CEE353 Civil Engineering Materials Lab Manual-Updated Fall 2019 (1)
pdf
keyboard_arrow_up
School
Arizona State University *
*We aren’t endorsed by this school
Course
353
Subject
Mechanical Engineering
Date
Feb 20, 2024
Type
Pages
103
Uploaded by ProfEelPerson978
CEE353/CNE353 C
IVIL E
NGINEERING M
ATERIALS
CEE353/CNE353 C
IVIL E
NGINEERING M
ATERIALS Laboratory Instruction Manual
* Please check every Monday for updated lab manual
C
IVIL E
NGINEERING M
ATERIALS Table of Contents LAB 1: MEASUREMENT CONCEPTS ...........................................................................................................
1 LAB 2: TENSION TEST OF STEEL AND ALUMINUM (ASTM E-8) & CHARPY V-NOTCH IMPACT TEST ON STEEL (ASTM E23) .........................................................................................................................
5 Part 1: Tension Test of Steel and Aluminum ..............................................................................................
5 Part 2: CHARPY V-NOTCH IMPACT TEST ON STEEL (ASTM E23) .................................................
................................
14 Part I: Rebound Hammer (ASTM C805) ....................................................................................................
15 Part II: Ultrasonic Pulse Velocity (UPV) testing (ASTM C597) ..............................................................
17 Part III: Image Analysis using ImageJ Software ......................................................................................
20 LAB 4: VISCOSITY OF LIQUIDS ............................................................................................................
23 LAB 5: FIBER-REINFORCED COMPOSITES AND CREEP OF POLYMERS .......................................
32 LAB 6: COMPRESSION TESTING OF WOOD .......................................................................................
38 LAB 7 & 8: AGGREGATES .............................................................................................................................
43 PART I: Sieve Analysis (ASTM C136) ........................................................................................................
43 PART II: Specific Gravity and Absorption of Coarse Aggregate (ASTM C127) .....................................
46 PART III: Dry Rodded Unit Weight and Voids in Aggregate (ASTM C29) ............................................
48 PART IV: Specific Gravity and Absorption of Fine Aggregate (ASTM C128) ........................................
49 PART V: Moisture Content of Aggregate Stockpiles (ASTM C566) ........................................................
51 PART VI: Uncompacted Void Content of Fine Aggregate (ASTM C1252) and Coarse Aggregate (AASHTO T 326) ...........................................................................................................................................
52 LAB 9: MIXING CONCRETE AND FRESH PCC PROPERTIES ..............................................................
56 PART I –
Concrete Mixing (by weight) .................................................................................................
56 PART II: Slump Test of Freshly Mixed Portland cement Concrete (ASTM C143) .............................
59 PART III: Air Content of Freshly Mixed Concrete by Pressure Method (ASTM C231) .......................
61 PART IV: Making and Curing Concrete Cylinders and Beams (ASTM C31) ........................................
63 LAB 10: HARDENED PROPERTIES OF PCC ........................................................................................
66 PART I: Compressive Strength of Cylindrical Concrete Specimens (ASTM C39) .................................
66 PART II: Flexural Strength of Concrete (ASTM C78) ...............................................................................
68 PART III: Splitting Tensile Strength of Cylindrical Concrete Specimens (ASTM C496) ......................
71 PART IV: Ultrasonic Pulse Velocity ...........................................................................................................
72 LAB 11: ASPHALT CEMENT TESTING AND GYRATORY COMPACTION ..........................................
74 PART I: Viscosity Determination of Asphalt Using a Rotational Viscometer (ASTM D4402) ............
74 PART II: Penetration Test of Asphalt Binder (ASTM D5) .......................................................................
77 PART III: Dynamic Shear Modulus of Asphalt Cement (ASTM D7175) .............................................
80 PART IV: Gyratory Compaction (ASTM D6925) .......................................................................................
82 LAB 12: ASPHALT CONCRETE TESTING .................................................................................................
87 PART I: Theoretical Maximum Specific Gravity of Hot Mix Asphalt (ASTM D2041) ..........................
87 PART II: Bulk Specific Gravity of Compacted Bituminous Mixtures (ASTM D2726) ..........................
89 10 LAB 3: MICROSTRUCTURE OF MATERIALS AND NDT (ASTM C597 & C805) CEE353/CNE353
Your preview ends here
Eager to read complete document? Join bartleby learn and gain access to the full version
- Access to all documents
- Unlimited textbook solutions
- 24/7 expert homework help
PART III: Mechanical Test ....................................................................................................................
94 Notes
-
For these labs you will need to review the ASTM or AASHTO standards prior to coming to the lab and when performing calculations. ASTM standards can be obtained digitally by going to http://library.lib.asu.edu/record=e1001646~S3
. AASHTO standards can be found in Knovel. -
Discussion questions may be modified during the course of the semester. Always pay attention to the TA in lab sessions for changes to the discussion questions.
Page 1 LAB 1: MEASUREMENT CONCEPTS Significance: Today’s
lab will let you examine some of the most commonly-used laboratory measurement
devices in Civil Engineering Materials experiments. These devices will be utilized in the
upcoming labs throughout the semester, and therefore it is important to gain a good
understanding of their characteristics, capabilities, and use. Apparatus: -
Load cell -
Strain gage -
Dial gage -
Proving ring -
Linear Variable Displacement Transducer (LVDT) -
Length measurement tools. Prior to this lab go to the internet and look up a photograph of a load cell, strain
gage, dial gage, proving ring, and LVDT and search to learn about the essential
function and operation of each device looking specifically for the physical quantity
that each device measures and the overall method by which this physical
measurement is taken. For example you should know that a proving ring measures
mass/force and does this based on measuring the elastic deformation of a ring and
then using this deformation with a known relationship between ring deformation
and mass. Also make sure that you are familiar with all terms that are given in the
procedure, e.g., what is meant by range, sensitivity or any other unfamiliar terms.
Procedure: 1.
Examine the dial gage, note its sensitivity and range, and state where it would be
used in a real-life application. 2.
Examine the strain gage and comment on its use. 3.
Examine the load cell and comment on its use. 4.
Examine the LVDT and comment on its use. a.
For the LVDT: Using the micrometer, adjust the displacement, recording the
five values “to
the left,”
and four values “to
the right”
of the zero point (see
Table 1-1). b.
Keep the following in mind: -
Ideally, the LVDT is “zeroed”
when the micrometer reads exactly 0.500
inches. -
One “rotation”
of the micrometer is equal to 0.025 inches of displacement. 5.
Examine the proving ring and attached dial gauge, and comment on its use. Fill out
Table 1-2 below, and keep the following in mind: -
Before you start measuring, make sure that the large hand is exactly on
zero, and adjust it if necessary. -
Note the initial position of the small hand of the dial gage. One full
“rotation”
of the large dial corresponds to one increment of movement on
the small dial. -
With the dial gage in the protective “cage,”
carefully stack the weights on.
Page 2 -
Before you measure the unknown weight, check once again that the large
hand is exactly on zero. 6.
For the given specimens of concrete (or asphalt), use the appropriate techniques to
accurately measure the lengths and the diameters. Make a table, providing the
dimensions of these members, along with the values that you would use if you are to
report this to a client. Results and Calculations: -
Fill out the tables below and include these tables in your lab report write-up. -
For the LVDT experiment, plot the displacement as a function of the voltage. After
plotting the points, develop an equation for the line that represents the voltage –
displacement relationship and calculate the R
2 for this relationship (Microsoft Excel
can do this for you). Show the best fit equation along with the R-squared value in the
plot you create. -
For the Dial Gage experiment, plot the weight as a function of the dial gauge reading. Calculate the “unknown”
weight, using the equation of the line you graphed under
“Results.”
Again, show the equation and R-squared value on your graph, and label, by
hand, the “unknown”
weight as a point on your graph. The only actual calculation
you must show is solving for the unknown weight. Note that for the latter result, you must convert the dial gage readings to actual
displacements (inches). Do not forget to label all axes (with units), and include an
original chart title. Table 1-1: Displacement with Corresponding Voltage Readings
Displacement (mm)
Distance from Zero
Point (mm)
Voltage Reading (V)
3.
00
-
1.00
2.
00
-
2
.00 1.
00
-
3.
00 0
.00
-
4
.00 5.
00
1.
00 4.
00 = “Zero
Point”
0.000
9.
00
5
.
00
8.
00
4.
00
7.
00
3.
00
6
.
00
2.
00
Your preview ends here
Eager to read complete document? Join bartleby learn and gain access to the full version
- Access to all documents
- Unlimited textbook solutions
- 24/7 expert homework help
Page 3 Table 1-2: Dial Gage Readings for Various Weights on Proving Ring
Weight (lbs)
Dial Gage Reading
(increments)
Deformation (in.)
Unknown Weight
Notes:
Page 4 Group Discussion: 1.
What is meant by accuracy, precision, and sensitivity, and how was this demonstrated
in this lab? 2.
Briefly explain how the micrometer works (i.e. what one full rotation of the rod means,
the relationship between “horizontal”
and “vertical”
increments on the micrometer,
and how the distances are converted to a voltage measurement.) What is the
relationship between voltage and displacement, as examined in the LVDT
experiment? Were the voltage readings within the linear range of the LVDT? After
taking a few readings, was the voltage reading still zero when you returned to 0.500
inches on the micrometer? Explain. 3.
Explain how the dial gage and proving ring work. What does one full rotation of the
“big
arm”
mean? What does one incremental movement of the “small
arm”
mean?
What is the sensitivity and range of the dial gage used? Based on your collected data,
how much does the “unknown”
weight weigh, and does this value make sense? 4.
Is there any discrepancy in your data? Do your graphs look like what you expected?
If yes, explain why. If not, did you encounter any sources of error during the
experiment? Explain. Individual Discussion: 1. Include a brief description (2-3 sentences) of each device you examined. Comment on
its use and real-life application.
Page 5 LAB 2: TENSION TEST OF STEEL AND ALUMINUM (ASTM E-8) & CHARPY V-NOTCH IMPACT TEST ON STEEL (ASTM E23) Part 1: Tension Test of Steel and Aluminum Significance: In this lab, you will observe the uniaxial tension testing of aluminum and steel samples,
according to ASTM E8 –
Tension Testing of Metallic Materials. From the results of the
tests, you will be able to graphically represent the stress-strain relationship, compare the
yield strength and ultimate strength of the two materials, determine elongation and
reduction in cross-sectional area, and find the Young’s
Modulus and rupture strength of
each specimen. Tension test of steel and aluminum →
https://www.youtube.com/watch?v=D8U4G5kcpcM
(
Note that the sample geometry in this video will be different than the one we use for the lab,
but the process will be similar
) Apparatus: -
Small aluminum and steel rods -
Instron testing machine -
Caliper -
Extensometer -
A computer to generate the data points during the test. Procedure: 1.
An overview of what will happen in today’s
lab: a.
A testing machine will apply a uniaxial tensile load at a controlled rate. The
machine will be connected to a computer that automatically provides numerical
values for the changing stress and strain during the testing. (I will post this data
on Blackboard for you to access later on.) b.
Two test specimens, one aluminum and one steel, will be loaded into the
machine. Axial load will be applied to the specimen at a controlled rate, and this
will cause axial stress within the gage length of the specimen. c.
An extensometer will measure the deformation of each specimen. 2.
Before testing, perform these steps: a.
Using a permanent marker, mark a line on each end of the specimen, just before
the threads. This will be L
0
, the original gage length. b.
Using the caliper, measure this gage length three times, and average the measurements to get a “true”
length. Measure the diameter of the specimen in
three different places (i.e. near the two ends and in the middle), and use the
average of these measurements as the “actual”
diameter, d
0
. Record all
measurements, and convert them to millimeters.
Your preview ends here
Eager to read complete document? Join bartleby learn and gain access to the full version
- Access to all documents
- Unlimited textbook solutions
- 24/7 expert homework help
Page 6 A
f
A
0 A
0
c.
Determine the initial cross-sectional area, A
0
, of the specimen, in square
millimeters. 3.
During testing, take note of the following: a.
How does each specimen visibly change as load is being applied? b.
Can you identify the yield point as the computer is generating the stress-strain
curve? c.
How long did it take each specimen to reach its rupture strength? 4.
After testing: a.
Determine the gage length after rupture, L
f
, of the specimen. Line up exactly the
two ends of the ruptured specimen, and measure between the gage length lines
you marked earlier. Again, take three measurements with the caliper, and use
the average as the “true”
value. b.
Determine the final cross-sectional area, using the narrowest diameter of the
ruptured specimen. Again, you will need to line up the two ends of the ruptured
specimen to make this measurement. Calculations: -
Calculate the average initial length (L
0
) and average final length (L
f
) for each
specimen. -
Determine the percent elongation using the following equation. L
f
L
0
% Elongation =
100
L
0
-
Calculate the average initial cross-sectional area (A
0
) and average final cross-
sectional area (A
f
) for each specimen. -
Determine the percent reduction in cross-sectional area using the following
equation. % Reduction in Cross-Sectional Area =
100 Results: -
Summarize your individual and average elongation and cross-sectional area results
in Table 2-1
. -
Plot the stress-strain curve for each specimen. Label the axes appropriately. Estimate the yield strength using the offset method (Section 7.7.1) and a 0.2% offset.
You can draw the required line by hand, but be neat and use a straight edge. Report
the yield strength according to the method given in the standard. You only need to
report values in the units of psi. -
On the same graphs above locate the ultimate strength and the rupture strength on
each curve. Neatly label the yield strength, ultimate strength, and rupture strength
on your graphs. -
For each specimen, find Young’s
Modulus. One way to do this is to create a graph
that shows only the linear portion of the stress-strain curve. Develop a best-fit line
for these points, and label the equation for the line. The slope of this line is Young’s
Modulus. If you use this method, you do NOT need to include these separate graphs
Page 7 in your report. You are only responsible for finding Young’s
Modulus, using your
method of choice. Summarize these results in
Page 8 - Table 2-2.
Your preview ends here
Eager to read complete document? Join bartleby learn and gain access to the full version
- Access to all documents
- Unlimited textbook solutions
- 24/7 expert homework help
Page 9 Table 2-1: Specimen Dimensions
Property
Steel
Aluminum
Length Before Test: After Test: Before Test: After Test: L
1
= L
1
= L
1
= L
1
= L
2
= L
2
= L
2
= L
2
= (in. or mm) L
3
= L
3
= L
3
= L
3
= L
0
= L
f = L
0
= L
f = Diameter d
1 = d
1 = d
1 = d
1 = d
2 = d
2 = d
2 = d
2 = and Area (in. and in.
2 or d
3 = d
3 = d
3 = d
3 = mm andmm
2
) d
0 = d
f = d
0 = d
f = A
0 = A
f = A
f = A
f =
Page 10 Table 2-2: Aluminum and Steel Properties
Material Property
Steel
Aluminum
Estimated 0.2% offset yield
strength (psi or MPa) Tensile strength (psi or MPa) Rupture strength (psi or MPa) Young’s
Modulus (psi or MPa) Percent elongation (%) Percent reduction of cross-
sectional area (%) Type of failure (ductile vs.
brittle) Group Discussion: 1.
Compare the two specimens. As a minimum, include in this comparison the
following items: a.
Which material provided higher yield strength? b.
Did each of the specimens exhibit ductile or brittle failure, and how do you know? c.
What was the plastic range of each specimen (Plastic range = difference between
yield strength and ultimate strength)? d.
Which specimen had the higher percent elongation, and how does this relate to
ductility? e.
How different were the Young’s
Moduli and the rupture strengths of the two
specimens? Individual Discussion: 1. Research the density of steel and aluminum. Combine this information with the
results you obtained to discuss the possible industrial applications of each material?
Page 11 Part 2: CHARPY V-NOTCH IMPACT TEST ON STEEL (ASTM E23) Purpose: In the Charpy V-Notch lab, students will investigate the energy absorbed by different V-
Notch steel specimens using an impact-testing machine. See schematic below for reference.
The amount of energy required to break a material is used to rate the material’s
toughness.
Toughness is a function of the material’s
temperature. Students will perform the Charpy V-
Notch test on four different specimens with properties as follows: -
Specimen #1: Soaked in isopropyl alcohol and dry ice mixture for 1 hour prior to
testing. Approximate testing temperature : -40
°
C -
Specimen #2: Soaked in a mixture of 30% isopropyl alcohol, 70% water, and dry ice
for 1 hour prior to testing. Approximate testing temperature: -20
°
C -
Specimen #3: Soaked in ice-water (using “regular”
ice) for 1 hour prior to testing. Approximate testing temperature: 4
°
C -
Specimen #4: Heated in the oven for 1 hour before testing. Approximate testing temperature: 40
°
C Overview of Testing Apparatus: The impact test machine consists of a 30-kg (66.14-
lb) pendulum that is raised to a given height and
locked in place. The specimen sits in the center
position of the hammer’s
path, with the “V”
notch
facing away from the swing of the hammer. A knob
is used to control when the hammer is released. Once the pendulum is in full swing, it can be
stopped by a small button that creates friction,
slowing down the hammer’s
motion. The top of the
machine has a scale readout to indicate the energy
in ft-lbs. As the hammer swings, a small cantilever
handle moves the readout mark. Safety Precautions: The hammer is extremely heavy and can seriously
injure a student who happens to be standing at the
wrong place during testing. Follow the TA’s
instructions carefully during this lab. But you
should also make sure to adhere to the following
rules: 1.
Do not approach the hammer while being
released or while in swing. 2.
Never stand in front of the hammer’s
swing path. 3.
Make sure that someone is holding up the hammer while specimens are placed in
position. Procedure: 1.
Before testing, each specimen’s
dimensions (length, width, height) will be recorded.
The recorded data set will be provided to the students in order to determine the
length, width, and height expansions after testing. Source: http://www.twi.co.uk/twiimages/
faqplm005f1.gif Figure 2-1: Charpy Test
Apparatus
Your preview ends here
Eager to read complete document? Join bartleby learn and gain access to the full version
- Access to all documents
- Unlimited textbook solutions
- 24/7 expert homework help
Page 12 2.
