Herrera_ME455_Lab2
pdf
keyboard_arrow_up
School
Metropolitan Community College, Kansas City *
*We aren’t endorsed by this school
Course
455
Subject
Mechanical Engineering
Date
Feb 20, 2024
Type
Pages
7
Uploaded by CountSparrow1077
FALL2021. ME 455. Mechanical Engineering Measurements and Experiments Experiment #2. Load Cell Calibration Name: _Brandan Herrera_ Group Members: __Tanner Smith___ Lab Section: _Wednesday 10am-12:50pm_ Table #__3__ Section 1. Experiment summary (15 Points) (
250 words)
(Provide a summary of your experiment, including the following: the focus of the experiment, the instruments/sensors/setup explored, measurement(s) taken, data analysis done, one primary result, and one primary overall conclusion. Must be
250 words!) In this experiment, understanding how to calibrate a load cell (an "S" beam load cell) using the sequential calibration method was key to be able to use these instruments later in life. The calibration process involved assessing and calculating various errors based on collected data through the digital multimeter as well as the program LabView. By familiarizing ourselves with the LabView software, it is possible to understand the Wheatstone circuit with strain gauges. Understanding the calibration process is a crucial procedure in instrumentation measuring to ensure accuracy. The process involves comparing measurement values from a test with a known accurate standard, with another calibrated device. Being able to identify an error without adjustment was the end goal of this experiment. It is possible to convert force into an electrical output by utilizing strain gauges arranged in a Wheatstone bridge. By using modern measurement systems that are often used in computer-based data acquisition systems, it is possible to use the LabVIEW software to record these values. Being able to understand LabVIEW, which is widely used for digital measurements, analysis, and control of test systems, it is possible to find ways to make items better as a mechanical engineer and show physical proof.
Section 2. Recorded data (5 Data Table: 8 Points each) Table 1: Data from OMEGADYNE Specification Shee
t Specifications for the load cell Static Sensitivity 1.201 mv/lbs Linearity
0.03% FSO Hysteresis
0.02% FSO Zero Balance
1% FSO Repeatability
0.01% FSO FSO 30.0144 mv Table 2: DMM vs. LabView Voltages before/after amplifier Equipment Before Amplifier After Amplifier Calculated Gain % Error (DMM as Base) DMM 0.079 10.16 128.61 N/A LabView N/A 10.15 128.48 0.1 Table 3: “Calibration” of Weights (Include Weighing Error Estimate)
Measurement # Designation on Weight or hanger/bucket (e.g., ME455-001) Weight from Digital Scale (lbs) 1 2.5 2.495 2 5 5.33 3 7.5 7.825 4 10 10.395 5 12.5 13.07 6 15 15.64 7 17.5 18.17 8 20 20.76 Table 4: Sequential Calibration Data from Load Cell Test #1 LOAD CELL DATA Sequence Data Pt. Load (lbs) Voltage (V) UP 1 0.000 (no hanger/bucket) -5.002 2 ~0.000 (hanger/bucket) -4.825
3 ~2.5 [2.495] -3.920 4 ~5.0 [5.33] -2.898 5 ~7.5 [7.825] -1.979 6 ~10.0 [10.395] -0.968 7 ~12.5 [13.07] -0.053 8 ~15.0 [15.64] 0.874 9 ~17.5 [18.17] 1.819 10 ~20.0 [20.76] 2.754 D0WN 11 ~17.5 [18.17] 1.825 12 ~15.0 [15.64] 0.8798 13 ~12.5 [13.07] -0.052 14 ~10.0 [10.395] -0.969 15 ~7.5 [7.825] -1.979 16 ~5.0 [5.33] -2.886 17 ~2.5 [2.495] -3.920 18 ~0.000 (hanger/bucket) -4.83 19 0.000 (no hanger/bucket) -4.396 Table 5: Sequential Calibration Data from Load Cell Test #2 LOAD CELL DATA Sequence Data Pt. Load (lbs) Voltage (V) UP 1 0.000 (no hanger/bucket) -5 2 ~0.000 (hanger/bucket) -4.8 3 ~2.5 [2.495] -4 4 ~5.0 [5.33] -2.9 5 ~7.5 [7.825] -2
Your preview ends here
