CARE FOR REUSABLE MEDICAL DEVICES
docx
keyboard_arrow_up
School
TAFE NSW - Sydney Institute *
*We aren’t endorsed by this school
Course
HLTSTE005
Subject
Mechanical Engineering
Date
Feb 20, 2024
Type
docx
Pages
4
Uploaded by AmbassadorCrab3523
HLTSTE005- Assignment 1
What you have to do
This unit is concerned with the essential knowledge required to follow correct procedures for preparing, handling and inspecting reusable medical devices. This includes the knowledge to identify instruments that require insulation testing and understand those items requiring disassembling and re-assembly.
Answer all knowledge questions below. Type your answers in the fields provided. Save your answers in this document then submit via the OLS.
You may need to refer back to your learning resource.
1.
What lubricate is suitable for lubricating instruments and is safe for sterilization?
All water soluble lubricants are suitable for lubricating instruments and sterilisation as
they allow steam penetration.
2.
What is classified as loan equipment?
Any. single or complete set of items not owned by the hospital and have beeen loaned for usage with the purpose of returning to the supplier
3.
You are inspecting instruments for packing when you come across a faulty instrument, what is the correct requirement for instrument repair?
The instrument should be removed immediately and workplace procedures and policies followed for reporting and documenting and the equipment should be sent to be repaired.
Your workplace should have a detailed instrument repair program in place and the instrument repair company contacted, this would allow for the instruments to be repaired properly and returned.
4.
Why is leak testing required for an endoscope?
Leak testing for endoscopes are very important to protect paitents from infection. If fluid leaks into the scope it can cause damage to the fibreoptic, image bundles and video chips. This could cause stiffness and loss of angulation capabilities. This would
then lead to expensive repairs.
5.
What procedures can we follow to ensure microsurgical instruments are not damaged during the reprocessing?
Most importantly follow manufacturers reccommendations and take extreme care. You must use special perforated tray with clip inserts for mechanical cleaning. Instruments should always be seperated and not stacked, when sterilising or stored they are to be in perforated trays with lids.
LA021003 Assignment 1, HLTSTE005, Ed 1
1
© New South Wales Technical and Further Education Commission, 2016 TAFE NSW – WSI, Archive version 1, March 2016
6.
You received a loan set that requires priority processing there will not be enough time
for the set to go through every step of the process, theatres are asking you to have it ready for the next case Do you take shortcuts after all the set looks clean? List the correct steps you will follow.
Short cuts are never acceptable. On arrival loan sets should be thoroughly checked for damage, cleaned and processed before sterilisation by the wrapped method.
Any instrument that isnt clean should be reported to the supplier. Check delivery documents and follow suppliers information and instructions for each piece of equipment.
After usage all loan equipment should be cleaned and sterilised before returning it to the supplier
7.
How are telescopes checked after they have been cleaned?
You will need to look through the eye piece towards the light to check that the telescope lens is clear, if it appears foggy or is damaged it would need to be sterilised and sent out for repairs.
8.
Why is it important to follow manufacturer’s instructions for soaking any instruments in enzyme solution?
It is important to follow manufacturers instructions to avoid injury to staff or paitents. With its ability to break down proteins this raises concerns about inhalation of enzymes which can result in asthma or allergic effects.
9.
What do you need to do with a dental hand piece at the end of each procedure? At the end of each procedure the hand piece needs to be changed, to discharge water and air for atleast 30 seconds or follow manufacturers instructions. This will ensure any gross debris will be distrubed.
10. What is the correct procedure for cleaning a light lead? Fibre optic light leads should be handled with care to protect the fine glass rods. They should be manually cleaned with a soft lint free cloth with the appropiate cleaning chemicals. A neutral or mild alkali detergent diluted in water, then gently rinse manufacturers instructions should always be referred to.
