it aside for later use as a “cushion”. Cut another tape strip about the same length. On both ends, fold in the sticky side about a quarter inch to form a non-sticky tab for easier handling and peeling off later. This is our “carrier” tape strip. Figure 3. Surface of aluminum specimen is being prepared and cleaned prior to strain gage installation. Also note the markings of centerlines.
Aer E 322 Aerospace Structures Laboratory Spring 2024
Lab 5 Strain Gage Application and Testing rev F23
5 (f)
Grab the two end tabs of the “carrier” tape strip, move it over right above the strain gage (now on the glass slide), orient the long side of the tape perpendicular to the long side of the slide and have the tape centered at the gage. Then line up the edge of the tape with the edge of strain gage having the lead wires. Pick the gage up from the slide by a light tap directly on the gage. (g)
While still grabbing the tape ends, move the “carrier” tape (with strain gage on it) onto the aluminum specimen, carefully
fine tune its position and orientation the best you can, so that the gage is directly above the marked center location of the specimen, and the long side of strain gage runs parallel to the long side of the specimen (Fig. 4). Press down lightly the tape to the specimen surface. If the gage orientation is not satisfactory, peel the tape off and try again. (h)
Grab the tab on one end of the “carrier” tape and slowly peel off the tape until the gage (still on the tape) just comes off the specimen. (i)
Apply one tiny
drop (we do mean tiny
!)
of glue from the 496 bonder to the specimen surface where the gage will be located (Fig. 5). Pull up the lead wires of the strain gage in an upright position and then smoothly push the tape back onto the specimen. (j)
Grab the “cushion” tape you made earlier and place it on top of the “carrier” tape centered at the strain gage underneath. Through both tapes, evenly press down on the gage with a fingertip. You may see some excessive adhesive gets squeezed out from the edge of the “carrier” tape and the “cushion” tape should prevent it from getting onto your fingertip. Hold firmly for 2 minutes to allow the adhesive to set
. The lead wires of the strain gage should be kept in upright position the whole time and try not to glue any portion of the wires onto the specimen. (k)
Release the finger pressure, remove the “cushion” tape and grab one tape tab to peel off the “carrier” tape: do this
very slowly and as close to zero degree as possible, i.e., with near pure shear force or you may peel off the strain gage too! Remove as much tape or glue residues as you can. Be careful not to touch the gage itself. Figure 4. “Carrier” tape strip used to transport strain gage for installation. Note the gage orientation parallel to the long side of specimen.
Aer E 322 Aerospace Structures Laboratory Spring 2024
Lab 5 Strain Gage Application and Testing rev F23
6 (l)
Insulate the gage by taping the specimen surface area below the lead wires to prevent the gage’s lead wires from touching the specimen (metal) surface. Also protects the gage by covering it with a strip of backside (not sticky) of tape. This can be done by taping a shorter tape strip under the longer covering strip with the sticky sides facing each other. This tape cover will allow the gage to expand freely underneath and protect the gage from accidental damage (Fig. 6). (m)
Obtain the second strain gage and a few paper towels from TA. Turn over the back side of the specimen and install this second strain gage exactly the same way as described in steps (b)-(l). To protect the gage you just installed, be sure to pad the layer of paper towel underneath the specimen during this second installation. Figure 5. Tiny drop of adhesive is being applied for strain gage installation. Figure 6. Tape cover and insulation are made to protect the strain gages.
Your preview ends here
Eager to read complete document? Join bartleby learn and gain access to the full version
- Access to all documents
- Unlimited textbook solutions
- 24/7 expert homework help
Aer E 322 Aerospace Structures Laboratory Spring 2024
Lab 5 Strain Gage Application and Testing rev F23
7 (n)
The next part of strain gage installation is to solder the connecting electrical wires together with the lead wires of strain gages. Note that we will skip the use of terminal pad as the go-between. We will also try to minimize the footprint of the combined strain gage and connecting electrical wires so that the two fiducial marks (to be painted on the centerline of specimen as mentioned in step (b)) for the video extensometer will not be too far away from each other. (o)
Cut two red or black thin (28 awg) electrical wires about 18” long and strip about an inch from all ends. On one side of the specimen, match a gage lead wire with a connecting electric wire end to end, get them crossed at a point which is about half inch to end of electrical wire and about three-quarter inch to strain gage, as shown in Fig. 7a. Then set the two wires in parallel and twist them together inline
. If you do this as suggested, after the two wires were twisted together, you should still have about half inch bare lead wire left (Fig. 7b). This will give you enough bare lead wire to try again in case the soldering coming next turns out failed. (p)
Repeat the same twisting process to connect the other electrical wire with the second lead wire of the gage. (q)
Now you are ready to solder the twisted joints. Turn on the solder station and set the temperature at 650
o
F. Start the soldering process by cleaning up the iron tip with the wet sponge and make sure the iron tip was properly tinned (Fig. 8). Then hold the solder in place on front side of the twisted joint and melt it with the iron tip touching the back side of the joint. Promptly “brush” through the joint with a thin coat of solder – avoid melting too much solder and becoming a lumpy ball (Fig. 9)! Repeat the same for the other twisted joint. (r)
Remove the solder iron and the soldered joints will solidify. Once the soldered joint cools off, pull it slightly to ensure a good connection. Trim off all remaining bare ends of the electrical wires as well as the lead wires of the gage. (s)
Protect the soldered joints by firmly taping them down onto the tape insulation previously made with one strip of tape perpendicular to the long side of specimen. Also pull the soldered joints apart to form a V shape (Fig. 10). (t)
Continue taping down about one inch of each electrical wire, beyond the soldered joint, to the specimen surface. Doing these will prevent the connecting wires from breaking off the gage accidentally and save the area along the centerline for the two fiducial marks to be used by video extensometer. (u)
Test the continuity of the soldered joints with a voltmeter by first turning the voltmeter dial to the Ohm setting and then connecting the voltmeter’s leads with the soldered joints to form a closed circuit (Fig. 11). If the soldering was done successfully, the resistance readout should be within 1-2 ohm accuracy to the gage’s nominal ohm specs. (v)
Turn the specimen over and repeat steps (o)-(u) to solder the electrical wires of the other color to the lead wires of the gage on the second side of specimen.
