Lab 1 Report
docx
keyboard_arrow_up
School
Louisiana State University *
*We aren’t endorsed by this school
Course
3410
Subject
Mechanical Engineering
Date
Feb 20, 2024
Type
docx
Pages
7
Uploaded by carsoncaruso72
CE 3410
Section 1
Mechanics of Materials Laboratory Lab 1 Report
Brinell Hardness Test
Rockwell Hardness Test
Submitted By:
Caroline Johnson
Carson Caruso
Date Performed: Date Submitted:
August 28, 2023 September 10, 2023
Department of Civil and Environmental Engineering
Fall 2023
I.
Purpose
1
The purpose of this experiment is to test the hardness of different materials to compute the corresponding tensile strength. The process of hardness testing involves applying a local load
and observing the resistance to penetration. The materials tested were brass, aluminum, and steel.
The Rockwell hardness test and the Brinell hardness test are both performed to test the hardness of the materials. The difference between the Rockwell and Brinell hardness test depends on the specific material being tested, its surface tension, and the desired level of accuracy. After the tests were performed, the tensile strengths of the materials were compared.
II.
Description During this experiment, each group was given cubes made of brass, steel, and aluminum. The group would take the metal cube they were given and perform a hardness test through two types of testing. The two testing methods used in this laboratory were the Brinell Hardness Test and the Rockwell Hardness Test. Figure 1 and 2 shows the testing mechanisms used. The Brinell Hardness Test was conducted by placing a metal cube on a platform and raised till the penetrating screw was touching the metal cube. After the cube was loaded, each type of metal endured loads of 500 kg, 1000 kg, and 1500 kg for 12 seconds a piece. After indenting the metal 3 times for each specimen, the indention made on the metal was measured using a low power microscope. Using the applied load and the diameter of the indention, the Brinell Hardness Number (BHN) can be found in a table, per ASTM E 10. The second type of testing used for this laboratory was the Rockwell Hardness. During this testing, the cube was placed on a platform and raised to the indenter. Then the students were to adjust the indenter until the small hand was in the vertical position and the dial was at the set position. From there a 100 kilogram load was applied through a 1/16 inch steel ball by pulling down the lever. The Rockwell Hardness Test uses small loads which in turn yields a smaller indention. Instead of measuring the diameter, this test uses the major stress to measure the amount of hardness. The reading on the dial from the major stress gives the hardness number directly. This is done three times to each specimen.
.
2
Figure 1. Brinell Hardness Test
Figure 2. Rockwell Hardness Test
III.
Theory
Brinell Hardness Test:
The equation below is used to find the Brinell Hardness Number (BHN). Once the BHN is found, the tensile strength can also be found. The equation for tensile strength is obtained from
the lab manual and was given during the lab. BHN=
P
πD
2
(
D
−
√
D
2
−
d
2
)
Equation I: Brinell Hardness Number (BHN)
P=applied load
D=indenter diameter d=diameter of the indentation.
Page T1-7 from the lab manual was used to find the tensile strength from the Brinell Hardness Number. The linear interpolation formula was used.
y
2
−
y
1
y
❑
−
y
1
=
x
2
−
x
1
x
❑
−
x
1
Equation II: Linear Interpolation
x=calculated Brinell Hardness number
y=tensile strength to be calculated.
3
Your preview ends here
Eager to read complete document? Join bartleby learn and gain access to the full version
- Access to all documents
- Unlimited textbook solutions
- 24/7 expert homework help
Rockwell Hardness Test:
The Rockwell Hardness Test does not require an equation to calculate the hardness number. Instead, the Rockwell Hardness testing machine displays the hardness number on a dial.
Since a 100 kg load and 1/16 inch indenter was utilized, Rockwell B Number was extracted from
the dial on the machine. The tensile strength from the Rockwell Hardness Test was found using the page T1-7 from the lab manual. The linear interpolation formula, Equation II, is also used in this test. Lastly, Microsoft Excel is again used with this test to find the average and standard deviation, using the same methods utilized in the BHN.
IV.
Results
The below results show the Rockwell Hardness Test findings on steel, aluminum, and brass specimens. The results displayed in Table 1 reflect the Rockwell Hardness Number obtained by Groups A, B, and C while running three tests on each tested material.
