ENGR 244 Lab 4
docx
keyboard_arrow_up
School
Concordia University *
*We aren’t endorsed by this school
Course
244
Subject
Mechanical Engineering
Date
Dec 6, 2023
Type
docx
Pages
9
Uploaded by AgentSnail2002
Lab 4:
Stress Analysis of Beams Using Strain Gauges
Lab Section CI – X
Winter 2022
Professor Ahmed Soliman
Concordia University
Montreal, QC, Canada
Tuesday February 15
th
, 2022
Table of Contents
Nomenclature pg 3
List of Tables pg 3
List of Figures pg 3
Objective pg 4
Introduction pg 4
Procedure pg 4
Results pg 4-7
Discussion and Conclusion pg 8-9
References pg 10
Original Data pg 11
Nomenclature
σ = bending stress
ε = strain
δ
ε
L
= change in longitudinal strain
δ
ε
T
= change in transverse strain
δP = change in applied load
ν = Poisson’s ratio
b = base
E = elastic modulus
G = shear modulus
h = height
I = moment of inertia
M = moment caused by the applied load
y = distance from the neutral axis
List of Tables
Table 1: Strain Indicator reading units are in micro-strain (10
-6
strain)
p. 4
Table 2: Bending Stress at each gauge point in MPa
p. 6
Table 3: Stress Values for Each Channel Using the Theoretical Elastic Modulus for Steel
p. 7
List of Figures
Figure 1: Stress vs Strain for gauge channels 1 and 5 (Absolute Values)
p. 6
Figure 2: Longitudinal Strain (Channel 5) and Transverse Strain (Channel 6) vs Applied Load
(Absolute Values)
p. 6
Figure 3: Strain vs Distance from the Horizontal Mid-Plane for the 5060N Load
p. 7
Objective:
The objective of this lab is to compare the practical values of the stress and strain
distribution with their theoretical values. The elastic modulus, Poisson's ratio and the shear modulus
will also be calculated using these measurements.
Introduction:
Bending is a common English word and a term that everyone understands, but
what isn’t always known is that bending occurs when the forces applied to the material causes both
compressive and tensile stresses over different surfaces [ CITATION Con \l 4105 ]. While bending
generally includes many different types of stresses, we will only be looking at bending stress to
simplify things a little. This can also be referred to as pure bending, which is bending in the beam when
shear force is absent [ CITATION SRa22 \l 4105 ]. Pure bending can be achieved applying two couples
to each end of a rod, acting in opposite directions [ CITATION SRa22 \l 4105 ]. Through observation,
we can say that bending strain is proportional to the distance of the force applied to the neutral axis of
the material [ CITATION Con \l 4105 ]. The neutral axis, also referred to as the neutral surface, is the
plane of the object that experiences bending, but does not experience extension or contraction
[ CITATION Dep00 \l 4105 ]. Stating the obvious, it can be said that bending takes place in the
direction of the force that is placed uniaxially. What isn’t as obvious, but has been studied, is that the
material is also either expanded or contracted while being bent depending on whether the stress applied
is tensile or compressive [ CITATION Con \l 4105 ]. Using this expansion or contraction, Poisson’s
ratio can be figured out which is the constant that relates lateral strain and axial strain [ CITATION Con
\l 4105 ]. Since structural design must consider all dimensional changes, it is an important constant to
know how different surfaces will react to different forces applied [ CITATION Con \l 4105 ].
Procedure:
First, measure the cross section of the bar and record the values of the height and
width. A sketch of the bar with the strain gauges should be made and labelled with their number. Make
sure no load is applied and then check that the center line is the axis of symmetry for the support
beams. Verify that each gauge has a value of 0 (+/- 2) while there is no load applied and adjust it if
needed. Now apply a load of 1000N and record the strain measurements of each gauge. Continue doing
this, in increments of 1000N, until you reach 5000N. Remove the total load and record the values of the
strain once more for verification of calibration.
