NDT Assignment 3
docx
keyboard_arrow_up
School
Conestoga College *
*We aren’t endorsed by this school
Course
QUAL 8290
Subject
Mechanical Engineering
Date
Feb 20, 2024
Type
docx
Pages
3
Uploaded by DukeToadMaster645
Student
Name: HUNNY VATS 8817275
Deliverable: Assignment #3- Individual
– Non-Destructive Testing
Course Name:
Qual8290 Non-Destructive Testing Date Assigned: 10-03-2023
Date Due: 26-03-2023 Rules: 1)
This assignment will be completed individually 2)
You will use Word, PowerPoint, and other tools you feel appropriate for this exercise 3)
Your work must be your own 4)
Each deliverable should be clear and simple to read 1.
List 3 applications of Digital Radiography and How is it different from Manual Radiography?
2.
List 3 applications of Thermal Infrared Testing?
3.
Imagine yourself a supervisor for a machine shop. You would like to communicate welding discontinuity for a welder. What kind of NDT principles you need to include in your communication plan?
1.
An NDT method known as "digital radiography" (DR) uses digital sensors to take pictures of inside structures for inspection purposes. As an example of how digital radiography varies from manual radiography, consider these three NDT applications:
Aerospace Industry:
For the inspection of aircraft parts, including engine blades, turbine discs, and landing gear, digital radiography is frequently utilized in the aerospace sector. Due to DR's high-
resolution photos, inspectors can more precisely find flaws, including fractures, corrosion, and voids.
DR creates images faster than manual radiography, exposes inspectors to less radiation, and simplifies saving and retrieving digital images.
Oil and gas sector:
Digital radiography is also used to inspect pipelines, tanks, and other crucial parts
in the oil and gas sector. Due to DR's high-resolution photos, inspectors can more accurately spot flaws like corrosion, leaks, and obstructions. Manufacturing:
For the examination of welds, castings, and other crucial parts, digital radiography is
frequently employed in the manufacturing sector. Thanks to DR's high-resolution photographs, inspectors can more precisely identify flaws, including porosity, cracks, and incomplete fusion. In conclusion, digital radiography is a cutting-edge NDT method with several benefits over manual radiography. These benefits include quicker image processing, better image resolution, less radiation
exposure, and more straightforward digital image storage and retrieval. In numerous applications, digital radiography is used in the manufacturing, oil & gas, and aerospace sectors to provide high-
quality images that enable more precise inspection and flaw detection.
2.A non-destructive testing method called thermal infrared testing (TIR) employs the detection of infrared radiation emitted from a surface to pinpoint potential issues. These are three typical uses for TIR:
Inspections in Buildings
: TIR is used in building inspections to find electrical problems, air leaks, moisture, and inadequate insulation. The method helps to spot temperature variations on a building's surface that signify heat loss, which can be linked to the issue's root.
Inspections in the industrial setting:
TIR is used to find flaws in machinery, including motors, boilers,
and pipes. The method helps in spotting hot spots that might be signs of corrosion, wear or other issues like overheating.
Medical Diagnostics: TIR is used in medical diagnostics to identify diseased or inflamed regions, including breast cancer. This method helps in detecting temperature changes between healthy and diseased tissue, allowing the problem's exact location to be determined.
3.To convey welding discontinuity to a welder as a machine shop supervisor, I would need to incorporate the following Non-Destructive Testing (NDT) principles into my communication strategy:
Visual Inspection:
The simplest type of NDT is visual inspection, which entails inspecting the weld for
flaws such as undercutting, porosity, and surface fractures. I would give the welder instructions to evaluate the weld and note any defects visually.
Radiographic Testing
: X-rays or gamma rays are used in radiographic testing (RT) to provide an image of the weld. I would explain RT to the welder and give them instructions to run this test on the
weld to look for internal flaws, such as fractures or a lack of fusion.
Ultrasonic Testing (UT): This method uses high-frequency sound waves to examine the weld for flaws or imperfections. I would inform the welder of UT and request that they use it to find any subsurface flaws or discontinuities.
Magnetic Particle Testing:
Iron particles are applied to the surface, and the weld is magnetized in the magnetic particle testing (MT) method. Any locations where the magnetic field is warped because of a crack or another flaw will see an accumulation of particles. I would explain MT to the welder and request that they run this test on the weld to look for any surface or subsurface flaws.
Overall, I can assist the welder in identifying welding discontinuity and taking corrective action to guarantee that the weld complies with the necessary quality requirements by including these NDT principles in my communication plan.
Your preview ends here
Eager to read complete document? Join bartleby learn and gain access to the full version
- Access to all documents
- Unlimited textbook solutions
- 24/7 expert homework help
Related Documents
Related Questions
I need parts 8, 9, and 10 answered. Number 1 is an example of how it should be answered.
