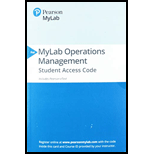
Concept explainers
a)
To develop: A net requirements plan for items.
Introduction:
Net requirements plan:
The net requirements plan is the plan which is established on the gross requirements plan formed by deducting the stock on and the
a)

Explanation of Solution
Given information:
Product structure:
Period | 8 | 9 | 10 | 11 | 12 |
Gross requirements: A | 100 | 50 | 150 | ||
Gross requirements: H | 100 | 50 |
Inventory and lead time:
Item | A | B | C | D | E | F | G | H | J | K |
Lead time | 1 | 2 | 2 | 1 | 2 | 2 | 1 | 1 | 2 | 2 |
On hand | 0 | 100 | 50 | 50 | 75 | 75 | 75 | 0 | 100 | 100 |
- 1 assembly for each item
Item A:
Week | ||||||||||||
Item A | 1 | 2 | 3 | 4 | 5 | 6 | 7 | 8 | 9 | 10 | 11 | 12 |
Gross requirements | 100 | 50 | 150 | |||||||||
Scheduled receipt | ||||||||||||
On hand (0) | 0 | 0 | 0 | |||||||||
Net requirement | 100 | 50 | 150 | |||||||||
Planned order receipt | 100 | 50 | 150 | |||||||||
Planned order release | 100 | 50 | 150 |
Week 8:
The gross requirement is 100 (1 assembly). The on hand inventory is 0. Hence, the net requirement is 100. The lead time is 1 week. Therefore, the planned order release will be 100 in week 7 which will be the planned order receipt in week 8.
Week 10:
The gross requirement is 50 (1 assembly). The on hand inventory is 0. Hence, the net requirement is 50. The lead time is 1 week. Therefore, the planned order release will be 50 in week 9 which will be the planned order receipt in week 10.
Week 12:
The gross requirement is 150 (1 assembly). The on hand inventory is 0. Hence, the net requirement is 150. The lead time is 1 week. Therefore, the planned order release will be 150 in week 11 which will be the planned order receipt in week 12.
Item H:
Week | ||||||||||||
Item H | 1 | 2 | 3 | 4 | 5 | 6 | 7 | 8 | 9 | 10 | 11 | 12 |
Gross requirements | 100 | 50 | ||||||||||
Scheduled receipt | ||||||||||||
On hand (0) | 0 | 0 | ||||||||||
Net requirement | 100 | 50 | ||||||||||
Planned order receipt | 100 | 50 | ||||||||||
Planned order release | 100 | 50 |
Week 9:
The gross requirement is 100 (1 assembly). The on hand inventory is 0. Hence, the net requirement is 1000. The lead time is 1 week. Therefore, the planned order release will be 100 in week 8 which will be the planned order receipt in week 10.
Week 11:
The gross requirement is 50 (1 assembly). The on hand inventory is 0. Hence, the net requirement is 50. The lead time is 1 week. Therefore, the planned order release will be 50 in week 9 which will be the planned order receipt in week 11.
Item B:
Week | ||||||||||||
Item B | 1 | 2 | 3 | 4 | 5 | 6 | 7 | 8 | 9 | 10 | 11 | 12 |
Gross requirements | 100 | 50 | 150 | |||||||||
Scheduled receipt | ||||||||||||
On hand (100) | 100 | 0 | 0 | |||||||||
Net requirement | 0 | 50 | 150 | |||||||||
Planned order receipt | 50 | 150 | ||||||||||
Planned order release | 50 | 150 |
Week 7:
The gross requirement is 100 (1 assembly) derived from planned order release of A. The on hand inventory is 100. Hence, the net requirement is 0. Therefore, there will be no planned order release.
Week 9:
The gross requirement is 50 (1 assembly) derived from the planned order release of A. The on hand inventory is 0. Hence, the net requirement is 50. The lead time is 2 weeks. Therefore, the planned order release will be 50 in week 7 which will be the planned order receipt in week 9.
Week 11:
The gross requirement is 150 (1 assembly) derived from planned order release of A. The on hand inventory is 0. Hence, the net requirement is 150. The lead time is 2 weeks. Therefore, the planned order release will be 150 in week 9 which will be the planned order receipt in week 11.