Results:
Applied Load, P(N)
Channel 1
Channel 2
Channel 3
Channel 4
Channel 5
Channel 6
Your preview ends here
Eager to read complete document? Join bartleby learn and gain access to the full version
- Access to all documents
- Unlimited textbook solutions
- 24/7 expert homework help
1012
-162
-110
-18
83
152
-50
1999
-309
-206
-25
181
306
-93
3003
-476
-309
-30
283
462
-135
4035
-639
-413
-34
391
631
-181
5060
-806
-516
-34
498
794
-225
Unload
4
-2
-5
-2
0
0
Table 1: Strain Indicator reading units are in micro-strain (10
-6
strain)
Sample Calculations
Formulas used:
I = bh
3
/12,
σ = My/I, E = σ/ε,
ν = |(δ
ε
T
/δP)/(δ
ε
L
/δP)|,
σ = Eε
and
G
= E/[2(1+ν)]
I = bh
3
/12
I = (0.01897m)(0.03184m)
3
/12 = 51.0276 x10
-9
m
4
FBD Diagram:
Shear Diagram:
Moment Diagram:
σ
1
= My/I
σ
1
= (1012N)(0.0701m)(-0.03184m/2)/(51.0276 x10
-9
m
4
) = -11.0664 MPa
(compression)
σ
2
= My/I
σ
2
= (1012N)(0.0701m)(-0.0101m)/(51.0276 x10
-9
m
4
) = -7.0208 MPa
σ
3
= My/I
σ
3
= (1012N)(0.0701m)(0m)/(51.0276 x10
-9
m
4
) = 0
σ
4
= My/I
σ
4
= (1012N)(0.0701m)(0.0101m)/(51.0276 x10
-9
m
4
) = 7.0208 MPa
(Tension)
σ
5
= My/I
σ
5
= (1012N)(0.0701m)(0.03184m/2)/(51.0276 x10
-9
m
4
) = 11.0664 MPa
σ
6
= My/I
σ
6
= (1012N)(0.0701m)(0.03184m/2)/(51.0276 x10
-9
m
4
) = 11.0664 MPa
Applied Load (N)
Stress 1
Stress 2
Stress 3
Stress 4
Stress 5
Stress 6
1012
-22.1328
-14.0415
0
14.0415
22.1328
22.1328
1999
-43.7189
-27.7362
0
27.7362
43.7189
43.7189
3003
-65.6767
-41.6667
0
41.6667
65.6767
65.6767
4035
-88.2469
-55.9858
0
55.9858
88.2469
88.2469
5060
-110.6640
-70.2077
0
70.2077
110.6640
110.6640
Table 2: Bending Stress at each gauge point in MPa
0
100
200
300
400
500
600
700
800
900
0
20
40
60
80
100
120
Stress vs Strain of Channels 1 and 5
Gauge 1
Linear (Gauge 1)
Gauge 5
Linear (Gauge 5)
Linear (Gauge 5)
MicroStrain
Stress (MPa)
Figure 4: Stress vs Strain for gauge channels 1 and 5 (Absolute Values)
E = (σ
2 –
σ
1)
/(ε
2
- ε
1
)
E = (110.6640MPa – 22.1328MPa)/(806x10
-6
-162 x10
-6
) = 137.4708GPa
0
1000
2000
3000
4000
5000
6000
0
100
200
300
400
500
600
700
800
900
f(x) = 0.16 x − 5.22
f(x) = 0.04 x + 2.95
Longitudinal and Transverse Strain vs Applied Load
Transverse Strain
Linear (Transverse Strain)
Longitudinal Strain
Linear (Longitudinal Strain)
Applied Load (N)
MicroStrain
Figure 5: Longitudinal Strain (Channel 5) and Transverse Strain (Channel 6) vs Applied Load (Absolute Values)
δ
ε
L
/δP = (794-152)/(5060-1012) = 0.1586N
-1
and
δ
ε
T
/δP = (-225 – (-50))/(5060-1012) = -0.04323N
-1
ν = |(δ
ε
T
/δP)/(δ
ε
L
/δP)|
ν = |(-0.04323N
-1
)/(0.1586N
-1
)| = 0.2726
σ = Eε where E = 200GPa
σ = (200 x10
9
Pa)(-162 x10
-6
Pa) = -32.4 MPa
(compression)
Load (N)
Stress 1 (MPa)
Stress 2 (MPa)
Stress 3 (MPa)
Stress 4 (MPa)
Stress 5 (MPa)
Stress 6 (MPa)
1012
-32.4
-22.0
-3.6
16.6
30.4
-10.0
1999
-61.8
-41.2
-5.0
36.2
61.2
-18.6
3003
-95.2
-61.8
-6.0
56.6
92.4
-27.0
4035
-127.8
-82.6
-6.8
78.2
126.2
-36.2
5060
-161.2
-103.2
-6.8
99.6
158.8
-45.0
Table 3: Stress Values for Each Channel Using the Theoretical Elastic Modulus for Steel
G = E/[2(1+ν)]
G = (137.4708GPa)/[2(1+0.2726)] = 54.0118 GPa
This value is close to the theoretical G value of 77 GPa.