11. Write down the correct procedure for cleaning a power drill.
Power drills should be inspected before cleaning or sterilisation. A cabinet or exhaust
hood should be used to reduce exposure from aerosols. They should never be immersed in water or put in an ultrasonic cleaner. All power hoses should be attached when cleaning, this prevents cleaning fluids from entering the hose or hand piece. A drying cabinet or another separate non-lint cloth needs to be used to dry them.
12. What is the correct procedure for cleaning general instruments?
Manual or mechanically clean instruments in a designated area wearing appropiate PPE. Cleaning minimises staining, corrosion and pitting.
2
LA021003 Assignment 1, HLTSTE005, Ed 1 © New South Wales Technical and Further Education Commission, 2016 TAFE NSW – WSI, Archive version 1, March 2016
After cleaning thoroughly rinse instruments with water ensuring debris and detergent residue is removed. Inspect each instrument before drying for left over debris or damage. Then continue reprocessing. 13. Define single use instrument.
A single use instrument is only to be used once and then discarded. The same single
use item can be used multiple times on the same paitent following manufacturers instructions for cleaning between uses.
14. Why is it important that multipart instruments are pulled apart for cleaning and sterilisation? Always follow manufacturers guidelines when dismantling multipart instruments. This allows easier removal of visable or non-visable soils when cleaning. Also during sterilisation it makes for total access to destroy all micro-organisms for total sterility.
15. Why is it important to have ratcheted instruments left open for cleaning? The importance of ratcheted instruments left in the open position is to ensure the jaws and box joints are thoroughly cleaned and all debris removed.
16. Scenario question A nurse has come in the department with an instrument you have
not seen before and ask you to clean and sterilise it for the next case. What is the correct procedure to follow before you process this equipment?
You would need to call the manufacturer to get the correct advise on how to clean and sterilise this particular piece of equipment. That way you would then know the correct cleaning fluids needed, if a rinse is needed, what tempertaure it can withstand
and the sterilising method.
17. What is the correct technique for cleaning cannulated instruments?
Cannulated instruments need you to use a soft bristle brush and the suitable size brush which is inserted and pulled through to the other side to remove all debris, if you pull the brush back and forth you could dislodge in the middle thus leaving them dirty.
18. Describe how you would handle an endoscope after patient use.
As proteinaecious matter is extremely hard to remove once dried, it is very important that once the endoscope and accessories are removed from the paitent, the process of cleaning needs to start immediately.
19. Instruments on loan should not be interchanged between human, necropsy and animal use.
All instruments used on animals should never be reprossed in sterilisers or other equpiment used for reprocessing instruments that are used for humans. if tehse requirements are not met infection transmission hazards exist.
20. How often should insulation testing be performed on insulated instruments? LA021003 Assignment 1, HLTSTE005, Ed 1
3
© New South Wales Technical and Further Education Commission, 2016 TAFE NSW – WSI, Archive version 1, March 2016
Your preview ends here
Eager to read complete document? Join bartleby learn and gain access to the full version
- Access to all documents
- Unlimited textbook solutions
- 24/7 expert homework help
caution should be followed and always follow manufacturers instuctions when testing insulated instruments.
Testing should be attended to everytime the instrument or equipment has been used.
Documentation should be kept for all failures and repairs.
Checklist
I have:
answered all questions in the space provided
saved my answers in this document.
If you are unable to complete this task for a specific reason, please contact your teacher to discuss alternative arrangements for demonstrating your skills and knowledge.
4
LA021003 Assignment 1, HLTSTE005, Ed 1 © New South Wales Technical and Further Education Commission, 2016 TAFE NSW – WSI, Archive version 1, March 2016
Related Documents
Related Questions
Question 2
You are a biomedical engineer working for a small orthopaedic firm that fabricates rectangular shaped fracture
fixation plates from titanium alloy (model = "Ti Fix-It") materials. A recent clinical report documents some problems with the plates
implanted into fractured limbs. Specifically, some plates have become permanently bent while patients are in rehab and doing partial
weight bearing activities.
