continuous assesment
docx
keyboard_arrow_up
School
University of Nairobi *
*We aren’t endorsed by this school
Course
1
Subject
Management
Date
Nov 24, 2024
Type
docx
Pages
8
Uploaded by LieutenantDanger3005
Running Head:
IMPROVEMENT PLAN FOR OPERATIONAL EFFICIENCY IN MANUFACTURING ORGANIZATION
1
Building a Continuous Improvement Plan for Operational Efficiency in a Manufacturing
Organization
Mario Fortenberry
The University of Arizona Global Campus
ISM643: Leadership in Business Systems Development
Professor: Dr. Osama Morad May 19, 2023
IMPROVEMENT PLAN FOR OPERATIONAL EFFICIENCY IN A MANUFACTURING
ORGANIZATION
2
Introduction Continuous improvement is a crucial concept in manufacturing organizations, driving operational efficiency and overall performance. Through ongoing efforts to identify waste, optimize processes, and enhance productivity, organizations can meet customer demands, reduce costs, and increase profitability (Khan et al., 2019). This paper aims to explore the significance of developing a comprehensive continuous improvement plan for operational efficiency in manufacturing. By establishing a structured approach, organizations can drive sustainable growth, enhance quality, and outperform competitors. The paper will delve into the key elements of a continuous improvement plan, the steps involved in its development and implementation, and evaluation methods to measure effectiveness. Ultimately, the focus is to provide insights and guidance on how a well-structured continuous improvement plan can significantly contribute to operational efficiency, productivity, and success in the manufacturing sector.
Continuous improvement is a systematic approach that drives organizational success by optimizing processes, products, and services through ongoing incremental enhancements. By fostering a culture of innovation and learning, continuous improvement empowers employees to proactively address inefficiencies and drive creativity (Khan et al., 2019). It enhances operational
efficiency by eliminating waste, streamlining processes, and optimizing resource allocation. Moreover, continuous improvement improves product and service quality, leading to higher customer satisfaction and loyalty. However, organizations may face challenges in implementing continuous improvement, such as resistance to change and the need for sustained leadership commitment. Overcoming these challenges requires effective change management strategies and establishing relevant metrics for evaluation. By embracing continuous improvement and
IMPROVEMENT PLAN FOR OPERATIONAL EFFICIENCY IN A MANUFACTURING
ORGANIZATION
3
addressing these challenges, organizations can create a culture of excellence and achieve sustainable success (E. Klotins & Gorschek, 2022).
Key Components of a Continuous Improvement Plan
A continuous improvement plan for operational efficiency should include several essential elements. These may include clearly defined goals and objectives that align with the organization's strategic direction. Additionally, it should identify specific improvement initiatives
and establish a timeline for implementation. The plan should also outline the roles and responsibilities of key stakeholders involved in driving improvement efforts. Furthermore, it should incorporate mechanisms for monitoring progress, evaluating outcomes, and making adjustments as needed (Porumboiu, 2022).
Leadership commitment is crucial in driving continuous improvement efforts. Leaders must actively demonstrate their support, provide necessary resources, and set an example for the rest of the organization. They should communicate the importance of continuous improvement, create a safe and supportive environment for sharing ideas, and recognize and reward employee contributions. Employee engagement is equally important, as it encourages ownership and fosters a sense of accountability for driving improvement. Engaged employees are more likely to
generate innovative ideas, actively participate in improvement initiatives, and contribute to a culture of continuous improvement (Cullen, 2018).
Data analysis plays a vital role in the continuous improvement process. It involves collecting and analyzing relevant data to identify areas of improvement, measure performance, and track progress over time. Process mapping, on the other hand, helps visualize and understand
existing workflows, identify bottlenecks and inefficiencies, and design more streamlined processes. Waste reduction is a critical aspect of continuous improvement, aiming to eliminate
Your preview ends here
Eager to read complete document? Join bartleby learn and gain access to the full version
- Access to all documents
- Unlimited textbook solutions
- 24/7 expert homework help
IMPROVEMENT PLAN FOR OPERATIONAL EFFICIENCY IN A MANUFACTURING
ORGANIZATION
4
non-value-added activities, minimize defects, reduce cycle times, and optimize resource utilization. These elements collectively enable organizations to make informed decisions, prioritize improvement efforts, and drive operational efficiency (Porumboiu, 2022).