To account for the effects of friction, the impact machine will be calibrated by
performing a free swing energy dissipation measurement. The calibration procedure
“zeroes”
the testing machine. The gage mark from the free swing will be used as the
“zero”
energy mark. 3.
A thermometer will be used to double check the actual temperature of each specimen
prior to testing. 4.
A tong will be used to remove each specimen from the medium and place into testing
position. In the meantime, a student will have to hold the hammer for safety
reasons. 5.
The gage mark on the readout will be moved to the high end of the scale prior to
each trial. The swinging motion will bring the gage mark back up, indicating the
actual energy measurement. 6.
The hammer will be set in full swing and will break the steel specimen in two upon
impact. The broken specimen will be collected using the tong, and at room
temperature height, width, and length will be measured and recorded. 7.
The fracture pattern of each specimen will be observed. Feel free to take pictures of
the fracture surface of each specimen and comment on the fracture surface. Calculations: All units must be in English customary. Show numerical calculations (with units) when
finding energy absorbed by each steel specimen. Also note the “zeroed”
value of the testing
machine. Results: -
Summarize your measurements in Table 2-3 and Table 2-4. -
Create a temperature versus energy plot, where the energy dissipated is shown as a
function of temperature. -
Connect your four data points using a curve-fit, and label the ductile-to-brittle
transition zone.
Page 13 Table 2-3: Specimen Dimensions
Dimension
Specimen 1
(at -40
°
C)
Specimen 2
(at -20
°
C)
Specimen 3
(at 4
°
C)
Specimen 4
(at 40
°
C)
Length L
0 L
f ΔL
Width W
0 W
f ΔW
Height H
0 H
f ΔH
Table 2-4: Specimen Measurements and Observations
Specimen
#
Actual Temp.
(
°
C)
Energy
(ft-lbs)
Fracture Pattern
1 2 3 4 Notes
Page 14 Group Discussion: 1.
What were the typical failure modes? 2.
Describe the failure surface (pictures or diagrams would be helpful), and comment
on how temperature influences the type of failure mode. 3.
Describe how the dimensions of each specimen changed. Which of the specimens
exhibited the largest/smallest deformation, and why? What does this suggest about
the packing of the atoms (closely packed vs. loosely packed)? Individual Discussion: 1.
What is the relationship between testing temperature and energy required to break
the steel specimen? 2.
What does temperature versus energy relationship suggest about the toughness of
the material at different temperatures? Appendix: Include any handwritten observations/drawings/calculations that you did during lab. Your
actual typed-up calculations should go in the “Calculations”
section.
Your preview ends here
Eager to read complete document? Join bartleby learn and gain access to the full version
- Access to all documents
- Unlimited textbook solutions
- 24/7 expert homework help
Page 15 LAB 3: MICROSTRUCTURE OF MATERIALS AND NDT (ASTM C597 & C805) Purpose: In this lab, you will examine microstructure assessment and nondestructive testing
concepts by doing the following tasks: Predict the strength of concrete using a Rebound
Hammer; Predict the elastic modulus of a material from the wave transmissions through
the material; and Back-calculate material constituents, void fractions, etc. from non-
destructive measurements and Image Analysis software. Equipment and Materials: -
Rebound hammer -
UPV meter -
Calipers and scale -
Image J software (Specimens to be scanned) -
Concrete, Porous Concrete and Asphalt Concrete Specimens Table 3-1: Specimen Properties
Sample
Weight
(lb)
Length
(in.)
Void Ratio
Poisson’s
Ratio
Porous
0.15 OPC
0.20 Asphalt
0.35
Page 16 Part I: Rebound Hammer (ASTM C805) Overview of Testing Apparatus: The rebound hammer consists of a spring-
loaded steel hammer that when released
strikes a steel plunger in contact with the
concrete surface. The spring-loaded hammer
must travel with a consistent and
reproducible velocity. The rebound distance of
the steel hammer from the steel plunger is
measured on a linear scale attached to the
frame of the instrument. The rebound value
depends on the surface hardness of the
concrete and can be related to the
compressive strength of the material. Procedure: 1.
Observe the rebound hammer. Note the different angling positions and associated
curves on the chart provided. 2.
Grind and clean the concrete surface by rubbing with the abrasive stone that
accompanies the rebound hammer. 3.
Firmly hold the hammer in a position that allows the plunger to strike
perpendicular to the testing surface. 4.
Slowly increase the pressure in the plunger by pressing down until you hear the
“click”
and the hammer impacts. 5.
Push the small button near the end of the rebound hammer to hold the reading. 6.
Using the appropriate line on the chart, record the rebound number to two
significant digits. 7.
Press the hammer all the way down to release the small button, and slowly lift up
the hammer. This step resets the readout. 8.
Repeat Steps 1-7 and take 10 readings from each testing area. Record your numbers
in the table below and find the average value. 9.
NOTE: if one data point is not within 7 units of the average, dismiss that data point.
If more than 2 points are not within 7 units of the average, the test must be redone. Calculations: Average the rebound numbers and compressive strengths for each test area. Results: Summarize your measurements and calculations in Table 3-2 below.
Page 17 Table 3-2: Rebound Data
Location 1: Breezeway
Floor (sound)
Location 2: Breezeway
Floor (cracked)
Location 3: Garden
Walls
Angle of Attack: Angle of Attack: Angle of Attack: Trial
#
Rebound
Number Compressive
Strength Rebound
Number Compressive
Strength Rebound
Number Compressive
Strength 1
2
3
4
5
6
7
8
9
10
Avg.
Notes:
Your preview ends here
Eager to read complete document? Join bartleby learn and gain access to the full version
- Access to all documents
- Unlimited textbook solutions
- 24/7 expert homework help
Page 18 Part II: Ultrasonic Pulse Velocity (UPV) testing (ASTM C597) Overview of Testing Apparatus: This test is used to assess the uniformity and quality of concrete. It can indicate the presence of voids and cracks and estimate the depth of cracks. The pulse generator/receiver has a timer that measures the elapsed time between initiation of a wave at the generating transducer and the receipt of the wave at the receiving transducer. This time together with the knowledge of the length of the sample allows for the calculation of the wave velocity. This wave velocity, along with the density of the specimen, can then be used to calculate the elastic modulus of the given sample. *
Note: The testing device has been previously calibrated so that any signal transmission
delay between the 2 cylindrical probes in neglected in all velocity measurements. Procedure: 1.
Before testing, each specimen’s
dimensions (length, width, height) will be recorded. 2.
Make sure that the surface of the specimen is clean. 3.
Turn on the UPV testing device and navigate to the “Test”
menu. 4.
Input the length of the specimen. 5.
Apply a dime-size amount of grease to the two cylindrical receivers in order to make
sure that the sound wave transmits correctly. 6.
Place the first concrete specimen between the cylindrical probes so that the
diameters of the probes are lined up exactly. Make sure that the setup is stable
enough and the receivers do not tip over. 7.
Under the test menu, scroll down to the second line, and press the ENTER. This will
start the sound wave transmission. Students should be hearing 10 fast clicks; the
sending probe is set up to send 10 signals per 1 seconds. 8.
Let the clicks run for about 5-7 times, and record the highest number on the
readout. This is the ultrasonic pulse velocity.
9.
Once you obtain the velocity measurement, hit the CANCEL button to end the test.
The machine should return to the Test Menu. 10.
Carefully remove the concrete specimen from the probes, and check the probes to see
if additional grease is needed. 11.
Repeat Steps 1-8 for the other 4 specimens, and record the ultrasonic pulse velocity
for each. Calculations: Calculate the average pulse velocity of each specimen using the equation: Length
Time
The relationship between the elastic modulus, E, and the calculated pulse velocity is given
by the following equation: V
Your preview ends here
Eager to read complete document? Join bartleby learn and gain access to the full version
- Access to all documents
- Unlimited textbook solutions
- 24/7 expert homework help
Page 19 1
4
G
2
K
V
3
(1) Where K = material bulk modulus;
K
E
3
1
2
E
(2) G = material shear modulus; G
2
1
(3)
= material density (units consistent with units of K and G), and
= Poisson’s
ratio of the specimen Substituting Eqns. (2) and (3) into Eqn. (1) gives: V
Results: -
Summarize the specimen properties in Table 3-3. -
Summarize the UPV results in Table 3-4. Table 3-3: Specimen Properties
Sample
Weight
(lb)
Length
(in.)
Width
(in.)
Height
(in.)
Diameter
(in.)
Volume
(in.
3
)
Density
(lb/in.
3
)
Porous
OPC
Asphalt
E
1
1
2
1
Your preview ends here
Eager to read complete document? Join bartleby learn and gain access to the full version
- Access to all documents
- Unlimited textbook solutions
- 24/7 expert homework help
Page 20 Table 3-4: Ultrasonic Pulse Velocities and Stiffness Values of Specimens
Specimen
Velocity (ft/s)
Elastic Modulus (psi)
Plain Concrete Pervious Concrete Asphalt Notes:
Your preview ends here
Eager to read complete document? Join bartleby learn and gain access to the full version
- Access to all documents
- Unlimited textbook solutions
- 24/7 expert homework help
Page 21 Part III: Image Analysis using ImageJ Software Procedure: Scanning Procedure: 1.
Connect the scanner to one laptop per group 2.
Open Windows Fax and Scan 3.
Place the sample in the middle of the scanner 4.
Press “New
Scan”
5.
In the pop-up window, choose Document, Color, and set the resolution to 600. 6.
Make sure to crop and prepare the pictures as neatly as possible Analysis using ImageJ for circular sections: 1.
Open the image using ImageJ. File>>Open 2.
Crop the image to a circular shape. First select a circular region (Elliptical selection
tool while pressing shift key). Then go to Image>>Crop. The actual diameter of the
circular section is 95 mm. 3.
To specify the outer edges to remove, go to >>Edit>>Selection>>Specify. Enter the
dimensions 900H×900W, ensure Oval is checked and hit OK. Reposition the circle to
include more of the concrete. 4.
Remove the outer edges using Edit>>Clear outside. 5.
Resize the image to 570 pixels by >>Image>>Adjust>>Size (make sure to maintain
the aspect ratio). 6.
Select a 400x400 pixels section on the processed image. Rectangular
selection>>Edit>>Selection>>Specify. Crop the selection. 7.
Save the image in .jpg format for future use. 8.
Now you may analyze the images. 9.
Check whether the image is 8-bit by going to Image>>Type. If it is not an 8-bit
image select 8-bit. 10.
Crop any unwanted sections out if required (scale bar, empty spaces around sample,
etc.) 11.
Threshold the pores (Black phase) by >>Image>>Adjust>>Threshold>>Apply (in the
window). 12.
Note: ImageJ will analyze the areas of the image that have a value=0. To check
which section this corresponds to (pore/solid or aggregate/paste), hover over one of
the sections and note down the value shown on the Fiji Menubar. 13.
Remove the noise in the image by going to Process>>Noise>>Despeckle. Repeat the
process until you get a better image if required. You can also use the short keys
(Ctrl+Shift+R). 14.
Set the measurement data to analyze by going to Analyze>>Set measurements.
Another window will pop up and check for area, shape descriptors, perimeter etc.
Make sure to select “Limit
to threshold”.
15.
Analyze the image by going to Analyze>>Analyze Particles. Select Summarize.
Your preview ends here
Eager to read complete document? Join bartleby learn and gain access to the full version
- Access to all documents
- Unlimited textbook solutions
- 24/7 expert homework help
Page 22 Calculations: Using the Paste/Aggregate and Solids/Void fractions extracted from the ImageJ software,
and the elastic modulus of the pervious concrete in Part II, calculate the Elastic Modulus
of the solids using the following formula. Note that this applies for both OPC, Porous and
Asphalt Concrete: E
conc =E
solids
V
solids
E
voids
V
voids
Noting that the elastic modulus of air is zero and 𝑉
𝑠
olids + 𝑉
𝑣
oid
𝑠
= 1
. Then, using the elastic modulus of the solids, calculate the elastic modulus of the paste using: E
solids
E
paste
V
paste +
E
agg
V
agg
Your preview ends here
Eager to read complete document? Join bartleby learn and gain access to the full version
- Access to all documents
- Unlimited textbook solutions
- 24/7 expert homework help
Page 23 Results: Tabulate the program pore results as shown Table 3-5: Table 3-5: ImageJ Results
Slice
No. of
Pores
(Count)
Total
Area
Area
Fraction
Mean size
E
paste or E
soilds (psi)
Notes:
Your preview ends here
Eager to read complete document? Join bartleby learn and gain access to the full version
- Access to all documents
- Unlimited textbook solutions
- 24/7 expert homework help
Page 24 Group Discussion: 1.
Is the rebound hammer test a legitimate way to determine the strength of in-place
concrete? Justify. 2.
Are the estimated compressive strength values within the acceptable range for
concrete? 3.
Which surface had the highest estimated compressive strength, which had the
lowest, and is this what you expected to see? If not, why not? What could be some
reasons for the discrepancy? 4.
How do the UPV values for the different mix design specimens compare? Which
sample had the highest UPV value, which one had the lowest, and based upon the
relative air void content, do the UPV values make sense? 5.
Are the calculated stiffness values within the acceptable range for concrete? If not,
what could have caused the discrepancy? 6.
Which sample had the highest stiffness and lowest stiffness, and how does this
relate to the amount of air voids in the sample? 7.
How did the pervious concrete specimens compare and why? Individual Discussion: 1.
If the aggregate content was 10% more what would happen to the elastic modulus of
the resultant concrete? 2.
If porosity is increased/decreased to 30% what would happen to the elastic modulus
of the resultant pervious concrete? Appendix Include any handwritten observations/drawings/calculations that you did during lab. Your
actual typed-up calculations should go in the “Calculations”
section.
Your preview ends here
Eager to read complete document? Join bartleby learn and gain access to the full version
- Access to all documents
- Unlimited textbook solutions
- 24/7 expert homework help
Page 24 Significance: In this lab, you will be measuring the viscosity of different liquids through different
methods: rolling-bottle viscometer, Figure 4-1(a); sinking-ball viscometer, Figure 4-1(b); and
a Zahn cup viscometer, Figure 4-1(c). The rolling-bottle viscometer is useful for liquids with
low viscosities, the sinking-ball useful for high viscosity liquids, and the Zahn cup can be
used with liquids from a range of viscosities by changing the specific design details of the
cup. Different experimental techniques will be required to obtain accurate measurements of
this widely varying property of liquids. Figure 4-1. Viscometers used in this lab; (a) rolling-ball viscometer, (b) Sinking-
ball viscometer, and (c) Zahn cup viscometer.
Apparatus: -
Sinking-Ball Viscometer: Single steel ball o
Asphalt cement -
Zahn Cup Viscometer o
Oil samples and paint Procedure: Before testing:
1.
Understand what needs to be done before starting the test. 2.
During testing, take note of the following (include in report): 3.
Does the way the vial with the viscous liquid is being held against the back of the
ramp affect the result? 4.
What is the purpose of waiting while testing the viscous liquid? (c)
(a) (b)
LAB 4: VISCOSITY OF LIQUIDS
Your preview ends here
Eager to read complete document? Join bartleby learn and gain access to the full version
- Access to all documents
- Unlimited textbook solutions
- 24/7 expert homework help
Page 25 5.
Are the tests accurate? 6.
Why does the mass and volume of the liquids in the vials have to be consistent? Rolling-Ball:
1.
Hold vial with one finger at the top of the ramp and release. 2.
Recording the rolling distance. 3.
Repeat 5 times for each liquid and take the average value. Precautions
Handle the vials as little as possible to avoid warming the liquid.
For the more viscous liquid wait about 3 minutes before running the test to
assure temperature is ambient.
Release vial by lifting finger straight up. (Do not push or restrict the vial in any
way) Sinking-Ball
1.
Record height of container and the diameter of the steel ball. (Adding the two will
give the initial height) 2.
Place steel ball in the center of the binder. 3.
Record the height of the steel ball every 3 minutes. 4.
Keep recording until the steel ball disappears from view. Precautions
Once the ball is placed on the surface it cannot be removed.
Stokes law assumes that the particle is sinking in a fluid of infinite extent so
there are no wall effects as it sinks. Zahn-Cup
1.
Record cup number being used and sample number being tested. 2.
Dip cup into fluid until it is completely submerged. 3.
Remove the cup from the fluid in a gentle vertical motion and start the timer. 4.
Observe the fluid coming from the bottom of the cup and stop the timer at the first
break in the fluid stream. Record this time as the efflux time for the sample. 5.
When diluting the paint samples carefully weigh in the mass of water added and
blend thoroughly. We will add water at 0% (non-diluted), 10%, 20%, and 40% by
mass. After testing:
1.
Assure tables are filled completely. 2.
Review calculation section and understand equations. Calculations: For each specimen, show (with both symbols and numbers) how you calculated: Zahn Cup
Zahn cup and similar viscometers utilize the correlation between flow and viscosity. The
time that it takes a fluid to flow is dependent on the orifice that it must flow out of, the
volume of material above the orifice (the head), and the viscosity of the fluid. This
correlation is repeatable and well known even though the mathematics are highly complex.
The cup type viscometers use the repeatable nature of the physical system and sidestep the
Your preview ends here
Eager to read complete document? Join bartleby learn and gain access to the full version
- Access to all documents
- Unlimited textbook solutions
- 24/7 expert homework help
Page 26 complex mathematics with relatively simple empirical expressions to relate the effluent
time to the viscosity. Since the physical conditions suggest that the drain time is dependent
on the orifice diameter a different equation is used for each cup type. The equations are
below where t is the efflux time in seconds and h is the viscosity in Centistokes. Cup #1,
1
.
1
t
29
Cup #2,
3
.
5
t
14
Cup #3,
11
.
7
t
7
.
5
Cup #4,
14
.