Aer E 322 Aerospace Structures Laboratory Spring 2024
Lab 5 Strain Gage Application and Testing rev F23
8 Figure 7. Gage lead wire and connecting electrical wire made (a, left) crossed each other before inline twisting and (b, right) after twisted together. Figure 8. Solder iron properly tinned and cleaned prior to soldering. Figure 9. The twisted wire joint is being soldered.
Aer E 322 Aerospace Structures Laboratory Spring 2024
Lab 5 Strain Gage Application and Testing rev F23
9 (w)
We can now paint the fiducial marks for the video extensometer. Go find the white marking pen and the marking jig, both available in the lab. Mark two ink dots through the jig hole on the specimen’s centerline (which you have drawn in step (b)) centered at the gage as much as possible. These two ink dots serve as the fiducial marks in determining the gage length for the video extensometer (Fig. 12). The dot diameter should be within the range of 2-4 mm, and the gage length should be around 2 inches. Wait for the ink dots to dry out, then cut a strip of black electrical tape (also available in lab) and tape it vertically on the specimen in-between the two dots (Fig. 13). This will help to block out light reflection that may affect the performance of video extensometer. (x)
If you will proceed with the mechanical tests afterwards, wait another 10 minutes for a quick cure of the adhesive. Figure 10. Strain gage installed and configurated on specimen. Figure 11. Check the electric continuity of the installed strain gages.
Your preview ends here
Eager to read complete document? Join bartleby learn and gain access to the full version
- Access to all documents
- Unlimited textbook solutions
- 24/7 expert homework help
Aer E 322 Aerospace Structures Laboratory Spring 2024
Lab 5 Strain Gage Application and Testing rev F23
10 (y)
Once the gage installation is completed and/or after you have done testing with the specimen, write down your section and group numbers on the specimen and leave it to TA, who will store your masterpiece to be tested in the second week. (z)
Finally, be sure to wash your hands thoroughly to remove any residues of the lead solder – very important for your health! Figure 12. White ink dots painted on specimen as fiducial marks for video extensometer. Figure 13. Black electrical tape applied to enhance the performance of video extensometer.
Aer E 322 Aerospace Structures Laboratory Spring 2024
Lab 5 Strain Gage Application and Testing rev F23
11 Mechanical Tests The tasks in this part of lab involve mechanical tests of the aluminum specimen you fabricated in Week 1. The main data are load/stress and elongation/strain measured from the strain gages, video extensometer and the Instron dual-column test system. The mechanical tests consist of a bending test done on a simple stand and a tensile test done with the Instron test system. The goal is to determine the mechanical properties of the aluminum specimen. As stated above, the newest addition to our measurement modalities is the video extensometer, which has been proven effective in testing composites. It would be interesting to see its applicability to our metallic specimen and its performance against the Instron test system and strain gages. (I) Bending Test We will first test the strain gages installed on the aluminum specimen via a three-point bending test using the blue P3 strain reader made by Micro Measurements as shown in Fig. 14. (a)
Connect wires from specimen to the lead wires of the P3 strain reader using the hook clips: red to red and black to black. (b)
Verify the Wheatstone bridge configuration on the P3 strain reader. It should be a half bridge I gage-adjacent configuration (as learned from the lecture notes) with one gage measuring the strain on top side of specimen and the other measuring the bottom side. (c)
Try pulling (in tension) on the specimen by hand. Do you get any substantial change in the readout? (d)
Measure the span length of the opening of the supporting wood stand edge-to-edge. Place the specimen across the opening and keep the gage in the middle of the span. Make sure the specimen is placed on the wood stand freely with minimal pull or push by the wires in any direction. (e)
Place the two or more small flat spacers (as provided on the countertop) around the gage, at least one on each side. When the weight (also provided on the countertop) is placed on these spacers, the load would be more evenly distributed around the gage and the footprint is smaller to be closer to a point load (Fig. 15). (f)
press the Bal
button on the P3 strain reader to balance the bridge as close to zero as possible (Fig. 16a). Press MENU
on prompt for saving setting (Fig. 16b). (g)
Use the caliper to measure the vertical deflection of the specimen closest to the gage. The procedure is as follows: •
extend out the caliper’s end stick to be in contact with the countertop, •
align the bottom end of the caliper vertically against the edge of the specimen closest to gage’s horizontal position (Fig. 17a), •
zero out the caliper reading, •
set the weight on the spacers, •
realign the bottom end of caliper with the edge of the specimen (Fig. 17b),
Aer E 322 Aerospace Structures Laboratory Spring 2024
Lab 5 Strain Gage Application and Testing rev F23
12 •
record the caliper reading: the net height change would be the specimen deflection, •
record the corresponding strain reading on the P3 strain reader (after the weight is applied). (h)
Repeat steps (f)-(g) at least three times; record the deflections and strain readings each time. Remember to balance the bridge in each repeat before the weight is applied. Figure 14. The complete setup for the three-point bending test. Figure 15. Flat spacers used for even distribution of load (weight) with gage aligned the middle of span.
