ENGR 244 Lab 6
docx
keyboard_arrow_up
School
Concordia University *
*We aren’t endorsed by this school
Course
244
Subject
Mechanical Engineering
Date
Dec 6, 2023
Type
docx
Pages
17
Uploaded by AgentSnail2002
Lab 6:
Behaviour of Columns Under Axial Load
Lab Section CI – X
Winter 2022
Professor Ahmed Soliman
Concordia University
Montreal, QC, Canada
Tuesday March 22
nd
, 2022
Table of Contents
Nomenclature pg 3
List of Tables pg 3
List of Figures pg 3
Objective pg 4
Introduction pg 4
Procedure pg 4
Results pg 4-5
Discussion pg 5-6
Conclusion pg 6
References pg 7
Appendix pg 8-13
Original Data pg 14
Nomenclature
λ = slenderness ratio
σ
all = allowable stress
σ
crit experiment
= experimental critical stress
σ
crit theo
= theoretical critical stress
A = cross sectional area
D = diameter
d
i = inner diameter
d
o
= outer diameter
E = modulus of elasticity
I = polar moment of inertia
K = effective length factor
L = length
L
eff
= effective length
R = radius of gyration
P
crit experiment
= experimental critical load
P
crit theo
= theoretical critical load
List of Tables
Appendix A:
Experimental and Theoretical Results for Hollow Specimens pg. 8
Appendix B: Experimental and Theoretical Results for Solid Specimens pg. 9
List of Figures
Figure 1: Stresses vs Slenderness Ratio pg. 5
Appendix C: Fixed-Fixed Hollow pg. 9
Appendix D: Fixed-Fixed Solid pg. 10
Appendix E: Pin-Fixed Hollow pg. 10
Appendix F: Pin-Fixed Solid pg. 11
Appendix G: Pin-Pin Solid 74mm pg. 11
Appendix H: Pin-Pin Solid 125mm pg. 12
Appendix I: Pin-Pin Hollow 225mm pg. 12
Appendix J: Pin-Pin Solid 225mm pg. 13
Objective:
The objective of this lab is to determine the experimental and theoretical buckling loads of columns with different lengths and different end conditions. The buckling loads will be found for both hollow and solid columns.
Introduction: Deformation of a column can occur when an axial load is applied. As the load increases, the deformation shall also increase and will eventually reach a point called the critical buckling load. The critical
buckling load will vary throughout columns based on the length, end conditions, cross sectional shape and the location of the load on the material [ CITATION Con \l 4105 ]. The critical stresses are also dependent on the stiffness, strength and ductility of the material used for the column [ CITATION RMA17 \l 4105 ]. Using the
Your preview ends here
Eager to read complete document? Join bartleby learn and gain access to the full version
- Access to all documents
- Unlimited textbook solutions
- 24/7 expert homework help
previous equation used for deflection, (d
2
y/dx
2
) = M/EI, we can derive a new equation used to find the theoretical critical buckling load: P
cr
= (π
2
EI)/L
2
. This equation is called Euler’s formula which requires three conditions to be met: the load must be along the centroidal axis of the column, the ends of the column must be pinned and the column must behave elastically [ CITATION Con \l 4105 ]. In practice, these assumptions are not
met as columns are expected to show inelastic behaviour to axial loads [ CITATION RMA17 \l 4105 ]. Since σ
cr
= P
cr
/A, we can also say that σ
cr
= (π
2
E)/(L/r)
2
where r = (I/A)
1/2
and (L/r)
2
= λ
2
. In this equation, r is the radius of gyration, A is the cross-sectional area of the column and λ is the slenderness ratio. Euler’s formula assumes that both ends of the column are pinned and so a new factor, K, comes in when different types of supports are used. Different support types give different “effective lengths” to the column. The effective length can be given by the following equation: L
e
= KL where K is the effective length ratio, which varies with each type of support. Although Euler’s formula gives the theoretical critical buckling loads, the value calculated tends to be significantly higher than the experimental values due to assumptions that are not met in real life [ CITATION Con \l 4105 ].
Procedure: Prepare the compression testing device and measure the inner diameter, outer diameter, and length of each specimen. For the 225 mm specimens, do tests using all of the support conditions provided (pin-
pin, pin-fixed, fixed-fixed). When the specimen is well placed at the supports, start increasing the compressive load and watch for bending. Record the maximum load after the specimen bends. For the smaller specimen, 75mm and 125mm, repeat the same steps but only using the pin-pin supports.