Your preview ends here
Eager to read complete document? Join bartleby learn and gain access to the full version
- Access to all documents
- Unlimited textbook solutions
- 24/7 expert homework help
-20
-15
-10
-5
0
5
10
15
20
-1000
-800
-600
-400
-200
0
200
400
600
800
1000
f(x) = 50.24 x − 12.8
R² = 1
Channel Strains at 5060N vs Distance from Horizontal Mid-Plane
Distance (mm)
MicroStrain
Figure 6: Strain vs Distance from the Horizontal Mid-Plane for the 5060N Load
The experimental value of neutral axis can be determined using the equation of the slope in figure 3. By making
y = 0 we find that x is 0.2548mm instead of the theoretical 0mm for pure bending, but the difference is small
enough to compare the theoretical and experimental values together.
Discussion and conclusion:
If we look at figure 3, we can see that the experimental value for
the neutral axis is not exactly where it should be in theory, but it is close enough to the theoretical value
to say that the neutral axis experiences little to no elongation or contraction. The small discrepancies in
values can be caused by many sources, such as: rust, the loads being applied at a slight angle,
temperature, non uniform material, uncalibrated strain indicator, non constant load, and damaged
material.
Some of these sources can account for differences in the experimental vs theoretical stresses.
Our experimental E value calculated with the experimental stress was considerably lower than the
theoretical value which might be due to the difference in height and width of the beam, and load
distance or angle from the center axis. The experimental negative and positive values for channels 1
through 5 were in conformity with the theoretical values, meaning that we had tensile and compressive
loads on the correct sides of the horizontal mid-plane as expected. The only exception was for channel
6 which was experimentally calculated as tension (positive), but the theoretical value shows that it is in
compression (negative). This is likely because the experimental values were calculated using the
distance from the horizontal mid-plane instead of the vertical plane. The transverse strain acts
perpendicular to the longitudinal strain and therefore should be calculated using the vertical mid-plane.
It is also known that if a surface experiences longitudinal elongation, then the transverse direction will
experience contraction [ CITATION Tre22 \l 4105 ]. Since both channels 5 and 6 are on the same
surface, they should have opposite signs and so we know the theoretical value for the stress in channel
6 is correct since it is in compression.
In conclusion, we were able to find stress and strain values that, while imperfect, were
comparable to the theoretical values. The relationships between the experimental stress and strain
values, the elastic modulus, the shear modulus, and Poisson’s ratio were all were as expected even if
the values weren’t correct. Despite the many possible sources of error, the experiment was a success to
demonstrate these relationships.
References
[1] C. U. E. a. C. Science, ENGR 244 Mechanics of Materials Lab Manual, Montreal: Concordia University.
[2] S. R. Kumar, "ecourses online," e-Krishi Shiksha, [Online]. Available:
http://ecoursesonline.iasri.res.in/mod/page/view.php?id=3662. [Accessed 27 02 2022].
[3] Department of Engineering Mechanics, University of Nebraska, Lincoln, NE 68588-0526, Mehrdad
Negahban and the University of Nebraska, 2000. [Online]. Available:
http://emweb.unl.edu/NEGAHBAN/Em325/11-Bending/Bending.htm. [Accessed 27 02 2022].
[4] Trenchlesspedia, "Trenchlesspedia," [Online]. Available:
https://www.trenchlesspedia.com/definition/4246/transverse-strain-tensile-force. [Accessed 27 02 2022].