Your preview ends here
Eager to read complete document? Join bartleby learn and gain access to the full version
- Access to all documents
- Unlimited textbook solutions
- 24/7 expert homework help
Aer E 322 Aerospace Structures Laboratory Spring 2024
Lab 5 Strain Gage Application and Testing rev F23
13 (II) Compliance Test (for calibration) In mechanical testing of materials, the front and center task is to determine the materials’ mechanical properties such as the Young’s modulus most often through the tensile test. However, as explained on pages 24-26 in Week 6&7 lecture notes, the seemingly rock-solid Instron test system can still produce significant system errors in elongation measurements even on specimens as thin and small like our specimen plate. These system errors in this lab mainly come from Instron’s side-action grip which, due to the way it is constructed, can incur large moments. Thus, some correction must be done to calibrate the Instron test system by performing the so-called compliance test. Here the trick is to use a much thicker steel plate that acts very close to a rigid body so any elongation Figure 16. Balance the gages on P3 strain reader: (a, left) press Bal button to balance and (b, right) press MENU to exit. Figure 17. Align the bottom edge of the caliper with the edge of the specimen before (a, left) and after (b, right) the weight is applied for measuring the net height change, i.e. the specimen deflection.
Aer E 322 Aerospace Structures Laboratory Spring 2024
Lab 5 Strain Gage Application and Testing rev F23
14 measured would come from the test system itself. The complete setup of the compliance test is shown in Fig. 18. (a)
Just like the riveting lab, go find the compliance test method file in the AerE 322\method
subfolder on the desktop and double click it to start the Bluehill Universal software. (b)
In the first screen, there is a warning about being unable to communicate with the video extensometer as it is not turned on yet. Just close this warning prompt. (c)
This first screen similarly asks you to double check the travel limits. For this lab, the lower limit is the key. Since we are doing tensile test, the crosshead should not go blow this lower limit (Fig. 19). This is particularly important as we are testing a real thick plate in this compliance test. Click Ok
to continue. (d)
Lower down the Instron crosshead by using the arrow button on the control pad and fit the thick steel plate into the side-action grips. Make sure the steel plate is flushed with all three edges of both upper and lower grips. Adjust the grip face plates to line up the centerline of the steel plate with the two arrows marked on the side of grips, as shown in Fig. 20. Then firmly tighten both grips by turning the screws on the same side. (e)
As you are tightening up the steel plate, you see a large compressive load is induced. Roll the dial up to minimize this load as close to zero as possible on the tension side with about 20-50 lbs load (Fig. 21). (f)
In the second screen, enter the name of the output file as you did in riveting lab. The Output file will be in the AerE 322\strain gage compliance test output
subfolder on desktop. Also click on Balance All to zero out both the load and elongation; this shifts the origin up higher on the load vs. elongation curve. Click Before Test
to continue. (g)
The third screen shows the plotting area on the left and the data viewer window on the right. If everything looks good, click the Start
button on the lower right corner of the screen to begin the compliance test. (h)
The test is elongation based at the rate of 0.002 inch per minute and data will be sampled 10 times every second. We only load it up to 300 lbs. Once the load gets there, the Bluehill method will automatically stop the test and unload. Fig. 22 shows a complete load vs. elongation trace, most of which looks linear and the corresponding data are listed to the right. Click the endzone flag icon on the top right to terminate the test and generate the output. (i)
Bluehill software will prompt you about another sample run, answer No
to end it. (j)
Remove the steel plate and proceed with the tensile test of the thin aluminum specimen plate with the gages installed.
Aer E 322 Aerospace Structures Laboratory Spring 2024
Lab 5 Strain Gage Application and Testing rev F23
15 Figure 18. The complete setup for the compliance test. Figure 19. Lower travel limit set for the Instron crosshead as the safety measure.
Your preview ends here
Eager to read complete document? Join bartleby learn and gain access to the full version
- Access to all documents
- Unlimited textbook solutions
- 24/7 expert homework help
Aer E 322 Aerospace Structures Laboratory Spring 2024
Lab 5 Strain Gage Application and Testing rev F23
16 Figure 20. Fitting the thick steel plate specimen in Instron grips: flush all edges between the specimen and grips and align the specimen with the grip centerline marked by the alignment arrows (enclosed in red). Figure 21. Release the excessive compression load (incurred after tightening up the grips) and replace with small tension load.
Aer E 322 Aerospace Structures Laboratory Spring 2024
Lab 5 Strain Gage Application and Testing rev F23
17 (III) Tensile Test After the compliance test is done, we can proceed with the tensile test (complete setup shown in Fig. 23), in which three data sets are obtained simultaneously. First, the standard load vs. elongation data are collected from the dual-column Instron test system (right of Fig.23). At the same time, the strain changes at the gage are measured by the P3 strain reader and output to the computer (left of Fig. 23). Simultaneously the video extensometer measures the distance change between the two fiducial marks painted on the specimen and produces its own strain data (middle of Fig. 23). (a)
Like in the bending test, connecting specimen wires to the lead wires of P3 strain reader is straightforward: red to red and black to black. Here we use two external resistors in the full bridge mode on the P3 strain reader to set up a half bridge II configuration (Fig. 24) with opposite gages having like changes. Please consult the lecture notes for more details. (b)
Try bending the specimen a little bit. Do you get any substantial change in the readout compared with that of the bending test? (c)
Connecting the P3 strain reader to computer is through the USB cable. Click the P3-D4 Application
software icon on top left of the monitor desktop to start the software so that it can take control of the P3 strain reader. A simple overall control panel will appear along with a display window showing the strain reading of the channel currently active (Fig. 25). We have pre-programmed the software to only activate channel 1. Set these two P3-D4 screens on the leftmost edge of the desktop. Figure 22. Complete load vs. system elongation trace of the compliance test. The endzone flag icon is enclosed in red.
