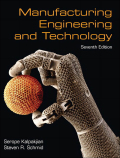
EBK MANUFACTURING ENGINEERING & TECHNOL
7th Edition
ISBN: 8220100793431
Author: KALPAKJIAN
Publisher: PEARSON
expand_more
expand_more
format_list_bulleted
Concept explainers
Textbook Question
Chapter 14, Problem 32QTP
Take two solid, cylindrical specimens of equal diameter, but different heights, and compress them (frictionless) to the same percent reduction in height. Show that the final diameters will be the same.
Expert Solution & Answer

Want to see the full answer?
Check out a sample textbook solution
Students have asked these similar questions
For hot rolling processes, show that the average strain rate can be given as:
=
(1+5)√RdIn(+1)
: +0
usão
العنوان
on
to
A vertical true centrifugal casting process is used to produce bushings that are 250 mm
long and 200 mm in outside diameter. If the rotational speed during solidification is 500
rev/min, determine the inside radii at the top and bottom of the bushing if R-2R. Take:
-9.81 mis
۲/۱
ostrar
: +0
العنوان
use only
In conventional drawing of a stainless steel wire, the original diameter D.-3mm, the area
reduction at each die stand r-40%, and the proposed final diameter D.-0.5mm, how many
die stands are required to complete this process.
он
Chapter 14 Solutions
EBK MANUFACTURING ENGINEERING & TECHNOL
Ch. 14 - What is the difference between cold, warm, and hot...Ch. 14 - Explain the difference between open-die and...Ch. 14 - Explain the difference between fullering, edging,...Ch. 14 - What is flash? What is its function?Ch. 14 - Why is the intermediate shape of a part important...Ch. 14 - Describe the features of a typical forging die.Ch. 14 - Explain what is meant by load limited, energy...Ch. 14 - What type of parts can be produced by rotary...Ch. 14 - Why is hubbing an attractive alternative to...Ch. 14 - What is the difference between piercing and...
Ch. 14 - What is a hammer? What are the different kinds of...Ch. 14 - Why is there barreling in upsetting?Ch. 14 - What are the advantages and disadvantages of...Ch. 14 - Why are draft angles required in forging dies?Ch. 14 - Is a mandrel needed in swaging?Ch. 14 - Describe and explain the factors that influence...Ch. 14 - How can you tell whether a certain part is forged...Ch. 14 - Identify casting design rules, described in...Ch. 14 - Describe the factors involved in precision...Ch. 14 - Why is control of the volume of the blank...Ch. 14 - Why are there so many types of forging machines...Ch. 14 - What are the advantages and limitations of cogging...Ch. 14 - What are the advantages and limitations of using...Ch. 14 - Review Fig. 14.6e and explain why internal draft...Ch. 14 - Comment on your observations regarding the...Ch. 14 - Describe your observations concerning the control...Ch. 14 - Prob. 27QLPCh. 14 - Describe the difficulties involved in defining the...Ch. 14 - Describe the advantages of servo presses for...Ch. 14 - List the general recommendations you would make...Ch. 14 - Which would you recommend, (a) hot forging and...Ch. 14 - Take two solid, cylindrical specimens of equal...Ch. 14 - Calculate the room-temperature forging force for a...Ch. 14 - Using Eq. (14.2), estimate the forging force for...Ch. 14 - To what thickness can a solid cylinder of 1020...Ch. 14 - In Example 14.1, calculate the forging force,...Ch. 14 - Using Eq. (14.1), make a plot of the forging...Ch. 14 - How would you go about estimating the punch force...Ch. 14 - A mechanical press is powered by a 30-hp motor and...Ch. 14 - A solid cylindrical specimen, made of a perfectly...Ch. 14 - Devise an experimental method whereby you can...Ch. 14 - Assume that you represent the forging industry and...Ch. 14 - Figure P14.44 shows a round impression-die forging...Ch. 14 - Prob. 45SDPCh. 14 - Prob. 46SDPCh. 14 - Review the sequence of operations in the...Ch. 14 - Prob. 48SDPCh. 14 - Discuss the possible environmental concerns...Ch. 14 - List the advantages and disadvantages in using a...