Item C:
Week | ||||||||||||
Item C | 1 | 2 | 3 | 4 | 5 | 6 | 7 | 8 | 9 | 10 | 11 | 12 |
Gross requirements | 100 | 100 | 50 | 50 | 150 | |||||||
Scheduled receipt | ||||||||||||
On hand (50) | 50 | 0 | 0 | 0 | 0 | |||||||
Net requirement | 50 | 100 | 50 | 50 | 150 | |||||||
Planned order receipt | 50 | 100 | 50 | 50 | 150 | |||||||
Planned order release | 50 | 100 | 50 | 50 | 150 |
Week 7:
The gross requirement is 100 (1 assembly) derived from planned order release of A. The on hand inventory is 50. Hence, the net requirement is 50. The lead time is 2 weeks. Therefore, the planned order release will be 50 in week 5 which will be the planned order receipt in week 7.
Week 8:
The gross requirement is 100 (1 assembly) derived from planned order release of H. The on hand inventory is 0. Hence, the net requirement is 100. The lead time is 2 weeks. Therefore, the planned order release will be 100 in week 6 which will be the planned order receipt in week 8.
Week 9:
The gross requirement is 50 (1 assembly) derived from the planned order release of A. The on hand inventory is 0. Hence, the net requirement is 50. The lead time is 2 weeks. Therefore, the planned order release will be 50 in week 7 which will be the planned order receipt in week 9.
Week 10:
The gross requirement is 50 (1 assembly) derived from planned order release of H. The on hand inventory is 0. Hence, the net requirement is 50. The lead time is 2 weeks. Therefore, the planned order release will be 50 in week 8 which will be the planned order receipt in week 10.
Week 11:
The gross requirement is 150 (1 assembly) derived from planned order release of A. The on hand inventory is 0. Hence, the net requirement is 150. The lead time is 2 weeks. Therefore, the planned order release will be 150 in week 9 which will be the planned order receipt in week 11.
Item J:
Week | ||||||||||||
Item J | 1 | 2 | 3 | 4 | 5 | 6 | 7 | 8 | 9 | 10 | 11 | 12 |
Gross requirements | 100 | 50 | ||||||||||
Scheduled receipt | ||||||||||||
On hand (100) | 100 | 0 | ||||||||||
Net requirement | 0 | 50 | ||||||||||
Planned order receipt | 0 | 50 | ||||||||||
Planned order release | 50 |
Week 8:
The gross requirement is 100 (1 assembly) derived from planned order release of H. The on hand inventory is 100. Hence, the net requirement is 0. Therefore, there will be no planned order release.
Week 10:
The gross requirement is 50 (1 assembly) derived from the planned order release of H. The on hand inventory is 0. Hence, the net requirement is 50. The lead time is 2 weeks. Therefore, the planned order release will be 50 in week 8 which will be the planned order receipt in week 10.
Item K:
Week | ||||||||||||
Item K | 1 | 2 | 3 | 4 | 5 | 6 | 7 | 8 | 9 | 10 | 11 | 12 |
Gross requirements | 100 | 50 | ||||||||||
Scheduled receipt | ||||||||||||
On hand (100) | 100 | 0 | ||||||||||
Net requirement | 0 | 50 | ||||||||||
Planned order receipt | 50 | |||||||||||
Planned order release | 50 |
Week 8:
The gross requirement is 100 (1 assembly) derived from planned order release of H. The on hand inventory is 100. Hence, the net requirement is 0. Therefore, there will be no planned order release.
Week 10:
The gross requirement is 50 (1 assembly) derived from the planned order release of H. The on hand inventory is 0. Hence, the net requirement is 50. The lead time is 2 weeks. Therefore, the planned order release will be 50 in week 8 which will be the planned order receipt in week 10.
Item D:
Week | ||||||||||||
Item D | 1 | 2 | 3 | 4 | 5 | 6 | 7 | 8 | 9 | 10 | 11 | 12 |
Gross requirements | 50 | 150 | ||||||||||
Scheduled receipt | ||||||||||||
On hand (50) | 50 | 0 | ||||||||||
Net requirement | 150 | |||||||||||
Planned order receipt | 150 | |||||||||||
Planned order release | 150 |
Week 7:
The gross requirement is 50 (1 assembly) derived from planned order release of B. The on hand inventory is 500. Hence, the net requirement is 0. Therefore, there will be no planned order release.