Your preview ends here
Eager to read complete document? Join bartleby learn and gain access to the full version
- Access to all documents
- Unlimited textbook solutions
- 24/7 expert homework help
Related Documents
Related Questions
Which of these statements are correct?
arrow_forward
Can someone please help me to correctly solve all the following parts of this question. Thank you!
arrow_forward
explain the strain here? include the minimum and the max .
arrow_forward
Hi can you please help me with the attached question?
arrow_forward
A metallic strain gauge produces an electrical resistance change when subjected to
mechanical strain. However, engineers don't measure this voltage drop directly using
a voltmeter. Why don't we directly measure the voltage drop across the strain gauge,
and instead, use a Wheatstone Bridge?
Damgraph
>
arrow_forward
Please show work for practice problem 12
arrow_forward
The engineering constants for an orthotropic material are found to be
E1= 27.579 GPa V12 = 0.2 G12=41.368 GPa
E2=20.684 GPa V23 = 0.4 G23=48.263 GPa
E3=21.374 GPaV13 = 0.6G31=13.790 GPa
Find the stiffness matrix [C] and the compliance matrix [S] for the preceding orthotropicmaterial.
arrow_forward
Help me solve this please
arrow_forward
University of Babylon
Collage of Engineering\Al-Musayab
Department of Automobile
Engineering
Under Grad/Third stage
Notes:
1-Attempt Four Questions.
2- Q4 Must be Answered
3-Assume any missing data.
4 تسلم الأسئلة بعد الامتحان مع الدفتر
Subject: Mechanical
Element Design I
Date: 2022\01\25
2022-2023
Time: Three Hours
Course 1
Attempt 1
Q1/ Design a thin cylindrical pressure tank (pressure vessel) with hemispherical ends to the
automotive industry, shown in figure I below. Design for an infinite life by finding the
appropriate thickness of the vessel to carry a sinusoidal pressure varied from {(-0.1) to (6) Mpa}.
The vessel is made from Stainless Steel Alloy-Type 316 sheet annealed. The operating
temperature is 80 C° and the dimeter of the cylinder is 36 cm. use a safety factor of 1.8.
Fig. 1
(15 Marks)
Q2/ Answer the following:
1- Derive the design equation for the direct evaluation of the diameter of a shaft to a desired
fatigue safety factor, if the shaft subjected to both fluctuated…
arrow_forward
Can anyone help me with this question
arrow_forward
The following data were collected from a 12 mm diameter test specimen of Magnesium.
LOAD (N)
GAUEGE LENGTH (mm)
0
5000
10000
15000
20000
25000
26500
27000
26500
30.000
25000
30.0296
30.0592
30.0888
30.15
30.51
30.90
31.50 (maximum load)
32.10
32.79 (fracture)
After the fracture, the gauge length is 32.61 mm and the diameter is 11.74 mm.
a) What is the elastic modulus?
b) Percent elongation at fracture?
c) Percent elongation after fracture?
d) What is the Poisson's ratio?
e)Draw the engineering stress-strain diagram corresponding to the values in the table. Call this plot I. Now consider this experiment is repeated at a higher
temperature with an identical sample. Draw the new engineering stress-strain diagram, call it plot II and highlight the differences (on the same graph) between
I and II.
arrow_forward
PHYS X PHYS X
印 PHYS X
PHYS X
POTPHYS X
PHYS X
E PHYS X E PHYS
top/semester2/physics%20for%20engineers/PHYS220_CH15_Lecture%20Notes_Problems%2015 19,15.29 S
(D Page view
A Read aloud
V Draw
Problem-15-19: page-475
A 0.500-kg object attached to a spring with a force constant of 8.00 N/m vibrates in simple harmonic motion
with an amplitude of 10.0 cm. Calculate the maximum value of its
(a) speed, and acceleration.
(b) the speed and the acceleration when the object is 6.00 em from the equilibrium position, and
(c) the time interval required for the object to move from.r50 to r5 8.O0 cm.