Rockwell Hardness Number
Steel
Aluminum
Brass
Group A
67.9
70.0
69.5
48.5
56.0
51.9
40.0
40.5
37.1
Group B
70.2
70.0
68.0
50.0
48.5
50.3
41.4
39.9
41.0
Group C
67.5
69.1
73.1
49.75
49.75
51.2
37.5
35.0
38.5
Table 1. Rockwell Hardness Test Results
Table 2 below displays the results for the Brinell Hardness Test for each group. Brinell hardness
results as averages for each material tested per group is also
displayed in Figure 4. Though the visual similarities of the scatter plots should be taken into
account, the scaling of the dependent variable should also be observed. A smaller
confidence interval tends to suggest a greater certainty for the total average of all samples.
Brinell Hardness Numbers
Load 500 kg
Load 1000 kg
Load 1500 kg
Material
Steel
Alumi-num
Brass
Steel
Aluminum
Brass
Steel
Alumi-num
Brass
Group A
136.1116
85.70615
69.10646
185.1103
94.95028
84.86734
155.5328
103.2625
91.40757
4
157.5472
79.57747
79.57747
153.5041
92.27379
87.23784
155.5328
100.7239
98.273
136.1116
85.70615
69.10646
191.0439
92.27379
87.23784
170.4651
103.2625
111.4487
Group B
22.31672
9.445411
10.22986
22.22873
12.35548
10.90535
26.23938
12.99129
12.30688
14.56776
9.826107
8.121019
16.24204
10.2716
10.5816
12.99129
11.67304
12.64244
13.89042
9.086051
8.425217
16.24204
10.5816
10.90535
17.39626
12.30688
11.67304
Group C
8.746462
13.89042
7.55912
19.65221
10.90535
8.428291
19.78185
12.64244
9.787353
8.425217
14.56776
7.299342
15.66536
12.35548
7.782028
21.1573
10.02893
10.53812
8.746462
14.56776
8.425217
16.85043
10.5816
7.782028
19.78185
11.08489
10.27905
Table 2. Brinell Hardness Test Results Figure 3 below displays a comparison of results between all three groups of the Rockwell
Hardness Test. Figure 3. Rockwell Hardness vs. Material
Brinell Hardness vs. Load Separated by Material
5
Figure 4. Brinell Hardness Scatter Plots with Confidence Ellipses
V.
Discussion
The Rockwell Hardness results in Table 1 shows that all of the groups had very similar results with steel. The Rockwell Hardness was 69.5, the copper had a Rockwell hardness of 39.0,
and the aluminum had a rockwell hardness of 50.5. In figure 3, The rockwell Hardness test shows that the material with the greatest strength was steel, then aluminum, then finally copper. The results from this test indicate precision and accuracy. The results from the Brinell hardness test indicate that there was an error in calculation for one of the groups A, B, or C. Presented in table 2 and figure 4, the data shows that Group A has significantly higher numerical values than Group B and C. Even with the difference in numerical data between the groups, the steel data from Group B, and the aluminum data from group C, there is a positive correlation between increasing harness and increasing load for the test in figure 4. Group A and B reveal that the load applied for steel shows much less of a correlation with hardness than the other materials, and the data of all groups show a large confidence interval for steel. 6
Your preview ends here
Eager to read complete document? Join bartleby learn and gain access to the full version
- Access to all documents
- Unlimited textbook solutions
- 24/7 expert homework help
The Rockwell Hardness Test showed all groups yielding similar results. This test also leaves less room for error because there is no calculation needed. The diameter also does not have to be measured. The errors that did occur during the Rockwell Hardness test are the zeroing
of the tester, measurement observation, and user error. Errors that occurred during the Brinell Hardness test include user error, calculation error, mechanical error, and measurement error. VI.
Conclusion
The results of the hardness tests indicate that steel exhibited the highest Rockwell
Hardness, followed by aluminum and then brass. The Rockwell Hardness Test showed to have consistent results due to them being fairly similar. The Rockwell Hardness Test displayed that steel was the hardest material, followed by aluminum, then brass. Although all groups had miniscule differences, Group B finished with the greatest values, followed by Group A then B. This test demonstrated advantages in terms of simplicity and reduced potential for measurement errors.
The Brinell Hardness Test results showed that Group A had significantly higher values compared to Groups B and C. This means there could have been a few errors in the laboratory procedure for Group A or B and C. Despite these differences, increasing loads and hardness results showed a correlation for all groups. It revealed a general trend of increasing hardness with
increasing load. The Brinell Test results also revealed a larger confidence interval for steel across
all groups. 7
Related Documents
Related Questions
Question 8. The following figure represents three hardness-testing techniques of materials.
Describe their specifications, how there are conducted and their potential applications?
