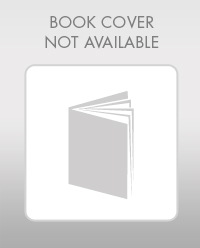
Concept explainers
a)
To determine: The optimal order quantity.
Introduction: Inventory management is the process of ordering, storing and using inventory of the company such raw material, components and finished goods. It governs the flow of goods from manufacturers to warehouse and to the point of sale. The key function is to maintain record of flow of new or returned products which enters or leaves the company.
a)

Answer to Problem 24P
The optimal order quantity is 16,970.56.
Explanation of Solution
Given information:
Formula:
Where
Calculation of optimal order quantity:
Calculation of EOQ for orders less than 2000 pieces:
Holding cost is 5% of the purchase price for orders less than 2000 pieces which is 0.05 multiplied by 7.80 which yields 0.39.
EOQ for order less than 2000 pieces is calculated by multiplying 2, 45,000 and 200 and dividing the resultant with 0.39 and taking square root which gives 6,793.66 pieces.
Calculation of EOQ for orders between 2,001 to 5,000 pieces:
Holding cost is 5% of the purchase price for orders between 2001 to 5000 pieces which is 0.05 multiplied by 1.60 which yields 0.08.
EOQ for order orders between 2,001 to 5,000 pieces is calculated by multiplying 2, 45,000 and 200 and dividing the resultant with 0.08 and taking square root which gives 15,000 pieces.
Calculation of EOQ for orders between 5,001 to 10,000 pieces:
Holding cost is 5% of the purchase price for orders between 5,001 to 10,000 pieces which is 0.05 multiplied by 1.40 which yields 0.07.
EOQ for order orders between 5,001 to 10,000 pieces is calculated by multiplying 2, 45,000 and 200 and dividing the resultant with 0.07 and taking square root which gives 16,035.67 pieces.
Calculation of EOQ for orders more than 10,001 pieces:
Holding cost is 5% of the purchase price for orders more than 10,001 pieces which is 0.05 multiplied by 1.25 which yields 0.0625.
EOQ for order orders more than 10,001 pieces is calculated by multiplying 2, 45,000 and 200 and dividing the resultant with 0.0625 and taking square root which gives 16,970.56 pieces.
Based on the above calculations, EOQ for orders more than 10,001 pieces gives optimal order quantity as the EOQ lies within the quantities ordered. Therefore the optimal order quantity is 16,970.56 pieces at $1.25.
Hence, the optimal order quantity is 16,970.56.
b)
To determine: The annual holding cost.
b)

Answer to Problem 24P
The annual holding cost is $530.33.
Explanation of Solution
Given information:
Formula:
Calculation annual holding cost:
Annual holding cost is calculated by multiplying half of the economic order quantity which is 16,971 divided by 2 and multiplying with 0.0625 which yields $530.33.
Hence, the annual holding cost is $530.33.
c)
To determine: The annual setup cost.
c)

Answer to Problem 24P
The annual setup cost is $530.33.
Explanation of Solution
Given information:
Formula:
Calculation annual ordering cost:
Annual ordering cost is calculated by dividing 45,000 with 16,971 and multiplying the resultant with 200 which yields $530.33.
Hence, the annual ordering cost is $530.33.
d)
To determine: The annual cost of silverware with optimal order quantity.
d)

Answer to Problem 24P
The annual cost of silverware with optimal order quantity is $56,250.
Explanation of Solution
Given information:
Formula:
Calculation of annual cost of silverware with optimal order quantity:
Annual cost of silverware with optimal order quantity is calculated by multiplying 1.25 with 45,000 which gives $56,250.
Hence, the annual cost of silverware with optimal order quantity is $56,250.
e)
To determine: The total annual cost including ordering, holding and purchasing the silverware.
e)