8
t
5
Cup #5,
23
t
Likewise there are some general guidelines for selection of the correct cup for a given fluid.
In general the following guidelines are suggested: Cup #1, 18 cSt
56 cSt
Cup #2, 40 cSt
230 cSt
Cup #3, 150 cSt
790 cSt
Cup #4, 220 cSt
1100 cSt
Cup #5, 460 cSt
1725
cSt
Combining the equations above with these ranges in viscosity tells us that the typical Zahn
cup test should take approximately 20 seconds and 80 seconds. Tests taking less than 20
seconds should use a smaller numbered cup and tests taking longer than 80 seconds should
use a higher numbered cup (unless you are already using a #5 cup). Blending Liquids
The Refutas equation suggests that the viscosity of a blend of two viscous liquids is given
by:
VBN
10
.
975
exp
exp
Blend
0
.
8
blend
14
.
534
VBN
Blend
a
VBN
A
b
VBN
B
VBN
i
14
.
534
ln
ln
i
0
.
8
10
.
975
Where; Results: exp
VBN
a,b = = = exponential function (e
j
),
Viscosity Blending Number, Mass proportion of liquid a and liquid b (e.g., if a blend consisted of 40% liquid
= A and 60% liquid B then a = 0.4 and b = 0.6), and
Kinematic viscosity of the liquids (cSt).
Your preview ends here
Eager to read complete document? Join bartleby learn and gain access to the full version
- Access to all documents
- Unlimited textbook solutions
- 24/7 expert homework help
Page 27 -
Summarize your results in Tables 4.1 and 4.2. -
Plot the penetration in the sinking-ball viscometer versus time. -
Use the penetration versus time data with Stokes Law to estimate the viscosity
of the asphalt cement. -
Plot the viscosity versus water content for the paint from the Zahn cup viscometer. Table 4-1: Penetration Depth with Time from Sinking-Ball Viscometer.
Time
Scale Reading
Table 4-2: Zahn Cup Times.
Sample Type
Zahn Cup
Used
Test
Number
Zahn Time
(sec)
Viscosity (cSt)
Oil #1 1 2 3 Oil #2 1 2 3 Latex Paint Non-
Diluted 1 2 3 Latex Paint +
10% water 1
Your preview ends here
Eager to read complete document? Join bartleby learn and gain access to the full version
- Access to all documents
- Unlimited textbook solutions
- 24/7 expert homework help
Page 28 2 3 Latex Paint +
20% water 1 2 3 Latex Paint +
40% water 1 2 3 Group Discussion: 1.
Discuss the results from these tests. Address all of the following issues in
this discussion: a.
What is viscosity? b.
Why is the sinking-ball viscometer so important looking at it from
an applications perspective? c.
What effect does temperature have on viscosity? d.
Does the viscosity calculated from Stokes Law seem reasonable for the
given binder (why or why not)? e.
Discuss any limitations of the test and testing equipment. f.
As always ELABORATE when answering questions in the discussion. 2.
Compare your water-paint blended viscosities to the Refutas equation
predicted results. Discuss any similarities or differences in both the
magnitude of these comparisons and the trend with respect to water content. Individual Discussion: 1. The two oil samples are standard SAE motor oils. Using your results estimate which
two standard grade oils were tested and explain how you made this conclusion. Cite
at least two corroborating references for the standard viscosity of these oils.
Your preview ends here
Eager to read complete document? Join bartleby learn and gain access to the full version
- Access to all documents
- Unlimited textbook solutions
- 24/7 expert homework help
Page 29
Your preview ends here
Eager to read complete document? Join bartleby learn and gain access to the full version
- Access to all documents
- Unlimited textbook solutions
- 24/7 expert homework help
Page 30 LAB 5: FIBER-REINFORCED COMPOSITES AND CREEP OF POLYMERS Objective I.
Understand the influence of fiber orientation on composite properties (E in this case) II.
Be able to use principles of deflection of beams to calculate their properties III.
Be able to set up, conduct and report experimental data in concise engineering terms Materials and Equipment 1.
Fiber reinforced composite sheet from which 5 different beam pieces have been cut
with differing fiber angles (beam size 7 in. long × 1 in. wide × 1/8 in. deep); 2.
A simply supported set up with a span of 6 in. Span is changeable to understand the
effects of span on deflection; 3.
A dial gauge for deformation measurements; 4.
Weights that are incremental by 250 g. Overview of Testing Materials Fiber-reinforced sheets are made up of fibers woven into a cloth mat orienting fibers into
two orthogonal directions: the warp direction (lengthwise in the loom) and the woof
direction (across the loom). When such a mat is used as a composite, the resulting
mechanical properties are influenced by this orientation and are not isotropic. The purpose
of this experiment is to measure the variation of the elastic modulus with respect to the
orientation of the woven reinforcing mat in a composite. The second purpose is to
demonstrate another technique for measure the elastic modulus of a material. The fiber reinforcement is glass and the matrix is a polyester polymer, with the fibers being
placed as several layers of woven mats. The orientation of the specimens that were cut is
shown in Appendix A. the object is to find the elastic modulus of each sample and
determine how this modulus varies with the angle from the warp of the reinforcing mat. Note: The shading of the mat in Appendix A does not necessarily represent the orientation of
the reinforcing fibers.
Procedure 1.
Examine the dial gauge; note its sensitivity and range. Note down the specimen
number being tested. 2.
Before you start measuring, make sure that the large hand is exactly on zero, and
adjust it if necessary. Ensure there is good contact between the gauge head and the
fiber-reinforced composite specimen and that it is located at mid-span. 3.
Carefully stack the weights at mid-span in 250 g increments, up to 1250 g. Gently
tap the dial indicator to ensure the needle is not stuck and read and record the
deflection readings at each load increment. 4.
Remove all the loads and repeat the above process twice (three readings in total) and
calculate the average. 5.
Move to the next station and repeat.
Your preview ends here
Eager to read complete document? Join bartleby learn and gain access to the full version
- Access to all documents
- Unlimited textbook solutions
- 24/7 expert homework help
Page 31 Calculations The mid-span deflection for a simply supported beam is well established. Consult
engineering references to identify the appropriate equation for a simply supported beam
subjected to a center point load. This equation can be rearranged to yield: E
P
f
b
,
h
Results Record the deformation measurements in Table 0-1 and Table 0-2 . Using the results in Table 0-1 and Table 0-2, plot the graph of load (
P
) as a function of
deflection (
), similar to the one shown below in Figure 0-1. Use the same axes for all five
beams and label them appropriately. Use a linear regression to find the slope P/
of each
plot (show on plot) and use it to calculate the Young’s
Modulus of each beam, as outlined in
the Calculations section. Express the Young’s
Modulus in units of pounds per square inch.
Finally prepare a plot of the Young’s
modulus, on the ordinate, versus fiber direction, on the
abscissa. Using the plot, develop a simple equation that relates E to the fiber direction. Figure 0-1: Load versus deflection plot
𝑃
Where
= mid-span deflection, P
= applied load; and ?
= a function of the beam’s width (b) and height (h) [consult the references to
determine
Your preview ends here
Eager to read complete document? Join bartleby learn and gain access to the full version
- Access to all documents
- Unlimited textbook solutions
- 24/7 expert homework help
Page 32 Table 0-1: Dial Gauge Readings
Sample
Weight (g)
Dial Gauge Readings
Deformation
(in.)
Set 1
Set 2
Set 3
Average
1
250 500 750 1000 1250 2
250 500 750 1000 1250 3
250 500 750 1000 1250 4
250 500 750 1000 1250
Your preview ends here
Eager to read complete document? Join bartleby learn and gain access to the full version
- Access to all documents
- Unlimited textbook solutions
- 24/7 expert homework help
Page 33 Table 0-2: Dial Gauge Readings (continued)
Sample
Weight
(g)
Dial Gauge Readings
Deformation
(in.)
Set 1
Set 2
Set 3
Average
5
250 500 750 1000 1250 Table 0-3: Specimen Material Properties
Specimen Fiber Orientation (
°
) Young’s
Modulus (psi)
Group Discussion: 1.
Which fiber orientation do expect displayed the largest/smallest deformation? Why
do you think this is? 2.
What is the relationship between fiber orientation and the materials Young’s
Modulus? 3.
What do your findings suggest about the structural applications of these fiber-
reinforced composite materials? 4.
List at least three items made of Composites; identify the Matrix and Reinforcement
materials for each. 5.
List a few advantages and disadvantages of using fiber-reinforced composites for
structural applications. 6.
Is there any discrepancy in your data? Do your graphs look like what you expected?
If yes, explain why. If not, did you encounter any sources of error during the
experiment? Explain. Individual Discussion: 1.
Most composites are Pseudo-Isotropic, Orthotropic or Anisotropic; what do these
three terms mean? 2.
What is the primary function of the matrix in a composite material?
Your preview ends here
Eager to read complete document? Join bartleby learn and gain access to the full version
- Access to all documents
- Unlimited textbook solutions
- 24/7 expert homework help
Page 34 Appendix Any handwritten notes, such as observations during testing, dial gauge measurements, etc.
Your preview ends here
Eager to read complete document? Join bartleby learn and gain access to the full version
- Access to all documents
- Unlimited textbook solutions
- 24/7 expert homework help
Page 35 CREEP IN POLYMERS Objectives I.
Explain the concept of creep and viscoelasticity using simple experimental tools II.
Be able to predict the creep behavior of a polymer using simple equations for long
term loading III.
Understand the effects of molecular structure on long term deflections. IV.
Understand the concept of fitting equations to describe observed physical
phenomena Materials and Equipment - Samples with dimensions 12”
long × 2”
wide × 0.5”
thick: a)
Low molecular weight polyethylene b)
High molecular weight polyethylene c)
Polycarbonate d)
Polystyrene e)
Poly methyl methacrylate (PMMA) -
Tip loads -
Strain gauges -
Data acquisition system that plots strains as a function of time The five different beams will be above or near their glass transition temperature at room
temperature. However, their viscoelastic properties will be different owing to their different
molecular structures and the fact that some of them are closer to their glass temperatures
than others. Procedure A constant stress must be applied to the material to observe creep. A cantilever beam of
each polymer will have a weight hung from its end, and the strain in the beam will be
monitored as time passes. The loading situation is shown in Figure 0-1 below. The strain
sensed by the gauge will be fed as an electrical signal to a recorder so that a plot of strain
versus time will be obtained directly. Figure 0-1: Cantilever Beam Loading from side and end
Your preview ends here
Eager to read complete document? Join bartleby learn and gain access to the full version
- Access to all documents
- Unlimited textbook solutions
- 24/7 expert homework help
Page 30 Calculations:
The stress at the gauge is given by: 2
Mh
I
=
M
P
l
=
3
12
bh
I
=
The Burger’s model will be used to fit an equation for the creep curves obtained. A Burger’s model is shown below in Figure 2, where each of its mechanical elements has a constant associated with it. It should be noted that polymers are not actually made up of spring and dashpots, but it is merely a convenient way to visualize the various viscoelastic responses in order to derive an equation that describes them. Figure 0-2: Mechanical Representation of Burger's Model
Burger’s equation for creep is:
2
2
1
1
2
1
1
1
E t
t
e
E
E
−
=
+
+
−
𝜎 =
stress 1.
For each polymer, decide how many terms are required in the above equation based on the observed behavior. 2.
Find the values of the constants in the equation, which will have units of a modulus or a viscosity. A
BRIEF NOTE ON VISCOSITIES
: Viscosity is defined as the ratio if sear stress to shear strain rate. In this experiment, normal stresses are applied and normal strain rates are measures, thus the viscosities calculated are not necessarily the same those measured in a classical shearing viscosity test (but are related). The viscosities in this experiment represent the “flow situation” and are the operant viscosities that allow the calculation of normal strains as a function of time where 1
2
where 𝜖 =
strain and 𝜆
are model constants. A particular polymer may not exhibit all three fundamental responses (described by a separate term), in which case the term is simply dropped from the equation. The steps to fit the equation are as follows: ? =
time 𝐸
, 𝜆
, 𝐸
1
2
Your preview ends here
Eager to read complete document? Join bartleby learn and gain access to the full version
- Access to all documents
- Unlimited textbook solutions
- 24/7 expert homework help
Page 31 when normal stresses are applied in the loading situation. Thus, the symbol 𝜆
is used to differentiate them from the true viscosity 𝜂
(which involves shear). The procedure for finding the values of these constants are based on the creep curve obtained from the experiment. A generalized version of the creep curve is shown below in Figure 0-3. Figure 0-3: Generalized Creep Curve
1.
Section I of the curve is the instantaneous elastic response and is governed by the 𝐸
1
term, which is given by: E
1
=
2.
Section III of the curve corresponds to the long-term viscous flow of the material and is associated with the 𝜆
1
, which is governed by the slope of the linear section III: 1
=
3.
The extrapolation of the section III portion of the creep curve back till it intersects with zero time provides
𝜖
2
, which is the sum of both the instantaneous and delayed elastic strains. This, 𝜖
2
− 𝜖
1
represents the amount of delayed elastic strain and is governed by 𝐸
2
in the general equation, given by: 2
2
1
E
=
−
4.
The value 𝜆
2
controls the curvature of section II of the creep curve. It can be found by taking a data point within section II (
?
II
, 𝜖
II
)
and putting these into the overall equation with the previously calculated values of 𝐸
1
, 𝐸
2
and 𝜆
1
and solving for 𝜆
2
. It is best to do this along several points along the curved portion and using the average as
𝜆
2
. Section II
Section I
Section III
Time
Your preview ends here
Eager to read complete document? Join bartleby learn and gain access to the full version
- Access to all documents
- Unlimited textbook solutions
- 24/7 expert homework help
Page 32 Perform a sanity check of your resulting equation by calculating several strains that should
develop at several times during the first few minutes of loading. These calculated strains
should be close to those that were actually measured. Use your equations to calculate the expected strain at the gauge if a 1 kg weight were hung
on the beams for 1 month. Also, calculate the time that will be required for a 1 kg weight to
generate a strain of 0.1 in/in (10%) at the gauge. Report these values in tabular form in
your results. Include all calculations as part of the report!
Results Of the five different beams, only the polystyrene and poly methyl methacrylate needs to
be fit for an equation using the creep data using the calculations above. 1.
Include a tabular summary of the constants for both polymers, with the moduli
being reported as pounds per square inch (psi) and viscous constants in units of
poise; 1 poise = 1 dyn · s/cm
2
. 2.
Also include the strain v. time plots used for the calculations, adequately labeling
the different sections and the corresponding model constants/variables on the plot
(similar to Figure 0-3). Group Discussion: 1.
Why are the materials “viscoelastic”?
What is meant by this term? 2.
Briefly talk about the various models used to represent viscoelastic materials and
discuss their limitations. 3.
Describe the three main stages of creep and what they represent. (Bonus: show a
plot (strain as a function of time) representing the three main stages of creep with
the stages adequately labeled). 4.
How did the creep deformation of the five different beams differ? Which one
demonstrated the most and least strain? 5.
How did the strain v. time plot differ for each specimen? What does this tell you
about their “spring
and dashpot”
behavior? 6.
Understanding the relationship between instantaneous and delayed elastic
response, how does the strain behave at prolonged periods? What do you think
would happen after the load is removed? 7.
How does temperature affect creep? 8.
What are the real structural applications of creep? Individual Discussion: 1.
Given that you have characterized a reference material with the Burger’s
model.
Examine the two scenarios below. Then identify and explain which model parameter
will change and whether that parameter will increase or decrease. a.
Under a fixed load, the instantaneous strain value is larger than that of the
reference material. b.
Under a fixed load, the instant strain value is the same as the reference
material, but the rate of strain accumulation after 2 minutes is greater.
Your preview ends here
Eager to read complete document? Join bartleby learn and gain access to the full version
- Access to all documents
- Unlimited textbook solutions
- 24/7 expert homework help
Page 38
Your preview ends here
Eager to read complete document? Join bartleby learn and gain access to the full version
- Access to all documents
- Unlimited textbook solutions
- 24/7 expert homework help
Page 39 Significance: This test allows us to compare mechanical properties of various species and data for
establishing strength functions. The test provides us with information about how the
moisture content of wood influences the strength of wood in compression. Bending test on wood →
http://vimeo.com/1704966 (Note: This video is for bending test and you will be doing a compression test) Test Specimens: Table 0-1: Dimensions of Test Specimen
Specimen
Condition
Average Initial
Length
(in. or mm)
Average Initial
Width
(in. or mm)
Average Initial
Depth
(in. or mm)
Poplar
Saturated Oven Dried Ambient Oak
Saturated Oven Dried Ambient Apparatus: -
Compression Testing Machine -
Calipers and scale Procedure 1.
Measure the length, width, and height of each specimen in 3 different places, and
record the average values. 2.
Measure the weight of each specimen and record the values. 3.
Load the specimen vertically in the compression testing equipment so that the
application of load is parallel to the direction of the grains. Additional Information
: COMPRESSION TESTING OF WOOD
Each group will receive 6 specimens: 1 saturated, 1 oven-dried and 1 ambient wood sample
of both Poplar (Low Density Hardwood) and Oak (High Density Hardwood) wood species
with the general dimension of 1.5”×1.5”×6”.
Initial dimensions of samples subject to
saturation or oven-drying will be provided by the TA. Summarize these values in the table
below.
Your preview ends here
Eager to read complete document? Join bartleby learn and gain access to the full version
- Access to all documents
- Unlimited textbook solutions
- 24/7 expert homework help
Page 49 4.
Apply load at a constant rate of 50lb/sec, or at a known constant rate that will run
the test within a reasonable time (ASTM recommends a strain rate of 0.003 mm/mm
(in/in)). 5.
Continue loading the specimen until maximum load is reached, or if no peak is
reached, until the load approaches a constant value. Observe when the specimen
first starts to fail, and make note of any other observations during testing. 6.