8 -
Shape of Indentation
Test
Indenter
Side View
Top View
Load
Brinell
10-mm sphere
P
of steel or
tungsten carbide
Vickers
Diamond
136°
microhardness
ругamid
Rockwell and
60 kg)
100 kg } Rockwell
150 kg)
Diamond
120°
superficial
cone:
s - in.-
diameter
Rockwell
15 kg
30 kg } Superficial Rockwell
45 kg)
steel spheres
arrow_forward
In your summer internship, you are tasked with measuring the ultimate tensile strength of a material to determine if it meets your company’s (Superior Super Ships Inc) specification. Your boss is worried that the new low-cost supplier, Shoddy Alloys Inc, may not be reliable but it is the only way to source on-time the SS304 needed to make finishings for Jeff Bezos’ new yacht, the Black Pearl. You collect several load versus displacement curves, as illustrated below. The initial diameter of the round gauge section is 0.25 in.
You also collect the instantaneous diameter of the specimen during the test using a laser.
Using the provided data, calculate what is the ultimate tensile strength measured in this test?
arrow_forward
Test Specimen
4140 CF steel
6061 T6 Al
Gray Cast iron 40
FC Brass 360
Impact Energy (J or ft-lb)
48.5 ft-lb
25 ft-lb
12 ft-lb
27 ft-lb
Impact Strength (J/m
or ft-lb/in)
123.096 ft-lb/in
63.452 ft-lb/in
What is the final analysis/ overall observation from the data?
30.457 ft-lb/in
68.528 ft-lb/in
arrow_forward
Figure 1 shows the tensile testing results for different materials. All specimens have an initial
diameter of 12 mm and an initial gauge length of 50 mm.
300
250
Low carbon steel
Network polymer
200
Crystalline polymer
150
Amorphous polymer
100
50
5
10
15
20
25
30
Strain (%)
Figure 1: Stress-strain curve
b. Determine the following parameters for each material:
• the tensile strength
the 0.2% offset yield strength
the modulus of elasticity
• the ductility
Stress (MPa)
LO
arrow_forward
Review
Data taken from a stress-strain test for a ceramic are
given in the table. The curve is linear between the origin
and the first point.
No elements selected
a(ksi)
50 +
40 -
30
Figure
1 of 1
20
10 +
o (ksi)
€ (in./in.)
ex 10(in./in.)
0.5
1.0
1.5
2.0
2.5
33.2
0.0006
45.5
0.0010
Press (ENTER) to select this element. Press ESC) to return to the main menu. Press CTRL+Q) to quit the application.
49.4
0.0014
51.5
0.0018
53.4
0.0022
arrow_forward
You have been given the following test sample data following mechanical testing of 15
test pieces of a modified Alumina.
What is the Weibull modulus of this material?
Would you advise the use of this material over one with a Weibull Modulus of 19.6 and a
mean failure stress of 270 MPa, if you anticipate that the peak stress on the material
could be 255 MPa?
Sample
1
2
3
4
5
6
7
8
9
10
11
12
13
14
15
Select one or more:
a. 185
b. No
Yes
□d. 49
□e. 28.6
3.7
Failure Stress (MPa)
297
293
270
300
g. 22.8
260
296
265
295
280
288
263
290
298
275
arrow_forward
I need assistance designing three structural models on Fusion 360 (bamboo-inspired, bone-inspired, and a control cylinder) for a mechanics project. These models will be tested under compression to compare their load-bearing capacity, energy absorption, and failure modes. Here are the specific details and requirements for each design:
General Requirements:
External Dimensions:
All models must have the same outer dimensions: height = 15 cm, diameter = 5 cm.
Material Volume:
Ensure each design uses approximately the same material volume (e.g., relative density = 30% of the total volume). If you have any other ideas on how to ensure the test is fair between all 3 samples please note it!
File Format:
Provide the designs as STL files compatible with 3D printing or a step-by-step process.
Design Specifications:
1. Control Cylinder:
A simple hollow cylinder with:
Wall Thickness: 2 mm.
Inner Diameter: 4.6 cm (to maintain the outer diameter and wall thickness).
No additional…
arrow_forward
The engineering stress-strain curve below was obtained for a
precipitation hardened Aluminum alloy.
What is the approximate Yield Strength for this alloy in psi?
