Fluid Mechanics Lab Report
docx
keyboard_arrow_up
School
Curtin University *
*We aren’t endorsed by this school
Course
12925
Subject
Mechanical Engineering
Date
Oct 30, 2023
Type
docx
Pages
13
Uploaded by ChiefFog12162
Your preview ends here
Eager to read complete document? Join bartleby learn and gain access to the full version
- Access to all documents
- Unlimited textbook solutions
- 24/7 expert homework help
Your preview ends here
Eager to read complete document? Join bartleby learn and gain access to the full version
- Access to all documents
- Unlimited textbook solutions
- 24/7 expert homework help
Your preview ends here
Eager to read complete document? Join bartleby learn and gain access to the full version
- Access to all documents
- Unlimited textbook solutions
- 24/7 expert homework help
Your preview ends here
Eager to read complete document? Join bartleby learn and gain access to the full version
- Access to all documents
- Unlimited textbook solutions
- 24/7 expert homework help
Recommended textbooks for you
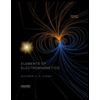
Elements Of Electromagnetics
Mechanical Engineering
ISBN:9780190698614
Author:Sadiku, Matthew N. O.
Publisher:Oxford University Press
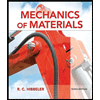
Mechanics of Materials (10th Edition)
Mechanical Engineering
ISBN:9780134319650
Author:Russell C. Hibbeler
Publisher:PEARSON
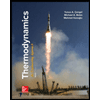
Thermodynamics: An Engineering Approach
Mechanical Engineering
ISBN:9781259822674
Author:Yunus A. Cengel Dr., Michael A. Boles
Publisher:McGraw-Hill Education
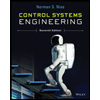
Control Systems Engineering
Mechanical Engineering
ISBN:9781118170519
Author:Norman S. Nise
Publisher:WILEY
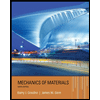
Mechanics of Materials (MindTap Course List)
Mechanical Engineering
ISBN:9781337093347
Author:Barry J. Goodno, James M. Gere
Publisher:Cengage Learning
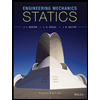
Engineering Mechanics: Statics
Mechanical Engineering
ISBN:9781118807330
Author:James L. Meriam, L. G. Kraige, J. N. Bolton
Publisher:WILEY
Recommended textbooks for you
- Elements Of ElectromagneticsMechanical EngineeringISBN:9780190698614Author:Sadiku, Matthew N. O.Publisher:Oxford University PressMechanics of Materials (10th Edition)Mechanical EngineeringISBN:9780134319650Author:Russell C. HibbelerPublisher:PEARSONThermodynamics: An Engineering ApproachMechanical EngineeringISBN:9781259822674Author:Yunus A. Cengel Dr., Michael A. BolesPublisher:McGraw-Hill Education
- Control Systems EngineeringMechanical EngineeringISBN:9781118170519Author:Norman S. NisePublisher:WILEYMechanics of Materials (MindTap Course List)Mechanical EngineeringISBN:9781337093347Author:Barry J. Goodno, James M. GerePublisher:Cengage LearningEngineering Mechanics: StaticsMechanical EngineeringISBN:9781118807330Author:James L. Meriam, L. G. Kraige, J. N. BoltonPublisher:WILEY
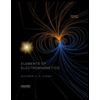
Elements Of Electromagnetics
Mechanical Engineering
ISBN:9780190698614
Author:Sadiku, Matthew N. O.
Publisher:Oxford University Press
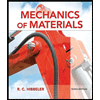
Mechanics of Materials (10th Edition)
Mechanical Engineering
ISBN:9780134319650
Author:Russell C. Hibbeler
Publisher:PEARSON
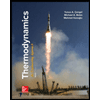
Thermodynamics: An Engineering Approach
Mechanical Engineering
ISBN:9781259822674
Author:Yunus A. Cengel Dr., Michael A. Boles
Publisher:McGraw-Hill Education
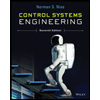
Control Systems Engineering
Mechanical Engineering
ISBN:9781118170519
Author:Norman S. Nise
Publisher:WILEY
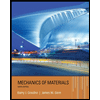
Mechanics of Materials (MindTap Course List)
Mechanical Engineering
ISBN:9781337093347
Author:Barry J. Goodno, James M. Gere
Publisher:Cengage Learning
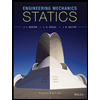
Engineering Mechanics: Statics
Mechanical Engineering
ISBN:9781118807330
Author:James L. Meriam, L. G. Kraige, J. N. Bolton
Publisher:WILEY
Browse Popular Homework Q&A
Q: Given that h(x)=2g(x), what is h'(6) ?
1
O
-6
5
-4
3
2
0
6
O-1/2
18
-6
O 1/2
2
11
Off
g
3
A
1
1
1
01…
Q: Use l'Hôpital's rule to find the following limit.
lim 9x²e-x
lim 9x'e
(
(Type an exact answer.)
Q: side b
Angle B
Angle M
0
M
35 yards
24 yards
Q: Factor 16t^2+40t-96
Q: Briefly discuss the erikson fifth stage of development personality development.
Q: Which of the following statements is true?
a. An adapter can be used only to take information from…
Q: Which of the following do we NOT look at when determining results of a TSI
a. Color of the butt
b.…
Q: Assume that a procedure yields a binomial distribution with a trial repeated n=5 times. Use some…
Q: Given ABC. ABC is rotated 270° clockwise around point R. What are the coordinates of A', the vertex…
Q: Consider the function below. (If an answer does not exist, enter DNE.)
f(x) = x4 - 4x2 + 4
(a) Find…
Q: Ch. 5: The condition which results from insufficient production of surfactant and the
resulting…
Q: This is a molarity problem that I cannot figure out. If you could please help me understand the…
Q: he 10-lb block has a speed of 4 ft/s when the force of F=(8t2) lb is applied. The coefficient of…
Q: Find the exact solutions to each equation on the interval of [0,2π).
1. 4 cos2 (π/2 - t) - 3 =
Q: Divide by using synthetic division.
(23+8²-6x-9) = (x+2)
2²+ 6x +18+
2³ +6r²18r+27
O³ +10² +14r + 19…
Q: angle 75°
93107904
SUI
alan
I vectors together, what is the magnitude.
of
Q: Find the requested value and identify each of the other values as the periodic rate, the number of…
Q: what is the magnitude of the resultant force due to the distributed load in the diagram above? Do…
Q: Solve the LP problem. If no optimal solution exists, indicate whether the feasible region is empty…
Q: The owner of a chain of mini-markets wants to compare the sales performance of two of her stores,…
Q: In the Sussex Pledge, Germany promised that it would stop sinking ships if the British
O did the…
Q: Which of the following is false? Hint: It might be useful to sketch the distributions.
Z scores…
Q: 3. Suppose the prisoner's dilemma in question 2 is played an infinite number of times.
Assume a…
Q: Find the missing side/angles for the following.
Angle A
Angle C
side a
O
O
C
9 yd
77⁰
PA 9
B
Q: Can "Internet" and "World Wide Web" be used interchangeably, or are there differences between the…