Eager to read complete document? Join bartleby learn and gain access to the full version
- Access to all documents
- Unlimited textbook solutions
- 24/7 expert homework help
6 ~10.0 [10.395] -1 7 ~12.5 [13.07] -0.1 8 ~15.0 [15.64] 0.9 9 ~17.5 [18.17] 1.8 10 ~20.0 [20.76] 2.8 D0WN 11 ~17.5 [18.17] 1.8 12 ~15.0 [15.64] 0.9 13 ~12.5 [13.07] -0.1 14 ~10.0 [10.395] -1 15 ~7.5 [7.825] -2 16 ~5.0 [5.33] -2.9 17 ~2.5 [2.495] -3.9 18 ~0.000 (hanger/bucket) -4.8 19 0.000 (no hanger/bucket) -5 Table 6: Sequential Calibration Data from Load Cell Test #3 LOAD CELL DATA Sequence Data Pt. Load (lbs) Voltage (V) UP 1 0.000 (no hanger/bucket) -5.001 2 ~0.000 (hanger/bucket) -4.873 3 ~2.5 [2.495] -3.964 4 ~5.0 [5.33] -2.800 5 ~7.5 [7.825] -1.930 6 ~10.0 [10.395] -0.950 7 ~12.5 [13.07] -0.049 8 ~15.0 [15.64] 0.869
9 ~17.5 [18.17] 1.825 10 ~20.0 [20.76] 2.754 D0WN 11 ~17.5 [18.17] 1.832 12 ~15.0 [15.64] 0.872 13 ~12.5 [13.07] -0.049 14 ~10.0 [10.395] -0.973 15 ~7.5 [7.825] -1.984 16 ~5.0 [5.33] -2.892 17 ~2.5 [2.495] -3.930 18 ~0.000 (hanger/bucket) -4.825 19 0.000 (no hanger/bucket) -4.402 Section 4. Questions (5 Points Each) Suggest to use a MATLAB code to calculate the parameters requested and for submitting the code and answering the following questions.
Answer the following questions, and submit graphs and tables, as well as your MATLAB code as appendices if there is. Note: Remember the load cell signal has been amplified by a gain of ~333 or ~500
. 1)
Calculate the static sensitivity of the load cell based on your data. Compare this to the value provided by the manufacturer. If different, how much and why? The value provided by the manufacturer is that the amplifier is a 1.20 mV/load amplifier. Based on my calculations using the equation 𝑆𝑡𝑎𝑡𝑖𝑐 𝑆𝑒𝑛𝑠𝑖𝑡𝑖𝑣𝑖𝑡𝑦 =
∆ை௨௧௨௧ ௌ
∆ௗ ௗ
, I got a mV rating of 3.73 mV/lb which is off by at least 2.53 mV. This is the case because it is the most ideal situation that they get the 1.2 mV/load as well as it is in a controlled environment but in a regular lab it may not be the only thing effecting it. It also might differ if there is a smaller load difference between the two weights and they can get the weights closer than not. Another issue is that the load cell could have been through higher stresses over the course of when it was first bought so calibration might be a bit off or sensor is worn out.
2)
Calculate the maximum linearity error of the load cell based on your data. Is this within the specified tolerance given by the manufacturer? If not, suggest why? By taking the differences between the points at each weight we can figure out the maximum linearity error of the load cell could be to which the maximum that was calculated was after the weight was removed and it was just left with a difference of around 0.601 V. This is a little out of the specifications but the issue that could have happened was wear and tare of the load cell which over time it can give a different variation depending on how long it has been serviced and recalibrated. 3)
What is the zero balance error for this load cell? Is this within the specified tolerance given by the manufacturer? If not, postulate why? To calculate the zero balance error we will use the equation of Zero Balance error = |𝑀𝑒𝑎𝑠𝑢𝑟𝑒𝑑 𝑂𝑢𝑡𝑝𝑢𝑡
ௗ
− 𝑆𝑝𝑒𝑐𝑖𝑓𝑖𝑒𝑑 𝑂𝑢𝑡𝑝𝑢𝑡
ௗ
|
which gives us the value of 0.285. This is close to the tolerance specified by the manufacturer but still because of the time that the load cell could have been maintained, it probably was not which for the future it would give future teams issues and values that are not close to what the manufacturer specified if it was bought brand new.