Results:
Sample Calculations
Formulas used: L
eff
= KL, r = (I/A)
1/2
, λ = L
eff
/r, P
crit theo
= (π
2
EI)/L
eff
2
, σ
crit experiment
= P
crit experiment
/A, σ
crit theo
= (π
2
E)/λ
2
, σ
all
= (139 – 0.868λ) MPa, σ
all
= (351000/λ
2
) MPa
For hollow bar: A = (π/4)(d
o
2
– d
i
2
), I = π(d
o
4
– d
i
4
)/64
For solid bar: A = (π/4)(d
2
), π(d
4
)/64
Calculations for 225mm, pin-fixed, hollow tube L
eff
= (0.707)(225mm) = 159.075
Cross section: A = (π/4)(6.363
2
– 4.5825
2
)
A = 15.3062mm
2
I = π(6.363
4
– 4.5825
4
)/64
I = 58.8209mm
4
r = (58.8209/15.3062)
1/2
= 1.9603mm
λ = 159.075/1.9603 = 81.1465
σ
all
= 351000/81.1465
2
σ
all
= 53.3049MPa
P
crit theo
= (π
2
(70x10
9
)(58.8209))/0.159075
P
crit theo
= 1605.9262N
σ
crit theo = (π
2
)(70x10
9
)/81.1465
2
= 104.9200MPa
σ
crit experiment = 1285/15.3062
σ
crit experiment
= 83.9529MPa
20
40
60
80
100
120
140
160
0
50
100
150
200
250
300
350
400
450
500
Stresses vs Slenderness Ratio
Theoretical Critical Stress
Exponential (Theo-
retical Critical Stress)
Experimental Critical Stress
Exponential (Exper-
imental Critical Stress)
Allowable Stress
Exponential (Al-
lowable Stress)
Slenderness Ratio
Critical Stress (MPa)
Figure 1: Stresses vs Slenderness Ratio
Discussion: The results seen on tables 1 and 2 (page 8-9) are in line with our original assumptions. Due to having varying conditions, the experimental stresses tended to be lower than the theoretical stresses. Figure 1 above shows two cases where the experimental stress was higher than the theoretical stress, but this can be explained due to issues at the end points. Since both cases came from pin-pin end conditions, we can assume the higher experimental stress was due to a transfer of load onto the pins instead of the load being held by only the specimen. Transfer loads can be caused by the pins lacking mobility once connected to the columns and can therefore get jammed into unfavorable positions. In the opposite cases, where the experimental stress is much lower than the theoretical stress, it can be explained by unforeseen lateral forces. The equipment used did not have a reliable way to position the columns straight under the axial load, so it is very likely that the columns were at a slight angle which takes a portion of our axial load and turns it into a lateral load. Since columns are more susceptible to lateral loads [ CITATION RMA17 \l 4105 ], small angles can lead to much earlier buckling stresses.
When comparing the experimental stresses to the allowable stresses, we can see in figure 1 that the curve
is comparable, and the experimental values were higher. Since the allowable stress values were designed to include a factor of safety, it was expected that the critical stresses would be higher. Comparing the allowable stresses to the theoretical stresses, we can see that a factor of safety of approximately 2 was used. Although this factor of safety wasn’t reached with our experimental results, it can be explained by all the discrepancies mentioned between the theoretical and experimental stresses.
In construction, columns are commonly made of cement or concrete with possibilities of steel rod reinforcements[ CITATION فعج
15 \l 4105 ]. These types of columns are expected to be inelastic and therefore experiment permanent deformation if ever moved [ CITATION RMA17 \l 4105 ]. Since these types of columns are extremely resistant to buckling from axial loads. The most common sources of failure are due to unexpected lateral loads. These loads can range from strong winds, earthquakes, or high impacts [ CITATION فعج
15 \l 4105 ]. The steel rod reinforcements help to strengthen the columns against lateral loads, as steel has more buckling resistance than concrete when subjected to lateral loads [ CITATION فعج
15 \l 4105 ]. Though highly resistant to compressive loads, columns can still fail if the axial load exceeds the critical point [ CITATION فعج
15 \l 4105 ]. Changes in temperature can also compromise columns as they will expand or contract, but columns are designed to be able to withstand most temperature changes [ CITATION فعج
15 \l 4105 ]. It is also possible that the steel bars or the concrete get corroded or damaged due to water or acids [ CITATION فعج
15 \l 4105 ].