Solution:
arrow_forward
Q4. Two are applied to the pipe AB as shown. Knowing that the pipe has inner and outer
diameters equal to 35 and 42 mm, respectively. Determine the normal and shear stresses at (a)
point a, (b) point b.
arrow_forward
Please Provide correct solution, correct Method.
No Missing steps / calculations.
No Handwriting please
arrow_forward
A helical compression spring is to be made of a steel wire. If the coil diameter is limited to 12 mm and a spring index of 6.4 is chosen. From the following wire size chart, determine
the correct gauge size of an off-the-shelf spring wire to be used. [gauge]
BAS GAUGE
INCH
MILLIMETER
162
4.12
3.25 mm
poups
2.39mm
10 gange
081
2.06mm
064
1.63mm
16
CST"
1.29 mm
DAY
1.02
813
635 mm
24 P
508 mm
20 gange
OM
OXY
330
254
X
14
arrow_forward
Show work
Part 1 website: https://ophysics.com/r5.html
PArt 2 website: https://ophysics.com/r3.html
arrow_forward
solve question 29.3 only by hand and explain step by step please
arrow_forward
SEE MORE QUESTIONS
Recommended textbooks for you
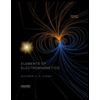
Elements Of Electromagnetics
Mechanical Engineering
ISBN:9780190698614
Author:Sadiku, Matthew N. O.
Publisher:Oxford University Press
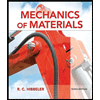
Mechanics of Materials (10th Edition)
Mechanical Engineering
ISBN:9780134319650
Author:Russell C. Hibbeler
Publisher:PEARSON
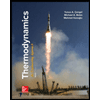
Thermodynamics: An Engineering Approach
Mechanical Engineering
ISBN:9781259822674
Author:Yunus A. Cengel Dr., Michael A. Boles
Publisher:McGraw-Hill Education
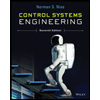
Control Systems Engineering
Mechanical Engineering
ISBN:9781118170519
Author:Norman S. Nise
Publisher:WILEY
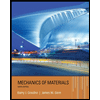
Mechanics of Materials (MindTap Course List)
Mechanical Engineering
ISBN:9781337093347
Author:Barry J. Goodno, James M. Gere
Publisher:Cengage Learning
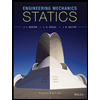
Engineering Mechanics: Statics
Mechanical Engineering
ISBN:9781118807330
Author:James L. Meriam, L. G. Kraige, J. N. Bolton
Publisher:WILEY
Related Questions
- Hi can you please help me with the attached question?arrow_forwardA metallic strain gauge produces an electrical resistance change when subjected to mechanical strain. However, engineers don't measure this voltage drop directly using a voltmeter. Why don't we directly measure the voltage drop across the strain gauge, and instead, use a Wheatstone Bridge? Damgraph >arrow_forwardPlease show work for practice problem 12arrow_forward
- The engineering constants for an orthotropic material are found to be E1= 27.579 GPa V12 = 0.2 G12=41.368 GPa E2=20.684 GPa V23 = 0.4 G23=48.263 GPa E3=21.374 GPaV13 = 0.6G31=13.790 GPa Find the stiffness matrix [C] and the compliance matrix [S] for the preceding orthotropicmaterial.arrow_forwardHelp me solve this pleasearrow_forwardUniversity of Babylon Collage of Engineering\Al-Musayab Department of Automobile Engineering Under Grad/Third stage Notes: 1-Attempt Four Questions. 2- Q4 Must be Answered 3-Assume any missing data. 4 تسلم الأسئلة بعد الامتحان مع الدفتر Subject: Mechanical Element Design I Date: 2022\01\25 2022-2023 Time: Three Hours Course 1 Attempt 1 Q1/ Design a thin cylindrical pressure tank (pressure vessel) with hemispherical ends to the automotive industry, shown in figure I below. Design for an infinite life by finding the appropriate thickness of the vessel to carry a sinusoidal pressure varied from {(-0.1) to (6) Mpa}. The vessel is made from Stainless Steel Alloy-Type 316 sheet annealed. The operating temperature is 80 C° and the dimeter of the cylinder is 36 cm. use a safety factor of 1.8. Fig. 1 (15 Marks) Q2/ Answer the following: 1- Derive the design equation for the direct evaluation of the diameter of a shaft to a desired fatigue safety factor, if the shaft subjected to both fluctuated…arrow_forward