Week 9:
The gross requirement is 150 (1 assembly) derived from the planned order release of B. The on hand inventory is 0. Hence, the net requirement is 150. The lead time is 1 week. Therefore, the planned order release will be 150 in week 8 which will be the planned order receipt in week 9.
Item E:
Week | ||||||||||||
Item E | 1 | 2 | 3 | 4 | 5 | 6 | 7 | 8 | 9 | 10 | 11 | 12 |
Gross requirements | 50 | 100 | 150 | |||||||||
Scheduled receipt | ||||||||||||
On hand (75) | 75 | 25 | 0 | |||||||||
Net requirement | 0 | 75 | 150 | |||||||||
Planned order receipt | 75 | 150 | ||||||||||
Planned order release | 75 | 150 |
Week 7:
The gross requirement is 50 (1 assembly) derived from planned order release of B. The on hand inventory is 75. Hence, the net requirement is 0. Therefore, there will be no planned order release.
Week 8:
The gross requirement is 100 (1 assembly) derived from the planned order release of J and K. The on hand inventory is 25. Hence, the net requirement is 75. The lead time is 2 weeks. Therefore, the planned order release will be 75 in week 6 which will be the planned order receipt in week 8.
Week 9:
The gross requirement is 150 (1 assembly) derived from planned order release of B. The on hand inventory is 0. Hence, the net requirement is 150. The lead time is 2 weeks. Therefore, the planned order release will be 150 in week 7 which will be the planned order receipt in week 9.
Item F:
Week | ||||||||||||
Item F | 1 | 2 | 3 | 4 | 5 | 6 | 7 | 8 | 9 | 10 | 11 | 12 |
Gross requirements | 50 | 100 | 50 | 100 | 150 | |||||||
Scheduled receipt | ||||||||||||
On hand (75) | 75 | 25 | 0 | 0 | 0 | |||||||
Net requirement | 0 | 75 | 50 | 100 | 150 | |||||||
Planned order receipt | 75 | 50 | 100 | 150 | ||||||||
Planned order release | 75 | 50 | 100 | 150 |
Week 5:
The gross requirement is 50 (1 assembly) derived from planned order release of C. The on hand inventory is 75. Hence, the net requirement is 0. Therefore, there will be no planned order release.
Week 6:
The gross requirement is 100 (1 assembly) derived from planned order release of C. The on hand inventory is 25. Hence, the net requirement is 75. The lead time is 2 weeks. Therefore, the planned order release will be 75 in week 4 which will be the planned order receipt in week 6.
Week 7:
The gross requirement is 50 (1 assembly) derived from the planned order release of C. The on hand inventory is 0. Hence, the net requirement is 50. The lead time is 2 weeks. Therefore, the planned order release will be 50 in week 5 which will be the planned order receipt in week 7.
Week 8:
The gross requirement is 100 (1 assembly) derived from planned order release of C and J. The on hand inventory is 0. Hence, the net requirement is 100. The lead time is 2 weeks. Therefore, the planned order release will be 100 in week 6 which will be the planned order receipt in week 8.
Week 9:
The gross requirement is 150 (1 assembly) derived from planned order release of C. The on hand inventory is 0. Hence, the net requirement is 150. The lead time is 2 weeks. Therefore, the planned order release will be 150 in week 7 which will be the planned order receipt in week 9.
Item G:
Week | ||||||||||||
Item G | 1 | 2 | 3 | 4 | 5 | 6 | 7 | 8 | 9 | 10 | 11 | 12 |
Gross requirements | 50 | 100 | 50 | 100 | 150 | |||||||
Scheduled receipt | ||||||||||||
On hand (75) | 75 | 25 | 0 | 0 | 0 | |||||||
Net requirement | 0 | 75 | 50 | 100 | 150 | |||||||
Planned order receipt | 75 | 50 | 100 | 150 | ||||||||
Planned order release | 75 | 50 | 100 | 150 |
Week 5:
The gross requirement is 50 (1 assembly) derived from planned order release of C. The on hand inventory is 75. Hence, the net requirement is 0. Therefore, there will be no planned order release.