Engineering Stress Based on Original Area (psi)
50,000
45,000
40,000
35,000
30,000
25,000
20,000
15,000
10,000
5,000
0
O
0.02
0.04
0.06
Aluminum 6061-T6
0.08
0.1
0.12
Engineering Strain (in/in)
0.14
X
0.16
0.18
arrow_forward
Mild steel 1
Young;s modulus 1219.5
Yield strain and stress (0.4101,500.08)
Failure stress and strain :not able to find because the given data shows the experiment did not reach the failure point.
if the material stress and strain does not reach a failure point ,what dose it means , does it means that the material is more stronger?
arrow_forward
Flag question
You have been given the following test sample data following mechanical testing of 15 test pieces of a modified Alumina.
What is the Weibull modulus of this material?
Would you advise the use of this material over one with a Weibull Modulus of 19.6 and a mean failure stress of 270 MPa, if you
anticipate that the peak stress on the material could be 255 MPa?
Sample
1
2
3
4
5
6
7
8
9
10
11
12
13
14
15
Select one or more:
Failure Stress (MPa)
297
293
270
300
260
286
265
295
4
293
280
288
263
290
298
275
arrow_forward
Need help with this Mechanics of Materials review
arrow_forward
A structural member 10 cm long must be able to support a load of 50,000 N without experiencing any plastic deformation. Given the following data for brass, steel, aluminum, and
titanium, rank them from least to greatest weight in accordance with these criteria.
Yield strength
Ultimate tensile
Alloy
Density (g/cm3)
(MPa)
strength (MPa)
Brass
415
600
8.5
Steel
860
800
7.9
Aluminum
310
435
2.7
* 700
Titanium
550
4.5
arrow_forward
Given the following data for five different materials answer parts A B C D E & F with an explanation
arrow_forward
question C please
arrow_forward
(d) Following experimental data (TableQ1b) has obtained from the
torsion test for the specimen dimension given in Table Q1a.
Determine the material of a circular bar. (Take the material
Poisson's Ratio as 0.32)
Table Q1a Specimen Dimensions
Dimensions
Material
Diameter (mm)
6
Length (mm)
77.15
TableQ1b Experimental Results from Torsion test
Angular Deflection
Degree
Radian
Torque/Nm
0.5
0.008727
0.06
1
0.017453
0.47
1.5
0.02618
0.76
2
0.034907
1.01
2.5
0.043633
1.32
3
0.05236
1.65
3.5
0.061087
1.99
4
0.069813
2.32
4.5
0.07854
2.66
5
0.087267
3.00
5.5
0.095993
3.33
6
0.10472
3.64
10
0.174533
5.92
20
0.349066
7.74
30
0.523599
8.07
40
0.698132
8.17
50
0.872665
7.93
60
1.047198
8.10
70
1.221731
8.2
80
1.396264
8.4
90
1.570797
8.24
100
1.74533
8.7
110
1.919863
8.7
120
2.094396
8.7
180
3.141594
9.02
240
4.188792
9.11
300
5.23599
9.48
360
6.283188
9.51
420
7.330386
9.71
arrow_forward
Please complete the following with full workings. :)
arrow_forward
dear tutor please provide neat and clean and detailed answer.
dont copy from google
adress both questions well
arrow_forward
Question 2
You are a biomedical engineer working for a small orthopaedic firm that fabricates rectangular shaped fracture
fixation plates from titanium alloy (model = "Ti Fix-It") materials. A recent clinical report documents some problems with the plates
implanted into fractured limbs. Specifically, some plates have become permanently bent while patients are in rehab and doing partial
weight bearing activities.
Your boss asks you to review the technical report that was generated by the previous test engineer (whose job you now have!) and used to
verify the design. The brief report states the following... "Ti Fix-It plates were manufactured from Ti-6Al-4V (grade 5) and machined into
solid 150 mm long beams with a 4 mm thick and 15 mm wide cross section. Each Ti Fix-It plate was loaded in equilibrium in a 4-point bending
test (set-up configuration is provided in drawing below), with an applied load of 1000N. The maximum stress in this set-up was less than the
yield stress for the…
arrow_forward
SEE MORE QUESTIONS
Recommended textbooks for you
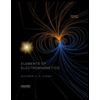
Elements Of Electromagnetics
Mechanical Engineering
ISBN:9780190698614
Author:Sadiku, Matthew N. O.