Your boss asks you to review the technical report that was generated by the previous test engineer (whose job you now have!) and used to
verify the design. The brief report states the following... "Ti Fix-It plates were manufactured from Ti-6Al-4V (grade 5) and machined into
solid 150 mm long beams with a 4 mm thick and 15 mm wide cross section. Each Ti Fix-It plate was loaded in equilibrium in a 4-point bending
test (set-up configuration is provided in drawing below), with an applied load of 1000N. The maximum stress in this set-up was less than the
yield stress for the…
arrow_forward
I need answers for problems 13, 14, and 15 pertaining to the print provided.
NOTE: If you refuse to answers all 3 parts and insist on wasting my question by breaking down 1 simple question into 3 parts, then just leave it for someone else to answer. Thank you.
arrow_forward
Case Study – The New Engineer
Jeff was just hired by GSI, Inc. to be their Environmental and Safety Coordinator. This is Jeff's first position after completing his engineering degree. He had taken a course in safety engineering as part of his studies and felt confident that he could handle the job.
Management at GSI, Inc. has assured him that they are committed to maintaining a safe workplace. They have never had an individual dedicated to this task full-time. They will implement his recommendations if he can justify them.
As Jeff begins to get familiar with the operations, he spends considerable time on the production floor. He notices workers clean their tools before break with a liquid from an unmarked 55-gallon drum. They also use this liquid to clean residue from their skin. They use paper towels to dry their tools and hands, throw these towels in the trash, and head to the break room for a snack and/or smoke.
In talking with the workers, Jeff learns of some of…
arrow_forward
Case Study – The New Engineer
Jeff was just hired by GSI, Inc. to be their Environmental and Safety Coordinator. This is Jeff's first position after completing his engineering degree. He had taken a course in safety engineering as part of his studies and felt confident that he could handle the job.
Management at GSI, Inc. has assured him that they are committed to maintaining a safe workplace. They have never had an individual dedicated to this task full-time. They will implement his recommendations if he can justify them.
As Jeff begins to get familiar with the operations, he spends considerable time on the production floor. He notices workers clean their tools before break with a liquid from an unmarked 55-gallon drum. They also use this liquid to clean residue from their skin. They use paper towels to dry their tools and hands, throw these towels in the trash, and head to the break room for a snack and/or smoke.
In talking with the workers, Jeff learns of some of…
arrow_forward
please help solve A-F. thank you
You are an engineer working on a project and your prototype has failed prematurely. You question whether or not a key component of the prototype was manufactured with the correct material. There are two way to check for the material properties. The first way is to have a material certification done to confirm the exact material composition. This will take some time. The second method to confirm the material properties is to make an ASTM test sample and test for the material properties. This tensile test was completed on a test sample with an initial diameter of .501” and an initial length of 2”. The Load-Deflection data for this tensile test is below. Use this data to answer the first set of questions on the Final Exam in eLearning. A. Determine the Ultimate Tensile Strength B. Determine the 0.2% Offset Yield Strength C. Determine the value of the Proportional Limit D. Determine the Modulus of Elasticity E. Determine the Strain at Yield F. Calculate %…
arrow_forward
Case Study: Paula’s Pain
Paula has worked for Brindle Corporation for 3 years. During this time, she has worked as a machine operator/cell leader in various work cells. Recently, the plant went to mandatory 12-hour shifts and plans to remain on this schedule for several months.
Paula’s present work cell is manufacturing 3-inch diameter exhaust tubes that are made from stainless steel. These tubes get a hole punched in them, a flange welded on, and burrs ground off. The pipe then gets placed into a gage to check that it was made correctly. (The tubes weigh about six pounds.)
Paula has been performing the welding operation. She leans into the machine and loads the part into a fixture then positions the flange. Both pieces are clamped (using hand clamps) into position and the machine is cycled by depressing two palm buttons.
The gaging operation requires placing the finished part into the gage and clamping it (using hand clamps) into place. A pin is depressed to verify the position…
arrow_forward
I need problems 6 and 7 solved.