Week 6:
The gross requirement is 100 (1 assembly) derived from planned order release of C. The on hand inventory is 25. Hence, the net requirement is 75. The lead time is 1 week. Therefore, the planned order release will be 75 in week 5 which will be the planned order receipt in week 6.
Week 7:
The gross requirement is 50 (1 assembly) derived from the planned order release of C. The on hand inventory is 0. Hence, the net requirement is 50. The lead time is 1 week. Therefore, the planned order release will be 50 in week 6 which will be the planned order receipt in week 7.
Week 8:
The gross requirement is 100 (1 assembly) derived from planned order release of C and K. The on hand inventory is 0. Hence, the net requirement is 100. The lead time is 1 week. Therefore, the planned order release will be 100 in week 7 which will be the planned order receipt in week 8.
Week 9:
The gross requirement is 150 (1 assembly) derived from planned order release of C. The on hand inventory is 0. Hence, the net requirement is 150. The lead time is 1 week. Therefore, the planned order release will be 150 in week 8 which will be the planned order receipt in week 9.
b)
To develop: A net requirements plan for all items.
Introduction:
Net requirements plan:
The net requirements plan is the plan which is established on the gross requirements plan formed by deducting the stock on and the scheduled receipts. If the total requirement is below the safety stock levels, a planned order is made based on the given lot sizing technique.
b)

Explanation of Solution
Given information:
Product structure:
Period | 8 | 9 | 10 | 11 | 12 |
Gross requirements: A | 100 | 50 | 150 | ||
Gross requirements: H | 100 | 50 |
Inventory and lead time:
Item | A | B | C | D | E | F | G | H | J | K |
Lead time | 1 | 2 | 2 | 1 | 2 | 2 | 1 | 1 | 2 | 2 |
On hand | 0 | 100 | 50 | 50 | 75 | 75 | 75 | 0 | 100 | 100 |
- 1 assembly for each item
- 2 assemblies for item B, C and F.
Item A:
Week | ||||||||||||
Item A | 1 | 2 | 3 | 4 | 5 | 6 | 7 | 8 | 9 | 10 | 11 | 12 |
Gross requirements | 100 | 50 | 150 | |||||||||
Scheduled receipt | ||||||||||||
On hand (0) | 0 | 0 | 0 | |||||||||
Net requirement | 100 | 50 | 150 | |||||||||
Planned order receipt | 100 | 50 | 150 | |||||||||
Planned order release | 100 | 50 | 150 |
Week 8:
The gross requirement is 100 (1 assembly). The on hand inventory is 0. Hence, the net requirement is 100. The lead time is 1 week. Therefore, the planned order release will be 100 in week 7 which will be the planned order receipt in week 8.
Week 10:
The gross requirement is 50 (1 assembly). The on hand inventory is 0. Hence, the net requirement is 50. The lead time is 1 week. Therefore, the planned order release will be 50 in week 9 which will be the planned order receipt in week 10.
Week 12:
The gross requirement is 150 (1 assembly). The on hand inventory is 0. Hence, the net requirement is 150. The lead time is 1 week. Therefore, the planned order release will be 150 in week 11 which will be the planned order receipt in week 12.
Item H:
Week | ||||||||||||
Item H | 1 | 2 | 3 | 4 | 5 | 6 | 7 | 8 | 9 | 10 | 11 | 12 |
Gross requirements | 100 | 50 | ||||||||||
Scheduled receipt | ||||||||||||
On hand (0) | 0 | 0 | ||||||||||
Net requirement | 100 | 50 | ||||||||||
Planned order receipt | 100 | 50 | ||||||||||
Planned order release | 100 | 50 |
Week 9:
The gross requirement is 100 (1 assembly). The on hand inventory is 0. Hence, the net requirement is 1000. The lead time is 1 week. Therefore, the planned order release will be 100 in week 8 which will be the planned order receipt in week 10.
Week 11:
The gross requirement is 50 (1 assembly). The on hand inventory is 0. Hence, the net requirement is 50. The lead time is 1 week. Therefore, the planned order release will be 50 in week 9 which will be the planned order receipt in week 11.