Comparing our results in tables 1 and 2 (page 7), we can see that the hollow specimens are significantly more resistant to buckling than their solid counter parts. Mathematically explained, it is simply because hollow columns have a greater moment of inertia compared to solid columns of the same cross-sectional area. It can also
be explained by the lower slenderness ratio for higher moments of inertia. In other words, the columns are wider for the same cross-sectional area which provides more stability and strength. Hollow columns also lower the overall weight of the structure [ CITATION Ard19 \l 4105 ] which is a large factor in bigger buildings.
Conclusion:
Looking at our results on tables 1 and 2 (page 8-9) and figure 1 (page 5), we can say that the experiment was a success. The experimental values were where they were expected to be except for a few cases where equipment affected the outcomes. The specimen buckled where they were expected to buckle, and it
was able to be concluded that the hollow specimen had higher buckling resistance than their solid counterparts. To get better and more conclusive results, more tests would need to be done while adhering to the requirements of Euler’s formula.
References
[1] C. U. E. a. C. Science, ENGR 244 Mechanics of Materials Lab Manual, Montreal: Concordia University. [2] R. A. e. A. Awazli, "Behaviour of Reinforced Concrete Columns Subjected to Axial Load and Cyclic Lateral Load," University of Baghdad Engineering Journal, vol. 23, pp. 21-40, 2017. [3] فاقسلا نيز يدنه رفعج .ا .ا .م ., .أ .م
, "bayt Employer," 17 01 2015. [Online]. Available:
Your preview ends here
Eager to read complete document? Join bartleby learn and gain access to the full version
- Access to all documents
- Unlimited textbook solutions
- 24/7 expert homework help
https://specialties.bayt.com/en/specialties/q/148975/what-are-the-causes-for-buckling-and-yielding-of-
reinforcement-in-concrete-structures/. [Accessed 25 03 2022].
[4] A. e. Margaret.Abraham, "Comparison of Seismic Behaviour of Solid and Hollow Conrete Members in R.C.C Framed Buildings using ETABS," International Journal of Applied Engineering Research, vol. 14, no. 0973-
4562, pp. 161-166, 2019. Appendix
Appendix A: Experimental and Theoretical Results for Hollow Specimens
Type of Column
Hollow
Hollow
Hollow
Hollow
Hollow
Column Length, L(mm)
75
125
225
225
225
End Condition
Pin-Pin
Pin-Pin
Pin-Pin
Pin-Fixed
Fixed-Fixed
Effective length factor, K
1
1
1
0.707
0.5
Effective length, 75
125
225
159.075
112.5
L
eff
(mm)
Inner diameter, d
i
(mm)
4.6075
4.59
4.6
4.5825
4.6175
Outer diameter, d
out
(mm)
6.37
6.353
6.36
6.363
6.363
Cross sectional area, A(mm
2
)
15.1958
15.1523
15.1500
15.3062
15.0533
Moment of inertia, I(mm
4
)
58.6992
58.1741
58.3367
58.8209
58.1519
Radius of gyration, r(mm)
1.9654
1.9594
1.9623
1.9603
1.9655
Slenderness ratio, λ
38.1602
63.7950
114.6614
81.1465
57.2373
Allowable stress, σ
all
(MPa)
105.8769
83.6259
26.6976
53.3049
89.3180
Theoretical critical load,
P
crit theo
(N)
7209.5381
2572.2160
796.1128
1605.9262
3174.3634
Theoretical critical stress, σ
crit theo
(MPa)
474.4428
169.7575
52.5487
104.9200
210.8749
Experimental critical load, P
crit experiment
(N)
3940
3542
2018
1285
2017
Experimental critical stress, σ
crit experiment
(MPa)
259.2823
233.7599
133.2013
83.9529
133.9906
Appendix B:
Experimental and Theoretical Results for Solid Specimens
Type of Column
Solid
Solid
Solid
Column Length, L(mm)
225
225
225
End Condition
Pin-Pin
Pin-Fixed
Fixed-Fixed
Effective length factor, K
1
0.707
0.5
Effective length, L
eff
(mm)
225
159.075
112.5
diameter, d(mm)
6.4
6.443
6.47
Cross sectional area, A(mm
2
)
32.1699
32.6036
32.8775
Moment of inertia, I(mm
4
)
82.3550
84.5907
86.0175
Radius of gyration, r(mm)
1.6000
1.6108
1.6175
Slenderness ratio, λ
140.6250
98.7553
69.5518
Allowable stress, σ