Stop the test. Remove the specimen from the machine and observe the failure type
and direction of failure line. Calculations Calculate the stress and strain for each specimen (if you do not know how to calculate
stress and strain review your statics and deformable solids notes). Calculate the moisture content of the saturated and ambient specimens using the equation: m
m
od
100 is the mass of the oven-dried wood. Results -
Summarize the dimensions after testing in Table 0-2. -
Summarize the sample dimensional properties in Table 0-3. -
Summarize the characteristics of the test samples in Table 0-4 and Table 0-5. Table 0-2: Sample Dimensions After Testing
Specimen
Condition
Average Final
Length
(in. or mm)
Average Final
Width
(in. or mm)
Average Final
Depth
(in. or mm)
Poplar
Saturated Oven Dried Ambient Oak
Saturated Oven Dried Ambient where MC
m
od
m
od
Your preview ends here
Eager to read complete document? Join bartleby learn and gain access to the full version
- Access to all documents
- Unlimited textbook solutions
- 24/7 expert homework help
Page 41 Table 0-3: Sample Dimensional Properties
Specimen
Condition
Change in Length
(in. or mm)
Change in Width
(in. or mm)
Change in Depth
(in. or mm)
Poplar
Saturated Oven Dried Ambient Oak
Saturated Oven Dried Ambient Table 0-4: Characteristics of Specimens in Compression
Specimen
Condition
Volume
(in.
3 or mm
3
)
Weight
(kg or lb)
Density
(lb/in
3 or kg/m
3
)
Poplar
Saturated Oven Dried Ambient Oak
Saturated Oven Dried Ambient
Your preview ends here
Eager to read complete document? Join bartleby learn and gain access to the full version
- Access to all documents
- Unlimited textbook solutions
- 24/7 expert homework help
Page 42 Table 0-5: Characteristics of Specimens in Compression
Specimen
Condition
Maximum
Stress
(psi or MPa)
Maximum
Strain
Moisture
Content (%)
Failure
Observations
Poplar
Saturated Oven Dried Ambient Oak
Saturated Oven Dried Ambient Notes:
Your preview ends here
Eager to read complete document? Join bartleby learn and gain access to the full version
- Access to all documents
- Unlimited textbook solutions
- 24/7 expert homework help
Page 43 Group Discussion: 1.
Note the type of timber used, and the rate of load application. Compare the six
samples. Which samples displayed the most deformation (pictures or diagrams
would be helpful)? Also describe how the dimensions of each specimen changed. 2.
Is timber stronger when saturated, oven-dried or at ambient conditions? 3.
Which type of timber was able to withstand the most applied pressure? How
different were the failure strengths of each material? 4.
How does the density of the timber affect its ability to withstand loads? 5.
Which of the two materials was most affected by the saturation and drying process
(compare with initial dimensions provided by the TA)? Why do you think this is? 6.
Why is the moisture content of wood species important? Would the best wood to be
used in outdoor structural purposes be the oven-dried wood? Why or why not? 7.
What is meant by the Equilibrium Moisture Content (EMC)? Why is this important? 8.
List a few advantages and disadvantages of drying timber for structural
applications. 9.
How do you think the timber would react if loaded perpendicular to the grain? Individual Discussion: 1. Explain what do your findings suggest about the nature and possible uses of each
material?
Your preview ends here
Eager to read complete document? Join bartleby learn and gain access to the full version
- Access to all documents
- Unlimited textbook solutions
- 24/7 expert homework help
Page 44 Significance: In today’s
lab, you will be performing many different experiments –
sieve analysis of a
given mixture of aggregates, determining the dry rodded unit weight (DRUW) of a coarse
aggregate, bulk specific gravity of a coarse and fine aggregate, moisture content of fine and
coarse aggregate, and fine aggregate angularity.
Sieve Analysis →
http://www.youtube.com/watch?v=-4qqqwzDWvI
Coarse Aggregate Specific Gravity (at a minimum watch until 4:15)
→
http://www.youtube.com/watch?v=O_Zi1U_IEaI&list=PLW9tOoRoXttcocpaa2WezVk _mbYcTSJqM
Fine Aggregate Specific Gravity (at a minimum watch until 6:45)
→
http://www.youtube.com/watch?v=D8YMIgW-
3UY&list=PLW9tOoRoXttcocpaa2WezVk_mbYcTSJqM
Uncompacted Void Content →
http://www.youtube.com/watch?v=TJ7tOadgKyM PART I: Sieve Analysis (ASTM C136) Purpose: To determine the particle size distribution of an aggregate stockpile. Apparatus: -
A mixture of fine and coarse aggregates that is at room temperature. -
A stack of sieves arranged numerically from the pan (bottom container) to the top, as
follows: Pan → No.200 → No.100 →
No.50 →
No.30 →
No.16
→
No.8 →
No. 4 → 3/8 in. →
1/2 in. →
3/4 in. -
Mechanical sieve shakers that will help separate out the particle sizes. -
Scales used to measure the mass of aggregate retained on each sieve. Procedure: 1.
Measure the mass of the sample. This will be the original mass, M
0
. You will later
compare this original mass to the cumulative mass after sieve analysis is done. 2.
Check to make sure that the sieves are stacked in the correct order. 3.
Carefully place the entire sample on the top sieve, and close the top sieve with a lid. 4.
Place the stack of sieves into the sieve shaker, and agitate the sample for the time
given by the TA. 5.
Stop the sieve shaker, and carefully remove the stack of sieves, making sure that
they stay in place. 6.
Measure the mass of sample retained in each sieve. To do this, first place the empty
container on the scale and tare it, then separately place the contents of each sieve
into this container, and record the mass of each size increment. 7.
Add up the masses retained on each sieve, and call this final mass M
f (referred to as
“Total”
in the table). The final mass should be very close to M
0
. By convention, if the
two amounts differ by more than 0.3%, the results cannot be accepted. (For the
purposes of this lab we will ignore this requirement, but we will note it in the tables) 8.
Re-stack the sieves in the correct order, making sure that they are “clean”
enough for the next group to use. LAB 6
: AGGREGATES
Your preview ends here
Eager to read complete document? Join bartleby learn and gain access to the full version
- Access to all documents
- Unlimited textbook solutions
- 24/7 expert homework help
Page 45 Calculations: -
Calculate the fineness modulus. -
From your results, calculate the cumulative mass retained, the cumulative percent
retained, and the percent passing for each sieve size (see sample Problem 5.3). Report all percentages to the precision specified in ASTM C136. In your report,
under calculations, show one numerical example of how you obtained:
cumulative mass retained,
cumulative percent retained, and
percent passing for a sieve size of your choice. Results: -
Summarize the calculations for each sieve in Table 0-1 -
Create a semi-log aggregate gradation chart just like the one on P. 499 of your
textbook. Create the graph in Excel (or equivalent software) and make certain that
you select a graph that correctly spaces the x-axis
. -
Create a 0.45-power chart like the one on P. 500 of your book (you may use the chart
in Figure 0-1). Table 0-1: Results of Sieve Analysis
Sieve
Size
Mass Retained
(a), g
Cumul. Mass
Retained (b), g
Cumul. Percent
Retained
(c) = (b)×100/Total
Percent Passing
(d)=100-(c)
¾ in. ½ in. 3/8 in. No. 4 No. 8 No. 16 No.30 No.50 No.100 No.200 Pan Total
Your preview ends here
Eager to read complete document? Join bartleby learn and gain access to the full version
- Access to all documents
- Unlimited textbook solutions
- 24/7 expert homework help
Figure 0-1: FHWA 0.45 Power Gradation Chart.
Page 46
Your preview ends here
Eager to read complete document? Join bartleby learn and gain access to the full version
- Access to all documents
- Unlimited textbook solutions
- 24/7 expert homework help
Page 47 PART II: Specific Gravity and Absorption of Coarse Aggregate (ASTM
C127) Purpose: To determine the mass-volume relationship quantities and water absorption potential of a
coarse aggregate. Apparatus: -
A sample of coarse aggregate that has been soaked (brought to 100% saturation) prior
to lab. -
Balance used to measure the dry mass, SSD mass, and submerged mass of the sample. -
Wire basket used to immerse the coarse aggregate sample under water. -
Towel/cloth used to quickly surface dry the sample. -
Oven used to dry the sample so that the dry weight can be obtained. Procedure: 1.
The coarse aggregate sample has already been soaked for 24+ hours prior to lab. 2.
Take the tray out of the “water
bath,”
and try to remove as much water from the tray
as you can. 3.
Take the sample over to the wire basket, carefully dump the entire sample into the
basket, and hang the basket from the scale so that the sample is submerged in the
water. Record the scale reading as “C”
–
this is the mass in water. 4.
Carefully remove the wire basket from the tub, and dump all the aggregate onto the
cloth/towel. Roll the sample in the towel until all visible films of water are removed.
You do not have to “dry”
the sample, just towel dry it enough to remove the moisture
from the surface of the aggregate. 5.
Record the mass of the sample after towel-drying, and call this “B”
–
this is the
saturated surface-dry mass. 6.
Place the sample back into the original tray, and label the tray with your Group Name.
Place the tray into the oven. The oven will be set at 110 ±5°C. Someone from your
group will be responsible for coming back the next day and weighing the sample in
order to get the oven-dry weight, “A.”
Coordinate with your TA on the time that you
will return Calculations: -
Using the formulae from ASTM C127, show the numerical calculations for the
following (don’t
forget units on final answers and the required precision
):
Bulk Specific Gravity (Equation 1)
Bulk Specific Gravity (Saturated Surface Dry) (Equation 2)
Apparent Specific Gravity (Equation 3)
Absorption (%) (Equation 11) Results: -
Use Table 0-2 and Table 0-3 to record the measurements Table 0-2: Coarse Aggregate Specific Gravity Measurements
Your preview ends here
Eager to read complete document? Join bartleby learn and gain access to the full version
- Access to all documents
- Unlimited textbook solutions
- 24/7 expert homework help
Page 48 Air
Water
Dry Mass Sample (A), g
SSD Mass Sample (B), g
Submerged Mass (C), g
Table 0-3: Coarse Aggregate Specific Gravity Values
Quantity
Value
Bulk Specific Gravity (OD) Bulk Specific Gravity (SSD) Apparent Specific Gravity Absorption % Notes:
Your preview ends here
Eager to read complete document? Join bartleby learn and gain access to the full version
- Access to all documents
- Unlimited textbook solutions
- 24/7 expert homework help
Page 49 PART III: Dry Rodded Unit Weight and Voids in Aggregate (ASTM C29) Purpose: To determine the dry compacted unit weight of a coarse aggregate stockpile. Apparatus: -
Balance used to measure the mass of the sample -
Tamping Rod -
A cylindrical metal measure -
Scoop for filling the measure with the aggregate Procedure: 1.
Dry the aggregate sample to a constant mass, in an oven at 110 ± 5 °
C (This has
already been done for you). 2.
Fill the cylindrical measure one third full and level the surface with your fingers. 3.
Rod the layer of aggregate with 25 strokes of the tamping rod evenly distributed over
the surface. When rodding the first layer do not allow the rod to strike the bottom of
the measure forcibly. 4.
Fill the measure two-thirds full and again level and rod as above. When rodding this
layer apply only enough force to cause the rod to penetrate to the first layer. 5.
Finally fill the measure to overflowing and again rod as above. When rodding this layer
apply enough force to cause the rod to penetrate to the second layer. 6.
Level the surface of the aggregate with a straightedge in such a way that any slight
projections of the larger pieces of the coarse aggregate approximately balance the
larger voids in the surface below the top of the measure. 7.
Determine the mass of the measure plus its contents and the mass of the measure
alone. 8.
Convert all of your masses to weights. Calculations: -
Using the formulae from ASTM C29, show the numerical calculations for the following
(
don’t
forget units on final answers and the required precision
):
Dry Rodded Unit Weight (DRUW) or bulk density (Equation 1)
Voids % (Equation 4). Results: -
Table 0-4 can be used to record the values you determine in the laboratory. Table 0-4: Dry Rodded Unit Weight and Voids
Volume (ft
3
)
W
measure (lb)
W
total (lb)
DRUW (lb/ft
3
)
Voids (%)
0.25
Your preview ends here
Eager to read complete document? Join bartleby learn and gain access to the full version
- Access to all documents
- Unlimited textbook solutions
- 24/7 expert homework help
Page 50 PART IV: Specific Gravity and Absorption of Fine Aggregate (ASTM
C128) Purpose: To determine the mass-volume relationships and water absorption potential of a fine
aggregate. Apparatus: -
Mold and Tamper. -
Heat Gun to help us getting the sample to SSD. -
Mason jar and pycnometer lid. -
A balance or scale. -
An oven Procedure: CONE TEST FOR SURFACE MOISTURE 1.
Hold the mold on a firm non-absorbent surface. 2.
Place a portion of the sample in the mold until overflowing. 3.
Lightly tap the sample into the mold with 25 light taps of the tamper. 4.
Lift the mold vertically, looking for the fine aggregate to slump slightly. TEST FOR SPECIFIC GRAVITY 1.
The first step in this lab will be to calibrate the pycnometer. In order to do so, weigh
the empty jar and then add water up to the calibration mark and weigh it again with
the water. 2.
Partially fill mason jar with water. 3.
Weigh out 500 g ± 10g of SSD fine aggregate (Make sure to record the exact amount
that you weighed). 4.
Introduce the SSD fine aggregate into the mason jar and add more water to about 90%
of jar capacity. 5.
Place the lid and roll or agitate the mason jar to remove air bubbles for 5 min (be sure
not to spill the contents of the jar). 6.
Once full agitated add water to the calibrated mark. 7.
Weight the mason jar with the fine aggregate and water up to the calibration mark. 8.
Label a bowl with your group name and number. Remove fine aggregate from mason
jar, place in your labeled bowl. 9.
Place the sample in a oven at 110 ± 5
°C, and dry it to constant mass 10.
Someone from your group will be responsible for coming back the next day and
weighing the sample. Coordinate with your TA on the time that you will return. Calculations: -
Using the formulae from ASTM C128, show the numerical calculations for the
following (don’t
forget the required precision
):
Bulk Specific Gravity (Equation 1)
Bulk Specific Gravity (Saturated Surface Dry) (Equation 3)
Apparent Specific Gravity (Equation 5)
Your preview ends here
Eager to read complete document? Join bartleby learn and gain access to the full version
- Access to all documents
- Unlimited textbook solutions
- 24/7 expert homework help
Page 51
Absorption (%) (Equation 19) Results: -
Table 0-5 and Table 0-6 can be used to record the values you determine in the
laboratory. Table 0-5: Fine Aggregate Specific Gravity Measurements
OD
Specimen
(A), g
Pycnometer+Water
(B), g
Pycnometer+Sample+Water
(C), g
SSD
Sample (S),
g
Table 0-6: Fine Aggregate Specific Gravity Values
Quantity
Value
Bulk Specific Gravity (OD) Bulk Specific Gravity (SSD) Apparent Specific Gravity Absorption % Notes:
Your preview ends here
Eager to read complete document? Join bartleby learn and gain access to the full version
- Access to all documents
- Unlimited textbook solutions
- 24/7 expert homework help
Page 52 PART V: Moisture Content of Aggregate Stockpiles (ASTM C566) Purpose: To determine the amount of water held within an aggregate stockpile. Apparatus: -
Balance -
Oven -
Sample container Procedure: 1.
Determine the mass of the sample container and the weigh the aggregate sample. 2.
Place the sample container in the oven until it is completely dry. 3.
Someone from your group will be responsible for coming back the next day and
weighing the sample in order to get the mass of the dried sample, after it has cooled. Calculations: -
Calculate the moisture content using Equation 1 from ASTM C566. Results: -
Use Table 0-7 to write your results. Table 0-7: Moisture Content Measurements
Material
Mass
Container
(g)
Mass
Sample
(g)
SP Mass
Sample+
Container (g)
OD Mass
Sample+
Container (g)
Moisture
Content
(%)
Sand Coarse
Aggregate Describe the Visual Condition of the Sand: Describe the Visual Condition of the Coarse Aggregate: Notes:
Your preview ends here
Eager to read complete document? Join bartleby learn and gain access to the full version
- Access to all documents
- Unlimited textbook solutions
- 24/7 expert homework help
Page 53 Figure 0-2: Fine Aggregate
Angularity Test Apparatus
PART VI: Uncompacted Void Content of Fine Aggregate (ASTM C1252)
and Coarse Aggregate (AASHTO T 326) Purpose: To estimate the angularity of fine aggregate and coarse aggregate particles. Significance: This test method provides the void content of the fine aggregate and coarse aggregate which
depends on the particle shape and texture. An increase in void content indicates a greater
angularity or rougher surface texture. Apparatus: -
Cylindrical Measure -
Funnel -
Funnel Stand -
Glass Plate -
Pan -
Metal Spatula -
Scale Procedure for determination of void content of fine aggregate 1.
Weigh out the fine aggregate. 2.
Position the jar and funnel in the stand
and center of the cylindrical measure. 3.
Use a finger to block the opening of the
funnel and pour the test sample into the
funnel. 4.
Remove the finger and allow the sample to fall
freely into the cylindrical measure. 5.
After the funnel empties, strike off excess
heaped fine aggregate from the cylindrical
measure by a simple rapid pass of the
spatula. 6.
Try to avoid any vibration or any disturbance that can cause compaction of the
fine aggregate. 7.
Brush any grains from the outside and
determine the mass of the cylindrical
measure and contents. 8.
Repeat the procedure for a second time. Procedure for determination of void content of coarse aggregate 1.
Weigh out 5000 ± 10 g of coarse aggregate. 2.
Center the cylindrical measure under the cylindrical hopper. Close and lock the gate of
the hopper.
Your preview ends here
Eager to read complete document? Join bartleby learn and gain access to the full version
- Access to all documents
- Unlimited textbook solutions
- 24/7 expert homework help
Page 54 3.
Use a finger to block the opening of the door and
pour the aggregate sample into the funnel. 4.
Remove the finger and allow the sample to fall
freely into the cylindrical measure. 5.