Item B:
Week | ||||||||||||
Item B | 1 | 2 | 3 | 4 | 5 | 6 | 7 | 8 | 9 | 10 | 11 | 12 |
Gross requirements | 200 | 100 | 300 | |||||||||
Scheduled receipt | ||||||||||||
On hand (100) | 100 | 0 | 0 | |||||||||
Net requirement | 100 | 100 | 300 | |||||||||
Planned order receipt | 100 | 100 | 300 | |||||||||
Planned order release | 100 | 100 | 300 |
Week 7:
The gross requirement is 200 (2 assembly) derived from planned order release of A. The on hand inventory is 100. Hence, the net requirement is 100. Therefore, the planned order release will be 100 in week 5 which will be the planned order receipt in week 7.
Week 9:
The gross requirement is 100 (2 assembly) derived from the planned order release of A. The on hand inventory is 0. Hence, the net requirement is 100. The lead time is 2 weeks. Therefore, the planned order release will be 100 in week 7 which will be the planned order receipt in week 9.
Week 11:
The gross requirement is 300 (2 assembly) derived from planned order release of A. The on hand inventory is 0. Hence, the net requirement is 300. The lead time is 2 weeks. Therefore, the planned order release will be 300 in week 9 which will be the planned order receipt in week 11.
Item C:
Week | ||||||||||||
Item C | 1 | 2 | 3 | 4 | 5 | 6 | 7 | 8 | 9 | 10 | 11 | 12 |
Gross requirements | 200 | 200 | 100 | 100 | 300 | |||||||
Scheduled receipt | ||||||||||||
On hand (50) | 50 | 0 | 0 | 0 | 0 | |||||||
Net requirement | 150 | 200 | 100 | 100 | 300 | |||||||
Planned order receipt | 150 | 200 | 100 | 100 | 300 | |||||||
Planned order release | 150 | 200 | 100 | 100 | 300 |
Week 7:
The gross requirement is 200 (2 assembly) derived from planned order release of A. The on hand inventory is 50. Hence, the net requirement is 150. The lead time is 2 weeks. Therefore, the planned order release will be 150 in week 5 which will be the planned order receipt in week 7.
Week 8:
The gross requirement is 200 (2 assembly) derived from planned order release of H. The on hand inventory is 0. Hence, the net requirement is 200. The lead time is 2 weeks. Therefore, the planned order release will be 200 in week 6 which will be the planned order receipt in week 8.
Week 9:
The gross requirement is 100 (2 assembly) derived from the planned order release of A. The on hand inventory is 0. Hence, the net requirement is 100. The lead time is 2 weeks. Therefore, the planned order release will be 100 in week 7 which will be the planned order receipt in week 9.
Week 10:
The gross requirement is 100 (2 assembly) derived from planned order release of H. The on hand inventory is 0. Hence, the net requirement is 100. The lead time is 2 weeks. Therefore, the planned order release will be 100 in week 8 which will be the planned order receipt in week 10.
Week 11:
The gross requirement is 300 (2 assembly) derived from planned order release of A. The on hand inventory is 0. Hence, the net requirement is 300. The lead time is 2 weeks. Therefore, the planned order release will be 300 in week 9 which will be the planned order receipt in week 11.
Item J:
Week | ||||||||||||
Item J | 1 | 2 | 3 | 4 | 5 | 6 | 7 | 8 | 9 | 10 | 11 | 12 |
Gross requirements | 100 | 50 | ||||||||||
Scheduled receipt | ||||||||||||
On hand (100) | 100 | 0 | ||||||||||
Net requirement | 0 | 50 | ||||||||||
Planned order receipt | 0 | 50 | ||||||||||
Planned order release | 50 |
Week 8:
The gross requirement is 100 (1 assembly) derived from planned order release of H. The on hand inventory is 100. Hence, the net requirement is 0. Therefore, there will be no planned order release.
Week 10:
The gross requirement is 50 (1 assembly) derived from the planned order release of H. The on hand inventory is 0. Hence, the net requirement is 50. The lead time is 2 weeks. Therefore, the planned order release will be 50 in week 8 which will be the planned order receipt in week 10.
