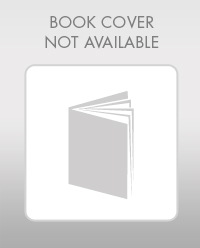
Concept explainers
a)
To determine: The daily demand of the product.
Introduction: Inventory management is the process of ordering, storing and using inventory of the company such raw material, components and finished goods. It governs the flow of goods from manufacturers to warehouse and to the point of sale. The key function is to maintain record of flow of new or returned products which enters or leaves the company.
a)

Answer to Problem 30P
The daily demand of the product is 32.
Explanation of Solution
Given information:
Calculation of daily demand of the product:
The daily demand is calculated by dividing the annual demand, 8000 with the number of working days, 250 which gives the result as 32 units.
Hence, the daily demand is 32 units.
b)
To determine: The number of day production must be carried out.
b)

Answer to Problem 30P
The number of day production must be carried out is 2days.
Explanation of Solution
Given information:
Calculation of number of days in production runs:
Number of days production must be carried out is calculated by dividing the production quantity, (400) with production rate (200) which gives 2 days.
Hence, the number of day production must be carried out is 2days.
c)
To determine: The number production runs per year and annual setup cost.
c)

Answer to Problem 30P
The number of day production runs per year is 20 and annual setup cost is $2,400.
Explanation of Solution
Given information:
Calculation of number of production runs per year and annual setup cost:
Number of production runs per year:
Number of production runs per year is calculated by dividing the demand (8000) with production quantity (400) which gives 20.
Annual setup cost:
Annual setup cost is calculated by multiplying number of production runs per year (20) with setup cost (120) which gives $2,400 as annual setup cost.
Hence, the number of production runs per year is 20 and annual setup cost is $2,400.
d)
To determine: The maximum and average inventory levels.
d)

Answer to Problem 30P
The maximum and average inventory levels are 336 and 168 respectively.
Explanation of Solution
Given information:
Calculation of maximum inventory and average inventory level:
Maximum inventory level:
Maximum inventory is calculated by multiplying production quantity (400) with
Average inventory level:
Average inventory is calculated by dividing maximum inventory level, 336 by 2 which gives168.
Hence, the maximum and average inventory levels are 336 and 168 respectively.
e)
To determine: The total annual setup cost and holding cost.
e)

Answer to Problem 30P
The total annual setup cost and holding cost is $8,400 and $2400 respectively.
Explanation of Solution
Given information:
Calculation of total annual setup and holding cost:
Total holding cost is calculated by multiplying average inventory (168) with holding cost (50) which yields $8,400.
Total setup cost is calculated by multiplying number of production runs (20) with setup cost (120) which yields $2,400.
Hence, the total annual setup cost and holding cost is $8,400 and $2400 respectively.
f)
To determine: The number of refrigerators to be produced in each production line to minimize the total annual inventory cost and the net saving in inventory.
f)

