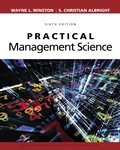
Practical Management Science
6th Edition
ISBN: 9781337671989
Author: WINSTON
Publisher: Cengage
expand_more
expand_more
format_list_bulleted
Concept explainers
Question
Chapter 6, Problem 49P
a)
Summary Introduction
To determine: The way to maximize the profit of the manufacturer.
Introduction: The variation between the present value of the
b)
Summary Introduction
To analyze: The given situation using SolverTable.
Introduction: The variation between the present value of the cash outflows and the present value of the cash inflows are known as the Net Present Value (NPV).
Expert Solution & Answer

Trending nowThis is a popular solution!

Students have asked these similar questions
Need help or ideas to design out two slides as my script and writing quite long to squeese into two slides. But can just point form in slides with correct title and a good script for me to present two slides in only 2.5 mins. Following is my draft, pls guide me step by step on powerpoint creation and good script to present findings.
My draft: Slide 1: Foreign Labor Exploitation in Dyson's Supply Chain
Introduction
Dyson's former Malaysian supplier, ATA IMS Bhd, became embroiled in serious labor exploitation allegations in 2021.
These concerns surfaced when whistleblowers exposed unethical labor practices affecting migrant workers, primarily from Nepal and Bangladesh.
Key Forms of Exploitation
Debt Bondage Due to Recruitment Fees
Workers were forced to pay exorbitant recruitment fees before securing employment, often taking loans at high interest rates.
This financial burden trapped them in debt bondage, leaving them with little choice but to accept exploitative working…
Not use ai please
The Business Development Bank of Canada. (2023). Canadian economic outlook for 2024: Shifting into neutral. https://www.bdc.ca/en/articles-tools/blog/canadian-economic-outlook-for-2024-shifting-into-neutral
“Despite persistently high inflation and rising interest rates, the news was generally better than expected for the Canadian economy in 2023” (BDC Blog 2024).
Discussion Question:
In your view, what are the most pressing problems for Canadian companies or consumers in 2024? Explain your answer using current examples of companies or consumer concerns.
Chapter 6 Solutions
Practical Management Science
Ch. 6.3 - Prob. 1PCh. 6.3 - Prob. 2PCh. 6.3 - Solve Problem 1 with the extra assumption that the...Ch. 6.3 - Prob. 4PCh. 6.3 - Prob. 5PCh. 6.3 - Prob. 6PCh. 6.3 - Prob. 7PCh. 6.3 - Prob. 8PCh. 6.3 - Prob. 9PCh. 6.3 - Prob. 10P
Ch. 6.4 - Prob. 11PCh. 6.4 - Prob. 12PCh. 6.4 - Prob. 13PCh. 6.4 - Prob. 14PCh. 6.4 - Prob. 15PCh. 6.4 - Prob. 16PCh. 6.4 - Prob. 17PCh. 6.4 - Prob. 18PCh. 6.4 - Prob. 19PCh. 6.4 - Prob. 20PCh. 6.4 - Prob. 21PCh. 6.4 - Prob. 22PCh. 6.4 - Prob. 23PCh. 6.5 - Prob. 24PCh. 6.5 - Prob. 25PCh. 6.5 - Prob. 26PCh. 6.5 - Prob. 28PCh. 6.5 - Prob. 29PCh. 6.5 - Prob. 30PCh. 6.5 - In the optimal solution to the Green Grass...Ch. 6.5 - Prob. 32PCh. 6.5 - Prob. 33PCh. 6.5 - Prob. 34PCh. 6.5 - Prob. 35PCh. 6.6 - Prob. 36PCh. 6.6 - Prob. 37PCh. 6.6 - Prob. 38PCh. 6 - Prob. 39PCh. 6 - Prob. 40PCh. 6 - Prob. 41PCh. 6 - Prob. 42PCh. 6 - Prob. 43PCh. 6 - Prob. 44PCh. 6 - Prob. 45PCh. 6 - Prob. 46PCh. 6 - Prob. 47PCh. 6 - Prob. 48PCh. 6 - Prob. 49PCh. 6 - Prob. 50PCh. 6 - Prob. 51PCh. 6 - Prob. 52PCh. 6 - Prob. 53PCh. 6 - Prob. 54PCh. 6 - Prob. 55PCh. 6 - Prob. 56PCh. 6 - Prob. 57PCh. 6 - Prob. 58PCh. 6 - Prob. 59PCh. 6 - Prob. 60PCh. 6 - Prob. 61PCh. 6 - Prob. 62PCh. 6 - Prob. 63PCh. 6 - Prob. 64PCh. 6 - Prob. 65PCh. 6 - Prob. 66PCh. 6 - Prob. 67PCh. 6 - Prob. 68PCh. 6 - Prob. 69PCh. 6 - Prob. 70PCh. 6 - Prob. 71PCh. 6 - Prob. 72PCh. 6 - Prob. 73PCh. 6 - Prob. 74PCh. 6 - Prob. 75PCh. 