I got it solved on 2 different occasions and it is not worded correctly.
NOTE: Problem 1 is an example of how it should be answered. Below are 2 seperate links to same question asked and once again it was not answered correctly. 1. https://www.bartleby.com/questions-and-answers/it-vivch-print-reading-for-industry-228-class-date-name-review-activity-112-for-each-local-note-or-c/cadc3f7b-2c2f-4471-842b-5a84bf505857
2. https://www.bartleby.com/questions-and-answers/it-vivch-print-reading-for-industry-228-class-date-name-review-activity-112-for-each-local-note-or-c/bd5390f0-3eb6-41ff-81e2-8675809dfab1
arrow_forward
A Team of Engineers asked for an internal combustion engine to use it in a designed car. Your role is to describe the operation sequence of different types of available engines, explain their mechanical efficiency, and deliver a detailed technical report to show your approach in solving and discussing the following tasks and issues.
You must follow the following steps to help the team:
STEP 1
Describe the operational sequence of four-stroke spark ignition and four-stroke compression ignition engines with the aid of sketches by constructing simple sketch representing the operation and plotting the P-V diagrams for each process during the cycle to show the following:
The input and output heat and net output work
The expansion and compression strokes
The air-fuel mixture intake and exhaust gasses
The spark plug when it is in the active mode
The complete cycle of ideal Otto and Diesel cycles that shows the input and output heat and net output work.
STEP 2
Explain the mechanical…
arrow_forward
LESSON: AUTODESK AUTOCAD
Choose from the choices:
arrow_forward
Stuck need help!
Problem is attached. please view attachment before answering.
Really struggling with this concept.
Please show all work so I can better understand !
Thank you so much.
arrow_forward
Question 3
You are working on a design team at a small orthopaedic firm. Your team is starting to work on a lower limb
(foot-ankle) prosthesis for individuals who have undergone foot amputation (bone resection at the distal tibia). You remember hearing
about "osseointegration" in an exciting orthopaedic engineering class you attended at Clemson, so you plan to attach the foot
prosthesis using a solid metal rod inserted into the distal tibia. You think stainless steel or titanium alloy might be a useful rod material.
You decide to begin this problem by identifying typical tibial bone anatomy and mechanical behavior (as provided in the tables and
image below). You assume the tibial bone can be modeled as a hollow cylinder of cortical bone, as represented in the image. You
anticipate the length of the rod will be 1/2 the length of the tibia.
Q3G: Critical Thinking: What would you propose to your team as the next step in this analysis? Is it reasonable to assume the rod
will experience the…
arrow_forward
Help!!! Please answer part B correctly!!! Please
arrow_forward
Please answer the 4th question
arrow_forward
What letter choice is for number one
arrow_forward
Please show work in a handwritten format.
Don't use chatgpt.
Mechanics of materials/design.
arrow_forward
As an engineer responsible for monitoring works in the area of mechanical systems, you must evaluate the following situation: a large client in the retail area has a refrigeration system where it stores some chilled or frozen products to be sold on the sales floor.Recently, the customer's maintenance department has been questioning the system's performance and requested an evaluation of the system's behavior. You went to the location and requested some information from the maintenance manager about the system, who provided the following data: - The system operates with R-134a refrigerant;- The refrigerated environment is maintained at 0°C and the external environment at 26°C;- The refrigerant flow rate in the system is 0.08 kg/s; In addition to the data provided, you carried out some tests and measured the temperature of the refrigerant fluid at some specific points in the system, such as the compressor inlet and condenser outlet, finding values of 0°C and 26°C respectively.…
arrow_forward
As an engineer responsible for monitoring works in the area of mechanical systems, you must evaluate the following situation: a large client in the retail area has a refrigeration system where it stores some chilled or frozen products to be sold on the sales floor.Recently, the customer's maintenance department has been questioning the system's performance and requested an evaluation of the system's behavior. You went to the location and requested some information from the maintenance manager about the system, who provided the following data: - The system operates with R-134a refrigerant;- The refrigerated environment is maintained at 0°C and the external environment at 26°C;- The refrigerant flow rate in the system is 0.08 kg/s; In addition to the data provided, you carried out some tests and measured the temperature of the refrigerant fluid at some specific points in the system, such as the compressor inlet and condenser outlet, finding values of 0°C and 26°C respectively.…
arrow_forward
Help!!! Please answer part b correctly like part A. Please!!!!
