Assignment_Week 6_Control
docx
keyboard_arrow_up
School
Hutchinson Community College *
*We aren’t endorsed by this school
Course
601
Subject
Mechanical Engineering
Date
Feb 20, 2024
Type
docx
Pages
7
Uploaded by PrivateIceGiraffe15
Week 6 Assignment – Control
Task
Points Possible
1.
Mistake Proofing
10
2.
Updated FMEA
10
3.
Standard Operating Procedures
10
4.
Control Plan
20
5.
Control Charts
30
6.
Process Monitoring Communication 20
1.
Mistake Proofing
– Your Lean Six Sigma team is seeking to reduce the incidence of ventilator associated pneumonia by ensuring the head of the patient’s bed is elevated between 30° and 45°. Describe a detection and prevention approach that could be used to solve this problem, then score each of them with the solution priority
number scale provided in the presentation. a.
Detection Approach
– One possible detection approach to ensure the head of the patient's bed is elevated between 30° and 45° is by implementing an automated monitoring system. This system could consist of sensors or electronic devices that continuously measure and monitor the angle of the bed. The sensors would be programmed to detect any deviations from the desired range (30°-45°) and trigger an alert or notification to the healthcare staff.
Solution Priority Number (SPN) Scale: To assign a score to this detection approach, we can use a solution priority number scale that evaluates various factors such as impact, feasibility, and resources required. Assuming a scale from 1 to 10, with 1 being the lowest priority and 10 being the highest, the score for this detection approach could be:
Impact: The impact of implementing an automated monitoring system would be relatively high, as it would help detect and prevent incidences of ventilator-associated pneumonia. Score: 8
Feasibility: Depending on the availability of technology and resources, implementing an automated monitoring system may have different levels of feasibility. Score: 6
Resources Required: The implementation of an automated monitoring system would require an initial investment in sensors, devices, and software, as well as training for healthcare staff. Ongoing maintenance and support would also be necessary. Score: 7
Overall SPN: The overall solution priority number for this detection approach could be 7.3 (average of the scores).
b.
Prevention Approach
– A prevention approach to ensure the head of the patient's bed is elevated between 30° and 45° could involve the use of physical restraints or positioning aids. These aids could be designed to keep the patient's head in the desired position and prevent unintentional movement or slippage.
Solution Priority Number (SPN) Scale:
Similar to the detection approach, we can evaluate the prevention approach using the SPN scale:
Impact: The impact of using physical restraints or positioning aids would be moderate, as it can help maintain the desired head elevation and reduce the risk of ventilator-associated pneumonia. Score: 6
Feasibility: Implementing physical restraints or positioning aids may require training for healthcare staff and ensuring patient comfort and safety. Score: 7
Resources Required: The resources required for this prevention approach would primarily involve the procurement of appropriate physical restraints or positioning aids, along with any necessary training and
maintenance. Score: 6
Overall SPN: The overall solution priority number for this prevention approach could be 6.3 (average of the scores).
2.
Updated Failure Modes and Effects Analysis - Insert the first nine steps of the FMEA which you completed in prior modules into the table below and complete the remaining rows. Process Step
Identifying areas of improvement in medical care processes and practices.
Potential Failure
Overlooking critical areas for improvement
Potential Failure Effect
Missed opportunities for enhancing care
Severity
8
Potential Cause of Failure
Unclear criteria for identifying improvement areas.
Occurrence Likelihood
5
Current Control
Regular performance reviews and feedback system
Detection
Low visibility of improvement opportunities
Risk Priority Number
40 (Severity * Occurrence * Detection)
Recommended Action
Develop clear criteria for identifying improvement areas
Who and When?
Project Team
Action Completed
Occurrence Likelihood
4
Detection
6
Risk Priority Number
192
3.
Standard Operating Procedures – write an SOP for the
process described in question 2 above.
Standard Operating Procedure (SOP) for Improving Medical Care and Attention
1. Purpose:
The purpose of this Standard Operating Procedure (SOP) is to outline the process for improving medical care and
attention within the organization. This SOP aims to address patient complaints, enhance patient satisfaction, and
ensure a patient-centric approach throughout the healthcare delivery process.