NOTE: Read the instructions, no where does it say any drawing is required. It is really frustrating when I wait all this time for an answer to a question and some tutor does even read the instructions and just declines it...its ridicilous.
arrow_forward
I need answers to questions 1, 2, and 3 pertaining to the print provided.
Note: A tutor keeps putting 1 question into 3 parts and wasted so many of my questions. Never had a issue before until now, please allow a different tutor to answer because I was told I am allowed 3 of these questions.
arrow_forward
I need parts 1, 2, and 3 answered pertaining to the print provided.
NOTE: If you refuse to answers all 3 parts and insist on wasting my question, then just leave it for someone else to answer. I've never had an issue until recently one single tutor just refuses to even read the instructions of the question and just denies it for a false reasons or drags on 1 part into multiple parts for no reason.
arrow_forward
Please give me the answers for this i been looking at this for a hour and my head hurts
arrow_forward
I need answers for problems 13, 14, and 15 pertaining to the print provided.
NOTE: If you refuse to answers all 3 parts and insist on wasting my question by breaking down 1 simple question into 3 parts, then just leave it for someone else to answer. Thank you.
arrow_forward
I need answers to questions 7, 8, and 9 pertaining to the print provided.
Note: A tutor keeps putting 1 question into 3 parts and wasted so many of my questions. Never had a issue before until now, please allow a different tutor to answer because I was told I am allowed 3 of these questions.
arrow_forward
Please answer the 4th question
arrow_forward
Please make the charts for the questions. Please refer to Successful Project Management (7th Edition). Attached is the example
Thank you.
arrow_forward
I need problems 6 and 7 solved.
I got it solved on 2 different occasions and it is not worded correctly.
NOTE: Problem 1 is an example of how it should be answered. Below are 2 seperate links to same question asked and once again it was not answered correctly. 1. https://www.bartleby.com/questions-and-answers/it-vivch-print-reading-for-industry-228-class-date-name-review-activity-112-for-each-local-note-or-c/cadc3f7b-2c2f-4471-842b-5a84bf505857
2. https://www.bartleby.com/questions-and-answers/it-vivch-print-reading-for-industry-228-class-date-name-review-activity-112-for-each-local-note-or-c/bd5390f0-3eb6-41ff-81e2-8675809dfab1
arrow_forward
This is Mechanical Engineering. Please answer with clear work and answers. Thank you
arrow_forward
Question 2
You are a biomedical engineer working for a small orthopaedic firm that fabricates rectangular shaped fracture
fixation plates from titanium alloy (model = "Ti Fix-It") materials. A recent clinical report documents some problems with the plates
implanted into fractured limbs. Specifically, some plates have become permanently bent while patients are in rehab and doing partial
weight bearing activities.
Your boss asks you to review the technical report that was generated by the previous test engineer (whose job you now have!) and used to
verify the design. The brief report states the following... "Ti Fix-It plates were manufactured from Ti-6Al-4V (grade 5) and machined into
solid 150 mm long beams with a 4 mm thick and 15 mm wide cross section. Each Ti Fix-It plate was loaded in equilibrium in a 4-point bending
test (set-up configuration is provided in drawing below), with an applied load of 1000N. The maximum stress in this set-up was less than the
yield stress for the…
arrow_forward
I asked for problems 6 and 7 to be answered, but I did not get a properly structured answered as the example shows on problem number 1. Here is the link to the questions I already had answered, could you please rewrite the answer so its properly answered as the example shows (Problem 1)?
https://www.bartleby.com/questions-and-answers/it-vivch-print-reading-for-industry-228-class-date-name-review-activity-112-for-each-local-note-or-c/cadc3f7b-2c2f-4471-842b-5a84bf505857
arrow_forward
Help!!! Please answer part b correctly like part A. Please!!!!
arrow_forward
all one question help asap please!
arrow_forward
please help solve A-F. thank you
You are an engineer working on a project and your prototype has failed prematurely. You question whether or not a key component of the prototype was manufactured with the correct material. There are two way to check for the material properties. The first way is to have a material certification done to confirm the exact material composition. This will take some time. The second method to confirm the material properties is to make an ASTM test sample and test for the material properties. This tensile test was completed on a test sample with an initial diameter of .501” and an initial length of 2”. The Load-Deflection data for this tensile test is below. Use this data to answer the first set of questions on the Final Exam in eLearning. A. Determine the Ultimate Tensile Strength B. Determine the 0.2% Offset Yield Strength C. Determine the value of the Proportional Limit D. Determine the Modulus of Elasticity E. Determine the Strain at Yield F. Calculate %…
arrow_forward
Help!!! Answer all parts correctly!! Please
arrow_forward
please read everything properly... Take 3 4 5 hrs but solve full accurate drawing on bond paper don't use chat gpt etc okk
arrow_forward
I need answers to questions 13, 14, and 15 pertaining to the print provided.