arrow_forward
You are assigned as the head of the engineering team to work on selecting the right-sized blower that will go on your new line of hybrid vehicles.The fan circulates the warm air on the inside of the windshield to stop condensation of water vapor and allow for maximum visibility during wintertime (see images). You have been provided with some info. and are asked to pick from the bottom table, the right model number(s) that will satisfy the requirement. Your car is equipped with a fan blower setting that allow you to choose between speeds 0, 1,2 and 3. Variation of the convection heat transfer coefficient is dependent upon multiple factors, including the size and the blower configuration.You can only use the following parameters:
arrow_forward
SEE MORE QUESTIONS
Recommended textbooks for you
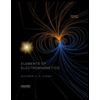
Elements Of Electromagnetics
Mechanical Engineering
ISBN:9780190698614
Author:Sadiku, Matthew N. O.
Publisher:Oxford University Press
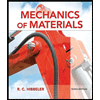
Mechanics of Materials (10th Edition)
Mechanical Engineering
ISBN:9780134319650
Author:Russell C. Hibbeler
Publisher:PEARSON
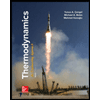
Thermodynamics: An Engineering Approach
Mechanical Engineering
ISBN:9781259822674
Author:Yunus A. Cengel Dr., Michael A. Boles
Publisher:McGraw-Hill Education
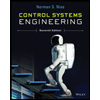
Control Systems Engineering
Mechanical Engineering
ISBN:9781118170519
Author:Norman S. Nise
Publisher:WILEY
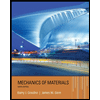
Mechanics of Materials (MindTap Course List)
Mechanical Engineering
ISBN:9781337093347
Author:Barry J. Goodno, James M. Gere
Publisher:Cengage Learning
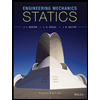
Engineering Mechanics: Statics
Mechanical Engineering
ISBN:9781118807330
Author:James L. Meriam, L. G. Kraige, J. N. Bolton
Publisher:WILEY
Related Questions
- Question 2 You are a biomedical engineer working for a small orthopaedic firm that fabricates rectangular shaped fracture fixation plates from titanium alloy (model = "Ti Fix-It") materials. A recent clinical report documents some problems with the plates implanted into fractured limbs. Specifically, some plates have become permanently bent while patients are in rehab and doing partial weight bearing activities. Your boss asks you to review the technical report that was generated by the previous test engineer (whose job you now have!) and used to verify the design. The brief report states the following... "Ti Fix-It plates were manufactured from Ti-6Al-4V (grade 5) and machined into solid 150 mm long beams with a 4 mm thick and 15 mm wide cross section. Each Ti Fix-It plate was loaded in equilibrium in a 4-point bending test (set-up configuration is provided in drawing below), with an applied load of 1000N. The maximum stress in this set-up was less than the yield stress for the…arrow_forwardI need answers for problems 13, 14, and 15 pertaining to the print provided. NOTE: If you refuse to answers all 3 parts and insist on wasting my question by breaking down 1 simple question into 3 parts, then just leave it for someone else to answer. Thank you.arrow_forwardCase Study – The New Engineer Jeff was just hired by GSI, Inc. to be their Environmental and Safety Coordinator. This is Jeff's first position after completing his engineering degree. He had taken a course in safety engineering as part of his studies and felt confident that he could handle the job. Management at GSI, Inc. has assured him that they are committed to maintaining a safe workplace. They have never had an individual dedicated to this task full-time. They will implement his recommendations if he can justify them. As Jeff begins to get familiar with the operations, he spends considerable time on the production floor. He notices workers clean their tools before break with a liquid from an unmarked 55-gallon drum. They also use this liquid to clean residue from their skin. They use paper towels to dry their tools and hands, throw these towels in the trash, and head to the break room for a snack and/or smoke. In talking with the workers, Jeff learns of some of…arrow_forward
