dhl as3
docx
keyboard_arrow_up
School
Academy of Business Computers (Karimabad), Karachi *
*We aren’t endorsed by this school
Course
202
Subject
Management
Date
Nov 24, 2024
Type
docx
Pages
8
Uploaded by ProfessorRain9773
4. Analysis and Findings:
4.1 Agile and Lean Logistics:
Enhanced Operational Efficiency: Agile and Lean Logistics practises have the potential to dramatically improve DHL's productivity. These tenets define a philosophy of logistics that prioritises flexibility, incremental progress, and the removal of unnecessary procedures. Dey et al.'s (2019) research shows that by adhering to these principles, DHL may reduce operational expenses and improve the efficiency of its logistics operations by methodically identifying and eliminating any non-value-added tasks.
One major benefit is that it streamlines logistical processes by doing away with extra steps. DHL may streamline its operations by examining them in detail to determine which steps do not directly contribute to value generation. By reducing inefficiencies, the supply chain is able to make better use of its assets and distribute resources like time and labour. This results in lower operating expenses and greater flexibility to use those savings to initiatives with a higher return on investment.
In addition, the tenets of Agile and Lean Logistics stress the need of speed and flexibility in responding to the ever-changing needs of the market and the preferences of individual customers.
DHL may use these ideas to maintain flexibility and quick reaction time in the face of uncertainty. The organisation is able to respond quickly to changes in the market, supply chain problems, and client preferences by embracing flexibility and reducing needless complexity. DHL is able to maintain its excellent service quality and timeliness because to its quick response time, which in turn increases customer happiness and loyalty.
Adaptability to Market Dynamics: Due to Agile Logistics' flexibility, DHL now has an effective tool with which to deal with the dynamic nature of the logistics business. The capacity to quickly and effectively adapt to changing market conditions and consumer expectations is a crucial competitive advantage in today's business environment.
If DHL can keep up with the ever-changing nature of the industry, it will be able to take advantage of the flexibility that Agile Logistics provides. Economic swings, geopolitical upheavals, new technology, and changes in consumer behaviour are just some of the elements that might affect market circumstances. Such fluctuations may have far-reaching effects on the demand for logistics services, influencing changes in traffic patterns, shipment quantities, and timetable anticipation.
DHL may foster an atmosphere of proactiveness and adaptability by adopting the concepts of Agile Logistics. This necessitates keeping tabs on the market, keeping an eye out for new trends, and being able to quickly adjust your tactics and procedures to meet the needs of your customers as they change. This flexibility allows DHL to stay ahead of the competition by responding quickly to the changing demands of its customers in the logistics business.
Agile Logistics promotes teamwork not just inside DHL but also with its clients. Agile practises rely heavily on open lines of communication and cooperation across teams, departments, and with clients. This helps DHL learn more about its customers' wants, so the company may better provide its services to them. As a result, the logistics system is flexible enough to provide individualised services that meet the needs of each client.
Improved Customer Satisfaction: DHL has used Agile and Lean Logistics practises to increase efficiency and better serve its customers. Meeting and surpassing client expectations is essential in the logistics sector, which is
service-driven by its very nature. DHL can increase customer satisfaction and loyalty by placing a premium on quickly responding to customer needs and offering timely, individualised delivery options.
DHL's promptness in responding to customer requests is a major factor in the company's high level of customer satisfaction. Companies today expect real-time insight into their supply chains and rely heavily on just-in-time inventory management, making it imperative that they respond quickly to consumer demands. DHL is able to promptly respond to the needs of its customers by using the concepts of agile logistics to modify delivery times, alter routes, and fulfil unique demands. Customers are more likely to be pleased with DHL's services because of the company's
responsiveness to their needs.
Also, in logistics, it is crucial to be able to guarantee on-time deliveries. A client's whole supply chain may be negatively impacted by delays and missed deadlines, which can result in higher prices and unhappy customers. DHL is able to improve delivery reliability and timeliness by employing Agile and Lean Logistics practises, which have helped the company streamline its processes, decrease bottlenecks, and eliminate inefficiencies. Meeting or beating promised delivery times not only pleases customers but also solidifies DHL's standing as a trustworthy logistics provider.
The ability to tailor services to each individual client is also crucial. The concepts of Agile Logistics make it possible to adapt delivery methods to the individual requirements of each customer. DHL may customise the logistics experience for each customer by providing unique packaging, rerouting shipments, and providing other value-added services. Customers appreciate DHL's dedication to their demands, and their satisfaction and loyalty to the company increase as a result.
4.2 Digital Twin Technology:
Real-time Simulation and Optimization: DHL's logistics operations may benefit greatly from the real-time modelling and optimisation made possible by digital twin technology. DHL's capacity to quickly and efficiently adapt to
shifts in the supply chain and customer needs is boosted by the construction of exact digital duplicates of the company's logistical procedures.
