Homework 3 - F23 Solution
pdf
keyboard_arrow_up
School
University of Michigan *
*We aren’t endorsed by this school
Course
250
Subject
Mechanical Engineering
Date
Feb 20, 2024
Type
Pages
11
Uploaded by BailiffRiverChinchilla37
ME250 | F23 | University of Michigan
HW3: Lectures 9, 10, 11, and 12 (67 pts)
Engineering Drawings & Mfg Plans, Dimensions and Tolerances, Electric Motors, Machine Elements
Due
Friday, October 20th
by 11:59 pm on Canvas
This is an
individual
assignment, and your solution must be entirely prepared by you. Homework
assignments must be completed on your own (unless they are team assignments), however you are
encouraged to discuss the problems with your classmates. Upload a
PDF
of your solution to the
Assignments tab on Canvas.
Problem 1: Dynamic Analysis and Motors (20 points)
Figure 1: FBD of the setup
A.
Answer:
1.
Sum the moments:
𝐹
?
?
?
+ 𝐹
???
?
???
=
τ
??????
(1.28 oz)(3”) + (0.488 oz)(1.5”) = 4.572 oz-in
+1 point
for sum of moments equation
+1 point
for correct answer (within ±0.05)
2.
Apply Safety Factor:
τ
??????
?
??????
=
τ
??????, ????
4. 15 ??𝑖?
(
)
2
(
) =
9. 144 ??𝑖?
+1 point
for applying safety factor
+1 point
for applying safety factor of 2
3.
Motor Specs from
here
:
Stall torque (
τ
?
) ?? 3𝑉 = 1. 2 ??𝑖?
Stall torque (
τ
?
) ?? 6𝑉 = 2. 4 ??𝑖?
+1 point
for scaling the voltage
4.
Apply loss of efficiency:
τ
?
=
0. 2γτ
?
=
0. 2
(
)
0. 3
(
)
2. 4
(
) =
0. 144 ??𝑖?
+1 point
for applying loss of efficiency
NOTE: some students may use 0.4 efficiency, this will affect the answers following by a factor of
2, but should be treated as correct due to also applying the factor of safety in pt 2.
5.
Calculate required gear ratio:
𝑀 = τ
?
τ
?
= 9.144
0.144
= 63. 5
+1 point
for equation
+1 point
for calculating correct gear ratio required
6.
The smallest gear ratio that satisfies the torque requirement is
80:1
and verify:
τ
?
≤ 0. 2γ𝑀τ
?
=
9. 144??𝑖? ≤
0. 2
(
) 0. 3
(
) 80
(
) 2. 4??𝑖?
(
) = 11. 52??𝑖?
+1 point
for picking correct gear ratio
+1 point
for correct units throughout problem
Verifying if the torque requirement is met is good
practice, but not required
B.
With an 80:1 gear ratio,
is scaled by 80 and the no-load speed
is divided by 80. The torque
τ
?
?
?
speed curves change as shown below (they do not need to show a plot):
τ
?
≤ γ𝑀τ
?
=
9. 144??𝑖? ≤
0. 3
(
) 80
(
) 2. 4??𝑖?
(
) = 57. 6??𝑖?
z
To calculate the speed of the motor, use the torque speed curve where the torque is 57.6 oz-in. The
equation to calculate the speed is where y is the torque and x is the angular velocity:
?
?
τ
?
τ
?
− ?
(
)
= ?
For the 80:1 gear ratio:
170
57.6
57. 6
−
9. 144
(
) =
?
=
143 ???
NOTE:
may vary based on the results of part a. A consistent answer should not be penalized
τ
?
twice.
+1 point
for finding T_s
+2.5 points
for showing any work for calculating the speed (a plot, equation, etc.)
+1.5 points
for getting the correct speed (within ±3 rpm)
C.
The highest gear ratio is 400:1, the angular velocity is:
34
288
288
−
9. 144
(
) =
?
=
32. 9 ???
+2 points
for picking 400:1 gear ratio
+3 points
for calculating the correct speed correctly based on the gear ratio they put
Your preview ends here
Eager to read complete document? Join bartleby learn and gain access to the full version
- Access to all documents
- Unlimited textbook solutions
- 24/7 expert homework help
Problem 2: Power Screws (10 pts)
A standard 3/8-24 UNF threaded rod is used as a power screw to raise and lower a load. It has a lead of
0.0417 inches, a pitch diameter of 0.3479 inches, and a coefficient of friction of 0.3.