all
(MPa)
17.7493
35.9904
72.5588
Theoretical critical load, P
crit theo
(N)
1123.8872
2309.4924
4695.4753
Theoretical critical stress, σ
crit theo
(MPa)
34.9360
70.8355
142.8173
Experimental critical load, P
crit experiment
(N)
1752
2502
3131
Experimental critical stress, σ
crit experiment
(MPa)
54.4608
76.7400
95.2323
Appendix C: Fixed-Fixed Hollow
Your preview ends here
Eager to read complete document? Join bartleby learn and gain access to the full version
- Access to all documents
- Unlimited textbook solutions
- 24/7 expert homework help
Appendix D: Fixed-Fixed Solid
Appendix E: Pin-Fixed Hollow
Appendix F: Pin-Fixed Solid
Your preview ends here
Eager to read complete document? Join bartleby learn and gain access to the full version
- Access to all documents
- Unlimited textbook solutions
- 24/7 expert homework help
Appendix G: Pin-Pin Solid 74mm
Appendix H: Pin-Pin Solid 125mm
Appendix I: Pin-Pin Hollow 225mm
Your preview ends here
Eager to read complete document? Join bartleby learn and gain access to the full version
- Access to all documents
- Unlimited textbook solutions
- 24/7 expert homework help
Appendix J: Pin-Pin Solid 225mm
Original Data
Related Documents
Related Questions
Please show work for practice problem 12
arrow_forward
Arrangement of the solution:
The following section should be underlined and numbered in your solution
Problem statement
Given
Required
Drawing/ sketch / free body diagram V. Solution with explanation
arrow_forward
7. A steel connecting rod is subjected to a completely reversed axial load of 160 kN. Suggest the suitable
diameter of the rod using a factor of safety 2. The ultimate tensile strength of the material is 1100
MPa, and yield strength 930 MPa. Neglect column action and the effect of stress concentration.
[Ans. 30.4 mm]
arrow_forward
A bracket is riveted to a column by 6 rivets of equal size as shown in Fig. It carries a load of 100 kN at a distance of 250 mm from the column. If the maximum shear stress in the rivet is limited to 63 MPa, find the diameter of the rivet.
arrow_forward
PHYS X PHYS X
印 PHYS X
PHYS X
POTPHYS X
PHYS X
E PHYS X E PHYS
top/semester2/physics%20for%20engineers/PHYS220_CH15_Lecture%20Notes_Problems%2015 19,15.29 S
(D Page view
A Read aloud
V Draw
Problem-15-19: page-475
A 0.500-kg object attached to a spring with a force constant of 8.00 N/m vibrates in simple harmonic motion
with an amplitude of 10.0 cm. Calculate the maximum value of its
(a) speed, and acceleration.
(b) the speed and the acceleration when the object is 6.00 em from the equilibrium position, and
(c) the time interval required for the object to move from.r50 to r5 8.O0 cm.
Solution:
arrow_forward
University of Babylon
Collage of Engineering\Al-Musayab
Department of Automobile
Engineering
Under Grad/Third stage
Notes:
1-Attempt Four Questions.
2- Q4 Must be Answered
3-Assume any missing data.
4 تسلم الأسئلة بعد الامتحان مع الدفتر
Subject: Mechanical
Element Design I
Date: 2022\01\25
2022-2023
Time: Three Hours
Course 1
Attempt 1
Q1/ Design a thin cylindrical pressure tank (pressure vessel) with hemispherical ends to the
automotive industry, shown in figure I below. Design for an infinite life by finding the
appropriate thickness of the vessel to carry a sinusoidal pressure varied from {(-0.1) to (6) Mpa}.
The vessel is made from Stainless Steel Alloy-Type 316 sheet annealed. The operating
temperature is 80 C° and the dimeter of the cylinder is 36 cm. use a safety factor of 1.8.
Fig. 1
(15 Marks)
Q2/ Answer the following:
1- Derive the design equation for the direct evaluation of the diameter of a shaft to a desired
fatigue safety factor, if the shaft subjected to both fluctuated…
arrow_forward
R10
O Reaction Points
84 cm
Loading Points
Area = 1594 cm^2
W/2
W/2
54 cm
L1=27 cm
Figure 2. Skateboard dimensions and loading conditions.