Note: A tutor keeps putting 1 question into 3 parts and wasted so many of my questions. Never had a issue before until now, please allow a different tutor to answer because I was told I am allowed 3 of these questions.
arrow_forward
I will rate you with “LIKE/UPVOTE," if it is COMPLETE STEP-BY-STEP SOLUTION.
If it is INCOMPLETE SOLUTION and there are SHORTCUTS OF SOLUTION, I will rate you with “DISLIKE/DOWNVOTE.”
THANK YOU FOR YOUR HELP.
PS: If you have answered this already, DON'T ANSWER IT AGAIN; give chance to OTHER EXPERTS to answer it. I want to verify if all of you will arrive in the same final answer; thats why I ask it multiple times. If you answer it again, i'll DISLIKE all your entries/answers.
arrow_forward
I will rate you with “LIKE/UPVOTE," if it is COMPLETE STEP-BY-STEP SOLUTION.
If it is INCOMPLETE SOLUTION and there are SHORTCUTS OF SOLUTION, I will rate you with “DISLIKE/DOWNVOTE.”
THANK YOU FOR YOUR HELP.
PS: If you have answered this already, DON'T ANSWER IT AGAIN; give chance to OTHER EXPERTS to answer it. I want to verify if all of you will arrive in the same final answer; thats why I ask it multiple times. If you answer it again, i'll DISLIKE all your entries/answers.
arrow_forward
I will rate you with “LIKE/UPVOTE," if it is COMPLETE STEP-BY-STEP SOLUTION.
If it is INCOMPLETE SOLUTION and there are SHORTCUTS OF SOLUTION, I will rate you with “DISLIKE/DOWNVOTE.”
THANK YOU FOR YOUR HELP.
PS: If you have answered this already, DON'T ANSWER IT AGAIN; give chance to OTHER EXPERTS to answer it. I want to verify if all of you will arrive in the same final answer; thats why I ask it multiple times. If you answer it again, i'll DISLIKE all your entries/answers.
arrow_forward
LESSON: AUTODESK AUTOCAD
Choose from the choices:
arrow_forward
SEE MORE QUESTIONS
Recommended textbooks for you
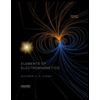
Elements Of Electromagnetics
Mechanical Engineering
ISBN:9780190698614
Author:Sadiku, Matthew N. O.
Publisher:Oxford University Press
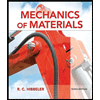
Mechanics of Materials (10th Edition)
Mechanical Engineering
ISBN:9780134319650
Author:Russell C. Hibbeler
Publisher:PEARSON
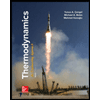
Thermodynamics: An Engineering Approach
Mechanical Engineering
ISBN:9781259822674
Author:Yunus A. Cengel Dr., Michael A. Boles
Publisher:McGraw-Hill Education
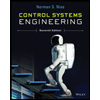
Control Systems Engineering
Mechanical Engineering
ISBN:9781118170519
Author:Norman S. Nise
Publisher:WILEY
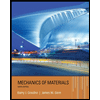
Mechanics of Materials (MindTap Course List)
Mechanical Engineering
ISBN:9781337093347
Author:Barry J. Goodno, James M. Gere
Publisher:Cengage Learning
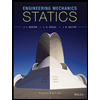
Engineering Mechanics: Statics
Mechanical Engineering
ISBN:9781118807330
Author:James L. Meriam, L. G. Kraige, J. N. Bolton
Publisher:WILEY
Related Questions
- I need parts 8, 9, and 10 answered. Number 1 is an example of how it should be answered. NOTE: Read the instructions, no where does it say any drawing is required. It is really frustrating when I wait all this time for an answer to a question and some tutor does even read the instructions and just declines it...its ridicilous.arrow_forwardI need answers to questions 1, 2, and 3 pertaining to the print provided. Note: A tutor keeps putting 1 question into 3 parts and wasted so many of my questions. Never had a issue before until now, please allow a different tutor to answer because I was told I am allowed 3 of these questions.arrow_forwardI need parts 1, 2, and 3 answered pertaining to the print provided. NOTE: If you refuse to answers all 3 parts and insist on wasting my question, then just leave it for someone else to answer. I've never had an issue until recently one single tutor just refuses to even read the instructions of the question and just denies it for a false reasons or drags on 1 part into multiple parts for no reason.arrow_forward
- Please give me the answers for this i been looking at this for a hour and my head hurtsarrow_forwardI need answers for problems 13, 14, and 15 pertaining to the print provided. NOTE: If you refuse to answers all 3 parts and insist on wasting my question by breaking down 1 simple question into 3 parts, then just leave it for someone else to answer. Thank you.arrow_forwardI need answers to questions 7, 8, and 9 pertaining to the print provided. Note: A tutor keeps putting 1 question into 3 parts and wasted so many of my questions. Never had a issue before until now, please allow a different tutor to answer because I was told I am allowed 3 of these questions.arrow_forward