Answer to Problem 30P
The number of refrigerators to be produced in each production line to minimize the total annual inventory cost is 37.1 and the net saving in inventory is $1,820.
Explanation of Solution
Given information:
Calculation of number of refrigerators produced in each production run:
Number of refrigerators produced in each production run is calculated by dividing
Calculation of holding and setup cost:
Maximum inventory level:
Maximum inventory is calculated by multiplying production quantity (213.81) with
Average inventory level:
Holding cost:
Total holding cost is calculated by multiplying average inventory (89.6002) with holding cost (50) which yields $4,490.
Number of production runs per year:
Number of production runs per year is calculated by dividing the demand (8000) with production quantity (213.81) which gives 37.41.
Setup cost:
Total cost:
Total cost is the sum of holding cost and set up cost which is sum of $4,490 and $4,490 which gives $8,980.
Total saving:
Total savings in cost is calculated by taking the difference of $10,800 and $8,980 which gives $1,820.
Hence, the number of refrigerators to be produced in each production line to minimize the total annual inventory cost is 37.1 and the net saving in inventory is $1,820.
Want to see more full solutions like this?
Chapter 12 Solutions
Principles Of Operations Management
- Currently a company that designs Web sites has five customers in its backlog. The time since the order arrived, processing time, and promised due dates are given in the following table. The customers are ready to be scheduled today, which is the start of day 190. Time Since Order Arrived Customer (days ago) Processing Time (days) Due Date (days from now) A 3 24 58 B 2 32 100 с 10 20 26 D E 8 6 12 28 50 66 a. Develop separate schedules by using the FCFS and EDD rules. Compare the schedules on the basis of average flow time and average days past due. Using the FCFS (first come, first served) decision rule for sequencing the customers, the order is: Sequence Customer 1 2 3 4 5arrow_forwardThe Donald Fertilizer Company produces industrial chemical fertilizers. The projected manufacturing requirements (in gallons) for the next four quarters are 60,000, 90,000, 90,000, and 140,000 respectively. A level workforce is desired, relying only on anticipation inventory as a supply option. Stockouts and backorders are to be avoided, as are overtime and undertime. a. Determine the quarterly production rate required to meet total demand for the year, and minimize the anticipation inventory that would be left over at the end of the year. Beginning inventory is 0. The quarterly production rate is ☐ gallons. (Enter your response as an integer.)arrow_forwardHow would you design an operations plan and schedule for a new product/service? What factors would you consider and what challenges would you anticipate? Why are these factors and challenges relevant and how would you address them?arrow_forward
- You are the newly appointed CEO of TechSouth, a South African multinational technology company based in Cape Town. TechSouth specialises in manufacturing smartphones, laptops, and smart home devices. The company has a significant presence in the African market and has recently expanded into Europe and Asia. However, TechSouth is facing several critical challenges:· Declining Market Share - Over the past three years, TechSouth has lost considerable market share to both localcompetitors and international giants like Samsung and Apple. The company's products are perceived as outdated and lacking innovation.· Employee Engagement Issues - Recent employee surveys indicate low morale and engagement levels, particularly among the younger workforce, leading to high turnover rates. Many employees feel disconnected from the company's vision and mission.· Siloed Departments - The organizational structure at TechSouth is highly siloed, with departments operatingindependently rather than…arrow_forwardWhat is the best way to manage emotions and thoughts? How to work through Emotions and thoughts?arrow_forwardWhat are the emotions or stressful thoughts? What are the differences between them? How can we work through the emotions or stressful thoughts? How can we avoid or prevent emotions or stressful thoughts from happening or occurring? What are the obstacles?arrow_forward
- Main Challenges at TechInnovateStrategic DirectionTechInnovate's board of directors is pushing for a more aggressive expansion into emerging markets, particularly in Africaand Southeast Asia. However, there's internal disagreement about whether to focus on these new markets or consolidatetheir position in existing ones. Sarah Chen favors rapid expansion, while some senior executives advocate for a morecautious approach.Ethical ConcernsThe company's AI algorithms have come under scrutiny for potential biases, particularly in facial recognition technology.There are concerns that these biases disproportionately affect minority groups. Some employees have voiced ethicalconcerns about selling this technology to law enforcement agencies without addressing these issues.Team Leadership and DiversityTechInnovate's leadership team is predominantly male and Western, despite its global presence. There's growing pressurefrom employees and some board members to diversify the leadership team to…arrow_forwardSarah Anderson, the Marketing Manager at Exeter Township's Cultural Center, is conducting research on the attendance history for cultural events in the area over the past ten years. The following data has been collected on the number of attendees who registered for events at the cultural center. Year Number of Attendees 1 700 2 248 3 633 4 458 5 1410 6 1588 7 1629 8 1301 9 1455 10 1989 You have been hired as a consultant to assist in implementing a forecasting system that utilizes various forecasting techniques to predict attendance for Year 11. a) Calculate the Three-Period Simple Moving Average b) Calculate the Three-Period Weighted Moving Average (weights: 50%, 30%, and 20%; use 50% for the most recent period, 30% for the next most recent, and 20% for the oldest) c) Apply Exponential Smoothing with the smoothing constant alpha = 0.2. d) Perform a Simple Linear Regression analysis and provide the adjusted…arrow_forwardRuby-Star Incorporated is considering two different vendors for one of its top-selling products which has an average weekly demand of 70 units and is valued at $90 per unit. Inbound shipments from vendor 1 will average 390 units with an average lead time (including ordering delays and transit time) of 4 weeks. Inbound shipments from vendor 2 will average 490 units with an average lead time of 2 weeksweeks. Ruby-Star operates 52 weeks per year; it carries a 4-week supply of inventory as safety stock and no anticipation inventory. Part 2 a. The average aggregate inventory value of the product if Ruby-Star used vendor 1 exclusively is $enter your response here.arrow_forward
- Sam's Pet Hotel operates 50 weeks per year, 6 days per week, and uses a continuous review inventory system. It purchases kitty litter for $13.00 per bag. The following information is available about these bags: > Demand 75 bags/week > Order cost = $52.00/order > Annual holding cost = 20 percent of cost > Desired cycle-service level = 80 percent >Lead time = 5 weeks (30 working days) > Standard deviation of weekly demand = 15 bags > Current on-hand inventory is 320 bags, with no open orders or backorders. a. Suppose that the weekly demand forecast of 75 bags is incorrect and actual demand averages only 50 bags per week. How much higher will total costs be, owing to the distorted EOQ caused by this forecast error? The costs will be $higher owing to the error in EOQ. (Enter your response rounded to two decimal places.)arrow_forwardYellow Press, Inc., buys paper in 1,500-pound rolls for printing. Annual demand is 2,250 rolls. The cost per roll is $625, and the annual holding cost is 20 percent of the cost. Each order costs $75. a. How many rolls should Yellow Press order at a time? Yellow Press should order rolls at a time. (Enter your response rounded to the nearest whole number.)arrow_forwardPlease help with only the one I circled! I solved the others :)arrow_forward
- Practical Management ScienceOperations ManagementISBN:9781337406659Author:WINSTON, Wayne L.Publisher:Cengage,Purchasing and Supply Chain ManagementOperations ManagementISBN:9781285869681Author:Robert M. Monczka, Robert B. Handfield, Larry C. Giunipero, James L. PattersonPublisher:Cengage Learning
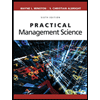
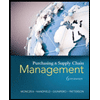