A.
When the power screw is used to raise the load, the input torque is 2.4 inch-pounds. What is the
weight of the load that is being raised? (4 pts)
?
?
=
𝐹 𝐷
?
2
?+ µπ𝐷
?
π𝐷
?
− µ?
(
)
𝐹 =
2?
?
𝐷
?
?+ µπ𝐷
?
π𝐷
?
− µ?
(
)
F = 40.33 lbf
+2 points
for equation
+2 points
for correct force
B.
How much torque does it take to lower this same load using the power screw? (4 pts)
?
?
=
𝐹 𝐷
?
2
µπ𝐷
?
−?
π𝐷
?
+ µ?
(
)
?
?
=
1. 82 ??
− 𝑖?.
+2 points
for equation
+2 points
for correct torque
C.
A lubricant is applied to the threads, how would this affect your answer to part B? (2 pts)
NEW
This would lower the coefficient of friction, hence
decreasing
the lowering torque.
+2 pts
for correct answer
Problem 3: Stackup Analysis and GD&T (13 pts)
A.
What is the nominal thread engagement? Does this meet the minimum thread engagement
requirement? ( pts)
L
e, nominal =
L
b
- a
1
- a
2
- a
3
= 1.25 - 0.2 - 0.3 - 0.1 =
0.65in
Minimum engagement for aluminum: 2 * .25 =
0.5in
Since 0.65 > 0.5, this
does
meet the minimum thread engagement requirement.
Also, since a
4
is 0.5in, then 0.5in is the maximum thread engagement possible so it still
does
meet
minimum thread engagement requirement.
+1pts
for correctly calculating L
e, nominal
(0.65in or 0.5in is acceptable)
+1pts
for correctly stating L
e, nominal
does
meet the minimum requirement for thread engagement
(
-0.25pts
if minimum thread engagement calculation is not shown anywhere in parts A-B for
comparison)
B.
Calculate the WCS stackup for thread engagement. Does this meet the minimum thread
engagement requirement? (2 pts)
WCS = L
b
tol
+ a
1
tol
+ a
2
tol
+ a
3
tol
= 0.1 + 0.05 + 0.05 + 0.010 = 0.19in
L
e, WCS
= 0.65 - 0.21 =
0.44in
Since 0.44 < 0.5, this
does not
meet the minimum thread engagement requirement.
+1pts
for correctly calculating L
e, WCS
+1pts
for correctly stating L
e,WCS
does not
meet the minimum thread engagement requirement.
C.
Respond to and explain your answer to the following:
a.
Do you think the worst-case scenario (WCS) method used above is a good strategy for
calculating tolerance stack ups? (1 pt)
(+1 pt)
Any answer with justification is acceptable here (ie, yes because it’s conservative, or no
because it’s probably never going to actually happen unless manufacturing volume is very high)
b.
Is the WCS likely to ever occur? (1 pt)
+1 pt
for correctly answering NO. Intuitively, it’s more likely that an actual measurement would
fall somewhere in between the high and low of the tolerance zone than the high or low
themselves.
D. A different part in the same assembly has these two feature control frames. Translate each
tolerance description into a feature control frame by filling in the provided blank feature
control frames. (7 pts)
a.
Position of 0.005 at MMC to datum A, datum B at MMC, and datum C at LMC.
+0.5 pts
for each correct symbol above (
4.5 pts total
)
-0.5 points
for each extraneous symbol (ie, adding MMC anywhere but on datum B)
b.
Profile of a surface of 0.01 to datum E at MMC and datum C.
+ 0.5 points
.for each correct symbol above (
2.5 pts total
)
-0.5 points
for each extraneous symbol (ie, putting diameter symbol, adding MMC
anywhere but on datum E)
Your preview ends here
Eager to read complete document? Join bartleby learn and gain access to the full version
- Access to all documents
- Unlimited textbook solutions
- 24/7 expert homework help
Problem 4: Engineering Drawings (14 pts)
A.
Using the provided top and right views of the drawing below, draw the missing front view to
scale on the provided sheet. (6 pts)
+1 point
if problem was attempted
+0.5 points
per centreline (1.5 points total)
+0.25 points
per hidden line (1.5 points total)
+0.5 points
for each proper height circled below (1.5 points total)
+ 0.5 points
for cut-out shown below
B.