After the funnel empties, strike off excess
heaped coarse aggregate from the cylindrical
measure by a simple rapid pass of the spatula. 6.
Try to avoid any vibration or any disturbance
that can cause compaction of the coarse
aggregate. 7.
Remove any aggregate that fell outside the
cylindrical measure and determine the mass of
the cylindrical measure and its contents. 8.
Retain all aggregate particles to perform the test
for second time. Calculations: -
Use the formulae from ASTM C1252 (Test Method A) and AASHTO T 326 to calculate the uncompacted voids in the materials. Results: -
Use Table 0-8 to record the measurements from the test. Table 0-8: Uncompacted Voids for Fine Aggregate
Sample
Volume
Container (V),
mL
Mass Sample
(F), g
Specific
Gravity (G)
Voids (U),
%
Aggregate 1 100 Aggregate 2 100 Glass Beads 1 100 Glass Beads 2 100 Table 0-9: Uncompacted Voids for Coarse Aggregate
Sample
Volume Container
(V), mL
Mass Sample
(F), g
Specific
Gravity (G)
Voids (U),
%
Aggregate 1 Aggregate 2 Figure 9-3: Angularity Test
of Coarse Aggregates
Your preview ends here
Eager to read complete document? Join bartleby learn and gain access to the full version
- Access to all documents
- Unlimited textbook solutions
- 24/7 expert homework help
Page 55 Marble 1 Marble 2 Notes:
Your preview ends here
Eager to read complete document? Join bartleby learn and gain access to the full version
- Access to all documents
- Unlimited textbook solutions
- 24/7 expert homework help
Page 56 Group Discussion: 1.
Using your gradation analysis and the stockpile definitions given in ASTM D448,
determine the most likely aggregate stockpile that you sieved. 2.
List and discuss three potential problems with a sieve analysis. How would each
problem affect the test results? 3.
In ASTM C128 and ASTM C127, what would be the consequences of failing to dry the
aggregate to SSD before weighing it? Use a simple numerical example to prove your
conclusion. 4.
How is absorption of the aggregate related to the workability of concrete and to the
amount of binder that is needed in an AC mix? 5.
The method to find the specific gravity of coarse and fine aggregates is different, but
both are based on the same basic physical phenomenon. What is this phenomenon?
Explain the formulas used to calculate the fine and coarse specific gravities as well as
the absorption. 6.
Why is it important to calculate the specific gravity for both dry and SSD condition? Individual Discussion: 1. Look back at all of your calculated quantities (specific gravity, gradation, etc.) and
assess their accuracy. Do any seem unusual? If so indicate which numbers are unusual.
What are the expected range of values for the quantities measured, and why you think
the numbers you obtained were right or wrong (experimental error, miscalculation,
etc.). The answer to this problem will be unique to your team. Mis-identifying valid
numbers as invalid will cost just as many points as not identifying
questionable values
. Even though this lab has 6 parts, you do NOT need to write four separate lab reports. Under “Apparatus
and Procedure,”
describe what each part of the lab entailed. You can put all your calculations under the same “Calculations”
section (but be sure to clearly identify the calculations associated with each part).
Your preview ends here
Eager to read complete document? Join bartleby learn and gain access to the full version
- Access to all documents
- Unlimited textbook solutions
- 24/7 expert homework help
Page 57 In today’s
four-part concrete lab, groups will create molds consisting of cement, aggregates,
and water. The lab will consist of mixing a batch, performing a slump and air voids test, and
preparing beams and cylinders to be used for further testing in lab the following two weeks.
Prior to this lab you should watch the following videos:
Mixing PCC →
http://www.youtube.com/watch?v=KNb0IbYrK8E
Slump test →
https://www.youtube.com/watch?v=lwZf217v5XA
Measuring yield test →
https://www.youtube.com/watch?v=2o9QFeDoIJU
Measuring air voids of PCC air method
→
https://www.youtube.com/watch?v=CfVaR79OgX8
Measuring air voids of PCC volume method →
https://www.youtube.com/watch?v=_Gq8PWmi7LQ
Casting cylinders →
https://www.youtube.com/watch?v=TnEq-8I5Jn8 PART I –
Concrete Mixing (by weight) The lab class will be separated into 6 teams and 5 students for this lab. Each team will create
a PCC mixture at a specific w/c ratio as shown in Table 0-1: Table 0-1: Water/Cement Ratio per Team
Team Water/Cement Ratio 1 & 2 0.40 3 & 4 0.48 5 & 6 0.55 Since the aggregate is not at the saturated surface-dry (SSD) condition the aggregate will
absorb water from the system (if it is in the air dried condition) or provide excess water to the
system (if it is in the saturated surface wet condition) The w/c ratio is the weight of the free
moisture above the absorption value divided by the weight of cement. Your TA should
therefore provide you with the absorption of your aggregate and the moisture content of your
aggregate. The amount of concrete you need to mix was calculated based upon the dimensions of the
different molds and pressure meter you will be using: 1. 6 cylinders, 8”
in height, and 4”
in diameter
2. 1 beam, 4”x
4”
x 18”
3.
1 cylinder, 12”
in height, and 6”in
diameter 4.
1 slump cone, (assumed to be a cylinder in order to stay conservative), 12”
in height,
and 6”
in diameter (average) 5.
1 cylindrical pressure meter, 8.5”
in height, and 8”
in diameter LAB
7
: MIXING CONCRETE AND FRESH PCC
PROPERTIES
Your preview ends here
Eager to read complete document? Join bartleby learn and gain access to the full version
- Access to all documents
- Unlimited textbook solutions
- 24/7 expert homework help
Page 58 The TA will provide you with the mix design for your team before the lab begins. Write this
information down in Table 0-2. To develop these mix designs the TA used the properties
shown in Table 0-3. Also, the amount of mixing water provided by the TA incorporates the
water that will be absorbed by the aggregate. General Mixing Procedure: 1.
Using a plastic bucket, scoops, and containers provided, measure out each ingredient on a scale. Make sure you zero the scale with the empty container on it, so that you are
only weighing the materials, not the container also. 2.
Wet the mixer and the wooden beam molds when used for the first time to avoid
absorbing some of the mixing water. 3.
Place the ingredients into the mixer in the following order: a.
Fine aggregates (sand) b.
Coarse aggregates c.
Mix the coarse and fine aggregates for 1 minute d.
Add 1 ½ lb of water e.
Cement, in 2 equal increments. Continuously mix for about 30 seconds between
each increment. f.
Water, in 2 equal increments. Continuously mix for about 30 seconds between each
increment. g.
Mix the complete batch for an additional 5 minutes to ensure full distribution. Results: -
Use Table 0-4 to record the actual batch weights for each team Table 0-2: Trial Batch Weights
Material
Trial Batch Wts. (lb)
Teams 1 & 2
Teams 3 & 4
Teams 5 & 6
w/c Ratio 0.4 0.48 0.55 Cement Coarse Aggregate Fine Aggregate Water Table 0-3: Specific Gravity of Component Materials
Material
Dry Specific
Gravity
SSD Specific
Gravity
Water
Content (%)
Cement 3.15 N/A N/A
Your preview ends here
Eager to read complete document? Join bartleby learn and gain access to the full version
- Access to all documents
- Unlimited textbook solutions
- 24/7 expert homework help
Page 59 Coarse Aggregate Fine Aggregate Table 0-4: Actual Batch Weights
Team
Cement (lb)
Coarse
Aggregate (lb)
Fine
Aggregate (lb)
Water (lb)
1 2 3 4 5 6 Notes:
Your preview ends here
Eager to read complete document? Join bartleby learn and gain access to the full version
- Access to all documents
- Unlimited textbook solutions
- 24/7 expert homework help
Page 60 Figure 0-1: Measuring the
slump of freshly mixed
PART II: Slump Test of Freshly Mixed Portland cement Concrete (ASTM
C143) Purpose: To measure the slump of a freshly mixed PCC sample. Significance: The slump test is used to measure the consistency of freshly mixed PCC Apparatus: -
Slump cone -
Base -
Tamping rod Procedure: 1.
Place the base on the plastic sheet on the floor. 2.
Place the slump cone on top of the base, and lock it in place. 3.
Pour a 3”
thick layer of concrete into the cone through the top opening. 4.
Once poured, use the taming rod to agitate the sample 25 times –
10 times in the
center, and 15 times around the edges. 5.
Pour a 4”
thick layer of concrete into the cone. Agitate this layer 25 times also (10 times
in the center and 15 times around the edges), making sure to reach into the underlying
layer with the tamping rod. 6.
Pour a 5”
thick layer of concrete into the cone, so that there is a “hump”
on the top of
the cone. This hump will go down once you agitate the sample. Again, rod the topmost
layer 25 times, making sure to reach into the underlying (second) layer, but not into the first
layer. 7.
After the top layer has been rodded, strike off
the surface of concrete by screening and rolling
the tamping rod across the top opening. 8.
Release the clutches on the base, and lift up the
cone vertically, without any horizontal or
torsional motion. 9.
Once the sample comes out, flip the cone upside
down, and place it next to the sample, with the
smaller opening on the bottom 10.
Measure the slump by placing the tamping rod across the larger opening of the mold,
and comparing the height of the sample to the height of the mold (see picture above). 11.
Record the slump. 12.
Repeat procedure 2 more times for a total of three replicates Results: -
Use Table 0-5 to write down your results.
Your preview ends here
Eager to read complete document? Join bartleby learn and gain access to the full version
- Access to all documents
- Unlimited textbook solutions
- 24/7 expert homework help
Page 61 Table 0-5: Summary of Slump Test Results
Team
Trial
Slump
(in.)
Team
Trial
Slump
(in.)
1 1 2 1 2 2 3 3 3 1 4 1 2 2 3 3 5 1 6 1 2 2 3 3 Notes:
Your preview ends here
Eager to read complete document? Join bartleby learn and gain access to the full version
- Access to all documents
- Unlimited textbook solutions
- 24/7 expert homework help
Page 62 PART III: Air Content of Freshly Mixed Concrete by Pressure Method
(ASTM C231) Purpose: To determine the air void content of freshly mixed PCC using an air meter. Significance: Air content is an important for the workability of freshly mixed concrete and for the strength
and durability of hardened concrete. The air content of freshly mixed concrete is important for
the proper proportioning of the mix. Apparatus: -
Cylindrical volume measure -
Balance or scale -
Tamping rod used to agitate the samples -
Mallet for striking side of container -
Pressure meter Procedure: The operating instructions for the pressure meter are as follows: 1.
Fill the base with a sample of fresh concrete, placing the concrete in the base by
tamping. Place the concrete in three layers of approximately equal volume. Rod each
layer 25 times uniformly. Rod the first layer throughout its depth. For each upper
layer, allow the rod to penetrate through the layer being rodded and into the layer
below approximately 1 in. After each layer is rodded, tap the sides of the bowl 10 to 15
times with a mallet to close any voids. Wipe the straight edge clean. 2.
Weigh the container with the concrete sample, so you can calculate the unit weight of
the concrete (TA will give you the volume of the measure). 3.
Clamp on the cover with the petcocks open. 4.
Using the rubber syringe, inject water through one petcock, while leaving the other
petcock open. 5.
Using the black built-in pump, pump up air to the “initial
pressure”
line on the dial
gage. 6.
Wait a few seconds for the compressed air to cool to normal temperature and then
bleeding off, as needed. 7.
Close both petcocks and press down on “thumb
lever”
to release the air into the base.
Hold thumb lever down for a few seconds, lightly tapping the gauge with the finger to
stabilize the hand on the dial. 8.
DO NOT TILT THE METER AT ANY TIME. 9.
Read the percent of air in concrete on dial. Record the air content below. 10.
Open the petcocks to release the pressure and then remove the cover. Clean up the
base, cover, and petcocks, using the hose. 11.
Repeat this procedure one more time. Results: -
Use Table 0-6 to write the results from each team.
Your preview ends here
Eager to read complete document? Join bartleby learn and gain access to the full version
- Access to all documents
- Unlimited textbook solutions
- 24/7 expert homework help
Page 63 Table 0-6: Summary of Unit Weight and Void Content Measurements
Team
Trial
Volume of
Measure (cf)
Weight of
Sample (lbs)
Unit Weight
(pcf)
Air Content
(%)
1 1 0.25 2 0.25 2 1 0.25 2 0.25 3 1 0.25 2 0.25 4 1 0.25 2 0.25 5 1 0.25 2 0.25 6 1 0.25 2 0.25 Notes:
Your preview ends here
Eager to read complete document? Join bartleby learn and gain access to the full version
- Access to all documents
- Unlimited textbook solutions
- 24/7 expert homework help
Page 64 PART IV: Making and Curing Concrete Cylinders and Beams (ASTM C31) Purpose: To determine how to make and cure concrete cylindrical and beam specimens. Significance: There are standardized requirements for making and curing Portland cement concrete
specimens. The specimens will be used in next week’s
lab to determine the strength and
quality of the mix design. Apparatus: -
Seven cylindrical plastic molds with covers (6 = 8”
x 4”,
1 = 12”
x 6”
) -
One beam mold, with dimensions 4”x4”x18”
-
Tamping rod used to agitate the samples -
Mallet for striking side of container -
Concrete curing chamber in Concrete Lab Procedure: CYLINDERS: 1.
Obtain two plastic cylinders for each sample you are to cast. 2.
Coat the inside of each cylinder using a paper towel and the release agent. Be sure to
thoroughly coat inside to promote release of the cylinder after initial cure. 3.
Fill up the first-third of the cylinder with concrete. Using the tamping rod, rod the
sample 25 times (10 times in the center and 15 times around the edges). 4.
After the first layer has been rodded, tap the outside of the cylinder 10-15 times. 5.
Add the second layer of concrete, so that the cylinder is 2/3 full. Use the tamping rod to
agitate the sample 25 times as described above. Make sure that to “reach”
into the first
layer when rodding. Once done rodding, tap the outside of the cylinder 10-15 times. 6.
Fill up the last third of the cylinder. Rod the sample again, making sure to “reach”
into
the second layer, but not the bottommost layer. Once done rodding, tap the outside of
the cylinder 10-15 times. 7.
Once done rodding and tapping, scrape off the top of the cylinder so that the sample
has a smooth surface. 8.
Do NOT cover the samples with the lid –
this will be done just before you leave the lab. 9.
Let the samples sit for one day. Come back the day after lab, and place the samples in
the curing chamber located in the concrete lab. Make sure to label the samples with
each group’s
number and lab day. 10.
The cylinders will cure in a curing chamber for one week. Remove the samples from the
curing chamber just before the following week’s
lab. BEAMS: 1.
Pick a beam mold. Groups with the same water content should share beam mold trays
(i.e. Group 1 and 2 share a tray, Group 3 and 4 share a tray, and Group 5 and 6 share a
tray). 2.
Fill the beam mold with an even 2”
layer of concrete. Using the tamping rod, rod the
sample 60 times, making sure that you tamp the entire area evenly.
Your preview ends here
Eager to read complete document? Join bartleby learn and gain access to the full version
- Access to all documents
- Unlimited textbook solutions
- 24/7 expert homework help
Page 65 3.
Fill the remaining 2 inches of the mold, and tamp the sample again 60 times. Make
sure you “reach”
into the underlying layer, but do not touch the very bottom of the
mold. 4.
Once done tamping, scrape off any excess concrete from the surface. Try to get the
surface of the beam to be as smooth as possible. Do not cover the beam. 5.
Let the beam sit for 1 day. Come back the day after lab and remove the sample from
the mold. 6.
Place the beam into the curing container, next to your group’s
cylinder samples. Label
your beam with your group number and lab day. 7.
The beam will cure in water for 1 week. You will remove the samples from the curing
medium just before the following week’s
lab. Results: -
Use Table 0-7 to summarizing the water-cement ratio, slump, unit weight, and air
voids of the three different mixes: Table 0-7: Water Content, Slump, Unit Weight, and Air Voids of the Six Teams
Team
Actual Water-
Cement Ratio
Slump (in)
Unit Weight
(pcf)
Air Voids (%)
1 2 3 4 5 6 Notes:
Your preview ends here
Eager to read complete document? Join bartleby learn and gain access to the full version
- Access to all documents
- Unlimited textbook solutions
- 24/7 expert homework help
Page 66 Group Discussion: 1.
Go to ASTM C143, Section 9 and identify the allowable variability for the slump test. If
each team represents a “Single
-
Operator”,
which teams produced acceptable slump
data and which teams produced unacceptable data? List three possible errors that could have occurred and explain if those errors would increase or decrease the
measured slump. 2.
Do you see any trends between water cement ratio and slump, unit weight, and air
voids? How do these trends compare with your expectations? Be as specific as possible
and include the amount of change you expect with changes in water cement ratio (it is
insufficient to say you expect slump to increase/decrease with increases in water
cement ratio, instead make sure you explain how much the value should change with
the given water cement ratio changes). If expected trends are not met give three
reasons why you think this occurred. Be sure to include example calculations in the
appendix for any analysis that you perform. Individual Discussion: 1.
Based on each team’s
actual mixing results and what you know about the effects of
water cement ratio on the strength and workability of PCC. Order the teams from 1 t
o 3
based on which team you think will have the highest compressive strength. If you
think more than one team will have the same (or approximately the same) strength
then rank both equally. Explain your ranking.