Aer E 322 Aerospace Structures Laboratory Spring 2024
Lab 5 Strain Gage Application and Testing rev F23
18 (d)
Now turn to the Instron test system. As before, find the tensile test method file in the AerE 322\method
subfolder on the desktop and start the Bluehill Universal software. Different than the compliance test, this time we also turn on the video extensometer by pushing the power button on it. Once the Bluehill screen appears, re-size it and place it on the right side of desktop to properly share the desktop space with the two P3-D4 screens. (e)
Double check the travel limits which is set the same as in compliance test. (f)
Next, follow the same process as in compliance test, fit the specimen into the side-
action grips: centerline aligned and all edges flushed (Fig. 26). (g)
Just like in the compliance test, excessive load is induced after tightening up the grips and this time the specimen plate is buckled. Roll up the “fine position” dial a few clicks to preload about 50-100lbs tension load to make the specimen straight and tight with minimal wiggle room in the middle of specimen around the gage (Fig. 26). (h)
To later convert the elongation into strain, we need to obtain the gage length between the edges of top and bottom grips
. The face plate of the grip is 2 inches long each and the aluminum specimen is 8 inches long, so 4 inches gage length would be an accurate guess. Still you should measure it using caliper. (i)
On the second Bluehill screen, enter the name of data output file like before. The output file is similarly in the csv format containing the time, elongation, load, plus the video extensometer data. The default location is AerE 322\strain gage tensile test output
subfolder on desktop. (j)
We also need to set the name and location for the strain gage data output file. This is done by clicking on the Select File
button on the rightmost of the overall P3-D4 control panel (enclosed in red in Fig. 25). Then follow the standard Windows operation to enter the name for strain gage output file. You should set the file location same as the Instron output file to AerE 322\strain gage tensile test output subfolder on desktop. (k)
The third Bluehill screen has two graphic displays on the left, a real-time image of the two fiducial marks as seen by the video extensometer in the middle and a data viewer window on the right (Fig. 27). On the video strain image, you should see a green line box encloses the two fiducial marks and if the two fiducial marks can be automatically detected by the video extensometer, each fiducial mark will be enclosed by a small red line box (Fig. 28a). Click on the L-shape ruler icon (last one to the right of the image) to confirm this detection and the value of the axial gage length will show up in a few seconds (Fig. 28b). (l)
Click Balance All
to zero out the elongation, load and video strain. (m)
To balance the strain gage in the P3-D4 software, first toggle off Real Time Display
under Hardware
menu. This will enable the setting
under the Channels
menu. Click into the setting control panel, review to see if the settings are all correct. Then click Zero
button near the bottom left and click Ok
to exit the setting control panel. Once the Real Time Display
is toggled on again, you will see the strain of Channel 1 updated to zero or near zero. Fig. 29 illustrates this sequence of actions.
Your preview ends here
Eager to read complete document? Join bartleby learn and gain access to the full version
- Access to all documents
- Unlimited textbook solutions
- 24/7 expert homework help
Aer E 322 Aerospace Structures Laboratory Spring 2024
Lab 5 Strain Gage Application and Testing rev F23
19 (n)
If everything is ready at this point, first click Record
button in the P3-D4 overall control panel to start taking strain gage measurements, then right away click the Start
button on Bluehill screen to start the tensile test (Fig. 30). The top graph will plot the load vs. elongation data as measured by Intron test system, the bottom graph will plot the strain measured by the video extensometer vs. the stress calculated based on the load data and the default cross sectional area of the specimen. Just like the compliance test, the tensile test will automatically stop and unloads once 300 lbs load is reached. Then you should immediately click the Close Capture
button in P3-D4 panel to stop the strain gage measurements and generate the strain gage output. The lower graph in the Bluehill screen should have plotted the complete trace of estimated stress vs. video strain. The data are noisy but the trend is nevertheless positively correlated. If the scales of the two graphs in Bluehill screen are off, click on the cross-arrow buttons on top of the graphs to rescale them. Finally, click on the endzone flag icon in Bluehill screen to end the tensile test and to produce the Instron output file. Fig. 31 illustrates this sequence of actions and the end results of Instron measurements. (o)
As before, Bluehill software will prompt for another run, just click No to end it. Also select Exit under the File menu in P3-D4 panel to end the P3-D4 software. Figure 23. The complete setup for the tensile test.
Aer E 322 Aerospace Structures Laboratory Spring 2024
Lab 5 Strain Gage Application and Testing rev F23
20 Figure 24. P3 strain reader setup for tensile test: two external resistors used in the full bridge mode for a half bridge II configuration (see lecture notes for details). Figure 25. The displays of P3-D4 Application software: overall control panel on top and active channel strain output on bottom. The Select File
button (enclosed in red) is to be clicked on to set name and location of strain gage output file.
Aer E 322 Aerospace Structures Laboratory Spring 2024
Lab 5 Strain Gage Application and Testing rev F23
21 Figure 26. Properly fit the aluminum specimen into the grips and preload it with tension load to remove looseness in specimen. Figure 27. The third Bluehill screen showing the output graphs on left, the image of fiducial marks (enclosed by green and red line boxes) for video extensometer in middle and a data viewer on right.