With the three views you now have, create an isometric sketch of the part on the provided
isometric grid paper. (8 pts)
Note:
Example solution is shown from right side angle, but left side angle is acceptable and
should be graded the same.
+2 points
for correct scale (allow .25” of variation in lengths)
+1 point
for each hole (3 points total, be lenient on quality of drawings of holes)
+1 point
if front cut-out is drawn properly (see above)
+2 points
if general shape is correct
Problem 5: Fasteners and Joining Techniques (10 pts)
Diagram for reference.
A. To solve the fasteners questions, we need to reference the Drill and Tap Chart provided:
(5 pts)
Based on the Drill and Tap Chart, for a #18 free fit, we identify that this is for a #6 screw.
Next, we are provided that the tapped hole uses a #33 drill. Looking at the tap size
column, we see this corresponds to a 6-40 screw. The major diameter of a #6 screw is
listed as 0.138”. The threads per inch is 40. The minimum required thread engagement is
twice the major diameter when tapping aluminum, which is
.
2×0. 138" = 0. 276"
+1.5 points
for correct major diameter
+1.5 points
for correctly threads per inch
+2 points
for correct minimum thread engagement.
Your preview ends here
Eager to read complete document? Join bartleby learn and gain access to the full version
- Access to all documents
- Unlimited textbook solutions
- 24/7 expert homework help
B. To solve the fasteners questions, we need to reference the Drill and Tap Chart provided:
(3 pts)
Based on the charts, for a #29 free fit, we are using a #4 screw. The #4 screw has two
thread count options: 40, 48. Thus, 40 is the coarse thread count. The major diameter is
listed as 0.112”, and the threads/inch is 40 threads/inch.
+1.5 points
for correct major diameter
+1.5 points
for correct threads/inch
C. To solve the fasteners questions, we need to reference the Drill and Tap Chart provided:
(2 pts)
Based on the chart, for a 9/32” size drill free fit, we identify this is a ¼” screw. Looking
at the other chart, since it is a coarse thread fastener, we identify this is a ¼”-20. The
major diameter for a ¼” fastener is 0.250”, and the coarse threads/inch is 20.
+1 point
for correct major diameter
+1 point
for correct threads/inch
Related Documents
Related Questions
Need help with this
arrow_forward
The class I'm taking is physics for scientists and engineers!
**** I need help with part D only*****
Can you please write out the solution and not type out the solution? I had to reask this question because the last tutor typed out the solution and it was very hard for me to follow . Please and thank you for the special request.
I have attached the problem. Please view attachment before answering. Thank you!
arrow_forward
I pay for professionals monthly to help with my homework questions and every question I’ve asked for the last two weeks have been rejected. Honestly just trying to psd this class so I can retake after I learn the basics. This is supposed to be introduction to engineering and it’s definitely exceeding introduction. Could I please get some assistance drawing this problem?
arrow_forward
Please make the charts for the questions. Please refer to Successful Project Management (7th Edition). Attached is the example
Thank you.
arrow_forward
Help!!! Answer all parts correctly!! Please
arrow_forward
LESSON: AUTODESK AUTOCAD
Choose from the choices:
arrow_forward
Question 3
You are working on a design team at a small orthopaedic firm. Your team is starting to work on a lower limb
(foot-ankle) prosthesis for individuals who have undergone foot amputation (bone resection at the distal tibia). You remember hearing
about "osseointegration" in an exciting orthopaedic engineering class you attended at Clemson, so you plan to attach the foot
prosthesis using a solid metal rod inserted into the distal tibia. You think stainless steel or titanium alloy might be a useful rod material.
You decide to begin this problem by identifying typical tibial bone anatomy and mechanical behavior (as provided in the tables and
image below). You assume the tibial bone can be modeled as a hollow cylinder of cortical bone, as represented in the image. You
anticipate the length of the rod will be 1/2 the length of the tibia.