Item K:
Week | ||||||||||||
Item K | 1 | 2 | 3 | 4 | 5 | 6 | 7 | 8 | 9 | 10 | 11 | 12 |
Gross requirements | 100 | 50 | ||||||||||
Scheduled receipt | ||||||||||||
On hand (100) | 100 | 0 | ||||||||||
Net requirement | 0 | 50 | ||||||||||
Planned order receipt | 50 | |||||||||||
Planned order release | 50 |
Week 8:
The gross requirement is 100 (1 assembly) derived from planned order release of H. The on hand inventory is 100. Hence, the net requirement is 0. Therefore, there will be no planned order release.
Week 10:
The gross requirement is 50 (1 assembly) derived from the planned order release of H. The on hand inventory is 0. Hence, the net requirement is 50. The lead time is 2 weeks. Therefore, the planned order release will be 50 in week 8 which will be the planned order receipt in week 10.
Item D:
Week | ||||||||||||
Item D | 1 | 2 | 3 | 4 | 5 | 6 | 7 | 8 | 9 | 10 | 11 | 12 |
Gross requirements | 100 | 100 | 300 | |||||||||
Scheduled receipt | ||||||||||||
On hand (50) | 50 | 0 | 0 | |||||||||
Net requirement | 50 | 100 | 300 | |||||||||
Planned order receipt | 50 | 100 | 300 | |||||||||
Planned order release | 50 | 100 | 300 |
Week 6:
The gross requirement is 100 (1 assembly) derived from the planned order release of B. The on hand inventory is 50. Hence, the net requirement is 50. The lead time is 1 week. Therefore, the planned order release will be 50 in week 5 which will be the planned order receipt in week 6.
Week 8:
The gross requirement is 100 (1 assembly) derived from the planned order release of B. The on hand inventory is 0. Hence, the net requirement is 100. The lead time is 1 week. Therefore, the planned order release will be 100 in week 7 which will be the planned order receipt in week 8.
Week 8:
The gross requirement is 300 (1 assembly) derived from the planned order release of B. The on hand inventory is 0. Hence, the net requirement is 300. The lead time is 1 week. Therefore, the planned order release will be 300 in week 9 which will be the planned order receipt in week 10.
Item E:
Week | ||||||||||||
Item E | 1 | 2 | 3 | 4 | 5 | 6 | 7 | 8 | 9 | 10 | 11 | 12 |
Gross requirements | 100 | 100 | 100 | 300 | ||||||||
Scheduled receipt | ||||||||||||
On hand (75) | 75 | 0 | 0 | 0 | ||||||||
Net requirement | 25 | 100 | 100 | 300 | ||||||||
Planned order receipt | 25 | 100 | 100 | 300 | ||||||||
Planned order release | 25 | 100 | 100 | 300 |
Week 5:
The gross requirement is 100 (1 assembly) derived from planned order release of B. The on hand inventory is 75. Hence, the net requirement is 25. The lead time is 2 weeks. Therefore, the planned order release will be 25 in week 3 which will be the planned order receipt in week 5.
Week 7:
The gross requirement is 100 (1 assembly) derived from planned order release of B. The on hand inventory is 0. Hence, the net requirement is 100. The lead time is 2 weeks. Therefore, the planned order release will be 100 in week 5 which will be the planned order receipt in week 7.
Week 8:
The gross requirement is 100 (1 assembly) derived from the planned order release of J and K. The on hand inventory is 0. Hence, the net requirement is 100. The lead time is 2 weeks. Therefore, the planned order release will be 100 in week 6 which will be the planned order receipt in week 8.
Week 9:
The gross requirement is 300 (1 assembly) derived from planned order release of B. The on hand inventory is 0. Hence, the net requirement is 300. The lead time is 2 weeks. Therefore, the planned order release will be 300 in week 7 which will be the planned order receipt in week 9.