Your preview ends here
Eager to read complete document? Join bartleby learn and gain access to the full version
- Access to all documents
- Unlimited textbook solutions
- 24/7 expert homework help
Page 67 In today’s
lab, you will observe the behavior of last week’s
concrete cylinders under a
compressive load, and the behavior of the concrete beam under flexural testing. Prior to this
lab you should watch the following videos to have a general idea about the nature of the
different tests. The exact protocols followed in the lab may be slightly different than these
videos. All of your writing should reflect what was actually done in the lab. In today’s
lab, you will observe the behavior of concrete cylinders under a compressive load
after 7 days of time in the curing room (depending on the semester schedule). Prior to this
lab you should watch the following videos: Compression Test on Concrete →
https://www.youtube.com/watch?v=IR1U_bBiJic (fast forward to approximately 4:20 mark for testing. Prior to this is sample preparation,
and we follow a different method) Splitting Tension Test →
http://www.youtube.com/watch?v=m bAeHLwvQ Flexural test on concrete →
https://www.youtube.com/watch?v=--ah--2R0wo&x-yt-
cl=84924572&x-yt-ts=1422411861 PART I: Compressive Strength of Cylindrical Concrete Specimens
(ASTM C39) Purpose: To measure the compressive strength of laboratory cast PCC samples. Significance: The compressive strength of concrete is a vital part of construction. It is a universal
measure of the quality of the concrete mix. Apparatus: -
A loading machine with two steel breaking blocks –
the upper block is spherically
seated, and the bottom block is a solid surface. Test Specimens: -
The specimens used will be the same specimens we molded in last week’s
lab. The
dimensions of all specimens are 4 inches in diameter, and 8 inches in height. LAB 8
: HARDENED PROPERTIES OF PCC
Your preview ends here
Eager to read complete document? Join bartleby learn and gain access to the full version
- Access to all documents
- Unlimited textbook solutions
- 24/7 expert homework help
Page 68 Procedure: 1.
Using the digital caliper, measure the diameter of the two specimens in two different
locations near the middle height of the specimen. Measure the diameter at a right-
angle to the specimen. Report your values to the nearest 0.01 in (or to the nearest
0.25mm) and average them. This will be the “actual”
diameter. 2.
Put the breaking blocks on the machine into position. 3.
Clean the surfaces of the breaking blocks and of the specimen. 4.
Place a Neoprene cap on each side of the specimen. 5.
Seat the specimen into the spherically-seated block, aligning the specimen’s
axis
with that of the block. 6.
Apply a compressive load continuously (without shocks or breaks). The load we’ll
be
applying will be moving at 0.5% strain/minute. 7.
Continue applying the load until the specimen breaks. During loading, observe the
specimen for crack development, and once the test is finished, note the type of
failure (failure angle, how long it took to fail, etc.). 8.
Record the maximum load carried by the specimen during the test. Calculations: -
Calculate the compressive strength of the PCC in pounds per square inch. Results: -
Report the f
c value of each specimen in tabular form (
follow precision specified in standard
). Also, record the maximum load it carried: Table 8-1: Properties of 7-day Old Concrete Cylinders
Specimen ID#
Max. Load
(lbs)
f
c (psi)
Failure Observations
a
Team
Sample
1 1 2 3 2 1 2 3 3 1 2 3
Your preview ends here
Eager to read complete document? Join bartleby learn and gain access to the full version
- Access to all documents
- Unlimited textbook solutions
- 24/7 expert homework help
Page 69 4 1 2 3 5 1 2 3 6 1 2 3 a brittleness, surface texture, angle of breakage, level of crushing, time to fail, etc. PART II: Flexural Strength of Concrete (ASTM C78) Purpose: To measure the flexural strength of a laboratory cast PCC beam under four point (third
point) loading conditions. Significance: Like the compression test, the flexural strength of concrete also indicates quality. Apparatus: -
Loading machine that is capable of delivering loads at a constant rate. Force must
be applied perpendicular to the face of the specimen and applied without any
eccentricity. Test Specimens: -
The specimen used will be the beam molded in last week’s
lab. Its dimensions are 4”
by 4”
by 18”.
Procedure: 1.
Mark each specimen 1 in. from each side and then divide the span of the beam L by 3. Mark each section as shown in Figure 8-1.
Your preview ends here
Eager to read complete document? Join bartleby learn and gain access to the full version
- Access to all documents
- Unlimited textbook solutions
- 24/7 expert homework help
Page 70 2.
Turn the test specimen on its side so that it is positioned exactly as it was molded,
and center it on the bearing blocks. 3.
Center the loading apparatus with
respect to the applied force. Bring the
load-applying blocks in contact with the
surface of the specimen at the third
points between the supports. 4.
If there exists a gap in excess of 25 mm
(0.004 in.) between the load-applying
blocks , the supports, and the specimen,
grind or cap the contact surfaces of the
specimen, or shim with leather strips. 5.
Apply the load rapidly up to about 50%
of the breaking load. Then, apply the
load continuously at a rate that
constantly increases the extreme fiber
stress between 125psi and 175 psi
(860kPa and 1210kPa) per minute. The
rate we’re
using is 0.05 in/minute.
Continue loading until rupture occurs. Calculations: -
Calculate the modulus of rupture using either Equation 2 or Equation 3 in ASTM
C78. Follow precision requirements. If the fracture occurs outside of the acceptable
range for ASTM C78 make a note of this and use Equation 3. Results: -
Summarize your findings in Table 8-2 and Table 8-3: Table 8-2: Dimensions of Flexural Test Specimen
Team
Average
width (in.)
Average
depth (in.)
Span length
(in.)
Line of Fracture
Location
a
1 2 3 6.
Measure the dimensions of the specimen
to the nearest 0.05in (1.3mm) using the
digital caliper. Take three measurements across each dimension, and average these to find the average width,
average depth, and average length. Locate the line of fracture location at the section
of fracture and record your findings in the table below.
Your preview ends here
Eager to read complete document? Join bartleby learn and gain access to the full version
- Access to all documents
- Unlimited textbook solutions
- 24/7 expert homework help
Page 71 4 5 6 a middle third, outside the middle third but acceptable, outside middle third and unacceptable Table 8-3: Properties of Concrete Beam used in Flexural Bending Test
Team
Maximum
applied load (lb)
Modulus of
rupture (psi)
Existing defects in specimen
prior to testing
1 2 3 4 5 6 a surface voids, pre-existing cracks, uneven surface, etc.
Your preview ends here
Eager to read complete document? Join bartleby learn and gain access to the full version
- Access to all documents
- Unlimited textbook solutions
- 24/7 expert homework help
Page 72 PART III: Splitting Tensile Strength of Cylindrical Concrete Specimens
(ASTM C496) Purpose: To measure the splitting tensile strength (Brazilian Test strength) of a laboratory cast PCC
sample. Significance: The splitting tensile strength of PCC is another indicator of the tensile properties of PCC
and is also used to design structural lightweight concrete members. Apparatus: -
Testing Machine -
Supplementary Bearing Bar or Plate Procedure: 1.
Draw diametric lines on each end of the specimen using a suitable device that will
ensure that they are in the same axial plane. 2.
Determine the diameter of the specimen by averaging three diameters measured
near the ends and the middle of the specimen. 3.
Determine the length of the specimen by averaging at least two length
measurements taken in the plane containing the lines marked on the two ends. 4.
Center one of the strips along the center of the lower-bearing block. Then, place the
specimen on the strip and align so that the lines marked on the ends of the specimen
are vertical and centered over the strip. 5.
Place the second strip lengthwise on the cylinder, centered on the lines marked on
the ends of the cylinder. Make sure that the projection of the two lines marked
intersects the center of the upper bearing plate. 6.
Apply the load continuously at a constant rate within the range of 100 to 200 psi/min
splitting tensile stress until failure. 7.
Record the maximum load applied. Calculations: -
In order to calculate the splitting tensile strength of your specimen refer to Equation
1 from the ASTM C496 standard. Results: -
Use Table 8-4 and write the results from each team.
Your preview ends here
Eager to read complete document? Join bartleby learn and gain access to the full version
- Access to all documents
- Unlimited textbook solutions
- 24/7 expert homework help
Page 73 Table 8-4: Splitting Tensile Strength of Concrete
Team
Diameter (in.)
Max Load (lb)
Splitting Tensile Strength (psi)
1
2
3
4
5
6
PART IV: Ultrasonic Pulse Velocity Group Discussion: 1.
Give typical values for the 7 day compressive strength of PCC. Cite your reference
for these values and provide a second reference that confirms this range of values.
Then comment on your 7 day strength tests with respect to these values. Are they
higher, lower, approximately the same, etc. Also, comment on your overall trends
with respect to water/cement ratio and the trends that are typically reported, e.g.,
are your results the same or different and how are they different from those
typically observed. If differences in either the compressive strength or trends with
water/cement ratio are observed speculate as to why these differences occurred. 2.
List and discuss the sequence of events that led up to the failure of a concrete
cylinder in direct compression. Explain why a tensile failure in PCC is very rapid
and brittle in comparison. 3.
Suppose that an overnight rainstorm increased the % total moisture content for all
aggregates by 2.5 percentage above those that were used in the mix you made (e.g. if
the water content for the aggregates in your mix was 1% then the new water content
would be 3.5%). What effect could this change have in terms of strength and
workability if you weighed in the same amount of aggregate, free water, and cement?
Quantify these effects as much as possible. For example it is insufficient to simply
say that the strength would increase/decrease you should discuss how much of increase or decrease you would expect. 4.
Compare the UPV elastic modulus with the elastic modulus determined by ASTM
C469. 5.
Compare the lab results for compression and elastic modulus at 7 days and
compression, splitting tension, and modulus of rupture at 14/21 days to the ACI *For the Ultrasonic Pulse Velocity refer to Lab 3
Part II*
Your preview ends here
Eager to read complete document? Join bartleby learn and gain access to the full version
- Access to all documents
- Unlimited textbook solutions
- 24/7 expert homework help
Page 74 predictions that are shown below. Use the average f
c values for these calculations.
Create a summary table with the measured and predicted values from each team.
Estimate the error of the predictions based on the equation shown in the table
below. Discuss how well these equations predicted the measurements. Quantity Relationship Error Modulus of Rupture f
r
7
.
5
f
c
Error
Measured
Predicted
100
Measured
Splitting Tension f
ct
6 f
c
Elastic Modulus E
57
,
000
f
c
6.
The most general form of Abram’s
law for portland cement concrete is summarized
below. a.
Determine the values of coefficients A and B for both the 7 day and 14/21 day
strengths. b.
Assuming a linear relationship between these coefficients and time, estimate
the values of A and B for the 28 day case and predict the 28 day compressive
strength of your PCC. c.
Compare your predictions to the rule of thumb that is typically used to
estimate the 28 day compressive strength from the 7 day strength. d.
Discuss three reasons why these two predictions do or do not match well. A
f
c
B
w
/ c
Individual Discussion: 1. In this lab we have tried to examine the effects of water cement ratio on PCC strength,
modulus, workability, and void content. Suppose you are in charge of a lab that is
responsible for developing a very high strength concrete for use by a small Southeast
Asian country. Devise a study to comprehensively evaluate the effects of air void
content on the engineering behavior of PCC for structural application. Include in this
study the specific experiments that are necessary, appropriate standard specification
designations, necessary replicates, mixing conditions, air void levels to study,
component materials to include, etc. Include all the details necessary for a technician to
take your document and carry out the study. In a separate section of your answer
include a list of any information that you cannot readily assume, but that would need
to be found out before embarking on this study. You may type your answer to this discussion question, but your answer should be
unique. Copying another person’s
answer or replicating another person’s
answer in a close way will result in penalties to both parties.
Your preview ends here
Eager to read complete document? Join bartleby learn and gain access to the full version
- Access to all documents
- Unlimited textbook solutions
- 24/7 expert homework help
Page 75 PART I: Viscosity Determination of Asphalt Using a Rotational
Viscometer (ASTM D4402) Purpose: To determine the rotational viscosity of asphalt cement binder at elevated temperatures. Significance: Asphalt viscosity is important for quality control and quality assurance. It allows proper
handling of asphalt and is used to find the mixing and compaction temperatures of asphalt
concrete. Apparatus: -
Rotational viscometer. -
Spindles (No. 27). -
Thermosel system. Procedure: 1.
Initial setup including powering the Thermosel and initial temperature equilibrium
has already been performed by your TA. 2.
Remove the sample holder with the test specimen from the oven. 3.
Place the loaded chamber back into the thermo-container using the extracting tool. 4.
Lower the viscometer and align the thermo-container. 5.
Insert the spindle into the liquid in the chamber and couple it to the viscometer. 6.
Allow the asphalt to come to the equilibrium temperature (about 15minutes). 7.
Start the viscometer at 20rpm. 8.
Record three readings, taken at 60-second intervals, at each test temperature in the
table below. Calculations: -
Average the three viscosity readings taken at each test temperature. Results: -
Record your measurements in Table 0-1. -
Plot your data on the viscosity chart shown in Figure 0-1. Table 0-1: Viscometer Readings for Asphalt Binder
Test Temperature
(°C)
Viscometer
Reading 1
Viscometer
Reading 2
Viscometer
Reading 3
Average Viscometer
Reading (cP)
135 LAB 9
: ASPHALT CEMENT TESTING AND GYRATORY COMPACTION
Your preview ends here
Eager to read complete document? Join bartleby learn and gain access to the full version
- Access to all documents
- Unlimited textbook solutions
- 24/7 expert homework help
Page 76 160
Your preview ends here
Eager to read complete document? Join bartleby learn and gain access to the full version
- Access to all documents
- Unlimited textbook solutions
- 24/7 expert homework help
Figure 0-1. Temperature-Viscosity chart for identifying mixing and compaction temperatures.
Your preview ends here
Eager to read complete document? Join bartleby learn and gain access to the full version
- Access to all documents
- Unlimited textbook solutions
- 24/7 expert homework help
Page 78 PART II: Penetration Test of Asphalt Binder (ASTM D5) Purpose: To measure the penetration of an unknown asphalt cement binder at two different
temperatures. Prior to the lab watch →
https://www.youtube.com/watch?v=HQH5Wf07tRk Significance: The penetration test is used to measure binder consistency. A higher penetration value
indicates a softer consistency. Apparatus: - Penetration apparatus and needle (Each increment on the dial gage is equal to 1/10
mm), sample container of binder, water bath, transfer dish, thermometer Procedure: 1.
Clean and dry the needle with a clean cloth, and insert it into the penetrometer. For
room temperature of 25
°
C, place a 50-gram mass on top of the needle, so that the
total moving load comes to 100 grams. For 4
°
C, place the 50-gram and the 100-gram
mass on top of the needle, so that the total moving load comes to 200 grams. 2.
Place the sample container in a transfer dish, and transport the specimen over to
the penetrometer. The transfer dish is vital to keeping the temperature of the
sample constant. 3.
Place the transfer dish on the stage of the penetrometer. 4.
Using the large dial, adjust the moving head of the penetrometer so that the needle
is positioned close to the surface of the binder. Using the smaller controller right
above the needle, make fine adjustments to the needle. Position the needle so that it
just barely touches the surface of the binder. 5.
Move the top black handle down so that the “gap”
between the two measuring rods is
closed. This is the “base”
position. 6.
Mark the base reading in the table below, under “start.”
7.
With the metallic button in the “up”
position, press the red button. The timer will
start, and the needle will penetrate the sample for 5 seconds. 8.
Again, move the top black handle down so that the gap is closed. This is the “end”
position. 9.
Mark the dial gage reading from the “end”
position in the table below. The difference
between the “end”
and the “base”
reading is the penetration value (or pen value). 10.
Repeat Steps 1-11 in three different positions throughout the surface of the binder. 11.
Each member from the team will perform this test at 25
°C and only one per team at 4°C. Calculations: - Using the following formula to calculate the viscosity, in centipoises Results: -
State the average penetration value for each of the two test temperatures in Table
0-2 and Table 0-3. -
Use Table 0-4 to summarize the average penetration values from each team.
Your preview ends here
Eager to read complete document? Join bartleby learn and gain access to the full version
- Access to all documents
- Unlimited textbook solutions
- 24/7 expert homework help
Page 79 Table 0-2: Penetration Values at 4
°
C
Temp.
4°C Group 1
4°C Group 2
Trial #
1
2
3
4
5
6
Start End Difference Start End Difference Start End Difference Average Table 0-3: Penetration Values at 25
°
C
Trial
Measure
S1
S 2
S 3
S 4
S 5
S 6
Average
1 Start End Diff. 2 Start End Diff. 3 Start
Your preview ends here
Eager to read complete document? Join bartleby learn and gain access to the full version
- Access to all documents
- Unlimited textbook solutions
- 24/7 expert homework help
Page 80 End Diff. Table 0-4: Penetration Values from All Teams
Group
Team
Machine
4
°
C
Penetration
(avg.)
4
°
C
Viscosity
(avg.), cP
25
°
C
Penetration
(avg.)
25
°
C
Viscosity
(avg.), cP
1 1 2 3 2 4 5 6 Notes:
Your preview ends here
Eager to read complete document? Join bartleby learn and gain access to the full version
- Access to all documents
- Unlimited textbook solutions
- 24/7 expert homework help
Page 81 PART III: Dynamic Shear Modulus of Asphalt Cement (ASTM D7175) Purpose: To determine the dynamic shear modulus, |G*|, and phase angle,
, of an unknown
asphalt cement binder. Significance: The Dynamic Shear Rheometer is an important apparatus in characterizing asphalt cement
binder. The dynamic shear modulus is an indicator of the stiffness or resistance of asphalt
binder to deformation under load. The dynamic modulus and phase angle define the
resistance to shear deformation of the asphalt binder in the linear viscoelastic range. The
linearity test sets the linear viscoelastic limits. Apparatus: -
A Dynamic Shear Rheometer Procedure: SHEAR MODULUS 1.
Place the 25 mm upper and lower plates. 2.
Set the gap as follow: a.
Observe the upper and lower plate measuring contact by rotating the upper plate
and slowly lowering the tube with the knob on the right hand side of the DSR
until the plate stops rotating b.
Raise or lower the vernier scale ring so that when the tube is bottomed out
against the scale collar, the plates are just touching. This is ZERO gap position c.
Adjust the gauge to read zero by rotating the zero with the indicator, then
tighten the Allen screw d.
Raise the upper plate using the position adjustment knob on the right to allow
clearance for setting the gap e.
Rotate the micrometer stop adjustment knob turning it counterclockwise to the
desired gap (1.05 mm for the 25 mm plates) 3.
Loading the sample: a.