Knowledge Booster
Learn more about
Need a deep-dive on the concept behind this application? Look no further. Learn more about this topic, mechanical-engineering and related others by exploring similar questions and additional content below.Similar questions
- In non-continuous dieless drawing process for copper tube as shown in Fig. (1), take the following data: Do-20mm, to=3mm, D=12mm, ti/to=0.6 and vo-15mm/s. Calculate: (1) area reduction RA, (2) drawing velocity v. Knowing that: t₁: final thickness D₁ V. Fig. (1) Darrow_forwardA vertical true centrifugal casting process is used to produce bushings that are 250 mm long and 200 mm in outside diameter. If the rotational speed during solidification is 500 rev/min, determine the inside radii at the top and bottom of the bushing if R-2Rb. Take: 8-9.81 m/sarrow_forwardIn conventional drawing of a stainless steel wire, the original diameter D.-3mm, the area reduction at each die stand r-40%, and the proposed final diameter D₁-0.5mm, how many die stands are required to complete this process.arrow_forward
- A vertical true centrifugal casting process is used to produce bushings that are 250 mm long and 200 mm in outside diameter. If the rotational speed during solidification is 500 rev/min, determine the inside radii at the top and bottom of the bushing if R-2Rb. Take: 8-9.81 m/sarrow_forwardIn non-continuous dieless drawing process for copper tube as shown in Fig. (1), take the following data: Do-20mm, to=3mm, D=12mm, ti/to=0.6 and vo-15mm/s. Calculate: (1) area reduction RA, (2) drawing velocity v. Knowing that: t₁: final thickness D₁ V. Fig. (1) Darrow_forward-6- 8 من 8 Mechanical vibration HW-prob-1 lecture 8 By: Lecturer Mohammed O. attea The 8-lb body is released from rest a distance xo to the right of the equilibrium position. Determine the displacement x as a function of time t, where t = 0 is the time of release. c=2.5 lb-sec/ft wwwww k-3 lb/in. 8 lb Prob. -2 Find the value of (c) if the system is critically damping. Prob-3 Find Meq and Ceq at point B, Drive eq. of motion for the system below. Ш H -7~ + 目 T T & T тт +arrow_forward
- Q For the following plan of building foundation, Determine immediate settlement at points (A) and (B) knowing that: E,-25MPa, u=0.3, Depth of foundation (D) =1m, Depth of layer below base level of foundation (H)=10m. 3m 2m 100kPa A 2m 150kPa 5m 200kPa Barrow_forwardW PE 2 43 R² 80 + 10 + kr³ Ø8=0 +0 R²+J+ kr200 R² + J-) + k r² = 0 kr20 kr20 8+ W₁ = = 0 R²+1) R²+J+) 4 lec 8.pdf Mechanical vibration lecture 6 By: Lecturer Mohammed C. Attea HW1 (Energy method) Find equation of motion and natural frequency for the system shown in fig. by energy method. m. Jo 000 HW2// For the system Fig below find 1-F.B.D 2Eq.of motion 8 wn 4-0 (1) -5- marrow_forwardThe hose supplying the cylinder operating the bucket of a large excavator has fluid at 1000 psi flowing at 5 gpm. What is theavailable power in the line?arrow_forward
- Q For the following plan of building foundation, Determine immediate settlement at points (A) and (B) knowing that: E,-25MPa, u=0.3, Depth of foundation (D) =1m, Depth of layer below base level of foundation (H)=10m. 3m 2m 100kPa A 2m 150kPa 5m 200kPa Barrow_forwardGiven the following data for crack rocker mechanism. If θ2 = 4π/3 and ω2 = 1 rad/s, Determine all possible values of ω4 and ω3 analytically. The lengths of links are a = 2, b = 8, c = 7 and d = 9 in cm.arrow_forwardQ6] (20 Marks) Select the most suitable choice for the following statements: modo digi -1A 10 af5 1 -The copper-based alloy which is responded to age hardening is a) copper-nickel b) aluminum bronze c) copper - beryllium d) brass besincaluy 2- Highly elastic polymers may experience elongations to greater than.... b) 500% bromsia-P c) 1000%. d) 1200% 15m or -2 a)100% 3- The cooling rate of quenching the steel in saltwater will be ......the cooling rate of quenching ir c) faster than sold) none of them a) slower than 4- Adding of a) Cr b) the same as ...... Will lead to stabilize the b) Mo 10 austenite in steel. c) Nimble avolls 1d) Sized loloin nl 5- The adjacent linear chains of crosslinked polymers are joined one to another at various positic DIR... by.........bonds c) covalent noisqo gd) ionic lg 120M 6- For the ceramic with coordination number 6 the cation to anion radius ratio will be a) Van der Waals a) 0.155-0.225 a) linear b) hydrogen (b) 0.225-0.414 c) 0.414 0.732 ..polymers.…arrow_forward
arrow_back_ios
SEE MORE QUESTIONS
arrow_forward_ios
Recommended textbooks for you
- Elements Of ElectromagneticsMechanical EngineeringISBN:9780190698614Author:Sadiku, Matthew N. O.Publisher:Oxford University PressMechanics of Materials (10th Edition)Mechanical EngineeringISBN:9780134319650Author:Russell C. HibbelerPublisher:PEARSONThermodynamics: An Engineering ApproachMechanical EngineeringISBN:9781259822674Author:Yunus A. Cengel Dr., Michael A. BolesPublisher:McGraw-Hill Education
- Control Systems EngineeringMechanical EngineeringISBN:9781118170519Author:Norman S. NisePublisher:WILEYMechanics of Materials (MindTap Course List)Mechanical EngineeringISBN:9781337093347Author:Barry J. Goodno, James M. GerePublisher:Cengage LearningEngineering Mechanics: StaticsMechanical EngineeringISBN:9781118807330Author:James L. Meriam, L. G. Kraige, J. N. BoltonPublisher:WILEY
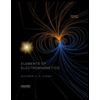
Elements Of Electromagnetics
Mechanical Engineering
ISBN:9780190698614
Author:Sadiku, Matthew N. O.
Publisher:Oxford University Press
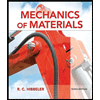
Mechanics of Materials (10th Edition)
Mechanical Engineering
ISBN:9780134319650
Author:Russell C. Hibbeler
Publisher:PEARSON
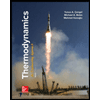
Thermodynamics: An Engineering Approach
Mechanical Engineering
ISBN:9781259822674
Author:Yunus A. Cengel Dr., Michael A. Boles
Publisher:McGraw-Hill Education
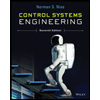
Control Systems Engineering
Mechanical Engineering
ISBN:9781118170519
Author:Norman S. Nise
Publisher:WILEY
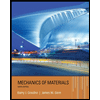
Mechanics of Materials (MindTap Course List)
Mechanical Engineering
ISBN:9781337093347
Author:Barry J. Goodno, James M. Gere
Publisher:Cengage Learning
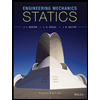
Engineering Mechanics: Statics
Mechanical Engineering
ISBN:9781118807330
Author:James L. Meriam, L. G. Kraige, J. N. Bolton
Publisher:WILEY
Types of Manufacturing Process | Manufacturing Processes; Author: Magic Marks;https://www.youtube.com/watch?v=koULXptaBTs;License: Standard Youtube License