Item F:
Week | ||||||||||||
Item F | 1 | 2 | 3 | 4 | 5 | 6 | 7 | 8 | 9 | 10 | 11 | 12 |
Gross requirements | 300 | 400 | 200 | 300 | 600 | |||||||
Scheduled receipt | ||||||||||||
On hand (75) | 75 | 0 | 0 | 0 | 0 | |||||||
Net requirement | 225 | 400 | 200 | 300 | 600 | |||||||
Planned order receipt | 225 | 400 | 200 | 300 | 600 | |||||||
Planned order release | 225 | 400 | 200 | 300 | 600 |
Week 5:
The gross requirement is 300 (2 assembly) derived from planned order release of C. The on hand inventory is 75. Hence, the net requirement is 225. The lead time is 2 weeks. Therefore, the planned order release will be 225 in week 3 which will be the planned order receipt in week 5.
Week 6:
The gross requirement is 400 (2 assembly) derived from planned order release of C. The on hand inventory is 0. Hence, the net requirement is 400. The lead time is 2 weeks. Therefore, the planned order release will be 400 in week 4 which will be the planned order receipt in week 6.
Week 7:
The gross requirement is 200 (2 assembly) derived from the planned order release of C. The on hand inventory is 0. Hence, the net requirement is 200. The lead time is 2 weeks. Therefore, the planned order release will be 200 in week 5 which will be the planned order receipt in week 7.
Week 8:
The gross requirement is 300 (2 assembly) derived from planned order release of C and J. The on hand inventory is 0. Hence, the net requirement is 300. The lead time is 2 weeks. Therefore, the planned order release will be 300 in week 6 which will be the planned order receipt in week 8.
Week 9:
The gross requirement is 600 (2 assembly) derived from planned order release of C. The on hand inventory is 0. Hence, the net requirement is 600. The lead time is 2 weeks. Therefore, the planned order release will be 600 in week 7 which will be the planned order receipt in week 9.
Item G:
Week | ||||||||||||
Item G | 1 | 2 | 3 | 4 | 5 | 6 | 7 | 8 | 9 | 10 | 11 | 12 |
Gross requirements | 150 | 200 | 100 | 150 | 300 | |||||||
Scheduled receipt | ||||||||||||
On hand (75) | 75 | 0 | 0 | 0 | 0 | |||||||
Net requirement | 75 | 200 | 100 | 150 | 300 | |||||||
Planned order receipt | 75 | 200 | 100 | 150 | 300 | |||||||
Planned order release | 75 | 200 | 100 | 150 | 300 |
Week 5:
The gross requirement is 150 (1 assembly) derived from planned order release of C. The on hand inventory is 75. Hence, the net requirement is 75. The lead time is 1 week. Therefore, the planned order release will be 75 in week 4 which will be the planned order receipt in week 5.
Week 6:
The gross requirement is 200 (1 assembly) derived from planned order release of C. The on hand inventory is 0. Hence, the net requirement is 200. The lead time is 1 week. Therefore, the planned order release will be 200 in week 5 which will be the planned order receipt in week 6.
Week 7:
The gross requirement is 100 (1 assembly) derived from the planned order release of C. The on hand inventory is 0. Hence, the net requirement is 100. The lead time is 1 week. Therefore, the planned order release will be 100 in week 6 which will be the planned order receipt in week 7.
Week 8:
The gross requirement is 150 (1 assembly) derived from planned order release of C and K. The on hand inventory is 0. Hence, the net requirement is 150. The lead time is 1 week. Therefore, the planned order release will be 150 in week 7 which will be the planned order receipt in week 8.
Week 9:
The gross requirement is 300 (1 assembly) derived from planned order release of C. The on hand inventory is 0. Hence, the net requirement is 300. The lead time is 1 week. Therefore, the planned order release will be 300 in week 8 which will be the planned order receipt in week 9.
Want to see more full solutions like this?