Your preview ends here
Eager to read complete document? Join bartleby learn and gain access to the full version
- Access to all documents
- Unlimited textbook solutions
- 24/7 expert homework help
Aer E 322 Aerospace Structures Laboratory Spring 2024
Lab 5 Strain Gage Application and Testing rev F23
22 Figure 28. The identifications of the fiducial marks (enclosed by green and red line boxes) for video extensometer (a, left) and the corresponding gage length (b, right) in Bluehill software. Figure 29. illustrations showing how to balance the gages in P3-D4 software.
Your preview ends here
Eager to read complete document? Join bartleby learn and gain access to the full version
- Access to all documents
- Unlimited textbook solutions
- 24/7 expert homework help
Aer E 322 Aerospace Structures Laboratory Spring 2024
Lab 5 Strain Gage Application and Testing rev F23
23 Figure 30. Sequence to start the tensile test. Figure 31. End results of Instron measurements and sequence of action to end the tensile test.
Your preview ends here
Eager to read complete document? Join bartleby learn and gain access to the full version
- Access to all documents
- Unlimited textbook solutions
- 24/7 expert homework help
Aer E 322 Aerospace Structures Laboratory Spring 2024
Lab 5 Strain Gage Application and Testing rev F23
24 3. After Lab You have now obtained the three output files containing the compliance test, strain gage and tensile test measurements. Examine these files to confirm the following: the output data file of the compliance test is in csv format and has three columns: first is time, second elongation and third load. It can be seen that the elongation rate is quite accurate. The tensile test, also in csv format, is load based at the rate of 10 lbs per second. This rate is also accurate so the whole test will last very close to 30 seconds. On the other hand, the strain gage output file is in ASCII format containing the actual time stamp in first column and the gage strain in second column in microstrain. The strain gage is sampled every 0.5 second. Your group then proceeds with the following after-lab work to determine the Young’s modulus from each of three data sets. The percentage allocated in each part reflects the importance of that part in the Analysis section which you will prepare for the lab report. (i)
(10%) In bending test step (c), explain why were (or weren’t) you able to get any substantial change in the readout when pulling the specimen. Can you come up with a theoretical support? Hint: like in Week 6&7
lecture, apply the Wheatstone bridge equation (page 5) to a half bridge I configuration (page 8) but with like changes, i.e. both gages having positive increase in resistance. Work out the derivation. (ii)
(10%) In tensile test step (b), explain why were (or weren’t) you able to get any substantial change in the readout when bending the specimen. How is the scale of change here in comparison with that of (i) above? Can you come up with a theoretical support? Hint: similar to (i), work out the results for half bridge II configuration (page 10 of lecture notes) but with opposite changes. That little theorem called binomial theorem (page 6) would be useful here. Compare this result with that from (i).
(iii)
(15%) For the three-point bending test, can you work out a theoretical prediction for the strain and see if it agrees with the experimental data you obtained in lab? Note that the readouts you obtained from the P3 strain reader directly correspond to the strain
, equal to the left-hand side of the Wheatstone bridge equation divided by (
β
GF), i.e. (V/E)/(
β
GF)=
ε
(see also Week 6&7 lecture page 15). These readouts are in microstrain, i.e. a reading of 1000 is actually 1000x10
-6
. Hint: Let us treat the thin aluminum specimen plate as a beam. The maximum vertical deflection in a three-point beam bending with central loading is given by y
max
=PL
3
/(48EI), which occurs right in the middle span where load P is applied and the gages are located. Draw yourself a free-body diagram for the middle span and determine the bending moment M there. Then derive an expression relating y
max
to strain ε
(recall σ
=My/I and σ
=E
ε
). The opening of the wood plate is about 13cm long that you have measured in lab
, which would be your length L. Also recall the thickness of the specimen is 0.025 inch. Remember: do not rush to crank out the numbers on your calculator or PC right away – wait until you derive the final expression.
(iv)
(10%) For the data you obtained from the compliance test, first plot the system elongation (as vertical axis) vs. the load (as horizontal axis). As described on page 26
Your preview ends here
Eager to read complete document? Join bartleby learn and gain access to the full version
- Access to all documents
- Unlimited textbook solutions
- 24/7 expert homework help
Aer E 322 Aerospace Structures Laboratory Spring 2024
Lab 5 Strain Gage Application and Testing rev F23
25 of lecture notes, from this compliance test data, you can build a look-up line or curve for the system error of elongation (Lg in lecture notes) as a function of load by applying what you have learned in Lab 1. As seen in Fig. 22, the overall data is not quite linear, so instead you may want to fit with polynomial curve, as lecture notes suggested. (v)
(5%) Using either model obtained from (iv), you can compute the system elongation error for any given load for tensile test done in the same load range. Correct the elongation data in your aluminum plate data by subtracting these system elongation errors from them. (vi)
(10%) Convert the corrected elongation data from step (v) into average strain (in microstrain) by dividing the corrected elongation by the gage length that you have measured in step (h) in tensile test. Then convert the load data into stress. Remember the specimen width is 2” and thickness is 0.025”. Plot the strain vs. stress and fit a straight line to the data. Then determine its slope as the Young’s modulus. (vii)
(15%) Next, work on the video extensometer data by first plotting the stress vs. video extensometer strain. Since the video extensometer data were sampled at the same rate, you can simply reuse the stress data obtained from (vi). Are you bothered by the fact that the video extensometer data are pretty noisy? Given this, you may want to smooth them out by applying say the running average you learned back in Lab 1. Then go ahead to fit a line to the curved stress-strain data anyway and determine the slope for the Young’s modulus. Do again by skipping the first one third of data and again by using the top one third of data. Any difference between these three lines and the corresponding slopes? (viii)
(10%) Next, work on the strain gage data. First please note that, since we used full bridge mode to set up half bridge II in P3 strain reader for the tensile test, all the strain gage data in the strain gage output file need to be divided by 2
. To align the strain gage data with the Instron data is rather easy: the load will reach the maximum at 300 lbs and unload right after. So is the strain gage data. You just need to find the maximal gage reading and count 30 seconds back to locate the start of the loading and the corresponding initial gage reading. Since the loading rate is accurate at 10 lbs per second as stated above, you can just “reinvent” the load data every 0.5 second alongside the strain gage data. Got it?! Convert the load data into stress and plot the gage strain vs. stress, fit a line to the data and obtain the Young’s modulus from it. (ix)
(5%) Compare the three Young’s moduli from (vi) - (viii) and validate them with the nominal literature values (73.1 GPa or 10600 ksi). (x)
(10%) Now you are coming to the end of your analyses, have you figured out how did these three data sets come to be? What are your assessments about the pros and cons of the corresponding techniques that generated these data sets?