Q3G: Critical Thinking: What would you propose to your team as the next step in this analysis? Is it reasonable to assume the rod
will experience the…
arrow_forward
Astronomy Question:
Read the questions slowly and answer with precise and long details about each of the questions. Answer correctly and follow my guidelines for a long and wonderful review after results. Your target/main observable galaxy is the whirlpool galaxy. Target: Whirlpool Galaxy Object Type: Galaxy Distance: 37 million light-years Constellation: Canes Venatici. DO NOT COPY AND PASTE OTHER WORK OR THINGS FROM THE INTERNET, use your own words.Provide refernces if used
In 500 words, please explain the relevance of this object to the physics course material in university andits importance to astronomy. (Some question you may seek to answer are: What beyond the objectitself is learned by studying this class of objects? What sorts of telescopes and observations would beneeded for more detailed, broader reaching studies of this source and objects of its nature?)
arrow_forward
Mech. Engg. Dept.
4th year 2022-2023
Solar Energy
Spring course MEC364
Dr. Mahmoud U. Jasim
Review/Recap Sheet
Q1- Answer with true or false and rewrite the false statements completely in
correct form, otherwise no mark will be put on the false statements.
1
2
To represent a location on earth surface you need to define its altitude and longitude
angles.
3
Solar zenith and solar incidence angles have the same value for horizontal surface.
At sunset time the value of solar altitude angle is maximum.
4
The angle which represents the inclination of a given surface is the zenith angle
5
6
7
8
When the absolute value of sun-wall azimuth angle exceeds 90' this means that the sun
rays are reaching the receiving plane.
The solar irradiance and the solar irradiation have the same physical meaning.
In the case of clear sky weather, the beam solar irradiation on a horizontal surface is less
than the diffused irradiation.
The total solar radiation received by a tilted surface is the same as that…
arrow_forward
I need answers to problems 7, 8, and 9.
NOTE: Please stop wasting my time and yours by rejecting my question because it DOES NOT REQUIRE YOU TO DRAW anything at all. They are simple questions pertaining to the print provided. READ THE INSTRUCTIONS of the assignment before you just reject it for a FALSE reason or leave it for someone to answer that actually wants to do their job. Thanks.
arrow_forward
J 6
arrow_forward
Case Study: Paula’s Pain
Paula has worked for Brindle Corporation for 3 years. During this time, she has worked as a machine operator/cell leader in various work cells. Recently, the plant went to mandatory 12-hour shifts and plans to remain on this schedule for several months.
Paula’s present work cell is manufacturing 3-inch diameter exhaust tubes that are made from stainless steel. These tubes get a hole punched in them, a flange welded on, and burrs ground off. The pipe then gets placed into a gage to check that it was made correctly. (The tubes weigh about six pounds.)
Paula has been performing the welding operation. She leans into the machine and loads the part into a fixture then positions the flange. Both pieces are clamped (using hand clamps) into position and the machine is cycled by depressing two palm buttons.
The gaging operation requires placing the finished part into the gage and clamping it (using hand clamps) into place. A pin is depressed to verify the position…
arrow_forward
I need answers to questions 1, 2, and 3 pertaining to the print provided.
Note: A tutor keeps putting 1 question into 3 parts and wasted so many of my questions. Never had a issue before until now, please allow a different tutor to answer because I was told I am allowed 3 of these questions.
arrow_forward
I need parts 1, 2, and 3 answered pertaining to the print provided.
NOTE: If you refuse to answers all 3 parts and insist on wasting my question, then just leave it for someone else to answer. I've never had an issue until recently one single tutor just refuses to even read the instructions of the question and just denies it for a false reasons or drags on 1 part into multiple parts for no reason.
arrow_forward
as per your policy, customer service from bartley stated since you took a incomplete question and answered it instead of questions that actually need answering.
you owe me my questions and not to only solve one question, kindly solve all 3. And when i end up switching to CHEG not only will i be posting this on my vlog and social media i will also be contacting BBB and i will make sure to find out whos the special kid behind answering and trolling me ((:
kindly answer all 3 , thanks
arrow_forward
I need answers for problems 13, 14, and 15 pertaining to the print provided.
NOTE: If you refuse to answers all 3 parts and insist on wasting my question by breaking down 1 simple question into 3 parts, then just leave it for someone else to answer. Thank you.
arrow_forward
This is an engineering problem and not a writing assignment. Please Do Not Reject. I had other engineering tutors on bartleby help me with problems similar to this one.