Place the sample in the center of the bottom plate b.
Lower the upper plate onto the sample, slowly squeezing the sample between the
plates until you reach the stop setting (1.05 mm) c.
Trim the excess material with the trimming tool 4.
Once the sample is trimmed, remove the extra 50 microns from the gap turning the
stop adjustment knob clockwise 50 microns. Turn the right position adjustment knob
counterclockwise to lower the upper plate to this setting 5.
Place the plastic cover and let the water run at test temperature. LINEARITY TEST 1.
After shear modulus test is done. Change the test mode to Linearity Test on the
DSR Software. 2.
The test will start running at a 2% strain and be increased in 2% increments up to
30%. Record all shear modulus (G*) for each strain level. You should have a total of
15 readings.
Your preview ends here
Eager to read complete document? Join bartleby learn and gain access to the full version
- Access to all documents
- Unlimited textbook solutions
- 24/7 expert homework help
Page 82 Results: -
Use Table 0-5 to write down the results from all groups. -
In Table 0-6 record the readings for the linearity test. -
Your TA will send you data for the other tests needed to determine the asphalt
binder grade. Table 0-5: DSR Test Results
Team
Aging
Level
Temperature
(°C)
|G*| (Pa)
Phase Angle (degree)
1 2 3 4 5 6 Table 0-6: Linearity Test Results
Strain
(%)
Shear
Modulus
|G*| (Pa)
Strain
(%)
Shear
Modulus
|G*| (Pa)
Strain
(%)
Shear
Modulus
|G*| (Pa)
2 12 22 4 14 24 6 16 26 8 18 28 10 20 30 Notes:
Your preview ends here
Eager to read complete document? Join bartleby learn and gain access to the full version
- Access to all documents
- Unlimited textbook solutions
- 24/7 expert homework help
Page 83 PART IV: Gyratory Compaction (ASTM D6925) Purpose: To demonstrate the use and functionality of the Superpave gyratory compactor. Watch the
following video →
https://www.youtube.com/watch?v=2xpfiqF1kiw Significance: The device is used for the Superpave volumetric mix design of asphalt concrete mixes and
for field quality control during the construction of HMA pavements. The gyratory compactor
is used to create samples that will ultimately be used to determine the asphalt content and
aggregate gradation for asphalt concrete mixtures. Different trial specimens, with different
aggregate gradations and asphalt contents are prepared, and they are compacted using the
gyratory compactor. For Superpave requirements the internal angle of gyration is 1.16
degrees, the compaction rate is 30 gyrations per minute, and the vertical pressure is 600
kPa (87 psi). The number of gyrations used to achieve different levels of compaction is as
follows: -
N
ini –
the number of gyrations represents the initial compaction level that helps
identify “tender”
mixes. Such mixes lack stability during construction, and they tend
to displace rather than compact under loads. -
N
des –
the number of gyrations necessary to achieve a level of compaction that
represents the compaction level just after the end of the construction process. -
N
max –
the anticipated compaction level that is achieved at the end of the pavement’s
lifetime. Depending on the projected number of equivalent single axle loads (ESALs) the pavement is
going to experience, the number of gyrations varies. For light traffic, with ESALS of less
than 0.3 million applications of load, the maximum number of gyrations (N
max
) is 75,
whereas for heavy traffic, with ESALs exceeding 30 million applications of load, the
maximum number of gyrations is up to 205. You can find a summary table of this
information in Table 9.9 on page 367 of your book. Apparatus: -
Superpave Gyratory Compactor Sample Preparation: Each group will make 2 replicates of their mix design. The asphalt content for each mix will
vary; some will have 5.0, 5.5 and 6% asphalt content by weight. The materials used in this
mix design have the properties summarized in Table 0-7. The mix design will be given by
your TA. You can write your mix design in Table 0-8. For this exercise we will be designing
the asphalt mixture for a traffic level of 2 million EASAL (
N
ini
= 7, N
des
= 75, N
max
= 115
). Table 0-7: Material Specific Gravities
Material
Specific Gravity
Asphalt Cement 1.030 Coarse Aggregate Fine Aggregate
Your preview ends here
Eager to read complete document? Join bartleby learn and gain access to the full version
- Access to all documents
- Unlimited textbook solutions
- 24/7 expert homework help
Page 84 Table 0-8: Asphalt Mixture Design for each Team
Team
Coarse Aggregate (g)
Fine Aggregate (g)
Asphalt (g)
1 2 3 4 5 6 Procedure: MIXING ASPHALT CONCRETE 1.
Weigh out the appropriate amounts of the required aggregate size fractions and
combine in a bowl to the proper batch weight. Typically, a batch weight of 4500 -
4700 grams of aggregate will provide enough material for a finished specimen height
of 115 ± 5 mm, if the combined aggregate specific gravity is between 2.55 - 2.70. 2.
Heat the binder and the combined aggregate in an oven to the appropriate mixing
temperature for the binder to be used. This ensures that the binder is fluid enough
to coat the aggregate particles. 3.
Place the heated aggregate in the mixing bowl and thoroughly dry mix the sample.
Make a crater in the center of the aggregate in the bowl and weigh in the required
amount of binder. Begin mixing immediately. A mechanical mixer may be used. 4.
Determine the proper compaction temperature range for the binder used. 5.
After mixing, spread the loose mixture in a flat, shallow pan and short term
condition the mixture as detailed in AASHTO R 30. 6.
Place the compaction mold and base plate in an oven to preheat to the required
compaction temperature. 7.
Bring the mixture to the proper compaction temperature, by placing it in another
oven at the compaction temperature (normally there would be an aging step, but we
will omit this process for this lab). 8.
Once compaction temperature is reached proceed with compaction. GYRATORY COMPACTION OF ASPHALT CONCRETE 1.
Verify all settings for angle, pressure and number of gyrations. 2.
Verify the height recording device is turned on and is reading in the proper units. 3.
When the compaction temperature has been reached, remove the mold and base
plate from the oven. Put the base plate in position in the mold and place a paper
disk in the bottom of the mold. 4.
Charge the mixture into the mold in one lift. A funnel or other device may be used to
place the mixture into the mold. Take care to avoid segregating the mix in the mold,
Your preview ends here
Eager to read complete document? Join bartleby learn and gain access to the full version
- Access to all documents
- Unlimited textbook solutions
- 24/7 expert homework help
Page 85 but work quickly so that the mixture does not cool excessively during loading. Level
the mix in the mold and place a paper disk on top. 5.
Place the mold in the gyratory. 6.
Press mold lower and once the mold is lowered press mold lock to secure the mold
and then press start. 7.
The gyratory will stop automatically when the specified number of gyrations has
been reached. 8.
Remove the mold from the compactor and extrude the specimen from the mold. Take
care not to distort the specimen when removing the specimen from the mold. A
cooling period of 5 to 10 minutes may be necessary with some mixtures; a fan may
help speed the cooling process. Remove the paper disks while the specimen is still
warm to avoid excessive sticking. Calculations: -
Estimate the G
mb of each compacted sample by using the measured height and
assuming a smooth walled cylinder. Results: -
Summarize the results from each compaction in Table 0-9. -
Summarize the actual asphalt contents that were blended in the laboratory in Table
0-10 (you will use the actual asphalt contents in Lab 13). Table 0-9: Compaction Results for Each Team
Team
Sample
Height (mm)
Bulk Specific Gravity (
Estimated
)
@ N
ini
@ N
des
@ N
max
@ N
ini
@ N
des
@ N
max
1 1 2 2 1 2 3 1 2 4 1 2 5 1 2 6 1
Your preview ends here
Eager to read complete document? Join bartleby learn and gain access to the full version
- Access to all documents
- Unlimited textbook solutions
- 24/7 expert homework help
Page 86 Table 0-10: Actual Asphalt Content for Each Sample
Team
Target Asphalt Mass (g)
Actual Asphalt Mass (g)
1 2 3 4 5 6 Notes: 2
Your preview ends here
Eager to read complete document? Join bartleby learn and gain access to the full version
- Access to all documents
- Unlimited textbook solutions
- 24/7 expert homework help
Page 87 Group Discussion: 1.
Estimate the proper mixing and compaction temperatures for your binder. Then,
discuss three consequences that might occur during the mixing and compaction
process if your thermosel was mis-calibrated so that the actual temperature of the
sample was 5
° above the recorded temperature. 2.
Determine the strain limit for your asphalt binder at the test temperature where
you performed the test. Use a threshold error of 90% of the |G*| value at 2% strain
in this determination. Include in this answer a logarithmic plot of |G*| versus
strain level and a vertical line indicating where you determined the limit to exist
(include sample calculations in the appendix to support this strain level). Based on
this plot, what would be the consequence on the asphalt binder grade if the |G*|/sin(
) test was performed at too high of a strain level. 3.
For the 25
°
C penetration tests, evaluate each member of your team and determine
who performed the penetration test with an acceptable level of repeatability. For 4
°
C
penetration results assess your team’s
results for acceptability. Show your
assessment and discuss the results (refer to ASTM D5 for appropriate thresholds). 4.
For both the 25
°
C and 4
°
C penetration tests use the average values from each team
to assess the within laboratory and between laboratory precision. Treat all teams in
a group as a single laboratory and the two groups as two separate laboratories.
Discuss the results (threshold values can be found in ASTM D5). 5.
Briefly summarize the general procedure for preparing, placing, and compacting
samples using the gyratory compactor. What criteria are considered choosing the
materials and when putting together the mix design? Individual Discussion: 1. Determine the standard PG grade of your asphalt binder. Show all the steps you
took in determining this grade.
Your preview ends here
Eager to read complete document? Join bartleby learn and gain access to the full version
- Access to all documents
- Unlimited textbook solutions
- 24/7 expert homework help
Page 88 PART I: Theoretical Maximum Specific Gravity of Hot Mix Asphalt
(ASTM D2041) Purpose: To determine the maximum theoretical specific gravity of an asphalt concrete mixture. Significance: Theoretical Maximum Specific Gravity (G
mm
) is used to calculate the percent of air voids in
a compacted HMA. The values for G
mm will depend on the mix design and the aggregates
used. Air void content is an important indicator of the quality of an asphalt concrete
mixture. Due to the time requirements we will only be performing two of these tests per
group. Apparatus: -
Vacuum Container -
Balance -
Vacuum Pump -
Mechanical Shaker Procedure: 1.
The first step is to weigh the container with water (D). 2.
Separate the particles of the HMA sample by hand, taking care to avoid fracturing
the aggregate. 3.
Place sample into the container and determine the mass and designate the net mass
of the sample as A. 4.
Add enough water to cover the sample completely. 5.
Remove air trapped in the sample by applying gradually increased vacuum for 15
minutes. Make sure to agitate the container and contents using the mechanical
shaker. 6.
After vacuum, fill up the container with water, close the cap and weigh the container
filled with water and the mix sample (E). Calculations: -
Using the formulae from AASHTO T209, show the numerical calculations for the
maximum specific gravity (don’t
forget the required precision
). Results: -
Summarize your results in Table 0-1 LAB 1
0
: ASPHALT CONCRETE TESTING
Your preview ends here
Eager to read complete document? Join bartleby learn and gain access to the full version
- Access to all documents
- Unlimited textbook solutions
- 24/7 expert homework help
Page 89 Table 0-1: Maximum Specific Gravity Test
Team
Mass Sample
(OD) (A), g
Mass
Container+
Water (D), g
Mass Container+
Water+Sample (E), g
Maximum
Specific
Gravity
1 2 3 4 5 6 Notes:
Your preview ends here
Eager to read complete document? Join bartleby learn and gain access to the full version
- Access to all documents
- Unlimited textbook solutions
- 24/7 expert homework help
Page 90 PART II: Bulk Specific Gravity of Compacted Bituminous Mixtures
(ASTM D2726) Purpose: To determine the bulk specific gravity of an asphalt concrete sample. Significance: The outcome of the Bulk Specific Gravity of Compacted Bituminous Material’s
test is used
in the void analysis of the compacted asphalt mix. The air void content of an asphalt
concrete mixture is an important indicator of quality. Test Specimens: Students will be using the specimens that were compacted during the Preparation of
Asphalt Concrete Specimens Using the Gyratory Compactor lab. Fill in Table 0-2 Table 0-2: G
mm values
Asphalt Content (%)
Maximum Specific Gravity
Apparatus: -
A balance suitable for suspending specimens into a water bath and measuring the
submerged weight. Procedure: 1.
Weigh the specimen in air, and record the mass as A. 2.
Immerse the specimen in water that is at 25±1°C (77±2°F) while it is suspended
from the balance for 3 to 5 minutes. Record the immersed mass as C. 3.
Remove the specimen from the water bath, and surface dry it by blotting with a
damp cloth. Weigh the specimen, and record the surface-dry mass as B. Calculations: -
Using the formulae from ASTM D2726, show the numerical calculations for the bulk
specific gravity and water absorption (don’t
forget the required precision
). Designate the specific gravity determined by these equations as G
mb
(
measured
)@
N
max
Your preview ends here
Eager to read complete document? Join bartleby learn and gain access to the full version
- Access to all documents
- Unlimited textbook solutions
- 24/7 expert homework help
Page 91
-
Compare your measured G
mb to the G
mb calculated for N
max from your previous lab
(see Table 13-9) and calculate the correction factor, C. G
mb
measured
@ N
max
C
G
mb
estimated
@ N
max
-
Use the correction factor to calculate the G
mb
(c
orrected
) for each sample from Lab 12
at N
ini and N
des (assume C is constant for both samples of a given team). G
mb
corrected
C
G
mb
estimated
-
Use the G
mm in Table 0-2 and the G
mb
(
corrected
)@N
des to compute the air void
content at N
des
. P
1
G
mb
corrected
@ N
des
100
a
G
mm
-
Average and report the air void content for each compacted asphalt concrete sample. -
For each sample, calculate %G
mm
@N
ini
, %G
mm
@N
des
, %G
mm
@N
max
, VMA @ N
des and
VFA @ N
des G
mb
corrected
%
G
mm
G
mm
100
VMA
100
%
G
mm @ N
design
G
mm
R
s
G
sb
VFA
(
VMA
P
a )
VMA
100
In the VMA equation you will need to calculate the G
sb of your fine and coarse
aggregate blend (G
sb values were given in the previous lab). The R
s variable
represents the proportion of aggregate in the mix; M
coarse
M fine
R
s
M
M
M
coarse fine asphalt
Results: -
Report the bulk specific gravity (G
mb
) value and the water absorption (%) at N
des
.,
Table 0-3. -
Report the correction values for each team in Table 0-4 -
Report G
mb
(
Corrected
), %G
mm
@N
ini
, %G
mm
@N
des, and %G
mm
@N
max for each team in
Table 0-5. -
Report the air void content, VMA, and VFA at N
des in Table 0-6
Your preview ends here
Eager to read complete document? Join bartleby learn and gain access to the full version
- Access to all documents
- Unlimited textbook solutions
- 24/7 expert homework help
Page 92 -
Create a plot of air void content versus asphalt content using all 12 of the lab
samples and identify the asphalt content that should yield an air void content of 4%. -
Create similar plots for VMA and VFA at N
des and indicate whether the mix design
meets the required specifications (your TA will inform you about the type of mixture
you are working with so that you can identify these specifications). Table 0-3: Density Results for Each Team
Team
Sample
Mass Sample (A), g
Saturated Surface Dry Mass (B), g
Immersed Mass (C), g
Bulk Specific Gravity @ N
max
Water Absorption
(%)
1 1 2 1 3 1 4 1 5 1 6 1 Table 0-4: Summary of Correction Values for Each Team
Team
Sample
C
1 1 2 1 3 1 4 1 5 1 6 1 Bulk Specific Gravity (
Measured
)@N
max
Bulk Specific Gravity (
Estimated
)@N
max
Your preview ends here
Eager to read complete document? Join bartleby learn and gain access to the full version
- Access to all documents
- Unlimited textbook solutions
- 24/7 expert homework help
Page 93 Table 0-5: Corrected Bulk Specific Gravity and %G
mm
Team
Sample
Bulk Specific Gravity (
Corrected
)
%Gmm
@ N
ini
@ N
des
@ N
max
@ N
ini
@ N
des
@ N
max
1 1 2 2 1 2 3 1 2 4 1 2 5 1 2 6 1 2
Your preview ends here
Eager to read complete document? Join bartleby learn and gain access to the full version
- Access to all documents
- Unlimited textbook solutions
- 24/7 expert homework help
Page 94 Table 0-6: Volumetric Properties of Sample Specimens at N
des
Team
Sample
Air Void Content @
N
des (%) VMA @ N
des VFA @ N
des 1 1 2 2 1 2 3 1 2 4 1 2 5 1 2 6 1 2 Notes:
Your preview ends here
Eager to read complete document? Join bartleby learn and gain access to the full version
- Access to all documents
- Unlimited textbook solutions
- 24/7 expert homework help
Page 95
PART III: Mechanical Test Purpose: To evaluate the moisture susceptibility of an asphalt concrete mixture. Significance: The significance of this test is evaluating the sensitivity of a given material to the negative
effects of moisture, which can erode the bond between aggregate and asphalt and
negatively impact the long-term performance of the material. Specimens, Apparatus, and Procedure: Your TA will explain and show you the basic procedure for the indirect tension test. You will combine your testing efforts with another team to learn about the impacts of
moisture damage in asphalt concrete. One of the samples that you compacted last week has
been cut into two test specimens prior to the lab. Also prior to the lab one of the test
specimens has been saturated with water via vacuum saturation and then left overnight in
a 60
°
C water bath. Depending on the material and the void structure, this water may react
with the asphalt cement to degrade the adhesive bond between the aggregate and asphalt
(we refer to this as stripping since it visually appears that the asphalt has been stripped
away from the aggregate surface). If severe enough the strength of the sample can be negatively affected and you will visually
see evidence of the moisture damage. Approximately 2.5 hours before the lab this water
bath was cooled to the testing temperature of approximately 25C. The second specimen was
also submerged in the same water bath (although protected from the water) to ensure that
both specimens were at the same test temperature. The indirect tension test is an incredibly popular test for asphalt concrete for three
essential reasons; 1) it is relatively quick to do, 2) it provides an indication of the tensile
properties of the sample, and 3) the sample geometry involves a thin asphalt concrete disk
that can be easily obtained from in-service pavements, which are built-up in lifts of
approximately 1-3 inch layers of asphalt. The test is very similar to the splitting tension
test that we say in portland cement concrete, except we use a thin sample. When loaded
along the diametrical axis the sample experiences compressive stress in the vertical
direction and a mostly uniform tensile stress in the horizontal direction. You may not be
able to visualize that there is tensile stress in the horizontal direction, but think about how
the splitting tension test failed, it was a vertical crack, driven by the horizontal tensile
stresses. Calculations: -
Observe and record the peak force from the computer screen. -
Calculate the tensile strength by using the following formula (be aware of units!): S
t
2
P
t
d
S
t = Tensile strength (psi),
Your preview ends here
Eager to read complete document? Join bartleby learn and gain access to the full version
- Access to all documents
- Unlimited textbook solutions
- 24/7 expert homework help
Page 96 P = Maximum load (lbf), t d = = Thickness of the specimen (in.), and Diameter of the specimen (in.). - Compile the tensile strength for both the non-moisture conditioned sample and the
moisture conditioned sample and calculate the tensile strength ratio (TSR), defined
as: TSR
S
t
Moisture Conditioned
S
t
Dry
- Visually observe the failure surface and comment on whether you see any visual
evidence of stripping. Table 0-7: Air Void Content for Each Sample at N
des
Sample
Peak Load (lbf)
Maximum Stress (psi)
TSR
Comments
Moisture Conditioned Non-Moisture Conditioned Notes:
Your preview ends here
Eager to read complete document? Join bartleby learn and gain access to the full version
- Access to all documents
- Unlimited textbook solutions
- 24/7 expert homework help
Page 97 Group Discussion: 1.