Standardization is essential for ensuring consistent and reliable processes across the organization. It involves documenting best practices, creating standard operating procedures, and
establishing guidelines to drive efficiency and reduce variation. Training is crucial to equip employees with the necessary skills and knowledge to contribute effectively to continuous improvement initiatives. By providing training on problem-solving techniques, process improvement methodologies, and data analysis, organizations empower employees to identify and implement improvements. Cross-functional collaboration is key to achieving operational efficiency as it brings together diverse perspectives, knowledge, and expertise. Collaborative efforts allow for the identification of interdepartmental opportunities for improvement and foster a culture of shared learning and innovation (Porumboiu, 2022).
Steps to Develop and Implement a Continuous Improvement Plan
Developing and implementing a continuous improvement plan in a manufacturing organization involves a systematic approach that ensures successful outcomes. The first crucial step is to conduct a comprehensive assessment of the organization's current processes and systems. This assessment should involve collecting and analyzing relevant data, mapping process
flows, and actively involving employees at all levels (Porumboiu, 2022). By conducting this assessment, organizations can identify improvement opportunities and prioritize initiatives based on their potential impact and alignment with strategic objectives.
Once the improvement opportunities are identified, the next step is to set clear goals, develop action plans, and allocate necessary resources. Setting specific and measurable goals
IMPROVEMENT PLAN FOR OPERATIONAL EFFICIENCY IN A MANUFACTURING
ORGANIZATION
5
helps provide a clear direction for the continuous improvement efforts. Action plans outline the steps and activities required to achieve these goals, including timelines and responsible individuals or teams. Alongside goal setting, resource allocation is crucial to ensure the availability of adequate personnel, budget, and technology needed to support the implementation of improvement initiatives effectively (E. Klotins & Gorschek, 2022).
During the implementation phase, effective communication, change management, and employee empowerment play a vital role. Transparent and open communication helps ensure that
all employees are aware of the continuous improvement plan, its objectives, and progress. Regular updates and feedback channels should be established to foster a culture of engagement and collaboration. Change management techniques should be employed to address any resistance
or concerns that may arise during the implementation process (Khan et al., 2019). By providing training, addressing employee concerns, and involving them in decision-making, organizations can empower employees and create a sense of ownership in driving the continuous improvement efforts.
Evaluating the Effectiveness of the Continuous Improvement Plan
Evaluating the effectiveness of a continuous improvement plan involves several key components. Firstly, organizations utilize metrics and key performance indicators to measure operational efficiency and track improvement progress. These metrics may include cycle time, defect rate, customer satisfaction, and productivity measures. By monitoring these indicators, organizations can assess the impact of improvement initiatives and identify areas for further enhancement. Secondly, it is crucial to monitor and evaluate the outcomes of improvement initiatives to determine their effectiveness. This involves analyzing data, comparing performance
IMPROVEMENT PLAN FOR OPERATIONAL EFFICIENCY IN A MANUFACTURING
ORGANIZATION
6
against established goals, and conducting regular reviews to identify successes and areas requiring additional attention (Unzueta et al., 2020). Lastly, sustaining improvement efforts necessitates the establishment of feedback loops, regular reviews, and a commitment to continuous learning. Feedback loops enable organizations to gather input from employees, stakeholders, and customers, providing valuable insights and opportunities for refinement. Regular reviews allow for the assessment of progress and the identification of new improvement opportunities. Continuous learning ensures that organizations adapt and evolve in response to changing needs and challenges, fostering a culture of ongoing improvement and innovation (Unzueta et al., 2020). By employing these evaluation strategies, organizations can assess the effectiveness of their continuous improvement plan, make necessary
adjustments, and sustain long-term success.