2. Scope:
This SOP applies to all healthcare personnel involved in providing medical care and attention, including but not limited to doctors, nurses, support staff, and administrators.
3. Responsibilities:
3.1. Project Team:
- Develop and implement improvement strategies.
- Identify areas for enhancement based on patient complaints.
- Execute recommended actions.
- Monitor progress and evaluate outcomes.
3.2. Healthcare Personnel:
- Adhere to the revised protocols, guidelines, and practices.
- Report any issues or observations related to medical care and attention.
- Participate in training programs and performance reviews.
4. Process Steps:
4.1. Identifying Improvement Areas:
a. Review patient complaints and feedback collected through surveys, complaint forms, and other feedback channels.
b. Analyze common themes and patterns in patient complaints.
c. Identify specific areas of improvement, such as inadequate identification procedures, insufficient post-
surgical care, short and unsatisfactory doctor appointments, delayed response to urgent situations, unprofessional behavior from healthcare professionals, and discomfort during exams.
d. Document the identified improvement areas for further action.
4.2. Developing Improvement Strategies:
a. Form a project team responsible for developing improvement strategies.
b. Collaborate with relevant stakeholders, including healthcare personnel and patient representatives, to gather insights and perspectives.
c. Conduct root cause analysis to identify the underlying causes of the identified issues.
d. Brainstorm and develop targeted interventions, protocols, and guidelines to address the identified improvement areas.
e. Ensure that the improvement strategies align with the organization's goals and values.
4.3. Implementing Improvement Strategies:
a. Communicate the revised protocols, guidelines, and practices to all healthcare personnel through training sessions, workshops, and written documentation.
b. Provide necessary resources and support to implement the improvement strategies effectively.
c. Monitor and evaluate the adoption and adherence to the revised protocols and practices.
d. Address any challenges or barriers to implementation promptly and effectively.
4.4. Monitoring and Evaluation:
a. Establish performance indicators and metrics to measure the effectiveness of the improvement strategies.
b. Regularly monitor and evaluate patient satisfaction scores, patient complaints, and patient outcomes.
c. Collect feedback from healthcare personnel regarding the impact of the implemented changes.
d. Conduct periodic performance reviews to assess the progress and identify areas for further improvement.
5. Documentation:
All relevant documentation, including patient complaints, improvement strategies, protocols, training materials, and performance evaluation reports, should be appropriately documented and maintained for future reference and continuous improvement purposes.
6. Revision and Continuous Improvement:
This SOP should be reviewed periodically to ensure its effectiveness and relevance. Any necessary revisions should be made based on the evaluation of the improvement strategies and changing organizational requirements.
7. Training and Awareness:
All healthcare personnel should receive appropriate training on this SOP to ensure their understanding and compliance. Regular awareness programs can be conducted to reinforce the importance of providing improved medical care and attention.
8. References:
List any relevant references, guidelines, or standards that support the implementation of this SOP.
9. Approval:
This SOP is approved by [Name and Position] and is effective from [Effective Date].
Your preview ends here
Eager to read complete document? Join bartleby learn and gain access to the full version
- Access to all documents
- Unlimited textbook solutions
- 24/7 expert homework help
4.
Control Plan – develop a control plan using the table below for the process described in question 2 above. Add or delete rows as needed.