Your preview ends here
Eager to read complete document? Join bartleby learn and gain access to the full version
- Access to all documents
- Unlimited textbook solutions
- 24/7 expert homework help
Aer E 322 Aerospace Structures Laboratory Spring 2024
Lab 5 Strain Gage Application and Testing rev F23
26 4. Report Please write a formal full report with all necessary sections. Particularly include the after-lab hard work you just accomplished above in the Analysis section.
Your preview ends here
Eager to read complete document? Join bartleby learn and gain access to the full version
- Access to all documents
- Unlimited textbook solutions
- 24/7 expert homework help
Related Documents
Related Questions
Can someone please help me to correctly solve all the following parts of this question. Thank you!
arrow_forward
Figure 1 shows the tensile testing results for different materials. All specimens have an initial
diameter of 12 mm and an initial gauge length of 50 mm.
300
250
Low carbon steel
Network polymer
200
Crystalline polymer
150
Amorphous polymer
100
50
5
10
15
20
25
30
Strain (%)
Figure 1: Stress-strain curve
b. Determine the following parameters for each material:
• the tensile strength
the 0.2% offset yield strength
the modulus of elasticity
• the ductility
Stress (MPa)
LO
arrow_forward
Problem 1: (50 points)
In Avengers 2, Captain America's improved
shield is made from unobtainium, a new
material that will soon be available in a store
near you. Unobtainium has the normal stress-
strain diagram shown. The proportional limit,
the elastic limit and the yield point are
identical in this material.
o [MPa]
2001
175
150
125
100
Fig.1 Normal stress-strain
75
50
25
0
0. 0.05 0.1 0.15 0.2 0.25
Unobtainium has a Poisson's ratio of 0.3.
a. [6pts] Identify the yield point oy, the ultimate stress ou and the fracture
stress of. Include units.
c. [25pts] A bar of unobtainium has a length of
1.5 m, a width of 100mm and a height of 50
mm, as shown. The cross-sectional area is
50mm 100mm = 5 x 10-³m². The bar is
subjected to an axial force of 375 kN.
Find the normal stress in a cross-section of the bar.
b. [5pts] How do you find Young's modulus from this graph? Find its value with units.
whesta fins dus al hoss
P = 375 KN
1.5 m
0.3
50 mm
100 mm
& [mm/mm]
Is the material within its…
arrow_forward
Which of these statements are correct?
arrow_forward
The nuchal ligament in a horse supports the weight of the horse’s head. This ligament is much more elastic than a typical ligament, stretching from 15% to 45% longer than its resting length as a horse’s head moves up and down while it runs. This stretch of the ligament stores energy, making locomotion more efficient. Measurements on a segment of ligament show a linear stress-versusstrain relationship until the stress approaches 0.80. Smoothed data for the stretch are shown.
The volume of the ligament stays the same as it stretches, so the cross-section area decreases as the length increases. Given this, how would a force F versus change in length ΔL curve appear?
arrow_forward
explain the strain here? include the minimum and the max .
arrow_forward
The following data were collected from a 12 mm diameter test specimen of Magnesium.
LOAD (N)
GAUEGE LENGTH (mm)
0
5000
10000
15000
20000
25000
26500
27000
26500
30.000
25000
30.0296
30.0592
30.0888
30.15
30.51
30.90
31.50 (maximum load)
32.10
32.79 (fracture)
After the fracture, the gauge length is 32.61 mm and the diameter is 11.74 mm.
a) What is the elastic modulus?
b) Percent elongation at fracture?
c) Percent elongation after fracture?
d) What is the Poisson's ratio?
e)Draw the engineering stress-strain diagram corresponding to the values in the table. Call this plot I. Now consider this experiment is repeated at a higher
temperature with an identical sample. Draw the new engineering stress-strain diagram, call it plot II and highlight the differences (on the same graph) between
I and II.
arrow_forward
Please show work for practice problem 12
arrow_forward
1. A tensile test was conducted on a metal "505" specimen and the following stress-strain curves
were generated, both curves generated from the same set of data. Use the graphs to fill in the
mechanical properties of the material tested in the box below. Don't forget units!