This problem must be presented in a logical order showing the necessary steps used to arrive at an answer. Each homework problem should have the following items unless otherwise stated in the problem:
a. Known: State briefly what is known about the problem.
b. Schematic: Draw a schematic of the physical system or control volume.
c. Assumptions: List all necessary assumptions used to complete the problem.
d. Properties: Identify the source of property values not given to you in the problem. Most sources will be from a table in the textbook (i.e. Table A-4).
e. Find: State what must be found.
f. Analysis: Start your analysis with any necessary equations. Develop your analysis as completely as possible before inserting values and performing the calculations. Draw a box around your answers and include units and follow an…
arrow_forward
Case Study – The New Engineer
Jeff was just hired by GSI, Inc. to be their Environmental and Safety Coordinator. This is Jeff's first position after completing his engineering degree. He had taken a course in safety engineering as part of his studies and felt confident that he could handle the job.
Management at GSI, Inc. has assured him that they are committed to maintaining a safe workplace. They have never had an individual dedicated to this task full-time. They will implement his recommendations if he can justify them.
As Jeff begins to get familiar with the operations, he spends considerable time on the production floor. He notices workers clean their tools before break with a liquid from an unmarked 55-gallon drum. They also use this liquid to clean residue from their skin. They use paper towels to dry their tools and hands, throw these towels in the trash, and head to the break room for a snack and/or smoke.
In talking with the workers, Jeff learns of some of…
arrow_forward
Case Study – The New Engineer
Jeff was just hired by GSI, Inc. to be their Environmental and Safety Coordinator. This is Jeff's first position after completing his engineering degree. He had taken a course in safety engineering as part of his studies and felt confident that he could handle the job.
Management at GSI, Inc. has assured him that they are committed to maintaining a safe workplace. They have never had an individual dedicated to this task full-time. They will implement his recommendations if he can justify them.
As Jeff begins to get familiar with the operations, he spends considerable time on the production floor. He notices workers clean their tools before break with a liquid from an unmarked 55-gallon drum. They also use this liquid to clean residue from their skin. They use paper towels to dry their tools and hands, throw these towels in the trash, and head to the break room for a snack and/or smoke.
In talking with the workers, Jeff learns of some of…
arrow_forward
all one question help asap please!
arrow_forward
heck my work mode : This shows what is correct or incorrect for the work you have completed so far. It does not indicate completion.
Return to question
Required information
NOTE: This is a multi-part question. Once an answer is submitted, you will be unable to return to this part.
The loading for a beam is as shown in the figure, where F1= 19 lb, F2= 20 lb, F3= 35 lb, F4= 2O Ib, and F5 = 15 lb.
F1
F2
F3
F4
F5
O B
6 in 8 in.-8 in. -6 in.-
Determine the reaction at A. (You must provide an answer before moving to the next part.)
The reaction at A is
76 c 8 Ib
raw
ill
10:45 PM
ENG
69°F Mostly cloudy
10/6/2021
pe here to search
近
arrow_forward
I need problems 6 and 7 solved.
I got it solved on 2 different occasions and it is not worded correctly.
NOTE: Problem 1 is an example of how it should be answered. Below are 2 seperate links to same question asked and once again it was not answered correctly. 1. https://www.bartleby.com/questions-and-answers/it-vivch-print-reading-for-industry-228-class-date-name-review-activity-112-for-each-local-note-or-c/cadc3f7b-2c2f-4471-842b-5a84bf505857
2. https://www.bartleby.com/questions-and-answers/it-vivch-print-reading-for-industry-228-class-date-name-review-activity-112-for-each-local-note-or-c/bd5390f0-3eb6-41ff-81e2-8675809dfab1
arrow_forward
Don't use chatgpt will upvote
arrow_forward
SEE MORE QUESTIONS
Recommended textbooks for you
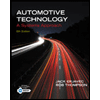
Automotive Technology: A Systems Approach (MindTa...