Loading conditions
Weight of a skateboarder, W 90 kg
Load case: Calculate Bending and twisting moment, Ms, Mxy
Use Tsai-Wu failure criterion for selection of relevant laminate design. Specifically, the core materials
failure is free of any failure; therefore, it can be analyzed based on maximum strain failure criterion with
=0.1.
D3D20 cm
arrow_forward
HEAT TRANSFER
CASE: I want to know what temperature in (°F) the cylinder will have inside. It's a heat transfer problem.
what is T2 ?
HEAT TRANSFER
They gave me an answer all squashed together that i can't make sense of it. If you could help me makes sense of it thank you!
arrow_forward
mathlab code:
%Press-Fit Example Problem 117
%Steel, psi
ES=30*10^6
MuS=0.292;
%Cast Iron
EC=14.5*10^6;
MuC=0.211;
di=0;
d0=2.002;
Di=2.000;
D0=3.000;
% tolerance
tol=d0-D0;
% Pressure Eq. (3-56)
R=Di/2;
r0=D0/2;
ri=di/2;
Hub=(1/ES)*((r0^2+R^2)/(r0^2-R^2)+MuS);
Inner=(1/EC)*((R^2+ri^2)/(R^2-ri^2)-MuC);
p=tol/(R*(Hub+Inner))
arrow_forward
The engineering constants for an orthotropic material are found to be
E1= 27.579 GPa V12 = 0.2 G12=41.368 GPa
E2=20.684 GPa V23 = 0.4 G23=48.263 GPa
E3=21.374 GPaV13 = 0.6G31=13.790 GPa
Find the stiffness matrix [C] and the compliance matrix [S] for the preceding orthotropicmaterial.
arrow_forward
Please answer the question clearly, stating how you chose the formulas and what each variable represents. Thank you!
arrow_forward
Item 1
(no subje X
C n
My Drive X
▼
Part A
ko = Value
Submit
Amazon.c
μA
Provide Feedback
X
Request Answer
ProblemID=15630894 Al LO
hp
idle game
Determine the radius of gyration of the pendulum about an axis perpendicular to the page and passing through point O.
Express your answer to three significant figures and include the appropriate units.
Units
X
SHE
?
ME Assign
W
Mastering
h
4:57 PM
11/29/2022
arrow_forward
Please use ANSYS SOFTWARE
arrow_forward
please wright by hand
arrow_forward
Need help with this engineering of materials
arrow_forward
The bar of negligible weight is supported by two springs
each having a stiffness 180 N/m The springs are
originally unstretched, and the force is vertical as shown (
Figure 1)
Figure
C
30 N
Im
B
2m
Part A
Determine the angle the bar makes with the horizontal, when the 30-N force is applied to the bar
Express your answer using three significant figures.
VAX
Submit
Request Amer
Return to Assignment
vec
Provide feedback
?
arrow_forward
Give a detailed solution in a handwritten format.
Don't use chatgpt.
arrow_forward
Show work
Part 1 website: https://ophysics.com/r5.html
PArt 2 website: https://ophysics.com/r3.html
arrow_forward
draw an ashby chart for a knife
By using this instructured:
arrow_forward
Units: mmgs
Mass = 538.9662 grams Volume = 199617.1105 cubic millimeters Surface area = 32076.7718 square millimeters
Material: 6061 Alloy
Any direction/guidance on how to make this would be greatly appreciated. Thank you!
arrow_forward
22°F
Clear
DDÈ DDE MMMBU BU ► ► ► 2GQ==§¤¤✰=aaa=Û¤ı1 × PDF PDF PDF PDF PDE
File | C:/Users/ignor/Downloads/Assignment%203%20(2).pdf
T❘ Read aloud
Draw
Ask Copilot
Search
Ө
3
R
of 6
THREE
A mass M₁ is fixed to the end of a rod which can rotate freely around origin O. The rod has a
constant length R and is massless. Mass M₁ (point P) is connected by a spring with stiffness
K to a follower that moves only in the horizontal direction. The weight of the follower is M₂
(point Q). Find the equations of motion of the system.