- Can anyone help me with this questionarrow_forwardThe following data were collected from a 12 mm diameter test specimen of Magnesium. LOAD (N) GAUEGE LENGTH (mm) 0 5000 10000 15000 20000 25000 26500 27000 26500 30.000 25000 30.0296 30.0592 30.0888 30.15 30.51 30.90 31.50 (maximum load) 32.10 32.79 (fracture) After the fracture, the gauge length is 32.61 mm and the diameter is 11.74 mm. a) What is the elastic modulus? b) Percent elongation at fracture? c) Percent elongation after fracture? d) What is the Poisson's ratio? e)Draw the engineering stress-strain diagram corresponding to the values in the table. Call this plot I. Now consider this experiment is repeated at a higher temperature with an identical sample. Draw the new engineering stress-strain diagram, call it plot II and highlight the differences (on the same graph) between I and II.arrow_forwardPHYS X PHYS X 印 PHYS X PHYS X POTPHYS X PHYS X E PHYS X E PHYS top/semester2/physics%20for%20engineers/PHYS220_CH15_Lecture%20Notes_Problems%2015 19,15.29 S (D Page view A Read aloud V Draw Problem-15-19: page-475 A 0.500-kg object attached to a spring with a force constant of 8.00 N/m vibrates in simple harmonic motion with an amplitude of 10.0 cm. Calculate the maximum value of its (a) speed, and acceleration. (b) the speed and the acceleration when the object is 6.00 em from the equilibrium position, and (c) the time interval required for the object to move from.r50 to r5 8.O0 cm. Solution:arrow_forward
arrow_back_ios
SEE MORE QUESTIONS
arrow_forward_ios
Recommended textbooks for you
- Elements Of ElectromagneticsMechanical EngineeringISBN:9780190698614Author:Sadiku, Matthew N. O.Publisher:Oxford University PressMechanics of Materials (10th Edition)Mechanical EngineeringISBN:9780134319650Author:Russell C. HibbelerPublisher:PEARSONThermodynamics: An Engineering ApproachMechanical EngineeringISBN:9781259822674Author:Yunus A. Cengel Dr., Michael A. BolesPublisher:McGraw-Hill Education
- Control Systems EngineeringMechanical EngineeringISBN:9781118170519Author:Norman S. NisePublisher:WILEYMechanics of Materials (MindTap Course List)Mechanical EngineeringISBN:9781337093347Author:Barry J. Goodno, James M. GerePublisher:Cengage LearningEngineering Mechanics: StaticsMechanical EngineeringISBN:9781118807330Author:James L. Meriam, L. G. Kraige, J. N. BoltonPublisher:WILEY
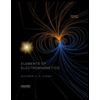
Elements Of Electromagnetics
Mechanical Engineering
ISBN:9780190698614
Author:Sadiku, Matthew N. O.
Publisher:Oxford University Press
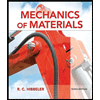
Mechanics of Materials (10th Edition)
Mechanical Engineering
ISBN:9780134319650
Author:Russell C. Hibbeler
Publisher:PEARSON
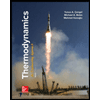
Thermodynamics: An Engineering Approach
Mechanical Engineering
ISBN:9781259822674
Author:Yunus A. Cengel Dr., Michael A. Boles
Publisher:McGraw-Hill Education
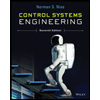
Control Systems Engineering
Mechanical Engineering
ISBN:9781118170519
Author:Norman S. Nise
Publisher:WILEY
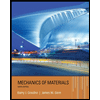
Mechanics of Materials (MindTap Course List)
Mechanical Engineering
ISBN:9781337093347
Author:Barry J. Goodno, James M. Gere
Publisher:Cengage Learning
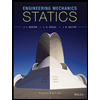
Engineering Mechanics: Statics
Mechanical Engineering
ISBN:9781118807330
Author:James L. Meriam, L. G. Kraige, J. N. Bolton
Publisher:WILEY