Digital twin technology's ability to simulate in real time is a major benefit. DHL is able to make digital twins of its physical logistics systems, which are near-perfect simulations of the real thing. These digital twins aren't just static images; they're living, breathing things, updated in real
time to reflect the state of the art in logistics. DHL has a significant responsiveness advantage because to this real-time feature, which allows the company to track and model its logistical processes in near real-time.
This allows DHL to quickly adjust to changes or interruptions in the supply chain. DHL may utilise digital twins to simulate alternative scenarios and analyse the impact on logistics operations in the event of, say, unexpected delays, route closures, or changes in demand. To keep
operations running smoothly and efficiently in the face of unforeseen challenges, the organisation may use this capacity to make quick, well-informed choices, such as re-routing deliveries, reallocating resources, or altering timetables.
In addition, Digital Twin Technology allows for in-depth enhancement. DHL may try out several paths, spend resources wisely, and fine-tune procedures by simulating different outcomes. The digital twins provide a foundation for data-driven decision making and continual improvement, whether the goal is to select the most efficient route for delivering goods, enhance the efficiency of storage facilities, or adapt workforce levels to changes in demand.
The ability to do predictive maintenance is yet another perk. Digital twins allow DHL to keep tabs on the health of its cars and machinery, preventing breakdowns and other disruptions to their
operations. By taking preventative actions, you may minimise delivery delays, repair expenses, and downtime.
Predictive Maintenance: DHL has adopted a new strategy for maintaining the dependability and continuity of its logistics operations: predictive maintenance, made possible by Digital Twin Technology. DHL's fleet management is revolutionised by this preventative approach, which has several advantages beyond a reduction in equipment breakdowns.
Predictive maintenance's key benefit is that it helps anticipate when machines may break down. DHL is able to receive real-time insights into the health of its assets thanks to the use of digital twins, which allow for continuous monitoring of the condition and performance of equipment and vehicles. Temperature, vibration, fuel usage, and other metrics are all tracked in real time. Early alerts are triggered the second any abnormalities or departures from normal operating conditions are identified.
DHL's ability to take preventative steps thanks to these early alerts is priceless. DHL can arrange maintenance and repairs at the most practical and economical periods instead of waiting for equipment to break down. This method not only keeps operations running smoothly, but also avoids the need for expensive, time-consuming emergency repairs.
Your preview ends here
Eager to read complete document? Join bartleby learn and gain access to the full version
- Access to all documents
- Unlimited textbook solutions
- 24/7 expert homework help
Equipment and automobiles both benefit from the increased longevity that comes with predictive
maintenance. DHL can save costs, increase asset life, and increase ROI by preventing problems before they worsen. since of this, you can save money in the long term since you won't have to replace things as often or do as many repairs.
Taking care of repairs before they break down also improves security. DHL is able to minimise the possibility of accidents and incidents caused by mechanical problems by maintaining its equipment and vehicles to the highest standards. This greatly improves the security of the transportation process for both workers and their cargo.
Predictive maintenance enhances operational preparation and asset distribution. To keep logistics
running as smoothly as possible, DHL might plan maintenance during times of lesser demand. Maintenance personnel, materials, and tools may all be better organised as a result.
Data-Driven Decision Making: DHL's deployment of Digital Twin Technology into its logistics operations has provided a significant benefit: data-driven decision making. Digital twins provide DHL with a plethora of real-time data and insights, allowing the company to make educated decisions that have a significant influence on many facets of its logistics operations.
The optimisation of delivery according to traffic circumstances is a major advantage of data-
driven decision making. The effectiveness of logistics operations can be negatively impacted by factors such as traffic congestion, road closures, and unanticipated delays. However, with real-
time data from digital twins, DHL can track traffic conditions in the places it serves, allowing it to make on-the-fly adjustments to its delivery schedule. This lessens the likelihood of delivery delays while also decreasing energy usage and carbon emissions. DHL can increase customer satisfaction by delivering packages on time by optimising routes using real-time data.
Data-driven decision making also plays an important role in warehouse management. The inventory, storage, and order volumes at a warehouse may all be better understood with the help of a digital twin. DHL is better able to manage its warehouse operations, such as stock replenishment, space utilisation, and employee scheduling, with the use of this information. DHL
can save money on warehouse space, speed up order processing, and simplify its logistics operations by optimising the way it utilises its facilities.
Data-driven decision making also improves workforce management significantly. DHL can track the amount of work being done at each stage of the logistics process with the use of data from digital twins. If there are delays or inefficiencies, management may easily modify staffing numbers to meet customer needs. This pliability makes sure that workers aren't over or underpaid, and that there aren't any shortages of workers when demand is high.