- Case Study – The New Engineer Jeff was just hired by GSI, Inc. to be their Environmental and Safety Coordinator. This is Jeff's first position after completing his engineering degree. He had taken a course in safety engineering as part of his studies and felt confident that he could handle the job. Management at GSI, Inc. has assured him that they are committed to maintaining a safe workplace. They have never had an individual dedicated to this task full-time. They will implement his recommendations if he can justify them. As Jeff begins to get familiar with the operations, he spends considerable time on the production floor. He notices workers clean their tools before break with a liquid from an unmarked 55-gallon drum. They also use this liquid to clean residue from their skin. They use paper towels to dry their tools and hands, throw these towels in the trash, and head to the break room for a snack and/or smoke. In talking with the workers, Jeff learns of some of…arrow_forwardplease help solve A-F. thank you You are an engineer working on a project and your prototype has failed prematurely. You question whether or not a key component of the prototype was manufactured with the correct material. There are two way to check for the material properties. The first way is to have a material certification done to confirm the exact material composition. This will take some time. The second method to confirm the material properties is to make an ASTM test sample and test for the material properties. This tensile test was completed on a test sample with an initial diameter of .501” and an initial length of 2”. The Load-Deflection data for this tensile test is below. Use this data to answer the first set of questions on the Final Exam in eLearning. A. Determine the Ultimate Tensile Strength B. Determine the 0.2% Offset Yield Strength C. Determine the value of the Proportional Limit D. Determine the Modulus of Elasticity E. Determine the Strain at Yield F. Calculate %…arrow_forwardCase Study: Paula’s Pain Paula has worked for Brindle Corporation for 3 years. During this time, she has worked as a machine operator/cell leader in various work cells. Recently, the plant went to mandatory 12-hour shifts and plans to remain on this schedule for several months. Paula’s present work cell is manufacturing 3-inch diameter exhaust tubes that are made from stainless steel. These tubes get a hole punched in them, a flange welded on, and burrs ground off. The pipe then gets placed into a gage to check that it was made correctly. (The tubes weigh about six pounds.) Paula has been performing the welding operation. She leans into the machine and loads the part into a fixture then positions the flange. Both pieces are clamped (using hand clamps) into position and the machine is cycled by depressing two palm buttons. The gaging operation requires placing the finished part into the gage and clamping it (using hand clamps) into place. A pin is depressed to verify the position…arrow_forward
- I need problems 6 and 7 solved. I got it solved on 2 different occasions and it is not worded correctly. NOTE: Problem 1 is an example of how it should be answered. Below are 2 seperate links to same question asked and once again it was not answered correctly. 1. https://www.bartleby.com/questions-and-answers/it-vivch-print-reading-for-industry-228-class-date-name-review-activity-112-for-each-local-note-or-c/cadc3f7b-2c2f-4471-842b-5a84bf505857 2. https://www.bartleby.com/questions-and-answers/it-vivch-print-reading-for-industry-228-class-date-name-review-activity-112-for-each-local-note-or-c/bd5390f0-3eb6-41ff-81e2-8675809dfab1arrow_forwardA Team of Engineers asked for an internal combustion engine to use it in a designed car. Your role is to describe the operation sequence of different types of available engines, explain their mechanical efficiency, and deliver a detailed