Publisher:Oxford University Press
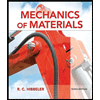
Mechanics of Materials (10th Edition)
Mechanical Engineering
ISBN:9780134319650
Author:Russell C. Hibbeler
Publisher:PEARSON
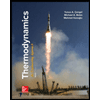
Thermodynamics: An Engineering Approach
Mechanical Engineering
ISBN:9781259822674
Author:Yunus A. Cengel Dr., Michael A. Boles
Publisher:McGraw-Hill Education
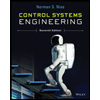
Control Systems Engineering
Mechanical Engineering
ISBN:9781118170519
Author:Norman S. Nise
Publisher:WILEY
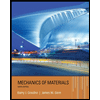
Mechanics of Materials (MindTap Course List)
Mechanical Engineering
ISBN:9781337093347
Author:Barry J. Goodno, James M. Gere
Publisher:Cengage Learning
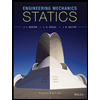
Engineering Mechanics: Statics
Mechanical Engineering
ISBN:9781118807330
Author:James L. Meriam, L. G. Kraige, J. N. Bolton
Publisher:WILEY
Related Questions
- Question 8. The following figure represents three hardness-testing techniques of materials. Describe their specifications, how there are conducted and their potential applications? 8 - Shape of Indentation Test Indenter Side View Top View Load Brinell 10-mm sphere P of steel or tungsten carbide Vickers Diamond 136° microhardness ругamid Rockwell and 60 kg) 100 kg } Rockwell 150 kg) Diamond 120° superficial cone: s - in.- diameter Rockwell 15 kg 30 kg } Superficial Rockwell 45 kg) steel spheresarrow_forwardIn your summer internship, you are tasked with measuring the ultimate tensile strength of a material to determine if it meets your company’s (Superior Super Ships Inc) specification. Your boss is worried that the new low-cost supplier, Shoddy Alloys Inc, may not be reliable but it is the only way to source on-time the SS304 needed to make finishings for Jeff Bezos’ new yacht, the Black Pearl. You collect several load versus displacement curves, as illustrated below. The initial diameter of the round gauge section is 0.25 in. You also collect the instantaneous diameter of the specimen during the test using a laser. Using the provided data, calculate what is the ultimate tensile strength measured in this test?arrow_forwardTest Specimen 4140 CF steel 6061 T6 Al Gray Cast iron 40 FC Brass 360 Impact Energy (J or ft-lb) 48.5 ft-lb 25 ft-lb 12 ft-lb 27 ft-lb Impact Strength (J/m or ft-lb/in) 123.096 ft-lb/in 63.452 ft-lb/in What is the final analysis/ overall observation from the data? 30.457 ft-lb/in 68.528 ft-lb/inarrow_forward
- Figure 1 shows the tensile testing results for different materials. All specimens have an initial diameter of 12 mm and an initial gauge length of 50 mm. 300 250 Low carbon steel Network polymer 200 Crystalline polymer 150 Amorphous polymer 100 50 5 10 15 20 25 30 Strain (%) Figure 1: Stress-strain curve b. Determine the following parameters for each material: • the tensile strength the 0.2% offset yield strength the modulus of elasticity • the ductility Stress (MPa) LOarrow_forwardReview Data taken from a stress-strain test for a ceramic are given in the table. The curve is linear between the origin and the first point. No elements selected a(ksi) 50 + 40 - 30 Figure 1 of 1 20 10 + o (ksi) € (in./in.) ex 10(in./in.) 0.5 1.0 1.5 2.0 2.5 33.2 0.0006 45.5 0.0010 Press (ENTER) to select this element. Press ESC) to return to the main menu. Press CTRL+Q) to quit the application. 49.4 0.0014 51.5 0.0018 53.4 0.0022arrow_forwardYou have been given the following test sample data following mechanical testing of 15 test pieces of a modified Alumina. What is the Weibull modulus of this material? Would you advise the use of this material over one with a Weibull Modulus of 19.6 and a mean failure stress of 270 MPa, if you anticipate that the peak stress on the material could be 255 MPa? Sample 1 2 3 4 5 6 7 8 9 10 11 12 13 14 15 Select one or more: a. 185 b. No Yes □d. 49 □e. 28.6 3.7 Failure Stress (MPa) 297 293 270 300 g. 22.8 260 296 265 295 280 288 263 290 298 275arrow_forward