Data-driven decision making is also applicable to logistics planning as a whole. DHL is able to analyse past data and current insights to spot patterns, client preferences, and improvement
opportunities. Strategic moves like entering a new market, introducing a new service, or fine-
tuning collaborations within the supply chain may all be informed by this data-driven method.
Identifying Bottlenecks and Inefficiencies: DHL's digital twins are crucial in helping the business discover and repair inefficiencies and slowdowns in its supply chain. DHL is able to take immediate remedial steps and promote continuous process optimisation with the help of these digital duplicates of the company's logistical systems.
Digital twins' capacity to display an all-encompassing picture of the logistical procedure is one of
its main benefits. Information from the order processing, stock management, shipping, and delivery phases of the supply chain are collected. DHL may use this information to locate workflow slowdowns and congestion spots, known as bottlenecks. Delays, higher prices, and unsatisfied customers are typically the results of these bottlenecks.
Digital twins allow DHL to quickly identify bottlenecks and implement fixes. If there's a delay in
processing orders, DHL can speed things up by, perhaps, hiring more people, streamlining the fulfilment process, or using automation. In a similar vein, if there is a bottleneck in transportation, optimising routes and redistributing resources can help get things moving again and reduce wait times for deliveries.
Improvement efforts could also focus on eliminating inefficiencies. Data on resource utilisation, equipment performance, and process efficiency are all available via digital twins. DHL may use this information to determine which regions have insufficient staffing, outdated machinery, or excessively complicated procedures. DHL will save money, improve efficiency, and make better use of resources by fixing these problems.
Digital twin technology is distinguished by its capacity for continuous process improvement. DHL is able to track the effectiveness of its efforts to eliminate bottlenecks and boost efficiency thanks to the data collected and analysed in real time by digital twins. The organisation can continuously improve its logistical efficiency thanks to this feedback loop, which allows it to fine-tune its operations over time.
In addition, digital twins allow DHL to test out potential improvements to processes by simulating a variety of situations. DHL is able to predict how a future change, like reorganising a
warehouse's structure or personnel, or switching up delivery routes, may affect operations thanks
to simulations. This preventative method reduces the uncertainty of making process modifications and guarantees that any adjustments made are well-informed and beneficial.
5. Discussion and Implications:
DHL's digital transformation initiatives and the logistics sector as a whole will be significantly affected by the results of the investigation into Agile and Lean Logistics and Digital Twin Technology.
Improved Ability to Compete: Adopting the tenets of Agile and Lean Logistics provides DHL with a potent toolkit for preserving and enhancing its competitiveness. Cost reduction, increased efficiency in operations, and customer happiness are of the utmost importance in today's ever-
changing logistics industry. DHL's ability to quickly adjust to shifting market conditions, meet customers' needs in real time, and provide consistently high-quality services is a direct result of adhering to these values. DHL is in a strong competitive position because of its flexibility to evolve with the requirements of its customers.
Applying Digital Twins Strategically: DHL's strategic goals fit perfectly with the use of Digital Twin Technology. As a result, logistical operations may be optimised, and equipment and vehicles can be managed proactively, unlocking the full potential of data-driven decision-making
for the organisation. DHL uses digital twins as a foundation for its logistics innovation since they
allow for continuous monitoring, simulation, and optimisation. This helps DHL not only keep up with the competition but also further establish itself as a frontrunner in the logistics sector. DHL has shown its dedication to operational excellence and customer happiness by adopting this cutting-edge technology, making it the standard by which others are measured.
Continuous Improvement: The importance of continuous improvement is emphasised by both digital twin technology and agile and lean logistics. Continuous process improvement, the removal of non-value-adding steps, and the maximisation of efficiency are the tenets of both agile and lean logistics. DHL is able to maintain its agility, adaptability, and responsiveness to market changes with the use of digital twins that enable real-time monitoring and optimisation. DHL has a culture of innovation and quality thanks to its dedication to constant development, which means the firm consistently meets and often exceeds consumer expectations.
Impact on the Logistics sector: The findings of this study have important implications for the logistics sector as a whole, not just for DHL. For other logistics firms that want to boost their efficiency, save expenses, and increase their responsiveness, the lessons learned through the successful use of Agile and Lean Logistics concepts and Digital Twin Technology can serve as a template. The entire sector can raise its operational standards, provide its clients with better services, and adjust to the changing needs of the global market if its members share best practises and adopt comparable policies.
In conclusion, this study has far-reaching and varied repercussions. DHL's adoption of Agile and Lean Logistics and strategic use of Digital Twin Technology not only sets the organisation up for
long-term success, but also leads the path for improvements across the logistics sector. Customers, stakeholders, and the global economy all win when DHL raises the bar for the
Your preview ends here
Eager to read complete document? Join bartleby learn and gain access to the full version
- Access to all documents
- Unlimited textbook solutions
- 24/7 expert homework help
industry by constantly improving procedures, welcoming innovation, and being responsive to client demands.