4)
What is the hysteresis error for this load cell? Is this within the specified tolerance given by the manufacturer? If not, postulate why? By using the equation to find hysteresis (Hysteresis Error = |𝑀𝑎𝑥 𝑂𝑢𝑡𝑝𝑢𝑡 − 𝑀𝑖𝑛 𝑂𝑢𝑡𝑝𝑢𝑡|
) we can find that the error for this certain load cell is 7.755 V. This is within the specified tolerance because the error on the load cell is ±0.02% FSO so it fits in the specifications that the load cell has. Section 5. Conclusions (2.5 Points Each) (~100 words)
Did the group complete the goal of the lab? Stating yes or no is insufficient for labs with more data driven goals. In this exercise’s case the goal is get “hands on” experience with the data analysis of wave functions and gain an understanding of the types of errors that can occur when sampling incorrectly. The group completed the goal because the group was able to apply a load and be able to use the LabView program in order to transfer a mass to a voltage using an S block. By being able to see how using an amplifier along with an S block to measure the voltage allows the group to be able to get numerical values and if need to plot the data. This also allowed us to be able to find some errors in the end solution because when weighing the weights, there was some sleight variations of the weights such
Your preview ends here
Eager to read complete document? Join bartleby learn and gain access to the full version
- Access to all documents
- Unlimited textbook solutions
- 24/7 expert homework help
as when weighing the, what was suppose to be, 5 pound weight. The actual weight of the weight was around 5.33 pounds which in a general purpose use it is not that much of a difference but in the experiment it plays a huge role in variations of the final results which means that there was either some error in our final results or there was an error in the manufacturer’s results since they were not used with the same amount of weight or there was some variations on both the weights.
What would you change about this lab? What data (if any) could you not obtain? Be specific as to the reason you would change the lab. If you feel that you didn’t meet the criteria for success on this lab how might you change that? If there was something I would have liked to see is use LabView to be able to see different values other than voltages. I would guess that we will be using LabView to find voltage differences in the future but being able to get a grasp on how to use LabView would be better for this experiment. I also would have a shortcut on the computers for lab view or a step by step on how to open lab view because not everyone has used it before so knowing where it was is half the time of class.
Related Documents
Related Questions
University of Babylon
Collage of Engineering\Al-Musayab
Department of Automobile
Engineering
Under Grad/Third stage
Notes:
1-Attempt Four Questions.
2- Q4 Must be Answered
3-Assume any missing data.
4 تسلم الأسئلة بعد الامتحان مع الدفتر
Subject: Mechanical
Element Design I
Date: 2022\01\25
2022-2023
Time: Three Hours
Course 1
Attempt 1
Q1/ Design a thin cylindrical pressure tank (pressure vessel) with hemispherical ends to the
automotive industry, shown in figure I below. Design for an infinite life by finding the
appropriate thickness of the vessel to carry a sinusoidal pressure varied from {(-0.1) to (6) Mpa}.
The vessel is made from Stainless Steel Alloy-Type 316 sheet annealed. The operating
temperature is 80 C° and the dimeter of the cylinder is 36 cm. use a safety factor of 1.8.
Fig. 1
(15 Marks)
Q2/ Answer the following:
1- Derive the design equation for the direct evaluation of the diameter of a shaft to a desired
fatigue safety factor, if the shaft subjected to both fluctuated…
arrow_forward
You are a biomedical engineer working for a small orthopaedic firm that fabricates rectangular shaped fracture
fixation plates from titanium alloy (model = "Ti Fix-It") materials. A recent clinical report documents some problems with the plates
implanted into fractured limbs. Specifically, some plates have become permanently bent while patients are in rehab and doing partial
weight bearing activities.
Your boss asks you to review the technical report that was generated by the previous test engineer (whose job you now have!) and used to
verify the design. The brief report states the following... "Ti Fix-It plates were manufactured from Ti-6Al-4V (grade 5) and machined into
solid 150 mm long beams with a 4 mm thick and 15 mm wide cross section. Each Ti Fix-It plate was loaded in equilibrium in a 4-point bending
test (set-up configuration is provided in drawing below), with an applied load of 1000N. The maximum stress in this set-up was less than the
yield stress for the Ti-6Al-4V…
arrow_forward
Instrumentation & Measurements
This homework measures your capability to design/analyze various components/variables of ameasurement system based on what you have studied.