2
M₁
| CD
P
40111
eac
M₂ Q
СО dal
o
+
ENG
60
T
6L
N
{0}
7:39 PM
1/17/2024
x
arrow_forward
SEE MORE QUESTIONS
Recommended textbooks for you
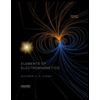
Elements Of Electromagnetics
Mechanical Engineering
ISBN:9780190698614
Author:Sadiku, Matthew N. O.
Publisher:Oxford University Press
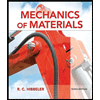
Mechanics of Materials (10th Edition)
Mechanical Engineering
ISBN:9780134319650
Author:Russell C. Hibbeler
Publisher:PEARSON
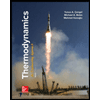
Thermodynamics: An Engineering Approach
Mechanical Engineering
ISBN:9781259822674
Author:Yunus A. Cengel Dr., Michael A. Boles
Publisher:McGraw-Hill Education
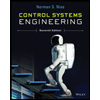
Control Systems Engineering
Mechanical Engineering
ISBN:9781118170519
Author:Norman S. Nise
Publisher:WILEY
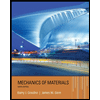
Mechanics of Materials (MindTap Course List)
Mechanical Engineering
ISBN:9781337093347
Author:Barry J. Goodno, James M. Gere
Publisher:Cengage Learning
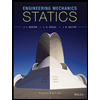
Engineering Mechanics: Statics
Mechanical Engineering
ISBN:9781118807330
Author:James L. Meriam, L. G. Kraige, J. N. Bolton
Publisher:WILEY
Related Questions
- Please show work for practice problem 12arrow_forwardArrangement of the solution: The following section should be underlined and numbered in your solution Problem statement Given Required Drawing/ sketch / free body diagram V. Solution with explanationarrow_forward7. A steel connecting rod is subjected to a completely reversed axial load of 160 kN. Suggest the suitable diameter of the rod using a factor of safety 2. The ultimate tensile strength of the material is 1100 MPa, and yield strength 930 MPa. Neglect column action and the effect of stress concentration. [Ans. 30.4 mm]arrow_forward
- A bracket is riveted to a column by 6 rivets of equal size as shown in Fig. It carries a load of 100 kN at a distance of 250 mm from the column. If the maximum shear stress in the rivet is limited to 63 MPa, find the diameter of the rivet.arrow_forwardPHYS X PHYS X 印 PHYS X PHYS X POTPHYS X PHYS X E PHYS X E PHYS top/semester2/physics%20for%20engineers/PHYS220_CH15_Lecture%20Notes_Problems%2015 19,15.29 S (D Page view A Read aloud V Draw Problem-15-19: page-475 A 0.500-kg object attached to a spring with a force constant of 8.00 N/m vibrates in simple harmonic motion with an amplitude of 10.0 cm. Calculate the maximum value of its (a) speed, and acceleration. (b) the speed and the acceleration when the object is 6.00 em from the equilibrium position, and (c) the time interval required for the object to move from.r50 to r5 8.O0 cm. Solution:arrow_forwardUniversity of Babylon Collage of Engineering\Al-Musayab Department of Automobile Engineering Under Grad/Third stage Notes: 1-Attempt Four Questions. 2- Q4 Must be Answered 3-Assume any missing data. 4 تسلم الأسئلة بعد الامتحان مع الدفتر Subject: Mechanical Element Design I Date: 2022\01\25 2022-2023 Time: Three Hours Course 1 Attempt 1 Q1/ Design a thin cylindrical pressure tank (pressure vessel) with hemispherical ends to the automotive industry, shown in figure I below. Design for an infinite life by finding the appropriate thickness of the vessel to carry a sinusoidal pressure varied from {(-0.1) to (6) Mpa}. The vessel is made from Stainless Steel Alloy-Type 316 sheet annealed. The operating temperature is 80 C° and the dimeter of the cylinder is 36 cm. use a safety factor of 1.8. Fig. 1 (15 Marks) Q2/ Answer the following: 1- Derive the design equation for the direct evaluation of the diameter of a shaft to a desired fatigue safety factor, if the shaft subjected to both fluctuated…arrow_forward