- I need assistance designing three structural models on Fusion 360 (bamboo-inspired, bone-inspired, and a control cylinder) for a mechanics project. These models will be tested under compression to compare their load-bearing capacity, energy absorption, and failure modes. Here are the specific details and requirements for each design: General Requirements: External Dimensions: All models must have the same outer dimensions: height = 15 cm, diameter = 5 cm. Material Volume: Ensure each design uses approximately the same material volume (e.g., relative density = 30% of the total volume). If you have any other ideas on how to ensure the test is fair between all 3 samples please note it! File Format: Provide the designs as STL files compatible with 3D printing or a step-by-step process. Design Specifications: 1. Control Cylinder: A simple hollow cylinder with: Wall Thickness: 2 mm. Inner Diameter: 4.6 cm (to maintain the outer diameter and wall thickness). No additional…arrow_forwardThe engineering stress-strain curve below was obtained for a precipitation hardened Aluminum alloy. What is the approximate Yield Strength for this alloy in psi? Engineering Stress Based on Original Area (psi) 50,000 45,000 40,000 35,000 30,000 25,000 20,000 15,000 10,000 5,000 0 O 0.02 0.04 0.06 Aluminum 6061-T6 0.08 0.1 0.12 Engineering Strain (in/in) 0.14 X 0.16 0.18arrow_forwardMild steel 1 Young;s modulus 1219.5 Yield strain and stress (0.4101,500.08) Failure stress and strain :not able to find because the given data shows the experiment did not reach the failure point. if the material stress and strain does not reach a failure point ,what dose it means , does it means that the material is more stronger?arrow_forward
- Flag question You have been given the following test sample data following mechanical testing of 15 test pieces of a modified Alumina. What is the Weibull modulus of this material? Would you advise the use of this material over one with a Weibull Modulus of 19.6 and a mean failure stress of 270 MPa, if you anticipate that the peak stress on the material could be 255 MPa? Sample 1 2 3 4 5 6 7 8 9 10 11 12 13 14 15 Select one or more: Failure Stress (MPa) 297 293 270 300 260 286 265 295 4 293 280 288 263 290 298 275arrow_forwardNeed help with this Mechanics of Materials reviewarrow_forwardA structural member 10 cm long must be able to support a load of 50,000 N without experiencing any plastic deformation. Given the following data for brass, steel, aluminum, and titanium, rank them from least to greatest weight in accordance with these criteria. Yield strength Ultimate tensile Alloy Density (g/cm3) (MPa) strength (MPa) Brass 415 600 8.5 Steel 860 800 7.9 Aluminum 310 435 2.7 * 700 Titanium 550 4.5arrow_forward
arrow_back_ios
SEE MORE QUESTIONS
arrow_forward_ios
Recommended textbooks for you
- Elements Of ElectromagneticsMechanical EngineeringISBN:9780190698614Author:Sadiku, Matthew N. O.Publisher:Oxford University PressMechanics of Materials (10th Edition)Mechanical EngineeringISBN:9780134319650Author:Russell C. HibbelerPublisher:PEARSONThermodynamics: An Engineering ApproachMechanical EngineeringISBN:9781259822674Author:Yunus A. Cengel Dr., Michael A. BolesPublisher:McGraw-Hill Education
- Control Systems EngineeringMechanical EngineeringISBN:9781118170519Author:Norman S. NisePublisher:WILEYMechanics of Materials (MindTap Course List)Mechanical EngineeringISBN:9781337093347Author:Barry J. Goodno, James M. GerePublisher:Cengage LearningEngineering Mechanics: StaticsMechanical EngineeringISBN:9781118807330Author:James L. Meriam, L. G. Kraige, J. N. BoltonPublisher:WILEY
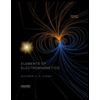
Elements Of Electromagnetics
Mechanical Engineering
ISBN:9780190698614
Author:Sadiku, Matthew N. O.
Publisher:Oxford University Press
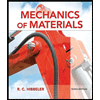
Mechanics of Materials (10th Edition)
Mechanical Engineering
ISBN:9780134319650
Author:Russell C. Hibbeler
Publisher:PEARSON
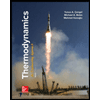
Thermodynamics: An Engineering Approach
Mechanical Engineering
ISBN:9781259822674
Author:Yunus A. Cengel Dr., Michael A. Boles
Publisher:McGraw-Hill Education
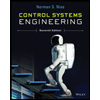
Control Systems Engineering
Mechanical Engineering
ISBN:9781118170519
Author:Norman S. Nise
Publisher:WILEY
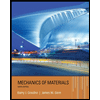
Mechanics of Materials (MindTap Course List)
Mechanical Engineering
ISBN:9781337093347
Author:Barry J. Goodno, James M. Gere
Publisher:Cengage Learning
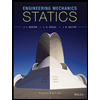
Engineering Mechanics: Statics
Mechanical Engineering
ISBN:9781118807330
Author:James L. Meriam, L. G. Kraige, J. N. Bolton
Publisher:WILEY