Conclusion In conclusion, building and implementing a continuous improvement plan in a manufacturing organization is essential for driving operational efficiency and sustained success. By embracing a culture of continuous improvement, organizations can optimize processes, enhance product and service quality, and meet customer expectations. The key components of a successful continuous improvement plan include conducting a comprehensive assessment, setting clear goals, and allocating necessary resources. Additionally, effective communication, change management, and employee empowerment play crucial roles in driving successful implementation. Evaluating the effectiveness of the continuous improvement plan involves measuring operational efficiency, monitoring outcomes, and establishing feedback loops and continuous learning processes. By consistently evaluating and refining the plan, organizations can sustain improvement efforts and adapt to changing market demands.
Your preview ends here
Eager to read complete document? Join bartleby learn and gain access to the full version
- Access to all documents
- Unlimited textbook solutions
- 24/7 expert homework help
IMPROVEMENT PLAN FOR OPERATIONAL EFFICIENCY IN A MANUFACTURING
ORGANIZATION
7
IMPROVEMENT PLAN FOR OPERATIONAL EFFICIENCY IN A MANUFACTURING
ORGANIZATION
8
References
Cullen, E. (2018, April 20). How to promote continuous improvement in the workplace
. Mentimeter. https://www.mentimeter.com/blog/great-leadership/how-to-promotes-
continuous-improvement-in-the-workplace
Dewar, C. (2019). How continuous improvement can build a competitive edge | McKinsey & Company
. Www.mckinsey.com. https://www.mckinsey.com/capabilities/people-and-
organizational-performance/our-insights/the-organization-blog/how-continuous-
improvement-can-build-a-competitive-edge
E. Klotins, & Gorschek, T. (2022). Continuous Software Engineering in the Wild
. 3–12. https://doi.org/10.1007/978-3-031-04115-0_1
Khan, S. A., Kaviani, M. A., J. Galli, B., & Ishtiaq, P. (2019). Application of continuous improvement techniques to improve organization performance. International Journal of Lean Six Sigma
, 10
(2), 542–565. https://doi.org/10.1108/ijlss-05-2017-0048
Porumboiu, D. (2022). How to Develop a Continuous Improvement Plan?
Www.viima.com. https://www.viima.com/blog/develop-continuous-improvement-plan
Unzueta, G., Esnaola, A., & Eguren, J. A. (2020). Framework to Evaluate Continuous Improvement Process Efficacy: A Case Study of a Capital Goods Company. Quality Innovation Prosperity
, 24
(2), 93. https://doi.org/10.12776/qip.v24i2.1436
Related Documents
Recommended textbooks for you
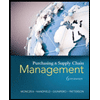
Purchasing and Supply Chain Management
Operations Management
ISBN:9781285869681
Author:Robert M. Monczka, Robert B. Handfield, Larry C. Giunipero, James L. Patterson
Publisher:Cengage Learning
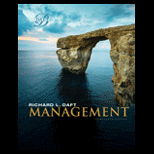
Management, Loose-Leaf Version
Management
ISBN:9781305969308
Author:Richard L. Daft
Publisher:South-Western College Pub
Recommended textbooks for you
- Purchasing and Supply Chain ManagementOperations ManagementISBN:9781285869681Author:Robert M. Monczka, Robert B. Handfield, Larry C. Giunipero, James L. PattersonPublisher:Cengage LearningManagement, Loose-Leaf VersionManagementISBN:9781305969308Author:Richard L. DaftPublisher:South-Western College Pub
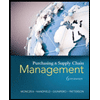
Purchasing and Supply Chain Management
Operations Management
ISBN:9781285869681
Author:Robert M. Monczka, Robert B. Handfield, Larry C. Giunipero, James L. Patterson
Publisher:Cengage Learning
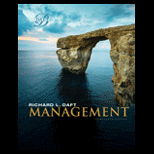
Management, Loose-Leaf Version
Management
ISBN:9781305969308
Author:Richard L. Daft
Publisher:South-Western College Pub