Stress vs Strain
Stress, psi
Stress, psi
80000
70000
60000
50000
40000
30000
20000
10000
0
0.00
80000
70000
60000
50000
40000
30000
20000
10000
0.02
0
0.000 0.002
0.04
0.004
0.06
0.006
0.08
0.10
Strain
Stress vs Strain
0.008
0.12
Elastic Modulus, E:
0.2% Offset Yield Strength, oo:
Tensile Strength, ou:
Breaking Strength, of:
% Elongation:
0.14
0.010 0.012 0.014
Strain
0.16
0.18
0.016 0.018
0.20
0.020
arrow_forward
Q19 and Q20
arrow_forward
6. State your answers to the following questions.Strain Gauge represents the deformation of a material through a change in resistance. If so, explain how temperature will affect the strain gauge in the experimental environment.①:In this experiment, the Strain Gauge measures the strain in micro units. Explain one possible error factor when applying a load by hanging a weight on the material with the strain gauge attached. (Hint: It is easy to shake by hanging the weight using a thread)①:
arrow_forward
3. A strip of chicken skin was excised for mechanical testing in tension. The initial
dimension of the rectangular specimen was 30 mm long and 15 mm wide, with
average thickness of 3 mm. The mechanical testing was conducted at a rate of 5
mm/sec. The following data were obtained:
gauge length, mm
20
22
24.2
26.3
27.9
30.1
force, N
0
0.8
2.7
7.9
12.9
19.6
a. Calculate the engineering stresses and strain from the information given and
plot the stress-strain curve. Assume that 5 mm of the specimen length is
clamped by the testing grip at each end, such that the initial gauge length of
the specimen is 20 mm.
arrow_forward
please solve part b, this is past paper and just iam studying, mechanical engineering
arrow_forward
Is answer 0.1111?
I am just asking ,Not sure.
Looking for someone who is 100% sure.
arrow_forward
30. In a typical tension test a dog-bone
shaped specimen is pulled in a
machine. During the test, the force F
needed to pull the specimen and the
length L of a gauge section are measured. This data is used for plotting a
stress-strain diagram of the material. Two definitions, engineering and true,
exist for stress and strain. The engineering stress
F
de
and strain
e are
defined by oe
F
%3D
and
A0
L-Lo where Lo and Ao are the initial gauge
6, =
Lo
length and the initial cross-sectional area of the specimen, respectively. The
true stress o, and strain e are defined by o,
는는 and q
%3D
= In
A0 Lo
The following are measurements of force and gauge length from a ten-
sion test with an aluminum specimen. The specimen has a round cross sec-
tion with a radius of 0.25 in. (before the test). The initial gauge length is 0.5
in. Use the data to calculate and generate the engineering and true stress-
strain curves, both on the same plot. Label the axes and use a legend to
identify the curves.
Units:…
arrow_forward
SEE MORE QUESTIONS
Recommended textbooks for you
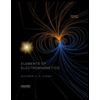
Elements Of Electromagnetics
Mechanical Engineering
ISBN:9780190698614
Author:Sadiku, Matthew N. O.
Publisher:Oxford University Press
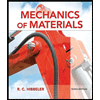
Mechanics of Materials (10th Edition)
Mechanical Engineering
ISBN:9780134319650
Author:Russell C. Hibbeler
Publisher:PEARSON
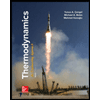
Thermodynamics: An Engineering Approach
Mechanical Engineering
ISBN:9781259822674
Author:Yunus A. Cengel Dr., Michael A. Boles
Publisher:McGraw-Hill Education
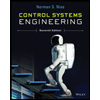
Control Systems Engineering
Mechanical Engineering
ISBN:9781118170519
Author:Norman S. Nise
Publisher:WILEY
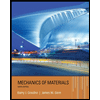
Mechanics of Materials (MindTap Course List)
Mechanical Engineering
ISBN:9781337093347
Author:Barry J. Goodno, James M. Gere
Publisher:Cengage Learning
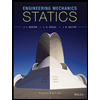
Engineering Mechanics: Statics
Mechanical Engineering
ISBN:9781118807330
Author:James L. Meriam, L. G. Kraige, J. N. Bolton
Publisher:WILEY
Related Questions
- Can someone please help me to correctly solve all the following parts of this question. Thank you!arrow_forwardFigure 1 shows the tensile testing results for different materials. All specimens have an initial diameter of 12 mm and an initial gauge length of 50 mm. 300 250 Low carbon steel Network polymer 200 Crystalline polymer 150 Amorphous polymer 100 50 5 10 15 20 25 30 Strain (%) Figure 1: Stress-strain curve b. Determine the following parameters for each material: • the tensile strength the 0.2% offset yield strength the modulus of elasticity • the ductility Stress (MPa) LOarrow_forwardProblem 1: (50 points) In Avengers 2, Captain America's improved shield is made from unobtainium, a new material that will soon be available in a store near you. Unobtainium has the normal stress- strain diagram shown. The proportional limit, the elastic limit and the yield point are identical in this material. o [MPa] 2001 175 150 125 100 Fig.1 Normal stress-strain 75 50 25 0 0. 0.05 0.1 0.15 0.2 0.25 Unobtainium has a Poisson's ratio of 0.3. a. [6pts] Identify the yield point oy, the ultimate stress ou and the fracture stress of. Include units. c. [25pts] A bar of unobtainium has a length of 1.5 m, a width of 100mm and a height of 50 mm, as shown. The cross-sectional area is 50mm 100mm = 5 x 10-³m². The bar is subjected to an axial force of 375 kN. Find the normal stress in a cross-section of the bar. b. [5pts] How do you find Young's modulus from this graph? Find its value with units. whesta fins dus al hoss P = 375 KN 1.5 m 0.3 50 mm 100 mm & [mm/mm] Is the material within its…arrow_forward