Question is Attached in image. Thank you.
arrow_forward
Access Pearson
Mastering Engineering
Back to my courses
Course Home
Course Home
Scores
■Review
Next >
arrow_forward
I need answers to questions 10, 11, and 12 pertaining to the print provided.
Note: A tutor keeps putting 1 question into 3 parts and wasted so many of my questions. Never had a issue before until now, please allow a different tutor to answer because I was told I am allowed 3 of these questions.
arrow_forward
I need help solving this problem.
arrow_forward
Subject: Air Pollution Formation and Control
Do not just copy and paster other online answers
arrow_forward
I need answers to questions 1, 2, and 3 pertaining to the print provided.
Note: A tutor keeps putting 1 question into 3 parts and wasted so many of my questions. Never had a issue before until now, please allow a different tutor to answer because I was told I am allowed 3 of these questions.
arrow_forward
Please show work in a handwritten format.
Don't use chatgpt.
Mechanics of materials/design.
arrow_forward
I need help with this before tomorrow’s exam if I can get all needed calculations please
arrow_forward
[Engineering Thermodynamics]
Please finish the answer with a diagram for reference to me (if needed).
Show the answer step by step and clear to see.
If you need to answer with words, please type directly. (to avoid cant see clear by handwriting)
Thank you.
P.S. Use the online software http://www.peacesoftware.de/einigewerte/r134a_e.html
or property table and p-h diagram for R134a where necessary.
arrow_forward
Subject: mechanical engi
arrow_forward
pls help me with this one :(
arrow_forward
Newton's Law of cooling states that the rate at which heat is lost by a heated body is
proportional to the difference in temperature between the body and the surrounding
medium. Match the following statements/phrases with the corresponding item in the
drop down box. Choices in the box
1. In accordance with the stated law obove, we have the equation?
2. If a thermometer is taken outdoors where the temperoture is 5 deg C, from a
room in which the temperature is 20 deg C and the reading drops 10 deg C in one
minute, the working equation is?
3. In the obove problem, separoting the variables and integrating will result to?
4. In the obove problem, how long, in minutes, after its removal from the room will
the reading be 6 deg C?
5. In the obove problem, ofter 30 seconds, whot will be the thermometer reading?
5.2
dT(body temp)/dt = k(Temp of medium - 5)
dr(body temp)/dt = k(Temp of body - Temp of medium)
Temp of body = Cenkt +5
2.5
13.7
dr(body temp)/dt = k(Temp of medium - Temp of body)…
arrow_forward
Part 1: Suppose that our company performs DNA analysis for a law enforcement agency. We currently have 1 machine that are essential to performing the analysis. When an analysis is performed, the machine is in use for half of the day. Thus, each machine of this type can perform at most two DNA analyses per day. Based on past experience, the distribution of analyses needing to be performed on any given day are as follows: (Fill in the table)
Part2: We are considering purchasing a second machine. For each analysis that the machine is in use, we profit 1400$. What is the YEARLY expected value of this new machine ( ASSUME 365 days per year - no weekends or holidays
arrow_forward
Case Study – The New Engineer
Jeff was just hired by GSI, Inc. to be their Environmental and Safety Coordinator. This is Jeff's first position after completing his engineering degree. He had taken a course in safety engineering as part of his studies and felt confident that he could handle the job.
Management at GSI, Inc. has assured him that they are committed to maintaining a safe workplace. They have never had an individual dedicated to this task full-time. They will implement his recommendations if he can justify them.
As Jeff begins to get familiar with the operations, he spends considerable time on the production floor. He notices workers clean their tools before break with a liquid from an unmarked 55-gallon drum. They also use this liquid to clean residue from their skin. They use paper towels to dry their tools and hands, throw these towels in the trash, and head to the break room for a snack and/or smoke.
In talking with the workers, Jeff learns of some of…
arrow_forward
Case Study – The New Engineer
Jeff was just hired by GSI, Inc. to be their Environmental and Safety Coordinator. This is Jeff's first position after completing his engineering degree. He had taken a course in safety engineering as part of his studies and felt confident that he could handle the job.