Mechanical Engineering
ISBN:9781133612315
Author:Jack Erjavec, Rob Thompson
Publisher:Cengage Learning
Related Questions
- Need help with thisarrow_forwardThe class I'm taking is physics for scientists and engineers! **** I need help with part D only***** Can you please write out the solution and not type out the solution? I had to reask this question because the last tutor typed out the solution and it was very hard for me to follow . Please and thank you for the special request. I have attached the problem. Please view attachment before answering. Thank you!arrow_forwardI pay for professionals monthly to help with my homework questions and every question I’ve asked for the last two weeks have been rejected. Honestly just trying to psd this class so I can retake after I learn the basics. This is supposed to be introduction to engineering and it’s definitely exceeding introduction. Could I please get some assistance drawing this problem?arrow_forward
- Question 3 You are working on a design team at a small orthopaedic firm. Your team is starting to work on a lower limb (foot-ankle) prosthesis for individuals who have undergone foot amputation (bone resection at the distal tibia). You remember hearing about "osseointegration" in an exciting orthopaedic engineering class you attended at Clemson, so you plan to attach the foot prosthesis using a solid metal rod inserted into the distal tibia. You think stainless steel or titanium alloy might be a useful rod material. You decide to begin this problem by identifying typical tibial bone anatomy and mechanical behavior (as provided in the tables and image below). You assume the tibial bone can be modeled as a hollow cylinder of cortical bone, as represented in the image. You anticipate the length of the rod will be 1/2 the length of the tibia. Q3G: Critical Thinking: What would you propose to your team as the next step in this analysis? Is it reasonable to assume the rod will experience the…arrow_forwardAstronomy Question: Read the questions slowly and answer with precise and long details about each of the questions. Answer correctly and follow my guidelines for a long and wonderful review after results. Your target/main observable galaxy is the whirlpool galaxy. Target: Whirlpool Galaxy Object Type: Galaxy Distance: 37 million light-years Constellation: Canes Venatici. DO NOT COPY AND PASTE OTHER WORK OR THINGS FROM THE INTERNET, use your own words.Provide refernces if used In 500 words, please explain the relevance of this object to the physics course material in university andits importance to astronomy. (Some question you may seek to answer are: What beyond the objectitself is learned by studying this class of objects? What sorts of telescopes and observations would beneeded for more detailed, broader reaching studies of this source and objects of its nature?)arrow_forwardMech. Engg. Dept. 4th year 2022-2023 Solar Energy Spring course MEC364 Dr. Mahmoud U. Jasim Review/Recap Sheet Q1- Answer with true or false and rewrite the false statements completely in correct form, otherwise no mark will be put on the false statements. 1 2 To represent a location on earth surface you need to define its altitude and longitude angles. 3 Solar zenith and solar incidence angles have the same value for horizontal surface. At sunset time the value of solar altitude angle is maximum. 4 The angle which represents the inclination of a given surface is the zenith angle 5 6 7 8 When the absolute value of sun-wall azimuth angle exceeds 90' this means that the sun rays are reaching the receiving plane. The solar irradiance and the solar irradiation have the same physical meaning. In the case of clear sky weather, the beam solar irradiation on a horizontal surface is less than the diffused irradiation. The total solar radiation received by a tilted surface is the same as that…arrow_forward
- I need answers to problems 7, 8, and 9. NOTE: Please stop wasting my time and yours by rejecting my question because it DOES NOT REQUIRE YOU TO DRAW anything at all. They are simple questions pertaining to the print provided. READ THE INSTRUCTIONS of the assignment before you just reject it for a FALSE reason or leave it for someone to answer that actually wants to do their job. Thanks.arrow_forwardJ 6arrow_forwardCase Study: Paula’s Pain Paula has worked for Brindle Corporation for 3 years. During this time, she has worked as a machine operator/cell leader in various work cells. Recently, the plant went to mandatory 12-hour shifts and plans to remain on this schedule for several months. Paula’s present work cell is manufacturing 3-inch diameter exhaust tubes that are made from stainless steel. These tubes get a hole punched in them, a flange welded on, and burrs ground off. The pipe then gets placed into a gage to check that it was made correctly. (The tubes weigh about six pounds.) Paula has been performing the welding operation. She leans into the machine and loads the part into a fixture then positions the flange. Both pieces are clamped (using hand clamps) into position and the machine is cycled by depressing two palm buttons. The gaging operation requires placing the finished part into the gage and clamping it (using hand clamps) into place. A pin is depressed to verify the position…arrow_forward
arrow_back_ios
SEE MORE QUESTIONS
arrow_forward_ios
Recommended textbooks for you
- Automotive Technology: A Systems Approach (MindTa...Mechanical EngineeringISBN:9781133612315Author:Jack Erjavec, Rob ThompsonPublisher:Cengage Learning
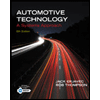
Automotive Technology: A Systems Approach (MindTa...
Mechanical Engineering
ISBN:9781133612315
Author:Jack Erjavec, Rob Thompson
Publisher:Cengage Learning