- Which of these statements are correct?arrow_forwardThe nuchal ligament in a horse supports the weight of the horse’s head. This ligament is much more elastic than a typical ligament, stretching from 15% to 45% longer than its resting length as a horse’s head moves up and down while it runs. This stretch of the ligament stores energy, making locomotion more efficient. Measurements on a segment of ligament show a linear stress-versusstrain relationship until the stress approaches 0.80. Smoothed data for the stretch are shown. The volume of the ligament stays the same as it stretches, so the cross-section area decreases as the length increases. Given this, how would a force F versus change in length ΔL curve appear?arrow_forwardexplain the strain here? include the minimum and the max .arrow_forward
- The following data were collected from a 12 mm diameter test specimen of Magnesium. LOAD (N) GAUEGE LENGTH (mm) 0 5000 10000 15000 20000 25000 26500 27000 26500 30.000 25000 30.0296 30.0592 30.0888 30.15 30.51 30.90 31.50 (maximum load) 32.10 32.79 (fracture) After the fracture, the gauge length is 32.61 mm and the diameter is 11.74 mm. a) What is the elastic modulus? b) Percent elongation at fracture? c) Percent elongation after fracture? d) What is the Poisson's ratio? e)Draw the engineering stress-strain diagram corresponding to the values in the table. Call this plot I. Now consider this experiment is repeated at a higher temperature with an identical sample. Draw the new engineering stress-strain diagram, call it plot II and highlight the differences (on the same graph) between I and II.arrow_forwardPlease show work for practice problem 12arrow_forward1. A tensile test was conducted on a metal "505" specimen and the following stress-strain curves were generated, both curves generated from the same set of data. Use the graphs to fill in the mechanical properties of the material tested in the box below. Don't forget units! Stress vs Strain Stress, psi Stress, psi 80000 70000 60000 50000 40000 30000 20000 10000 0 0.00 80000 70000 60000 50000 40000 30000 20000 10000 0.02 0 0.000 0.002 0.04 0.004 0.06 0.006 0.08 0.10 Strain Stress vs Strain 0.008 0.12 Elastic Modulus, E: 0.2% Offset Yield Strength, oo: Tensile Strength, ou: Breaking Strength, of: % Elongation: 0.14 0.010 0.012 0.014 Strain 0.16 0.18 0.016 0.018 0.20 0.020arrow_forward
- Q19 and Q20arrow_forward6. State your answers to the following questions.Strain Gauge represents the deformation of a material through a change in resistance. If so, explain how temperature will affect the strain gauge in the experimental environment.①:In this experiment, the Strain Gauge measures the strain in micro units. Explain one possible error factor when applying a load by hanging a weight on the material with the strain gauge attached. (Hint: It is easy to shake by hanging the weight using a thread)①:arrow_forward3. A strip of chicken skin was excised for mechanical testing in tension. The initial dimension of the rectangular specimen was 30 mm long and 15 mm wide, with average thickness of 3 mm. The mechanical testing was conducted at a rate of 5 mm/sec. The following data were obtained: gauge length, mm 20 22 24.2 26.3 27.9 30.1 force, N 0 0.8 2.7 7.9 12.9 19.6 a. Calculate the engineering stresses and strain from the information given and plot the stress-strain curve. Assume that 5 mm of the specimen length is clamped by the testing grip at each end, such that the initial gauge length of the specimen is 20 mm.arrow_forward
arrow_back_ios
SEE MORE QUESTIONS
arrow_forward_ios
Recommended textbooks for you
- Elements Of ElectromagneticsMechanical EngineeringISBN:9780190698614Author:Sadiku, Matthew N. O.Publisher:Oxford University PressMechanics of Materials (10th Edition)Mechanical EngineeringISBN:9780134319650Author:Russell C. HibbelerPublisher:PEARSONThermodynamics: An Engineering ApproachMechanical EngineeringISBN:9781259822674Author:Yunus A. Cengel Dr., Michael A. BolesPublisher:McGraw-Hill Education
- Control Systems EngineeringMechanical EngineeringISBN:9781118170519Author:Norman S. NisePublisher:WILEYMechanics of Materials (MindTap Course List)Mechanical EngineeringISBN:9781337093347Author:Barry J. Goodno, James M. GerePublisher:Cengage LearningEngineering Mechanics: StaticsMechanical EngineeringISBN:9781118807330Author:James L. Meriam, L. G. Kraige, J. N. BoltonPublisher:WILEY
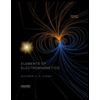
Elements Of Electromagnetics
Mechanical Engineering
ISBN:9780190698614
Author:Sadiku, Matthew N. O.
Publisher:Oxford University Press
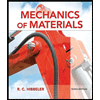
Mechanics of Materials (10th Edition)
Mechanical Engineering
ISBN:9780134319650
Author:Russell C. Hibbeler
Publisher:PEARSON
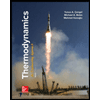
Thermodynamics: An Engineering Approach
Mechanical Engineering
ISBN:9781259822674
Author:Yunus A. Cengel Dr., Michael A. Boles
Publisher:McGraw-Hill Education
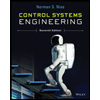
Control Systems Engineering
Mechanical Engineering
ISBN:9781118170519
Author:Norman S. Nise
Publisher:WILEY
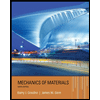
Mechanics of Materials (MindTap Course List)
Mechanical Engineering
ISBN:9781337093347
Author:Barry J. Goodno, James M. Gere
Publisher:Cengage Learning
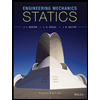
Engineering Mechanics: Statics
Mechanical Engineering
ISBN:9781118807330
Author:James L. Meriam, L. G. Kraige, J. N. Bolton
Publisher:WILEY