Management at GSI, Inc. has assured him that they are committed to maintaining a safe workplace. They have never had an individual dedicated to this task full-time. They will implement his recommendations if he can justify them.
As Jeff begins to get familiar with the operations, he spends considerable time on the production floor. He notices workers clean their tools before break with a liquid from an unmarked 55-gallon drum. They also use this liquid to clean residue from their skin. They use paper towels to dry their tools and hands, throw these towels in the trash, and head to the break room for a snack and/or smoke.
In talking with the workers, Jeff learns of some of…
arrow_forward
Please give a complete solution in Handwritten format.
Strictly don't use chatgpt,I need correct answer.
Engineering dynamics
arrow_forward
Hello, so i have attached two images. the first image is the quetions, i need part b) answered if possible. i have attached my findings to part a) to add to the little information we know to help with part b if needed. Thnks
arrow_forward
I want to briefly summarize what he is talking about and what you conclude.
pls very urgent
arrow_forward
I need the answer as soon as possible
arrow_forward
Could you please explain where and what is tight side and also how to find 5-9
arrow_forward
SEE MORE QUESTIONS
Recommended textbooks for you
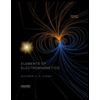
Elements Of Electromagnetics
Mechanical Engineering
ISBN:9780190698614
Author:Sadiku, Matthew N. O.
Publisher:Oxford University Press
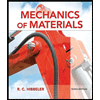
Mechanics of Materials (10th Edition)
Mechanical Engineering
ISBN:9780134319650
Author:Russell C. Hibbeler
Publisher:PEARSON
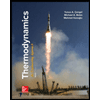
Thermodynamics: An Engineering Approach
Mechanical Engineering
ISBN:9781259822674
Author:Yunus A. Cengel Dr., Michael A. Boles
Publisher:McGraw-Hill Education
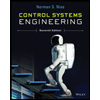
Control Systems Engineering
Mechanical Engineering
ISBN:9781118170519
Author:Norman S. Nise
Publisher:WILEY
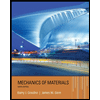
Mechanics of Materials (MindTap Course List)
Mechanical Engineering
ISBN:9781337093347
Author:Barry J. Goodno, James M. Gere
Publisher:Cengage Learning
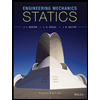
Engineering Mechanics: Statics
Mechanical Engineering
ISBN:9781118807330
Author:James L. Meriam, L. G. Kraige, J. N. Bolton
Publisher:WILEY
Related Questions
- University of Babylon Collage of Engineering\Al-Musayab Department of Automobile Engineering Under Grad/Third stage Notes: 1-Attempt Four Questions. 2- Q4 Must be Answered 3-Assume any missing data. 4 تسلم الأسئلة بعد الامتحان مع الدفتر Subject: Mechanical Element Design I Date: 2022\01\25 2022-2023 Time: Three Hours Course 1 Attempt 1 Q1/ Design a thin cylindrical pressure tank (pressure vessel) with hemispherical ends to the automotive industry, shown in figure I below. Design for an infinite life by finding the appropriate thickness of the vessel to carry a sinusoidal pressure varied from {(-0.1) to (6) Mpa}. The vessel is made from Stainless Steel Alloy-Type 316 sheet annealed. The operating temperature is 80 C° and the dimeter of the cylinder is 36 cm. use a safety factor of 1.8. Fig. 1 (15 Marks) Q2/ Answer the following: 1- Derive the design equation for the direct evaluation of the diameter of a shaft to a desired fatigue safety factor, if the shaft subjected to both fluctuated…arrow_forwardYou are a biomedical engineer working for a small orthopaedic firm that fabricates rectangular shaped fracture fixation plates from titanium alloy (model = "Ti Fix-It") materials. A recent clinical report documents some problems with the plates implanted into fractured limbs. Specifically, some plates have become permanently bent while patients are in rehab and doing partial weight bearing activities. Your boss asks you to review the technical report that was generated by the previous test engineer (whose job you now have!) and used to verify the design. The brief report states the following... "Ti Fix-It plates were manufactured from Ti-6Al-4V (grade 5) and machined into solid 150 mm long beams with a 4 mm thick and 15 mm wide cross section. Each Ti Fix-It plate was loaded in equilibrium in a 4-point bending test (set-up configuration is provided in drawing below), with an applied load of 1000N. The maximum stress in this set-up was less than the yield stress for the Ti-6Al-4V…arrow_forwardInstrumentation & Measurements This homework measures your capability to design/analyze various components/variables of ameasurement system based on what you have studied. Question is Attached in image. Thank you.arrow_forward