Answer to Problem 24P
The total annual cost including ordering, holding and purchasing the silverware is $57,310.66.
Explanation of Solution
Given information:
Calculation of total annual cost:
Total annual cost is calculated by adding holding cost, ordering cost and unit cost which is 530.33, 530.33 and 56,250 is summed up to give 57,310.66.
Hence, the total annual cost including ordering, holding and purchasing the silverware is $57,310.66.
Want to see more full solutions like this?
Chapter 12 Solutions
Principles Of Operations Management
- A small furniture manufacturer produces tables and chairs. Each product must go through three stages of the manufacturing process – assembly, finishing, and inspection. Each table requires 3 hours of assembly, 2 hours of finishing, and 1 hour of inspection. The profit per table is $120 while the profit per chair is $80. Currently, each week there are 200 hours of assembly time available, 180 hours of finishing time, and 40 hours of inspection time. Linear programming is to be used to develop a production schedule. Define the variables as follows: T = number of tables produced each week C= number of chairs produced each week According to the above information, what would the objective function be? (a) Maximize T+C (b) Maximize 120T + 80C (c) Maximize 200T+200C (d) Minimize 6T+5C (e) none of the above According to the information provided in Question 17, which of the following would be a necessary constraint in the problem? (a) T+C ≤ 40 (b) T+C ≤ 200 (c) T+C ≤ 180 (d) 120T+80C ≥ 1000…arrow_forwardAs much detail as possible. Dietary Management- Nursing Home Don't add any fill-in-the-blanksarrow_forwardMenu Planning Instructions Use the following questions and points as a guide to completing this assignment. The report should be typed. Give a copy to the facility preceptor. Submit a copy in your Foodservice System Management weekly submission. 1. Are there any federal regulations and state statutes or rules with which they must comply? Ask preceptor about regulations that could prescribe a certain amount of food that must be kept on hand for emergencies, etc. Is the facility accredited by any agency such as Joint Commission? 2. Describe the kind of menu the facility uses (may include standard select menu, menu specific to station, non-select, select, room service, etc.) 3. What type of foodservice does the facility have? This could be various stations to choose from, self-serve, 4. conventional, cook-chill, assembly-serve, etc. Are there things about the facility or system that place a constraint on the menu to be served? Consider how patients/guests are served (e.g. do they serve…arrow_forward
- Work with the chef and/or production manager to identify a menu item (or potential menu item) for which a standardized recipe is needed. Record the recipe with which you started and expand it to meet the number of servings required by the facility. Develop an evaluation rubric. Conduct an evaluation of the product. There should be three or more people evaluating the product for quality. Write a brief report of this activity • Product chosen and the reason why it was selected When and where the facility could use the product The standardized recipe sheet or card 。 o Use the facility's format or Design one of your own using a form of your choice; be sure to include the required elements • • Recipe title Yield and portion size Cooking time and temperature Ingredients and quantities Specify AP or EP Procedures (direction)arrow_forwardASSIGNMENT: Inventory, Answer the following questions 1. How does the facility survey inventory? 2. Is there a perpetual system in place? 3. How often do they do a physical inventory? 4. Participate in taking inventory. 5. Which type of stock system does the facility use? A. Minimum stock- includes a safety factor for replenishing stock B. Maximum stock- equal to a safety stock plus estimated usage (past usage and forecasts) C. Mini-max-stock allowed to deplete to a safety level before a new order is submitted to bring up inventory up to max again D. Par stock-stock brought up to the par level each time an order is placed regardless of the amount on hand at the time of order E. Other-(describe) Choose an appropriate product and determine how much of an item should be ordered. Remember the formula is: Demand during lead time + safety stock = amount to order Cost out an inventory according to data supplied. Remember that to do this, you will need to take an inventory, and will need to…arrow_forwardHuman Relations, Systems, and Organization Assignments ORGANIZATION: Review the organization chart for the facility • Draw an organization chart for the department. • . Identify and explain the relationships of different units in the organization and their importance to maintain the food service department's mission. Include a copy in your weekly submission. There is a feature in PowerPoint for doing this should you want to use it. JOB ORGANIZATION: ⚫ A job description is a broad, general, and written statement for a specific job, based on the findings of a job analysis. It generally includes duties, purpose, responsibilities, scope, and working conditions of a job along with the job's title, and the name or designation of the person to whom the employee reports. Job description usually forms the basis of job specification. • Work with your preceptor or supervisor to identify a position for which you will write a job description. Include a copy of the job description you write in your…arrow_forward
- Purchasing and Supply Chain ManagementOperations ManagementISBN:9781285869681Author:Robert M. Monczka, Robert B. Handfield, Larry C. Giunipero, James L. PattersonPublisher:Cengage LearningPractical Management ScienceOperations ManagementISBN:9781337406659Author:WINSTON, Wayne L.Publisher:Cengage,MarketingMarketingISBN:9780357033791Author:Pride, William MPublisher:South Western Educational Publishing
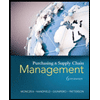
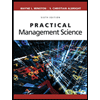