6 - Prob. 76PCh. 6 - Prob. 77PCh. 6 - Prob. 78PCh. 6 - Prob. 79PCh. 6 - Prob. 80PCh. 6 - Prob. 81PCh. 6 - Prob. 82PCh. 6 - Prob. 83PCh. 6 - Prob. 84PCh. 6 - Prob. 85PCh. 6 - Prob. 86PCh. 6 - Prob. 87PCh. 6 - Prob. 88PCh. 6 - Prob. 89PCh. 6 - Prob. 90PCh. 6 - Prob. 91PCh. 6 - Prob. 92PCh. 6 - This problem is based on Motorolas online method...Ch. 6 - Prob. 94PCh. 6 - Prob. 95PCh. 6 - Prob. 96PCh. 6 - Prob. 97PCh. 6 - Prob. 98PCh. 6 - Prob. 99PCh. 6 - Prob. 100PCh. 6 - Prob. 1CCh. 6 - Prob. 2CCh. 6 - Prob. 3.1CCh. 6 - Prob. 3.2CCh. 6 - Prob. 3.3CCh. 6 - Prob. 3.4CCh. 6 - Prob. 3.5CCh. 6 - Prob. 3.6C
Knowledge Booster
Learn more about
Need a deep-dive on the concept behind this application? Look no further. Learn more about this topic, operations-management and related others by exploring similar questions and additional content below.Similar questions
- how have idividual objectives led to the current situation at TeraCog? what should Emaa do?arrow_forwardCan you write me an email about addressing an issue to mentor my supervisor the right way of deligating operations dutiesarrow_forwardCan you right me an email about addressing an issue to mentor the right why of deligating operations dutiesarrow_forward
- Define delegation. Discuss in detail the four reasons why managers do delegation? Also statethe four main types of delegation.arrow_forwardB) Going forward, is Lean/JIT worth the risks? Should it be embraced (why?), abandoned (if so, why & what are the costs), or modified (how?) Do you think Lean works or not? Please write a complete response (about 1-2 paragraphs each part). Each team member should discuss and contribute so that the group agrees on their joint response. Please help each other and build upon and/or challenge others' points (in a respectful way!)arrow_forwardDiscuss the principle reasons that employee benefits have risen over the past 20 years, along with how best an organization can provide employees with a fair wage yet also provide some level of employee benefit coverage.arrow_forward
- Please assist with the Case Study below as attached. Read the case study below and answer the questions that follow. The Importance of the Planning Phase to Project Success. Traditional wisdom is that planning and analysis are very important and the more there is in a project, the more successful the project will be. Time spent on these activities will reduce risk and increase project success. On the other hand, inadequate analysis and planning will lead to a failed project. If poor planning has led to failed projects, then perhaps billions of dollars have been lost. But how much is too much? “Light weight” project management techniques such as agile are gaining popularity. Part of their ethos is that less initial planning is better and an evolutionary process is more efficient. QUESTION 1 The article above states: “Traditional wisdom is that planning and analysis are very important and the more there is in a project, the more successful the project will be”. Describe FIVE (5) ways…arrow_forwardOn a daily basis, the van is dispatched from Maplewood Hospital to pickup blood and platelet donations made at its local donation centers. The distances in miles between all locations may be found in the table below. Click the icon to view mileage data for Vampire Van. a. The van travels from the Hospital (A) to (B) to (C) to (D) to (E) and then returns to the Hospital (A). What is the total number of miles that the van must travel using this route? Route ABCDEA requires a total distance of 20.4 miles. (Enter your response rounded to one decimal place.) b. Using Maplewood Hospital as the beginning location, create a route using the Nearest Neighbor heuristic. What is the total number of