- R10 O Reaction Points 84 cm Loading Points Area = 1594 cm^2 W/2 W/2 54 cm L1=27 cm Figure 2. Skateboard dimensions and loading conditions. Loading conditions Weight of a skateboarder, W 90 kg Load case: Calculate Bending and twisting moment, Ms, Mxy Use Tsai-Wu failure criterion for selection of relevant laminate design. Specifically, the core materials failure is free of any failure; therefore, it can be analyzed based on maximum strain failure criterion with =0.1. D3D20 cmarrow_forwardHEAT TRANSFER CASE: I want to know what temperature in (°F) the cylinder will have inside. It's a heat transfer problem. what is T2 ? HEAT TRANSFER They gave me an answer all squashed together that i can't make sense of it. If you could help me makes sense of it thank you!arrow_forwardmathlab code: %Press-Fit Example Problem 117 %Steel, psi ES=30*10^6 MuS=0.292; %Cast Iron EC=14.5*10^6; MuC=0.211; di=0; d0=2.002; Di=2.000; D0=3.000; % tolerance tol=d0-D0; % Pressure Eq. (3-56) R=Di/2; r0=D0/2; ri=di/2; Hub=(1/ES)*((r0^2+R^2)/(r0^2-R^2)+MuS); Inner=(1/EC)*((R^2+ri^2)/(R^2-ri^2)-MuC); p=tol/(R*(Hub+Inner))arrow_forward
- The engineering constants for an orthotropic material are found to be E1= 27.579 GPa V12 = 0.2 G12=41.368 GPa E2=20.684 GPa V23 = 0.4 G23=48.263 GPa E3=21.374 GPaV13 = 0.6G31=13.790 GPa Find the stiffness matrix [C] and the compliance matrix [S] for the preceding orthotropicmaterial.arrow_forwardPlease answer the question clearly, stating how you chose the formulas and what each variable represents. Thank you!arrow_forwardItem 1 (no subje X C n My Drive X ▼ Part A ko = Value Submit Amazon.c μA Provide Feedback X Request Answer ProblemID=15630894 Al LO hp idle game Determine the radius of gyration of the pendulum about an axis perpendicular to the page and passing through point O. Express your answer to three significant figures and include the appropriate units. Units X SHE ? ME Assign W Mastering h 4:57 PM 11/29/2022arrow_forward
arrow_back_ios
SEE MORE QUESTIONS
arrow_forward_ios
Recommended textbooks for you
- Elements Of ElectromagneticsMechanical EngineeringISBN:9780190698614Author:Sadiku, Matthew N. O.Publisher:Oxford University PressMechanics of Materials (10th Edition)Mechanical EngineeringISBN:9780134319650Author:Russell C. HibbelerPublisher:PEARSONThermodynamics: An Engineering ApproachMechanical EngineeringISBN:9781259822674Author:Yunus A. Cengel Dr., Michael A. BolesPublisher:McGraw-Hill Education
- Control Systems EngineeringMechanical EngineeringISBN:9781118170519Author:Norman S. NisePublisher:WILEYMechanics of Materials (MindTap Course List)Mechanical EngineeringISBN:9781337093347Author:Barry J. Goodno, James M. GerePublisher:Cengage LearningEngineering Mechanics: StaticsMechanical EngineeringISBN:9781118807330Author:James L. Meriam, L. G. Kraige, J. N. BoltonPublisher:WILEY
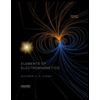
Elements Of Electromagnetics
Mechanical Engineering
ISBN:9780190698614
Author:Sadiku, Matthew N. O.
Publisher:Oxford University Press
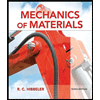
Mechanics of Materials (10th Edition)
Mechanical Engineering
ISBN:9780134319650
Author:Russell C. Hibbeler
Publisher:PEARSON
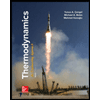
Thermodynamics: An Engineering Approach
Mechanical Engineering
ISBN:9781259822674
Author:Yunus A. Cengel Dr., Michael A. Boles
Publisher:McGraw-Hill Education
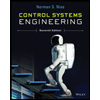
Control Systems Engineering
Mechanical Engineering
ISBN:9781118170519
Author:Norman S. Nise
Publisher:WILEY
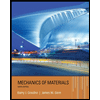
Mechanics of Materials (MindTap Course List)
Mechanical Engineering
ISBN:9781337093347
Author:Barry J. Goodno, James M. Gere
Publisher:Cengage Learning
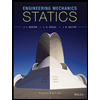
Engineering Mechanics: Statics
Mechanical Engineering
ISBN:9781118807330
Author:James L. Meriam, L. G. Kraige, J. N. Bolton
Publisher:WILEY