Chapter 14 Solutions
EBK PRINCIPLES OF OPERATIONS MANAGEMENT
- Employee In-Service Training ASSIGNMENT: In-Service Training. The intern is required to plan and implement two in-service training sessions for employees. Each in-service should last at least 10 but not more than 30 minutes and should be given to all employees affected. The preceptor or supervisor/unit manager must approve all in-service topics. 1) One presentation should be related to a policy or procedure of any kind (e.g. proper use of equipment); 2) The second presentation must be related to sanitation or safety. For each in-service presentation, the intern must develop a written class plan and a visual aid (may be a handout, poster, PowerPoint slide presentation, etc.) appropriate to the life experiences, cultural diversity and educational background of the target audience. The intern must also measure behavior change. Note, this cannot be measured by a written pre- and post- test. That would be measuring knowledge. The intern mustactually observe and document that the learners…arrow_forwardFor a dietary manager in a nursing home to train a dietary aidearrow_forwardDietary Management in a Nursing Home. As detailed as possible.arrow_forward
- For dietary management in a nursing home. As detailed as possible.arrow_forwardA small furniture manufacturer produces tables and chairs. Each product must go through three stages of the manufacturing process – assembly, finishing, and inspection. Each table requires 3 hours of assembly, 2 hours of finishing, and 1 hour of inspection. The profit per table is $120 while the profit per chair is $80. Currently, each week there are 200 hours of assembly time available, 180 hours of finishing time, and 40 hours of inspection time. Linear programming is to be used to develop a production schedule. Define the variables as follows: T = number of tables produced each week C= number of chairs produced each week According to the above information, what would the objective function be? (a) Maximize T+C (b) Maximize 120T + 80C (c) Maximize 200T+200C (d) Minimize 6T+5C (e) none of the above According to the information provided in Question 17, which of the following would be a necessary constraint in the problem? (a) T+C ≤ 40 (b) T+C ≤ 200 (c) T+C ≤ 180 (d) 120T+80C ≥ 1000…arrow_forwardAs much detail as possible. Dietary Management- Nursing Home Don't add any fill-in-the-blanksarrow_forward
- Menu Planning Instructions Use the following questions and points as a guide to completing this assignment. The report should be typed. Give a copy to the facility preceptor. Submit a copy in your Foodservice System Management weekly submission. 1. Are there any federal regulations and state statutes or rules with which they must comply? Ask preceptor about regulations that could prescribe a certain amount of food that must be kept on hand for emergencies, etc. Is the facility accredited by any agency such as Joint Commission? 2. Describe the kind of menu the facility uses (may include standard select menu, menu specific to station, non-select, select, room service, etc.) 3. What type of foodservice does the facility have? This could be various stations to choose from, self-serve, 4. conventional, cook-chill, assembly-serve, etc. Are there things about the facility or system that place a constraint on the menu to be served? Consider how patients/guests are served (e.g. do they serve…arrow_forwardWork with the chef and/or production manager to identify a menu item (or potential menu item) for which a standardized recipe is needed. Record the recipe with which you started and expand it to meet the number of servings required by the facility. Develop an evaluation rubric. Conduct an evaluation of the product. There should be three or more people evaluating the product for quality. Write a brief report of this activity • Product chosen and the reason why it was selected When and where the facility could use the product The standardized recipe sheet or card 。 o Use the facility's format or Design one of your own using a form of your choice; be sure to include the required elements • • Recipe title Yield and portion size Cooking time and temperature Ingredients and quantities Specify AP or EP Procedures (direction)arrow_forwardASSIGNMENT: Inventory, Answer the following questions 1. How does the facility survey inventory? 2. Is there a perpetual system in place? 3. How often do they do a physical inventory? 4. Participate in taking inventory. 5. Which type of stock system does the facility use? A. Minimum stock- includes a safety factor for replenishing stock B. Maximum stock- equal to a safety stock plus estimated usage (past usage and forecasts) C. Mini-max-stock allowed to deplete to a safety level before a new order is submitted to bring up inventory up to max again D. Par stock-stock brought up to the par level each time an order is placed regardless of the amount on hand at the time of order E. Other-(describe) Choose an appropriate product and determine how much of an item should be ordered. Remember the formula is: Demand during lead time + safety stock = amount to order Cost out an inventory according to data supplied. Remember that to do this, you will need to take an inventory, and will need to…arrow_forward
- Practical Management ScienceOperations ManagementISBN:9781337406659Author:WINSTON, Wayne L.Publisher:Cengage,MarketingMarketingISBN:9780357033791Author:Pride, William MPublisher:South Western Educational PublishingPurchasing and Supply Chain ManagementOperations ManagementISBN:9781285869681Author:Robert M. Monczka, Robert B. Handfield, Larry C. Giunipero, James L. PattersonPublisher:Cengage Learning
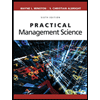
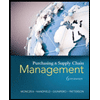