Issue
Timing
Measure
Trigger
Owner
Corrective Action
Process
Adjustment
Overlooking critical areas for improvement
Before identification
Review patient complaints and feedback
Completion of patient complaint review
Project Team
Develop clear criteria for identifying improvement areas
Revise identification criteria accordingly
Inadequate post-surgical care
During post-
surgical care
Post-surgical care checklist
Completion of post-surgical care
Healthcare
Personnel
Implement comprehensive post-surgical care
protocols
Update post-
surgical care checklist and protocols
Short and unsatisfactory doctor appointments
During doctor
appointments
Patient feedback surveys
Low patient satisfaction scores
Healthcare
Personnel
Enhance appointment scheduling and communication processes
Improve appointment scheduling system and communication protocols
Delayed response to urgent situations
During urgent
situations
Response time measuremen
t
Exceeding defined response time
Healthcare
Personnel
Implement escalation procedures for urgent situations
Train staff on escalation procedures and establish clear communication channels
Unprofessiona
l behavior from healthcare professionals
Ongoing monitoring
Patient feedback and staff observations
Reports of unprofessional
behavior Healthcare
Personnel
Conduct regular professionalism training and reinforce organizational values
Reinforce code of conduct and values through training and performance evaluations
Discomfort during exams
During exams
Patient feedback and observations
Reports of patient discomfort
Healthcare
Personnel
Improve communication and patient comfort measures during exams
Train staff on effective communication and implement comfort measures during
exams
5.
Control Charts – follow the steps outlined in Chapter 17 of the text beginning on page 247 to create the charts listed below using the “Control Module Data” excel document posted in blackboard. The tabs at the bottom of the excel sheet contain the data for the charts below. Make sure to include your name in the title of each chart and paste an image of the chart in the appropriate section below.
a.
Bar Chart –
3D Chart
b.
Stacked Bar Chart –
c.
Pie Chart – d.
Scatter Diagram –
Your preview ends here
Eager to read complete document? Join bartleby learn and gain access to the full version
- Access to all documents
- Unlimited textbook solutions
- 24/7 expert homework help
e.
X-Bar Control Chart (include Mean, UCL, LCL, and SD lines as displayed in the presentation) 6.
Process Monitoring Communication
– create a process monitoring communication tool for the process you described in question 2 above. Potential options include scheduling boards, Takt boards, issue boards, Kanban Cards, or Check Sheets.
Related Documents
Related Questions
In Agile:
All code should be written before test plans are created in case changes in the
code occur
Test plans should be written before coding begins
All coding should be stopped at a time in the sprint that allows adequate time to
write test plans and perform the testing
Testing is not a part of the sprint
DAD stands for:
Direct Agile Discipline
Disciplined Agile Delivery
Direct Agile Delivery
Detailed Agile Delivery
arrow_forward
Given the removal and replacement time data in the table, calculate IMART (mean time to repair)
Part identity
Bolts
Earth strap
Power lead
Signal lead
Cover plate
Brushes
Lesson 1.2 HW#1
Quantity Failure rate x 10-4 (h) Total M task time (h)
3
0.20
1
0.10
0.36
0.10
0.26
0.35
2
0.46
0.12
0.36
1.16
1.05
23.6
arrow_forward
Suppose a process has been monitored daily for the last ten days and the number of machine failures each day was noted. The results follow:
Day Number: 1 2 3 4 5 6 7 8 9 10
Number of Failures: 8 9 6 10 12 4 9 11 9 12
Compute control limits for a c-chart that monitors the average number of machine failures per day.
Is the process in a state of control?
arrow_forward
Describe the seven basic steps for logical diagnosis.
arrow_forward
Solve correctly please.
(Gpt/Ai wrong answer not allowed)
arrow_forward
SUBJECT: Industrial Safety Engineering
Do not use chatgpt , draw in handwritten note and explain deeply
Draw decision tree for following machines I. Any one machine tool Pump II. Air compressor III. Internal combustion engine IV. Boiler V. Electrical motors.
arrow_forward
In a continuous review inventory system, the lead time for doorknobs is 5 weeks. The standard deviation of demand during thelead time is 85 units. The desired cycle-service level is 99 per-cent. The supplier of door knobs streamlined its operations andnow quotes a one-week lead time. How much can safety stockbe reduced without reducing the 99 percent cycle-service level?
arrow_forward
A. A student establishes the time constant of a temperature sensor by first holding it immersed in hot water and then
suddenly removing it and holding it immersed in cold water. Several other students perform the same test with
similar sensors. Overall, their results are inconsistent, with estimated time constants differing by as much as a
factor of 1.2. Offer suggestions about why this might happen. Hint: Try this yourself and think about control of
test conditions.