- Access Pearson Mastering Engineering Back to my courses Course Home Course Home Scores ■Review Next >arrow_forwardI need answers to questions 10, 11, and 12 pertaining to the print provided. Note: A tutor keeps putting 1 question into 3 parts and wasted so many of my questions. Never had a issue before until now, please allow a different tutor to answer because I was told I am allowed 3 of these questions.arrow_forwardI need help solving this problem.arrow_forward
- Subject: Air Pollution Formation and Control Do not just copy and paster other online answersarrow_forwardI need answers to questions 1, 2, and 3 pertaining to the print provided. Note: A tutor keeps putting 1 question into 3 parts and wasted so many of my questions. Never had a issue before until now, please allow a different tutor to answer because I was told I am allowed 3 of these questions.arrow_forwardPlease show work in a handwritten format. Don't use chatgpt. Mechanics of materials/design.arrow_forward
- I need help with this before tomorrow’s exam if I can get all needed calculations pleasearrow_forward[Engineering Thermodynamics] Please finish the answer with a diagram for reference to me (if needed). Show the answer step by step and clear to see. If you need to answer with words, please type directly. (to avoid cant see clear by handwriting) Thank you. P.S. Use the online software http://www.peacesoftware.de/einigewerte/r134a_e.html or property table and p-h diagram for R134a where necessary.arrow_forwardSubject: mechanical engiarrow_forward
arrow_back_ios
SEE MORE QUESTIONS
arrow_forward_ios
Recommended textbooks for you
- Elements Of ElectromagneticsMechanical EngineeringISBN:9780190698614Author:Sadiku, Matthew N. O.Publisher:Oxford University PressMechanics of Materials (10th Edition)Mechanical EngineeringISBN:9780134319650Author:Russell C. HibbelerPublisher:PEARSONThermodynamics: An Engineering ApproachMechanical EngineeringISBN:9781259822674Author:Yunus A. Cengel Dr., Michael A. BolesPublisher:McGraw-Hill Education
- Control Systems EngineeringMechanical EngineeringISBN:9781118170519Author:Norman S. NisePublisher:WILEYMechanics of Materials (MindTap Course List)Mechanical EngineeringISBN:9781337093347Author:Barry J. Goodno, James M. GerePublisher:Cengage LearningEngineering Mechanics: StaticsMechanical EngineeringISBN:9781118807330Author:James L. Meriam, L. G. Kraige, J. N. BoltonPublisher:WILEY
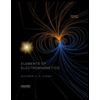
Elements Of Electromagnetics
Mechanical Engineering
ISBN:9780190698614
Author:Sadiku, Matthew N. O.
Publisher:Oxford University Press
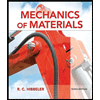
Mechanics of Materials (10th Edition)
Mechanical Engineering
ISBN:9780134319650
Author:Russell C. Hibbeler
Publisher:PEARSON
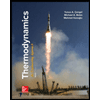
Thermodynamics: An Engineering Approach
Mechanical Engineering
ISBN:9781259822674
Author:Yunus A. Cengel Dr., Michael A. Boles
Publisher:McGraw-Hill Education
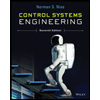
Control Systems Engineering
Mechanical Engineering
ISBN:9781118170519
Author:Norman S. Nise
Publisher:WILEY
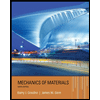
Mechanics of Materials (MindTap Course List)
Mechanical Engineering
ISBN:9781337093347
Author:Barry J. Goodno, James M. Gere
Publisher:Cengage Learning
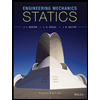
Engineering Mechanics: Statics
Mechanical Engineering
ISBN:9781118807330
Author:James L. Meriam, L. G. Kraige, J. N. Bolton
Publisher:WILEY