Use the heights of your samples to estimate the bulk specific gravity of all the
compacted samples at N
ini
, N
des
, and N
max (assume a smooth walled cylinder for this
purpose). a.
Average the replicate tests and summarize the results in a table. b.
Explain whether the true G
mb should be larger or smaller than your estimate. c.
Discuss your expectations with respect to specific gravity and asphalt
content. If the measured data do not support this expectation provide three
possible reasons why. d.
Will the following changes likely increase, decrease, or have no effect on the
density of a compacted asphalt concrete sample; 1) using coarse aggregate
with a higher density, 2) using coarse and fine aggregates with greater
angularity, and 3) using aggregates with greater absorption. 2.
Most agencies consider an acceptable mixture one that exhibits a TSR value above 0.8. Does your mixture meet this criterion? 3.
Speculate on what would happen to the dry tensile strength if the test were
performed at a higher temperature. Would you expect an increase or decrease in
tensile strength as the temperature increased? Individual Discussion: 1. Explain why you cannot compare the TSR results from the teams that tested other
asphalt contents to accurately assess the impacts of asphalt content on moisture
damage susceptibility. Then design a group of experiments that would let you
identify the effect of increasing asphalt content on moisture susceptibility. This
experimental design should be clear enough that a technician working in the
laboratory would have enough details to conduct your experiment. Hint: Technicians
and TA’s
like tables that neatly summarize everything (identify the asphalt
contents, air void contents, test rates, replicates, and all other necessary
information).
Your preview ends here
Eager to read complete document? Join bartleby learn and gain access to the full version
- Access to all documents
- Unlimited textbook solutions
- 24/7 expert homework help
Related Documents
Related Questions
Please answer the 4th question
arrow_forward
Problem 3:
Insulation
To=1
Toowwww
Steam
Tx2
T₂ T3
www www
R₁ R₁ R₂
www.T
R₂
Steam at T1 = 320 °C flows in a cast iron pipe (k= 80 W/m. °C) whose inner and outer diameters are
5 cm = 0.05 m and D₂ = 5.5 cm = 0.055 m, respectively. The pipe is covered with 3-cm-thick glass wool
insulation with k = 0.05 W/m. °C. Heat is lost to surroundings at T2 = 5 °C by natural convection and
radiation, with a combined heat transfer coefficient of h₂ = 18 W/m². °C. Taking the heat transfer coefficient
inside the pipe to be h₁ = 60 W/m². °C, determine the temperature drops across the pipe and the insulation.
The determination is based on a unit length of the pipe (L = 1 m).
Assumptions
1. Heat transfer is one-dimensional since there is no indication of any change with time.
2.
Heat transfer is one-dimensional since there is thermal symmetry about the centreline and no
variation in the axial direction.
3. Thermal conductivities are constant.
4. The thermal contact resistant at the interface is…
arrow_forward
I need help solving this problem.
arrow_forward
Please give a complete solution in Handwritten format.
Strictly don't use chatgpt,I need correct answer.
Engineering dynamics
arrow_forward
please read everything properly... Take 3 4 5 hrs but solve full accurate drawing on bond paper don't use chat gpt etc okk
arrow_forward
Instrumentation & Measurements
This homework measures your capability to design/analyze various components/variables of ameasurement system based on what you have studied.
Question is Attached in image. Thank you.
arrow_forward
Please give me the answers for this i been looking at this for a hour and my head hurts
arrow_forward
est 2 (copy) (page 4 of 9)
A wiseup.wsu.acza/mod/quiz/attempt.php7attempt=610918cmid 148960&page=3
ops
O YouTube
M Gmail
Maps
O GENERAL MATHEM.
O New Tab
:WSU WiSeUp
1 MONLO GOA
ashboard / My courses / FLM15B2_KF_WS6222 2021 / Tests / Test 2 (copy)
uestion 4
Quz navigation
Gate AB in Figure below is 1.0 m long and 0.9 wide. Calculate force F on the gate and position X of its centre of
Not yet
answered
pressure.
Marked out of
Finish attempt
10,000
Rag question
3m
Oil,
s.g.=Q81
7m
1.0m
B
50
Answer
arrow_forward
University of Babylon
Collage of Engineering\Al-Musayab
Department of Automobile
Engineering
Under Grad/Third stage
Notes:
1-Attempt Four Questions.
2- Q4 Must be Answered
3-Assume any missing data.
4 تسلم الأسئلة بعد الامتحان مع الدفتر
Subject: Mechanical
Element Design I
Date: 2022\01\25
2022-2023
Time: Three Hours
Course 1
Attempt 1
Q1/ Design a thin cylindrical pressure tank (pressure vessel) with hemispherical ends to the
automotive industry, shown in figure I below. Design for an infinite life by finding the
appropriate thickness of the vessel to carry a sinusoidal pressure varied from {(-0.1) to (6) Mpa}.
The vessel is made from Stainless Steel Alloy-Type 316 sheet annealed. The operating
temperature is 80 C° and the dimeter of the cylinder is 36 cm. use a safety factor of 1.8.
Fig. 1
(15 Marks)
Q2/ Answer the following:
1- Derive the design equation for the direct evaluation of the diameter of a shaft to a desired
fatigue safety factor, if the shaft subjected to both fluctuated…
arrow_forward
Hartley Electronics, Inc., in Nashville, producesshort runs of custom airwave scanners for the defense industry.The owner, Janet Hartley, has asked you to reduce inventory byintroducing a kanban system. After several hours of analysis, youdevelop the following data for scanner connectors used in onework cell. How many kanbans do you need for this connector?Daily demand 1,000 connectorsLead time 2 daysSafety stock 12 dayKanban size 500 connectors
arrow_forward
Technical graphics are the preferred method for communicating designs during a
design process.
True
False
arrow_forward
LESSON: AUTODESK AUTOCAD
Choose from the choices:
arrow_forward
Please show work in a handwritten format.
Don't use chatgpt.
Mechanics of materials/design.
arrow_forward
Chrome
File
Edit
View
History
Bookmarks
People
Tab
Window
Help
McGraw-Hill Campus - ALEKS Science - CHM1045 GEN CHEM 1 BLENDED 669113
A bconline.broward.edu/d21/le/content/466883/fullscreen/12868783/View
McGraw-Hill Campus - ALEKS Science
O GASES
Interconverting pressure and force
A chemistry graduate student is designing a pressure vessel for an experiment. The vessel will contain gases at pressures up to 470.0 MPa. The student's
design calls for an observation port on the side of the vessel (see diagram below). The bolts that hold the cover of this port onto the vessel can safely withstand
a force of 2.80 MN.
pressure vessel
bolts
side
View
port
Calculate the maximum safe diameter w of the port. Round your answer to the nearest 0.1 cm.
O cm
Explanation
Check
O2021 McGraw-Hill Education. All Rights Reserved. Terms of Use
FEB
arrow_forward
Mech. Engg. Dept.
4th year 2022-2023
Solar Energy
Spring course MEC364
Dr. Mahmoud U. Jasim
Review/Recap Sheet
Q1- Answer with true or false and rewrite the false statements completely in
correct form, otherwise no mark will be put on the false statements.
1
2
To represent a location on earth surface you need to define its altitude and longitude
angles.
3
Solar zenith and solar incidence angles have the same value for horizontal surface.
At sunset time the value of solar altitude angle is maximum.
4
The angle which represents the inclination of a given surface is the zenith angle
5
6
7
8
When the absolute value of sun-wall azimuth angle exceeds 90' this means that the sun
rays are reaching the receiving plane.
The solar irradiance and the solar irradiation have the same physical meaning.
In the case of clear sky weather, the beam solar irradiation on a horizontal surface is less
than the diffused irradiation.
The total solar radiation received by a tilted surface is the same as that…
arrow_forward
pls help me with this one :(
arrow_forward
Part 1. Using the simulator "Explore 2D option".
Activities.
1.1) Using the simulator, Explore 2D, and given the value for vectors a, b and c, represent all vectors in the
simulator and complete the data table 1, show all formulas and calculations.
1.2) Attach the diagram to the lab report with three vectors and their components.
1.3) In which quadrant are the vectors a, b and c. Describe the signs of its components.
Could you establish some rule about their signs? Explain.
Table 1.EXPLORE 2D
Vector a
Vector b
Magnitude Direction
Magnitude
Direction
23.3
59°
25
143.1°
Component
X
Component
y
Vector c
Magnitude
13.9
Direction
-159
arrow_forward
SEE MORE QUESTIONS
Recommended textbooks for you
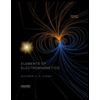
Elements Of Electromagnetics
Mechanical Engineering
ISBN:9780190698614
Author:Sadiku, Matthew N. O.
Publisher:Oxford University Press
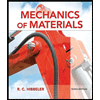
Mechanics of Materials (10th Edition)
Mechanical Engineering
ISBN:9780134319650
Author:Russell C. Hibbeler
Publisher:PEARSON
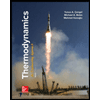
Thermodynamics: An Engineering Approach
Mechanical Engineering
ISBN:9781259822674
Author:Yunus A. Cengel Dr., Michael A. Boles
Publisher:McGraw-Hill Education
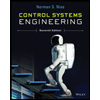
Control Systems Engineering
Mechanical Engineering
ISBN:9781118170519
Author:Norman S. Nise
Publisher:WILEY
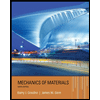
Mechanics of Materials (MindTap Course List)
Mechanical Engineering
ISBN:9781337093347
Author:Barry J. Goodno, James M. Gere
Publisher:Cengage Learning
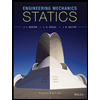
Engineering Mechanics: Statics
Mechanical Engineering
ISBN:9781118807330
Author:James L. Meriam, L. G. Kraige, J. N. Bolton
Publisher:WILEY
Related Questions
- Please answer the 4th questionarrow_forwardProblem 3: Insulation To=1 Toowwww Steam Tx2 T₂ T3 www www R₁ R₁ R₂ www.T R₂ Steam at T1 = 320 °C flows in a cast iron pipe (k= 80 W/m. °C) whose inner and outer diameters are 5 cm = 0.05 m and D₂ = 5.5 cm = 0.055 m, respectively. The pipe is covered with 3-cm-thick glass wool insulation with k = 0.05 W/m. °C. Heat is lost to surroundings at T2 = 5 °C by natural convection and radiation, with a combined heat transfer coefficient of h₂ = 18 W/m². °C. Taking the heat transfer coefficient inside the pipe to be h₁ = 60 W/m². °C, determine the temperature drops across the pipe and the insulation. The determination is based on a unit length of the pipe (L = 1 m). Assumptions 1. Heat transfer is one-dimensional since there is no indication of any change with time. 2. Heat transfer is one-dimensional since there is thermal symmetry about the centreline and no variation in the axial direction. 3. Thermal conductivities are constant. 4. The thermal contact resistant at the interface is…arrow_forwardI need help solving this problem.arrow_forward
- Please give a complete solution in Handwritten format. Strictly don't use chatgpt,I need correct answer. Engineering dynamicsarrow_forwardplease read everything properly... Take 3 4 5 hrs but solve full accurate drawing on bond paper don't use chat gpt etc okkarrow_forwardInstrumentation & Measurements This homework measures your capability to design/analyze various components/variables of ameasurement system based on what you have studied. Question is Attached in image. Thank you.arrow_forward
- Please give me the answers for this i been looking at this for a hour and my head hurtsarrow_forwardest 2 (copy) (page 4 of 9) A wiseup.wsu.acza/mod/quiz/attempt.php7attempt=610918cmid 148960&page=3 ops O YouTube M Gmail Maps O GENERAL MATHEM. O New Tab :WSU WiSeUp 1 MONLO GOA ashboard / My courses / FLM15B2_KF_WS6222 2021 / Tests / Test 2 (copy) uestion 4 Quz navigation Gate AB in Figure below is 1.0 m long and 0.9 wide. Calculate force F on the gate and position X of its centre of Not yet answered pressure. Marked out of Finish attempt 10,000 Rag question 3m Oil, s.g.=Q81 7m 1.0m B 50 Answerarrow_forwardUniversity of Babylon Collage of Engineering\Al-Musayab Department of Automobile Engineering Under Grad/Third stage Notes: 1-Attempt Four Questions. 2- Q4 Must be Answered 3-Assume any missing data. 4 تسلم الأسئلة بعد الامتحان مع الدفتر Subject: Mechanical Element Design I Date: 2022\01\25 2022-2023 Time: Three Hours Course 1 Attempt 1 Q1/ Design a thin cylindrical pressure tank (pressure vessel) with hemispherical ends to the automotive industry, shown in figure I below. Design for an infinite life by finding the appropriate thickness of the vessel to carry a sinusoidal pressure varied from {(-0.1) to (6) Mpa}. The vessel is made from Stainless Steel Alloy-Type 316 sheet annealed. The operating temperature is 80 C° and the dimeter of the cylinder is 36 cm. use a safety factor of 1.8. Fig. 1 (15 Marks) Q2/ Answer the following: 1- Derive the design equation for the direct evaluation of the diameter of a shaft to a desired fatigue safety factor, if the shaft subjected to both fluctuated…arrow_forward
- Hartley Electronics, Inc., in Nashville, producesshort runs of custom airwave scanners for the defense industry.The owner, Janet Hartley, has asked you to reduce inventory byintroducing a kanban system. After several hours of analysis, youdevelop the following data for scanner connectors used in onework cell. How many kanbans do you need for this connector?Daily demand 1,000 connectorsLead time 2 daysSafety stock 12 dayKanban size 500 connectorsarrow_forwardTechnical graphics are the preferred method for communicating designs during a design process. True Falsearrow_forwardLESSON: AUTODESK AUTOCAD Choose from the choices:arrow_forward
arrow_back_ios
SEE MORE QUESTIONS
arrow_forward_ios
Recommended textbooks for you
- Elements Of ElectromagneticsMechanical EngineeringISBN:9780190698614Author:Sadiku, Matthew N. O.Publisher:Oxford University PressMechanics of Materials (10th Edition)Mechanical EngineeringISBN:9780134319650Author:Russell C. HibbelerPublisher:PEARSONThermodynamics: An Engineering ApproachMechanical EngineeringISBN:9781259822674Author:Yunus A. Cengel Dr., Michael A. BolesPublisher:McGraw-Hill Education
- Control Systems EngineeringMechanical EngineeringISBN:9781118170519Author:Norman S. NisePublisher:WILEYMechanics of Materials (MindTap Course List)Mechanical EngineeringISBN:9781337093347Author:Barry J. Goodno, James M. GerePublisher:Cengage LearningEngineering Mechanics: StaticsMechanical EngineeringISBN:9781118807330Author:James L. Meriam, L. G. Kraige, J. N. BoltonPublisher:WILEY
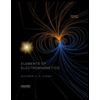
Elements Of Electromagnetics
Mechanical Engineering
ISBN:9780190698614
Author:Sadiku, Matthew N. O.
Publisher:Oxford University Press
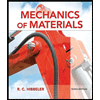
Mechanics of Materials (10th Edition)
Mechanical Engineering
ISBN:9780134319650
Author:Russell C. Hibbeler
Publisher:PEARSON
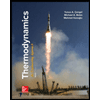
Thermodynamics: An Engineering Approach
Mechanical Engineering
ISBN:9781259822674
Author:Yunus A. Cengel Dr., Michael A. Boles
Publisher:McGraw-Hill Education
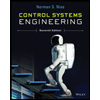
Control Systems Engineering
Mechanical Engineering
ISBN:9781118170519
Author:Norman S. Nise
Publisher:WILEY
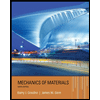
Mechanics of Materials (MindTap Course List)
Mechanical Engineering
ISBN:9781337093347
Author:Barry J. Goodno, James M. Gere
Publisher:Cengage Learning
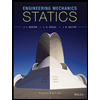
Engineering Mechanics: Statics
Mechanical Engineering
ISBN:9781118807330
Author:James L. Meriam, L. G. Kraige, J. N. Bolton
Publisher:WILEY