B. Which would you expect to be better suited to measure a time-dependent temperature, a thermal sensor (e.g., a
thermocouple) having a small diameter spherical bead or one having a large diameter spherical bead? Why?
arrow_forward
SEE MORE QUESTIONS
Recommended textbooks for you
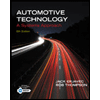
Automotive Technology: A Systems Approach (MindTa...
Mechanical Engineering
ISBN:9781133612315
Author:Jack Erjavec, Rob Thompson
Publisher:Cengage Learning
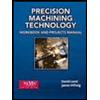
Precision Machining Technology (MindTap Course Li...
Mechanical Engineering
ISBN:9781285444543
Author:Peter J. Hoffman, Eric S. Hopewell, Brian Janes
Publisher:Cengage Learning
Related Questions
- In Agile: All code should be written before test plans are created in case changes in the code occur Test plans should be written before coding begins All coding should be stopped at a time in the sprint that allows adequate time to write test plans and perform the testing Testing is not a part of the sprint DAD stands for: Direct Agile Discipline Disciplined Agile Delivery Direct Agile Delivery Detailed Agile Deliveryarrow_forwardGiven the removal and replacement time data in the table, calculate IMART (mean time to repair) Part identity Bolts Earth strap Power lead Signal lead Cover plate Brushes Lesson 1.2 HW#1 Quantity Failure rate x 10-4 (h) Total M task time (h) 3 0.20 1 0.10 0.36 0.10 0.26 0.35 2 0.46 0.12 0.36 1.16 1.05 23.6arrow_forwardSuppose a process has been monitored daily for the last ten days and the number of machine failures each day was noted. The results follow: Day Number: 1 2 3 4 5 6 7 8 9 10 Number of Failures: 8 9 6 10 12 4 9 11 9 12 Compute control limits for a c-chart that monitors the average number of machine failures per day. Is the process in a state of control?arrow_forward
- Describe the seven basic steps for logical diagnosis.arrow_forwardSolve correctly please. (Gpt/Ai wrong answer not allowed)arrow_forwardSUBJECT: Industrial Safety Engineering Do not use chatgpt , draw in handwritten note and explain deeply Draw decision tree for following machines I. Any one machine tool Pump II. Air compressor III. Internal combustion engine IV. Boiler V. Electrical motors.arrow_forward
- In a continuous review inventory system, the lead time for doorknobs is 5 weeks. The standard deviation of demand during thelead time is 85 units. The desired cycle-service level is 99 per-cent. The supplier of door knobs streamlined its operations andnow quotes a one-week lead time. How much can safety stockbe reduced without reducing the 99 percent cycle-service level?arrow_forwardA. A student establishes the time constant of a temperature sensor by first holding it immersed in hot water and then suddenly removing it and holding it immersed in cold water. Several other students perform the same test with similar sensors. Overall, their results are inconsistent, with estimated time constants differing by as much as a factor of 1.2. Offer suggestions about why this might happen. Hint: Try this yourself and think about control of test conditions. B. Which would you expect to be better suited to measure a time-dependent temperature, a thermal sensor (e.g., a thermocouple) having a small diameter spherical bead or one having a large diameter spherical bead? Why?arrow_forward
arrow_back_ios
arrow_forward_ios
Recommended textbooks for you
- Automotive Technology: A Systems Approach (MindTa...Mechanical EngineeringISBN:9781133612315Author:Jack Erjavec, Rob ThompsonPublisher:Cengage LearningPrecision Machining Technology (MindTap Course Li...Mechanical EngineeringISBN:9781285444543Author:Peter J. Hoffman, Eric S. Hopewell, Brian JanesPublisher:Cengage Learning
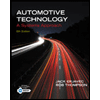
Automotive Technology: A Systems Approach (MindTa...
Mechanical Engineering
ISBN:9781133612315
Author:Jack Erjavec, Rob Thompson
Publisher:Cengage Learning
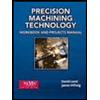
Precision Machining Technology (MindTap Course Li...
Mechanical Engineering
ISBN:9781285444543
Author:Peter J. Hoffman, Eric S. Hopewell, Brian Janes
Publisher:Cengage Learning