technical report to show your approach in solving and discussing the following tasks and issues. You must follow the following steps to help the team: STEP 1 Describe the operational sequence of four-stroke spark ignition and four-stroke compression ignition engines with the aid of sketches by constructing simple sketch representing the operation and plotting the P-V diagrams for each process during the cycle to show the following: The input and output heat and net output work The expansion and compression strokes The air-fuel mixture intake and exhaust gasses The spark plug when it is in the active mode The complete cycle of ideal Otto and Diesel cycles that shows the input and output heat and net output work. STEP 2 Explain the mechanical…arrow_forwardLESSON: AUTODESK AUTOCAD Choose from the choices:arrow_forward
- Stuck need help! Problem is attached. please view attachment before answering. Really struggling with this concept. Please show all work so I can better understand ! Thank you so much.arrow_forwardQuestion 3 You are working on a design team at a small orthopaedic firm. Your team is starting to work on a lower limb (foot-ankle) prosthesis for individuals who have undergone foot amputation (bone resection at the distal tibia). You remember hearing about "osseointegration" in an exciting orthopaedic engineering class you attended at Clemson, so you plan to attach the foot prosthesis using a solid metal rod inserted into the distal tibia. You think stainless steel or titanium alloy might be a useful rod material. You decide to begin this problem by identifying typical tibial bone anatomy and mechanical behavior (as provided in the tables and image below). You assume the tibial bone can be modeled as a hollow cylinder of cortical bone, as represented in the image. You anticipate the length of the rod will be 1/2 the length of the tibia. Q3G: Critical Thinking: What would you propose to your team as the next step in this analysis? Is it reasonable to assume the rod will experience the…arrow_forwardHelp!!! Please answer part B correctly!!! Pleasearrow_forward
arrow_back_ios
SEE MORE QUESTIONS
arrow_forward_ios
Recommended textbooks for you
- Elements Of ElectromagneticsMechanical EngineeringISBN:9780190698614Author:Sadiku, Matthew N. O.Publisher:Oxford University PressMechanics of Materials (10th Edition)Mechanical EngineeringISBN:9780134319650Author:Russell C. HibbelerPublisher:PEARSONThermodynamics: An Engineering ApproachMechanical EngineeringISBN:9781259822674Author:Yunus A. Cengel Dr., Michael A. BolesPublisher:McGraw-Hill Education
- Control Systems EngineeringMechanical EngineeringISBN:9781118170519Author:Norman S. NisePublisher:WILEYMechanics of Materials (MindTap Course List)Mechanical EngineeringISBN:9781337093347Author:Barry J. Goodno, James M. GerePublisher:Cengage LearningEngineering Mechanics: StaticsMechanical EngineeringISBN:9781118807330Author:James L. Meriam, L. G. Kraige, J. N. BoltonPublisher:WILEY
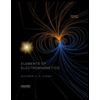
Elements Of Electromagnetics
Mechanical Engineering
ISBN:9780190698614
Author:Sadiku, Matthew N. O.
Publisher:Oxford University Press
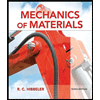
Mechanics of Materials (10th Edition)
Mechanical Engineering
ISBN:9780134319650
Author:Russell C. Hibbeler
Publisher:PEARSON
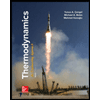
Thermodynamics: An Engineering Approach
Mechanical Engineering
ISBN:9781259822674
Author:Yunus A. Cengel Dr., Michael A. Boles
Publisher:McGraw-Hill Education
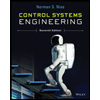
Control Systems Engineering
Mechanical Engineering
ISBN:9781118170519
Author:Norman S. Nise
Publisher:WILEY
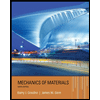
Mechanics of Materials (MindTap Course List)
Mechanical Engineering
ISBN:9781337093347
Author:Barry J. Goodno, James M. Gere
Publisher:Cengage Learning
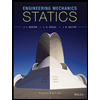
Engineering Mechanics: Statics
Mechanical Engineering
ISBN:9781118807330
Author:James L. Meriam, L. G. Kraige, J. N. Bolton
Publisher:WILEY