6. Recommendations:
Implementation of Agile and Lean Logistics:
Waste Reduction: DHL has to examine all of its current procedures to find waste and do away with it. These are activities that either don't benefit the client or create unneeded expenses. Workflows may be simplified using lean techniques like value stream mapping.
Streamlining Workflows: In order to guarantee seamless and effective operations, DHL needs streamline its logistics workflows. This includes establishing uniform procedures, shortening production times, and optimising use of available resources. By using agile approaches, businesses may be more flexible and quick to respond to shifting market demands.
Culture of Continuous Improvement: Promoting a mindset of constant improvement is crucial. DHL should promote an environment where workers at all levels are encouraged to suggest and execute changes. This culture of constant improvement may be fostered through regular Kaizen events and cross-functional teams.
Investment in Digital Twin Technology:
Comprehensive Digital Twins: To improve its logistics operations, DHL should invest in creating
comprehensive digital twins. The whole distribution process, from taking orders to sending them out, should be represented in these virtual twins. Digital twins must be updated often to guarantee their correctness and continued usefulness.
Data-Driven Decision-Making: DHL should use the insights and real-time data that digital twins bring to make well-informed decisions. Transportation route optimisation, maintenance requirement forecasting, and resource allocation may all be accomplished by monitoring and reacting to situations in real time.
Integration with Current Systems: It's critical that digital twins be integrated with current IT systems. DHL has to make sure that data from digital twins can be easily imported into its analytics and decision-making platforms.
Employee Training and Change Management:
Training Plans: DHL should create training plans to give staff members the abilities and information needed to adopt Agile and Lean Logistics concepts and make efficient use of Digital Twin Technology. Different employees in the company need different types of training.
Change Management Strategies: Digital transformation typically necessitates major adjustments to existing procedures and routines. DHL needs effective change management solutions to help
employees through the upcoming changes. Plans for spreading the word, motivating workers, and dealing with any opposition to change are all part of this.
Control and Assessment:
Establishing KPIs: To evaluate the success of its digital transformation initiatives, DHL should establish key performance indicators (KPIs). These key performance indicators should support efforts to save expenses, boost productivity, and delight customers.
Regular Assessments: Continuous monitoring and assessment is crucial, so make sure you do it on a regular basis. DHL needs to do regular audits in order to monitor development, locate roadblocks, and verify the efficacy of interventions. Continual progress requires adjusting to account for these evaluations.
Sharing Best Practices:
Industry Collaboration: DHL may work with other companies and organisations in its field to pool resources and knowledge as it undergoes its digital transformation. The logistics business can benefit from increased efficiency and effectiveness if more people participate in industry forums and conferences.
Publication of Case Studies: The results of DHL's digital transformation efforts may be documented in case studies and success stories that the company can publish. For other logistics firms planning comparable expansions, this might serve as a source of motivation and direction.
Conclusion of Findings and Analysis:
In conclusion, the study's data and analyses demonstrate how digital transformation may dramatically improve DHL's logistics performance. Agile and Lean Logistics practises have the potential to boost productivity, responsiveness to market changes, and patron approval. This strategy allows DHL to adapt to the dynamic nature of the logistics industry and meet the needs of its customers in a way that is both efficient and cost-effective.
DHL also gains the ability to make data-driven decisions and perform real-time simulations thanks to the implementation of Digital Twin Technology. DHL is now in a better position to not just meet but exceed consumer expectations thanks to these innovations. The results of this study
will have an effect on DHL, but they will also set a standard for the logistics industry as a whole.
To ensure DHL's sustained success and competitiveness in the ever-evolving logistics industry, these insights together create a compelling roadmap for the company's journey towards digital transformation.
Related Documents
Recommended textbooks for you
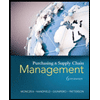
Purchasing and Supply Chain Management
Operations Management
ISBN:9781285869681
Author:Robert M. Monczka, Robert B. Handfield, Larry C. Giunipero, James L. Patterson
Publisher:Cengage Learning
Marketing
Marketing
ISBN:9780357033791
Author:Pride, William M
Publisher:South Western Educational Publishing
Recommended textbooks for you
- Purchasing and Supply Chain ManagementOperations ManagementISBN:9781285869681Author:Robert M. Monczka, Robert B. Handfield, Larry C. Giunipero, James L. PattersonPublisher:Cengage LearningMarketingMarketingISBN:9780357033791Author:Pride, William MPublisher:South Western Educational Publishing
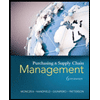
Purchasing and Supply Chain Management
Operations Management
ISBN:9781285869681
Author:Robert M. Monczka, Robert B. Handfield, Larry C. Giunipero, James L. Patterson
Publisher:Cengage Learning
Marketing
Marketing
ISBN:9780357033791
Author:Pride, William M
Publisher:South Western Educational Publishing