- Please answer the 4th questionarrow_forwardPlease make the charts for the questions. Please refer to Successful Project Management (7th Edition). Attached is the example Thank you.arrow_forwardI need problems 6 and 7 solved. I got it solved on 2 different occasions and it is not worded correctly. NOTE: Problem 1 is an example of how it should be answered. Below are 2 seperate links to same question asked and once again it was not answered correctly. 1. https://www.bartleby.com/questions-and-answers/it-vivch-print-reading-for-industry-228-class-date-name-review-activity-112-for-each-local-note-or-c/cadc3f7b-2c2f-4471-842b-5a84bf505857 2. https://www.bartleby.com/questions-and-answers/it-vivch-print-reading-for-industry-228-class-date-name-review-activity-112-for-each-local-note-or-c/bd5390f0-3eb6-41ff-81e2-8675809dfab1arrow_forward
- This is Mechanical Engineering. Please answer with clear work and answers. Thank youarrow_forwardQuestion 2 You are a biomedical engineer working for a small orthopaedic firm that fabricates rectangular shaped fracture fixation plates from titanium alloy (model = "Ti Fix-It") materials. A recent clinical report documents some problems with the plates implanted into fractured limbs. Specifically, some plates have become permanently bent while patients are in rehab and doing partial weight bearing activities. Your boss asks you to review the technical report that was generated by the previous test engineer (whose job you now have!) and used to verify the design. The brief report states the following... "Ti Fix-It plates were manufactured from Ti-6Al-4V (grade 5) and machined into solid 150 mm long beams with a 4 mm thick and 15 mm wide cross section. Each Ti Fix-It plate was loaded in equilibrium in a 4-point bending test (set-up configuration is provided in drawing below), with an applied load of 1000N. The maximum stress in this set-up was less than the yield stress for the…arrow_forwardI asked for problems 6 and 7 to be answered, but I did not get a properly structured answered as the example shows on problem number 1. Here is the link to the questions I already had answered, could you please rewrite the answer so its properly answered as the example shows (Problem 1)? https://www.bartleby.com/questions-and-answers/it-vivch-print-reading-for-industry-228-class-date-name-review-activity-112-for-each-local-note-or-c/cadc3f7b-2c2f-4471-842b-5a84bf505857arrow_forward
arrow_back_ios
SEE MORE QUESTIONS
arrow_forward_ios
Recommended textbooks for you
- Elements Of ElectromagneticsMechanical EngineeringISBN:9780190698614Author:Sadiku, Matthew N. O.Publisher:Oxford University PressMechanics of Materials (10th Edition)Mechanical EngineeringISBN:9780134319650Author:Russell C. HibbelerPublisher:PEARSONThermodynamics: An Engineering ApproachMechanical EngineeringISBN:9781259822674Author:Yunus A. Cengel Dr., Michael A. BolesPublisher:McGraw-Hill Education
- Control Systems EngineeringMechanical EngineeringISBN:9781118170519Author:Norman S. NisePublisher:WILEYMechanics of Materials (MindTap Course List)Mechanical EngineeringISBN:9781337093347Author:Barry J. Goodno, James M. GerePublisher:Cengage LearningEngineering Mechanics: StaticsMechanical EngineeringISBN:9781118807330Author:James L. Meriam, L. G. Kraige, J. N. BoltonPublisher:WILEY
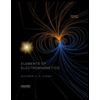
Elements Of Electromagnetics
Mechanical Engineering
ISBN:9780190698614
Author:Sadiku, Matthew N. O.
Publisher:Oxford University Press
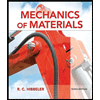
Mechanics of Materials (10th Edition)
Mechanical Engineering
ISBN:9780134319650
Author:Russell C. Hibbeler
Publisher:PEARSON
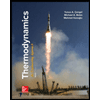
Thermodynamics: An Engineering Approach
Mechanical Engineering
ISBN:9781259822674
Author:Yunus A. Cengel Dr., Michael A. Boles
Publisher:McGraw-Hill Education
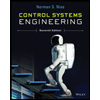
Control Systems Engineering
Mechanical Engineering
ISBN:9781118170519
Author:Norman S. Nise
Publisher:WILEY
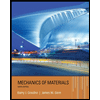
Mechanics of Materials (MindTap Course List)
Mechanical Engineering
ISBN:9781337093347
Author:Barry J. Goodno, James M. Gere
Publisher:Cengage Learning
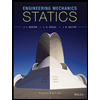
Engineering Mechanics: Statics
Mechanical Engineering
ISBN:9781118807330
Author:James L. Meriam, L. G. Kraige, J. N. Bolton
Publisher:WILEY