miles that the van must travel using this route? The new route is A A and requires a total distance of miles. (Enter your response rounded to one decimal place.) More Info Maplewood City Center Westbrook Hospital (A) Donation Site (B) Donation Site (C) Municipal Park Donation Site (D) Valley Hills…arrow_forwardView the video Noodles & Company (8.28minutes, Ctrl + Click on the link); what are your key takeaways (tie to one or more of the topics discussed in Chapters 7 & 7S – service process design, type of job design, methods analysis, work methods, job design, learning curve effect, etc.) after watching this video. https://media.gaspar.mheducation.com/GASPARPlayer/play.html?id=E5i8OKgpqhwywhgFmpp1bmM Note: As a rough guideline, please try to keep the written submission to one or two paragraphs. 2) Leland, the job analyst at Zevo Toys, wanted to perform a time study on the assembling of toys. He observed one of the workers, Magorium, for five hours. During that time, Magorium assembled 250 toys. Leland rated Magorium as performing at 110 percent. The allowance for rest, personal time, etc. at Zevo Toys is 12 percent. a) Compute the normal time for the job. b) Compute the standard time for the job. Note: You could work out the problem by hand or use excel; in chapter 7,…arrow_forward
- 1) Noodles & Company View the video Noodles & Company (8.28minutes, Ctrl + Click on the link); what are your key takeaways (tie to one or more of the topics discussed in Chapters 7 & 7S – service process design, type of job design, methods analysis, work methods, job design, learning curve effect, etc.) after watching this video. https://media.gaspar.mheducation.com/GASPARPlayer/play.html?id=E5i8OKgpqhwywhgFmpp1bmM Note: As a rough guideline, please try to keep the written submission to one or two paragraphs. 2) Leland, the job analyst at Zevo Toys, wanted to perform a time study on the assembling of toys. He observed one of the workers, Magorium, for five hours. During that time, Magorium assembled 250 toys. Leland rated Magorium as performing at 110 percent. The allowance for rest, personal time, etc. at Zevo Toys is 12 percent. a) Compute the normal time for the job. b) Compute the standard time for the job. Note: You could work out the problem by hand or use…arrow_forwardAn investigation of career development opportunities and job satisfaction atarrow_forwardThe Donald Fertilizer Company produces industrial chemical fertilizers. The projected manufacturing requirements (in gallons) for the next four quarters are 90,000, 90,000, 60,000, and 140,000 respectively. A level workforce is desired, relying only on anticipation inventory as a supply option. Stockouts and backorders are to be avoided, as are overtime and undertime. a. Determine the quarterly production rate required to meet total demand for the year, and minimize the anticipation inventory that would be left over at the end of the year. Beginning inventory is 0. The quarterly production rate is 95000 gallons. (Enter your response as an integer.) b. Specify the anticipation inventory that will be produced. (Enter your responses as an integers.) Quarter Anticipation inventory (gallons) 1 5000 2 10000 3 4 45000 c. Suppose that the requirements (in gallons) for the next four quarters are revised to 140,000, 60,000, 90,000, and 90,000 respectively. If total demand is the same, what level…arrow_forward
arrow_back_ios
SEE MORE QUESTIONS
arrow_forward_ios
Recommended textbooks for you
- Practical Management ScienceOperations ManagementISBN:9781337406659Author:WINSTON, Wayne L.Publisher:Cengage,
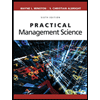
Practical Management Science
Operations Management
ISBN:9781337406659
Author:WINSTON, Wayne L.
Publisher:Cengage,